In many industries, nearly 10 percent of serious accidents result from a failure to control hazardous energy during servicing and maintenance activities. Preventing such accidents is the goal of the Occupational Safety and Health Administration’s standard for “The control of hazardous energy (lockout/tagout),” 29 CFR 1910.147. This standard outlines the procedures employees must use to prevent the unexpected release of hazardous energy from machines and equipment during servicing and maintenance.
The lockout/tagout standard requires each employer to establish a program for affixing lockout or tagout devices to energy-isolating devices on machines and equipment to prevent their unexpected energization, startup, or release of stored energy. This program must include documented energy-control procedures that are specifically tailored to machinery and equipment in the workplace and developed before any servicing or maintenance begins.
The principles and requirements for lockout/tagout apply to employers in all general industry workplaces where employees perform servicing or maintenance on machines or equipment that could expose them to the unexpected release of hazardous energy. All employers must understand the importance of compliance with this standard.
The standard doesn’t apply in certain situations such as transmission and distribution hot tap operations, unplugged equipment under the exclusive control of an authorized worker, when continuity of service is essential, where shutdown is impractical, and when following documented procedures and using special equipment that will provide proven effective protection for employees.
Full information about energy-control provisions may be found in the following OSHA standards:
Key definitions
Affected employee: An employee, such as a machine or equipment operator, who is required to use machines or equipment serviced or maintained under lockout or tagout, or who performs other job responsibilities in an area where such servicing or maintenance is performed. An affected employee becomes an authorized employee when that employee’s duties include performing servicing or maintenance covered under the lockout/tagout standard.
Authorized employee: An employee who locks out or tags out machines or equipment to perform servicing or maintenance on those machines or that equipment. Any employee who performs one or more procedural elements of an employer’s energy-control program for the purpose of servicing or maintenance is considered an authorized employee.
Capable of being locked out: One of the two categories of energy-isolating device. An energy-isolating device is considered capable of being locked out if it:
- Has a hasp or other means of attachment to or through which a lock can be affixed;
- Has a locking mechanism built in; or
- Can be locked without being dismantled, rebuilt, replaced, or permanently altered in its energy-control capability.
Energized: Of machinery or equipment, connected to an energy source or containing residual or stored energy.
Energy-isolating device: A mechanical device used to physically prevent the transmission or release of energy, including but not limited to the following:
- A manually operated electrical circuit breaker,
- A disconnect switch,
- A manually operated switch by which a circuit’s conductors can be disconnected from all ungrounded supply conductors and no pole can be operated independently,
- A line valve;
- A block; and
- Any similar device used to block or isolate energy. Excluded are push buttons, selector switches, and other control circuit type devices.
Energy source: Any source of electrical, mechanical, hydraulic, pneumatic, chemical, thermal, or other type of energy.
Hot tap. A procedure used in repair, maintenance, and servicing that involves welding on a piece of equipment (such as a pipeline, vessel, or tank) under pressure to install connections or appurtenances. It is commonly used to replace or add sections of pipeline without the interruption of service for air, gas, water, steam, and petrochemical distribution systems.
Lockout: The placement of a lockout device on an energy-isolating device, in accordance with an established procedure, ensuring that the energy-isolating device and the machine or equipment being controlled cannot be operated until the lockout device is removed.
Lockout device: Any device that uses positive means, such as a lock, to hold an energy-isolating device in a safe position, thereby preventing the energizing of machinery or equipment. Included are blank flanges and bolted slip blinds.
Other employees: All employees who are or may be in an area where energy-control procedures may be used.
Normal production operations: The use of a machine or equipment to perform its intended production function.
Servicing and/or maintenance: Workplace activities such as constructing, installing, setting up, adjusting, inspecting, modifying, and maintaining and/or servicing machines or equipment. These activities include lubrication, cleaning or unjamming machines or equipment, and making adjustments or tool changes, where employees could be exposed to the unexpected energization or startup of the equipment or release of hazardous energy.
Setting up: Any work performed to prepare a machine or equipment to perform its normal production operation.
Tagout: The placement of a tagout device on an energy-isolating device, in accordance with an established procedure, to indicate that the energy-isolating device and the machine or equipment being controlled may not be operated until the tagout device is removed.
Tagout device: Any prominent warning device, such as a tag and a means of attachment, that can be securely fastened to an energy-isolating device to indicate that the machine or equipment to which it is attached may not be operated until the tagout device is removed.
What are the requirements of the lockout/tagout standard? (General industry)
- Each employer is required to develop an energy-control program consisting of energy-control procedures, employee training, and periodic inspections.
The Occupational Safety and Health Administration’s (OSHA’s) lockout/tagout standard lays out the minimum requirements for employers whose employees are exposed to hazardous energy during the servicing and maintenance of machinery and equipment. Each employer covered by the standard must develop, implement, and enforce an energy-control program to protect employees against injury from the unexpected release of hazardous energy. Among the most critical requirements of this program for employers are to:
- Develop, implement, and enforce documented energy-control procedures;
- Use lockout devices for all energy-isolating devices that can be locked out, unless an employer can demonstrate that a tagout program will provide a level of safety equivalent to the protection provided by a lockout program;
- Ensure that all new and overhauled machinery and equipment can be locked out;
- Develop, implement, and enforce an effective tagout program if machines or equipment cannot be locked out;
- Use only lockout/tagout devices authorized for the specific machines and equipment to which they are applied;
- Ensure that lockout/tagout devices are standardized, durable, and substantial;
- Ensure that lockout/tagout devices identify their individual users;
- Permit only the employee who applied a lockout/tagout device to remove it;
- Provide effective training for all authorized, affected, and other employees covered by the standard, and document certification of this training;
- Inspect energy-control procedures at least annually and document certification of these inspections; and
- Comply with the additional energy-control provisions when machines or equipment must be tested or repositioned during servicing and maintenance, when outside contractors work at the site, when lockout is performed by a group of employees, and when shifts or personnel change.
What are the parts of an energy-control program?
- An energy control program is made up of energy-control procedures, training for those procedures, and inspections of employees following those procedures.
- Each energy-control procedure specifies the necessary steps to control hazardous energy on a particular machine or piece of equipment.
The Occupational Safety and Health Administration’s (OSHA’s) lockout/tagout standard requires employers to establish an energy-control program tailored to the machinery and equipment in each workplace to protect employees from the unexpected release of hazardous energy during servicing and maintenance activities. An energy-control program includes:
- Energy-control procedures, which specify the steps employees must take to isolate machines and equipment from their energy sources and to render them safe for employees to perform servicing and maintenance;
- Employee training, which teaches authorized employees, affected employees, and other employees their responsibilities as laid out by the energy-control procedures; and
- Periodic inspections of employees performing the energy-control procedures, which ensure the procedures are followed and understood.
Lockout vs. tagout
At the core of an employer’s energy-control program are the protective tools that control hazardous energy: the energy-control devices. There are two types of energy-control device:
- Energy-isolation devices¸ which physically prevent the transmission and release of energy; and
- Lockout/tagout devices, which are applied to energy-isolation devices to prevent them from being operated during servicing and maintenance.
Together, when properly used, energy-isolation devices and lockout/tagout devices protect employees from the unexpected energization of machines and equipment.
There are two kinds of energy-isolation device:
- Energy-isolation devices that are capable of being locked out, and
- Energy-isolation devices that are incapable of being locked out cannot be locked out.
The specific lockout/tagout devices that employers must provide to employees depends in large part on whether the energy-isolation devices on machinery and equipment in their workplaces are of one kind or another.
These two kinds of energy-isolation device correspond to two kinds of lockout/tagout device:
- Lockout devices, which when fastened to energy-isolation devices that can be locked out physically hold them in place; and
- Tagout devices, which display prominent warnings against operating energy-isolation devices while the tagout devices are in place.
OSHA requires employers to use lockout devices on energy-isolation devices that are capable of being locked out. On energy-isolation devices that are incapable of being locked out, OSHA requires tagout devices to be fastened as close as possible to the energy-isolation device to communicate their warnings as clearly as possible.
There is one exception to the lockout device requirement:
- An employer may have employees use tagout devices on energy-isolation devices that are capable of being locked out only if that employer demonstrates that the tagout program provides full employee protection. Full employee protection requires the use of additional protective measures: ...
Stand-alone tagout system
If, due to equipment age or construction, a lockout device cannot be used, the employer’s energy-control program must use a tagout system. If an energy-isolating device is capable of being locked out, it must be locked out during service and maintenance operations unless the employer can demonstrate that a tagout system provides full employee protection.
When a tagout system is used instead of lockout, the employer must supplement tagout with additional means to ensure full employee protection. These additional means could include the removal of an isolating circuit element, blocking of a controlling switch, opening of an extra disconnecting device, or the removal of a valve handle to reduce the likelihood of inadvertent energization. Tagout alone does not physically prevent activation of the control, and it may give a false sense of security to the employee. Further training will be required if the employer must use a tagout system.
Whenever machines or equipment are installed, replaced, renovated, modified, or repaired, the energy-isolating devices on such machines and equipment must be designed to accept a lockout device.
Energy-control procedures
Each employer must develop and document energy-control procedures for isolating machines and equipment in the workplace from their energy sources before any employees may service or maintain them. An energy-control procedure serves to guide employees through the application of lockout or tagout devices to energy isolation devices to disable a machine or piece of equipment inoperative and safe to service.
At minimum, each of an employer’s energy-control procedures must clearly specify the scope, purpose, authorization, rules, and techniques that employees will use to control potentially hazardous energy. To guide employees effectively, each written energy-control procedure must provide them with at least the following information:
- A specific statement on how employees are intended to use the procedure;
- Which employees are authorized to perform the procedure;
- The employer’s means for enforcing compliance;
- Each specific step for shutting down, isolating, blocking, and securing a machine or piece of equipment;
- Each specific step for placing, removing, and transferring lockout or tagout devices;
- Each specific step for releasing, draining, or otherwise controlling stored energy; and
- Each specific requirement for testing a machine to verify that lockout devices, tagout devices, and any other energy-control methods are effective.
If the information employees need to control hazardous energy effectively is the same for multiple machines in the workplace, then a single written procedure may be used for all such similar machines. However, machines or equipment with, for example, different kinds of energy sources, different energy-isolating devices, or different procedural steps to follow require separate written energy-control procedures.
NOTE: Exception to documentation requirements
Employers are not required to document an energy-control procedure for a particular machine or piece of equipment only if each of the following eight conditions apply:
- The machine or equipment has no potential for stored or residual energy, or the re-accumulation of stored energy after shutdown;
- The machine or equipment has a single energy source which can be readily identified and isolated;
- The isolation and locking out of that energy source completely de-energizes and deactivates the machine or equipment;
- The machine or equipment is isolated from that energy source and locked out during servicing or maintenance;
- A single lockout device achieves a locked-out condition;
- The lockout device is exclusively controlled by the authorized employee performing the servicing or maintenance;
- The servicing or maintenance does not create hazards for other employees; and
- The employer has had no accidents involving the unexpected activation or re-energization of the machine or equipment during servicing or maintenance.
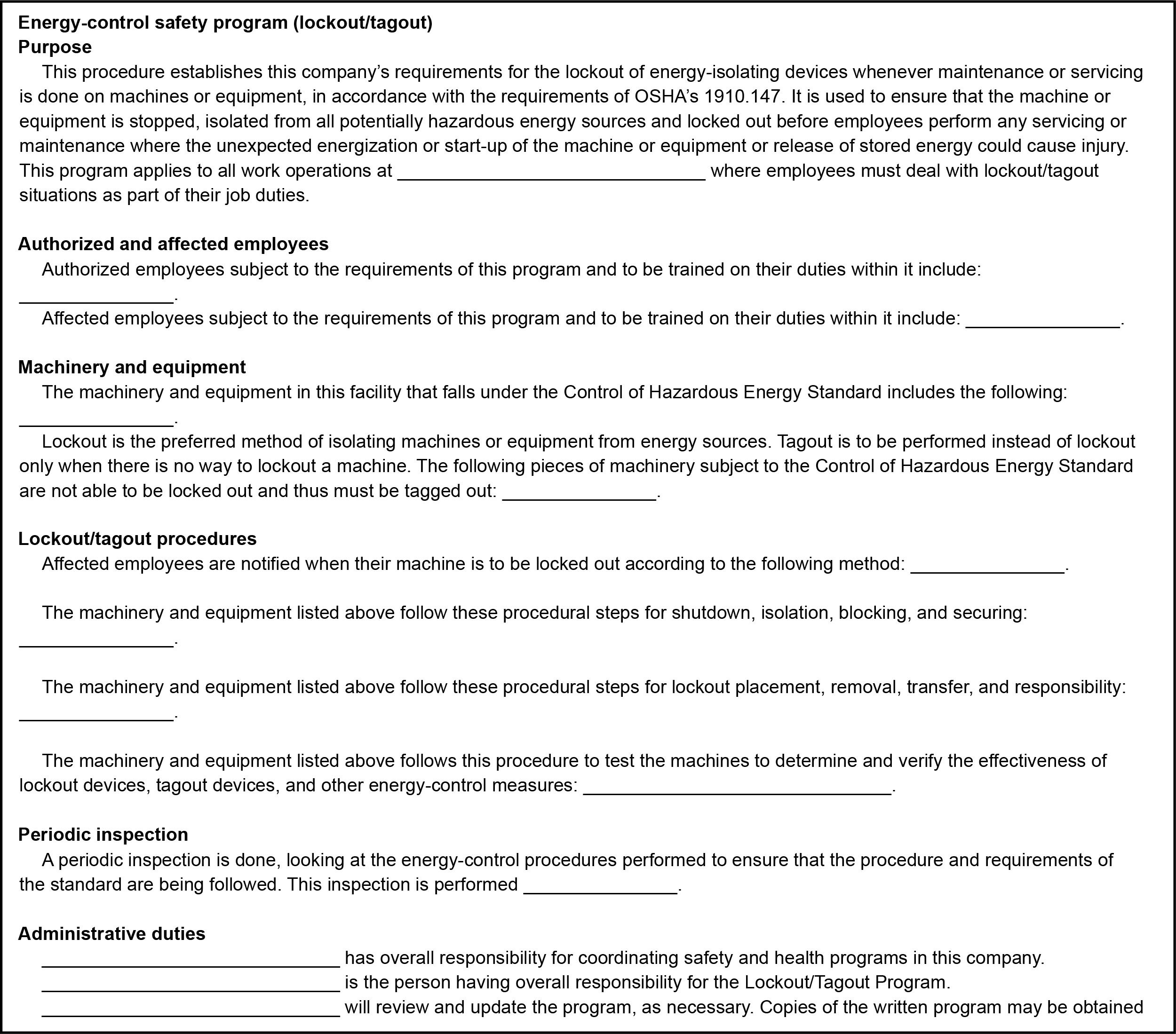
What are required steps of an energy-control procedure?
Energy-control procedures guide employees through the necessary steps for safely controlling hazardous energy on machines specific and equipment. Each energy-control procedure must detail, in the proper order, the six procedural steps for applying lockout/tagout to a given machine or piece of equipment before servicing or maintenance begins and the five procedural steps for releasing that machine from lockout/tagout after servicing or maintenance is complete. The six steps for applying lockout/tagout are:
- Preparation for shutdown,
- Shutdown,
- Energy isolation,
- Application of lockout/tagout devices,
- Release of stored energy, and
- Verification of isolation.
An energy-control procedure must also detail the steps for releasing a machine or piece of equipment from lockout/tagout once servicing and maintenance have been completed. The five steps for releasing machinery and equipment are:
- Inspection of system components,
- Checking for safe positioning,
- Removal of lockout/tagout devices,
- Notification of removal, and
- Safe re-energization.
Authorized employees
Importantly, the only employees who may perform energy-control procedures on machines and equipment are the employees who service and maintain them. It is essential that those employees who are exposed to hazardous energy during servicing and maintenance activities are the ones responsible for taking the procedural steps that protect against energization hazards.
Documenting LOTO events
The standard does not include any requirement to fill out or keep a log or other record of lockout/tagout events. If the employer keeps service or maintenance logs as a “best practice,” it would be up to that employer to establish whatever procedures and record retention times that best fit the need of the company.
What are the steps for applying controls?
Workers must follow their employer’s energy control plan while applying LOTO controls to avoid exposure to hazardous energy.
- Preparation for shutdown
The first step in an energy-control procedure is ensuring two conditions are met before a machine or piece of equipment is shut down. First, employers must ensure that each authorized employee who will perform servicing or maintenance knows the following information: - The types and magnitude of the energy to be controlled,
- The hazards this energy poses, and
- The devices and methods used to control this energy.
Second, an employer or authorized employee must notify all affected employees that lockout or tagout devices are about to be applied. Notifying affected employees before these devices are applied lets them know that the machine or piece of equipment will be off-limits for servicing and maintenance, which is essential for preventing employees from trying to operate locked out or tagged out machinery and equipment. - Shutdown
Once these conditions are satisfied, the machine or equipment must be turned off or shut down using the stop button or other normal stopping method. - This is the only step in an energy-control procedure that affected employees may perform as well as authorized employees. The limited involvement of affected employees serves to keep shutdown orderly and minimize additional hazards.
- Energy isolation
Once a machine or piece of equipment has been shut down, authorized employees must de-energize it by locating each energy-isolating device and setting each in the “safe” or “off” position. - Depending on the machine, operating energy-isolating devices may involve operating disconnect switches, closing valves, or other methods. Though different in structure, these all serve to physically separate or disconnect machines and equipment from their sources of energy.
- Because the number and layout of energy-isolating devices can be elaborate on complex machinery and equipment, an employer’s energy-control procedure needs to identify all energy-isolating devices for employees to locate.
- Application of lockout/tagout devices
Once all necessary energy-isolating devices are set to “safe” or “off,” authorized employees must apply to them the appropriate lockout devices (“locks”) or tagout devices (“tags”). - If the energy-isolating devices on a machine or piece of equipment can be locked out, then authorized employees must secure the appropriate locks to the energy-isolating devices so the latter are held in the “safe” or “off” position.
- If energy-isolating devices cannot be locked out or if a tagout program is used, authorized employees must secure tags as close as is safely possible to those energy-isolating devices so it is obvious that taking the latter out of the “safe” or “off” position is prohibited.
- Release of stored energy
After locks or tags are applied, authorized employee must relieve, disconnect, restrain, or render safe all potentially hazardous stored or residual energy in the machine or equipment. - Stored energy is potential energy that remains present in machines and equipment even after they are isolated from their energy sources. Each energy-control procedure must identify the types and sources of stored energy, such as capacitors, line pressure, and elevated parts, and explain what authorized employees must do to dissipate or strain it from these sources.
- If stored energy could reaccumulate in a machine or piece of equipment while employees perform servicing or maintenance service and maintain the machine or equipment, the employer must continually verify that the machine remains isolated to ensure no hazards arise. If hydraulic or pneumatic systems are present, bleed valves may be necessary to relieve built-up pressure.
- Verification of isolation
Finally, authorized employees must verify that energy isolation is complete and that the machinery or equipment is safe for servicing and maintenance. - Isolation can be verified by using test equipment, checking gauges, or by trying to restart the machinery or equipment.
- Authorized employees must always return all controls to the “off” or “stop” position following this verification step to ensure that no machine or piece of equipment starts automatically when power is restored. This is especially important for computerized machinery and equipment whose controls are programmed to remember and act on their last commands.
What are the steps for removing controls?
After servicing and maintenance is complete, authorized employees must follow the written procedural steps for reenergizing and starting up machinery and equipment.
- Inspection of system components
Authorized employees must first inspect a machine or piece of equipment to confirm that it has been returned to safe operating condition. Employees must check and ensure that:- All tools and other nonessential items have been removed,
- All safeguards removed during servicing or maintenance are reinstalled or replaced, and
- All controls at the control panel remain in the “off” or “stop” position.
This inspection is essential for worker safety: tools left behind in a machine or piece of equipment can damage it when it is reenergized, which can cause injury, downtime, and product loss; missing safeguards, meanwhile, leave employees exposed to hazardous areas when normal operations resume. For large, complex machinery and equipment, checklists or other administrative means may be necessary to ensure these inspections are sufficiently thorough. - Checking for safe positioning
Once they have completed the system inspection and reinstalled all guards, authorized employees must ensure that all affected and other employees in the area are positioned at a safe distance away from the machine or equipment before it is reenergized. - Alarms or other warning devices may be necessary for large machinery that blocks the sightlines of authorized employees.
- Removal of lockout/tagout devices
When the safe positioning of employees in the area is confirmed, each lockout or tagout device must be removed from its energy-isolating device by the authorized employee who applied it. The identity of this employee must be indicated on the device itself. - Notification of removal After authorized employees have removed lockout or tagout devices and before machinery or equipment is started up, the authorized employees or the employer must notify all affected employees that lockout or tagout devices have been removed.
- These notifications ensure that employees are safely positioned away from machines and equipment before they are reenergized.
- Restoration of energy
When these notifications are complete, an authorized employee can start the machine or equipment to confirm that it is functioning properly and is safe for normal operations to resume.
NOTE: Removal of a lockout device by others
Only the authorized employee who applies a lockout or tagout device may remove it. However, when this employee is unavailable, the employee’s device may be removed by another employee only if specific procedures documented in the employer’s lockout/tagout program are followed. The requirements of this specific procedure are that:
- The employer demonstrates that this specific procedure provides equivalent safety to that provided by the removal of the lockout or tagout device by the authorized employee who applied it,
- The employer verifies that the authorized employee who applied the device is absent from the facility,
- The employer makes all reasonable efforts to contact this authorized employee to report that the employee’s lockout/tagout device has been removed, and
- The authorized employee is informed that the device was removed before that employee resumes work at the facility.
The employer should not remove a lock without speaking to the employee who applied it. Whenever someone other than the employee who applied a lock or tag removes it, the machine or piece of equipment must be fully inspected by a qualified person to ensure that servicing or maintenance is complete and that it is safe to operate. If the authorized employee left the lock or tag in place out of negligence, the employer should strongly consider retraining or disciplinary action.
While bolt cutters or other device-destructive methods are permissible means to remove a lockout device, an employer’s specific procedure may use non-destructive methods if the employer demonstrates that it provides a degree of safety that is equivalent to the removal of the device by the authorized employee who first affixed it. A master key procedure, under which an employer has access to a key capable of opening multiple lockout devices, complies with the standard only if it includes a reliable method to ensure that access to the master key is carefully controlled by the employer. Safety is ensured through effective procedures that respect the sanctity of another employee’s lockout or tagout device.
What are the requirements for lockout/tagout devices?
- Lockout and tagout devices must be standardized, durable, substantial, and properly labeled.
All employers must provide authorized employees with lockout and tagout devices that meet the requirements of the lockout/tagout standard. These are the only devices that may be used with energy-isolating devices to control hazardous energy during servicing or maintenance, and neither type of energy-control device may be used for any other purpose.
While it’s easier to speak of “locks and tags” than always of “lockout and tagout devices,” different energy-isolating devices will need different protective hardware. To ensure that all such lockout and tagout devices remain easily noticeable and securely attached throughout servicing and maintenance, the Occupational Safety and Health Administration (OSHA) requires all lockout and tagout devices to be:
- Standardized
- Durable
- Substantial
- Labeled
Because lockout and tagout devices must be easily recognized by employees and contractors, all lockout and tagout devices in a facility must be standardized in one or more of the following ways:
For tagout devices, it is also a requirement that all text be standardized in both print and format.
Non-standardized devices make it difficult to distinguish what is locked out for servicing and maintenance from what is simply locked up. If the same kind of locks an employer assigns as lockout devices are also found on toolboxes or lockers in the employer’s facility, that employer is out of compliance with the standard.
Durable
All lockout and tagout devices must be resistant to wear and capable of withstanding the environment they are exposed to for the maximum period that exposure is expected. Tagout devices must be made and printed so that neither exposure to weather conditions, wet and damp locations, nor corrosive environments would cause tags to deteriorate or their messages to become illegible.
Substantial
Lockout devices must be substantial enough to be irremovable without the use of excessive force or unusual techniques, such as bolt cutters or other metal-cutting tools. For example, a simple little brass luggage lock is neither durable nor substantial enough to be used as an acceptable lockout device.
Tagout devices and their means of attachment must be substantial enough to prevent unintentional removal. The means of attachment for a tag must be:
- Attachable by hand,
- Self-locking,
- Non-releasable,
- Made with a minimum unlocking strength of 50 pounds,
- Designed with basic characteristics at least equivalent to a one-piece, all environment-tolerant nylon cable tie, and
- Made of non-reusable material.
- NOTE: Many employers mistake this to mean that the tags cannot be reused — the tags can be reused, but the attachment mechanism cannot.
Labeled
Each lockout device and tagout device must identify the authorized employee who applies it, using, for example, a warning tag attached to a lock’s hasp or an engraving. This identifies the person to ask about the status of the machine or equipment to which the lock or tag is applied and ensures that, after servicing or maintenance is complete, the employer can readily determine who is missing if a lock or tag is still in place.
These tags must warn employees that the machine or equipment is not to be energized and be properly labeled to accomplish this, with warnings such as “Do Not Start” or “Do Not Open.”
What training do employees need for lockout/tagout?
All employees working in areas where energy-control procedures are used must be trained in their duties under lockout/tagout. At minimum, an employer’s training program must cover:
- A review of the employer’s energy-control program,
- The elements of each energy-control procedure that relate to the employees’ duties, and
- The relevant requirements of the lockout/tagout standard (29 CFR 1910.147).
The specific training an employee receives depends on whether that employee is an authorized employee, affected employee, or other employee.
Authorized employees
Authorized employees must be trained:
- To recognize sources of hazardous energy,
- To understand the types and magnitudes of energy available to machinery and equipment and in the workplace,
- To know which lockout/tagout devices are used with which energy-isolation devices,
- To locate the energy-isolating devices on each machine and piece of equipment,
- To use the proper sequence for applying lockout/tagout devices to and removing them from the energy-isolating devices; and
- To only remove one’s personal lockout/tagout devices from energy-isolation devices.
Affected employees
Affected employees must be trained:
- On the purpose and use of energy-control procedures.
- To be alert and responsive to notifications about lockout/tagout activities in their areas,
- To stay clear of machinery and equipment when notified that lockout/tagout devices are going to be applied, and
- To position themselves a safe distance away when notified that lockout/ tagout devices have been removed.
Other employees
Other employees must be trained.
All employees working in areas where energy-control procedures may be used must be instructed about those procedures and must understand that they are prohibited from tampering with lockout/tagout devices and from restarting or reenergizing locked or tagged out machinery and equipment.
Employees not authorized to operate machinery must always stay clear of machinery and equipment when it is locked out for repairs. For instance, administrative employees delivering messages to employees in the work area must be able to identify and avoid contacting lockout devices, even if another employee asks for assistance.
This training does not have to be drawn out. Training is sufficient so long as it covers what lockout/tagout devices look like and that only trained, authorized employees can handle them.
Training for tagout programs
If a tagout program is used instead of a lockout program, further training is required for employees. Tagout training must ensure that all employees understand the limitations of tags: tags are warning devices that do not provide the same level of protection as lockout devices, which physically restrain the position of energy-isolation devices. Employees using tagout devices must be trained to understand that tagout devices might evoke a false sense of security.
As with lockout devices, a tagout device may only be removed by the authorized employee who attached it. Further, tagout devices should never be bypassed, ignored, or otherwise defeated, and must always be positioned so that their warnings against the hazards of energization, such as “Do Not Start,” are clearly visible and easily legible.
Retraining
The employer must retrain all authorized and affected employees whenever there is:
- A change in their job assignments;
- A change in machines, equipment, or processes that present a new hazard; or
- A change in the energy-control procedures.
Additional retraining is required whenever an inspection reveals or an employer reasonably suspect that an employee fails to understand or comply with the steps of an energy-control procedure.
For example, if an inspection reveals that an employee uses a lock other than the employee’s personal lockout device, that employee must be retrained. The retraining, along with the initial training, must establish employee proficiency and introduce new or revised control methods and procedures, as necessary.
Certification of training
The employer is required to certify that each trained employee has the knowledge, skills, and understanding to work safely. The certification must contain each employee’s name and the training date. Authorized employees and affected employees must be retrained whenever they have a change in job assignments or whenever a change in equipment, process, or energy-control procedures could expose them to a new hazard. Inspections that reveal inadequacies also trigger retraining.
The employer is required to certify that employee training has been accomplished and is being kept up to date. This certification must include the employee’s name and the dates of the training. Certifications must be updated after any refresher training.
What are the requirements for periodic inspections?
- Employers must conduct inspections of employees following energy-control procedures at least annually.
To ensure that employees perform the steps of each energy-control procedures correctly, inspections of authorized employees following each of an employer’s energy-control procedures must be conducted at least annually. Each of these periodic inspections is to be administered by an authorized employee other than the employee(s) using the energy-control procedure being inspected.
The periodic inspection is oriented around identifying deviations from procedure so they can be corrected. During an inspection, the inspector must observe how employees implement the steps of the procedure and talk with them to determine that all requirements are understood and followed. After the inspection, the inspector must prepare a certification statement that specifies:
- The machine or equipment inspected,
- The date of inspection,
- The names of employees included in the inspection, and
- The name of the inspector.
The format and recordkeeping method for documenting these certifications is up to the employer. The format for the inspections themselves is also reasonably flexible. So long as they meet the requirements listed here, periodic inspections may be accomplished through random audits, plant safety tours, or planned visual observations.
If the inspector identifies any deviations or inadequacies, employers must ensure that appropriate corrective action is taken, including retraining or disciplining any employees who failed to follow procedures.
- For any procedure using lockout devices, an inspector will speak with each authorized employee implementing it about that employee’s responsibilities under the procedure.
- For any procedure using tagout devices, an inspector will speak with each authorized employee and each affected employee both about that employees’ responsibilities under the procedure and about the limitations of tagout devices.
The periodic inspection must include a review of the responsibilities of each authorized employee implementing the lockout procedure. Group meetings between the inspector and authorized employees would constitute compliance with this requirement. When a tagout system is used, each affected employee is to be included in the review as well.
Two qualifications
Procedures used less often than once a year are exempt from the once-yearly requirement, and only need to be inspected when used.
For inspection purposes, the Occupational Safety and Health Administration (OSHA) allows employers to group lockout/tagout procedures for similar machines and conduct one inspection for the group. This approach is acceptable so long as the inspection sampling reasonably reflects plant servicing and maintenance operations and hazardous energy-control practices for the procedures being inspected.
The machines or equipment in the group must have the same or similar types of control measures.
For purposes of procedure grouping, machines and equipment may be grouped together as one procedure if they all are listed or identified in the scope of the energy-control procedure and if they all have the same or similar:
- Procedural steps for shutting down, isolating, blocking, securing, and dissipating stored energy in machines or equipment;
- Procedural steps for the placement, removal, and transfer of the lockout or tagout devices and the responsibility for them; and
- Requirements for testing a machine or equipment to verify that lockout or tagout devices and other control measures are effective.
For example, a single procedure intended to cover a group of machines and that part of the energy-control procedure requires using a start/stop button for both shutdown and energy-isolation verification. However, one of the machines does not have a start/stop button because it is wired directly to an electronic on-demand signal. In this scenario, the single procedure will not provide adequate instructions for the machine without a start/stop button because the single procedure will not provide sufficient employee guidance on how to effectively shut down the machine and verify energy isolation. The energy-control procedure for this machine may not be included in the group.
Employers who develop specific energy-control procedures for individual machines and pieces of equipment may still to group similar procedures for inspections if the procedures meet these criteria.
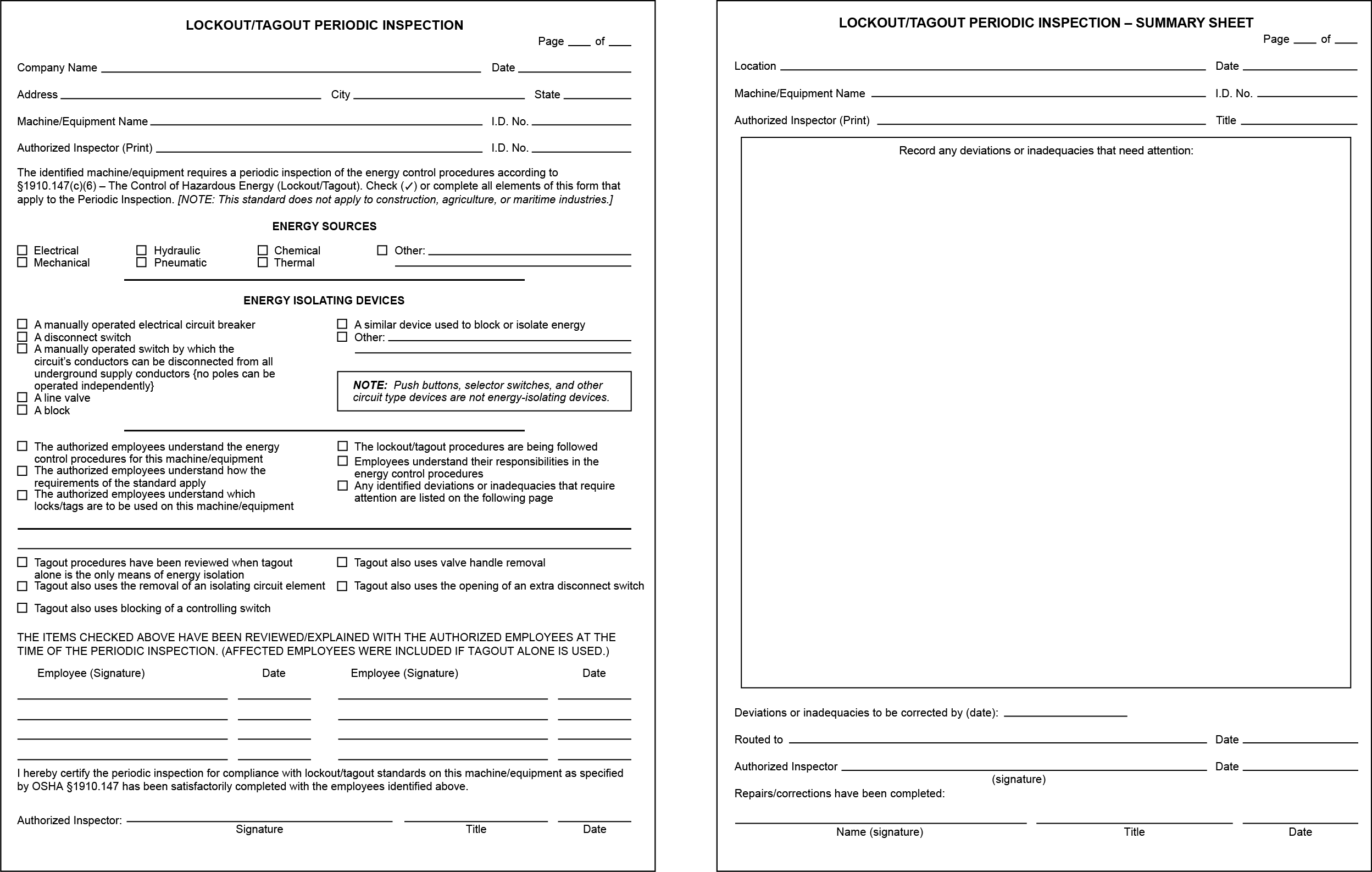
Working on energized equipment
It may be necessary to energize equipment to perform tests or reposition parts during servicing. The procedures for the testing or positioning of machines, equipment, or components in situations where lockout/tagout devices must be temporarily removed must follow this specific sequence:
- Clear the machine of tools and materials and remove all employees in the danger area.
- Have the authorized employee remove the lockout/tagout devices.
- Energize the equipment for the test.
- Test the equipment.
- De-energize the equipment after testing and reapply the lockout/tagout devices.
OSHA allows the temporary removal of lockout or tagout devices and the re-energization of the machine or equipment ONLY during the limited time necessary for the testing or positioning of machines, equipment, or components. Note that OSHA does not specifically require the reinstallation of machine guards during these procedures, but it is very important for employees to be safely positioned while the machine or equipment is energized. After the completion of the temporary re-energization, the authorized employees shall again de-energize the equipment and resume lockout/tagout procedures.
Group lockout
When more than one authorized employee services or maintains a machine, the group must use an energy-control procedure that protects each employee to the equivalent extent of a personal lockout or tagout device. Each authorized employee must affix a personal lockout or tagout device to a group lockout device, group lockbox, or comparable mechanism upon beginning work and must remove that personal device upon stopping. working on the machine or equipment being serviced or maintained.”
For example, if a single lockout device or set of lockbox devices (often referred to as “operations locks”) are used to isolate the machine or equipment from its energy sources, all authorized employees must be able to use their personal lockout or tagout devices so that no single employee can remove the group device while other employees are still servicing or maintaining the machine or equipment. This can be accomplished using a lockbox or other similar appliance.
Once the machine or equipment is locked out, the keys to the operations locks that were applied to the machine’s energy-isolating devices are placed into the lockbox. Then all authorized employees place their lockout or tagout devices on the box. When employees complete their individual portions of the work, they remove their individual lockout or tagout devices from the lockbox. Once all personal lockout or tagout devices have been removed, the keys for the operations locks can be used to remove the locks from the machine. This method provides individual protection for all employees working under the protection of a particular lockout or tagout device.
However group lockout is performed, the employer needs to ensure that employees are protected. Further, the employer should note that when more than one craft is involved in the group lockout, the different craft personnel must coordinate work to ensure continuity of protection.
Shift changes
The continuity of lockout or tagout protection during shift changes requires that a procedure for orderly transferring lockout or tagout devices between outgoing and incoming employees be included in the written energy-control procedures. A multiple-lock hasp may be used so incoming employees can apply their locks before outgoing employees remove their locks.
Following a shift change and before starting work, each group of incoming authorized employees must reverify that a locked or tagged out machine remains isolated and de-energized.
In situations where outgoing employees remove lockout or tagout devices before the incoming employees arrive, such as a change from second-shift to first-shift employees, this procedure could allow for outgoing employees to apply a tagout device to indicate that the lock had been removed but the machine or equipment had not been reenergized. Any incoming employee would verify that the system was still de-energized, would remove the interim tag, and would replace it with a personal lockout device. This would ensure that continuous protection is maintained from one shift to another.
Contractors
- The host employer has specific responsibilities for contractors that come on-site.
Host employers must assess contractors’ safety policies to ensure that the contractors’ employees are properly trained and that contractors have the appropriate written programs in place.
Before the contractor starts work, the host employer and the contractor employer are required to inform each other of their respective lockout/tagout procedures and the hazards involved in the task at hand. The host employer then must inform employees about the contractor relationship and how to safely interact with the contractor’s employees. The contractor must also communicate this information with the contractor’s employees.
Both employers must comply with the minimum standards. If the host employer takes a direct supervisory role over the contract employees (telling the contract employees what to do when they are on-site), then the host employer becomes responsible for training the contract employees. Typically, temporary employees who are hired through an agency would fall into this category. Supervising host employers could be cited when an on-site contractor does not comply with the Occupational Safety and Health Administration standards.
What are the requirements of the lockout/tagout standard? (Construction)
A lockout/tagout regulation for construction, comparable to OSHA’s general industry lockout/tagout rule, does not exist. Although the specific rules are limited, OSHA expects you to always protect your employees from situations that can cause injury or illness. In circumstances where there is not a specific construction regulation, OSHA’s General Duty Clause, Section 5(a)(1) of the OSH Act, would apply. The limited construction rules apply especially to electrical and mechanical situations.
Electrical controls, circuits, and equipment
When it is necessary to perform maintenance or servicing on machines or equipment, unexpected activation, reenergization, or release of stored energy is a real possibility.
Failure to adequately control energy accounts for many serious accidents in construction. Lockout/tagout procedures help safeguard employees from the unexpected start-up of machinery or equipment or release of hazardous energy while performing servicing or maintenance tasks.
Work should not be allowed on electrical circuits:
- Unless an effective lockout/tagout program is implemented.
- Which are not positively deenergized or tagged out.
The construction rules mention electrical lockout/tagout briefly and in only one place, 1926.417. However, this one place has specific rules to apply to lockout/tagout procedures for electrical equipment. Employers must:
- Tag all controls that are to be deactivated during the course of work on energized or deenergized equipment or circuits.
- Render equipment or circuits that are deenergized inoperative and attach tags at all points where such equipment or circuits can be energized.
- Place tags to plainly identify the equipment or circuits being worked on.
Although the above rules use tagout procedures, OSHA says that lockout is more effective for de-energizing equipment. It should always be the preferred method.
Mechanical equipment
Servicing and/or maintenance of equipment is an important aspect of keeping assets protected. It can also be a source of tragedy if not approached properly. This is why companies performing construction activities need proper lockout/tagout procedures.
Sometimes employees are required to place parts of their bodies into areas on machines or equipment where work is actually performed. Lockout/tagout procedures can prevent accidental exposures from electrical, mechanical, pneumatic, hydraulic, chemical, and thermal energy sources.
The construction rules actually mention mechanical lockout/tagout in only one place, and that is for mechanical concrete and masonry equipment (1926.703(j)). However, this one place has specific rules to apply to lockout/tagout procedures for mechanical equipment. Employers must ensure:
- No employee is permitted to perform maintenance or repair activity on equipment (such as compressors, mixers, screens, or pumps used for concrete and masonry construction activities) where the inadvertent operation of the equipment could occur and cause injury, unless all potential hazardous energy sources have been locked out and tagged.
- Tags read “Do Not Start” or similar language to indicate that the equipment is not to be operated.
In order to lockout and tag equipment, and ensure the safety of your employee performing maintenance or repairs, you need to have an effective program or procedure.
What is lockout/tagout?
Failing to perform lockout/tagout
Employees can be seriously or fatally injured if machinery they service or maintain unexpectedly energizes, starts up, or releases stored energy. OSHA’s standard on the Control of Hazardous Energy (Lockout/Tagout), found in 1910.147, spells out the steps employers must take to prevent accidents associated with hazardous energy. The standard addresses practices and procedures necessary to disable machinery and prevent the release of potentially hazardous energy while maintenance or servicing activities are performed.
Two other OSHA standards also contain energy control provisions: 1910.269 and 1910.333. In addition, some standards relating to specific types of machinery contain deenergization requirements such as 1910.179(l)(2)(i)(c) (requiring the switches to be “open and locked in the open position” before performing preventive maintenance on overhead and gantry cranes). The provisions of 1910.147 apply in conjunction with these machine-specific standards to assure that employees will be adequately protected against hazardous energy.
Application of the OSHA standard
If your employees service or maintain machines where the unexpected startup, energization, or the release of stored energy could cause injury, the standard can meet your lockout/tagout requirements. The standard applies to all sources of energy, including, but not limited to: mechanical, electrical, hydraulic, pneumatic, chemical, and thermal energy.
The standard does not cover electrical hazards from work on, near, or with conductors or equipment in electric utilization (premise wiring) installations, which are outlined by Subpart S of the general industry regulations. The specific lockout and tagout provisions for electrical shock and burn hazards are found at 1910.333. Controlling hazardous energy in installations for the exclusive purpose of power generation, transmission, and distribution, including related equipment for communication or metering, is covered by 1910.269.
The standard also does not cover the agriculture, maritime industries, or oil and gas well drilling and servicing. Other standards concerning the control of hazardous energy, however, apply in many of these industries/situations.
Excluded service and maintenance activities
The standard does not apply to general industry service and maintenance activities in the following situations, when:
- Exposure to hazardous energy is controlled completely by unplugging the equipment from an electric outlet and where the employee doing the service or maintenance has exclusive control of the plug. This applies only if electricity is the only form of hazardous energy to which employees may be exposed. This exception encompasses many portable hand tools and some cord and plug connected machinery and equipment.
- An employee performs hot-tap operations on pressurized pipelines that distribute gas, steam, water, or petroleum products, for which the employer shows the following:
- Continuity of service is essential.
- Shutdown of the system is impractical.
- The employee follows documented procedures and uses special equipment that provides proven, effective employee protection.
- The employee is performing minor tool changes or other minor servicing activities that are routine, repetitive, and integral to production, and that occur during normal production operations. In these cases, employees must have effective, alternative protection.
Energy control procedures
Employers must develop, document, and use procedures to control potentially hazardous energy. The procedures explain what employees must know and do to control hazardous energy effectively when they service or maintain machinery. If this information is the same for the various machines used at a workplace, then a single energy-control procedure may suffice. For example, similar machines (those using the same type and magnitude of energy) that have the same or similar types of control measures can be covered by a single procedure. Employers must develop separate energy-control procedures if their workplaces have more variable conditions such as multiple energy sources, different power connections, or different control sequences that workers must follow to shut down various pieces of machinery.
The energy-control procedures must outline the scope, purpose, authorization, rules, and techniques that employees will use to control hazardous energy sources, as well as the means that will be used to enforce compliance. These procedures must provide employees at least the following information:
- A statement on how to use the procedures.
- Specific procedural steps to shut down, isolate, block, and secure machines.
- Specific steps designating the safe placement, removal, and transfer of lockout/tagout devices and identifying who has responsibility for the lockout/tagout devices.
- Specific requirements for testing machines to determine and verify the effectiveness of lockout devices, tagout devices, and other energy-control measures.
Preparation for service or maintenance
Before beginning service or maintenance, the following steps must be accomplished in sequence and according to the specific provisions of the employer’s energy-control procedure:
- Prepare for shutdown.
- Shut down the machine.
- Disconnect or isolate the machine from the energy source(s).
- Apply the lockout or tagout device(s) to the energy-isolating device(s)
- Release, restrain, or otherwise render safe all potential hazardous stored or residual energy. If a possibility exists for reaccumulation of hazardous energy, regularly verify during the service and maintenance that such energy has not reaccumulated to hazardous levels.
- Verify the isolation and deenergization of the machine.
The energy-control procedures must outline the scope, purpose, authorization, rules, and techniques that employees will use to control hazardous energy sources, as well as the means that will be used to enforce compliance. These procedures must provide employees at least the following information:
- A statement on how to use the procedures.
- Specific procedural steps to shut down, isolate, block, and secure machines.
- Specific steps designating the safe placement, removal, and transfer of lockout/tagout devices and identifying who has responsibility for the lockout/tagout devices.
- Specific requirements for testing machines to determine and verify the effectiveness of lockout devices, tagout devices, and other energy-control measures.
Removal of lockout/tagout devices
Employees who work on deenergized machinery may be seriously injured or killed if someone removes lockout/tagout devices and reenergizes machinery without their knowledge. Thus, it is extremely important that all employees respect lockout and tagout devices and that only the person(s) who applied these devices remove them.
Before removing lockout or tagout devices, the employees must take the following steps in accordance with the specific provisions of the employer’s energy-control procedure:
- Inspect machines or their components to assure that they are operationally intact and that nonessential items are removed from the area.
- Check to assure that everyone is positioned safely and away from machines.
After removing the lockout or tagout devices but before reenergizing the machine, the employer must assure that all employees who operate or work with the machine, as well as those in the area where service or maintenance is performed, know that the devices have been removed and that the machine is capable of being reenergized. (See Sections 6(e) and (f) of 1910.147 for specific requirements.) In the rare situation in which the employee who placed the lockout/tagout device is unable to remove that device, another person may remove it under the direction of the employer, provided that the employer strictly adheres to the specific procedures outlined in the standard. (see 1910.147(e)(3).)
Lockout
You must use a lockout program (or tagout program that provides a level of protection equal to that achieved through lockout) whenever your employees engage in service or maintenance operations on machines that are capable of being locked out and that expose them to hazardous energy from unexpected energization, startup, or release of stored energy.
The primary way to prevent the release of hazardous energy during service and maintenance activities is by using energy-isolating devices such as manually operated circuit breakers, disconnect switches, and line valves and safety blocks. Lockout requires use of a lock or other lockout device to hold the energy-isolating device in a safe position to prevent machinery from becoming reenergized. Lockout also requires employees to follow an established procedure to ensure that machinery will not be reenergized until the same employee who placed the lockout device on the energy-isolating device removes it.
Energy-isolating device for lockout
An energy-isolating device is considered “capable of being locked out” if it meets one of the following requirements:
- Is designed with a hasp or other part to which you can attach a lock such as a lockable electric disconnect switch.
- Has a locking mechanism built into it.
- Can be locked without dismantling, rebuilding, or replacing the energy-isolating device or permanently altering its energy-control capability, such as a lockable valve cover or circuit breaker blockout.
Tagout only
Sometimes it’s not possible to lock out the energy-isolating device associated with the machinery. In that case, you must securely fasten a tagout device as close as safely possible to the energy-isolating device in a position where it will be immediately obvious to anyone attempting to operate the device. You also must meet all of the tagout provisions of the standard. The tag alerts employees to the hazard of reenergization and states that employees may not operate the machinery to which it is attached until the tag is removed in accordance with an established procedure.
Other energy-isolation options
If it’s possible to lock out an energy-isolating device, employers must use lockout devices unless they develop, document, and use a tagout procedure that provides employees with a level of protection equal to that provided by a lockout device. In a tagout program, an employer can attain an equal level of protection by complying with all tagout-related provisions of the standard and using at least one added safety measure that prevents unexpected reenergization. Such measures might include removing an isolating circuit element, blocking a controlling switch, opening an extra disconnecting device, or removing a valve handle to minimize the possibility that machines might inadvertently be reenergized while employees perform service and maintenance activities.
Using tagout devices instead of lockout devices
When an energy-isolating device cannot be locked out, the employer must modify or replace the energy-isolating device to make it capable of being locked out or use a tagout system. Whenever employers significantly repair, renovate, or modify machinery or install new or replacement machinery, however, they must ensure that the energy-isolating devices for the machinery are capable of being locked out.
Tagout devices may be used on energy-isolating devices that are capable of being locked out if the employer develops and implements the tagout in a way that provides employees with a level of protection equal to that achieved through a lockout system.
When using a tagout system, the employer must comply with all tagout-related provisions of the standard and train employees in the limitations of tags, in addition to providing normal hazardous energy control training for all employees.
Limitations of tagout devices
A tagout device is a prominent warning that clearly states that the machinery being controlled must not be operated until the tag is removed in accordance with an established procedure. Tags are essentially warning devices and do not provide the physical restraint of a lock. Tags may evoke a false sense of security. For these reasons, OSHA considers lockout devices to be more secure and more effective than tagout devices in protecting employees from hazardous energy.
Requirements for lockout/tagout devices
Whether lockout or tagout devices are used, they must be the only devices the employer uses in conjunction with energy-isolating devices to control hazardous energy. The employer must provide these devices and they must be singularly identified and not used for other purposes. In addition, they must have the following characteristics:
- Durable enough to withstand workplace conditions. Tagout devices must not deteriorate or become illegible even when used with corrosive components such as acid or alkali chemicals or in wet environments.
- Standardized according to color, shape, or size. Tagout devices also must be standardized according to print and format. Tags must be legible and understandable by all employees. They must warn employees about the hazards if the machine is energized, and offer employees clear instruction such as: “Do Not Start,” “Do Not Open,” “Do Not Close,” “Do Not Energize,” or “Do Not Operate.”
- Substantial enough to minimize the likelihood of premature or accidental removal. Employees should be able to remove locks only by using excessive force with special tools such as bolt cutters or other metal-cutting tools. Tag attachments must be non-reusable, self-locking, and non-releasable, with a minimum unlocking strength of 50 pounds. Tags must be attachable by hand, and the device for attaching the tag should be a one-piece nylon cable tie or its equivalent so it can withstand all environments and conditions.
- Labeled to identify the specific employees authorized to apply and remove them.
Testing machines, equipment, or components
OSHA allows the temporary removal of lockout or tagout devices and the reenergization of the machine only in limited situations for particular tasks that require energization — for example, when power is needed to test or position machines, equipment, or components. However, this temporary exception applies only for the limited time required to perform the particular task requiring energization. Employers must provide effective protection from hazardous energy when employees perform these operations.
The following steps must be performed in sequence before reenergization:
- Clear tools and materials from machines.
- Clear employees from the area around the machines.
- Remove the lockout or tagout devices as specified in the standard.
- Energize the machine and proceed with testing or positioning.
- Deenergize all systems, isolate the machine from the energy source, and reapply energy-control measures if additional service or maintenance is required.
The employer must develop, document, and use energy-control procedures that establish a sequence of actions to follow whenever reenergization is required as a part of a service or maintenance activity, since employees may be exposed to significant risks during these transition periods.
Employee training and retraining
Training must ensure that employees understand the purpose, function, and restrictions of the energy-control program. Employers must provide training specific to the needs of “authorized,” “affected,” and “other” employees.
“Authorized” employees are those responsible for implementing the energy-control procedures or performing the service or maintenance activities. They need the knowledge and skills necessary for the safe application, use, and removal of energy-isolating devices. They also need training in the following:
- Hazardous energy source recognition.
- The type and magnitude of the hazardous energy sources in the workplace.
- Energy-control procedures, including the methods and means to isolate and control those energy sources.
“Affected” employees (usually machine operators or users) are employees who operate the relevant machinery or whose jobs require them to be in the area where service or maintenance is performed. These employees do not service or maintain machinery or perform lockout/tagout activities. Affected employees must receive training in the purpose and use of energy-control procedures. They also need to be able to do the following:
- Recognize when the energy-control procedure is being used.
- Understand the purpose of the procedure.
- Understand the importance of not tampering with lockout or tagout devices and not starting or using equipment that has been locked or tagged out.
All other employees whose work operations are or may be in an area where energy-control procedures are used must receive instruction regarding the energy-control procedure and the prohibition against removing a lockout or tagout device and attempting to restart, reenergize, or operate the machinery.
In addition, if tagout devices are used, all employees must receive training regarding the limitations of tags. (1910.147(c)(7)(ii).) The employer must provide initial training before starting service and maintenance activities and must provide retraining as necessary. In addition, the employer must certify that the training has been given to all employees covered by the standard. The certification must contain each employee’s name and dates of training.
Employers must provide retraining for all authorized and affected employees whenever there is a change in the following:
- Job assignments.
- Machinery or processes that present a new hazard.
- Energy-control procedures.
Retraining also is necessary whenever a periodic inspection reveals, or an employer has reason to believe, that shortcomings exist in an employee’s knowledge or use of the energy-control procedure.
Group lockout/tagout
When a crew, department, or other group performs service or maintenance, they must use a procedure that provides all employees a level of protection equal to that provided by a personal lockout or tagout device. Each employee in the group must have control over the sources of hazardous energy while involved in service and maintenance activities covered by the standard. Personal control is achieved when each authorized employee affixes a personal lockout/tagout device to a group lockout mechanism instead of relying on a supervisor or other person to provide protection against hazardous energy.
Detailed requirements of individual responsibilities are provided in 1910.147(f)(3)(ii)(A) through (D). Appendix C of OSHA Directive STD 1-7.3, 29 CFR 1910.147, the Control of Hazardous Energy (Lockout/Tagout)-Inspection Procedures and Interpretive Guidance, (September 11, 1990), provides additional guidance.
Shift changes during machine service or maintenance
Employers must make sure that there is a continuity of lockout or tagout protection. This includes the orderly transfer of lockout or tagout device protection between outgoing and incoming shifts to control hazardous energy. When lockout or tagout devices remain on energy-isolation devices from a previous shift, the incoming shift members must verify for themselves that the machinery is effectively isolated and deenergized.
Review of lockout/tagout procedures
Employees are required to review their procedures at least once a year to ensure that they provide adequate worker protection. As part of the review, employers must correct any deviations and inadequacies identified in the energy-control procedure or its application.
The yearly review is intended to assure that employees are familiar with their responsibilities under the procedure and continue to implement energy-control procedures properly. The inspector, who must be an authorized person not involved in using the particular control procedure being inspected, must be able to determine the following:
- Employees are following steps in the energy-control procedure.
- Employees involved know their responsibilities under the procedure.
- The procedure is adequate to provide the necessary protection, and what changes, if any, are needed.
For a lockout procedure, the periodic inspection must include a review of each authorized employee’s responsibilities under the energy-control procedure being inspected. Where tagout is used, the inspector’s review also extends to affected employees because of the increased importance of their role in avoiding accidental or inadvertent activation of the machinery. In addition, the employer must certify that the designated inspectors perform periodic inspections. The certification must specify the following:
- Machine or equipment on which the energy-control procedure was used.
- Date of the inspection.
- Names of employees included in the inspection.
- Name of the person who performed the inspection.
Electrical standard and lockout/tagout
According to 29 CFR 1910.333, the selection and use of work practices associated with electrical equipment, including service and maintenance, is important to be outlined.
The employer must use the electrical standard’s safety-related work practices to ensure employees are protected and trained to prevent electric shock and other injuries resulting from either direct or indirect electrical contacts.
When work is performed near or on equipment or circuits which are or may be energized, specific safety-related work practices must be implemented. The employer needs to note that conductors (wires or similar conductive materials) and parts of electric equipment that have been de-energized, but have not been locked or tagged out, are to be treated as if they are energized. While any employee is exposed to contact with parts of fixed electric equipment or circuits that have been de-energized, the circuits energizing the parts must be locked out.
Lockout/tagout procedures that comply with paragraphs (c) through (f) of 29 CFR 1910.147, will also be deemed to comply with the electrical standard’s lockout requirements, provided that the procedures address the electrical safety hazards including the procedures for de-energizing circuits. Interlocks for electric equipment may not be used as a substitute for lockout and tagging procedures. The employer must also document the requirements for qualified employees to release stored electric energy that might endanger personnel during the service or maintenance function.
Capacitors must be discharged and high capacitance elements must be short-circuited and grounded. Further, the employer must control or eliminate stored non-electrical energy in devices by blocking or relieving the energy. If a tag is used without a lock, the tag must be supplemented by at least one additional safety measure that provides a level of safety equivalent to that obtained using a lock. Additional safety measures include the removal of an isolating circuit element, blocking of a controlling switch, or opening of an extra disconnecting device.
The employer must verify the electrical part is de-energized. A qualified person must conduct tests and visual inspections, as necessary, to verify that all tools, electrical jumpers, shorts, grounds, and other such devices have been removed, so that the circuits and equipment can be safely energized prior to equipment start-up.
Employees exposed to the hazards associated with reenergizing the circuit or equipment must be warned to stay clear of circuits and equipment. If the employee must work on exposed live parts, the employee must be a qualified person. The qualified person must be capable of working safely on energized circuits and be familiar with the proper use of special precautionary techniques, personal protective equipment, insulating and shielding materials, and insulated tools.
Electrical training
Employees working with electricity must have training that goes beyond that required under the lockout/tagout standard. These employees must be trained in and familiar with the safety-related work practices of the electrical standard, 29 CFR 1910.331-.335. Training requirements differ for “qualified” and “unqualified” electrical workers. This classification is specific to the task, and the same person may be considered “qualified” for some jobs and “unqualified” for others.
Generally, “qualified” employees are more directly exposed to electrical hazards — they may work on exposed electrical parts. “Qualified” employees must be trained on:
- How to avoid electrical hazards,
- How electrical equipment functions,
- The specific hazards of the job,
- How to distinguish between exposed “live” parts and other parts of the electrical equipment,
- How to determine nominal voltages, and
- The safe clearance distances corresponding to the voltages they are exposed to.
“Unqualified” employees may have only indirect exposure to electricity. They need basic training in the hazards associated with:
- Electric current,
- High voltages,
- Grounding,
- Arcing, and
- Lack of guarding.
These “unqualified” employees must also be trained in and familiar with any electrically related safety practices not specifically addressed by 1910.331 through 1910.335, but which are necessary for their safety.