InstituteLockout/TagoutAnalysisSafety & HealthIn Depth Sub Topics (Level 4)Lockout/TagoutGeneral Industry SafetyLockout/Tagout Written ProgramEnglishLockout/Tagout Authorized WorkersFocus AreaUSA
What are the steps for applying controls?
['Lockout/Tagout']
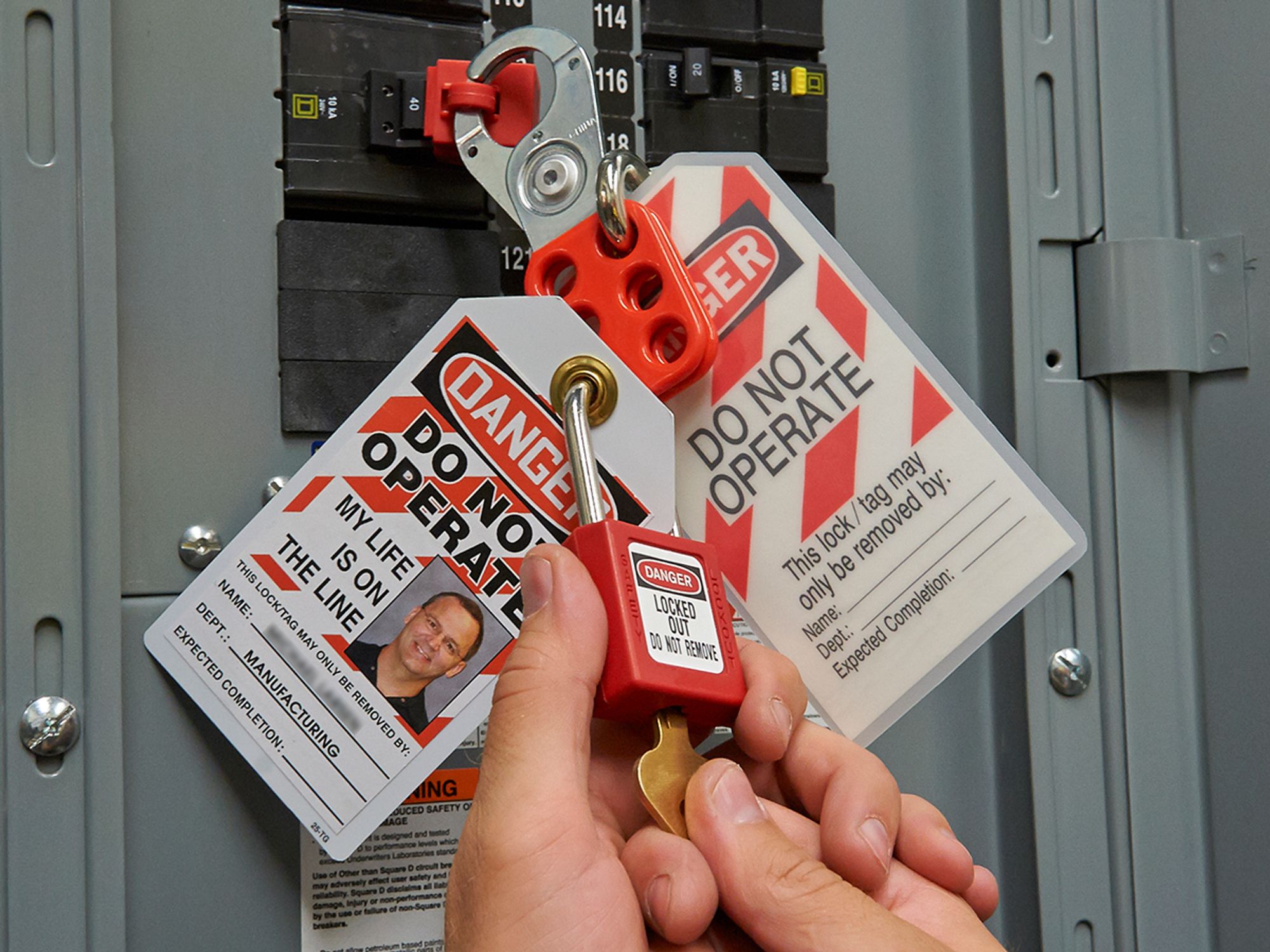
Workers must follow their employer’s energy control plan while applying LOTO controls to avoid exposure to hazardous energy.
- Preparation for shutdown
The first step in an energy-control procedure is ensuring two conditions are met before a machine or piece of equipment is shut down. First, employers must ensure that each authorized employee who will perform servicing or maintenance knows the following information:- The types and magnitude of the energy to be controlled,
- The hazards this energy poses, and
- The devices and methods used to control this energy.
- Shutdown
Once these conditions are satisfied, the machine or equipment must be turned off or shut down using the stop button or other normal stopping method.- This is the only step in an energy-control procedure that affected employees may perform as well as authorized employees. The limited involvement of affected employees serves to keep shutdown orderly and minimize additional hazards.
- Energy isolation
Once a machine or piece of equipment has been shut down, authorized employees must de-energize it by locating each energy-isolating device and setting each in the “safe” or “off” position.- Depending on the machine, operating energy-isolating devices may involve operating disconnect switches, closing valves, or other methods. Though different in structure, these all serve to physically separate or disconnect machines and equipment from their sources of energy.
- Because the number and layout of energy-isolating devices can be elaborate on complex machinery and equipment, an employer’s energy-control procedure needs to identify all energy-isolating devices for employees to locate.
- Application of lockout/tagout devices
Once all necessary energy-isolating devices are set to “safe” or “off,” authorized employees must apply to them the appropriate lockout devices (“locks”) or tagout devices (“tags”).- If the energy-isolating devices on a machine or piece of equipment can be locked out, then authorized employees must secure the appropriate locks to the energy-isolating devices so the latter are held in the “safe” or “off” position.
- If energy-isolating devices cannot be locked out or if a tagout program is used, authorized employees must secure tags as close as is safely possible to those energy-isolating devices so it is obvious that taking the latter out of the “safe” or “off” position is prohibited.
- Release of stored energy
After locks or tags are applied, authorized employee must relieve, disconnect, restrain, or render safe all potentially hazardous stored or residual energy in the machine or equipment.- Stored energy is potential energy that remains present in machines and equipment even after they are isolated from their energy sources. Each energy-control procedure must identify the types and sources of stored energy, such as capacitors, line pressure, and elevated parts, and explain what authorized employees must do to dissipate or strain it from these sources.
- If stored energy could reaccumulate in a machine or piece of equipment while employees perform servicing or maintenance service and maintain the machine or equipment, the employer must continually verify that the machine remains isolated to ensure no hazards arise. If hydraulic or pneumatic systems are present, bleed valves may be necessary to relieve built-up pressure.
- Verification of isolation
Finally, authorized employees must verify that energy isolation is complete and that the machinery or equipment is safe for servicing and maintenance.- Isolation can be verified by using test equipment, checking gauges, or by trying to restart the machinery or equipment.
- Authorized employees must always return all controls to the “off” or “stop” position following this verification step to ensure that no machine or piece of equipment starts automatically when power is restored. This is especially important for computerized machinery and equipment whose controls are programmed to remember and act on their last commands.