What are the steps for removing controls?
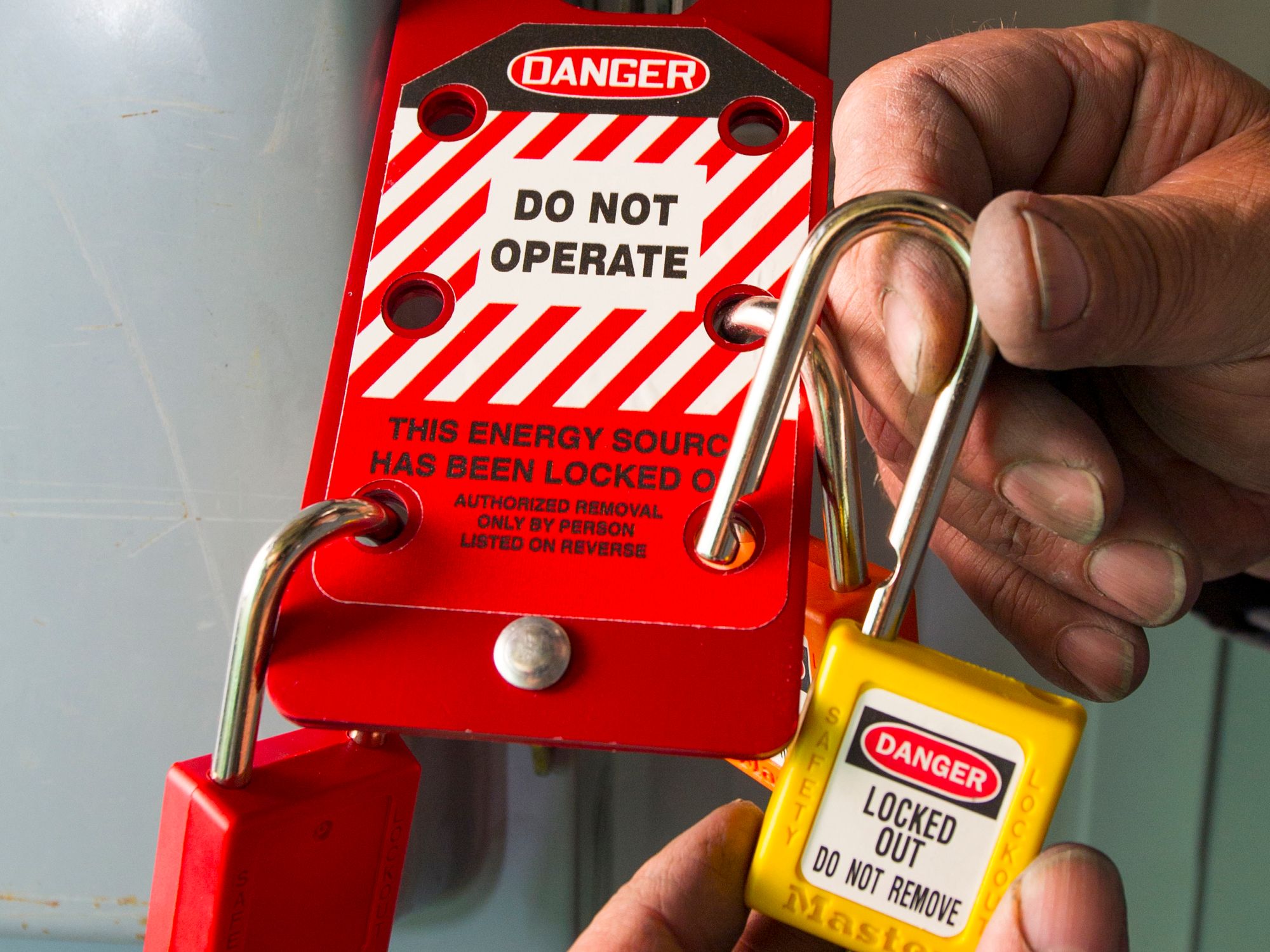
After servicing and maintenance is complete, authorized employees must follow the written procedural steps for reenergizing and starting up machinery and equipment.
- Inspection of system components
Authorized employees must first inspect a machine or piece of equipment to confirm that it has been returned to safe operating condition. Employees must check and ensure that:- All tools and other nonessential items have been removed,
- All safeguards removed during servicing or maintenance are reinstalled or replaced, and
- All controls at the control panel remain in the “off” or “stop” position.
- Checking for safe positioning
Once they have completed the system inspection and reinstalled all guards, authorized employees must ensure that all affected and other employees in the area are positioned at a safe distance away from the machine or equipment before it is reenergized.- Alarms or other warning devices may be necessary for large machinery that blocks the sightlines of authorized employees.
- Removal of lockout/tagout devices
When the safe positioning of employees in the area is confirmed, each lockout or tagout device must be removed from its energy-isolating device by the authorized employee who applied it. The identity of this employee must be indicated on the device itself.- Notification of removal After authorized employees have removed lockout or tagout devices and before machinery or equipment is started up, the authorized employees or the employer must notify all affected employees that lockout or tagout devices have been removed.
- These notifications ensure that employees are safely positioned away from machines and equipment before they are reenergized.
- Restoration of energy
When these notifications are complete, an authorized employee can start the machine or equipment to confirm that it is functioning properly and is safe for normal operations to resume.
NOTE: Removal of a lockout device by others
Only the authorized employee who applies a lockout or tagout device may remove it. However, when this employee is unavailable, the employee’s device may be removed by another employee only if specific procedures documented in the employer’s lockout/tagout program are followed. The requirements of this specific procedure are that:
- The employer demonstrates that this specific procedure provides equivalent safety to that provided by the removal of the lockout or tagout device by the authorized employee who applied it,
- The employer verifies that the authorized employee who applied the device is absent from the facility,
- The employer makes all reasonable efforts to contact this authorized employee to report that the employee’s lockout/tagout device has been removed, and
- The authorized employee is informed that the device was removed before that employee resumes work at the facility.
The employer should not remove a lock without speaking to the employee who applied it. Whenever someone other than the employee who applied a lock or tag removes it, the machine or piece of equipment must be fully inspected by a qualified person to ensure that servicing or maintenance is complete and that it is safe to operate. If the authorized employee left the lock or tag in place out of negligence, the employer should strongly consider retraining or disciplinary action.
While bolt cutters or other device-destructive methods are permissible means to remove a lockout device, an employer’s specific procedure may use non-destructive methods if the employer demonstrates that it provides a degree of safety that is equivalent to the removal of the device by the authorized employee who first affixed it. A master key procedure, under which an employer has access to a key capable of opening multiple lockout devices, complies with the standard only if it includes a reliable method to ensure that access to the master key is carefully controlled by the employer. Safety is ensured through effective procedures that respect the sanctity of another employee’s lockout or tagout device.