InstituteLockout/TagoutAnalysisSafety & HealthLockout/TagoutGeneral Industry SafetyLockout/Tagout Written ProgramLockout/Tagout Affected WorkersLockout/Tagout Periodic EvaluationEnglishLockout/Tagout Authorized WorkersFocus AreaCompliance and Exceptions (Level 2)USA
What are the requirements of the lockout/tagout standard? (General industry)
['Lockout/Tagout']
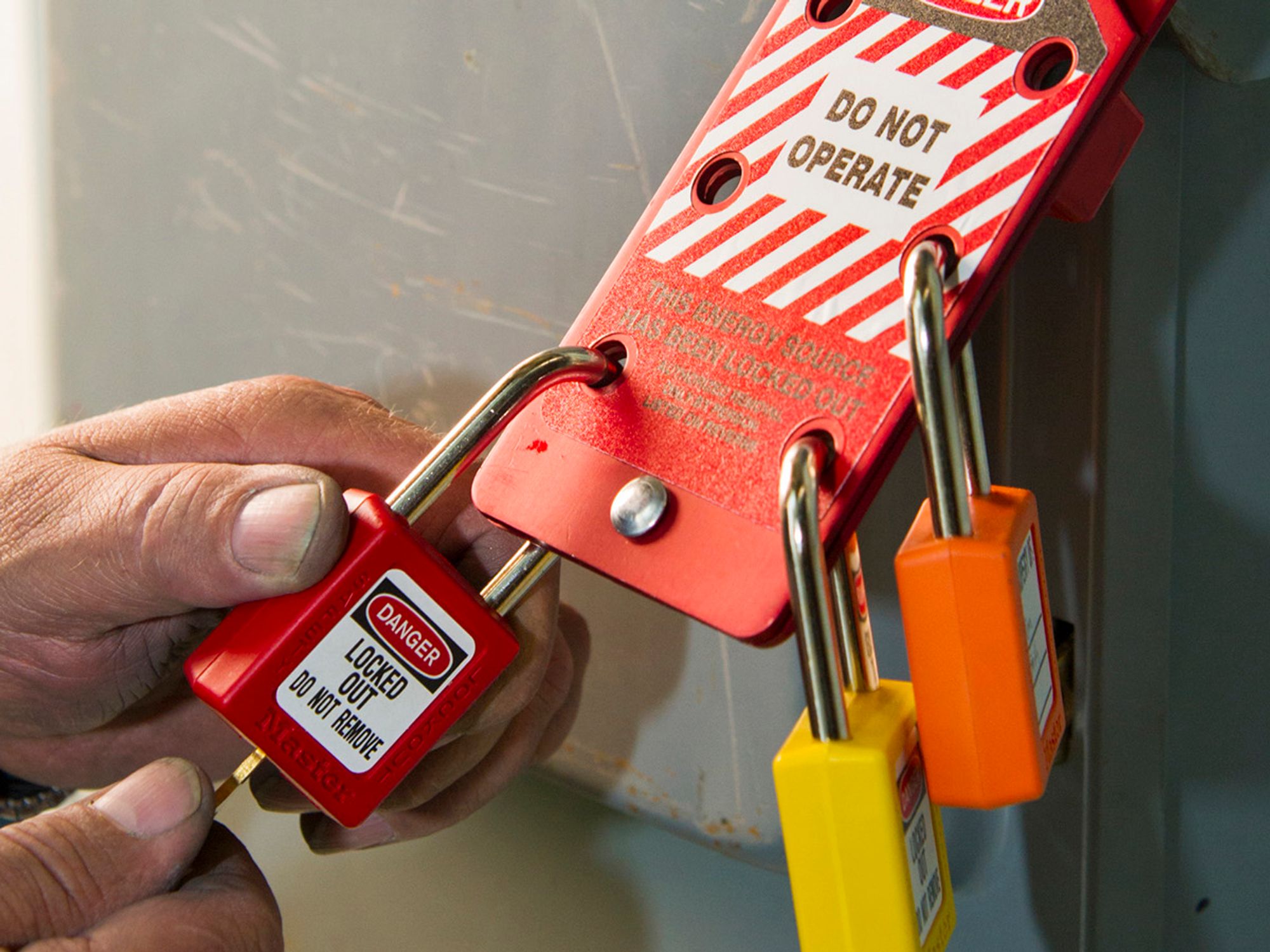
- Each employer is required to develop an energy-control program consisting of energy-control procedures, employee training, and periodic inspections.
The Occupational Safety and Health Administration’s (OSHA’s) lockout/tagout standard lays out the minimum requirements for employers whose employees are exposed to hazardous energy during the servicing and maintenance of machinery and equipment. Each employer covered by the standard must develop, implement, and enforce an energy-control program to protect employees against injury from the unexpected release of hazardous energy. Among the most critical requirements of this program for employers are to:
- Develop, implement, and enforce documented energy-control procedures;
- Use lockout devices for all energy-isolating devices that can be locked out, unless an employer can demonstrate that a tagout program will provide a level of safety equivalent to the protection provided by a lockout program;
- Ensure that all new and overhauled machinery and equipment can be locked out;
- Develop, implement, and enforce an effective tagout program if machines or equipment cannot be locked out;
- Use only lockout/tagout devices authorized for the specific machines and equipment to which they are applied;
- Ensure that lockout/tagout devices are standardized, durable, and substantial;
- Ensure that lockout/tagout devices identify their individual users;
- Permit only the employee who applied a lockout/tagout device to remove it;
- Provide effective training for all authorized, affected, and other employees covered by the standard, and document certification of this training;
- Inspect energy-control procedures at least annually and document certification of these inspections; and
- Comply with the additional energy-control provisions when machines or equipment must be tested or repositioned during servicing and maintenance, when outside contractors work at the site, when lockout is performed by a group of employees, and when shifts or personnel change.