InstituteBloodborne PathogensSafety & HealthGeneral Industry SafetyUSABloodborne PathogensEnglishAnalysisFocus AreaIn Depth (Level 3)
Requirements for both research laboratories and production facilities
['Bloodborne Pathogens']
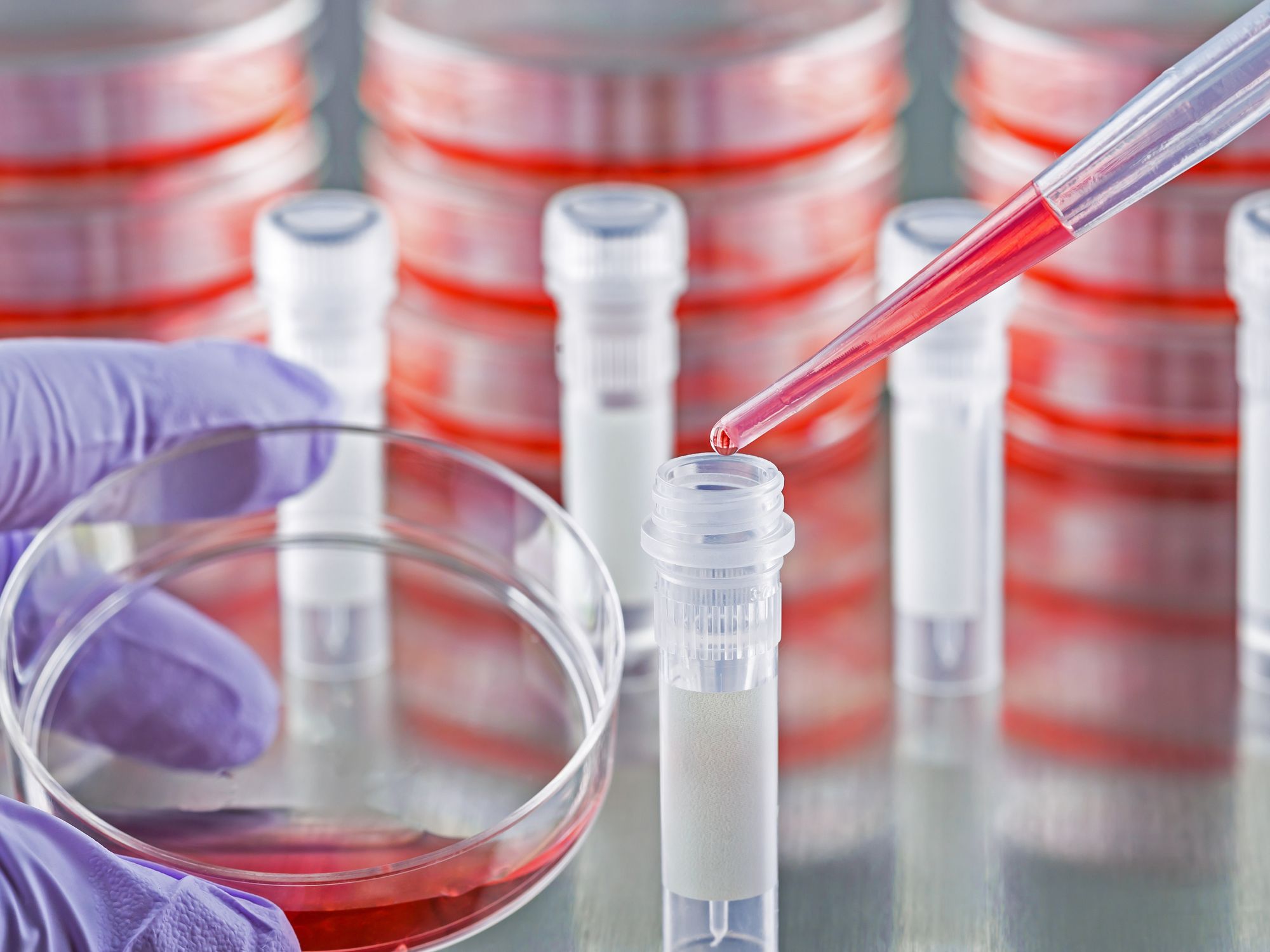
- Under the Bloodborne Pathogens Standard, additional requirements apply to HIV and HBV research labs and production facilities.
- These requirements concern elements of these workplaces that include decontamination, access, containment equipment, and ventilation.
Paragraph 1910.1030(e) applies to research laboratories and production facilities engaged in the culture, production, concentration, experimentation, and manipulation of human immunodeficiency virus (HIV) and hepatitis B virus (HBV). They are in addition to the other requirements of the standard. They don’t apply to clinical or diagnostic laboratories engaged solely in the analysis of blood, tissues, or organs.
The following practices are required of both research laboratories and production facilities.
Standard microbiological practices
- All regulated waste must either be incinerated or decontaminated by a method such as autoclaving that’s known to effectively destroy bloodborne pathogens.
Special practices
- Laboratory doors shall be kept closed when work involving HIV or HBV is in progress.
- Contaminated materials that are to be decontaminated at a site away from the work area shall be placed in a durable, leakproof, labeled or color-coded container that is closed before being removed from the work area.
- Access to the work area shall be limited to authorized people.
- Written policies and procedures shall be established under which only people who have been advised of the potential biohazard, meet entry requirements, and comply with all entry and exit procedures are allowed to enter the work areas and animal rooms.
- When other potentially infectious materials (OPIM) or infected animals are present in the work area or containment module, a hazard warning sign complying with 1910.1030(g)(1)(ii) and incorporating the universal biohazard symbol shall be posted on all access doors.
- All activities involving OPIM shall be conducted in biological safety cabinets or other physical containment devices within the containment module, never on the open bench.
- Laboratory coats, gowns, smocks, uniforms, or other appropriate protective clothing shall be used in the work area and animal rooms. Protective clothing shall not be worn outside the work area and shall be decontaminated before being laundered.
- Special care shall be taken to avoid skin contact with OPIM. Gloves shall be worn when handling infected animals and for unavoidable hand contact with OPIM.
- Before disposal, all waste from work areas and animal rooms shall either be incinerated or decontaminated by a method such as autoclaving known to effectively destroy bloodborne pathogens.
- Vacuum lines shall be protected with liquid disinfectant traps and high-efficiency particulate air (HEPA) filters or filters of equivalent or superior efficiency.
- Traps and filters must be checked routinely and maintained or replaced as necessary.
- In humid atmospheres, HEPA filters may be ineffective, so an alternative may be preferable.
- Hypodermic needles and syringes shall be used only for parenteral (under the skin) injection and aspiration of fluids from laboratory animals and diaphragm bottles.
- Only needle-locking syringes or disposable syringe-needle units (in which the needle is integral to the syringe) shall be used with OPIM.
- Extreme caution shall be used when handling needles and syringes.
- A needle shall not be bent, sheared, replaced in the sheath or guard, or removed from the syringe following use.
- The used needle and syringe shall be promptly placed in a puncture-resistant container and autoclaved or decontaminated before reuse or disposal.
- All spills shall be immediately contained and cleaned up by appropriate professional staff or others properly trained and equipped to work with potentially concentrated infectious materials.
- A spill or accident that results in an exposure incident shall be immediately reported to the laboratory director or other responsible person.
- A biosafety manual shall be prepared or adopted and periodically reviewed and updated at least annually or more often if necessary.
- Workers must be informed of potential hazards and required to read and follow instructions on practices and procedures.
- During review and update of the manual, any additional procedures shall be developed that are necessary to protect employees in situations unique to a research/production facility.
Containment equipment
- Certified biological safety cabinets (BSC) (Class I, II, or III) or other appropriate combinations of personal protection or physical containment devices shall be used for all activities that may involve exposure to OPIM droplets, splashes, spills, or aerosols.
- Examples of alternatives to BSC include special protective clothing, respirators, centrifuge safety cups, sealed centrifuge rotors, and containment caging for animals.
- BSC shall be certified when installed, whenever they are moved, and at least annually.
- A dated tag indicating who performed the certification should be affixed to the BSC.
- Alternatively, a certification report attesting to a minimum inward face velocity of at least 75 linear feet per minute and the integrity of the HEPA filters should be available to the compliance officer.
- This report must be dated and signed by the trained technician performing the measurements and integrity tests.
Additional training requirements for employees in HIV and HBV research laboratories and HIV and HBV production facilities are specified in 1910.1030(g)(2)(ix).