Provision, accessibility, and use
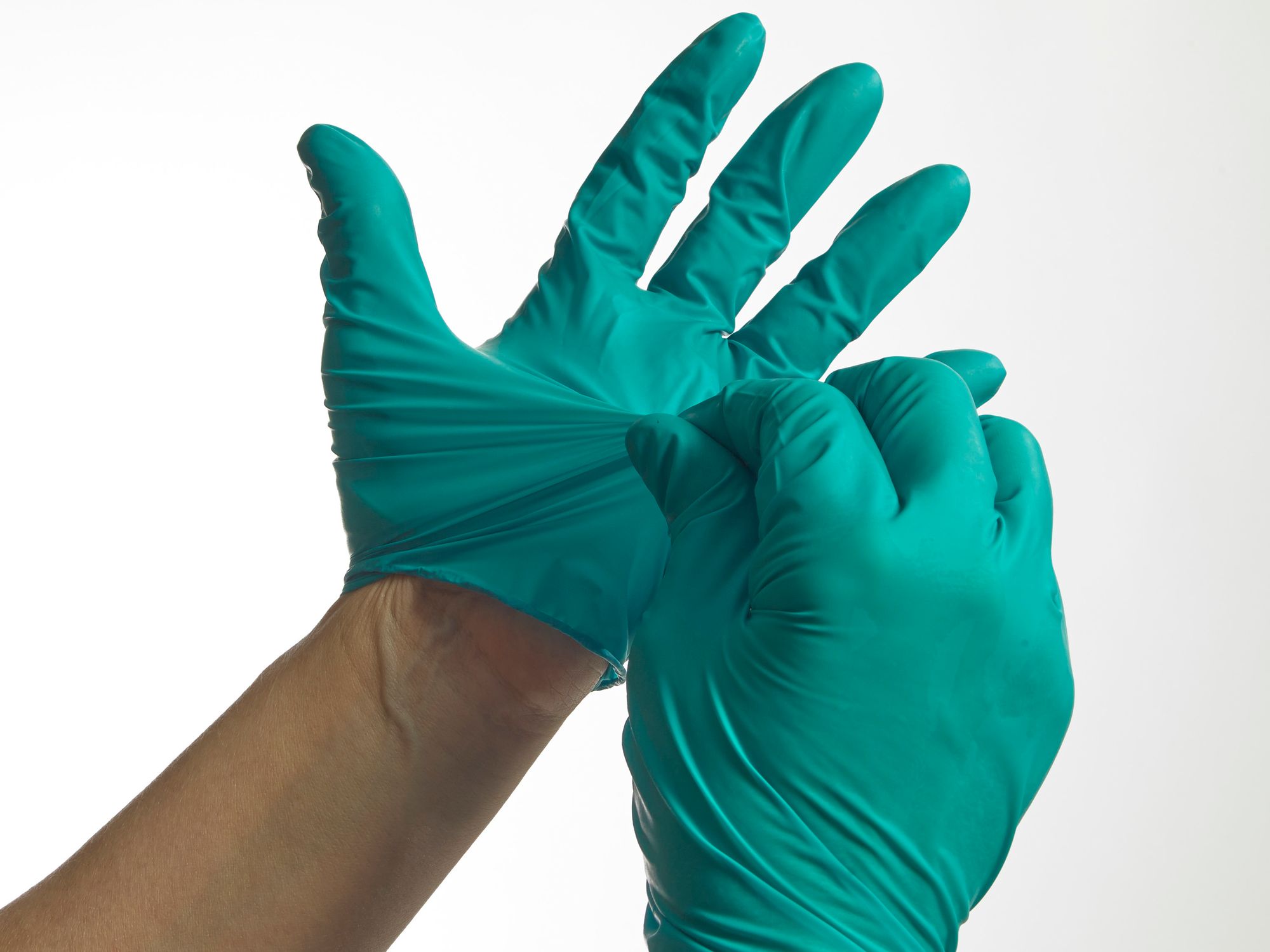
Personal protective equipment (PPE) is required if occupational exposure remains after engineering and work practice controls are in place, or if those controls are not feasible.
The employer must provide, at no cost to the employee, PPE that is appropriate to the employee’s level of risk. The employer must also train the employee in proper use of the PPE that’s available.
PPE includes but is not limited to the following:
- Gloves and shoe covers;
- Gowns, protective suits, and aprons;
- Laboratory coats and uniforms that are intended to protect the employee’s body from contamination;
- Face shields and masks;
- Safety glasses and goggles; and
- Mouthpieces, resuscitation bags, pocket masks, and other ventilation devices.
What is “appropriate”?
The type and amount of PPE must be chosen to protect against contact with blood or other potentially infectious materials (OPIM) based upon the type of exposure and amount of these substances that the employee can reasonably anticipate encountering during a task or procedure.
PPE is considered ‘‘appropriate’’ if it does not permit blood or OPIM to pass through or reach the employee’s work clothes, street clothes, undergarments, skin, eyes, mouth, or other mucous membranes under normal conditions. PPE with any breach, even as small as a pinhole in a glove, is not considered appropriate because blood or OPIM could reach the skin.
Appropriate PPE also must fit employees correctly. Ill-fitting PPE could cause tearing or inadvertently expose skin, or employees may simply refuse to wear it. Thus, employers must provide a variety of sizes so that all employees can wear PPE that fits their bodies.
Accessibility
Proper PPE in the appropriate sizes must be readily accessible at the worksite or be issued to employees. Employee training must include the location of the PPE and how to put it on.
Resuscitator devices must be readily available and accessible to employees who can reasonably be expected to perform resuscitation procedures. The same is true of emergency ventilation devices such as masks, mouthpieces, resuscitation bags, and shields/overlay barriers.
If an employee wants to choose, wear, and maintain a personal uniform or laboratory coat, that employee needs to wear additional employer-handled and employer-controlled PPE when performing tasks where it’s reasonable to anticipate exposure to blood or OPIM.
In the rare case that an employee has a good reason to decline wearing PPE (see “Special Circumstances” below), the employer still is responsible for ensuring that PPE is readily accessible at all times.
Proper use
Employees must receive training in proper use of the PPE. Inadequate training and improper use, including failure to follow the manufacturer’s instructions or accepted medical practice, will be cited.
Employees must remove any contaminated clothing before leaving a work area (such as to enter designated lunchrooms or break rooms). A work area is generally considered to be an area where work involving occupational exposure occurs or where the contamination of surfaces may occur.
Employees are not required to change PPE when traveling, for example, from one hospital laboratory area to another, as long as the connecting hallway is also considered to be a work area.
An example of a violation would be if an employee wearing contaminated gloves leaves a pathology laboratory to use a public telephone in a public hallway of the hospital. The surface of the phone would be likely to become contaminated, and it can be reasonably anticipated that another employee would use the phone without gloves and unwittingly pick up the contamination.