What training do employees need for lockout/tagout?
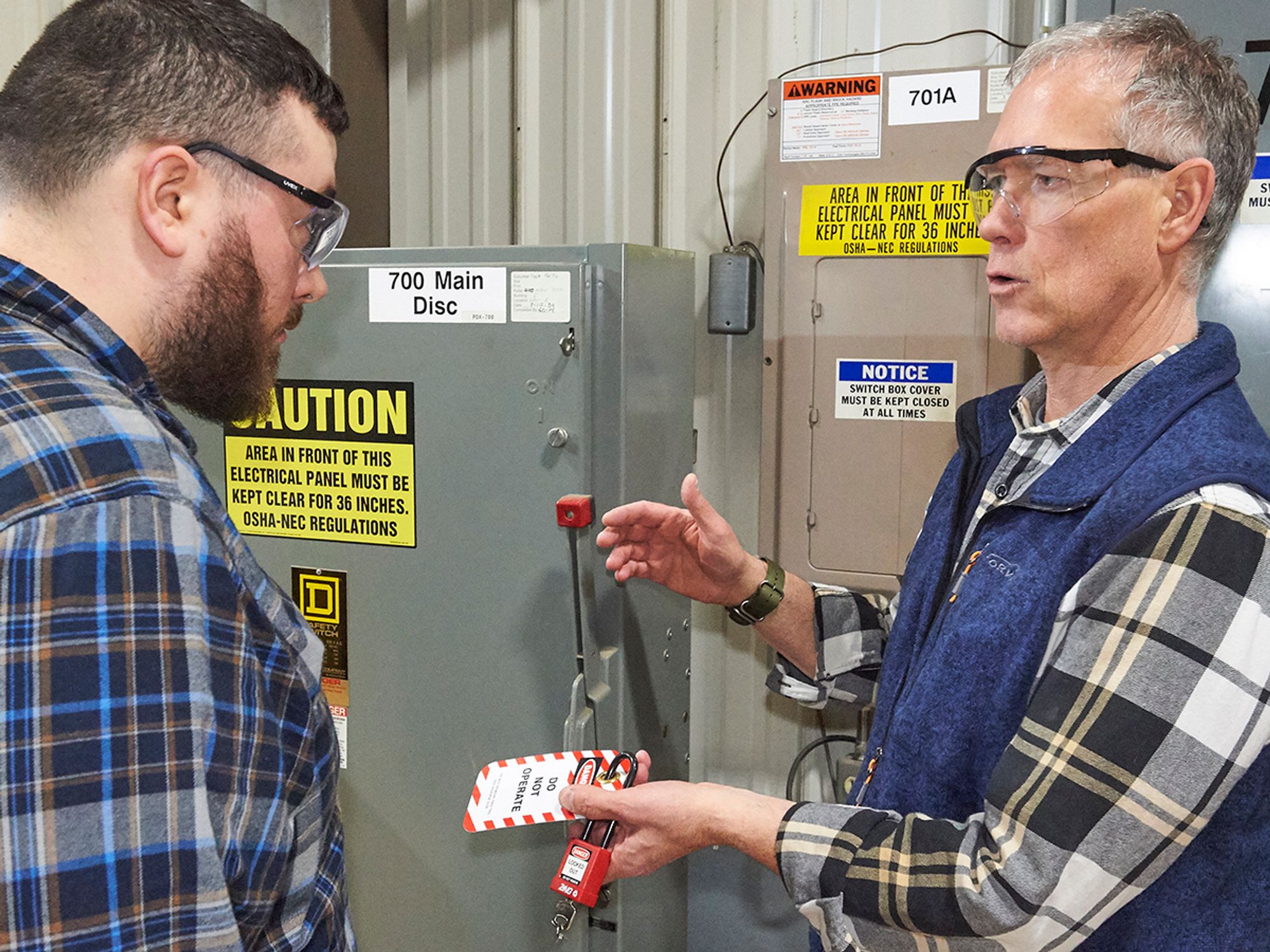
All employees working in areas where energy-control procedures are used must be trained in their duties under lockout/tagout. At minimum, an employer’s training program must cover:
- A review of the employer’s energy-control program,
- The elements of each energy-control procedure that relate to the employees’ duties, and
- The relevant requirements of the lockout/tagout standard (29 CFR 1910.147).
The specific training an employee receives depends on whether that employee is an authorized employee, affected employee, or other employee.
Authorized employees
Authorized employees must be trained:
- To recognize sources of hazardous energy,
- To understand the types and magnitudes of energy available to machinery and equipment and in the workplace,
- To know which lockout/tagout devices are used with which energy-isolation devices,
- To locate the energy-isolating devices on each machine and piece of equipment,
- To use the proper sequence for applying lockout/tagout devices to and removing them from the energy-isolating devices; and
- To only remove one’s personal lockout/tagout devices from energy-isolation devices.
Affected employees
Affected employees must be trained:
- On the purpose and use of energy-control procedures.
- To be alert and responsive to notifications about lockout/tagout activities in their areas,
- To stay clear of machinery and equipment when notified that lockout/tagout devices are going to be applied, and
- To position themselves a safe distance away when notified that lockout/ tagout devices have been removed.
Other employees
Other employees must be trained.
All employees working in areas where energy-control procedures may be used must be instructed about those procedures and must understand that they are prohibited from tampering with lockout/tagout devices and from restarting or reenergizing locked or tagged out machinery and equipment.
Employees not authorized to operate machinery must always stay clear of machinery and equipment when it is locked out for repairs. For instance, administrative employees delivering messages to employees in the work area must be able to identify and avoid contacting lockout devices, even if another employee asks for assistance.
This training does not have to be drawn out. Training is sufficient so long as it covers what lockout/tagout devices look like and that only trained, authorized employees can handle them.
Training for tagout programs
If a tagout program is used instead of a lockout program, further training is required for employees. Tagout training must ensure that all employees understand the limitations of tags: tags are warning devices that do not provide the same level of protection as lockout devices, which physically restrain the position of energy-isolation devices. Employees using tagout devices must be trained to understand that tagout devices might evoke a false sense of security.
As with lockout devices, a tagout device may only be removed by the authorized employee who attached it. Further, tagout devices should never be bypassed, ignored, or otherwise defeated, and must always be positioned so that their warnings against the hazards of energization, such as “Do Not Start,” are clearly visible and easily legible.
Retraining
The employer must retrain all authorized and affected employees whenever there is:
- A change in their job assignments;
- A change in machines, equipment, or processes that present a new hazard; or
- A change in the energy-control procedures.
Additional retraining is required whenever an inspection reveals or an employer reasonably suspect that an employee fails to understand or comply with the steps of an energy-control procedure.
For example, if an inspection reveals that an employee uses a lock other than the employee’s personal lockout device, that employee must be retrained. The retraining, along with the initial training, must establish employee proficiency and introduce new or revised control methods and procedures, as necessary.
Certification of training
The employer is required to certify that each trained employee has the knowledge, skills, and understanding to work safely. The certification must contain each employee’s name and the training date. Authorized employees and affected employees must be retrained whenever they have a change in job assignments or whenever a change in equipment, process, or energy-control procedures could expose them to a new hazard. Inspections that reveal inadequacies also trigger retraining.
The employer is required to certify that employee training has been accomplished and is being kept up to date. This certification must include the employee’s name and the dates of the training. Certifications must be updated after any refresher training.