What are the hazards?
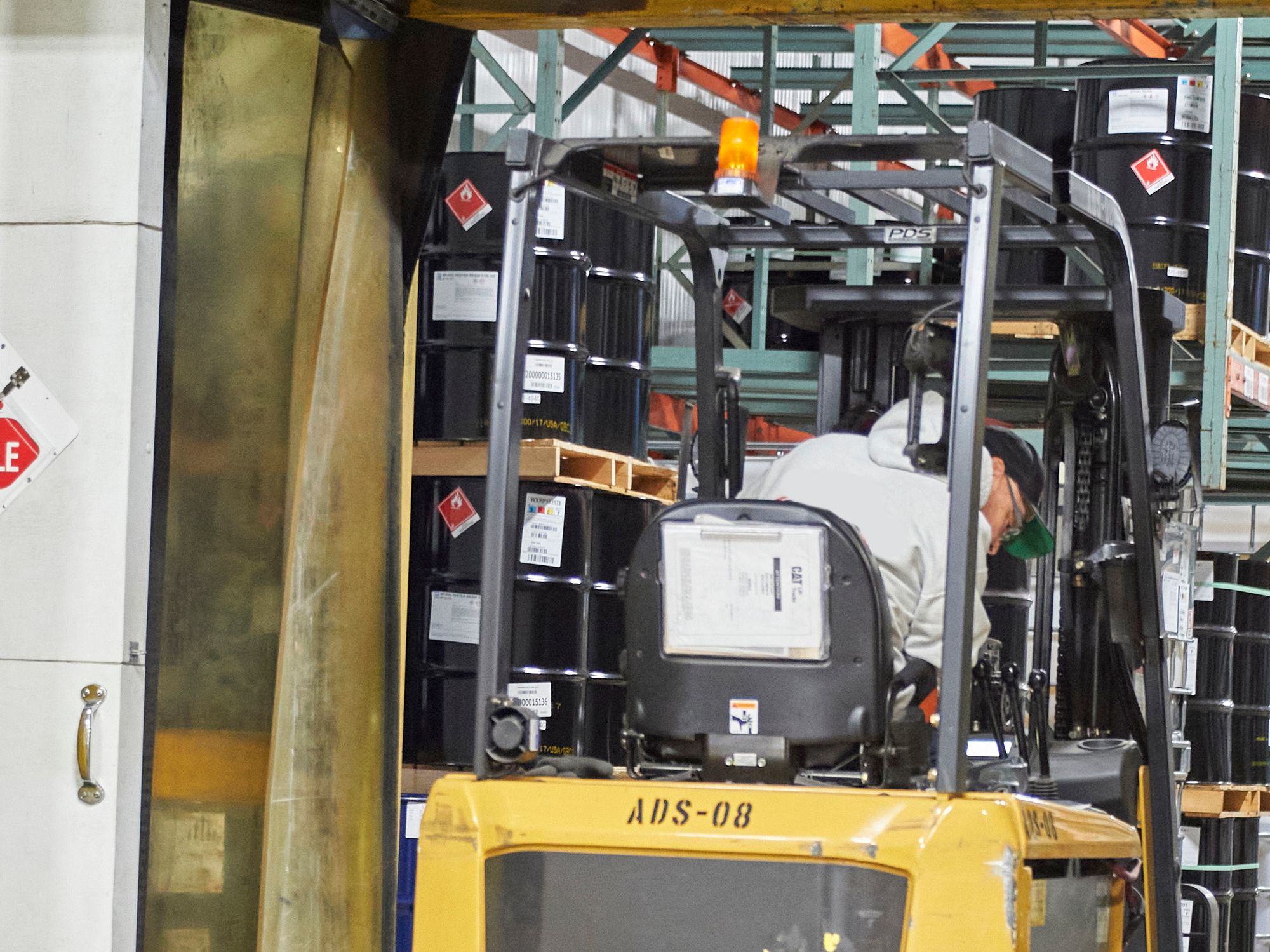
- Different classes of PITs have different associated hazards, therefore requiring specialized approaches to accident prevention.
- Excessive speed, obscured vision, load instability, workplace conditions, and improper use are all common causes of PIT accidents in the workplace.
Powered Industrial Trucks (PITs) are used in almost all industries. They can be used to move, raise, lower, or remove large objects or a number of smaller objects on pallets or in boxes, crates, or other containers. Because PIT movement is controlled by the operator and is not restricted by the frame of the machine or other impediments, virtually unrestricted movement of the vehicle about the workplace is possible.
The hazards commonly associated with PITs vary for different vehicle types, makes, and models. Each type of truck presents different operating hazards. For example, a sit-down, counterbalanced high lift rider truck is more likely than a motorized hand truck to be involved in a falling load accident, because the sit-down rider trucks can lift a load much higher than a hand truck can.
Accident prevention
The methods or means to prevent an accident and to protect employees from injury vary for different types of trucks. For example, operators of sit-down rider trucks are often injured in tip-over accidents because of the natural tendency to jump downward and land on the floor or ground, where they can then be crushed by the vehicle’s overhead guard as the vehicle tips over. Therefore, operators of sit-down trucks need to be trained to remain in the operator’s position in a tip-over accident and to lean away from the direction of fall to minimize the potential for injury.
On the other hand, when a stand-up rider truck tips over, the truck operator can exit the vehicle by simply stepping backward, perpendicular to the direction of the vehicle’s fall, to avoid being crushed. In this situation, the operator usually should attempt to jump clear of the vehicle and should be trained accordingly.
Safe operation and workplaces
Driving a PIT at excessive speed can result in loss of control, causing the vehicle to skid, tip over, or fall off a loading dock or other elevated walking-working surface. This accident can be made more dangerous if the load being carried partially obscures the operator’s vision. A vehicle that is out of control or being operated by a driver whose vision is obscured can strike an employee, run into a column or other part of the building, or strike material, causing it to topple and injure employees in the area. Effective driver training teaches operators to minimize these hazards.
Other characteristics of a PIT that affect safe truck operation are the truck’s tendency to become unstable, its ability to carry loads high off the ground, and its characteristic mode of steering with the rear wheels while being powered by the front wheels. Moving loads upward, downward, forward, and backward causes a shift of the center of gravity of the vehicle and can adversely affect its stability. When a load is raised or moved away from the vehicle, the vehicle’s longitudinal stability is decreased. When the load is lowered or moved closer to the vehicle, its longitudinal stability is increased.
The workplaces where PITs are being used can also present a variety of different hazards. The safety of industrial truck operations can be decreased by workplace conditions such as rough, uneven, or sloped surfaces; unusual loads; hazardous areas; narrow aisles, blind spots, or intersections; and pedestrian traffic or employees working close to the path of travel. Finally, there are hazardous work practices that relate to all trucks, including operating at excessive speed, operating too close behind another PIT, poor loading practices, and carrying unauthorized passengers. In addition, poor truck maintenance can contribute to accidents.
Many accidents have occurred because of unsafe truck operation. For example, employees have fallen from trucks while using them to change light bulbs on overhead fixtures or riding on the forks to manually retrieve items from high racks. Many accidents have occurred when an operator has attempted to drive with an obstructed view in the direction of travel and has run into another employee. Improper truck maintenance has caused death from over exposure to carbon monoxide, loss of brakes, or rupture of hydraulic lines. Also, PITs that damage the legs of a storage rack may expose employees to struck-by hazards from falling materials stored on the rack.
Caution about under-ride hazards
A stand-up forklift operator was crushed and killed when the bottom half of the forklift passed beneath a beam of a storage rack. The Occupational Safety and Health Administration (OSHA) cited the employer under section 5(a)(1) of the Occupational Safety and Health Act for not furnishing a workplace free of recognized serious hazards, such as the under-ride hazard. The Occupational Safety and Health Review Commission later confirmed that employer training and extra-wide aisles were “inadequate” precautions in the case. Instead, the commission said OSHA’s suggested abatement measures were physically and economically feasible and would materially reduce the hazard. Those measures included adjusting shelf heights, installing rack barriers, or installing rear post guards on the forklifts.