General
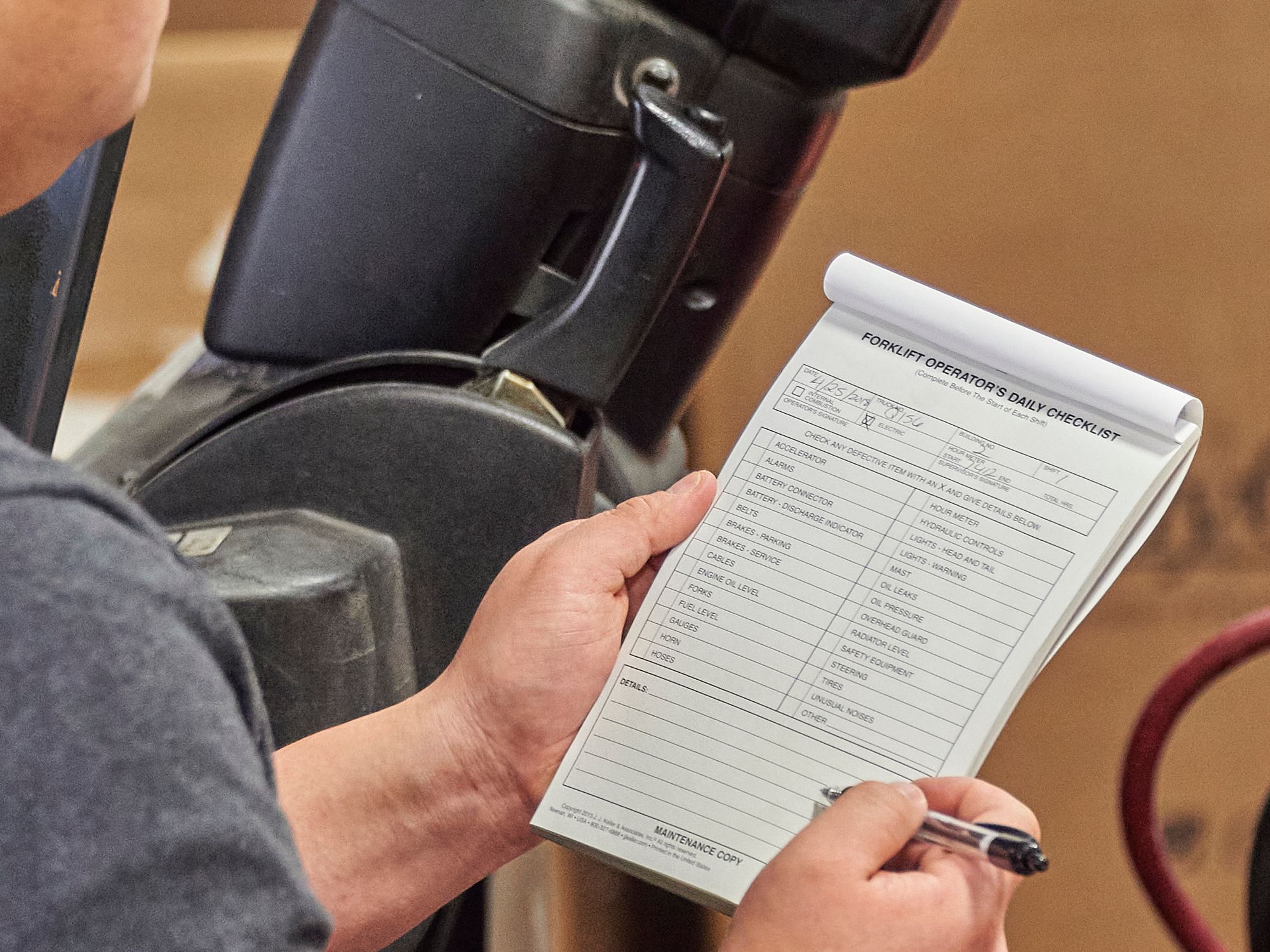
- There are specific ANSI standards for the general use and maintenance of PITs and the workplaces they operate in.
Operation
All Powered Industrial Trucks (PITs) must be designed and constructed in compliance with the American National Standards Institute (ANSI) standard B56.1-1969. (1910.178(a)(2)) Employers must ensure that only approved trucks are used in areas where flammable gases or vapors, combustible dust, or ignitable fibers are present in the atmosphere. Trucks with internal combustion engines that operate in buildings or enclosed areas must be checked to ensure they do not cause harmful concentrations of dangerous gases or fumes.
Any trucks not in safe operating condition are to be promptly removed from service. (1910.178(q)(1)) Repairs to fuel and ignition systems must be conducted only in areas specifically designated for them. (1910.178(q)(3)) Trucks are to be inspected daily, or after each shift if used around the clock, and before being placed in service. (1910.178(q)(7)) Directional lighting must be provided on each truck that operates in an area with less than two foot-candles per square foot of general lighting. (1910.178(h)(2)) Any trucks used by a company must be correctly designated for that type of operation (based on atmosphere, hazards of materials handled, etc.). (1910.178(c)(2))
Material handling
When assessing how a PIT will handle material, employers and operators must ensure there is sufficient clearance for equipment through aisles and doorways. (1910.176(a)) There must also be clearance signs to warn of clearance limits, and permanent aisles and passageways must be appropriately marked. (1910.176(e), 1910.176(a)) Bags, containers, bundles, etc. need to be stacked, blocked, interlocked, and limited in height so they are stable and secure. (1910.176(b))
Operators must use dock boards (bridge plates) when loading or unloading operations are taking place between vehicles and docks, and trucks and trailers should be secured from movement. (1910.178(m)(7))
Battery charging
Battery charging installations (located in areas designated for that purpose) and the batteries themselves must be charged in a properly vented room. (1910.178(g)(1), 1910.178(g)(2)) The local ventilation must be sufficient to disperse fumes. (1910.178(g)(2)). Facilities must be provided for flushing and neutralizing spilled electrolyte, fire protection, and protecting charging apparatus from damage by trucks. (1910.178(g)(2))
A conveyor, overhead hoist, or equivalent material handling equipment must be provided for handling batteries. (1910.178(g)(4)) Any reinstalled batteries must be properly positioned and secured in the truck. (1910.178(g)(5)) A carboy tilter or siphon must be provided for handling electrolyte. (1910.178(g)(6))
When charging batteries, employees must make certain not to pour water into acid, and that trucks are properly positioned with brakes applied first. (1910.178(g)(7), 1910.178(g)(8)) They must also ensure that the vent caps are functioning. (1910.178(g)(9)) Smoking must be prohibited in battery charging areas, and precautions taken to prevent open flames, sparks, or electric arcs in the charging area, such as keeping tools and other metallic objects away from the top of any uncovered batteries. (1910.178(g)(10)-(12))
Fueling
Fueling an internal combustion engine with a flammable liquid while the engine is running must be prohibited. (1910.178(p)(2)) Employees should ensure fueling operations are done in such a manner that the likelihood of spillage will be minimal. (1910.178(p)(2)) If spillage does occur, employees should take measures to control any vapors before restarting the engine. (1910.178(p)(3))
Aisles and walkways
Aisles must be marked and in good condition, with their widths maintained. (1910.22(b)(1)-(2)) They must also be clean and free of obstructions. (1910.22(b)(1)) Additionally, employees must ensure that fire aisles, access to stairways, and fire equipment are all clear. (1910.178(m)(14)) The aisles and passageways must be properly illuminated.
There should be safe clearance for equipment through all aisles and doorways. (1910.176(a)) Any pits and floor openings should be covered or otherwise guarded. (1910.22(c); .23(a)) Additionally, there must be standard guardrails present where aisle or walkway surfaces are elevated four feet or more above any adjacent floor or the ground. (1910.23(c)) Adequate barriers and warnings should be provided to prevent employees from stepping into the path of traffic where vehicles may be operated.
Housekeeping
Work areas, floors, walkways, and other surfaces should be clean and orderly. (1910.22(a), 1910.141(a)(3)(i)) Employees should check if there are any spilled materials or liquids present and if work surfaces are dry, and mats or grating should be used where drainage is needed. (1910.141(a)(3)(ii) 1910.22(a)(2)) Employees should use compressed air for cleaning under 30 pounds per square inch (psi). (1910.242(b)) Employees should also check for any accumulation of dust and/or other potential contaminants. (1910.141(a)(3))
Personal protective equipment (PPE)
Employees must wear foot protection anywhere there is risk of foot injuries in the workplace. (1910.132(a); .136(a)) They must also wear hard hats anywhere danger of falling objects exists. (1910.135(a)(1)) Companies should also ensure the use of protective goggles or face shields where there is danger of flying particles or corrosive materials. (1910.133(a)(1))
Approved safety glasses must be worn where there is a risk of eye injuries such as punctures, abrasions, contusions, or burns. 1910.133(a)(2) Employees should wear appropriate safety glasses, face shields, etc. while using hand tools or equipment which might produce flying materials or be subject to breakage. (1910.133(a)(1))
Companies must ensure that employees use required protective clothing or equipment as needed, and that it fits properly, is functional and in good repair, and marked with ANSI or ASTM International specifications. (1910.132(a), 1910.132(e), .135(b))
Postings
Required truck operating rules should be posted.
Recordkeeping
Any inspection and maintenance records should be kept on file.
Training
Only trained personnel should be allowed to operate industrial trucks, and the training methods used to train operators must be documented and meet the requirements specified in 1910.178(l).
Documentation
The Occupational Safety and Health Administration (OSHA) requires that forklift vehicles be inspected at least daily, or after each shift when used around the clock.