Standard operating procedures (SOPs)
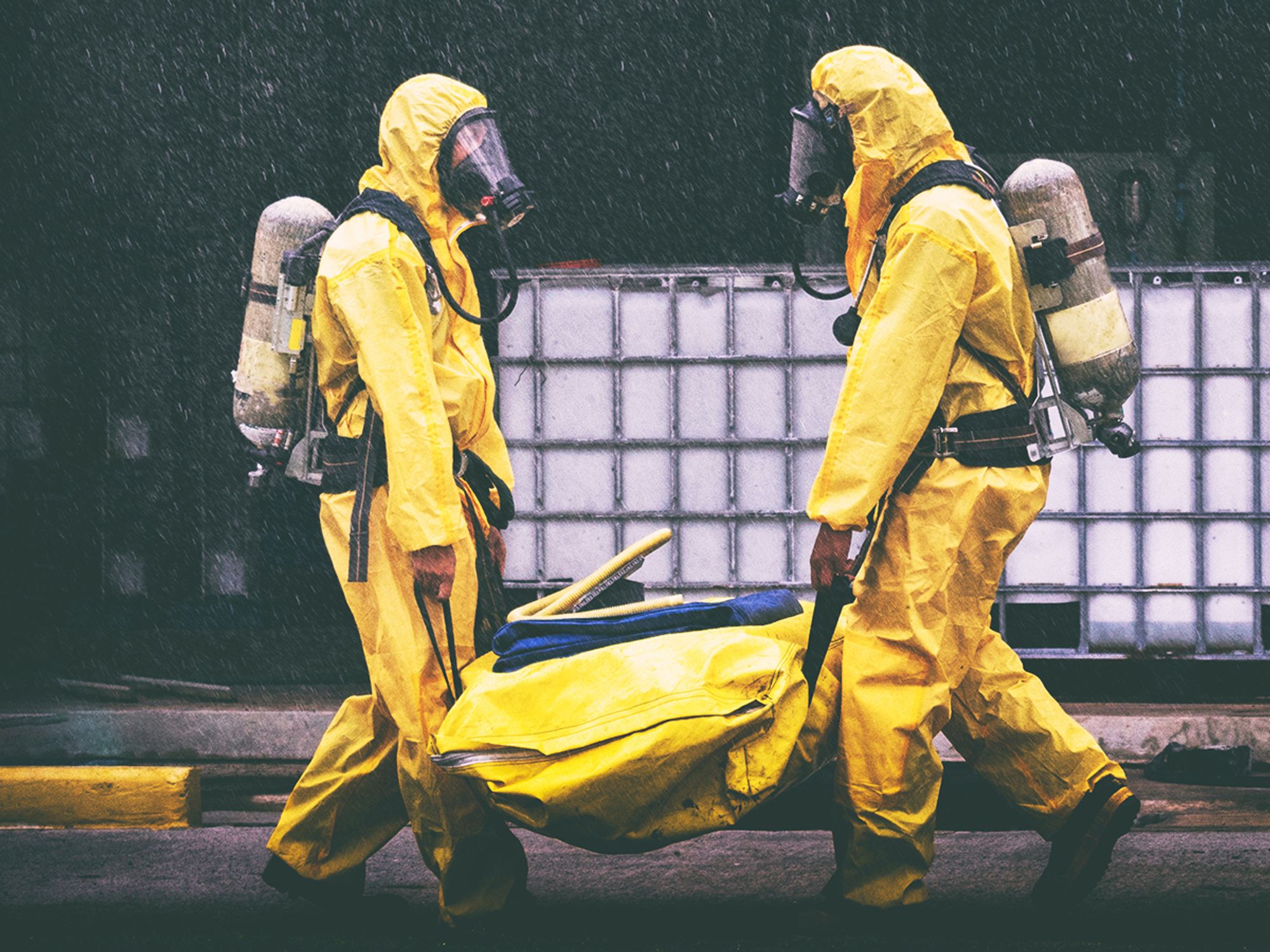
- Employees should be trained in relevant SOPs — procedures for activities that can be standardized — prior to using them in the field.
As part of the safety and health program, the Occupational Safety and Health Administration (OSHA) requires employers to have written procedures for safe work practices. These standard operating procedures (SOPs) are used for activities that can be standardized. Some examples include:
- Decontamination
- Confined space entry
- Respirator fit tests
- Spill control
- Emergency response
SOPs should be easy to understand; prepared in advance; and based on available information, operational principles, and technical guidance. In addition, they should be field tested and should be revised as necessary.
Employees should receive training on specific SOPs needed to perform their duties and should be encouraged to review them prior to using them in the field. This will ensure they understand all the steps involved in the tasks and are able to gather and prepare any equipment they may need.