- Signs and other marking systems are used in addition to other control measures to prevent work injury and illness.
- In some cases, signs and other marking systems are required.
Ideally, the workplace would be hazard-free and safe from potential injuries and accidents. However, many operations involve a certain amount of risk that cannot be completely controlled through engineering, administrative, and work practice controls or proper training. That’s where safety signs, tags, labels, and other marking systems come into play, as one additional means to prevent work accidents and subsequent injury or illness. These marking systems are not just a good idea; in many cases they’re required.
Key definitions
To understand the Signs and Markings topic, it is important to first understand what certain terms mean. These terms, as defined here, are used throughout this topic.
Aisle marking: Markings used to delineate permanent aisles or passageways. Any marking method may be used, including applying floor markings; marking pillars; or placing flags, traffic cones, barrels, and other devices.
ANSI: The American National Standards Institute.
Barricade tape: A non-adhesive strip of polyethylene, vinyl, or other material positioned to block and alert employees and others to a temporary hazard in order to prevent injury or illness. Safety colors, signal words, safety symbols, and message text may appear on the strip.
Floor marking: A marking method in which slip-resistant paint, tape, or another coating medium is applied to, adhered to, or integral with the floor. Floor marking patterns include solid color, angled bars of alternating color, a checkerboard of alternating color, a geometric combination of colors, and a photoluminescent application.
Floor sign: A non-required sign or decal adhered to or painted on the floor with text used for the following purposes: to identify clearances or the location of fire/safety equipment, for non-mandatory communication with employees, or as a supplement to required signs.
Label: Any written, printed, or graphic material displayed on or affixed to equipment, a container, or another item. Labels are not intended to be either the sole, or the most complete, source of information regarding the nature or identity of the item.
Marking system: A type of marking (sign, tag, label, barricade tape, pipe markings, etc.) that is intended to communicate with employees and/or the public and is part of a larger family of markings.
Message panel: The portion of a sign, tag, label, or other marking type with the basic words that convey what the employer wants to say to the employee, including hazard alerts, consequences, prohibitions, actions, and other information.
Pipe marking: A marking method that uses color, legends, arrows, symbols, and/or other details to identify the materials conveyed by a piping system and possibly the hazards of those materials if released.
Portable floor stand sign: A sign on a foldable stand positioned on the floor to alert employees and others to a temporary hazard in order to prevent injury or illness. An example is the CAUTION WET FLOOR stand sign often seen in retail or restaurant establishments.
Safety color: A standardized color used on signs, tags, labels, and other marking systems. The Occupational Safety and Health Administration (OSHA) and the American National Standards Institute (ANSI) offer 10 safety colors that follow certain ink color specifications.
Safety symbol panel: The portion of a sign, tag, label, or other marking type that depicts one or more graphical symbols that help communicate the sign’s meaning, sidestep language barriers, and attract employees’ attention.
Safe viewing distance: The nearest point from a sign at which an employee can read it but still avoid the hazard conveyed by the sign.
Sign: In most cases, a surface prepared for the warning of, or safety instructions for, industrial employees or members of the public who may be exposed to hazards. However, signs may also inform employees of the location of exit routes, safety equipment, and fire equipment and communicate other information, such as security, smoking, and hygiene policies. Excluded from this definition are news releases, displays commonly known as safety posters, and bulletins used for employee education.
Signal word: The word or phrase on a sign, tag, label, or other marking that is intended to grab the employee’s attention, such as DANGER, WARNING, CAUTION, NOTICE, SAFETY INSTRUCTIONS, SAFETY EQUIPMENT, FIRE EQUIPMENT, BIOHAZARD, or EXIT.
Signal word panel: The portion of a sign, tag, label, or other marking that offers the signal word. The safety alert symbol — an exclamation point in an equilateral triangle with rounded corners — may be placed immediately before the signal word.
Slow-moving vehicle emblem: An emblem used as a unique identification for vehicles that by design move slowly (25 miles per hour or less) on public roads. See 29 CFR 1910.145 for information about the dimensions, color, material, location, mounting, etc. of the emblem.
Tag: A device usually made of cardstock, paper, pasteboard, plastic, or other material used to identify certain types of hazardous conditions and affixed as close as safely possible to its respective hazard(s) by string, wire, adhesive, or other positive means that prevents loss or unintentional removal of the device. Tags are used to prevent accidental injury or illness to employees who are exposed to hazardous or potentially hazardous conditions, equipment, or operations that are out of the ordinary, unexpected, or not readily apparent.
Safety color codes
- Safety colors are associated with specific meanings and used consistently so that employees can quickly understand them.
- Both OSHA and ANSI regulate safety color codes.
Safety color may be applied to surfaces and equipment to convey a safety-related message. In some cases, the color is required. Between the Occupational Safety and Health Administration (OSHA) and the American National Standards Institute (ANSI), there are 10 safety colors.
Note: Safety colors are standardized on signs, tags, labels, and other markings; however, color schemes for each marking system type are covered not here but elsewhere, under each marking system discussion in the Signs and Markings topic, where applicable.
Purpose of safety color codes
Because certain colors are associated with specific meanings or messages, using those colors consistently makes them more effective. Applying these uniform colors for safety purposes allows employees to quickly understand and recall the meaning of those colors as they work for one employer after another. This enables employees to take the right action in an emergency or in day-to-day operations.
Related regulations and standards
Both OSHA and ANSI have standards that relate to safety color codes:
- 29 CFR 1910.144 — Safety Color Code for Marking Physical Hazards.
- ANSI Z53.1-1967 — Safety Color Code for Marking Physical Hazards.
- ANSI Z535.1-1998 — American National Standard Safety Color Code.
- ANSI Z535.1-2006(R2011) — American National Standard for Safety Colors.
- ANSI Z535.1-2017 — American National Standard for Safety Colors.
- ANSI Z535.1-2022 — American National Standard for Safety Colors.
OSHA safety colors
- OSHA specifies using red to signify fire protection, DANGER, and STOP, and yellow to signify CAUTION and physical hazards.
Originally, the Occupational Safety and Health Administration (OSHA) had safety color codes for red, orange, yellow, green, blue, purple, black, white, and combinations of black and white. The use of each of these colors was specified at 29 CFR 1910.144. However, in 1978, the agency revoked several of the provisions and colors from the regulation, leaving only a few color applications for red and yellow. OSHA determined that, in the interest of employee protection, these remaining red and yellow provisions would not be revoked.
Safety red
According to OSHA, red shall be the basic color for the identification of:
- Fire protection equipment and apparatus,
- DANGER, and
- STOP.
Additional uses of red:
- Portable containers of flammable liquids having a flash point at or below 80°F and table containers of flammable liquids, excluding shipping containers, shall be painted red, with either a yellow band around the can or the name of the contents conspicuously stenciled or painted on the can in yellow.
- Red lights shall be provided at barricades and at temporary obstructions.
- Danger signs shall be painted red.
- Emergency stop bars on hazardous machines such as rubber mills, wire blocks, and flat work ironers shall be red.
- Stop buttons or electrical switches that have letters or other markings and are used for emergency stopping of machinery shall be red.
Safety yellow
OSHA states that yellow shall be the basic color for designating CAUTION and for marking physical hazards such as striking against, stumbling, falling, tripping, and getting caught in between.
Revoked safety colors
OSHA explains that many of its pre-1978 provisions for 1910.144 were “unnecessarily detailed.” Colors used by themselves were not very effective because there were no criteria for the hue and, therefore, there was no standardization in the physical application. According to OSHA, the protection of employees could be better addressed by the use of signs with both color and legend. The agency added that color used by itself may cause those who are color blind to fail to understand the intended message.
Some of OSHA’s concerns have been corrected in American National Standards Institute (ANSI) standard Z535.1, which defines specific color tolerances, making the color choices uniform. Also, ANSI has adjusted color tolerances so they are distinguishable for color-deficient vision.
While the application of color by itself cannot replace required signs and/or training, such application can still reinforce the message of any required sign or training.
It is important to acknowledge the now-revoked color meanings from a historical perspective. An employer may opt to apply these colors to go above and beyond current OSHA regulations. The following text includes the revoked passages from 1910.144(a). The present passages from 1910.144(a) are not shown below.
- (1) Red. Red shall be the basic color for the identification of:
- (i) Fire protection equipment and apparatus.
- (a) Fire alarm boxes (pull boxes).
- (b) Fire blanket boxes.
- (c) Fire buckets or pails.
- (d) Fire exit signs.
- (e) Fire extinguishers (if painting the extinguisher is impractical or undesirable, color should be used on the housing, wall, or support to identify the location).
- (f) Fire hose locations (color should be used on the reel, supports, or housing but not on the hose).
- (p) Fire hydrants (industrial).
- (h) Fire pumps.
- (i) Fire sirens.
- (j) Post indicator valves for sprinkler system (it is suggested that if a traffic hazard is involved, the top should be colored red, and the barrel or post yellow and black stripes).
- (k) Sprinkler piping. (See ANSI Standard Scheme for the Identification of Piping Systems, A13.1-1956.)
- (2) Orange. Orange shall be used as the basic color for designating dangerous parts of machines or energized equipment which may cut, crush, shock, or otherwise injure and to emphasize such hazards when enclosure doors are open or when gear belt, or other guards around moving equipment are open or removed, exposing unguarded hazards.
- (4) Green. Green shall be used as the basic color for designating “Safety” and the location of first aid equipment (other than firefighting equipment).
- (5) Blue. Blue shall be the basic color for designating caution, limited to warning against the starting, the use of, or the movement of equipment under repair or being worked upon.
- (6) Purple. Purple shall be the basic color for designating radiation hazards. “Radiation” as used in this subparagraph refers to radiation types such as X-ray, alpha, beta, gamma, neutron, proton, deuteron, and meson. Yellow should be used in combination with purple for markers such as tags, labels, signs, and floor markers.
- (7) Black, white, or combinations of black and white. Black, white, or a combination of these two, shall be the basic colors for the designation of traffic and housekeeping markings. Solid white, solid black, single color striping, alternate stripes of black and white, or black and white checkers should be used in accordance with local conditions.
Similarly, it may be of value to revisit the revoked passage from 1910.144(b), which stated, “(b) Color specifications. Colors shall meet the tests specified in section 3, Color Definitions, of ANSI Z53.1-1967, Safety Color Code for Marking Physical Hazards.”
ANSI safety colors
- The current version of ANSI Z535.1 designates 10 safety colors but does not specify their meanings.
- No comprehensive consensus standard for color meanings exists, so the 1998 version of Z535.1 is commonly used for guidance.
American National Standards Institute (ANSI) regulation Z535.1 is regularly revised about every five years. The latest edition focuses on color tolerances for 10 safety colors: red, orange, yellow, green, blue, black, white, purple, brown, and gray.
The 1998 edition of the consensus standard offered color meanings, which have since been removed from the standard. The idea was that other consensus standards for marking systems would cover the “application” or use of safety colors found in ANSI Z535.1.
Currently, there is no comprehensive regulation or consensus standard that lists the meanings of all safety colors, so employers continue to refer to the 1998 edition of ANSI Z535.1 for guidance. Below is a list of the safety colors and their meanings recommended by ANSI in 1998:
Safety color | Meaning |
---|
Safety Red | - Fire protection equipment
- Danger
- Flammable liquid
- Stop, including emergency stop buttons
|
Safety Orange | - Warning
- Machine parts that may cause injury
- Exposed parts
|
Safety Yellow | - Potential hazards
- Caution against unsafe acts
- Physical hazards (striking against, stumbling, falling, tripping, and getting caught in between)
- Flammable materials storage
- Corrosives
- Instability
- Traffic designation
- Housekeeping mark
|
Safety Green | - Safety equipment
- First aid
- Evacuation routes
|
Safety Blue | - Safety information
- Personal protective equipment (PPE)
- Notice
|
Safety Black | - Traffic designation
- Housekeeping mark
|
Safety White | - Traffic designation
- Housekeeping mark
|
Safety Black and White combination | - Traffic designation
- Housekeeping mark
|
Safety Black and Yellow combination | - Traffic designation
- Housekeeping mark
|
Safety Purple | - No assigned meanings or applications
|
Safety Brown | - No assigned meanings or applications
|
Safety Gray | - No assigned meanings or applications
|
Accident prevention signs
- Safety signs help to prevent death, injury, illness, and property damage in situations where serious hazards can’t be eliminated or reduced through other control measures.
- OSHA and ANSI both have regulations that apply to safety signs.
In many work settings, operations may present hazards to employees. That’s why it’s critical to make every effort to protect them. Safety signs are a key part of those efforts.
Purpose
Safety signs may not seem necessary when the hazards in a facility are “obvious.” However, what appears obvious to someone who’s familiar with the workplace may not be as evident to a new or transferred employee, contractor, or visitor.
When serious hazards cannot be eliminated or reduced through other control measures, signs help to prevent death, injury, illness, and/or property damage. Signs don’t just communicate; they give an employer the power to alert, prohibit, instruct, warn, inform, reinforce, and remind. What’s more, they reflect the safety culture of the organization.
Safety professionals or supervisors cannot always be present to warn employees of hazards. When the right sign is in the right place, it helps to prevent injury and illness. Signs are no substitute for other control measures, but they can take an active role in the overall safety and health program.
Related regulations and standards
Signs are not just a good idea for the workplace. In many cases, they’re required.
Here’s a case in point of sign regulations in action. The Occupational Safety and Health Administration (OSHA) issued a $42,000 proposed penalty to a food company for failing to post “safety instruction signs” in areas where combustible food ingredients are processed. The agency explains that the ingredients, when processed, create a fire and explosion hazard; therefore, signs must be used to provide employees with instructions about safety measures, per 29 CFR 1910.145(c)(3).
The applicable federal OSHA regulations at 29 CFR 1910 to 1928 must be reviewed to ensure sign compliance. Sign requirements are found throughout those regulations for general industry, maritime, construction, and agriculture. Examples include, but are not limited to, the following:
- Accident prevention signs — 1910.145, 1915.91, 1917.128, 1926.200, and 1928.21.
- Bloodborne pathogens — 1910.145, 1910.1030, 1915.91, and 1915.1030.
- Blast areas — 1926.905.
- Clearance limits — 1910.176.
- Confined spaces — 1910.146, 1918.93, and 1926.1203.
- Cranes in construction — 1926.1422 and 1926.1424.
- Dipping and coating operations — 1910.125.
- Electrical hazards — 29 CFR 1910 Subpart S, 1917.1, 1918.1, and 1926 Subpart K.
- Exits and exit routes — 1910.37 and 1926.200.
- Falling materials — 1926.850.
- Fire extinguishers — 1910.157.
- Fire hose reels and cabinets — 1910.158.
- Hazard communication — 1910.1200, 1915.1200, 1917.1, 1918.1, 1926.59, and 1928.21.
- Manlifts — 1910.68.
- Nonionizing radiation — 1910.97.
- Nonpotable water — 1910.141, 1915.88, and 1926.51.
- No smoking — 1910.106, 1910.107, 1910.110, and 1910.125 (for example).
- Pulp, paper, and paperboard mills — 1910.261.
- Radiation areas — 1910.1096.
- Spray finishing — 1910.107.
- Toxic and hazardous substances — 29 CFR 1910 Subpart Z, 1915 Subpart Z, 1917.1, 1918.1, 1926.60, 1926.62, 1926 Subpart Z, and 1928.1027.
- Welding and cutting — 1910.253.
State and local codes and regulations may also require signs.
Note: Section 1910.145 calls for signs or symbols (or other effective means, such as training) when failure to post signs or symbols may lead to accidental injury or property damage in general industry or shipyard operations. This is a catch-all requirement for posting signs near hazards.
In addition to OSHA regulations, the following non-mandatory consensus standards are related to signs:
- ANSI Z35.1-1968 — Specifications for Accident Prevention Signs.
- ANSI Z535.2-2011 — American National Standard for Environmental and Facility Safety Signs.
- ANSI Z535.2-2017 — American National Standard for Environmental and Facility Safety Signs.
Note that for construction, OSHA 29 CFR 1926.200 explains that ANSI Z35.1-1968 and ANSI Z535.2-2011 contain rules in addition to those specifically prescribed by 1926.200. Employers in construction must follow either ANSI Z35.1-1968 or ANSI Z535.2-2011, with respect to such additional rules, OSHA says.
Signage needs assessment
- The employer should assess the signage in the workplace to see whether signs need to be moved, updated, replaced, or added.
Even if a facility has safety signs, it’s beneficial to conduct a workplace assessment to:
- Assess what signs are present. This includes documenting where signs are in place and looking for signage concerns, such as illegible, inaccurate, or obstructed signs; inconsistent sign formats; several signs overloading the same location; or “signs” scribbled on a piece of paper.
- Determine which signs are needed. The following should be noted if they are unmarked: hazards, hazardous areas, safety/fire equipment, exit pathways, clearances, traffic areas, and machinery. Any entrances leading to areas that require personal protective equipment (PPE) should be considered, as should changes at work, maintenance areas, or company policies that may call for a sign.
Employees may be able to point out needed safety signs in their work areas. It may also be helpful to develop a checklist for each area of the workplace to ensure the assessment doesn’t miss anything. The following list of sign types offer some ideas:
- Admittance and exits
- Emergency shelters
- Housekeeping and spill control
- Slips, trips, and falls
- PPE
- First aid and eyewashes
- Fire protection
| - Smoking control
- Confined spaces
- Lockout/tagout
- Electrical and arc flash
- Machinery and equipment
- Forklifts and warehouses
- Chemicals
| - Biohazards
- Radiation and lasers
- Welding and hot work
- Construction and demolition
- Traffic control and parking
- Signs on vehicles
|
After surveying the workplace and reviewing the notes, an employer should implement a plan to correct any signage issues and meet the sign needs of the facility.
Sign elements
- Safety signs are composed of one or more distinct areas called panels.
- The panels that can be included on a sign are the message, signal word, safety symbol, and directional arrow panels.
Safety signs are composed of one or more panels, including the message, signal word, safety symbol, and/or directional arrow panels. A panel is a distinct area of a sign.
Message panel
The message panel offers the basic words used to convey what is being said. Messages communicate hazards, the consequences of ignoring hazards, prohibitions, mandatory actions, and other information.
The Occupational Safety and Health Administration (OSHA) says the message should be easily read and concise. The message must be factually accurate and contain sufficient information to be clearly understood. Finally, the agency recommends positive rather than negative suggestions, when possible. This means, except where prohibitions are the best approach, the message should inform employees of what to do, rather than what not to do.
Signal word panel
Between OSHA and the American National Standard for Environmental and Facility Safety Signs (ANSI Z535.2), there are at least nine signal words, each with a different meaning:
- DANGER — Indicates an immediate severe hazard that presents a threat of death or serious injury.
- WARNING — Indicates a hazard that presents a potential threat of death or serious injury.
- CAUTION — Indicates a potential or non-immediate minor/moderate hazard.
- NOTICE — Indicates non-hazard information, like company policies for housekeeping.
- SAFETY INSTRUCTIONS — Indicate procedures relative to safety.
- SAFETY EQUIPMENT — Indicates the location of safety equipment, such as personal protective equipment (PPE) or eyewash stations.
- FIRE EQUIPMENT — Indicates the location of fire protection equipment.
- BIOHAZARD — Indicates an agent infectious to humans.
- EXIT — Indicates a way of travel to an exit discharge.
However, for general industry and shipyards, 29 CFR 1910.145 only offers four signal words — DANGER, CAUTION, SAFETY INSTRUCTIONS (or equivalent), and BIOHAZARD. What about the other signal words?
- WARNING is offered by ANSI Z535.2. If it can be demonstrated that this ANSI standard provides employee protection equal to or greater than 1910.145, the WARNING signal word can be used in accordance with ANSI Z535.2, and the employer risks only a de minimis (no penalty) violation from OSHA.
- NOTICE, SAFETY EQUIPMENT, and FIRE EQUIPMENT appear to be acceptable because they are outside the scope of 1910.145. (A sign under 1910.145 is intended for the warning of, or safety instruction of, employees or the public who may be exposed to hazards.)
- EXIT is required elsewhere at 1910.37 for general industry.
Note that ANSI advises the use of what it calls a “safety alert symbol” for DANGER, WARNING, and CAUTION signal word panels. This symbol has an exclamation point inside an equilateral triangle.
Safety symbol panel
The safety symbol panel depicts one or more graphical symbols that contribute to a sign’s meaning, help sidestep language barriers, and capture employees’ attention. Common hazard symbols include those for radiation, biohazard, high voltage, and no smoking.
Selecting or creating symbols for signs should take into account the design principles found in ANSI Z535.3, American National Standard for Criteria for Safety Symbols. These principles recommend designs that are consistent, legible, understandable, representational, and simple. Surround shapes (shapes that surround a symbol) also give meaning to a sign:
- Triangle — Depicts the nature of the hazard.
- Circle with slash — Depicts what not to do.
- Circle — Depicts a mandatory behavior.
- Square or rectangle — Depicts an equipment location, egress information, or permissible action.
Directional arrow panel
Only 29 CFR 1926.200 for construction mentions directional signs, which point the employee to a way out or way to something, such as a room, fire exit, fire escape, or first aid. The directional arrow panel, with its white arrow on a black background, may be used with other sign panel types.
Sign formats and color schemes
- The look of a sign hinges on its format, color scheme, and size.
Format
The message, signal word, and safety symbol panels can be thought of as puzzle pieces that fit together inside a larger, typically rectangular space. Depending on the panels included, the employer has options when formatting a sign. Most signs will have a two- or three-panel format, in either a horizontal or vertical configuration. A sign may even have multiple panels of the same type, e.g., two symbol panels on a single sign.
Because 29 CFR 1910.145 talks about signal word and message panels, it’s understood that DANGER, CAUTION, SAFETY INSTRUCTIONS, and BIOHAZARD signs must include those two panels at a minimum, in whichever configuration is preferred, in order to be compliant with the Occupational Safety and Health Administration (OSHA) regulation.
OSHA does not require the safety symbol panel unless failure to designate a symbol may lead to accidental injury or property damage. A symbol panel may still be included if not required, but a symbol panel by itself is not compliant under 1910.145.
Signs can be offered in multi-language formats, which offer text in both English and another language. This is not required but may be a better approach to employee safety.
Color scheme
Certain color schemes are associated with sign types and surround shapes. The color schemes of the sign elements of signs depend on whichever OSHA regulation applies (e.g., 1910.145, 1915.91, 1917.128, 1926.200, and 1928.21) and whether the employer chooses to follow the color scheme prescribed by American National Standards Institute (ANSI) Z535.2 instead of the one specified by OSHA.
Where OSHA specifies a color scheme, if the employer can demonstrate that the ANSI standard provides equal or greater employee protection than the OSHA regulation, the ANSI provisions may be followed instead. Taking this option simply risks a de minimis (no penalty) violation. Whichever color scheme is chosen (OSHA or ANSI), the employer should use it consistently in the workplace.
Sign size
Standard sign sizes in inches include 7x10, 10x14, 14x20, and 20x28. The size to choose depends not on the regulations but rather on:
- Font type — Best practice calls for a sans serif font type, such as Helvetica. All capital letters should be reserved for short messages or for words that need emphasis.
- Font size — Font size depends on the minimum safe viewing distance from the sign and the reading conditions. The greater the distance and the poorer the reading conditions, the greater the font size should be.
- Amount of text — Message text should be as concise as possible.
According to ANSI Z535.2, minimum safe viewing distance (MSVD) is “the closest distance a person can be to a safety sign and still have time to follow the safety sign’s message to avoid the hazard.” The ANSI standard provides recommended message text heights based on the MSVD and reading conditions.
However, note that for construction, OSHA 29 CFR 1926.200 explains that ANSI Z35.1-1968 and ANSI Z535.2-2011 contain rules in addition to those specifically prescribed by 1926.200. Employers in construction must follow either ANSI Z35.1-1968 or ANSI Z535.2-2011, with respect to such additional rules, OSHA says. This is important because ANSI Z35.1-1968 has required “standard proportions” for sign sizes and panel sizes.
Sign materials and construction
- Selecting the right sign material and construction leads to signs that last and that meet OSHA regulations.
Sign material
Performance and durability of sign materials (also called substrates) is based on:
- Locational factors — Sunlight, precipitation, temperature extremes, exposure to contaminants, lighting, and the mounting surface, among other factors.
- Sign features — Substrate, fade resistance, color protection, anti-graffiti coatings, chemical splash protection, impact resistance, mounting devices/adhesives, cleaning/maintenance procedures, and expected lifespan, among other features.
Examples of sign materials include polycarbonate, alumaboard, aluminum, plastic, tagboard, and adhesive vinyl. Other materials are also available.
Sign construction
A sign must not pose a hazard itself. Occupational Safety and Health Administration (OSHA) regulation 29 CFR 1910.145 requires that all signs be furnished with rounded or blunt corners and be free from sharp edges, burrs, splinters, or other sharp projections. The ends or heads of bolts or other fastening devices also must not constitute a hazard.
Sign location
- Signs should be placed where they will not be damaged or blocked, and proper illumination should be applied.
The placement of a safety sign should fulfill the following criteria:
- Close to the hazard or equipment
- Clearly visible
| - In the line of sight
- Free from obstructions
- Well lit
| - Legible at a safe viewing distance
- Not lost in a sea of signs
|
Signs should be located where they won’t be subjected to abrasion, chemical exposure, or other damage. They should not be blocked by doors or other obstructions. Finally, if a sign must be posted near other signs, they should be arranged by importance.
Proper illumination of signs should be applied, even in an emergency. If lighting may be interrupted, such as during a power outage, it may be wise to use emergency lighting or signs with what the American National Standards Institute (ANSI) calls “photoluminescent and/or retro-reflective materials.”
The Occupational Safety and Health Administration (OSHA), for the most part, does not address the illumination of signs. However, 29 CFR 1910.37 goes over the illumination and minimum luminance value of EXIT signs.
Posting and maintaining signs
- Any bolts, nails, or hooks used to secure the sign should be checked to make sure they don’t present a hazard.
- Employers should inspect signs regularly for damage, obstructions, and other issues.
Once a location for the sign has been chosen, it’s time to post it. Any bolts, nails, or hooks used to secure the sign should be checked to make sure they don’t present a hazard. Signs should be placed behind glass or plexiglass as needed, depending on the working environment. To reach the optimum lifespan of the sign, the sign supplier’s regular cleaning procedures should be followed to remove any dirt, dust, grime, and oil.
Because signs do not last forever, they need to be monitored. Employers should inspect signs regularly for:
- Dirt or dust
- Grime or oil
- Chemical degradation
- Graffiti or vandalism
- Fading or defacement
- Bending or curling
| - Tears, cracks, or breakage
- Other damage or wear
- Illegibility
- Obstructions
- Poor lighting
- Missing signs
| - Confusing or misleading messages
- Outdated/incorrect signs due to work changes or eliminated hazards
- Poor sign placement due to workplace layout changes
|
The results of these inspections will dictate when it’s time to replace, or even remove, a sign.
If the Occupational Safety and Health Administration (OSHA) adds or changes sign requirements, the facility will need to check all existing signs to ensure they meet the new rules.
Employee training in signs and symbols
- All employees in general industry and shipyards be instructed on the meaning of DANGER and CAUTION safety signs.
- No matter the industry, it’s good practice to provide employee training on the meaning of safety signs.
Many employees cannot distinguish between the signal words. However, the Occupational Safety and Health Administration (OSHA) requires that:
- All employees in general industry and shipyards be instructed on the meaning of DANGER and CAUTION safety signs, per 29 CFR 1910.145.
- All construction employees be trained to recognize and avoid unsafe conditions, per 29 CFR 1926.21. Because signs help construction employees to recognize and avoid unsafe conditions, safety sign training is a must.
No matter the industry, it’s good practice to provide employee training on the meaning of safety signs. A training program should cover the following:
- What signs are,
- Their importance,
- Message types,
- Signal words,
- Safety symbols,
- Surround shapes, and
- Sign color schemes used in the specific workplace.
During training, it may be helpful to show photos of signs found in the trainees’ work areas and take trainees on a “sign tour” to point out the various signs in action at the facility.
Accident prevention tags
- Accident prevention tags are a temporary way to mark unexpected or not readily apparent hazards and potential hazards.
- Both OSHA and ANSI have standards that relate to accident prevention tags.
A tag is a device usually made of cardstock, paper, pasteboard, plastic, or other material used to identify certain types of hazardous conditions.
Purpose
Accident prevention tags are used to prevent accidental injury or illness to employees who are exposed to hazardous or potentially hazardous conditions, equipment, or operations that are out of the ordinary, unexpected, or not readily apparent. They are meant to be temporary and must be used until the identified hazard is eliminated or the hazardous operation is completed.
According to 29 CFR 1926.200 for construction, accident prevention tags must be used as a temporary means of warning employees of an existing hazard, such as defective tools or equipment. They must not be used to substitute for accident prevention signs.
Related regulations and standards
The Occupational Safety and Health Administration (OSHA) has regulations that relate to accident prevention tags:
In general industry, when tagout is used to comply with 1910.147, not only will the employer need to meet the tag specifications of that regulation, but the employer will also need to meet the tag specifications of 1910.145. Refer to the Lockout/Tagout subject for more information about tagout.
The American National Standards Institute (ANSI) also has standards that relate to accident prevention tags:
- ANSI Z35.2-1968 — Specifications for Accident Prevention Tags.
- ANSI Z535.5-2011 — American National Standard for Safety Tags and Barricade Tapes (for Temporary Hazards).
- ANSI Z535.5-2017 — American National Standard for Safety Tags and Barricade Tapes (for Temporary Hazards).
- ANSI Z535.5-2022 — American National Standard for Safety Tags and Barricade Tapes (for Temporary Hazards).
Note that for construction, OSHA 29 CFR 1926.200 explains that ANSI Z35.2-1968 and ANSI Z535.5-2011 contain rules in addition to those specifically prescribed by 1926.200. Employers in construction must follow either ANSI Z35.2-1968 or ANSI Z535.5-2011, with respect to such additional rules, OSHA says.
Employee training in tags
According to 1910.145, employees in general industry and shipyards must be informed about the following:
- The meaning of the various tags used throughout the workplace, and
- What special precautions are necessary.
According to 1926.21, construction employees must be instructed about the following:
- Recognition and avoidance of unsafe conditions, and
- Regulations applicable to their work environment to control or eliminate hazards or other exposure to illness or injury.
Tag elements
- The primary elements of a tag are its signal word and message panels.
A tag must have a signal word and message panels but may use three additional types of panels:
- Signature block
- Safety symbol
- Border
A panel is a portion of a safety tag that has a background color that differs from the colors of adjacent areas, or that is separated from adjacent areas by white space, a border, or a line.
Signal word panel
The signal word panel includes the signal word, along with the safety alert symbol (when used). The signal word refers to the part of a tag that contains the word or words, like DANGER or CAUTION, intended to capture the employee’s immediate attention. The Occupational Safety and Health Administration (OSHA) and American National Standards Institute (ANSI) provide specifications for signal words that overlap significantly but not entirely.
OSHA offers the following signal words for tags:
- DANGER — Used only in major hazard situations where an immediate hazard presents a threat of death or serious injury to employees.
- WARNING — May be used to represent a hazard level between CAUTION and DANGER, with an appropriate message.
- CAUTION — Used only in minor hazard situations where a non-immediate hazard, potential hazard, or unsafe practice presents a lesser threat of employee injury.
- BIOLOGICAL HAZARD/BIOHAZARD — Used to identify the actual or potential presence of a biological hazard and to identify equipment, containers, rooms, experimental animals, or combinations thereof, that contain or are contaminated with hazardous biological agents.
OSHA allows other tags to be used in addition to these, or in situations where tags are not required, provided that they do not detract from the impact or visibility of any required tag.
ANSI also offers the DANGER, WARNING, and CAUTION signal words but also offers the following signal words:
- NOTICE — Indicates non-hazard information that is important, like property damage.
- SAFETY INSTRUCTIONS — Indicates procedures related to safety. Instead of the phrase SAFETY INSTRUCTIONS, more descriptive signal words may be used, such as LOCKOUT PROCEDURE.
The older ANSI Z35.2-1968, which OSHA accepts for construction tags, also offers the following signal words: DO NOT START, OUT OF ORDER, and RADIATION.
When used in the signal word panel, the safety alert symbol — an exclamation point inside an equilateral triangle — is provided with DANGER, WARNING, and CAUTION signal words to indicate a hazard. It is not applied on NOTICE or SAFETY INSTRUCTION tags.
Message panel
The message panel contains the major message, which means that portion of a tag’s inscription that is more specific than the signal word. This message indicates, in word text, the relevant hazardous condition or the instruction that needs to be communicated to the employee. Messages communicate hazards, the consequences of ignoring hazards, prohibitions, mandatory actions, and other information. The message panel will begin with the most important information.
The message should be concise and easy for employees to understand. Examples include:
- “High Voltage”
- “Close Clearance”
- “Do Not Start”
- “Do Not Use”
It should be noted that both OSHA and ANSI allow the employer to use a symbol panel instead of a message panel on a tag.
Signature block
The signature block is the area of a tag used to convey information such as a name, signature, date, department, and/or job-specific comments. This block is typically filled in by hand by the employee when in the field. The date(s) may relay a start date and/or completion date. The name identifies the person who authorized or applied the tag.
Safety symbol panel
The safety symbol panel contains a safety symbol(s). This panel offers a pictorial representation used to identify the hazardous condition, convey the safety instruction, or otherwise clarify or supplement the message. Symbols often capture the employees’ attention and help sidestep language barriers.
Safety symbols must contribute to the tag’s meaning, not conflict with it. The selected symbol should also be quickly understood by all employees. The symbol design for biological hazard tags must conform to the image shown below:
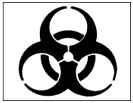
A symbol panel may also substitute for the message panel or part of the word message.
What’s more, many employers offer a personal photo in the safety symbol panel to assist others who need to quickly identify the employee who authorized or applied a tag. This may be the case in an emergency.
Border panel
A border color or colors may also be applied to the front and back edges. While not required, such a border may grab the attention of employees.
Tag formats and color schemes
- Tags can vary according to the circumstances.
- Tags typically offer panels on both the front and back.
General requirements
The American National Standards Institute (ANSI) offers some general guidelines, which are adopted by the Occupational Safety and Health Administration (OSHA) for construction operations, but not for general industry or maritime.
A rectangular tag is standard; however, it is acceptable to round or angle the corners.
The front of a tag should contain the following panels, from top to bottom, and elements inside these panels may be centered or left justified:
- Signal word
- Safety symbol (if any)
- Message
- Signature block
The tag back should contain the following panels, from top to bottom:
- Signal word
- Safety symbol (if any)
- Message
- Instruction to “See Other Side”
The back may also offer further instructions, phone numbers, and other supporting information.
Multi-language options are also offered by ANSI.
Signal word panel format
When a safety alert symbol is used, ANSI says it should be at least the same height of the signal word (or greater) and located just to the left of the signal word. Its color scheme varies depending on the signal word.
OSHA does not mandate the colors to be used on accident prevention tags but recommends the following color scheme to correspond with signal words:
- DANGER — Red, or predominantly red, with lettering in a contrasting color.
- CAUTION — Yellow, or predominantly yellow, with lettering in a contrasting color.
- WARNING — Orange, or predominantly orange, with lettering in a contrasting color.
- BIOLOGICAL HAZARD — Fluorescent orange or orange-red, or predominantly so, with lettering in a contrasting color.
ANSI requirements for signal word panels are more detailed. However, here is a summary:
- DANGER – Red with lettering in white.
- WARNING — Orange with lettering in black.
- CAUTION — Yellow with lettering in black.
- NOTICE — Blue with lettering in white.
- SAFETY INSTRUCTIONS — Green with lettering in white.
ANSI suggests using uppercase, sans serif font for all signal words, with legibility from five feet or more.
Message panel format
ANSI generally calls for the message panel to be white with black text. Yet, there are some exceptions for the symbol panel or the back of the tag.
ANSI also suggests using a headline-style capitalization (e.g., Do Not Touch) with sans serif font. All caps may be used for emphasis or shorter messages. Also, left justification is generally recommended.
Font size must be legible from the reading distance, and ANSI offers suggested sizes. For example, for a distance of five feet, a minimum of 16 point is suggested when reading conditions are good. A larger 42-point size is suggested for that distance if poor lighting or other conditions make reading difficult.
Tag materials, location, and attachment
- Tag material must be able to tolerate its environment.
- A tag must be placed as close as possible to the respective hazard.
Tag materials
Tags are usually made of:
- Card stock
- Paper
- Pasteboard
- Plastic
- Other material
However, the tag must, according to the American National Standards Institute (ANSI), also be able to tolerate its environment, for as long as it is used.
Tag location and attachment
OSHA says tags need not be used where signs, guarding, or other positive means of protection are being used. Tags must also be affixed as close as safely possible to their respective hazards using string, wire, adhesive, or other positive means that prevents their loss or unintentional removal. ANSI adds mention of tagging equipment controls and using nylon ties.
Safety labels
- A label is any written, printed, or graphic material displayed on or attached to equipment, containers, or other items.
- Various OSHA regulations and an ANSI standard can apply to safety labels, depending on the circumstances of a workplace or task.
The Occupational Safety and Health Administration (OSHA) does not have a comprehensive regulation for labeling. Instead, label requirements are scattered throughout the regulations. Whether a labeling requirement applies to a particular workplace depends on whether that establishment falls under the scope and applicability of the specific regulation and the labeling requirement.
A label is any written, printed, or graphic material displayed on or affixed to:
- Equipment
- A container
- Regulated waste, scrap, or debris
- Other item
Labels are intended to warn, inform, instruct, and prohibit employees. However, labels are not intended to be either the sole or the most complete source of information regarding the nature or identity of an item.
Safety label regulations and standards
- OSHA has numerous labeling requirements in its regulations, while ANSI has a non-mandatory product labeling standard.
Several Occupational Safety and Health Administration (OSHA) regulations call for safety labels. It is also worth noting that the American National Standards Institute (ANSI) has a non-mandatory standard on product safety labels.
General industry regulations
The following regulations include a labeling requirement, but there may be many others:
Construction industry regulations
The following regulations include a labeling requirement, but there may be many others:
Labeling regulations for the construction industry are identical to those for general industry found under 1910.1200.
Maritime industry regulations
Labeling regulations for the maritime industry are identical to those for general industry found under 1910.1200. There may be other labeling requirements for the maritime industry found in 29 CFR 1915, 1917, and 1918.
Agriculture industry regulations
Labeling regulations for the agriculture industry are identical to those for general industry found under 1910.1200. There may be other labeling requirements for the agricultural industry found in 29 CFR 1928.
ANSI standard
American National Standards Institute (ANSI) Z535.4-2017, American National Standard for Product Safety Signs and Labels, offers non-mandatory guidance for design, use, and placement of safety labels on products. These labels communicate hazards, instructions, consequences of ignoring the hazards or instructions, and other information.
The standard covers the following:
- Signal words (DANGER, WARNING, CAUTION, NOTICE, and SAFETY INSTRUCTIONS);
- Label format and color schemes; and
- Label placement, maintenance, and replacement.
Pipe markings
- Pipe markings are used to standardize the identification of pipe contents, hazards, and direction of flow.
- Some OSHA regulations apply to pipe markings, several of which reference an ANSI standard.
A pipe marking is a marking method that uses color, legends, arrows, symbols, and/or other details to identify the materials conveyed by a piping system and possibly the hazards of those materials if released. This marking method is not to be confused with signs or tags.
Purpose
Pipe markings are intended to standardize the identification of pipe contents, hazards, and direction of flow. Together, the legend, color code, arrows, and other indicators allow for quick recognition and understanding of the identity and hazards of the material conveyed by a pipe, as well as the direction of flow. When employees know the identity, hazards, and direction of the materials conveyed in a piping system, they should be better equipped to:
- Identify the correct pipe for the task;
- Turn the correct valve;
- Load material to or unload material from the correct pipe;
- Know which material is leaking from a pipe;
- Wear appropriate personal protective equipment (PPE) to handle the material; and
- Take appropriate first aid, fire, or spill response to an emergency involving the material.
Even when not required by the Occupational Safety and Health Administration (OSHA), pipe markings are recommended for active and abandoned piping in industrial, commercial, institutional, and public assembly facilities. Pipe markings are not intended for buried pipelines or electrical conduits, which may require other identification methods.
Related regulations and standards
OSHA mandates the identification of piping in:
Section 1910.144 says that red shall be the basic color for fire protection equipment and apparatus, such as sprinkler piping. If the employer applies color to fire protection piping for identification, it must be red.
For more on safety colors, see the American National Standards Institute (ANSI) A13.1-1956, Scheme for the Identification of Piping Systems, referenced at 1910.253(d)(4)(ii), 1910.261(a)(3)(ii), and 1910.262(c)(7). Therefore, where the ANSI 1956 references apply, the employer must follow the 1956 edition of ANSI A13.1.
However, if ANSI A13.1-1956 does not apply and no state laws or regulations call for pipe marking, then the employer may wish to use pipe markings in accordance with a more modern standard — American Society of Mechanical Engineers (ASME) A13.1-2020, Scheme for the Identification of Piping Systems, which has a different color scheme than the 1956 edition.
Pipe marking elements, format, color schemes, and location
- Requirements and best practices for pipe markings include their necessary elements, format and color schemes, and placement.
- The ASME standard uses color coding to signal what type of material a pipe contains.
Pipe marking elements
Pipe markings offer the following elements:
- The legend or wording is the primary means by which the employee can identify pipe contents.
- The legend may use the full name of the material or an abbreviation.
- Adding Globally Harmonized System (GHS) product identifier, pictogram(s), signal word, and/or hazard statements is optional.
- For abandoned pipes, the legend should mention any pressurized fluid or residual materials remaining in the piping.
- Arrows accompany the legend to indicate the directional flow of the contents.
- Other indicators, such as temperature or pressure, add further hazard information as needed.
Pipe marking format and color schemes
For readability, American Society of Mechanical Engineers (ASME) A13.1-2020 calls for the legend to use a readable font type, such as but not limited to Sans Serif Gothic Bold. Readable letter sizes are specified in the ASME standard based on the pipe diameter. Font sizes smaller than one-half inch are not recommended.
ASME A13.1-2020 uses a color code to designate whether a material is combustible, flammable, oxidizing, toxic, or corrosive or whether it is compressed air, water, a fire quencher, or other material type. The voluntary standard suggests pipes be colored as follows:
Material type | Color of letters | Color of background |
---|
Compressed air | White | Blue |
Water (potable, boiler, or cooling) | White | Green |
Combustible fluid | White | Brown |
Flammable | Black | Yellow |
Oxidizing fluid | Black | Yellow |
Toxic fluid | Black | Orange |
Corrosive fluid | Black | Orange |
Fire quencher (CO2, foam, or water) | White | Red |
Abandoned piping | Black | White with a black border |
Other materials as determined by facility | White | Purple, gray, or black |
Other materials as determined by facility | Black | White |
Pipe marking locations
The Occupational Safety and Health Administration (OSHA) has no requirements for the interval at which to apply pipe markers, except where the agency references the older ANSI standard from 1956. However, facility owners and operators may wish to check with state and local authorities for any applicable pipe marking requirements.
Non-mandatory ASME A13.1-2020 recommends that pipe markers be applied at intervals “sufficient for identification.” The standard adds that markings should be placed where pipes bend, divide, or pass through surfaces. Markings are also recommended near flanges/valves.
Permanent floor markings and floor signs
- Floor markings and floor signs are two types of markings that are found directly on the surface of and parallel to the floor.
- Both OSHA and ANSI have standards related to floor markings and floor signs.
Two types of markings may be found directly on the surface of and parallel to the floor:
- Floor markings are slip-resistant paint, tape, or other coating media applied to, adhered to, or integral with the floor. The markings can be a solid color, angled bars of alternating color, a checkerboard of alternating color, a geometric combination of colors, or a photoluminescent application.
- Floor signs are non-required slip-resistant signs or decals that are adhered to or painted on the floor.
Both types of markings have applications in the workplace. However, neither floor markings or floor signs replace signs, training, guarding, or protection required by the Occupational Safety and Health Administration (OSHA).
Purpose
Floor markings or floor signs are often used to indicate an area designated as a/an:
- Egress route;
- Safety zone, such as a pedestrian-only aisle;
- Hazard, such as a change in elevation like a stair, a loading dock edge, or an uneven sidewalk surface;
- Restricted area meant only for authorized employees;
- Clearance area, such as in front of fire extinguishers, eyewash stations, or live electrical parts;
- Location for a particular type of storage, piece of equipment, or work activity, such as an aisle designated for powered industrial truck traffic only; or
- Location where employees or customers are recommended to stand.
Related regulations and standards
OSHA has regulations that relate to floor markings and floor signs, including, but not limited to:
The American National Standards Institute (ANSI) also has standards that relate to floor markings and floor signs:
- ANSI Z535.1-1998, American National Standard Safety Color Code, which offers safety color definitions that give examples of the hazard or message identified by each color.
- ANSI Z535.1-2011, American National Standard for Safety Colors, which does not offer color definitions but does specify the latest safety colors incorporated by reference by OSHA.
- ANSI Z535.1-2017, American National Standard for Safety Colors, which does not offer color definitions but does specify the latest safety colors recommended by ANSI (not OSHA).
- ANSI Z535.1-2022, American National Standard for Safety Colors, which does not offer color definitions but does specify the latest safety colors recommended by ANSI (not OSHA).
- ANSI Z535.2-2011 — American National Standard for Environmental and Facility Safety Signs, which specifies the latest safety sign formats incorporated by reference by OSHA. While floor signs are not required, a facility may wish to follow the ANSI specifications for sign signal word, message, color, and format, when creating a floor sign.
- ANSI Z535.2-2017 — American National Standard for Environmental and Facility Safety Signs, which specifies the latest safety sign formats recommended by ANSI (not OSHA). While floor signs are not required, a facility may wish to follow the ANSI specifications for sign signal word, message, color, and format, when creating a floor sign.
Note: It is important to check state and local fire and building codes to see if any floor marking requirements are specified. For example, many states adopt National Fire Protection Association (NFPA) 101, Life Safety Code. The 2009 and later editions of NFPA 101 call for the marking of the top and bottom stair (on their tread nosing) with safety yellow if the riser is inconsistent with the other risers in the flight by over 3/8 inch.
Formats, color schemes, materials, construction, and locations
- Floor markings come in a variety of color schemes, while floor signs are configured in a variety of shapes.
- Floor markings and floor signs are vulnerable to employee and equipment traffic and should be chosen for durability but are not suitable for some locations for this reason.
Formats and color schemes
Floor markings are applied in a solid color, angled bars of alternating color, a checkerboard of alternating color, a geometric combination of colors, or a photoluminescent application. Color selection of these markings often contrasts with the floor color and may depend on Occupational Safety and Health Administration (OSHA) 29 CFR 1910.144, American National Standards Institute (ANSI) Z535.1-1998, ANSI Z535.1-2011, ANSI Z535.1-2017, ANSI Z535.1-2022, and/or other applicable international, U.S., state, or local codes.
Floor signs are often configured in a circular or oval format or a rectangle with rounded corners, so the panels of the sign may be oriented differently than an ordinary safety sign. Floor signs are not required, but the employer may wish to follow the color schemes applied to regular safety signs per 1910.145, 1926.200, ANSI Z535.2-2011, and ANSI Z535.2-2017.
Materials and construction
While floor markings and floor signs are intended to be permanent, the downside is that they may deteriorate due to employee and equipment traffic. That means floor marking and floor sign media should be selected for durability.
Some floor signs come not only with a durable substrate but also an overlaminate, making it a two-step application for extra protection. The employer should look for floor signs with a simple outer shape, such as a circle or oval or a square or rectangle with rounded corners. Finally, floor signs should be maintained as instructed and as needed.
Locations
Floor markings are often located:
- Around repair, service, and assembly pits less than 10 feet in depth, as required by OSHA 29 CFR 1910.28;
- At the perimeter or edge of a defined area, such as a permanent aisle/passageway or work area;
- Solidly throughout an entire defined area; or
- In angled bars of color across a defined area.
Floor signs, on the other hand, are often placed on the floor:
- In front of hazardous equipment, such as electrical panels;
- At approaches to hazardous or regulated areas, such as areas where:
- Personal protective equipment (PPE) is required,
- Smoking is prohibited,
- Forklift traffic is possible, or
- Chemicals are stored;
- At approaches where admittance is restricted or permitted for authorized personnel only;
- In front of fire equipment, such as:
- Fire extinguishers,
- Fire hoses, and
- Fire alarms;
- In front of safety equipment stations, such as those for:
- First aid supplies,
- Defibrillators,
- Eyewashes,
- Spill response,
- PPE supplies,
- Lockout/tagout, or
- Safety data sheets;
- In front of waste disposal stations;
- To demarcate pedestrian aisles;
- Where employees or others are required or recommended to stand; and
- In areas where safety or policy reminders may reinforce training and signs.
Floor markings and floor signs may be infeasible or impractical in certain work settings, such as on dirt floors and floors having continuous concentrations of sand or dust, like foundries. Other marking methods, such as pillar markings, flags, traffic cones, barrels, and signs, may be an appropriate alternative to floor markings and floor signs if employees are trained to recognize them.
Portable floor stand signs
- A portable floor stand sign is intended for temporary hazards.
Portable floor stand signs are often seen in restrooms and in retail and restaurant establishments. These are a type of accident prevention sign that is intended for temporary hazards. It is common practice for establishments to place portable floor stand signs on both ends of or in a triangle configuration around a hazard, as a means to keep people from entering the hazard area. In some cases, portable floor stand signs are placed just before a blind corner or in the doorway to warn people of the oncoming hazard.
However, it should be noted that according to the Occupational Safety and Health Administration (OSHA) regulation 29 CFR 1910.22
- (a) Surface conditions. The employer must ensure:
- (1) All places of employment, passageways, storerooms, service rooms, and walking-working surfaces are kept in a clean, orderly, and sanitary condition.
- (2) The floor of each workroom is maintained in a clean and, to the extent feasible, in a dry condition. When wet processes are used, drainage must be maintained and, to the extent feasible, dry standing places, such as false floors, platforms, and mats must be provided.
- (3) Walking-working surfaces are maintained free of hazards such as sharp or protruding objects, loose boards, corrosion, leaks, spills, snow, and ice.
- (b) Loads. The employer must ensure that each walking-working surface can support the maximum intended load for that surface.
- (c) Access and egress. The employer must provide, and ensure each employee uses, a safe means of access and egress to and from walking-working surfaces.
- (d) Inspection, maintenance, and repair. The employer must ensure:
- (1) Walking-working surfaces are inspected, regularly and as necessary, and maintained in a safe condition;
- (2) Hazardous conditions on walking-working surfaces are corrected or repaired before an employee uses the walking-working surface again. If the correction or repair cannot be made immediately, the hazard must be guarded to prevent employees from using the walking-working surface until the hazard is corrected or repaired; and
- (3) When any correction or repair involves the structural integrity of the walking-working surface, a qualified person performs or supervises the correction or repair.
The agency explains that taking immediate corrective action or guarding the floor hazard is important for the safety of employees; delaying either action can put employees at risk of injury or death. OSHA notes that corrective action may include removal of the hazard.
However, when employers cannot fix the hazard immediately and need to guard the hazard area, the regulation gives employers flexibility in selecting the type of guarding to use (e.g., erecting barricades, demarcating no-entry zones). OSHA does not specifically mention portable floor signs as an example of a type of guarding. Whatever method employers use for guarding, they must ensure it is effective in preventing employees from accessing or using the surface.
Barricade tape, also known as caution tape
- Barricade tape is used to block off and signal the presence of a temporary or unexpected hazard or condition.
Barricade tape is a non-adhesive strip of polyethylene, vinyl, or other material positioned to block employees and others and alert them to a temporary or unexpected hazard or condition.
Purpose
Barricade tape is used to restrict access to and/or prevent accidental injury or illness from:
- A temporary hazardous or potentially hazardous condition; or
- Equipment or operations that are:
- Defective
- Out of the ordinary
- Unexpected
- Not readily apparent
Related regulations and standards
The Occupational Safety and Health Administration (OSHA) has regulations that relate to barricade tape:
- 1910.109(e)(1)(iv),Table H-22, (i)(5)(ii)(c)
- 1910.265(d)(3) and (e)(5)(iii)
- 1910.268(j)(4)(iii)
- 1910.269(o)(2)(iii), (p)(4)(iii), (q)(3)(xii), (w)(6)(iii)-(iv), and (x)
- 1926.151(d)(7)
- 1926.252(b)
- 1926.451(h)(2)(i)
- 1926.501(b)(7), (b)(10), (c)(3)
- 1926.600(a)(1)
- 1926.651(f), (j)(1)
- 1926.800(b)(3), (o)(2)
- 1926.850(h)
- 1926.855(f)
- 1926.900(i)
- 1926.959(d)(3)(iii)(D)
- 1926.963(c)(3)(ii)
- 1926.964(c)(11)
- 1926.967(g)(3)-(4)
- 1926.968
- 1926.1053(b)(8)
- 1926.1202
- 1926.1203(e)(2)(ii)
- 1926.1204(c)(6), (d)(6)
- 1926.1407(b)(3)(v)
- 1926.1408(b)(3)
- 1926.1410(d)(3), (d)(8)
- 1926.1417(e)(1)(iv)
- 1926.1437(n)(5)(ii)
The American National Standards Institute (ANSI) also has standards that relate:
- ANSI Z535.5-2011, American National Standard for Safety Tags and Barricade Tapes (for Temporary Hazards), which is adopted by OSHA 1926.200.
- ANSI Z535.5-2017, American National Standard for Safety Tags and Barricade Tapes (for Temporary Hazards), which is the latest ANSI standard on barricade tape but is not adopted by OSHA.
- ANSI Z535.5-2022, American National Standard for Safety Tags and Barricade Tapes (for Temporary Hazards), which is the latest ANSI standard on barricade tape but is not adopted by OSHA.
Barricade tape elements, format, color schemes, materials, location, and attachment
- The primary elements of a barricade tape are its signal word and message panels.
The Occupational Safety and Health Administration (OSHA) does not specify the elements of barricade tape for general industry or shipyards. That means these industries have some flexibility.
However, for construction, OSHA 29 CFR 1926.200 adopts American National Standards Institute (ANSI) Z535.5-2011. That ANSI standard explains that barricade tape must contain the signal word and message panels. The safety symbol panel is optional.
Signal word panel
The signal word panel includes the signal word, along with the safety alert symbol (when used). The signal word refers to the part of a barricade tape that contains the word or words, like DANGER or CAUTION, intended to capture the employee’s immediate attention. ANSI provides specifications for signal words:
- DANGER — Used only in major hazard situations where an immediate hazard presents a threat of death or serious injury to employees.
- WARNING — May be used to represent a hazard level between CAUTION and DANGER, where serious injury or even death “could” occur.
- CAUTION — Used only in minor hazard situations where a non-immediate hazard, potential hazard, or unsafe practice presents a lesser threat of employee injury.
- NOTICE — Indicates non-hazard information that is important, like property damage.
- SAFETY INSTRUCTIONS — Indicates procedures related to safety. Instead of the phrase SAFETY INSTRUCTIONS, more descriptive signal words may be used, such as LOCKOUT PROCEDURE.
When used in the signal word panel, the safety alert symbol — an exclamation point inside an equilateral triangle — is provided with DANGER, WARNING, and CAUTION signal words to indicate a hazard. It is not applied on NOTICE or SAFETY INSTRUCTION tape.
Message panel
The message panel contains the major message. This message indicates, in word text, the relevant hazardous condition or the instruction that needs to be communicated to the employee. Messages communicate hazards, the consequences of ignoring hazards, prohibitions, mandatory actions, and other information.
The message should be concise and easy for employees to understand. Examples include:
- “Construction Area”
- “Open Trench”
- “Do Not Cross"
- “Keep Out!”
It should be noted that both OSHA and ANSI allow the employer to use a symbol panel instead of a message panel on a barricade tape.
Safety symbol panel
The safety symbol panel contains a safety symbol(s). This panel offers a pictorial representation used to identify the hazardous condition, convey the safety instruction, or otherwise clarify or supplement the message. Symbols often capture the employees’ attention and help sidestep language barriers.
A symbol panel may also substitute for the message panel or for a portion of the word message.
General format
The format of barricade tape is laid out from left to right, with the signal word panel followed by the safety symbol panel (if used), and then the message panel (if used). Angled striping is popular but optional. The back side can be identical or left blank. Multi-language options are also offered by ANSI.
Signal word panel format and color scheme
When the safety alert symbol is used, ANSI says it should be at least the same height of the signal word (or greater) and located just to the left of the signal word. Its color scheme varies depending on the signal word.
ANSI color scheme requirements for signal word panels are detailed. Here is a summary:
- DANGER – Red with lettering in white.
- WARNING — Orange with lettering in black.
- CAUTION — Yellow with lettering in black.
- NOTICE — Blue with lettering in white.
- SAFETY INSTRUCTIONS— Green with lettering in white
ANSI uses a formula to calculate the minimum recommended height of the signal word letters (the variables are in inches): Height = Distance/150
Message panel format and color scheme
Neither OSHA nor ANSI specifies a color scheme for the message panel on barricade tape, but the color scheme may naturally follow the same color scheme used for the signal word panel.
ANSI also suggests using the headline-style, sans serif font, and initial capitalization (e.g., Do Not Cross). All caps may be used for important words and shorter phrases. Also, left justification is generally recommended.
Font size must be legible from the reading distance, and ANSI offers suggested sizes. ANSI uses a formula to calculate the minimum recommended height of the message panel letters (the variables are in inches): Height = Distance/300.
However, ANSI also offers a table of recommended letter heights, which uses slightly different heights than the formula. A larger size is suggested where lighting or other conditions are poor for reading.
Materials
Despite its name, barricade tape is not adhesive. Rather, it is made of a non-adhesive strip of vinyl, polyethylene, or other material. Neither OSHA nor ANSI specify tape dimensions or thickness.
Location and attachment
Barricade tape is positioned to block employees or others and alert them to a temporary or unexpected hazard or condition. The employee should see it in time to take precautions. Barricade tape itself cannot pose a hazard or distraction, however.
Neither OSHA nor ANSI specify the means of attaching barricade tape to a scene, but typically the tape is tied to objects to form a line or perimeter. Some barricade tape even comes with a stand, wall-mounting, or dispenser that allows the tape to be drawn out and then retracted when no longer needed.
Other marking systems
- It’s important to be aware of other available marking systems other than signs, tags, and labels.
- These other systems may be required by federal, state, or local laws and regulations. If not required, they may be a better fit for the intended application.
Signs, tags, and labels are part of a larger family of safety marking systems intended to communicate with employees and the public. While much attention is focused on signs, tags, labels, pipe markings, and barricade tape specified by standards from the Occupational Safety and Health Administration (OSHA), American National Standards Institute (ANSI), and American Society of Mechanical Engineers (ASME), it’s important to be aware of other available marking systems. In some cases, these other systems may be required by federal, state, or local laws and regulations.
Where marking systems are not required, employers should consider whether these other marking systems may be a better fit for the intended application. Other marking systems could also be used in addition to OSHA, ANSI, and ASME signs, tags, labels, pipe markings, and barricade tape.
Listed below are some marking systems to consider. There may be others not listed here:
- ADAAG, Americans with Disabilities Act Accessibility Guidelines for Buildings and Facilities. See 36 CFR 1191 Appendices.
- API Recommended Practice 1109, Line Markers and Signage for Hazardous Liquid Pipelines and Facilities.
- Compressed Gas Association (CGA) consensus standards.
- Department of Defense Fire Division Symbols for Explosives.
- Department of Transportation standards for hazardous materials packaging labels, placards, and markings. See 49 CFR 171 to 180.
- Department of Transportation standards for vehicle markings. See 49 CFR 390.21T, 393.13, and 571.108.
- Environmental Protection Agency waste labels/markings. See 40 CFR 262, 273, and 279 and state environmental laws/regulations.
- Food and Drug Administration standards for medical equipment. See 21 CFR.
- International Fire Code (IFC).
- ISO standards, such as the ISO 3864 series, Graphical Symbols - Safety Colours and Safety Signs, and ISO 7010, Graphical Symbols - Safety Colours and Safety Signs – Registered Safety Sign.
- Labor law posters and postings.
- Manual on Uniform Traffic Control Devices for Streets and Highways (MUTCD).
- Mine Safety and Health Administration (MSHA) standards for surface and underground mines. See 30 CFR.
- Permits for confined spaces or hot work.
- Pesticide application posting, which may be a possible state requirement.
- Safety posters.
- Underground utility line marking. See 29 CFR 1926.651. Also see the Uniform Color Code from the American Public Works Association.
- Warning line systems. See 29 CFR 1926.502.
State requirements for accident prevention signs and tags
- The chart compares state requirements for safety signs and tags to federal OSHA 29 CFR 1910.145.
Each state manages safety signs and tags differently. This Signs, Tags, and Marking State Comparison chart can be used to determine if additional requirements apply to an operation.
Federal regulations
State comparison
Click this link to see the latest state comparison chart.