Maintenance records
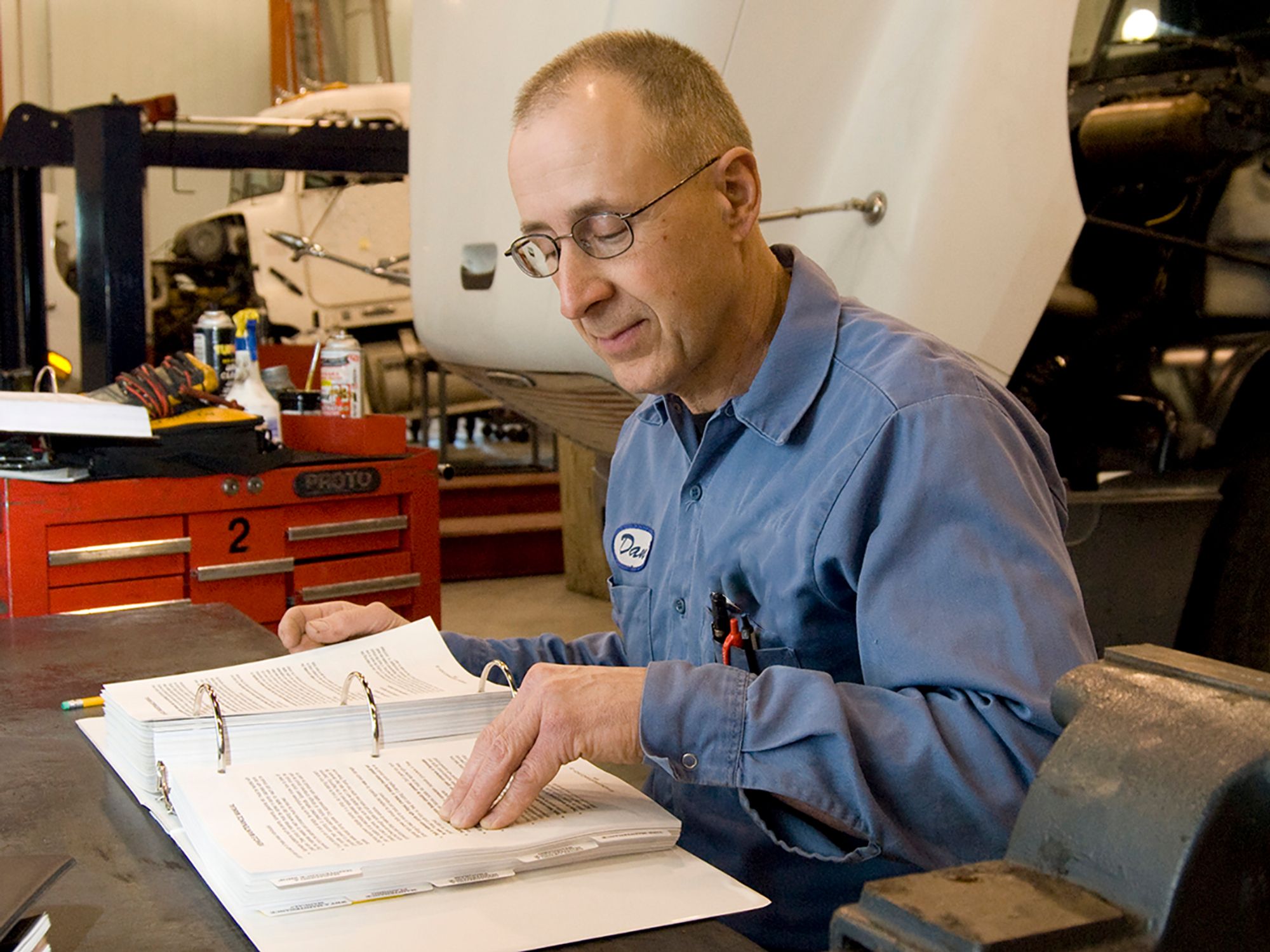
One key point about recordkeeping: As far as your internal tracking and the FMCSA are concerned, if you didn’t document it, it didn’t happen. This lack of documentation can create several problems. First, you will not have records to make sound decisions in the future. Second, you may end up fined for not complying with the regulations, even though the only regulations you are not complying with are the recordkeeping requirements. Finally, as mentioned earlier, if you do not have records showing what inspection, maintenance, and repairs were done on a vehicle, as far as investigators, attorneys, and courts are concerned, you did not maintain or repair your vehicle. The documentation that shows what was done in the shop is the repair order, or RO.
Roadside inspection reports are also a key component to your recordkeeping program. The reports from all roadside inspections must be retained for one year. There are two reasons why retaining them is important. First, the obvious: FMCSA requires that they be filed and retained for one year. Second, they provide a database of discovered issues that should be used for quality improvement.
Also, auditors use roadside inspection reports as a means to verify that repairs are being completed when they are necessary. During an audit, the auditor will request a record, receipt, or RO showing that any mechanical violation listed on a roadside inspection report was repaired. This is especially true of any out-of-service violations discovered during roadside inspections. To counter this, be sure that repairs conducted following a roadside inspection are documented (preferably on an RO) and that you can locate your ROs (or other record if an RO was not completed) based on vehicle and date.
There other compliance issues to consider when it comes to recordkeeping, and they are the prohibition of coercion rule and the whistleblowers protections.
Under the prohibition of coercion rule, no one can threaten a driver with future employment action in an attempt to get the driver to operate in violation of the safety regulations. If a driver complains about the condition of the vehicle (in writing or verbally), and someone threatens the driver in an effort to get him/her to drive it in an unacceptable condition (such as “drive it or you’re fired”), coercion has occurred. Having records that show that you accepted the complaint, acted on it, determined there was nothing wrong with the vehicle, and informed the driver of this finding will be critical if the driver later claims that he/she was threatened or forced to drive an unsafe vehicle. Of course, if the driver’s complaint has merit the correct action is to immediately make the necessary repairs.
As far as the whistleblower protections, any employee (technician, driver, dispatcher, etc.) has the right to bring a safety concern to the company without fear of repercussions. Also, the employee has the right to bring the concerns to DOT or OSHA or answer questions from one of these agencies, without fear of repercussions. Where the situation becomes a violation of the whistleblower protections is if you take employment action against the employee for bringing safety concerns to you, DOT, or OSHA. If a driver is able to show safety concerns were brought to you (such as the driver turned in a DVIR listing safety-related defects) and you failed to act on them (or it appears you failed to act on them due to a lack of documentation), and the company later took action against the driver for raising the concerns, you could be in serious trouble.
An example would be a driver complaining about the truck constantly “pulling” to the right. If a technician checked the tires, suspension, and alignment, and took the truck on a check-ride, but did not complete an RO for the inspection because he “really didn’t do anything,” you have no proof that the complaint was addressed. In other words, you do not have any proof that the vehicle was actually safe to operate. In this case, the driver could claim later that he/she was coerced into operating an unsafe vehicle, or if employment action was taken against him/her the driver could claim that it was tied to the vehicle complaint and his/her unwillingness to drive an unsafe vehicle. The proof that you addressed the driver’s safety concerns in such cases should be on the associated ROs.
A side note on whistleblowers and drivers filing coercion complaints. If you determine who the individual is, you cannot take adverse action against him or her due to the complaint. To do so can trigger serious consequences for the company, and potentially the supervisors and managers involved.
To sum this up, a good RO and RO system (some carriers and shops refer to this documentation as a “work order”) provides a detailed and accessible history of the vehicles and all work done to them.
Basic information. You expect the RO to identify the vehicle, the date, mileage at the time of repair, the reason for repair, the parts used, who performed the repair, and the cost. This information is called historical data; it is simply a collection of maintenance facts.
RO forms vary in complexity. The number of people who handle the RO is small in a little shop, but as the shop grows, the maintenance department may need a repair order with more detail. In the first repair order example (small shop) the “instructions” section of the RO is meant to be completed in writing by the person issuing the RO and read by the technician, supervisor of an outside shop, etc. It’s possible, though, for the reader to misunderstand the orders if they aren’t written clearly. There may not be too many choices for reason for repair (“Other” can invite a variety of definitions for the same thing).
Another problem with this type of RO is the maintenance manager has to go through lots of lines of handwritten material to figure out what’s going on in the shop!
To get a clear picture of your operation, you should be able to take the ROs for a single unit from the past year or so, and make some conclusions about your maintenance plan. Try not only to look at maintenance facts or historical data, but how the information categories can help you spot potential problems.
The RO should be a treasure chest of facts, but they are of little use until you put them to work.