Job hazard analysis/job safety analysis
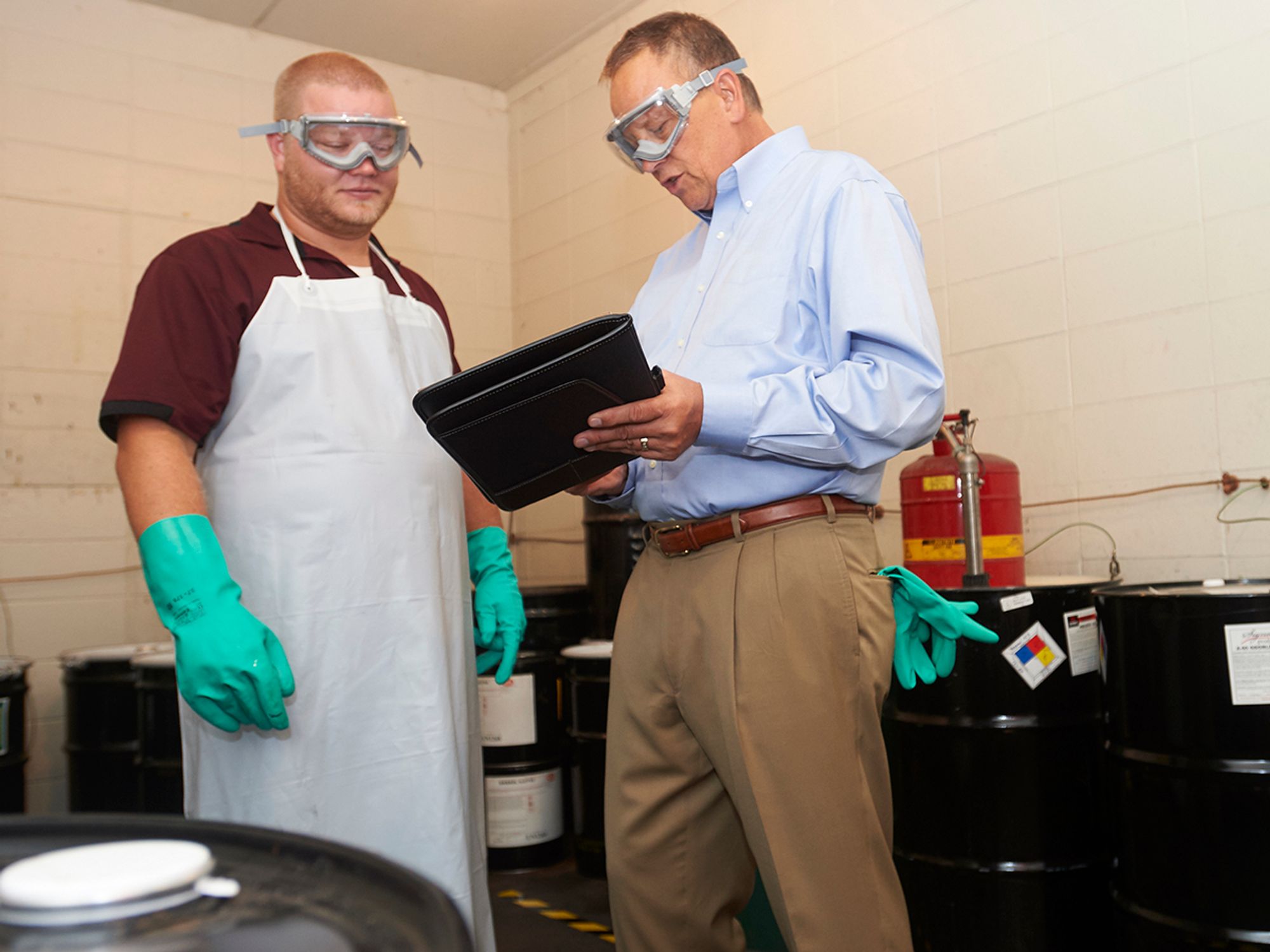
- JHA/JSA is an important component of a safety and health program.
The terms job hazard analysis (JHA) and job safety analysis (JSA) are different ways of describing the same process. That process involves breaking down a job into its smaller steps, identifying hazards, and implementing controls. No matter what the process is called, it is an important component of a safety and health program.
1. Analyze the “job”
- Priority is given to certain jobs regarding job hazard analysis.
Regarding a job hazard analysis, “job” means tasks or steps, such as chocking a trailer, changing a light bulb, or grinding a part. It does not refer to a job title or occupation, such as “warehouse worker” or “welder.” Ideally, all jobs at a workplace will be subjected to analysis at some point. The reality, however, is that there simply isn’t enough manpower in most organizations to perform job hazard analysis (JHA) on all jobs at once. For this reason, priority should be given to the following:
- Jobs with high number of incidents or near misses;
- Jobs with high number of employee complaints (e.g., heat, fatigue);
- Dangerous jobs (e.g., those under a permit);
- New jobs; and
- Jobs that have changed (e.g., new process, new equipment, new workers).
2. Break job down into steps
- Analyze each job by breaking it down into steps in order of typical sequence.
Once each job has been prioritized, the next step is to analyze each job by breaking it down into steps in order of typical sequence. It is advisable to work with the operator or employee(s) performing the job. They have a unique understanding of the job, and this knowledge is invaluable for finding hazards. Many employers will try to do the job hazard analysis (JHA) by simply observing the worker doing the job as normal, rather than working with the operator to work through the job. Record each step as the worker takes it. Be sure to record enough information to describe each job action without getting overly detailed. A good rule of thumb is 10 steps per job.
Avoid making the breakdown of steps so detailed that it becomes unnecessarily long or so broad that it does not include basic steps. Use action words (e.g., “lift,” “turn,” “pull”) and object words (e.g., “handle,” “lever”) to describe how tasks are being performed. It may be valuable to get input from other workers who have performed the same job. Later, review the job steps with the employee to make sure nothing has been omitted. Point out that the company is evaluating the job itself, not the employee’s job performance. It may be helpful to photograph or videotape the worker performing the job. These visual records can be handy references when doing a more detailed analysis of the work.
3. Analyze the hazards
- Identify hazards for each step once all the steps have been identified.
Once all the steps have been identified, then the hazards for each step must be identified. Focus on anything that could potentially cause harm. Along with the hazards, determine the outcome that would occur should an employee be exposed to the hazard (consequence). For example, what could happen if an employee’s hand encountered an unguarded pulley? This will help determine severity and probability when selecting hazard controls.
4. Implement controls
- Use a hierarchy of hazard controls.
Information obtained from a job hazard analysis (JHA) is useless unless hazard control measures recommended in the analysis are incorporated into the tasks. Managers should recognize that not all hazard controls are equal. Some are more effective than others at reducing the risk. A hierarchy of controls should be used as follows:
- Elimination (e.g., using an abrasive material instead of a hazardous chemical)
- Substitution (e.g., using a less toxic chemical instead of a hazardous one)
- Engineering controls
- Administrative controls
- Personal Protective Equipment
Often a combination of controls will be needed; also, interim controls may be used until a better and more permanent control can be implemented.
5. After finishing
- Periodically review the JHA to ensure that it remains current and continues to help reduce workplace accidents and injuries.
After the necessary controls have been implemented, it’s important to periodically review the job hazard analysis to ensure that it remains current and continues to help reduce workplace accidents and injuries. Even if the job has not changed, it is possible that during the review process the company will identify hazards that were not identified in the initial analysis. It is particularly important to review the job hazard analysis if an illness or injury occurs on a specific job.
Based on the circumstances, the company may determine that the job procedure may need to change to prevent similar incidents in the future. If an employee’s failure to follow proper job procedures results in a “near miss,” discuss the situation with all employees who perform the job and remind them of proper procedures. Any time a job hazard analysis is revised, it is important to train all employees affected by the changes in the new job methods, procedures, or protective measures adopted.
Remember, a job hazard analysis (JHA) is one component of the larger commitment of a safety and health management system.