Inspection and safety practices
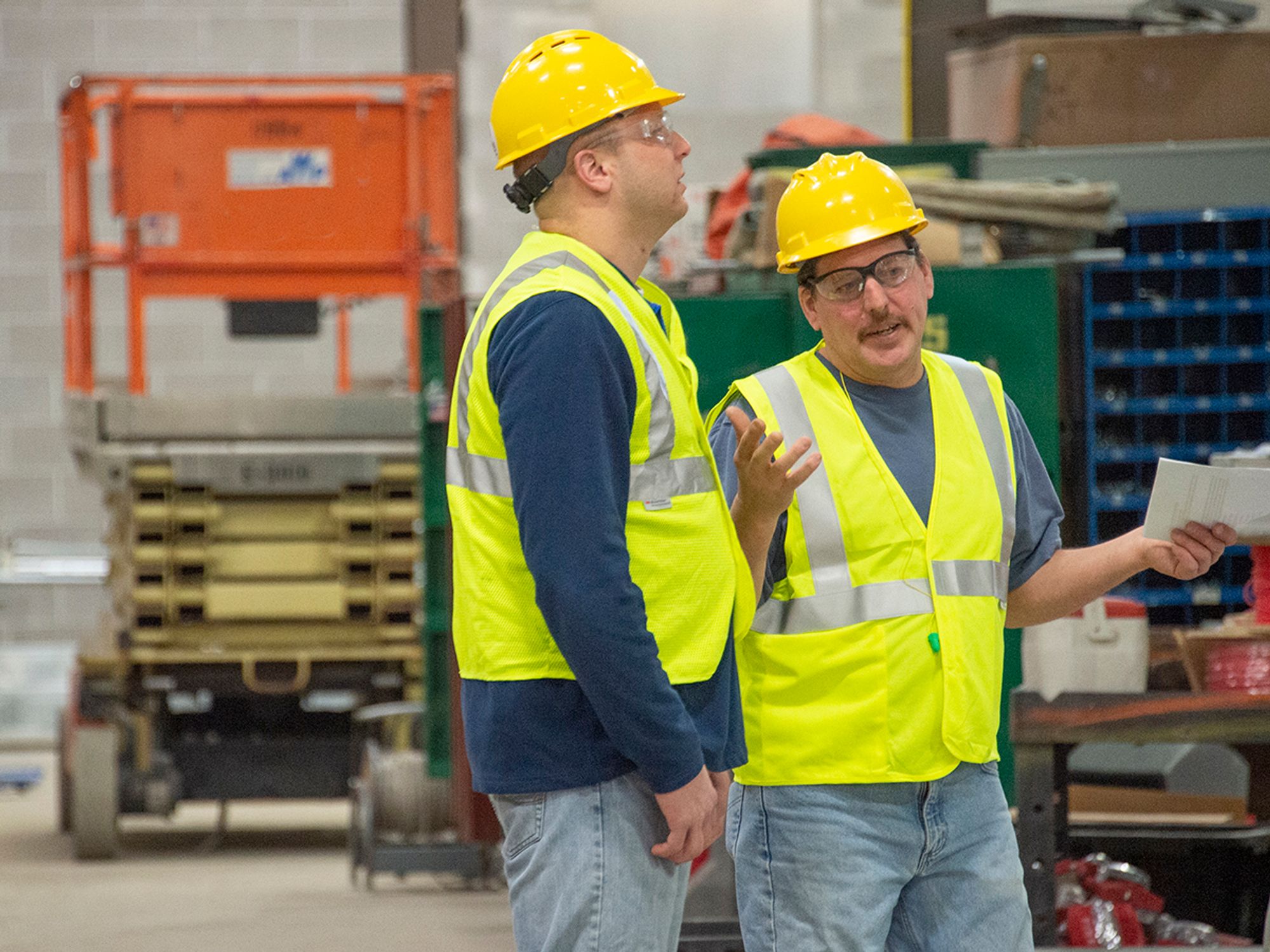
- Inspection and safety practices for aerial lifts apply to scissor lifts as well.
- Manufacturers’ maintenance and inspection instructions should be followed, generally including testing and inspecting controls and components, checking guardrails, and testing brakes.
Prior to each work shift, workers should conduct a pre-start inspection to verify that the equipment and all its components are in safe operating condition. The inspection should follow manufacturer recommendations and include a check of/for:
|
|
If any component is defective, a scissor lift must not be operated until it is repaired by a qualified person. Remove defective scissor lifts from service (tagged out) until repairs are made.
Work zone inspection
Employers must ensure that work zones are inspected for hazards and take corrective actions to eliminate such hazards before and during operation of a scissor lift. Items to look for include:
- Drop-offs, holes, or unstable surfaces such as loose dirt;
- Inadequate ceiling heights;
- Slopes, ditches, or bumps;
- Debris and floor obstructions;
- Overhead electric power lines and communication cables;
- Other overhead obstructions;
- Other hazardous locations and atmospheres;
- High wind and other severe weather conditions, such as ice; and
- The presence of others in close proximity to the work.
Maintenance
Employers must regularly maintain scissor lifts to ensure that they are safe to use (e.g., that the lifting mechanism will not collapse).
Manufacturers’ maintenance and inspection instructions should be followed. These will generally include how to:
- Test and inspect controls and components before each use;
- Ensure that guardrail systems are in good working condition; and
- Verify that brakes, once set, will hold the scissor lift in position.