Fluid sampling and testing
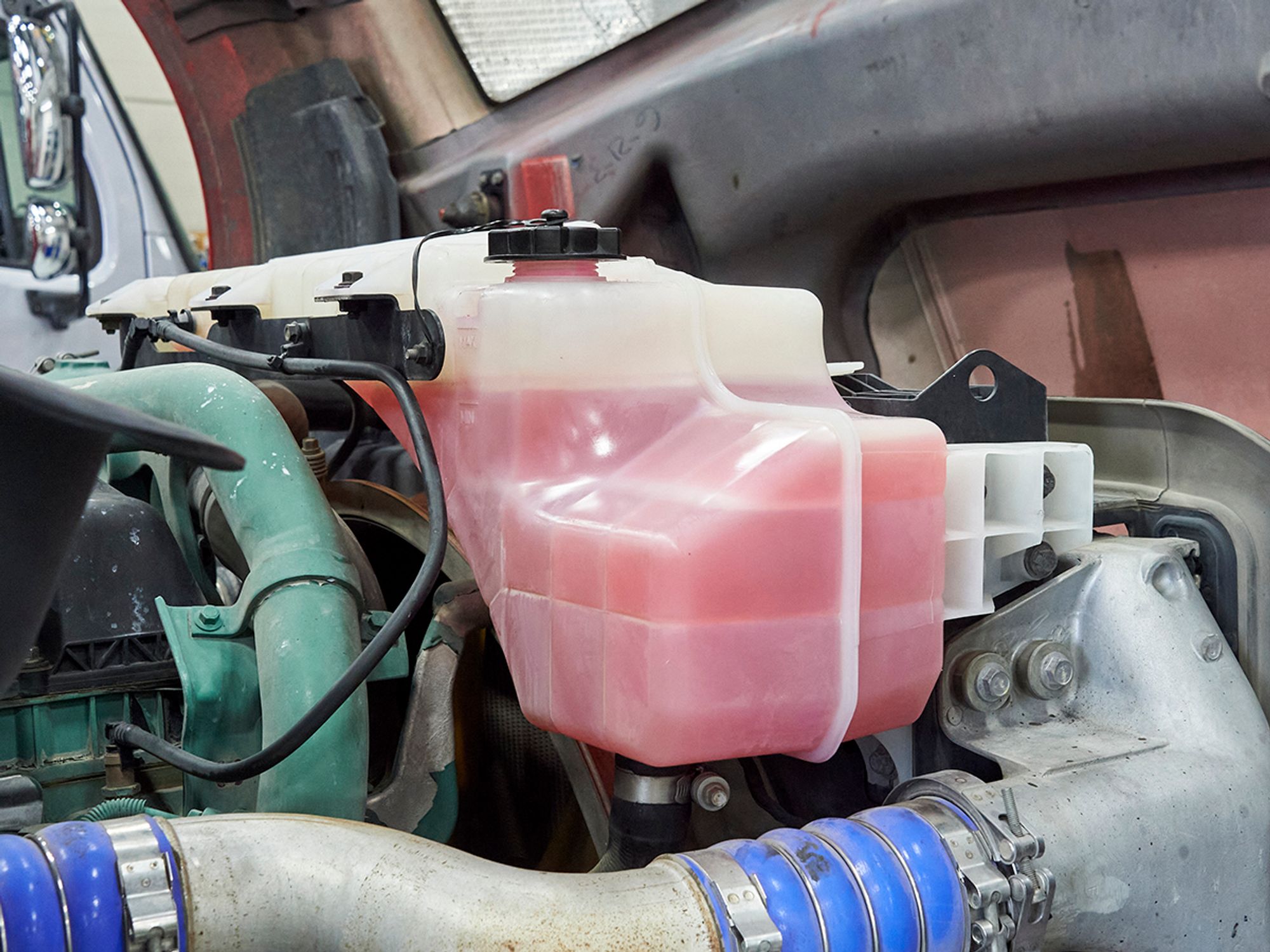
- Fluid sampling and testing can provide the maintenance manager with a “wear limit” method of analyzing the internal condition of a component.
- Sampling and testing of oil, transmission, differential, and auxiliary hydraulic systems (wet kits) are all examples of components where sampling and testing can indicate problems in advance of failure.
- Many carriers combine sampling and testing with analysis of MTBF and ECLS data.
Fluid sampling and testing can provide the maintenance manager with a “wear limit” method of analyzing the internal condition of a component. A prime example is the engine.
By simply looking at an engine the maintenance manager cannot tell the condition of the internal parts. A mean time between failures (MTBF) study can determine when most of the engines will fail. But with engine rebuilds being an expensive repair, doing a rebuild simply based on MTBF and expected component life cycle (ECLS) data could lead to unnecessary and costly maintenance.
Taking an oil sample, and having it tested, can give the maintenance manager a look inside the engine:
- If antifreeze is appearing in the oil, that can indicate a head gasket is leaking.
- Iron, steel, chromium, or aluminum particles in the oil sample can indicate that the one of the internal components of the engine is beginning to fail.
- The presence of excessive copper (or similar metals) in the oil can indicate that there are bushings or bearings that are beginning to wear.
Sampling and testing other components can also locate problems. Transmissions, differentials, and auxiliary hydraulic systems (wet kits) are all examples of components where sampling and testing can indicate problems in advance of failure.
Testing the fluids in every vehicle component at every service could get costly ($7 to $15 per test). Many carriers are willing to pay this and consider it part of the preventive maintenance (PM) cost of the vehicle. As well as providing early warning of problems, a regular sampling program can help with any warranty claims associated with the component (sampling will show the failure was a sudden failure, not due to neglect over time).
Combining MTBF and ECLS data with sampling
Many carriers that use sampling combine sampling with MTBF and ECLS data. When the vehicle first enters service, samples are only taken at benchmark intervals, such as during quarterly or the annual inspection. Once a vehicle reaches a predetermined threshold, the sampling and testing then become part of all regular inspections. Here is an example of a combination approach:
- Engine — The engine oil will be sampled and tested as part of the annual inspection for the first two years. After the second annual inspection, engine oil sampling and testing will be performed as part of each oil change.
- Transmission — The transmission oil will be sampled and tested as part of the annual inspection for the first five years. After the fifth annual inspection, transmission oil sampling and testing will be performed as part of each oil change.
- Differentials (including interaxle) — The differential oil will be sampled and tested as part of the annual inspection for the first five years. After the fifth annual inspection, differential oil sampling and testing will be performed as part of each oil change.