Documenting preventive maintenance
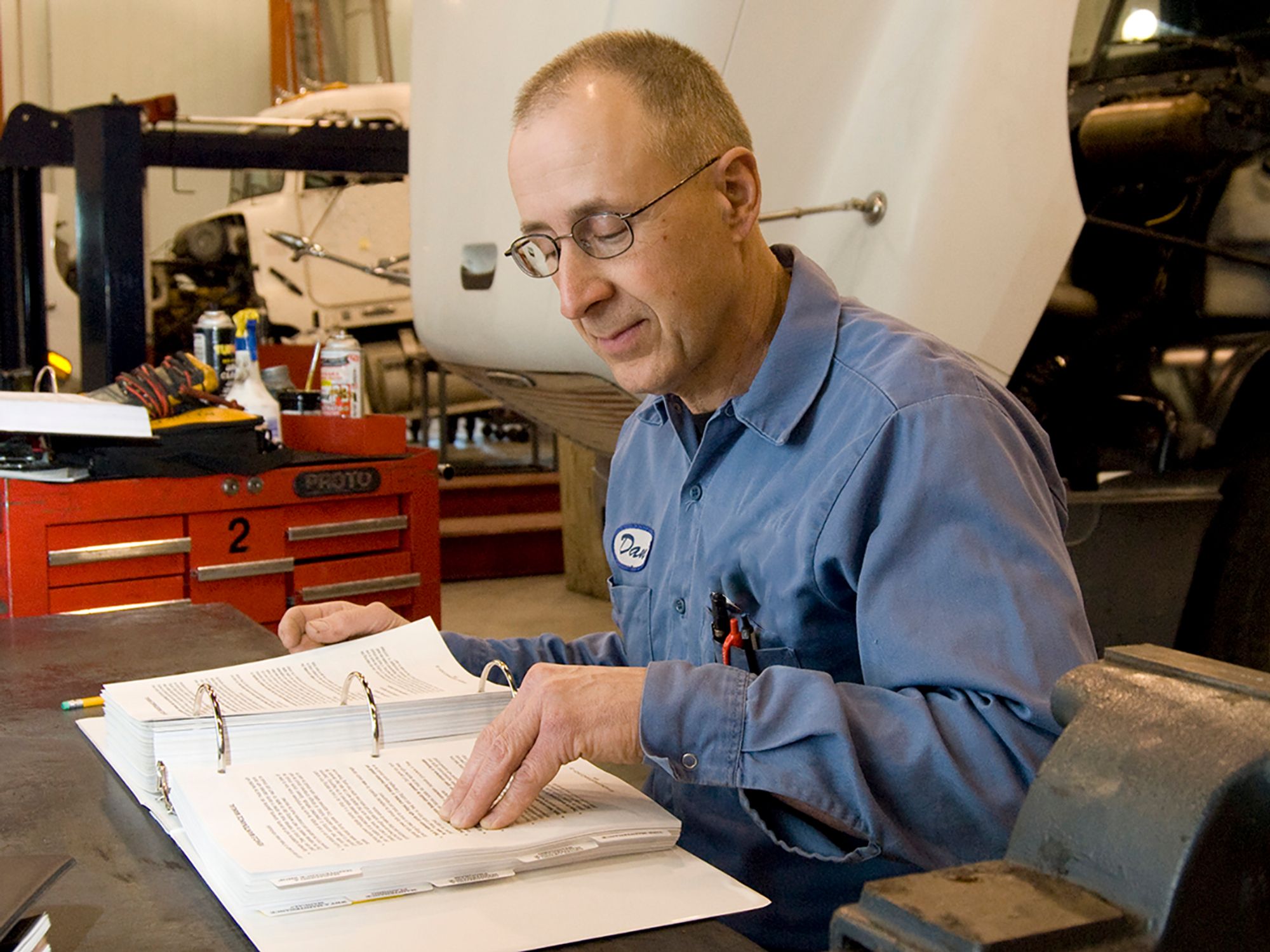
- FMCSA regulations require that a company have a record system that documents the vehicle’s maintenance schedule, and the last and next scheduled service, including both the due date and the nature of the service.
- To set up and document a PM program, the maintenance manager should divide vehicles into “dynamic groups” based on similar traits and maintenance requirements, write a PM schedule for each group, place the schedule in the corresponding vehicle files, keep track of each scheduled PM, and record when the next scheduled PM is due.
The Federal Motor Carrier Safety Administration (FMCSA) regulations require that a company have a record system that shows the vehicle’s maintenance schedule, and the last and next scheduled service (both due date and nature of the service).
The regulations do not spell out how a company is to accomplish this; nor do they provide a “required schedule” or “required form and format” for documentation. The regulations only require that a company have a systematic maintenance program and document it. One reason the FMCSA does not “spell out” a preventive maintenance (PM) schedule that carriers must follow is because of the wide variety of commercial vehicles that are in operation and covered by the regulations. Everything from pickup trucks to motorcoaches to tractor-trailers are covered by the regulations.
Steps by the maintenance manager
To develop and document a PM program, a maintenance manager will need to develop and document the maintenance program for each vehicle (or group of vehicles). This is not as complicated as it sounds.
- First, for PM purposes, and later tracking, the maintenance manager should divide the vehicles in the fleet into “dynamic groups.” Each group should be made up of similar vehicles (based on similar traits and maintenance requirements, not necessarily make and model).
- Next, review the existing information for each group and write a PM schedule (including intervals, checklists, and wears points for important and high-wear components).
- After the schedule for each of the dynamic groups has been established, copy the schedule and place it into the corresponding vehicle files. As well as containing the PM information, the vehicle files must also contain identifying information (vehicle number, make, VIN, year, tire size, and the entity providing the vehicle if it is not owned by the company), and records of all inspections, maintenance, and repairs. This is required by the FMCSA regulations under 396.3.
- Finally, either on a form in the file or physically on the file, keep track of each scheduled PM, and record when the next scheduled maintenance is due.
Some companies go one step further to make the process easier. In addition to the files, they use a wall board that displays the individual vehicles and last/next service. This way, technicians and supervisors can tell immediately when a vehicle received scheduled PM last, and if it is coming due for its next service.