Determining maintenance intervals
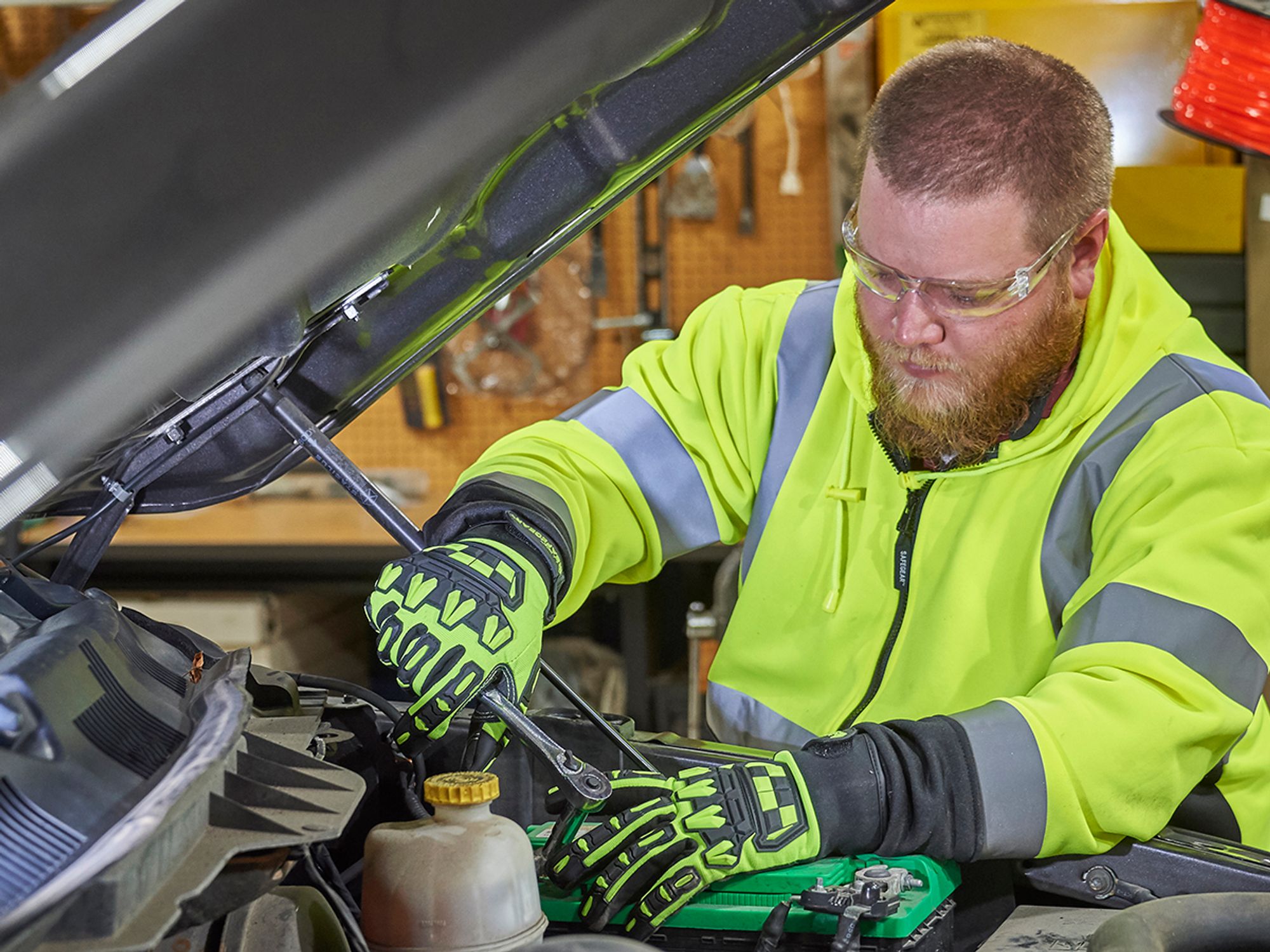
- The three most common methods used for scheduling vehicles for PM are time, miles, and engine hours.
- Important sources of information for determining the actual interval used for PM include OEM recommendations; fleet repair records; input from drivers, technicians, and other shop personnel; and tracking of internal performance measures.
- In scheduling PM, it should be noted that emission system parts, such as diesel particulate filters, selective catalytic reduction systems, and exhaust gas recirculation components all require routine service.
Scheduling methods
The first decision that needs to be made when determining a preventive maintenance (PM) schedule is what method of measurement will be used. There are several methods used to schedule vehicles for PM. The three most common methods are:
- Time — This method is by far the easiest for management but is often the most wasteful as far as technicians’ time, parts, and cost. Scheduling vehicle preventive maintenance based on time means exactly what it says. A vehicle will be scheduled into the shop after a set number of days regardless of mileage or engine hours used since its last PM.
- Miles — Scheduling based on vehicle miles driven is the most common method used for scheduling vehicle PM. A vehicle will be scheduled into the shop after a pre-determined number of miles have been driven. The biggest problem with this method is that scheduling PMs based on mileage does not take into account issues such as severe duty, excessive engine idle time, and power take off (PTO) time (i.e., the transfer of mechanical power of the vehicle’s engine over to another piece of the equipment). To compensate for this, some carriers that schedule PM based on miles driven shorten the mileage interval to compensate for severe duty, excessive idling, or PTO time.
- Engine hours — Scheduling PMs based on engine hours makes sense for vehicles that work hard during every mile, but do not log many miles. Waste trucks, concrete haulers, and gravel trucks are all good examples of vehicles that are typically scheduled for PMs based on engine hours. The reason these trucks are routed into the shop for PMs based on engine hours is because they are constantly working hard — even though the truck may be averaging low miles per hour and miles per day.
The type of vehicles and the type of operation will determine the best type of PM scheduling for an individual company.
Important sources of information
The next step is determining the actual interval. Developing this part of the maintenance program will involve using information from several sources, including:
- The original equipment manufacturers’ (OEM) recommendations for the engine, transmission, and other components are the primary source and most important source of PM information. If the fleet has bought a new vehicle, it’s the only reliable source of information. The fleet should follow the recommendations exactly until its own experience proves otherwise. Fleets can also get information about expected component life from OEMs’ and plan accordingly. Fleets must be careful about deviating from the OEM’s recommendations. If a fleet deviates too far it may lose some, or all, of the warranty on the vehicle or vehicle components.
- Repair records (PM history) are the second source. Even if planning PM for a new vehicle, past maintenance history on similar vehicles that do the same work can provide important clues about how the fleet vehicles have been operating and will help plan the maintenance schedule for the new vehicle.
- Drivers, technicians, and other shop personnel are the third source. Ask these individuals for suggestions. A successful PM program will need the cooperation of everyone. These individuals should help to put the PM program together. Ask for specific ideas about the PM intervals.
- Tracking of internal performance measures can include oil sampling (if oil samples tested following oil changes are indicating oil breakdown, shortening the interval may be necessary), part failure analysis, unscheduled repairs, on-the-road repairs and breakdowns, and out-of-service violations. It does not make any difference how well a PM schedule matches up with the OEM’s recommendations if the vehicles are constantly breaking down or are constantly in need of major repairs (such as engine replacements).
Emissions systems
One issue that will need to be considered when establishing the maintenance interval is the need to service the emissions system. In vehicles built to the 2007 and 2010 emissions standards there are parts in the emissions system that require regular service. Diesel particulate filters (DPF), selective catalytic reduction (SCR) systems, and exhaust gas recirculation (EGR) components all require routine service.