Behavioral observations
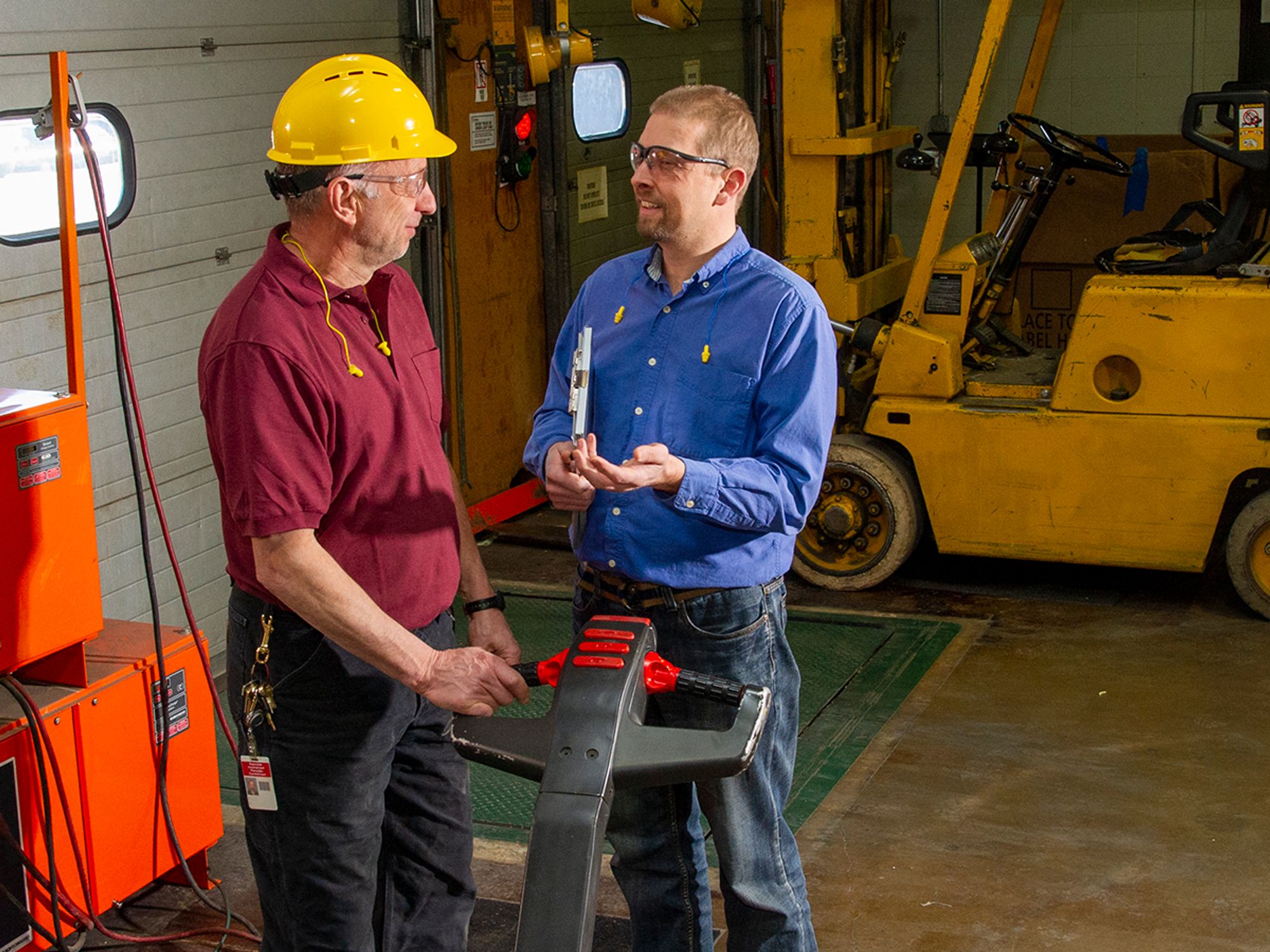
- Behavior-based observations can help to identify unsafe behaviors and hazards.
- Observations are not used to punish employees, but rather to make safety improvements and to assess the company’s safety efforts.
Many companies use behavior-based observations to identify unsafe behaviors and hazards. In the process, workers are given a list of safe behaviors to observe. The workers then spend a few minutes each week watching a coworker perform a task and observing whether the coworker is performing the safe behaviors on the list.
The safe behavior checklist should be developed through thorough analysis, using input from many different company personnel. The checklist should contain identified safe behaviors for given tasks. For example, a safe behavior checklist might contain items such as “Put on gloves,” “Set-up ladder,” “Use suction device to pick up part,” “Bend at the knees when lifting,” and so on.
When the observation is finished, the worker should give the coworker feedback on what was observed. This hopefully will be positive feedback, as in “Great job! All the behaviors on the list were performed, including … using the correct tool, maintaining a good posture with arms close to the body and wrists straight.” The goal here is that when a coworker is recognized for using safe behaviors, the worker will repeat those behaviors later, known as positive reinforcement.
But what about when a worker is observed not performing an identified safe behavior? In these situations, under a formal behavior-based safety system, the worker will identify the behavior to the coworker, but in a non-judgmental way. The point here is to reinforce what the desired safe behavior is, but not to be critical. If the coworker offers information on why the behavior was not performed, then note that information. Remember, observations are not used to punish employees. The observations are used to make safety improvements and to assess the company’s safety efforts.
To facilitate this effort, workers will turn in completed observation checklists to the appropriate safety personnel or committee. Names are usually not recorded on the checklists. The purpose of turning in the checklists is simply to measure the process and identify behavior trends and possible interventions. Remember, these observations are not linked to any discipline measures.