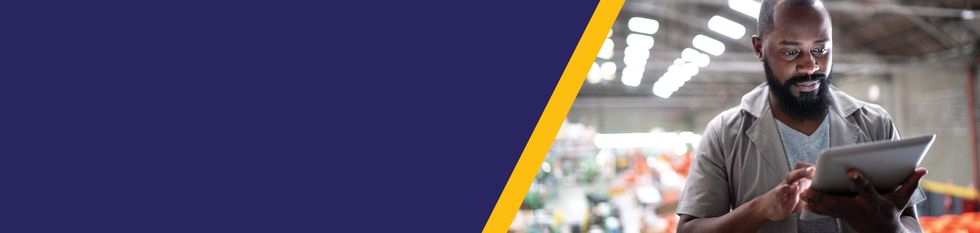
Be Part of the Ultimate Safety & Compliance Community
Trending news, knowledge-building content, and more – all personalized to you!
:
|
Third-party audits are an excellent way to get a fresh look at the hazards in a workplace. These can be done by private consultants, Occupational Safety and Health Administration (OSHA) consultation personnel, corporate personnel, and workers’ compensation representatives. These types of audits are very helpful in establishing the initial (comprehensive) list of hazards. They are also typically done every five years or so, to refresh the baseline of hazards.
To ensure that the worksite will receive the comprehensive survey, consider asking potential surveyors certain questions:
Self-inspections
Self-inspections are typically done by the site safety manager and/or safety committee. These types of inspections are usually done anywhere from monthly to yearly, depending on how comprehensive they are. Self-inspections are a good way to ensure ongoing hazard detection as well as provide visibility for the safety effort.
Third-party audits are an excellent way to get a fresh look at the hazards in a workplace. These can be done by private consultants, Occupational Safety and Health Administration (OSHA) consultation personnel, corporate personnel, and workers’ compensation representatives. These types of audits are very helpful in establishing the initial (comprehensive) list of hazards. They are also typically done every five years or so, to refresh the baseline of hazards.
To ensure that the worksite will receive the comprehensive survey, consider asking potential surveyors certain questions:
Self-inspections
Self-inspections are typically done by the site safety manager and/or safety committee. These types of inspections are usually done anywhere from monthly to yearly, depending on how comprehensive they are. Self-inspections are a good way to ensure ongoing hazard detection as well as provide visibility for the safety effort.