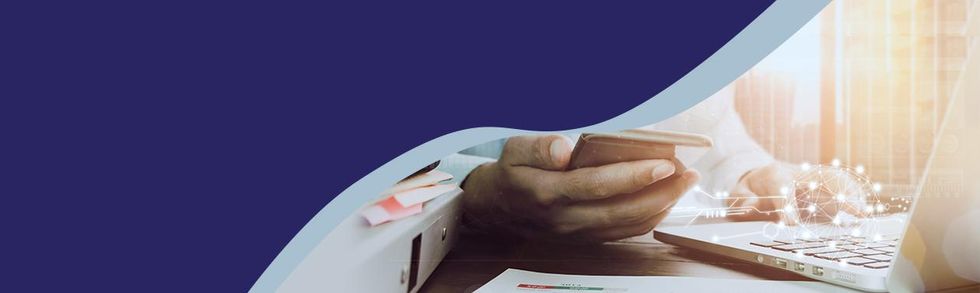
SAFETY & COMPLIANCE NEWS
Keep up to date on the latest developments affecting OSHA, DOT, EPA, and DOL regulatory compliance.
SAFETY & COMPLIANCE NEWS
Keep up to date on the latest developments affecting OSHA, DOT, EPA, and DOL regulatory compliance.
The Federal Motor Carrier Safety Administration (FMCSA) is undertaking a crucial initiative to enhance truck safety and reduce crashes involving commercial motor vehicles (CMVs) – the Crash Causal Factors Program (CCFP). Drivers and carriers have a critical role to play in this study.
This program builds on the foundation of the original Large Truck Crash Causation Study (LTCCS), conducted between 2001 and 2003. The CCFP recognizes the need for an updated understanding of crash factors, due to:
Echoes of the past: The LTCCS and its revelations
The LTCCS, a landmark study involving 963 crashes across 17 states, delved into the complex environment surrounding large truck crashes. Researchers collected a wealth of information, encompassing over 1,000 data elements per crash, to identify the factors contributing to these incidents. Their analysis determined the "critical event" – the action or event leading to the crash,and the "critical reason" – the immediate cause for that event.
According to FMCSA, the LTCCS identified leaving the lane (32 percent), traveling too fast for conditions (29 percent), and colliding with the rear of another vehicle (22 percent) as the most common critical events in crashes involving large trucks. Driver critical reasons were categorized into four areas: non-performance, recognition, decision, or performance failures. The study found that large trucks were assigned the critical reason in 55 percent of all crashes and in 44 percent of two-vehicle crashes. Decision-making errors were the most common critical reasons attributed to drivers of large trucks.
The LTCCS highlighted key associated factors contributing to crashes, including:
CCFP: A sharpened focus for the future
The CCFP's first phase, the Heavy-Duty Truck (crash) Study, aims to collect even more detailed data, focusing specifically on fatal crashes involving Class 7 and 8 heavy-duty trucks (gross vehicle weight rating of 26,001 pounds or more). This two-year study, projected to begin data collection in early 2026, will involve approximately 2,000 crashes from 30 states.
Data will be collected from multiple sources, including police accident reports, post-crash inspections, post-crash investigations conducted by trained officers, and detailed interviews with the involved CMV drivers, motor carrier officials (dispatchers/supervisors, managers, maintenance personnel, etc.), passenger vehicle drivers, pedestrians, and witnesses. These interviews, conducted by the Bureau of Transportation Statistics (BTS), will be strictly confidential and the records of the interviews will not be accessible to FMCSA or others (such as the officers investigating the crash and plaintiff’s attorneys). This meticulous approach seeks to uncover insights into factors like:
The data collection will begin in nine states in January 2026, with the remaining participating states following in April 2026. If you are involved in a crash that will be part of the study, the investigating officer will provide you with information related to the process. The final report is expected in 2029, with the possibility of interim findings being published beforehand.
Key to remember: By leveraging existing state and local data collection processes and supplementing them with confidential interviews, the CCFP aims to streamline the process and gather comprehensive, reliable data that can inform the development of effective strategies to reduce crashes and improve safety on our roads.
As every great military commander will tell you, “Know your enemy.” For motor carriers, this means gaining a deeper understanding of anyone who poses a security threat to the operation.
The following tabletop exercise may help you peer into the minds of those who might cause harm (physical or data theft, terrorism, violence, etc.). Seeing your facility from their perspective may be eye-opening and reveal real threats to security at your company.
The first step is assembling a team of “experts” to look at the vulnerabilities that exist in your organization. This brainstorming team should represent all departments, locations, and shifts.
During this tabletop exercise, participants take on the persona of a security threat and let their imaginations run wild. By putting themselves in the criminal’s shoes, participants look at how someone might gain entry, steal, vandalize, or cause physical harm based on their knowledge of the facility and organization.
A team cannot function properly unless it has specified objectives.
Members of the risk assessment team:
The objective of the group is simple: Find real-life vulnerabilities (and roadblocks) when considering fictitious security scenarios. The “enemy” in the scenario has an objective (e.g., stealing load information, workplace violence), and the group needs to think like the perpetrator to figure out how they might accomplish this goal.
Meetings need a sense of order no matter how much you promote thinking outside the box. You will need to explain the parameters being set.
Other important rules for the exercise include:
Discussion should be timed, and someone should be designated to take notes on the ideas. No idea should be viewed as “crazy.” Sometimes what appears totally absurd has merit and could be a real threat against an individual or the organization.
The notetaker should write all ideas down on a dry erase board or flip chart. Documenting what has been said:
By the close of the tabletop exercise, you hopefully have a wide array of ideas to consider. The group should select those vulnerabilities that warrant a more detailed examination.
Consider the following when determining which ideas to pursue:
The team’s decision should not be influenced by that of the leader/ facilitator. You do not want to experience groupthink. Whichever ideas receive the most votes should be investigated in greater detail.
Key to remember: A fun and engaging tabletop exercise that puts your staff in the shoes of a criminal might just reveal some overlooked vulnerabilities.
As of August 21, the Federal Motor Carrier Safety Administration (FMCSA) has updated a previous waiver to allow a paper copy of the medical examiner’s certificate to serve as proof of certification for up to 60 days after issue. The previous waiver, posted July 14, allowed the paper copy for 15 days. As before, this waiver is valid through October 12, 2025.
The FMCSA made this update to give carriers and drivers more support while medical examiners transition to the secure electronic transmission to medial certification data update. The FMCSA decided drivers should not be punished for delays that may occur while medical examiners and State Driver’s Licensing Agencies (SDLAs) transition to the new system. The agency feels that this waiver is in the best interest of the public and will provide the same, if not a greater, level of safety.
The agency recommends that certified medical examiners continue to issue paper medical examiner’s certificates as well as submit examination results electronically, until further notice.
This waiver applies to both CDL and commercial learner’s permit (CLP) holders. Non-CDL drivers are not affected by this waiver since they already are required to be issued a paper medical card.
As a reminder, the two key impacts of this waiver include:
The waiver does not apply to:
Additionally, the FMCSA reserves the right to revoke the waiver if safety conditions are negatively impacted in terms of the goals and objectives of the original order.
Effective date: June 1, 2026
This applies to: Illinois employers with 16 or more employees
Description of change: On August 15, Illinois Governor J.B. Pritzker signed HB 2978 into law, creating the Family Neonatal Intensive Care Leave Act.
Employees may choose to take the leave continually or intermittently, but employers may require them to take the leave in increments of at least two hours. Employers may not require employees to use their accrued paid time off during this leave, but employees may choose to do so.
Employers may require employees to provide reasonable verification of the child’s stay in a neonatal intensive care unit.
The leave does not run concurrently with leave under the federal Family and Medical Leave Act.
View related state info: FMLA - Illinois
Effective date: January 1, 2026
This applies to: Employers with employees in Illinois
Description of change: On August 15, Governor J.B. Pritzker signed HB 1278 into law, amending the state’s Victims’ Economic Security and Safety Act (VESSA) regarding employees’ personal use of employer-provided electronic devices.
View related state info: FMLA - Illinois
Effective date: January 1, 2026
This applies to: Illinois employers with 51 or more employees
Description of change: On August 15, Governor J.B. Pritzker signed HB 1616 into law, amending the state’s Employee Blood and Organ Donation Leave Act to include part-time employees.
For organ donation, employers must calculate the daily average pay part-time employees received during their previous two months of employment and pay the part-time employees the amount of the daily average pay for the leave days used.
All employees must get their employer’s approval before taking the leave.
View related state info: FMLA - Illinois
Did You Know You Can Ask Unlimited Questions to Our Compliance Experts?
Get answers to your most puzzling compliance questions from the industry’s top experts!