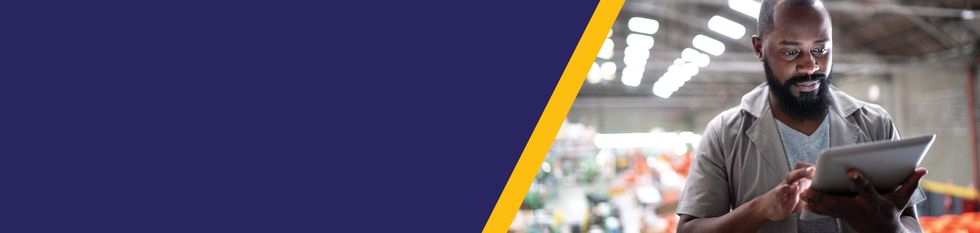
Be Part of the Ultimate Safety & Compliance Community
Trending news, knowledge-building content, and more – all personalized to you!
:
|
How could the maintenance case study have ended differently?
How could the maintenance case study have ended differently?