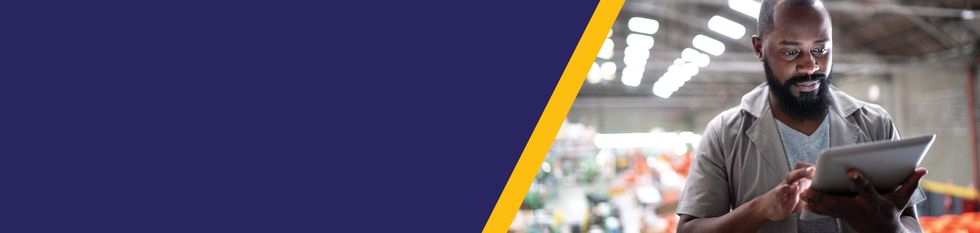
Be Part of the Ultimate Safety & Compliance Community
Trending news, knowledge-building content, and more – all personalized to you!
:
|
One element that really stands out in terms of employers with a formal safety and health program and those without is change analysis. With change analysis, employers want to make sure that there is a mechanism in place to review major changes before they happen and before equipment is purchased, etc. The safety aspect needs to be considered when evaluating vendors and products. Then, the employer must factor in the impact of those on such things as air flow, noise, ergonomic-type issues, and job procedures. If the procedures are changed, make sure the written procedures get changed and that training is conducted with the employees impacted.
While this is nothing radical, many companies don’t have a formal mechanism for doing this, so it’s often not done, or it’s done after the equipment is purchased or installed when there is little flexibility in the controls. The earlier that safety is brought into the mix the better chance employers stand at not introducing a hazard that they are later going to have to control through personal protective equipment (PPE) or work practices.
Not to mention, the cost of retrofitting a hazard control is usually much more expensive than incorporating it up-front.
One element that really stands out in terms of employers with a formal safety and health program and those without is change analysis. With change analysis, employers want to make sure that there is a mechanism in place to review major changes before they happen and before equipment is purchased, etc. The safety aspect needs to be considered when evaluating vendors and products. Then, the employer must factor in the impact of those on such things as air flow, noise, ergonomic-type issues, and job procedures. If the procedures are changed, make sure the written procedures get changed and that training is conducted with the employees impacted.
While this is nothing radical, many companies don’t have a formal mechanism for doing this, so it’s often not done, or it’s done after the equipment is purchased or installed when there is little flexibility in the controls. The earlier that safety is brought into the mix the better chance employers stand at not introducing a hazard that they are later going to have to control through personal protective equipment (PPE) or work practices.
Not to mention, the cost of retrofitting a hazard control is usually much more expensive than incorporating it up-front.