What are the OSHA requirements for emergency stop devices?
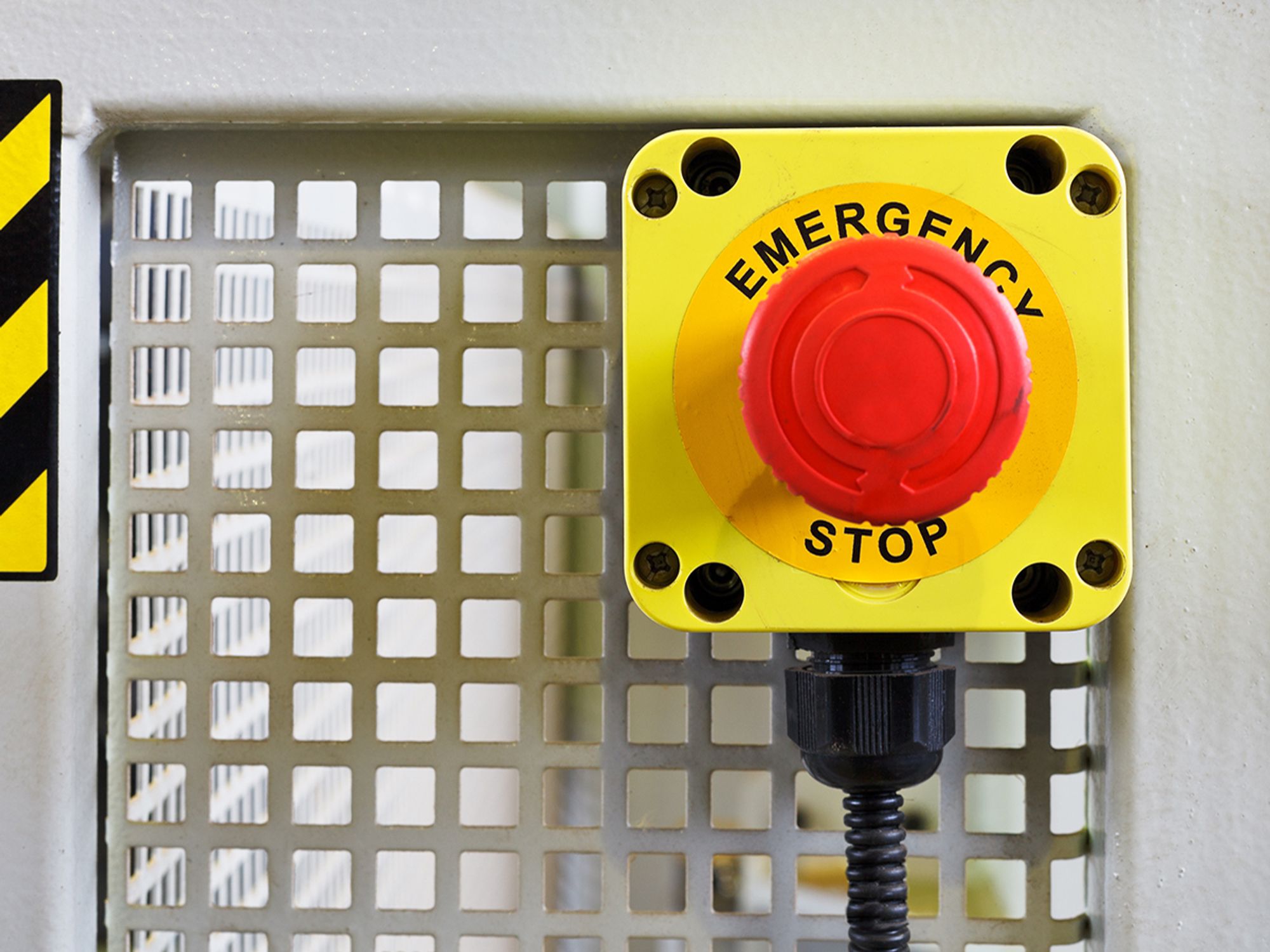
- Emergency stop devices protect employees by halting hazardous mechanical motion.
- Emergency stops must be clearly marked, easily accessible, and properly maintained.
Emergency stop devices, or “E-stops,” protect workers who become entangled in machinery. To protect workers effectively, these devices must be properly installed, identified, and maintained wherever workers are exposed to hazardous machinery. The Occupational Safety and Health Administration (OSHA) only addresses emergency stop controls in a few standards, and these standards do not provide a great deal of information. (For example, 29 CFR 1910.216, “Mills and calendars in the rubber and plastic industries”; 1910.217, “Mechanical power presses”; 1910.261, “Pulp, paper, and paperboard mills”; and 1910.144(a)(1)(iii), “Safety color code for marking physical hazards.”)
Absent a particular requirement, OSHA has used the General Duty Clause to cite for emergency stop issues, sometimes referencing NFPA 79, Electrical Standard for Industrial Machinery. In fact, the following is an excerpt from an actual General Duty Clause citation for lack of an e-stop:
- Section 5(a)(1) of the Occupational Safety and Health Act of 1970: The employer did not furnish employment and a place of employment which were free from recognized hazards that were causing or likely to cause death or serious physical harm to employees in that employees were exposed to being struck-by and caught-in rotating parts ... the employer failed to provide an emergency stop at the operator control station ... that would stop all motions of the machine that cause a hazardous condition, e.g., rotating parts, belts, gears, and cutting heads. Among other methods, one feasible and acceptable method to correct this hazard is to ensure that the "stop" and "emergency stop" functions on this machine ... conform to the requirements of the National Fire Protection Association (NFPA) standard 79; Electrical Standard for Industrial Machinery, 2007 edition; Section 9, "Control Circuits and Control Functions"; and Section 10, "Operator Interface and Control Devices" ...
E-stops cannot detect or prevent hazardous situations before they happen, but they are a vital last defense for employees exposed to mechanical hazards.
Safety requirements for emergency stop devices
In workplaces where employees are exposed to hazardous machinery, OSHA requires employers to:
- Ensure E-stop devices have red buttons, switches, or handles, and ensure that the backings for these E-stop buttons, switches, or handles are colored yellow (NFPA 79, Electrical Standard for Industrial Machinery);
- Install E-stops in such a way that they cannot be overridden from other locations;
- Require E-stop controls to be manually reset after activation and before operations resume;
- Ensure E-stops are easily accessible to operators, and ensure that for some equipment, such as continuously accessible conveyor belts, emergency stop cables extend the entire length of the equipment for employees’ easy access; and
- Test and inspect E-stops according to the manufacturer's guidance.