InstituteSafety & HealthGeneral Industry SafetyCompliance and Exceptions (Level 2)Machine GuardingFocus AreaEnglishMachine GuardingAnalysisMachine Guarding HazardsWoodworkingUSA
What are the OSHA requirements for woodworking machinery?
['Machine Guarding']
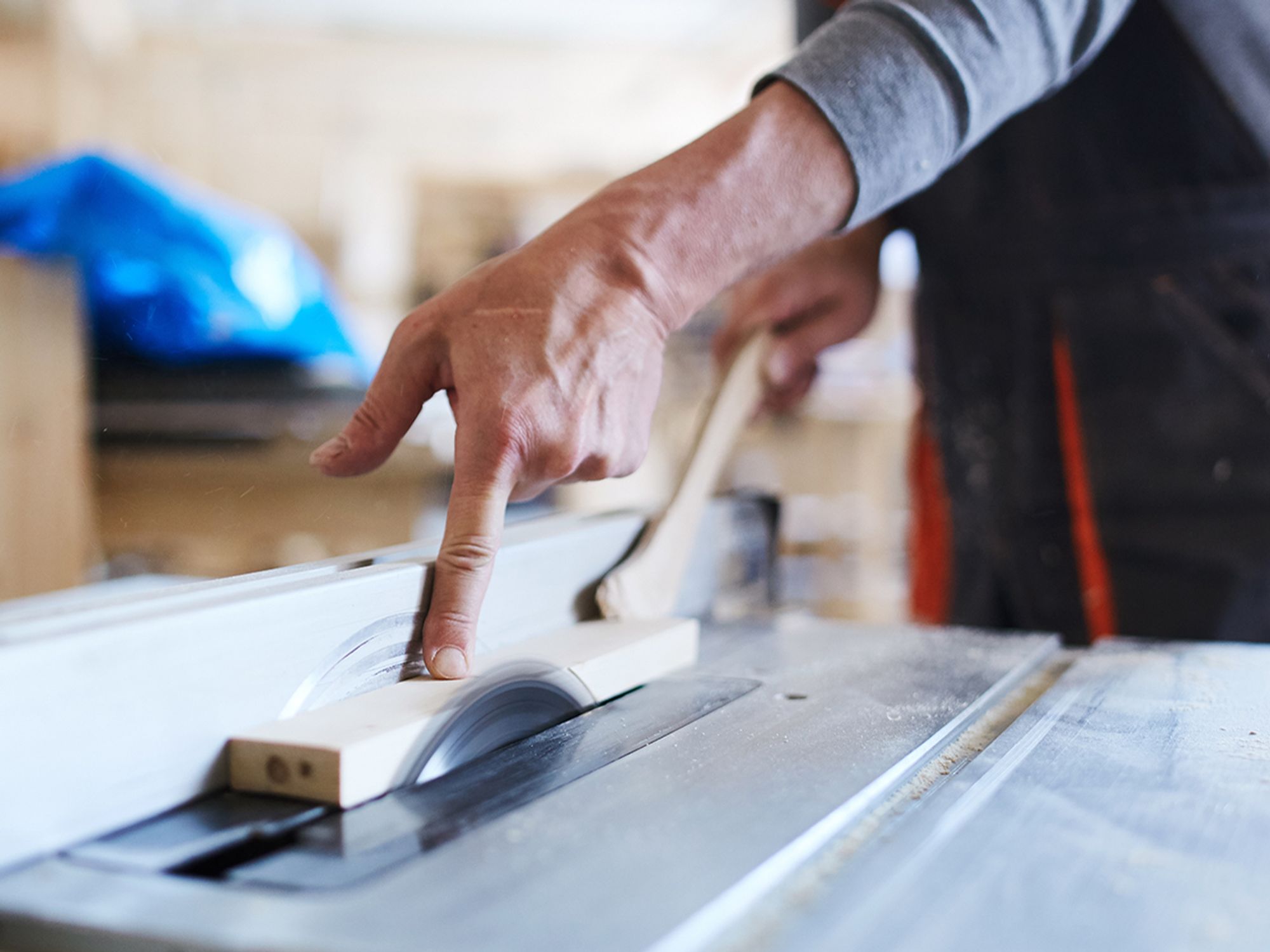
- Different saws call for different specific safeguarding methods, but all saws expose workers to point- of-operation hazards that must be properly guarded.
Machines used in woodworking are dangerous, particularly when used improperly or without proper safeguards. Operators of woodworking equipment commonly suffer laceration, amputation, severed fingers, and blindness. For this reason, the Occupational Safety and Health Administration requires employers to implement effective safeguards on all woodworking machines.
Safety requirements for woodworking machines
Employers must:
- Ensure employees use appropriate equipment for each operation;
- Ensure employees use each machine only for work within the rated capacity specified by the machine’s manufacturer;
- Ensure employees use the correct tools on each machine, such as using only the correct blade for the cutting action of a circular saw, and mounting only blades, cutter heads, and collars onto machine arbors that are accurately sized and shaped to fit them;
- Train employees on safe operating procedures and the proper use of machines;
- Allow only trained and authorized employees to operate and maintain the equipment;
- Frequently inspect equipment and guards to confirm they are in safe operating condition;
- Ensure employees use equipment only when guards are in place and in working order;
- Provide employees with push sticks or other hand tools so that their hands are away from the point of operation when they work on small pieces of stock;
- Ensure employees use a brush or stick to clean sawdust and scrap from machines;
- Provide regular preventive maintenance for all machinery;
- Instruct employees never to leave a machine unattended in the “on” position;
- Maintain proper housekeeping;
- Prohibit employees from wearing loose clothing or long hair;
- Prohibit employees from sawing freehand and ensure that they instead always hold stock against a gauge or fence;
- Select and ensure workers use the appropriate PPE; and
- Ensure all servicing and maintenance is performed under an energy control program in accordance with 29 CFR 1910.147, “The control of hazardous energy (lockout/tagout).”
(These guarding requirements for woodworking machinery are found in 29 CFR 1910.213, “Woodworking equipment,” and apply to all employers in General Industry who have workers using such equipment. Sections 1910.212 and 1910.219 can also apply.)