InstituteAnalysisSafety & HealthConveyorsGeneral Industry SafetyMachine Guarding HazardsFocus AreaUSAEnglishMachine GuardingMachine Guard Maintenance and RepairMachine GuardingIn Depth (Level 3)
What should employers look for when inspecting conveyors?
['Machine Guarding']
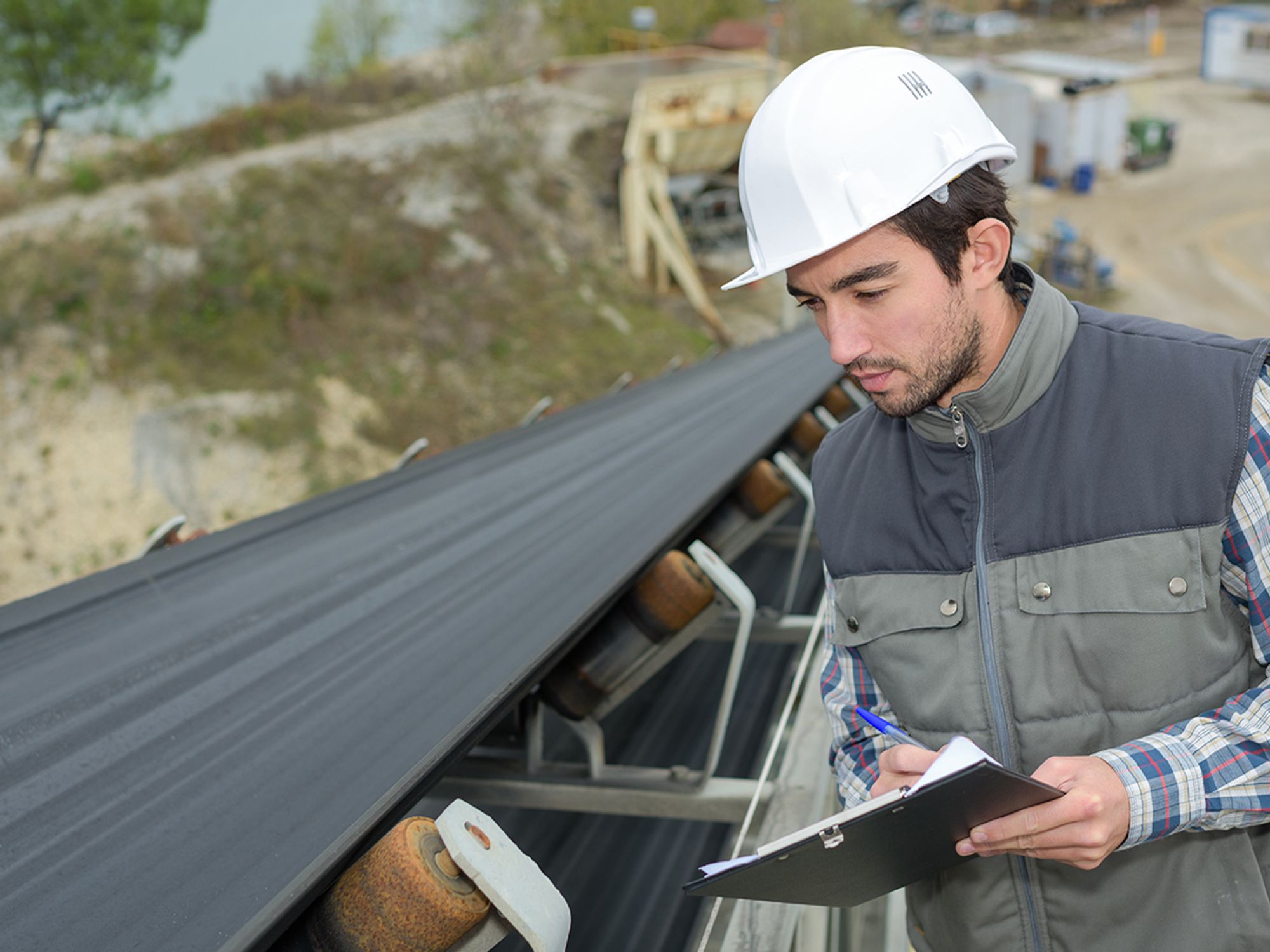
- Barrier guard installation, accessway placement, hazard warnings, emergency stops, and safe work practices are important safeguarding methods for conveyors.
General
Employers should check whether:
- Guards are installed for all sprockets, chains, rollers, belts, and other moving parts that prevent contact with nip points and shear points;
- Prominent warning signs or lights are installed to alert workers to the conveyor operation when installing guarding devices is not feasible;
- All conveyor openings, such as wall openings, floor openings, chutes, and hoppers, have guards when the conveyor is not in use;
- All start buttons have guards to prevent accidental operation;
- All conveyor controls and power sources accept a lockout/tagout device to allow safe maintenance procedures; and
- Each conveyor is equipped with audible start-up alarms.
(29 CFR 1910.212; Section 5(a)(1) of the OSH Act [General Duty Clause])
Crossovers, aisles, and passageways
Employers should check whether:
- All accesses and aisles that cross over, cross under, or are adjacent to the conveyor have adequate clearance and handrails or other guards;
- Crossovers are placed in areas where employees are most likely to use them;
- All underpasses have protected ceilings;
- Appropriate hazard warning signs are posted at all crossovers, aisles, and passageways; and
- Emergency egress is considered when determining the placement of crossovers, aisles, and passageways.
(1910.212; General Duty Clause)
Emergency stops/shut-offs
Employers should check whether:
- All conveyors are equipped with interlocking devices that shut the conveyors down in the case of an electrical or mechanical overload, such as a product jam or other stoppage;
- All conveyors arranged in series will automatically stop whenever any single conveyor in the series stops;
- All conveyors are equipped with emergency stop controls that must be manually reset before conveyors can resume operation;
- Clearly marked, unobstructed emergency stop buttons or pull cords are installed within easy reach of workers; and
- All continuously accessible conveyor belts are equipped with emergency stop cables that extend the entire belt length for workers’ easy access.
(1910.212; General Duty Clause)
Work practices and controls
Employers should check whether:
- All required safe operating procedures for conveyors are implemented;
- Periodic inspections are conducted to ensure compliance with applicable standards and regulations, such as 1910.212 and ANSI B20.1;
- Only trained individuals operate conveyors and only trained, authorized staff perform maintenance;
- Employees working with or near conveyors are trained on the location and use of emergency stop devices and the proper procedures for operating conveyors;
- Employees are prohibited from riding on conveyors;
- Employees are instructed to cross over or under conveyors only at properly designed and safeguarded passageways;
- Employees lubricate, align, and maintain conveyors only when conveyors are stopped;
- Note: If this is impractical, workers may perform this work at a safe distance from any ingoing nip points or pinch points, installing extended oiler tubes and adjusting screws when helpful.
- Employees are prohibited from wearing loose clothing or jewelry while working with or near conveyors;
- Employees secure long hair with nets or caps; and
- All servicing and maintenance is performed under an energy control program in accordance with 1910.147, ”The control of hazardous energy (lockout/tagout).”
(1910.212; General Duty Clause)