What are the general OSHA requirements for machine guarding?
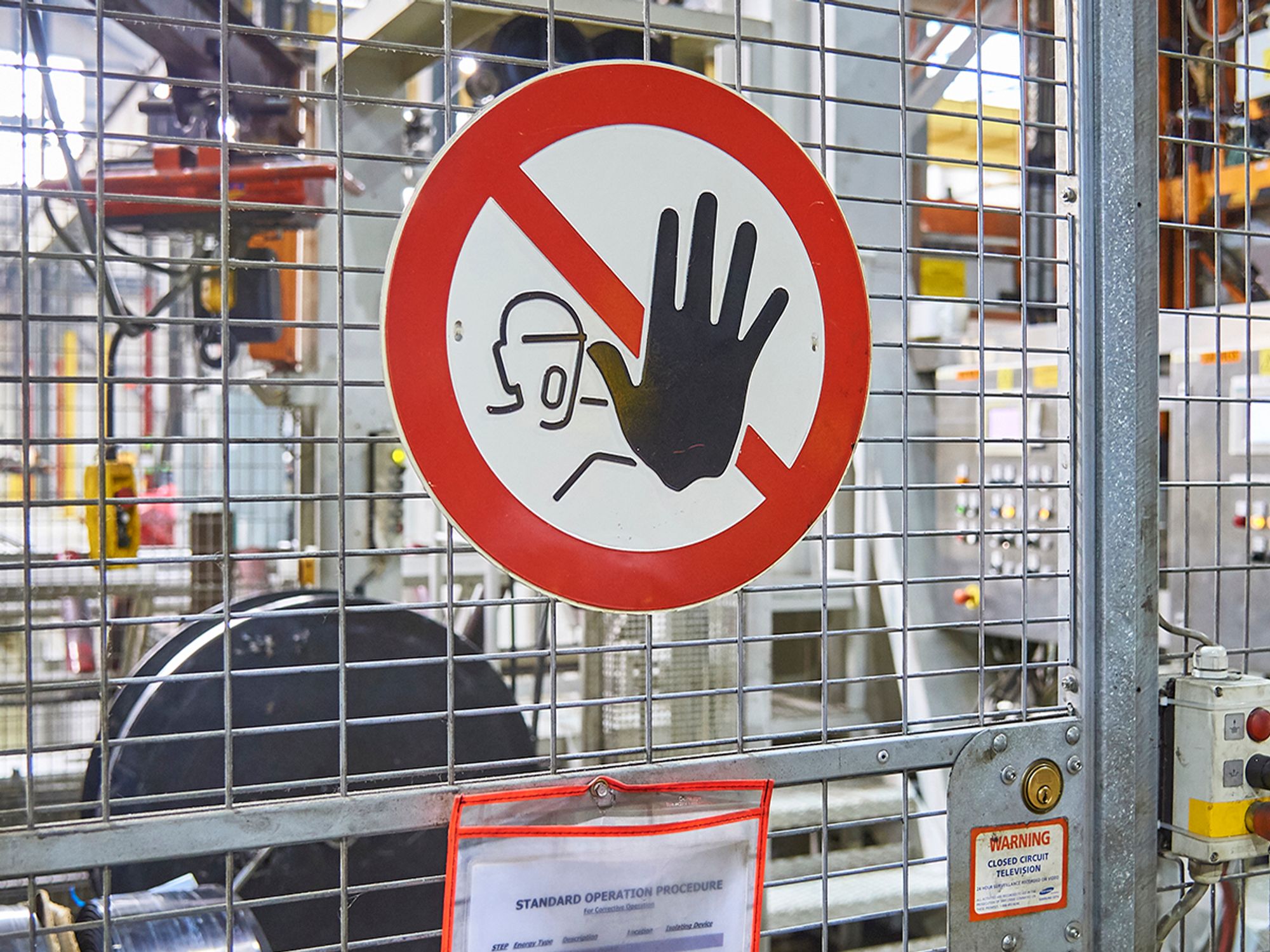
- Certain types of machinery have specific guarding requirements, but most equipment is covered by the general-purpose standard, 29 CFR 1910.212.
- All mechanical components that could cause injury to employees must be effectively safeguarded.
The Occupational Safety and Health Administration (OSHA) has specific guarding requirements for certain types of machinery (i.e., woodworking; grinding; power presses; forging machines; and pulleys, belts, and shafting). For most equipment, such as balers, compactors, shears, and press brakes, OSHA relies on the “catch-all” standard for machine safeguarding, 29 CFR 1910.212, “General requirements for all machines.”
Safeguarding machinery involves taking necessary steps to protect employees from hazardous mechanical components and processes. A central lesson of the catch-all standard is that any mechanical component or process that could injure employees must be safeguarded. Mechanical hazards for which employers must provide proper safeguarding include:
- The point of operation, where work is performed on the stock;
- The power-transmission apparatus, which comprises all parts that transmit energy to the part performing the work;
- Other parts of the machine that move during operation; and
- Flying chips and sparks.
Protecting employees from these hazards is a matter of choosing effective safeguarding methods. Effective safeguarding methods must:
- Prevent contact with hazardous components during machine operation;
- Not create additional hazards, such as new nip points between guards and rotating parts;
- Be secure, durable, and resistant to tampering;
- Not interfere with normal machine operation unless necessary for protecting employees; and
- Not interfere with servicing or maintenance.