What OSHA will look for
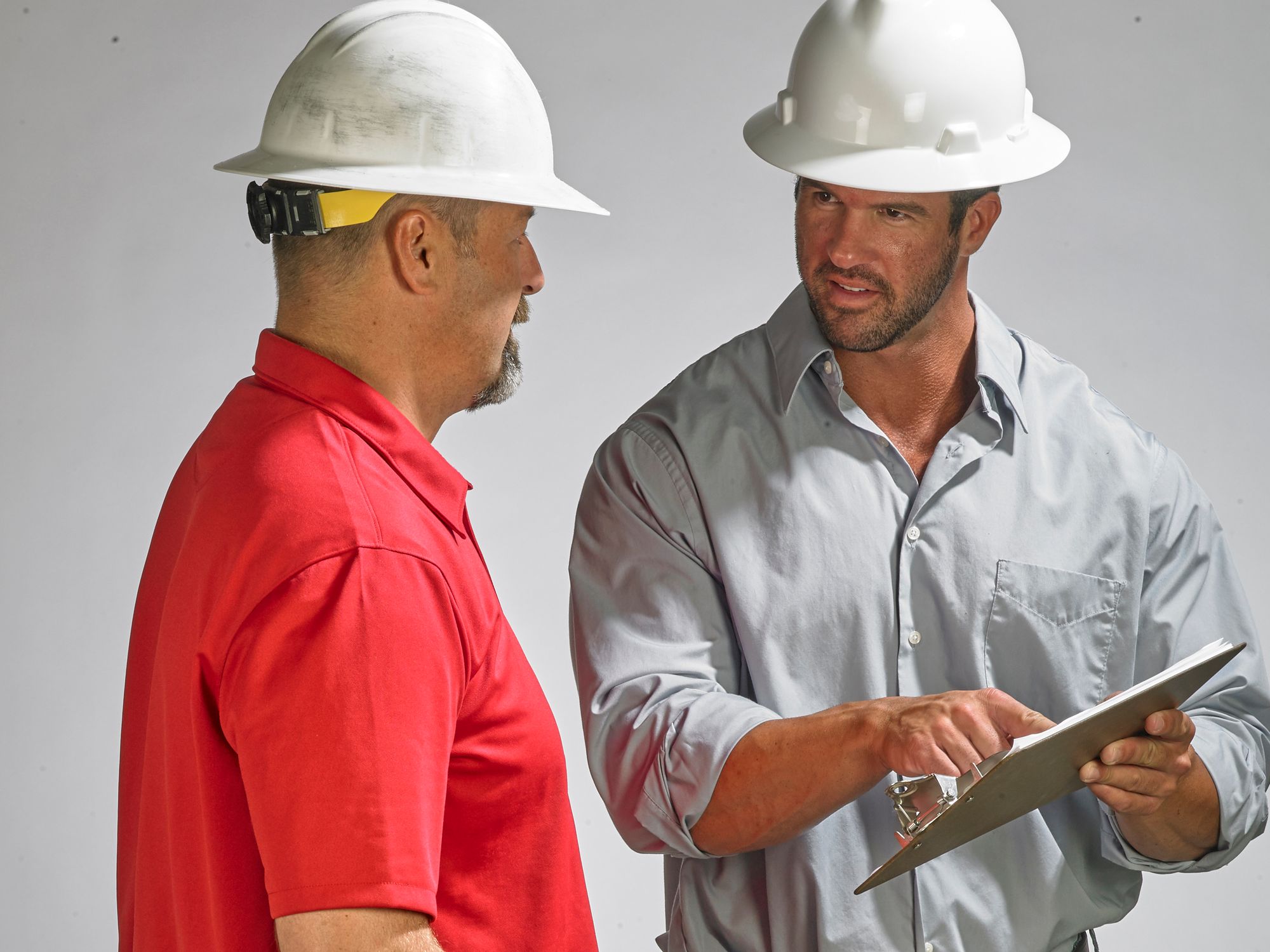
- OSHA will confirm that an employer has a written HazCom program, and that it addresses all the required topics.
- Designate someone to ensure all containers have labels that are readable.
- Compliance officers will look for appropriate labels, descriptions of written alternatives to labeling stationary process containers, descriptions of labels on shipped and workplace containers included in training, and procedures to review and update label information.
- OSHA will look for the following with safety data sheets: person(s) responsible for sheets, how the sheets are maintained, how workers gain access, sheet procedures to follow, a sheet for each hazardous chemical, and training of workers.
- Review and revise training as needed with workers. Set up a system for periodic retraining.
During an inspection, the Occupational Safety and Health Administration (OSHA) will confirm that an employer has a written HazCom program, and that it addresses all the required topics for that workplace.
The employer is expected to provide access to the written program upon request to all employees and employee representatives — failure to do so is a violation.
Assigning responsibility to one person for keeping the written program up to date can ensure that it remains compliant.
Chemical inventory
The list of hazardous chemicals in the workplace must be kept current. Revise the list as necessary when eliminating chemicals in the workplace, or when bringing in a new chemical.
Labels/Other forms of warning
Labeling is a continuing duty — all in-plant containers of hazardous chemicals, except for portable containers for immediate use, must always be labeled.
Written programs should include the person responsible for labeling, both shipped containers and workplace containers, a description of the labeling system used, and a description of any alternative labeling for workplace containers, if applicable.
Review and update labeling and the written program’s label information when necessary.
A compliance officer will check to see that container labels are legible and prominently displayed, and that the container can be cross-referenced to a safety data sheet (SDS). The compliance officer will also evaluate any in-house or workplace labeling, or any alternative labeling provisions used.
The compliance officer may also interview employees to determine if they are familiar with the labeling used in the workplace, and the hazards which the labels denote.
Since labels can come off, information can become smudged or otherwise made unreadable, designate someone to be responsible for ensuring that all containers are labeled, that labels are readable, and that newly purchased materials are checked for labels prior to use.
With these requirements in mind, a compliance officer will be looking for the following types of information to ensure that labeling is properly implemented:
- Designation of person(s) responsible for ensuring compliant labeling of shipped and in-plant containers;
- Description of written alternatives to labeling of stationary process containers (if used);
- Appropriate labels on all workplace containers, including those received from a supplier, secondary containers, and stationary process containers;
- A description and explanation of labels on both shipped and workplace containers included in the employee training program; and,
- Procedures to review and update workplace label information when necessary.
Safety data sheets (SDSs)
In order to ensure a current safety data sheet (SDS) for each chemical in the plant as required, and that worker access is provided, the Occupational Safety and Health Administration (OSHA) will look for:
- Designation of person(s) responsible for obtaining and maintaining the SDSs;
- How SDSs are maintained in the workplace (e.g., in notebooks in the work area(s) or electronically);
- How workers obtain access to them when they are in their work area during the work shift;
- Procedures to follow when the SDS is not received at the time of the first shipment;
- An SDS for each hazardous chemical in the workplace, and;
- Training of workers that includes review of SDS format and use.
Employers must maintain the most current version of the SDS provided by the supplier. When a new SDS is sent, check it against the chemical inventory and against the version of the SDS previously filed. If it is a newer version, replace the older version.
Check the new SDS for any updated hazard or protective information that might affect HazCom training, personal protective equipment (PPE), waste disposal, etc.
Make copies and provide to all necessary departments or make the new SDS available on a computer system.
If an SDS is missing, or the SDS received is deficient, document any efforts to contact the supplier and request a compliant data sheet. If a compliant data sheet from a supplier cannot be obtained, request assistance from the local OSHA office.
During an inspection, OSHA will interview employees to determine if they know the location of SDSs, and of what to do if an SDS is missing or if they do not understand the information. If SDSs are provided on a company website, OSHA will determine if all employees have access, and that all employees know how to use the system.
Information and training
Through proper training, employers can ensure that workers understand the hazards of the chemicals they work with, as well as what steps to take to ensure that they are protected from them.
If workers are not interested in the training as it is conducted, do not appear motivated, and/or do not exhibit an increased knowledge of hazards and the use of protective practices, it may be necessary to review and revise the training to achieve a better outcome.
Review the training whenever a new hazard is introduced, or when processes change that can affect potential exposures.
While refresher training is not required, it is an opportunity to review the hazard communication program and training.
Providing training once, then assuming that several years later employees are still knowledgeable is a risky assumption. It is wise to set up a system for periodic retraining. It does not have to be an annual, full-blown training session. Occasionally remind workers of where the safety data sheets (SDSs) are located or of what the pictograms represent during any applicable monthly or quarterly safety meetings.