What employee training is required?
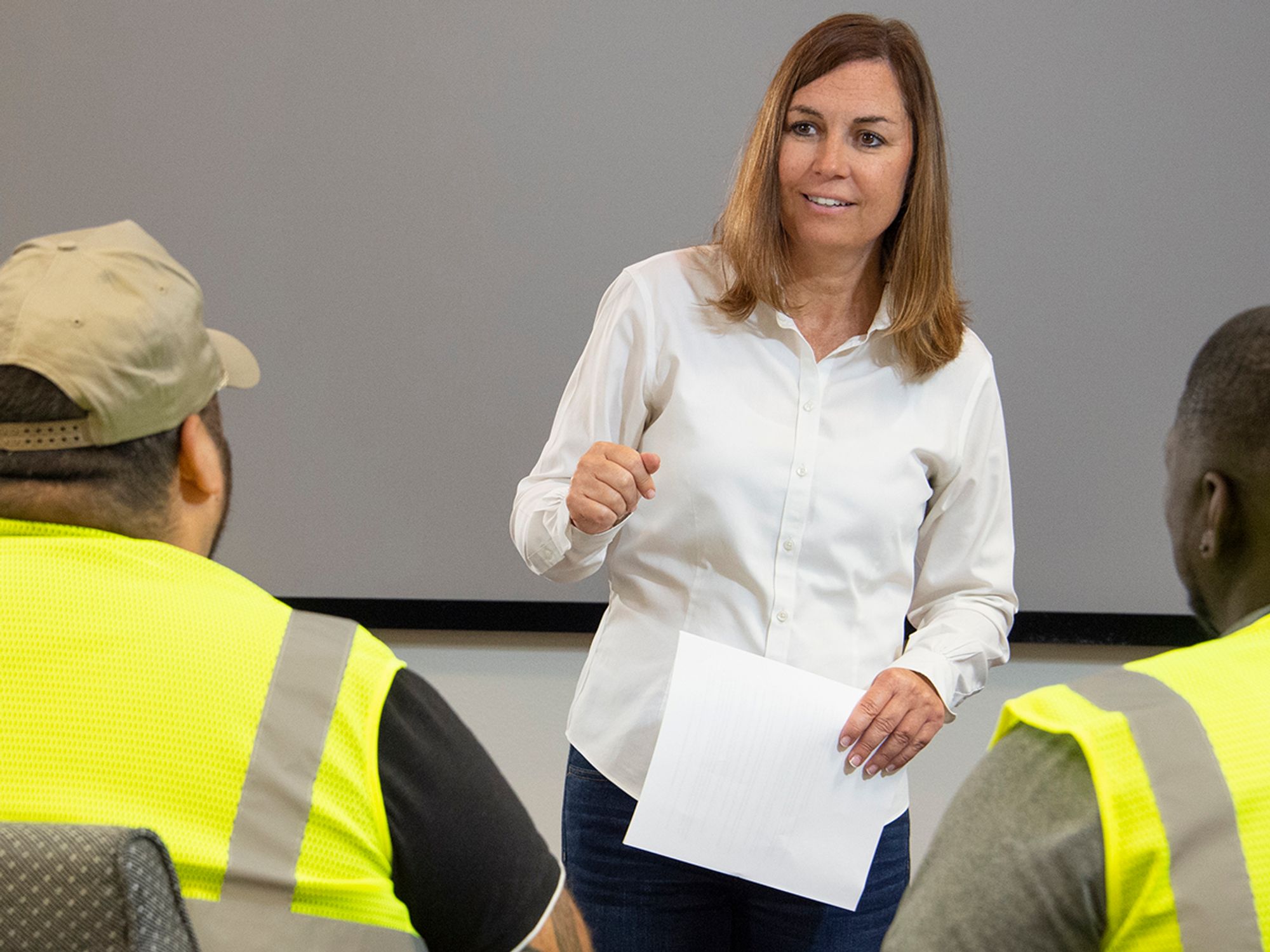
- Although OSHA doesn’t require training in lifting properly or avoiding back injury, employers may need to train employees on these things as part of their ergonomics plan.
- The basic procedure for proper lifting includes planning, situational awareness, and lifting with the legs.
The Occupational Safety & Health Administration (OSHA) doesn’t require training — nor do they say training will prevent back injuries from happening. However, training may need to be part of an employer’s ergonomics plan.
Training should be coupled with any workplace controls that are implemented, including engineering or administrative controls. Employees need training and hands-on practice with new tools, equipment, and work practices to make sure they have the skills necessary to work safely.
Training on safe lifting techniques and generally safe work practices to protect the back should be an element of any back-safety program. Communicating to employees the hazards of certain types of movements and methods can significantly reduce those high-hazard practices and cut down on back pain and injury.
Employee training should go over:
- Back hazards and their causes;
- Proper use of equipment and how to perform tasks (proper posture/lifting);
- Stretching and warmup exercises to perform prior to lifting tasks;
- How to recognize symptoms of back disorders; and
- Who to contact to report hazards and back disorders.
Training could also include:
- Planning ahead when lifting jobs are necessary;
- Getting help to lift objects that are too heavy;
- Never twisting or turning suddenly while carrying a load;
- Reducing vertical and horizontal lifting distances;
- Reducing reach distances;
- Making sure the path is clear before picking up the load;
- Taking careful steps;
- Lifting with the legs and not with the back;
- Maintaining proper posture when standing, sitting, or reclining; and
- Following a sensible diet and exercise program for overall good health.
Employers should enforce the lifting methods that are taught. The incident rates for lifting injuries speak for themselves, so employees should be taught to think of improper lifting as a dangerous activity.
In a well-run workplace, floors don’t accumulate grease, and ladders with missing rungs don’t get used. By the same token, poor lifting techniques shouldn’t pass unnoticed.
Proper lifting
Employees should be trained to lift correctly. Many low back strains and injuries can be avoided by this basic procedure for good lifting:
- Size up the load before trying to lift it. Test the weight by lifting at one of the corners. If the load is too heavy or of an awkward shape, get help from a fellow worker or use a mechanical lifting device like a dolly.
- Make sure the path to your destination is clear before picking up the load. Check for obstacles and hazards in your path, such as holes or spilled liquids. Make sure of your footing before setting out.
- Bend the knees, keep the back straight, and lift with the legs. This is the single most important rule when lifting moderate to heavy objects. Take a tip from professional weightlifters: they can lift tremendous weights because they lift with their legs, not their backs.
- When lifting a crate or box, place your feet close to the object.
- Center yourself over the load, then bend your knees and get a good handhold.
- Lift straight up, smoothly. Allow your legs, not your back, to do the work.
- Do not twist or turn the body during the lift or once a lift is made. Keep the load close to your body, and keep it steady. Turn your body by changing foot positions. Any sudden twisting or turning could result in injuring your back.
- Set the load down properly. Setting the load down is just as important as lifting it. Lower the load slowly by bending your knees, keeping your back upright, and letting your legs do most of the work. Don’t let go of the load until it is secure on the floor.