Repetitive motion injuries
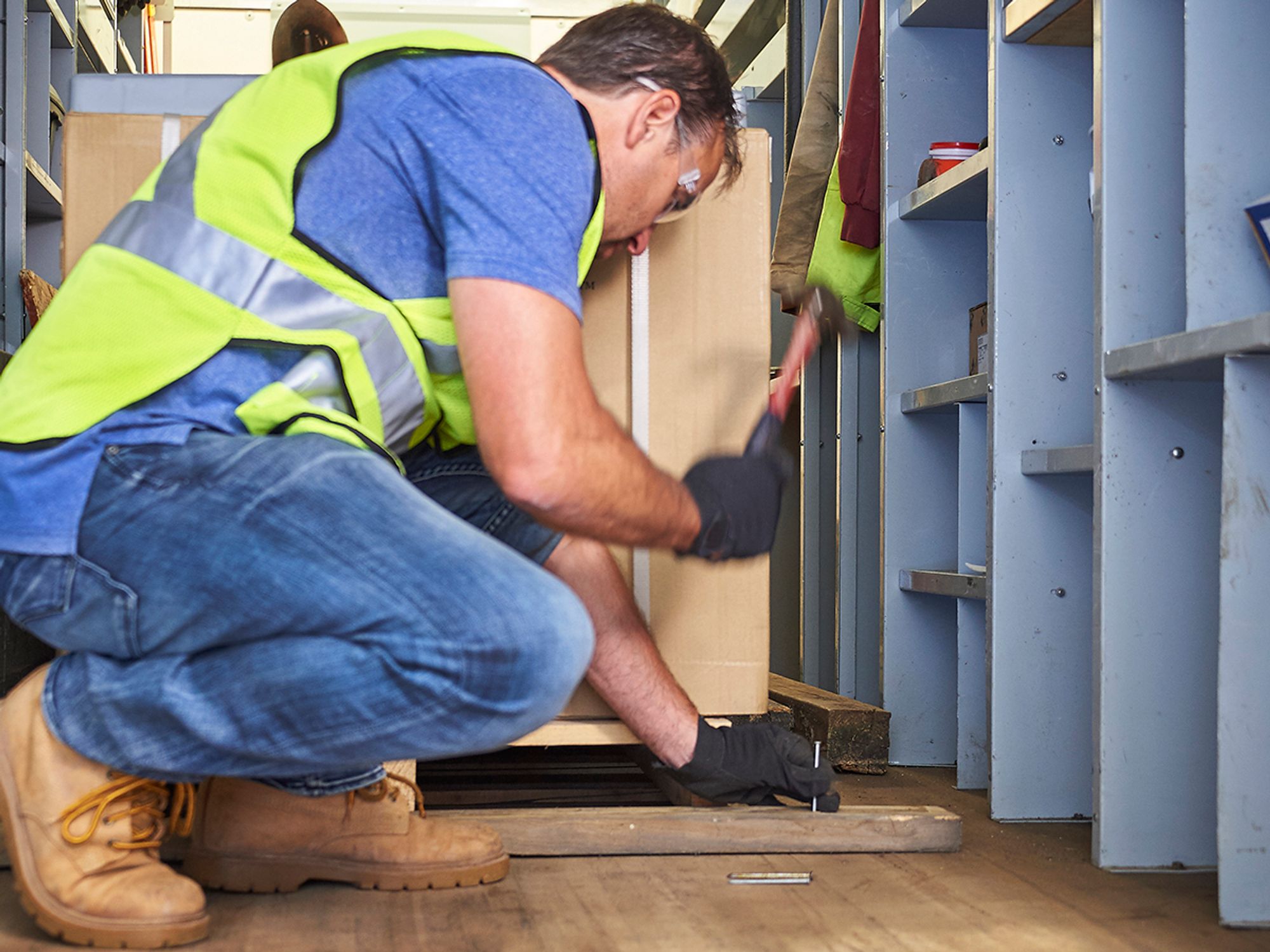
- Repetitive motion injuries are one of the most frequent types of injuries, caused by repeating the same action over and over.
- Risk factors include excessive force, motion, and compression, and inadequate recovery time.
Repetitive motion injuries are caused by repeating the same action over and over. These types of injuries are long-term and can affect employees’ health even years after they retire. That’s why it’s important that they know how to spot and avoid repetitive motion hazards, so they can avoid pain down the road.
Why is this important?
Among the many ergonomic disorders that can result from ergonomically incorrect actions or work/task design, repetitive motions are one of the most frequent types of injuries. Other than back injuries, repetitive motion injuries probably account for the largest percentage of ergonomic disorders in the work environment.
What are the regulatory requirements?
There are no specific regulatory requirements for repetitive motions. However, because repetitive motion injuries are a commonly recognized hazard, the Occupational Safety & Health Administration (OSHA) may cite their occurrence under the General Duty Clause, Section 5(a)(1) of the Occupational Safety and Health (OSH) Act.
What are the risk factors?
Prolonged exposure to repetitive motions can cause musculoskeletal disorders (MSDs) or cumulative trauma disorders (CTDs). Conditions likely to cause MSDs or CTDs include the following:
- Exerting excessive force puts strain on the body.
- Excessive repetition of movements can irritate tendons and increase pressure on nerves.
- Static hand postures, or positions that a worker must hold for long periods of time, can restrict blood flow and damage muscles.
- Motion, such as increased speed or acceleration when bending and twisting the hands, can increase the amount of force exerted on the palms or fingers.
- Compression, from grasping sharp edges like tool handles, can concentrate force on small areas of the body, reduce blood flow and nerve transmission, and damage tendons and tendon sheaths.
- Inadequate recovery time due to overtime, lack of breaks, and failure to vary tasks leaves tissues without enough time to heal.
CTDs can affect nearly all tissues, nerves, tendons, tendon sheaths, and muscles, with the upper extremities being the most frequently affected. These painful and sometimes crippling injuries develop gradually over periods of weeks, months, or years. They result from repeated actions, such as twisting and bending of the hands, arms, and wrists.
A common risk factor among these disorders is the use of force, combined with repetitive motion over time. These conditions are common to individuals who perform tasks such as assembly line work, sewing, meatpacking, and lifting.
Today, CTDs are recognized as a major occupational health hazard in the workplace and account for the largest share of occupational illnesses known as “repeated trauma” disorders.
What employee training is required?
There are no specific employee training requirements on ergonomics, but OSHA may cite employers under the General Duty Clause, Section 5(a)(1) of the OSH Act. The ergonomic guidelines emphasize training employees in proper work techniques to avoid repetitive motions, vibration, improper lifting, and other injury risks.
According to OSHA, training is an important element in the ergonomic process. It ensures that employees:
- Are aware of ergonomics and its benefits;
- Are informed about ergonomics-related concerns in the workplace; and
- Understand the importance of reporting early symptoms of MSDs.
Training prepares employees to actively participate in many aspects of the ergonomics process, including problem identification, solution implementation, and process evaluation. When training is effective, the employees will:
- Learn the principles of ergonomics and their applications, including risk factors associated with MSD hazards;
- Learn about the proper use of equipment, tools, and machine controls;
- Become more aware of work tasks that may lead to pain or injury;
- Recognize early signs and symptoms of MSDs or CTDs;
- Understand the importance of addressing early indications of MSDs and CTDs before serious injury develops; and
- Understand work procedures for reporting work-related injuries and illnesses, as required by OSHA’s injury and illness recording and reporting regulation (29 CFR 1904).
Employees will benefit from an orientation and job-specific hands-on training before they begin their tasks, especially on jobs with potential ergonomic risk factors. Employees should also be notified of workplace changes, informed about new work procedures, and instructed on using new equipment.