The Five Whys method
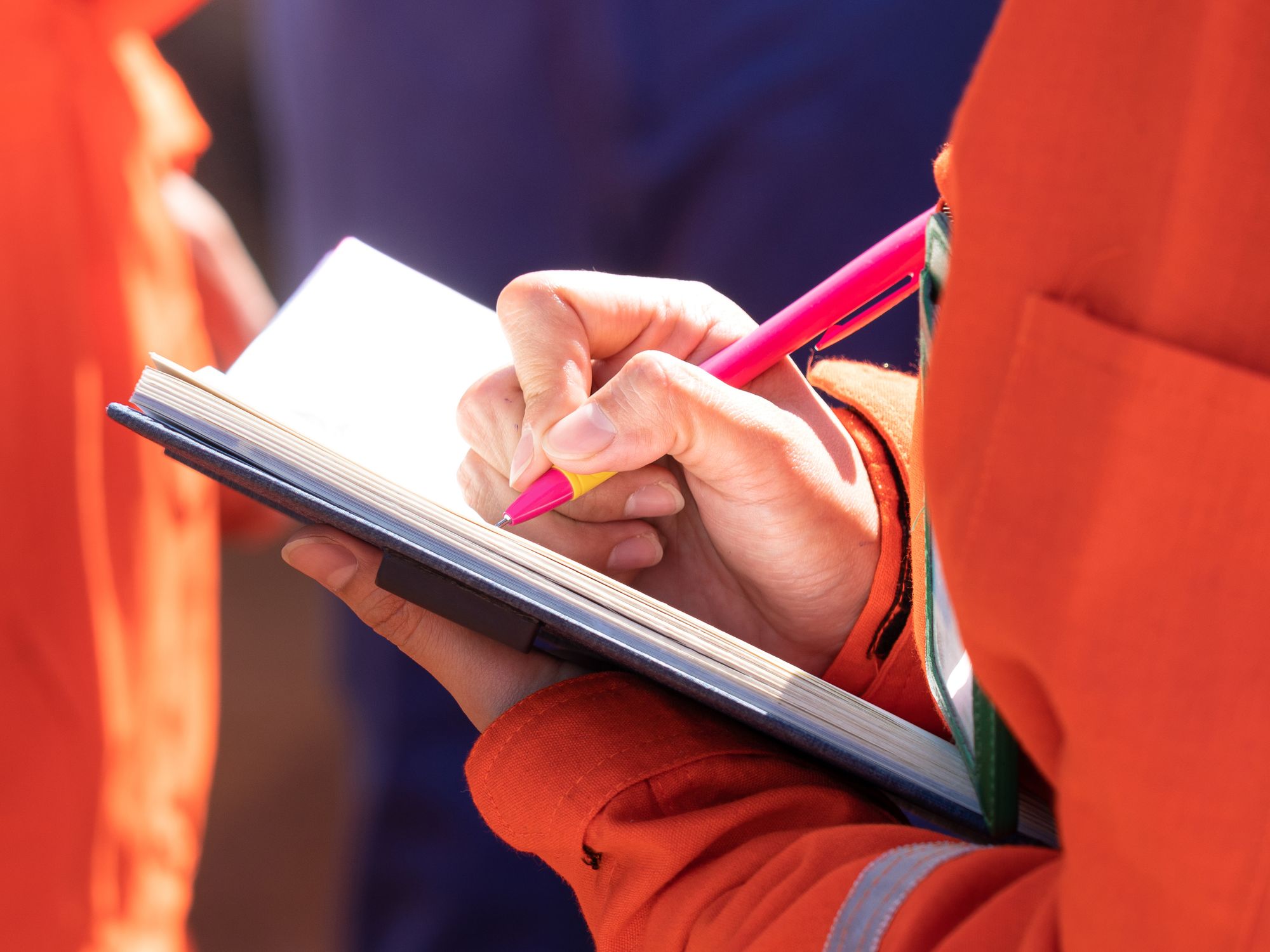
One option for uncovering a root cause is to repeatedly ask “why” questions until the process uncovers a deeper reason for a failure.
The Five Whys is one root cause analysis methodology. It is used to explore the cause/effect relationships underlying a particular problem. Ultimately, the goal of applying the Five Whys method is to determine a root cause of a defect or problem.
The following example of a car not starting demonstrates the basic process:
- Why? - The battery is dead.
- Why? - The alternator is not functioning.
- Why? - The alternator belt has broken.
- Why? - The alternator belt was beyond its useful service life and was never replaced.
- Why? - I have not been maintaining my car according to the recommended service schedule. (root cause)
Note that the questioning could be taken to a sixth, seventh, or even greater level since the “five” in Five Whys is not set in stone. However, five iterations is generally sufficient to identify a root cause. The real key is to encourage the troubleshooter to avoid assumptions and logic traps and instead to trace the chain of causality in direct increments from the effect through any layers of abstraction to a root cause that still has some connection to the original problem.