Determining the root causes
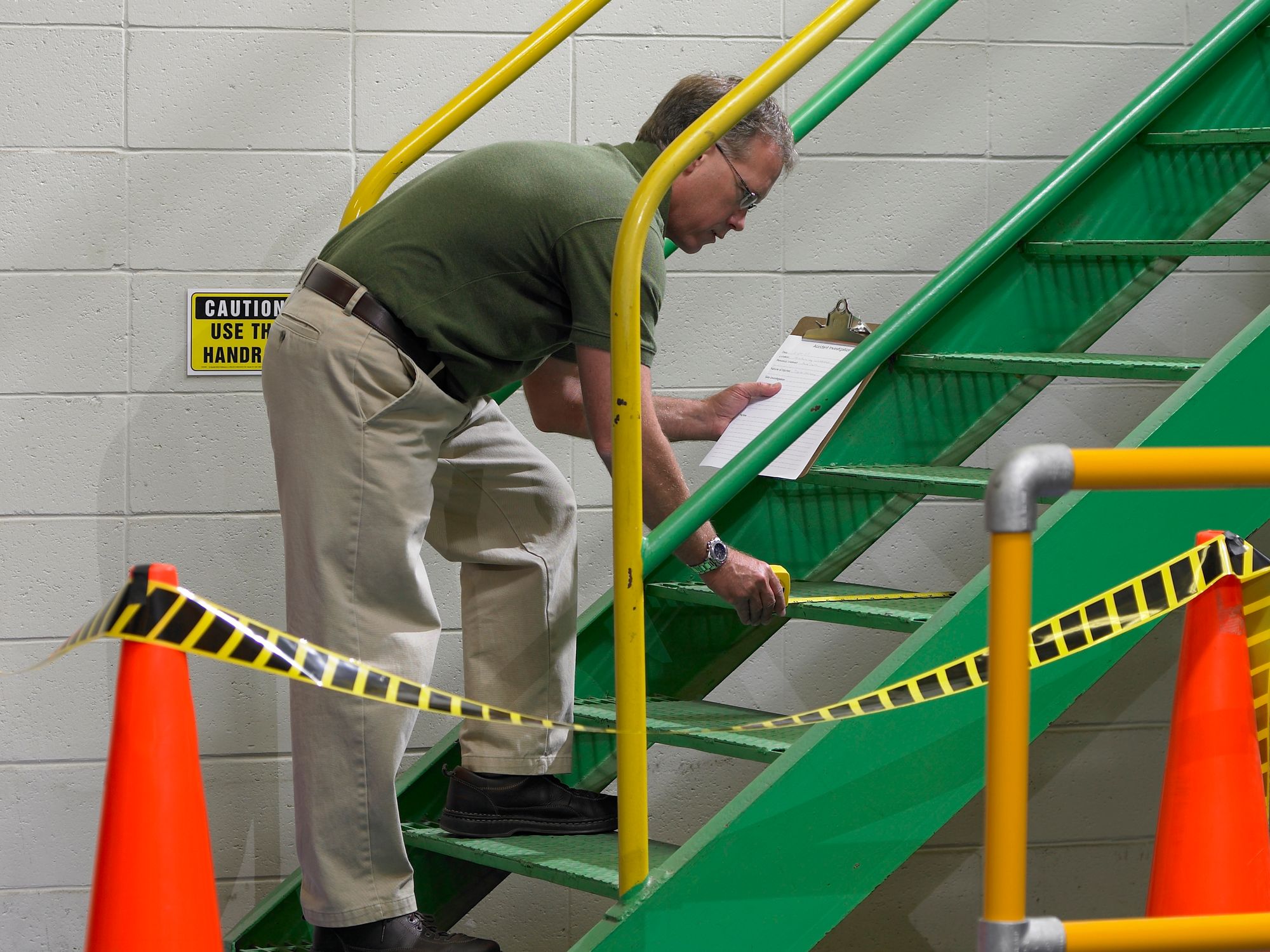
- Investigators must understand the difference between a surface cause and a root cause before searching for root causes of an accident.
- Reviewing the evidence and examining reasons for employee actions are instrumental in identifying root causes.
Identifying a root cause is ultimately what the accident investigation is all about. The investigation will likely discover several causes, not just one. Determining root causes involves:
- Looking at the overall effect of the accident on people, property, products, and processes;
- Examining all potential causes; and
- Determining the reasons for employee actions that contributed to the accident.
It’s important to understand the difference between a symptom or surface cause, and a root cause.
A symptom is a contributing factor, while a root cause is the actual cause of the accident. For example, if a hammer falls from a scaffold and strikes a worker, the symptom is the falling hammer. The root cause might be a missing toeboard on the scaffold, where the hammer was accidentally pushed off the edge. Telling a worker to be more careful is unlikely to prevent other items from falling in the future.
While it is important to evaluate surface actions and conditions, doing so often leads to an emphasis on the individuals, which then tends to focus blame.
After identifying the root cause or causes, use that information to develop the corrective and preventive actions that will help prevent future accidents.
Reviewing the evidence
Examining the evidence collected along with the notes, photos, and sketches should help identify a root cause. If clarification is needed, consulting further with the accident witnesses and victims may be an option. Understand that some witnesses and victims may be able to provide a detailed account of the accident, while others may not be able to recall much information. Simply try to get them to remember as much information as they can.
Finally, understand that some witnesses or victims may not wish to discuss the accident if they were traumatized by the event. Be sure to ask witnesses or victims if they are able to further discuss the accident.
Examining reasons for employee actions
When looking for root causes, determine why an employee acted a particular way prior to the accident, and look at the specific conditions of the task performed just prior to the accident. Some questions to consider include the following:
- Was there something unusual or different about the job or task on the day of the accident?
- Was there a production push at the time the accident occurred?
- Was there a communications breakdown between employees or supervisors?
- Was the employee properly trained?
- Was personal protective equipment available?
- Was the employee in a hurry? Fatigued? Taking shortcuts to complete the task?
- Were procedures inaccurate?
- Was the accident due to any external factors?
- Were tools being incorrectly used?
Remember, the goal should be to identify the failures at a deep level in order to prevent not only a recurrence of the accident, but all potential accidents stemming from the same root cause.