Developing corrective actions and communicating findings
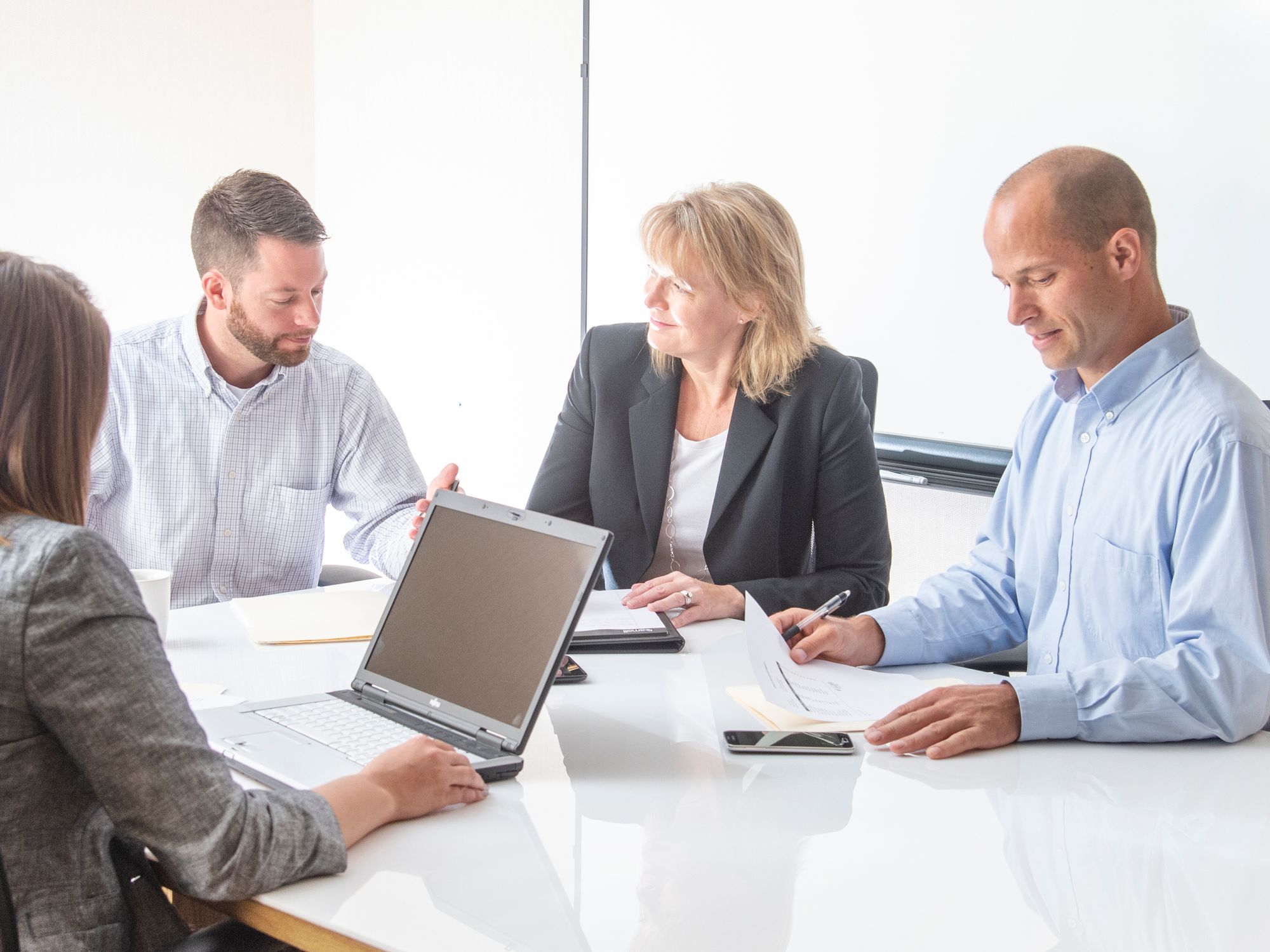
- Recommendations for corrective and preventive actions are necessary to minimize or eliminate the likelihood of another accident happening.
- Findings in a final report concerning an accident investigation must be communicated to upper management, with the goal of preventing future accidents.
After determining the root cause of an accident, corrective and preventive actions must be implemented that will eliminate, or at least reduce, the chances of another accident occurring.
Developing an effective set of corrective and preventive actions starts with an evaluation of the identified root cause(s). Usually, recommendations for corrective actions follow in a rather straightforward manner.
Evaluate each root cause to determine how it can be prevented in the future. With the help of other supervisors, managers, and employees, discuss ways to remove the root cause from the system. Ensure that root causes (not merely symptoms or surface causes) are evaluated and discussed.
To aid in a discussion of root causes, refer to the list of why or why-not questions that probably led to the root cause. Develop a list of potential employee actions that may have contributed to the accident. By thoroughly evaluating this information, an investigator will be one step closer to reducing or eliminating root causes of accidents.
Depending on the situation and the type of root cause, there may be several potential options for reducing or eliminating root causes. Some examples may include:
- Seeking input from employees about how to create a safer working atmosphere,
- Conducting hazard assessment classes,
- Establishing procedures to correct or control all current and potential hazards in a timely manner,
- Establishing safety committees,
- Providing for facility and equipment maintenance to reduce equipment malfunctions and breakdowns, and
- Conducting frequent job refresher training classes.
Often, a thorough accident investigation will result in recommendations for improving a process or reducing hazards. Use the investigation as an opportunity to look for ways to improve the efficiency of a process, the working habits of employees, and the overall safety of the working area.
Some example recommendations may include: increasing lighting in a work area, improving machine guarding, establishing new procedures for housekeeping, or improving communication between management and employees.
Communicating the findings
Because upper management is ultimately responsible for the health and safety of the workforce, the findings of the accident investigation must be reported to them. In order to effectively communicate the investigation findings, provide the following information in the final report:
- A description of the accident (including the date, time, and location);
- The facts determined during the investigation (including chronology as appropriate);
- A list of the suspected root causes; and
- The recommendations for corrective and preventive action (including timing and responsibility for completion).
Through proper documentation of the accident investigation findings, and by reviewing the results of the investigation with appropriate personnel, recurrence of accidents may be prevented.