InstituteAccident Investigation - OSHAAccident Investigation - OSHAAccident Root Cause DeterminationSafety & HealthGeneral Industry SafetyUSAEnglishAnalysisFocus AreaIn Depth (Level 3)
Sample questions for identifying root causes
['Accident Investigation - OSHA']
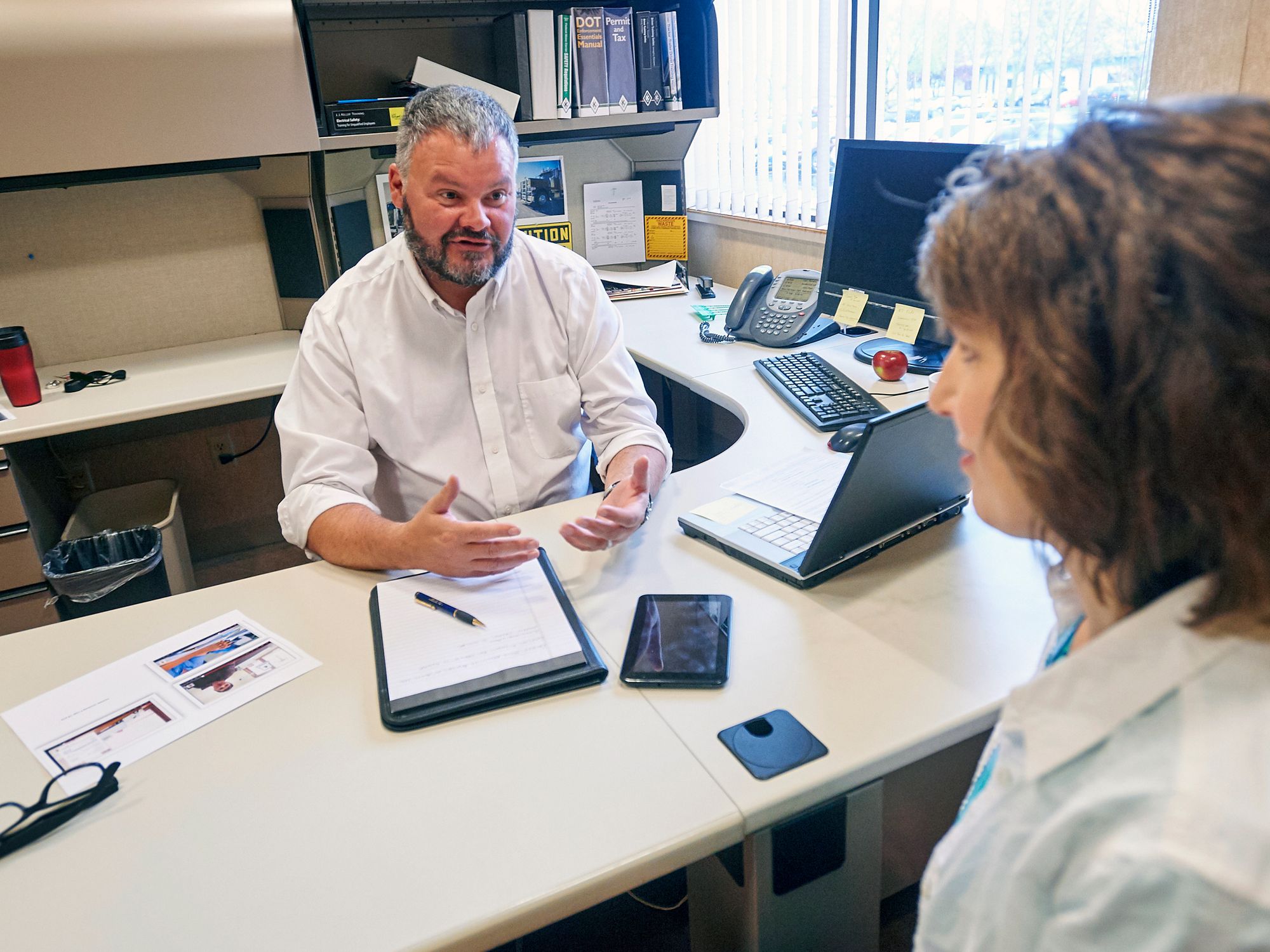
- Asking the right questions can simplify identification of root causes of an accident.
Source: Occupational Safety and Health Administration (OSHA) incident investigation guide, 2015
A thorough approach to identifying root causes involves questioning employees and supervisors about actions and conditions surrounding the accident. The following questions provide ideas to help an interviewer drill down to the root causes:
- Did a written or well-established procedure exist for employees to follow?
- Did job procedures or standards properly identify potential hazards of job performance?
- Were there any hazardous environmental conditions that may have contributed to the incident?
- Were the hazardous environmental conditions recognized by employees or supervisors?
- Were any actions taken by employees, supervisors, or both to eliminate or control environmental hazards?
- Were employees trained to deal with any hazardous environmental conditions that could arise?
- Was sufficient space provided to accomplish the job task?
- Was lighting adequate to properly perform all assigned tasks?
- Were employees familiar with job procedures?
- Was there any deviation from established job procedures?
- Were the proper equipment and tools available and being used for the job?
- Did any mental or physical conditions prevent the employee(s) from properly performing their jobs?
- Were there any tasks considered more demanding or difficult than usual (e.g., strenuous activities, excessive concentration required, etc.)?
- Was there anything different or unusual from normal operations (e.g., different parts, new or different chemicals used, recent adjustments/maintenance/cleaning on equipment)?
- Was the proper personal protective equipment (PPE) specified for the job or task?
- Were employees trained in the proper use of any PPE?
- Did employees use the prescribed PPE?
- Was PPE damaged or not properly functioning?
- Were employees trained and familiar with proper emergency procedures, including the use of any special emergency equipment, and was it available?
- Was there any indication of misuse or abuse of equipment and/or materials at the incident site?
- Is there any history of equipment failure, were all safety alerts and safeguards operational, and was the equipment functioning properly?
- If applicable, are all employee certification and training records current and up‐to‐date?
- Was there any shortage of personnel on the day of the incident?
- Did supervisors detect, anticipate, or report an unsafe or hazardous condition?
- Did supervisors recognize deviations from the normal job procedure?
- Did supervisors and employees participate in job review sessions, especially for those jobs performed infrequently?
- Were supervisors made aware of their responsibilities for the safety of their work areas and employees?
- Were supervisors properly trained in the principles of incident prevention?
- Was there any history of personnel problems or conflicts with or between supervisors and employees, or between employees themselves?
- Did supervisors conduct regular safety meetings with their employees?
- Were the topics discussed and actions taken during safety meetings recorded in the minutes?
- Were the proper resources (i.e., equipment, tools, materials, etc.) required to perform the job or task readily available and in proper condition?
- Did supervisors ensure employees were trained and proficient before assigning them to their jobs?