Compliance program elements
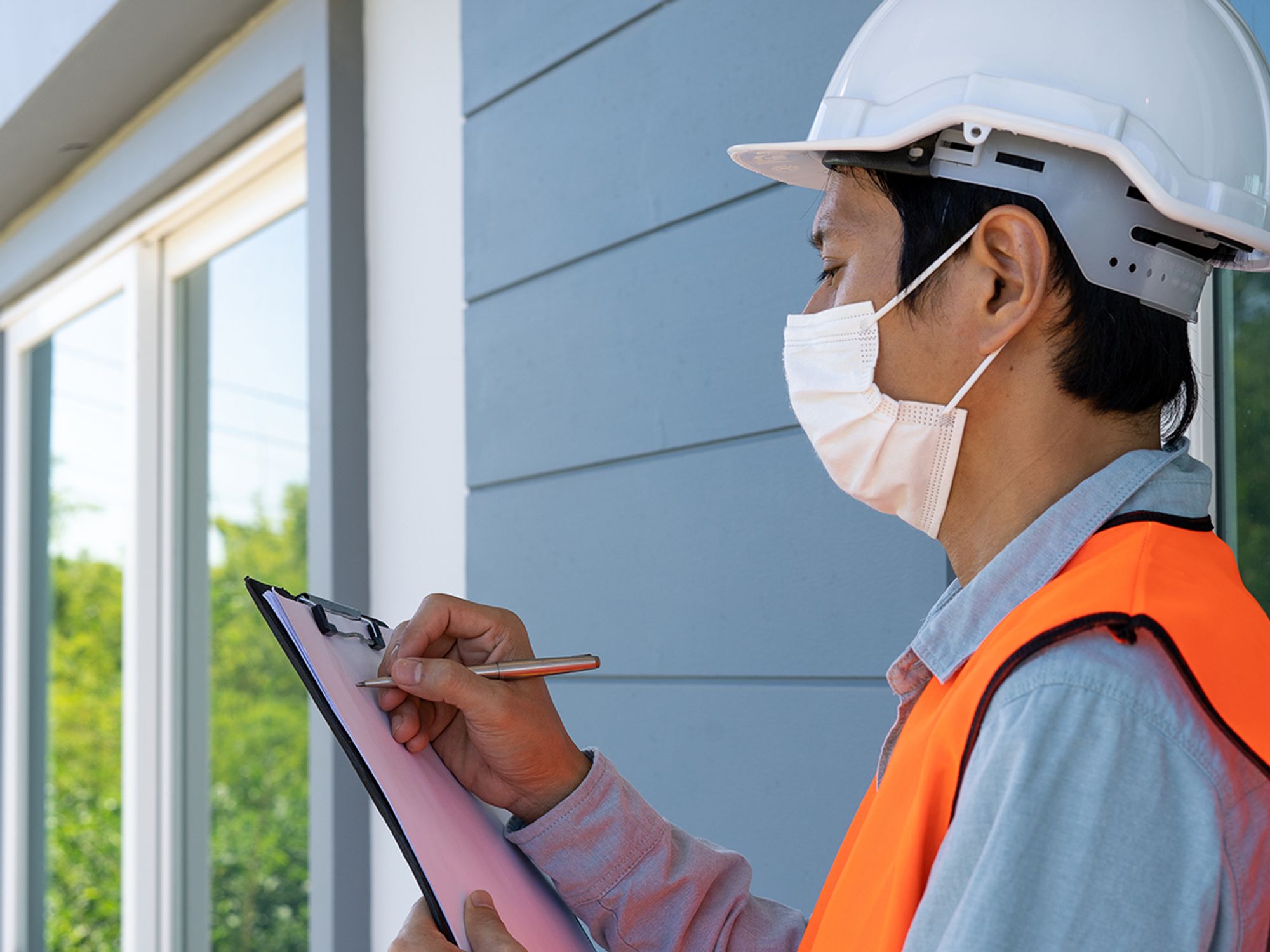
- Employers who work with lead should work with a qualified safety and health professional to develop a worker protection program.
The employer should, as needed, consult a qualified safety and health professional to develop and implement an effective, site-specific worker protection program. These professionals may work independently or may be associated with an insurance carrier, trade organization, or on-site consultation program.
For each job where employee exposure exceeds the permissible action limit (PEL), the employer must establish and implement a written compliance program to reduce employee exposure to the PEL or below. The compliance program must provide for frequent and regular inspections of job sites, materials, and equipment by a competent person. Written programs, which must be reviewed and updated at least annually to reflect the current status of the program, must include:
- A description of each activity in which lead is emitted (such as equipment used, material involved, controls in place, crew size, employee job responsibilities, operating procedures, and maintenance practices).
- The means to be used to achieve compliance and engineering plans and studies used to determine the engineering controls selected where they are required.
- Information on the technology considered to meet the PEL.
- Air monitoring data that document the source of lead emissions.
- A detailed schedule for implementing the program, including copies of documentation (such as purchase orders for equipment, construction contracts).
- A work practice program.
- An administrative control schedule, if applicable.
- Arrangements made among contractors on multi-contractor sites to inform employees of potential lead exposure.