Competent person
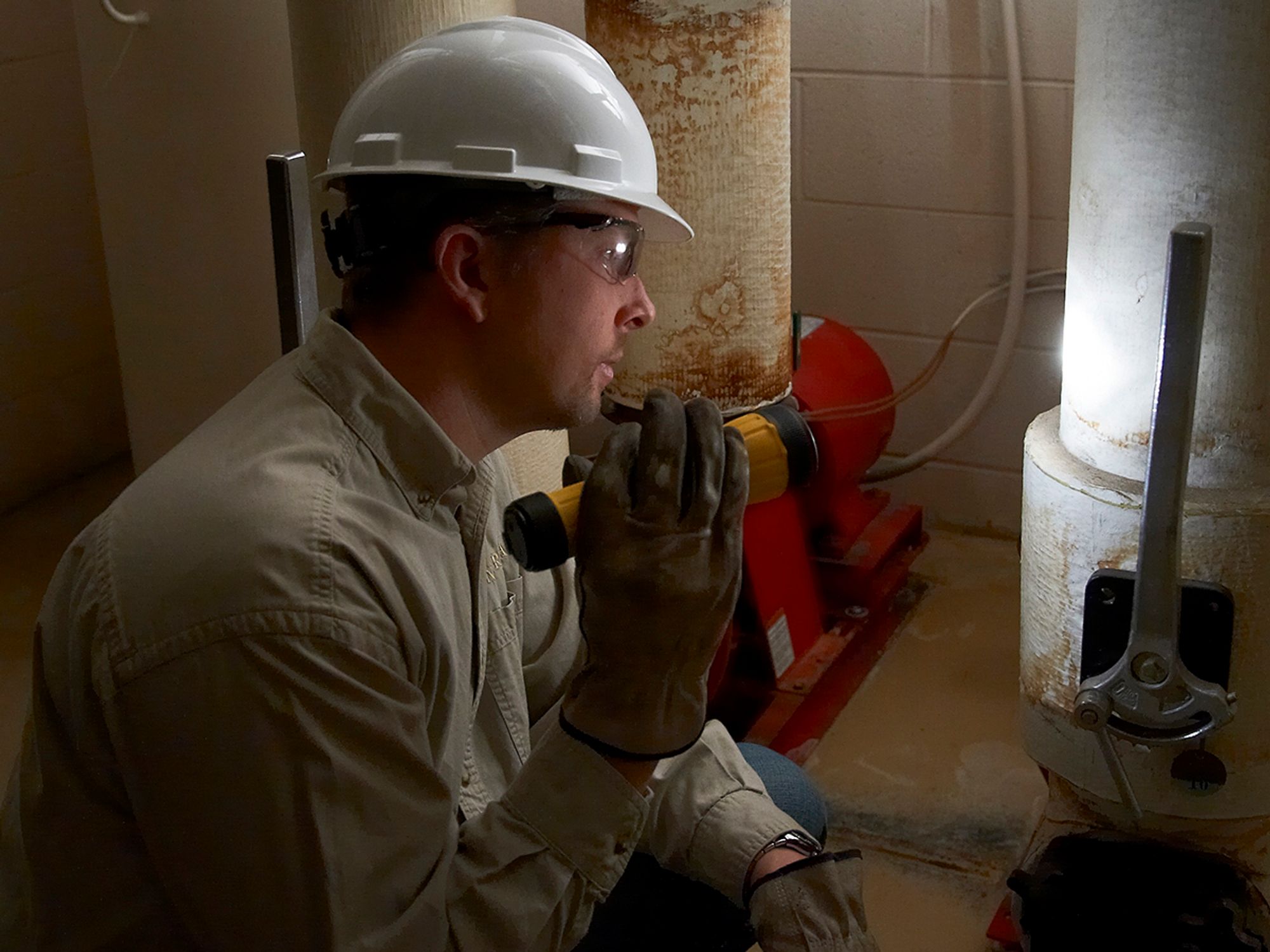
- A competent person is one who is able to identify asbestos hazards in the workplace and has the authority to correct them.
On all construction sites with asbestos operations, employers must designate a competent person — one who can identify asbestos hazards in the workplace and has the authority to correct them. This person must be qualified and authorized to ensure worker safety and health as required by Subpart C, General Safety and Health Provisions for Construction (1926.20). Under these requirements for safety and health prevention programs, the competent person must frequently inspect jobsites, materials, and equipment.
The competent person must attend a comprehensive training course for contractors and supervisors certified by the U.S. Environmental Protection Agency (EPA) or a state-approved training provider, or complete a course that is equivalent in length and content.
For Class III and IV asbestos work, training must include a course equivalent in length, stringency, and content to the 16-hour Operations and Maintenance course developed by EPA for maintenance and custodial workers. For more specific information, see 763.92(a)(2).
Duties
For Class II, III, and IV jobs, the competent person must inspect often enough to assess changing conditions and upon employee request.
For Class I or II asbestos work, the competent person must ensure the integrity of the enclosures or other containments by on-site inspection and supervise the following activities:
- Setup of regulated areas, enclosures, or other containments.
- Setup procedures to control entry to and exit from the enclosure or area.
- Employee exposure monitoring by ensuring it is properly conducted.
- Use of required protective clothing and equipment by employees working within the enclosure or using glove bags (a plastic bag-like enclosure affixed around asbestos-containing material (ACM), with glove-like appendages through which materials and tools may be handled).
- Setup, removal, and performance of engineering controls, work practices, and personal protective equipment through on-site inspection.
- Use of hygiene facilities by employees.
- Required decontamination procedures.
- Notification requirements.