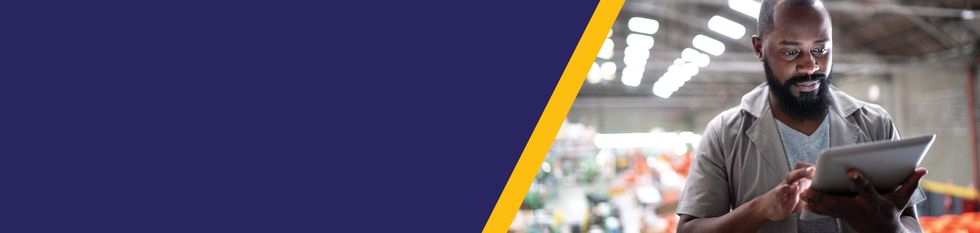
Be Part of the Ultimate Safety & Compliance Community
Trending news, knowledge-building content, and more – all personalized to you!
:
|
Control measures are essential to eliminating or reducing the hazards that are present at a hazardous waste site. The requirements for control measures are described in paragraph (g) of the Hazardous Waste Operations and Emergency Response (HAZWOPER) Standard.
Engineering controls
Engineering controls are physical changes at the site to isolate people from the hazard or otherwise eliminate or reduce the hazard on the job or during the task. Examples include:
Administrative controls
Administrative controls reduce the duration, frequency, and severity of exposure to hazards. These can include:
However, employee rotation should be a last resort in regard to radiation exposure or dose limits. The employer should only use this control if there is no other feasible way of complying with the airborne or dermal dose limits for ionizing radiation.
Safe work practices
Some common safe work practices at a hazardous waste cleanup site include:
Some other general safe work practices include keeping work areas clean, putting away tools or equipment, using safe lifting techniques, and wearing personal protective equipment (PPE) properly.
What about PPE?
The process of eliminating or substituting hazards and putting engineering, administrative, and work practice controls in place will help to mitigate many hazards; however, when hazards remain, there’s one more control method to turn to — PPE.
According to paragraph (g)(1) and (2) of 29 CFR 1910.120 and 1926.65,to the extent feasible, employers must institute engineering controls and work practices to help reduce and maintain employee exposure at or below permissible exposure limits. When this is not feasible, engineering and work practice controls may be supplemented with PPE to keep employee exposures at or below permissible exposure limits or dose limits.
Further requirements
In addition, the provisions of 29 CFR 1910 Subpart G or 29 CFR 1926 Subpart D must be followed. These subparts regulate occupational health and environmental controls for general industry and construction, respectively.
Control measures are essential to eliminating or reducing the hazards that are present at a hazardous waste site. The requirements for control measures are described in paragraph (g) of the Hazardous Waste Operations and Emergency Response (HAZWOPER) Standard.
Engineering controls
Engineering controls are physical changes at the site to isolate people from the hazard or otherwise eliminate or reduce the hazard on the job or during the task. Examples include:
Administrative controls
Administrative controls reduce the duration, frequency, and severity of exposure to hazards. These can include:
However, employee rotation should be a last resort in regard to radiation exposure or dose limits. The employer should only use this control if there is no other feasible way of complying with the airborne or dermal dose limits for ionizing radiation.
Safe work practices
Some common safe work practices at a hazardous waste cleanup site include:
Some other general safe work practices include keeping work areas clean, putting away tools or equipment, using safe lifting techniques, and wearing personal protective equipment (PPE) properly.
What about PPE?
The process of eliminating or substituting hazards and putting engineering, administrative, and work practice controls in place will help to mitigate many hazards; however, when hazards remain, there’s one more control method to turn to — PPE.
According to paragraph (g)(1) and (2) of 29 CFR 1910.120 and 1926.65,to the extent feasible, employers must institute engineering controls and work practices to help reduce and maintain employee exposure at or below permissible exposure limits. When this is not feasible, engineering and work practice controls may be supplemented with PPE to keep employee exposures at or below permissible exposure limits or dose limits.
Further requirements
In addition, the provisions of 29 CFR 1910 Subpart G or 29 CFR 1926 Subpart D must be followed. These subparts regulate occupational health and environmental controls for general industry and construction, respectively.