The Occupational Safety and Health Administration (OSHA)’s Personal Protective Equipment requirements generally apply to all employers who have employees exposed to any hazard that causes a need for protection. Individual requirements, such as for hearing protection, vary depending on exposure.
While personal protective equipment is part of the job in some industries — such as face shields for welding — as a rule, it is considered a last-resort, temporary type of protection. For normal operations, the priority should always be given to eliminating the hazard in the environment rather than using PPE. This is called implementing engineering controls.
No single combination of protective equipment and clothing can protect against all hazards. Thus, PPE should be used in conjunction with other protective methods. The use of PPE can itself create significant worker hazards, such as heat stress, physical and psychological stress, and impaired vision, mobility, and communication.
In general, the greater the level of PPE protection, the greater the associated risks. For any given situation, equipment and clothing should be selected that provide an adequate level of protection. Over-protection as well as under-protection can be hazardous and should be avoided.
Personal protective equipment for General Industry
- PPE includes any clothing, accessories and equipment that helps protect workers from workplace hazards.
- PPE should be the last line of defense against workplace injuries; implementing engineering controls to eliminate hazards in the first place should take precedence.
Personal protective equipment in general industry includes all clothing and accessories designed to create a barrier against workplace hazards. The basic element of any PPE management program should be an in-depth evaluation of the equipment needed to protect against the hazards at the workplace.
Much of this PPE information is framed in general terms and is intended to complement relevant regulations and manufacturers’ requirements.
While PPE is part of the job in some industries, it is considered a last-resort, temporary type of protection. For normal operations, first choice will always be given to eliminating the hazard in the environment rather than using PPE. This is called implementing engineering controls.
No single combination of protective equipment and clothing can protect against all hazards. Thus, PPE should be used in conjunction with other protective methods. The use of PPE can itself create significant worker hazards, such as heat stress, physical and psychological stress, and impaired vision, mobility, and communication.
In general, the greater the level of PPE protection, the greater are the associated risks. For any given situation, equipment and clothing should be selected that provide an adequate level of protection. Over-protection as well as under-protection can be hazardous and should be avoided.
Using PPE improperly or in a manner unsuited to its design and purpose is worse than using no protection at all. Without any protection, the worker knows he is vulnerable and perhaps, takes precautions. With some protection, the worker may rashly blunder into severe difficulty, thinking he is safe.
Workplace hazard assessment
- Employers must conduct a walk-through survey of the workplace to identify safety hazards and determine what PPE is needed.
- Employers must document in writing the results of the hazard assessment.
- OSHA’s Hazard Assessment at 1910.132 does not cover electrical or respiratory protective equipment; those are referenced in other sections of 1910.
Employers must assess any workplace to determine if hazards are present which necessitate the use of eye, face, head, foot, hand, and personal fall protection. (The hazard assessment provisions at 1910.132(d) do not apply to respiratory protection and electrical protective equipment.)
The Occupational Safety and Health Administration (OSHA) requires a walk-through survey of the areas in question to identify sources of hazards. These dangerous situations may include:
- Sources of motion,
- Sources of high temperatures,
- Types of chemical exposures,
- Sources of harmful dust or light radiation,
- Sources of falling objects or potential for dropping objects,
- Sources of sharp objects which might pierce the feet or cut the hands and rolling or pinching objects which could crush the feet,
- The layout of workplace and location of coworkers, and
- Any electrical hazards.
Following the walk-through survey, employers should prepare an analysis of the hazards to enable proper selection of protective equipment. The analysis should include an estimate of the potential for injuries and should determine the type, level of risk, and seriousness of potential injury from each hazard found in the area. Employers should also consider the possibility of exposure to several hazards simultaneously.
What documentation is required for a hazard assessment?
Employers must verify that the assessment has been completed through a written certification:
- Identifying the workplace,
- Identifying the person certifying that the evaluation has been performed,
- Listing the date of the assessment, and
- Containing a statement which identifies the document as certification of hazard assessment.
If it is determined that hazards are present, employers must select protective equipment for employees and communicate the selection decisions to them.
Are there exceptions to the hazard assessment requirement?
OSHA’s PPE Hazard Assessment at 1910.132(d) does not apply to electrical protective equipment (1910.137) or respiratory protection (1910.134). Employers should reference each standard for requirements specific to equipment selection and hazard abatement.
Employers’ responsibility for PPE training and provision
- Employers must provide training to their employees on who is required to use PPE, how to use it, and how to care for it.
- Retraining may be needed periodically if conditions in the workplace change, or an employee indicates lack of understanding of proper use of PPE.
- Most PPE must be provided by the employer with no cost to employees, with some exceptions.
Employers must provide training for each employee who is required to use eye, face, head, foot, hand, and personal fall protection. The training provisions at 1910.132(f) do not apply to respiratory protection and electrical protective equipment. Training should include:
- When PPE is necessary;
- What PPE is necessary;
- How to wear PPE;
- Limitations of the PPE; and
- The proper care, maintenance, useful life, and disposal of the PPE.
Employees must demonstrate an understanding of the training and the ability to use the PPE properly before being allowed to perform work requiring the use of the equipment.
If there is reason to believe an employee doesn’t have the necessary understanding or skill, retraining may be needed. Circumstances where retraining may be required include:
- Changes in the workplace,
- Changes in the types of PPE to be used, or
- Inadequacies in an employee’s knowledge or use of the assigned PPE that indicate the employee doesn’t have the necessary understanding or skills.
Payment for personal protective equipment
Under the requirements, most PPE must be provided at no cost to employees. However, there are a few exceptions. The following do not have to be paid for by the employer:
- Non-specialty safety-toe protective footwear (including steel-toe shoes or boots) and non-specialty prescription safety eyewear provided that the employer permits such items to be worn off the job site.
- Everyday clothing, such as long-sleeve shirts, long pants, street shoes, and normal work boots.
- Ordinary clothing, skin creams, or other items used solely for protection from weather, such as winter coats, jackets, gloves, parkas, rubber boots, hats, raincoats, ordinary sunglasses, and sunscreen.
- Items such as hair nets and gloves worn by food workers for consumer safety.
- Lifting belts, because their value in protecting the back is questionable.
- Replacement PPE, when an employee has lost or intentionally damaged the PPE and it must be replaced.
PPE for eye and face protection
- The OSHA standard for eye and face protection applies to all General Industry employers whose employees are exposed to certain hazards in the workplace.
- Employers must provide eye and face protection at no cost to employees and visitors whenever certain hazards are present.
- Eye and face protection must meet one of three editions of ANSI Z87.1 (2010, 2003, or 1989-Rev1998)
Eye and face protective equipment is required by the Occupational Safety and Health Administration (OSHA) where there is a reasonable probability of preventing injury when such equipment is used. Employers must provide a type of protector suitable for the work to be performed, and employees must use the protectors. These stipulations also apply to supervisors and management personnel and should apply to visitors while they are in hazardous areas.
Employees must use appropriate eye or face protection when exposed to eye or face hazards from flying particles, molten metal, liquid chemicals, acids or caustic liquids, chemical gases or vapors, or potentially injurious light radiation. Eye protection with side protectors is required where there is a hazard from flying objects. Workers who wear contact lenses must wear eye protection over the lenses. Eye and face PPE must be distinctly marked to identify the manufacturer. Filtered lenses should always be the appropriate shade number for the work being performed.
The OSHA standard number for eye and face protection is 1910.133.
What are the PPE requirements for eye and face protection?
The Occupational Safety and Health Administration (OSHA)’s eye and face protection requirement applies to all General Industry employers who have employees exposed to flying particles, molten metal, liquid chemicals, acids or caustic liquids, chemical gases or vapors, or potentially injurious light radiation.
Who must comply?
For eye and face protection, OSHA requires employers to:
- Assess the workplace and determine if hazards that necessitate the use of eye and face protection are present or are likely to be present.
- Select eye/face protection suitable to the hazard (e.g., impact, chemicals, dust) that meets one of three editions of American National Standards Institute (ANSI) Z87.1 (2010, 2003, and 1989-Rev1998).
- Ensure employees use eye protection that provides side protection when there is a hazard from flying objects. Detachable side protectors (e.g., clip-on or slide-on side shields) are acceptable.
- Provide eye/face protection at no cost to the employee, except for non-specialty prescription safety eyewear — provided it is allowed to be worn off the job.
- Ensure employees who require corrective lenses either use goggles/spectacles over their regular glasses, or use safety eyewear incorporating the prescription.
- Train employees on how to use, care for, and inspect their eye/face protection.
What are the types of eye and face protection?
- The main types of eye and face protection include face shields, safety spectacles and goggles, and side shields.
- Each type of protection comes in several styles depending on the hazard and the needs of the user.
Each type of eye, face, or face-and-eye protector is designed for a particular hazard. The main types of eye and face protection include:
- Face shields
- Safety spectacles
| - Safety goggles
- Side shields
|
Employees using corrective spectacles and those who are required by the Occupational Safety and Health Administration (OSHA) to wear eye protection must wear face shields, goggles, or spectacles of one of the following types:
- Spectacles with protective lenses providing optical correction;
- Goggles worn over corrective spectacles without disturbing the adjustment of the spectacles; or
- Goggles that incorporate corrective lenses mounted behind the protective lenses.
When limitations or precautions are indicated by the manufacturer, they should be transmitted to the user and strictly observed.
Over the years many types and styles of eye and face-and-eye protective equipment have been developed to meet the demands for protection against a variety of hazards.
Goggles come in a number of different styles:
- Eyecups,
- Flexible or cushioned goggles,
- Plastic eye shield goggles, and
- Foundrymen’s goggles.
Goggles are manufactured in several styles for specific uses such as protecting against dust and splash, and in chipper’s, welder’s, and cutter’s models.
Safety spectacles require special frames. Combinations of normal streetwear frames with safety lenses do not provide adequate protection and are not in compliance.
Many hard hats and nonrigid helmets are designed with face and eye protective equipment.
Face shields are intended to protect the entire face or portions of it from impact hazards such as flying fragments, objects, large chips, and particles. It is important to note, however, that when worn alone, face shields do not protect employees from impact hazards. OSHA says that face shields should only be used in combination with safety spectacles or goggles, even in the absence of dust or potential splashes, for additional protection beyond that offered by spectacles or goggles alone.
Face shield windows are made with different transparent materials and in varying degrees or levels of thickness. These levels should correspond with specific tasks. Window and headgear devices are available in various combinations to enable the worker to select the appropriate equipment.
What are the criteria for eye and face protection?
Protective eye and face protection devices must comply with any of the following consensus standards:
- American National Standards Institute (ANSI)/International Safety Equipment Association (ISEA) Z87.1–2010 — Occupational and Educational Personal Eye and Face Protection Devices,
- ANSI Z87.1–2003 — Occupational and Educational Personal Eye and Face Protection Devices, or
- ANSI Z87.1–1989 (R–1998) — Practice for Occupational and Educational Eye and Face Protection.
Training and maintenance for eye and face PPE
- Employers must train employees on the specific type of eye or face protection that they will be using.
- Eye and face protection must be cleaned and disinfected regularly, and properly stored when not in use.
- Protective equipment should be inspected regularly for damage.
Each eye, face, or face-and-eye protector is designed for a particular hazard. Employers must make training specific, depending on what type of equipment employees use (i.e., goggles, face shields, spectacles). In selecting the type of protector, employers should consider the kind and degree of hazard and train employees on how to use, care for, and inspect their eye/face protection.
Maintenance and inspection requirements
It is essential that the lenses of eye protectors be kept clean. Continuous vision through dirty lenses can cause eye strain — often an excuse for not wearing the eye protectors. Daily inspection and cleaning of the eye protector with soap and hot water, or with a cleaning solution and tissue, is recommended.
Pitted lenses, like dirty lenses, can be a source of reduced vision and should be replaced. Deep scratches or excessively pitted lenses are apt to break more readily.
Slack, worn-out, sweat-soaked, or twisted headbands do not hold the eye protector in proper position. Visual inspection can determine when the headband elasticity is reduced to a point beyond proper function.
Goggles should be kept in a case when not in use. Spectacles in particular should be given the same care as one’s own glasses, since the frame, nose pads, and temples can be damaged by rough usage.
Personal protective equipment which has been previously used should be disinfected before being issued to another employee. Even when each employee is assigned protective equipment for extended periods, it is recommended that such equipment be cleaned and disinfected regularly.
Several methods for disinfecting eye-protective equipment are acceptable. The most effective method is to disassemble the goggles or spectacles and thoroughly clean all parts with soap and warm water. The Occupational Health and Safety Administration (OSHA) recommends that employers:
- Carefully rinse all traces of soap and replace defective parts with new ones.
- Swab thoroughly or completely immerse all parts for 10 minutes in a solution of germicidal deodorant fungicide.
- Remove parts from solution and suspend in a clean place for air drying at room temperature or with heated air.
- Do not rinse after removing parts from the solution because this will remove the germicidal residue which retains its effectiveness after drying.
The dry parts or items should be placed in a clean, dust-proof container, such as a box, bag, or plastic envelope, to protect them until reissue.
PPE for hand protection
- PPE for hands includes various types of gloves, finger guards, and arm coverings.
- The OSHA standard for hand protection applies to all General Industry employers whose employees are exposed to certain hazards in the workplace.
- Employers must provide hand protection at no cost to employees when employees are exposed to risk of cuts, burns, punctures, chemical exposure, or other hand injuries.
Employees’ hands can be exposed to many hazards, including skin absorption of harmful substances, severe cuts or lacerations, severe abrasions, punctures, chemical burns, thermal burns, and harmful temperature extremes. The Occupational Health and Safety Administration (OSHA) requires employers to protect employees from these hazards. In some cases, guards on a machine can provide the protection. However, in many cases, workers must wear hand protection, such as specialty gloves, finger guards and arm coverings, or elbow-length gloves.
Gloves are often relied on to prevent cuts, abrasions, burns, and skin contact with chemicals that could cause local or systemic effects following dermal exposure. There is no one glove that provides protection against all potential hand hazards, and commonly available glove materials provide only limited protection against many chemicals. Therefore, employers must select the most appropriate glove for a particular application, determine how long it can be worn, and whether it can be reused.
OSHA’s hand protection standards are detailed in 1910.138.
What are the PPE requirements for hand protection?
Employers should select appropriate hand protection on an evaluation of the performance characteristics of the hand protection relative to the task(s) to be performed, conditions present, duration of use, and the hazards and potential hazards identified. To do this, employers should:
- Assess the workplace for work that exposes workers’ hands to hazards such as those from skin absorption of harmful substances, severe cuts or lacerations, severe abrasions, punctures, chemical burns, thermal burns, and harmful temperature extremes.
- Select appropriate hand protection for the hazards found.
- Provide hand protection (except ordinary everyday gloves to protect from weather) to workers at no cost.
- Train workers on the proper use, care, and maintenance of the equipment.
Who must comply?
The Occupational Health and Safety Administration (OSHA)’s hand protection standard applies to all General Industry employers who have employees whose hands are exposed to hazards such as those from skin absorption of harmful substances, severe cuts or lacerations, severe abrasions, punctures, chemical burns, thermal burns, and harmful temperature extremes.
What are the types of hand protection?
Several types of hand protection may be used, depending on the specific hazards present in the workplace:
- Aluminized gloves
- Aramid fiber gloves
- Butyl gloves
- Coated fabric gloves
- Fabric gloves
| - Natural (latex) rubber gloves
- Leather gloves
- Neoprene gloves
- Nitrile gloves
- Synthetic gloves
- Finger cots
| - Mitts with two divisions
- Thimbles
- Hand pads
- Sleeves or forearm cuffs
- Hand lotions and barrier creams
|
What are the criteria for hand protection?
Employers must know the performance characteristics of the types of gloves relative to the specific hazard. Other factors to be considered for glove selection include:
- Replacement: As long as the performance characteristics are acceptable, it may be more cost effective to regularly change cheaper gloves than to reuse more expensive types.
- Work activities: An employer should study how the employee performs job tasks to determine the degree of dexterity required, the duration, frequency, and degree of exposure of the hazard, and the physical stresses that will be applied.
When selecting gloves for protection against chemical hazards, employers should:
- Determine the toxic properties of the chemical(s) (generally, any “chemical resistant” glove can be used for dry powders);
- For mixtures and formulated products (unless specific test data is available), select a glove on the basis of the chemical component with the shortest breakthrough time, since it is possible for solvents to carry active ingredients through polymeric materials; and
- Be sure employees can remove the gloves in such a way as to prevent skin contamination.
Training and maintenance for hand PPE
- Employers must train employees on the specific hazards the employees may be exposed to, and on the proper use, care and maintenance of whichever type of hand protection they will be using.
- Hand protection equipment such as gloves should be kept clean and dry as much as possible and inspected regularly for damage.
Employers must select and train employees to use appropriate hand protection when workers’ hands are exposed to hazards such as:
- Skin absorption of harmful substances,
- Caught-in hazards,
- Severe cuts or lacerations,
- Severe abrasions,
- Punctures,
- Chemical burns,
- Thermal burns,
- Harmful temperature extremes, and
- Excessive vibration.
Employers should train workers on the proper use, care, and maintenance of the equipment. In addition, employers must train employees on each of the hazards above that may be associated with the work they do. Selection of appropriate hand protection and training in how to use such protection should be based on the performance characteristics of the hand protection relative to the tasks to be performed, conditions present, duration of use, and the hazards and potential hazards identified.
Employers must teach employees to wash hands often to prevent a build-up of sweat and dirt. It’s this combination that can cause skin irritation for the glove wearer.
Maintenance and inspection requirements
Employees should check gloves for cracks and holes, especially at the tips and between the fingers, and employers should replace worn or damaged gloves promptly. Employees should be trained to keep gloves clean and dry as much as practical, and to keep a spare pair of gloves for unexpected damage or loss.
- Employers must provide foot protection when workers are exposed to a variety of falling, rolling or crushing hazards.
- The OSHA standard for foot protection applies to all General Industry employers whose employees are exposed to certain hazards in the workplace.
- Employers must provide foot protection at no cost to employees whenever certain hazards are present.
- Foot protection must meet one of three industry standards: ANSI Z41-1991, ANSI-Z41 1999, or ASTM F-2412-2005 and F-2413-2005.
Employees who face possible foot or leg injuries from falling or rolling objects or from crushing or penetrating materials must wear protective footwear. Also, employees whose work involves exposure to hot substances or corrosive or poisonous materials must have protective gear to cover exposed body parts, including legs and feet. If an employee’s feet may be exposed to electrical hazards, non-conductive footwear should be worn.
The Occupational Safety & Health Administrations (OSHA)’s foot protection standard is detailed in 1910.136.
What are the PPE requirements for foot protection?
Employers covered under the foot protection standard should:
- Assess the workplace for areas where there is a danger of foot injuries due to falling or rolling objects, or objects piercing the sole, or when the use of protective footwear will protect the affected employee from an electrical hazard, such as a static-discharge or electric-shock hazard.
- Select footwear appropriate to the hazards of the job.
- Provide foot protection at no cost to the employee, except for non-specialty steel-toe shoes if the employer allows them to be taken off the jobsite.
- Ensure safety footwear meets one of three OSHA-accepted industry standards (American National Standards Institute (ANSI) Z41-1991, ANSI-Z41 1999, or American Society for Testing and Materials (ASTM) F-2412-2005 and F-2413-2005).
- Train employees on the use, care, maintenance, and inspection of safety footwear.
Who must comply?
The Occupational Health and Safety Administration (OSHA)’s foot protection standard applies to all General Industry employers who have employees with risk of exposure to foot injuries.
What are the types of foot protection?
Types of foot protection include various styles of safety shoes, boots, and guard:
- Combination foot and shin guards
- Electrically conductive
- Electrical hazard, safety-toe shoes
- Foundry shoes
- Leggings
- Metatarsal guards
- Safety shoes
- Toe guards
- Shoes and boots with instep protection
- Boots with built-in ankle protection
| - Insulated boots for protection against extreme temperatures
- Rubber or plastic safety boots that are effective against water, oil, acids, corrosives, and chemicals
- Foundry shoes with elastic gores rather than laces to provide easy removal in case sparks or hot metal get inside
- Add-on protections such as metatarsal guards, shoe covers, rubber spats, strap-on cleats, and puncture-proof steel inserts.
|
What requirements must foot protection meet?
In the foot protection standard, the Occupational Health and Safety Administration (OSHA) requires that safety shoes and boots must meet the protective criteria defined in any of the following consensus standards:
- American Society for Testing and Materials (ASTM) F–2412–2005, Standard Test Methods for Foot Protection and ASTM F–2413–2005, Standard Specification for Performance Requirements for Protective Footwear, or
- American National Standards Institute (ANSI) Z41–1999 — American National Standard for Personal Protection — Protective Footwear, or
- ANSI Z41–1991 — American National Standard for Personal Protection — Protective Footwear.
Safety shoes or boots with impact protection are required for carrying or handling materials such as packages, objects, parts, or heavy tools which could be dropped, and for other activities where objects might fall onto the feet. Safety shoes or boots with compression protection would be required for work activities involving skid trucks (manual material handling carts), around bulk rolls (such as paper rolls), and heavy pipes, all of which could potentially roll over employees’ feet. Safety shoes or boots with puncture protection would be required where sharp objects could be stepped on, causing a foot injury.
Training and maintenance for foot PPE
- Employers must train employees on the use and care of the specific type of foot protection that they will be using.
- Foot protection must be in good repair and free from damage.
Employees must wear protective footwear when working in areas where there is a danger of foot injuries due to falling or rolling objects, or objects piercing the sole, and where employees’ feet are exposed to electrical hazards. Employers must train employees on hazards associated with their work, and train them on the use, care, maintenance, and inspection of safety footwear.
The Occupational Health and Safety Administration (OSHA)’s general industry standard on personal protective equipment at 1910.132 also requires employee training on the use of protective footwear. Training should include:
- When PPE is necessary.
- What PPE is necessary.
- How to properly don, doff, adjust, and wear PPE.
- The limitations of the PPE.
- The proper care, maintenance, useful life, and disposal of the PPE.
Maintenance and inspection requirements
Employers are required to train employees on the proper care and maintenance of their foot protection. Foot protection must be in good repair and free from any damage in order to adequately protect employees from hazards associated with their work.
PPE for head protection
- Head injuries are among the most severe injuries workers might experience.
- The OSHA standard head protection applies to all General Industry employers whose employees are exposed to certain hazards in the workplace.
- Employers must provide head protection at no cost to employees whenever certain hazards are present.
- Head protection must meet one of three editions of ANSI Z89.1 (1997, 2003, 2009)
Injuries to the head can be some of the most severe injuries workers can experience. That is why the Occupational Health and Safety Administration (OSHA) requires employers to protect employees from hazards from falling objects that could strike the head. This takes the form of hard hats and similar PPE.
OSHA’s head protection standard is detailed in 1910.135.
What are the PPE requirements for head protection?
Employers covered under the head protection standard should:
- Assess the workplace for areas where employees could receive head injury from falling objects or contact with exposed electrical conductors.
- Select appropriate head protection for the hazard, taking into account any electrical hazards.
- Ensure head protection meets one of three editions of American National Standards Institute (ANSI) Z89.1 standard (1997, 2003, or 2009, or equivalent).
- Provide head protection at no cost to the employee.
- Train employees on how to use and care for head protection.
- Enforce the use of head protection when needed.
Who must comply?
OSHA’s head protection standard applies to all general industry employers who have employees with exposure to such hazards.
What are the types of head protection?
- Head protection is classified by ANSI as Type 1 or Type 2, and as Class G, E or C
- Head protection must comply with ANSI Z89.1, American National Standard for Industrial Head Protection.
The most recent editions of the American National Standards Institute (ANSI) head protection standards classify head protection as Type 1 and Type 2 and use three classes (G, E, and C) based on electrical class. (Earlier editions used Class A, B, and C designations.)
Types and classes — ANSI Z89.1-1997 (and later editions)Type | Impact |
---|
1 | Helmets intended to reduce the force of impact resulting from a blow only to the top of the head. |
2 | Helmets intended to reduce the force of impact resulting from a blow which may be received off center or to the top of the head. |
Electrical class | Protective helmet |
---|
G (General) | Class G helmets are intended to reduce the danger of contact exposure to low voltage conductors. Test samples are proof tested at 2,200 volts (phase to ground). However, this voltage is not intended as an indication of the voltage at which the helmet protects the wearer. |
E (Electrical) | Class E helmets are intended to reduce the danger of exposure to high voltage conductors. Test samples are proof-tested at 20,000 volts (phase to ground). However, this voltage is not intended as an indication of the voltage at which the helmet protects the wearer. |
C (Conductive) | Class C helmets are not intended to provide protection against contact with electrical conductors. |
What are the criteria for head protection?
While the Occupational Health and Safety Administration (OSHA)’s head protection standard does not spell out the criteria that protective helmets must meet to provide maximum protection, it does require that helmets conform to the performance criteria of the American National Standard, ANSI Z89.1.
This industry consensus standard describes the types and classes, materials, performance requirements, and tests that manufacturers must meet to ensure that their helmets provide adequate protection. Each helmet must be marked with the following information:
- Name and/or identification mark of the manufacturer,
- Date of manufacture,
- ANSI designation,
- Type and class designation, and
- Appropriate headband size range.
If any of this information is missing or obliterated, the helmet should not be worn.
Head protection must comply with any of the following consensus standards:
- ANSI Z89.1–2009, American National Standard for Industrial Head Protection,
- ANSI Z89.1–2003, American National Standard for Industrial Head Protection, or
- ANSI Z89.1–1997, American National Standard for Industrial Head Protection.
Training and maintenance for head PPE
- Employers must train employees in the use and care of the type of head protection they will be using.
- Helmets must be cleaned and inspected for damage regularly.
- Helmets must be stored properly.
The Occupational Health and Safety Administration (OSHA)’s general industry standard on personal protective equipment (PPE) at 1910.132 requires employee training that applies to the use of head protection. Employees must be trained to know:
- When PPE is necessary.
- What PPE is necessary.
- How to properly don, doff, adjust, and wear PPE.
- The limitations of the PPE.
- The proper care, maintenance, useful life, and disposal of the PPE.
There are no specific training requirements for head protection in the OSHA regulations. However, it is important to train employees in the proper use and care of their helmets.
During hard hat safety training, employers should review the types of head hazards most commonly found at their work areas and the proper head protection for those hazards.
Maintenance and inspection requirements
For helmets, employees should clean the shell with hot water and a mild detergent, then rinse with clear water. When the helmet is dry, the inspector should check for signs of cracks, penetration, or other damage due to rough treatment or wear. It’s a good idea to inspect the helmet daily, or prior to each use. If the helmet is damaged, it should not be worn. Employers should consult the manufacturer before painting a helmet shell or using a solvent to clean it. Some paints and solvents may damage the shell and reduce its protective level.
Holes should never be drilled or punched in a helmet shell for ventilation. This only serves to reduce the helmet’s ability to sustain impact. Class E helmets must never have holes drilled in the shell or any added accessory that contains metal.
Employees must not store a safety helmet on the rear window shelf of a vehicle. Overexposure to ultraviolet light such as sunlight and extreme heat may cause the shell to deteriorate.
A snug fitting helmet liner can be worn to protect the head, ears, and neck in cold weather.
Hearing protection
- OSHA’s hearing conservation program applies to employers in General Industry whose employees are exposed to noise at a certain level.
- Employers must develop and administer an effective hearing conservation program for all employees who are exposed to noise at a certain level, to include providing hearing protectors at no charge.
- Employers must establish and maintain an audiometric testing program where excessive noise is present in the workplace.
Noise, or unwanted sound, is one of the most pervasive occupational health problems. Noise is a by-product of many industrial processes. Sound consists of pressure changes in a medium (usually air) that are caused by vibration or turbulence. These pressure changes produce waves emanating away from the turbulent or vibrating source. Exposure to high levels of noise causes hearing loss and may cause other harmful health effects as well. The extent of damage depends primarily on the intensity of the noise and the duration of the exposure.
The Occupational Health and Safety Administration (OSHA) requires employers to determine if workers are exposed to excessive noise in the workplace and, if so, to implement feasible engineering or administrative controls to eliminate or reduce hazardous levels of noise. Where controls are not sufficient, employers must implement an effective hearing conservation program.
OSHA’s standard for hearing protection in the workplace is detailed in 1910.95.
What are the PPE requirements for hearing protection?
OSHA’s hearing conservation program is designed to protect general industry employees, such as those working in the manufacturing, utilities, and service sectors. It does not cover the construction or the oil and gas well drilling and servicing industries. General industry employers with certain noise levels are required to take certain actions:
- Time-weighted average (TWA) exposures at or above the action level of 85 dBA or, equivalently, a dose of 50 percent, require a hearing conservation program.
- Time-weighted average (TWA) exposures exceeding the PEL (90 dBA as an eight-hour TWA, see Table G-16) require feasible engineering or administrative controls to be implemented.
Who must comply?
Employers must provide employees with hearing protection if they will be exposed to excessive noise in the workplace. To be in compliance, employers should:
- Administer a continuing, effective hearing conservation program IF employee noise exposures equal or exceed an eight-hour time-weighted average sound level (TWA) of 85 decibels measured on the A scale (slow response); OR equivalently, a dose of 50 percent.
- Institute a training program for all employees who are exposed to noise at or above an eight-hour time-weighted average of 85 decibels, and ensure employee participation in such program.
- Make copies of 1910.95 available to affected employees or their representatives and post a copy in the workplace.
- Use feasible administrative or engineering controls where needed.
- Establish and maintain an audiometric testing program by making audiometric testing available to all employees whose exposures equal or exceed an eight-hour time-weighted average of 85 decibels.
- Develop and implement a monitoring program if information indicates that any employee’s exposure may equal or exceed an eight-hour time-weighted average of 85 decibels.
- Maintain an accurate record of all employee exposure measurements required.
- Make hearing protectors available, at no cost, to all employees exposed to an eight-hour time-weighted average of 85 decibels or greater.
- Evaluate hearing protector attenuation for the specific noise environments in which the protector will be used.
What is the PPE (noise) standard?
- The OSHA standard for noise exposure and protection is found at 1910.95
Per the Occupational Health and Safety Administration (OSHA) 1910.95:
Protection against the effects of noise exposure shall be provided when the sound levels exceed those shown in Table G-16 when measured on the A scale of a standard sound level meter at slow response. When noise levels are determined by octave band analysis, the equivalent A-weighted sound level may be determined as follows:
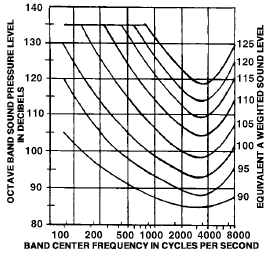 |
FIGURE G-9 Equivalent sound level contours. Octave band sound pressure levels may be converted to the equivalent A-weighted sound level by plotting them on this graph and noting the A-weighted sound level corresponding to the point of highest penetration into the sound level contours. This equivalent A-weighted sound level, which may differ from the actual A-weighted sound level of the noise, is used to determine exposure limits from Table 1.G-16. |
When employees are subjected to sound exceeding those listed in Table G-16, feasible administrative or engineering controls shall be utilized. If such controls fail to reduce sound levels within the levels of Table G-16, personal protective equipment shall be provided and used to reduce sound levels within the levels of the table.
- If the variations in noise level involve maxima at intervals of 1 second or less, it is to be considered continuous.
What are the types of hearing protection?
- The two main types of hearing protectors are ear plug and earmuffs.
- Employers should consider what level of noise employees are exposed to, and what the right hearing protection devices are for those conditions.
- Employers must ensure that the sound meters and dosimeters that are used to measure workplace noise levels meet ANSI standards.
There are two types of hearing protectors: ear plugs and earmuffs. Both types reduce the pressure of sound that reaches the eardrum and are the next line of defense when noise levels can’t be reduced to safe levels with engineering or administrative controls.
What are the criteria for hearing protection?
Some factors employers should consider when selecting the right hearing protection devices (HPDs) include:
- Noise hazard—how much noise will workers be dealing with?
- Noise frequency—will it be continuous or intermittent? (Some earplugs or muffs reduce the force of noise better at lower frequencies than at higher frequencies.)
- Fit and comfort—protective devices must fit properly and be comfortable enough to wear for as long as they are needed.
- Noise Reduction Rating (NRR)—All hearing protectors carry a label indicating the NRR; a higher number on the label means more effectiveness.
HPDs filter out loud noise. They do not block out sound completely, but they reduce the amount of sound reaching the delicate parts of the ear. By doing so, HPDs offer some protection so that hearing will not get overloaded by the surrounding noises (glare) that interfere with speech and machinery sounds.
ANSI standards for sound meters
Sound level meters used by the Occupational Health and Safety Administration (OSHA) meet the American National Standards Institute (ANSI) Standard S1.4 “Specifications for Sound Level Meters.” The ANSI standard sets performance and accuracy tolerances according to three levels of precision: Types 0, 1, and 2. Type 0 is used in laboratories, Type 1 is used for precision measurements in the field, and Type 2 is used for general-purpose measurements.
For compliance purposes, readings with an ANSI Type 2 sound level meter and dosimeter are considered to have an accuracy of ±2 dBA, while a Type 1 instrument has an accuracy of ±1 dBA.
A Type 2 meter is the minimum requirement by OSHA for noise measurements and is usually sufficient for general purpose noise surveys.
The Type 1 meter is preferred for the design of cost-effective noise controls.
For unusual measurement situations, employers should refer to the manufacturer’s instructions and appropriate ANSI standards for guidance in interpreting instrument accuracy.
Dosimeter
Like a sound level meter, a noise dosimeter can also measure sound levels. Unlike a sound level meter, the dosimeter is actually worn by the employee in order to determine the personal noise dose during the workshift or sampling period. Dosimeters can be used to:
- Take compliance measurements according to OSHA’s noise standard.
- Measure the employee’s exposure to noise and automatically compute the necessary noise dose calculations.
Factors to consider with the use of a dosimeter include:
- The microphone must be placed in the employee’s hearing zone. OSHA defines the hearing zone as a sphere with a two-foot diameter surrounding the head.
- The user must select specific instrument settings for the dosimeter.
- Special considerations may be involved with the use and care of a dosimeter.
ANSI standards for personal dosimeters
The ANSI standard for personal dosimeters is S1.25-1991, “Specifications for Personal Noise Dosimeters.” Some older dosimeters only meet the 1978 version of this standard. The 1978 version was not intended for measuring noise that is predominantly impulsive. For noise that is impulsive in nature, a dosimeter meeting the 1991 version of the standard is recommended.
Octave-band analyzers
Octave-band analyzers are sound level meters that can be used to:
- Help determine the adequacy of various types of frequency-dependent noise controls.
- Select hearing protectors because they can measure the amount of attenuation (how much a sound is weakened) offered by the protectors in the octave bands responsible for most of the sound energy in a given situation.
- Divide noise into its frequency components.
Some sound level meters may have an octave or one-third octave band filter attached or integrated into the instrument. Usually a Type 1 (precision) sound level meter is used for octave and one-third octave analysis.
The filters are used to analyze the frequency content of noise. They are also valuable for the calibration of audiometers and to determine the adequacy of various types of noise control.
Frequency components may include:
- Most octave-band filter sets provide filters with the following center frequencies: 31.5, 63, 125, 250, 500, 1,000, 2,000, 4,000, 8,000, and 16,000 Hertz (Hz).
For a more detailed analysis, the spectrum is sometimes measured in one-third octave bands.
The special signature of any given noise can be obtained by taking sound level meter readings at each of the center frequency bands. The results may indicate octave bands that contain most of the total sound power being radiated.
Training and maintenance for hearing PPE
- Employers must train employees on the effects of excess noise on hearing, the purpose and use of hearing protection, and the purpose of audiometric testing.
- Employers must train employees to properly care for and maintain hearing protection devices.
Workers exposed to time-weighted averages (TWAs) of 85 dB and above must be trained every year in:
- The effects of noise,
- The purpose, advantages, disadvantages, and attenuation of various types of hearing protectors,
- The selection, fitting, and care of protectors, and
- The purpose and procedures of audiometric testing.
The training requirements are found at 1910.95(k)—Training programs; 1910.95(l)—Access to information and training materials; and 1910.95(i)(4)—The employer shall provide training in the use and care of all hearing protectors provided to employees. The Occupational Health and Safety Administration (OSHA) requires employers to establish a training program for all employees with noise exposures at or above the action level and ensure employee participation. Training must be repeated annually for each employee in the hearing conservation program and the information must be updated to be consistent with changes in protective equipment and work processes.
The employer must ensure that each employee is informed of the following:
- The effects of noise on hearing.
- The purpose of hearing protectors, the advantages, disadvantages, and attenuation of various types, and instructions on selection, fitting, use, and care.
- The purpose of audiometric testing and an explanation of test procedures.
Employers must also train employees on the proper care and maintenance of their hearing protection.
Hearing protection
See the "Hearing Conservation and Noise" section of this In Depth tab.
Electrical protective equipment
- The OSHA standard for electrical protective equipment applies to all General Industry employers whose employees are exposed to electricity hazards in the workplace.
- Protective equipment may include safety shoes, insulated gloves, flame-resistant clothing, rubber hoods and blankets and insulating live-line tools.
- Any electrical protective equipment must be tested and certified.
Employees in a variety of industries work with or around electrical hazards. The Occupational Health and Safety Administration (OSHA) requires employers to protect these employees through a variety of methods and means, including, in some cases, the use of protective equipment — some of which is worn by employees and some equipment that is not worn.
Depending on the job task to be performed, PPE for the electric power industry generally includes safety glasses, face shields, hard hats, safety shoes, insulating (rubber) gloves with leather protectors, insulating sleeves, and flame-resistant (FR) clothing. In addition to PPE, electric power workers often use Insulating Protective Equipment (IPE), such as line hoses, rubber hoods, rubber blankets, and insulating live-line tools (for example, hotsticks, switchsticks, or shotgun sticks) for protection. However, since IPE is not worn, it is technically not considered to be PPE.
OSHA’s standard for electrical protective equipment is detailed in 1910.137.
What are the PPE requirements for electrical protective equipment?
Employers covered under the head protection standard should:
- Assess the workplace for work/hazards that would require the use of electrical protective equipment.
- Provide electrical protective equipment suitable for the hazard, task, and exposure.
- Certify that the electrical protective equipment used by workers have passed the tests specified in 1910.137. The certification must identify the equipment that passed the tests and the dates of the tests.
- Maintain equipment in proper and safe working condition.
- Immediately remove defective or damaged equipment.
Who must comply?
OSHA’s electrical protective equipment requirements apply to all general industry employers who have employees with such exposures. The type of work, type of electrical hazard, and other factors determine which specific protections are needed and applicable. The primary electrical protective equipment requirement covers how this equipment must be designed, maintained, and tested. However, various other OSHA General Industry regulations specify where and when this protective equipment must be used to protect workers.
What are the criteria, training and maintenance requirements for electrical protective equipment?
- Electrical protective equipment may include various rubber insulated items and flame-resistant clothing, and must meet OSHA requirements as defined in 1910.137(a).
- Employers must provide proper training to employees who work with or around electricity.
- Employers must ensure that electrical protective equipment is maintained and is properly cleaned and stored.
Electrical protective equipment can include rubber insulating:
Protective equipment may also include flame-resistant (FR) clothing, which is often used for protection from arc flashes, that has been designed and tested to provide protection against specified electrical/heat hazards.
What are the criteria for electrical protective equipment?
Electrical protective equipment must meet the Occupational Health and Safety Administration (OSHA)’s requirements set out at 1910.137(a). Rubber insulating blankets, rubber insulating matting, rubber insulating covers, rubber insulating line hoses, rubber insulating gloves, and rubber insulating sleeves must meet stringent requirements to ensure safety. This includes being:
- Produced by a seamless process.
- Clearly marked with the “class” and “type” of protection (e.g., Class 00 equipment should be marked Class 00).
- Designed to meet electrical requirements, such as withstanding the AC proof-test voltage specified in Table I-1 or the DC proof-test voltage specified in Table I-2 of OSHA’s requirements.
- Free of physical irregularities or imperfections.
- Capable of withstanding the voltages that may be imposed.
- Passing a current test as specified in the requirements.
Training, maintenance and inspection requirements
Training requirements for employees working with or around electricity are at 1910.332—Electrical Training. The training requirements cover:
- General requirements (safety-related work practices required by 1910.331 through 1910.335) that pertain to an employee’s respective job assignment,
- Additional requirements for unqualified persons, and
- Additional training for qualified employees.
Employers must ensure that electrical protective equipment is maintained in a safe, reliable condition. This includes ensuring maximum use voltages conform to those listed in the requirements, inspecting insulating equipment for damage each day and after incidents, removing defective equipment, cleaning the equipment, and storing the equipment properly.
PPE for respiratory protection
- Employers should eliminate or reduce atmospheric hazards in the workplace such as dust, smoke, fumes, vapors and more.
- Respiratory protection must be supplied to all employees when atmospheric hazards are present.
Hazards to the lungs are not always easy to detect. Some of the most common hazards are the lack of oxygen and the presence of harmful dust, fogs, smokes, mists, fumes, gases, vapors, or sprays including substances that may cause cancer, lung impairment, other diseases, or death. In these instances, respiratory protection is necessary to prevent these harmful substances from entering the lungs during breathing. Some respirators contain filters to catch and contain the contaminants while others provide a separate supply of breathable air so work can be performed where there is inadequate oxygen, or where greater protection is needed.
Eliminating or reducing atmospheric hazards through engineering controls is the first step an employer should take, such as enclosing or confining the contaminant-producing operation, exhausting the contaminant, or substituting a chemical with a less toxic material. However, in instances where effective engineering controls are not feasible, while those controls are being installed, or during clean-up operations, appropriate respiratory protection must be provided to exposed employees.
The employer needs to understand that respirators do have limitations and are not substitutes for effective engineering controls or work practices. Where respirators are necessary for health protection, a specific written plan and procedures are necessary to ensure the effectiveness of the equipment and the safety of the employees using it.
Employers are responsible for establishing an effective respirator program — different hazards require different respirators — and employees are responsible for wearing the respirators and complying with the employer’s program.
The Occupational Safety and Health Administration (OSHA) standard for respiratory protection is detailed in 1910.134 — Respiratory protection, and appendices (Appendix A — Fit Testing Procedures, Appendix B-1 — User Seal Check Procedures, Appendix B-2 — Respirator Cleaning Procedures, Appendix C — OSHA Respirator Medical Evaluation Questionnaire, and Appendix D — Information for Employees Using Respirators When Not Required Under Standard).
What are the PPE requirements for respiratory protection, and who must comply?
- The OSHA standard for respiratory protection applies to all General Industry employers whose employees are exposed to respiratory hazards in the workplace.
- Employers must develop a written respiratory protection program, conduct evaluations of the workplace, train employees on respiratory protection, fit-test employees regularly, and other requirements.
The Occupational Health and Safety Administration (OSHA)’s respiratory protection standard applies to General Industry employers who have employees exposed to hazards for which respiratory protection is required or used voluntarily (there are limited employer requirements for certain voluntary use).
Respirators are devices that prevent the entry of harmful substances into the lungs. The two basic types of respirators are: (1) air purifying—these remove hazardous substances from the breathing air, and (2) atmosphere supplying—these deliver safe breathing air from an outside source.
Employers who are covered under this standard must:
- Identify and evaluate the respiratory hazard(s) in the workplace.
- Develop and implement a written respiratory protection program with required worksite-specific procedures and elements for required respirator use.
- Designate a program administrator to administer the respiratory protection program.
- Conduct evaluations of the workplace as necessary to ensure that the provisions of the current written program are being effectively implemented, and that it continues to be effective.
- Select and provide appropriate respirators.
- Train employees on respiratory protection.
- Provide a medical evaluation to determine the employee’s ability to use a respirator, including N95 (dust masks) if required to be used.
- Identify a physician or other licensed health care professional to perform medical evaluations.
- Fit test employees initially and at least annually thereafter with the same make, model, style, and size of respirator that will be used. This applies to all tight-fitting respirators, including N95 (dust masks) if required to be used.
- Clean and disinfect respirators per the OSHA requirements.
- Store all respirators to protect them from damage, contamination, dust, sunlight, extreme temperatures, excessive moisture, and damaging chemicals.
- Use compressed air, compressed oxygen, liquid air, and liquid oxygen for respiration that meets OSHA specifications.
- Retain records of medical evaluations required by 1910.134, and make them available in accordance with 1910.1020.
- Establish a record of the qualitative and quantitative fit tests administered to an employee.
- Retain fit test records for respirator users until the next fit test is administered.
- Retain a written copy of the current respirator program.
- Provide any retained written materials, upon request, to affected employees and to OSHA or designee for examination and copying.
- Ensure any voluntary respirator use is done in a way that poses no hazards to the worker. Also provide a copy of Appendix D from the Respiratory Protection standard to all voluntary respirator users.
Voluntary respirator use
- If an employer chooses to have employees wear a dust mask, or an employee chooses to wear one even when not required, this is considered voluntary use.
If a workplace is covered by the respirator protection standard, the employer must establish a written respiratory protection program. In addition, the employer must include elements in the program to ensure that employees:
- Are medically able to use that respirator,
- Maintain and keep their respirators clean, and
- Know where to store their respirators.
Exception: Employers are not required to include in a written respiratory protection program for employees whose only use of respirators involves the voluntary use of filtering facepieces (dust masks).
Dust masks
Disposable paper respirators, or dust masks, are still considered “respirators” and their use is regulated under the Occupational Health and Safety Administration (OSHA)’s Respiratory Protection Standard. However, in many cases, respirators are not required by OSHA because exposures are below official exposure limits.
If an employer chooses to have employees wear a dust mask even though the use of a dust mask or any other respirator is not required, it’s considered “voluntary use.” OSHA allows this without a medical evaluation, fit test, or clean shave, IF it is determined that wearing the dust mask will not in itself create a hazard or interfere with an employee’s ability to work safely.
If the employer determines that any voluntary dust mask use is permissible, employees must be provided with the information found in 1910.134 Appendix D so they understand how to select, use, and care for dust masks properly.
Training and maintenance for respiratory PPE
- Employers must train employees on the types of respiratory protection that they will be using, and the limitations of such equipment. Employees who are working in atmospheres immediately dangerous to life or health should also be trained in rescue procedures.
- Respiratory protection must be cleaned and disinfected regularly, inspected for damage, and properly stored when not in use.
- Employers must provide written schedules and procedures for these activities.
Training is essential for correct respirator use. Employers must teach both supervisors and employees how to properly select, use, and maintain respirators. The training program should be developed based on employees’ education level and language background.
All employees required to use respiratory protective equipment must be trained in the proper use of the equipment and its limitations. Additionally, those employees who will be required to use respiratory protective equipment in atmospheres immediately dangerous to life or health should be trained in rescue procedures.
The training must include instructions on fitting and how to check the facepiece-to-face seal. The employee must be given an opportunity to handle the respirator, wear it in normal air for a period of time to become familiar with it, practice adjusting it, and then wear it in a test atmosphere.
The Occupational Health and Safety Administration (OSHA) requires that employee respirator training must include an explanation of the following:
- Why the respirator is necessary, including the nature of the respiratory hazard and what may happen if the respirator is not fitted, used, or maintained properly;
- Engineering and administrative controls being used and the need for the respirator as added protection;
- Reason(s) for selecting a particular type of respirator;
- Capabilities and limitations of the selected respirator;
- How to inspect, put on and remove, and check the seals of the respirator;
- Respirator maintenance and storage requirements;
- How to use the respirator effectively in emergency situations, including when the respirator malfunctions; and
- How to recognize medical signs and symptoms that may limit or prevent the effective use of the respirator.
Users should know that improper respirator use or maintenance may cause overexposure. They also need to understand that continued use of poorly fitted and maintained respirators can cause chronic disease or death from overexposure to air contaminants.
Maintenance and inspection requirements
Thorough training in care and maintenance of respirators will help keep the program running smoothly for a long time. Employers should make sure to have sufficient equipment and supplies to provide for the cleaning and disinfecting, storage, inspection, and repair of respirators. The written program must include schedules and procedures for these activities. OSHA provides procedures for cleaning and disinfecting respirators in Appendix B-2 of the Respiratory Protection regulation. If manufacturer recommended procedures are used, they must be equally effective.
Personal protective equipment for Construction
- PPE includes any clothing, accessories and equipment that helps protect workers from workplace hazards.
- PPE should be the last line of defense against workplace injuries; implementing engineering controls to eliminate hazards in the first place should take precedence.
- Using PPE improperly can be worse than using no protection at all.
Personal protective equipment in construction includes all clothing and accessories designed to create a barrier against workplace hazards. The basic element of any PPE management program should be an in-depth evaluation of the equipment needed to protect against the hazards at the workplace.
Much of this PPE information is framed in general terms and is intended to complement relevant regulations and manufacturers’ requirements. While PPE is part of the job in some industries — face shields for welding — as a rule, it is considered a last-resort, temporary type of protection. For normal operations, first choice will always be given to eliminating the hazard in the environment rather than using PPE. This is called implementing engineering controls.
No single combination of protective equipment and clothing can protect against all hazards. Thus, PPE should be used in conjunction with other protective methods. The use of PPE can itself create significant worker hazards, such as heat stress, physical and psychological stress, and impaired vision, mobility, and communication.
In general, the greater the level of PPE protection, the greater are the associated risks. For any given situation, equipment and clothing should be selected that provide an adequate level of protection. Over-protection as well as under-protection can be hazardous and should be avoided.
Using PPE improperly or in a manner unsuited to its design and purpose is worse than using no protection at all. Without any protection, the worker knows he is vulnerable and perhaps, takes precautions. With some protection, the worker may rashly blunder into severe difficulty, thinking he is safe.
The OSHA standard for PPE for Construction is detailed in 1926.95. (Effective January 13, 2025, OSHA amended the regulation to include "proper fit" in the design and selection of PPE)
Employers’ responsibility for PPE training and provision
- Employers must provide training to their employees on who is required to use PPE, how to use it, and how to care for it.
- Required PPE must be provided by the employer with no cost to employees, with certain exceptions.
The first step that employers must take to determine what exposures warrant PPE is to do a hazard assessment of the workplace. Although doing a hazard assessment is not a specific and recordable requirement for Construction (as it is for General Industry), it is an excellent way to identify jobsite hazards and provide the appropriate PPE.
Employers are required to train employees who must use PPE. Employees must be trained to know at least the following:
- When PPE is necessary.
- What PPE is necessary.
- How to properly put on, take off, adjust and wear the PPE.
- The limitations of the PPE.
- Proper care, maintenance, useful life, and disposal of PPE.
Employers should make sure that each employee demonstrates an understanding of the PPE training as well as the ability to properly wear and use PPE before they are allowed to perform work requiring the use of the PPE.
Payment for personal protective equipment
The employer is responsible to provide and pay for any personal protective equipment that is required in order to comply with one of the PPE requirements in the Occupational Health and Safety Administration (OSHA)’s standards. If the PPE is not required, then the employer doesn’t have to pay for it. When an employer selects a specific type of PPE to be used at the workplace to comply with a standard, the employer is required to pay for it.
OSHA also says that the employer is not required to pay for non-specialty safety-toe protective footwear (including steel-toe shoes or steel-toe boots) and non-specialty prescription safety eyewear, provided that the employer permits these items to be worn off the jobsite.
If the employer requires employees to keep non-specialty safety-toe protective footwear and non-specialty prescription safety eyewear at the workplace, the employer must pay for the items.
If the safety-toe protective footwear (including steel-toe shoes or steel-toe boots) and prescription safety eyewear are non-standard “specialty” items, the employer must pay for them. For example, prescription eyeglass inserts for full-facepiece respirators and non-skid shoes for floor strippers are specialty items, so payment will be required.
OSHA allows employers to use metatarsal guards or footwear with built-in metatarsal protection when metatarsal protection is needed in the workplace. If the employer requires employees to wear metatarsal shoes or boots, the employer must pay for the footwear.
However, when the employer provides metatarsal guards and allows the employee, at their request, to use shoes or boots with built-in metatarsal protection, the employer is not required to pay for the metatarsal shoes or boots.
Employers may contribute to the cost of metatarsal shoes or boots. Some employers may offer their employees a choice between using a metatarsal guard provided and paid for by the employer or a metatarsal shoe or boot with some portion of the cost of the shoe or boot paid for by the employer, essentially establishing an allowance system. OSHA believes this to be an acceptable practice.
Employers are not required to pay for everyday clothing, such as long-sleeve shirts, long pants, street shoes, and normal work boots. This exception applies even when the employer requires employees to use these items, and the clothing provides protection from a workplace hazard.
Similarly, employers are not required to pay for ordinary clothing, skin creams, or other items used solely for protection from weather, such as:
- Winter coats, jackets, gloves, parkas;
- Rubber boots, hats, raincoats;
- Ordinary sunglasses; and
- Sunscreen.
If ordinary weather gear does not provide sufficient protection and special equipment or extraordinary clothing is needed to protect the employee from unusually severe weather conditions, the employer is required to pay for the protection.
Where an employee provides adequate protective equipment that is personally owned and brings to the worksite, the employer may allow the employee to use it and is not required to reimburse the employee for that equipment. However, the employer cannot require an employee to provide or pay for PPE, unless there is an exception in the rule.
PPE for eye and face protection
- The OSHA standard for eye and face protection applies to Construction employers whose employees are exposed to certain hazards in the workplace.
- Employers must provide eye and face protection at no cost to employees whenever certain hazards are present.
- Eye and face protection must meet one of three editions of ANSI Z87.1 (2010, 2003, or 1989-Rev1998)
Employees can be exposed to many hazards that pose danger to their eyes and face. The Occupational Health and Safety Administration (OSHA) requires employers to ensure that employees have appropriate eye or face protection if they are exposed to eye or face hazards from flying particles, molten metal, liquid chemicals, acids or caustic liquids, chemical gases or vapors, potentially infected material, or potentially harmful light radiation.
The OSHA standard for eye and face protection is detailed in 1926.102.
What are the PPE requirements for eye and face protection?
OSHA requires employers covered by the standard to:
- Select eye and face protection suitable to the hazard (e.g., impact, heat, chemicals, dust, radiation) that meets one of three editions of American National Standards Institute (ANSI) Z87.1 (2010, 2003, and 1989-Rev1998).
- Ensure employees use eye protection that provides side protection when there is a hazard from flying objects. Detachable side protectors (e.g., clip-on or slide-on side shields) are acceptable.
- Provide eye and face protection at no cost to the employee, except for non-specialty prescription safety eyewear — provided it is allowed to be worn off the job.
- Ensure employees who require corrective lenses either use goggles/spectacles over their regular glasses or use safety spectacles/goggles that incorporate the employee’s prescription.
- Train employees on how to use, care for, and inspect their eye and face protection.
Who must comply?
The OSHA standard for eye and face protection applies to all Construction employers with workers exposed to eye or face hazards from flying particles, molten metal, liquid chemicals, acids or caustic liquids, chemical gases or vapors, potentially infected material, or potentially harmful light radiation.
What are the types of eye and face protection?
- The main types of eye and face protection include face shields, safety spectacles and goggles, and side shields.
- Each type of protection comes in several styles depending on the hazard and the needs of the user.
Selecting the most suitable eye and face protection for employees should take into consideration the following elements:
- Ability to protect against specific workplace hazards.
- Should fit properly and be reasonably comfortable to wear.
- Should provide unrestricted vision and movement.
- Should be durable and cleanable.
- Should allow unrestricted functioning of any other required PPE.
The eye and face protection selected for employee use must clearly identify the manufacturer.
An employer may choose to provide one pair of protective eyewear for each position rather than individual eyewear for each employee. If this is done, the employer must make sure that employees disinfect shared protective eyewear after each use. Protective eyewear with corrective lenses may only be used by the employee for whom the corrective prescription was issued and may not be shared among employees. Some of the most common types of eye and face protection include:
Safety spectacles: These protective eyeglasses have safety frames constructed of metal or plastic and impact-resistant lenses. Side shields are available on some models.
Goggles: These are a type of tight-fitting eye protection that completely covers the eyes, eye sockets, and the facial area immediately surrounding the eyes and provide protection from impact, dust, and splashes. Some goggles will fit over corrective lenses.
Welding shields: Constructed of vulcanized fiber or fiberglass and fitted with a filtered lens, welding shields protect eyes from burns caused by infrared or intense radiant light; they also protect both the eyes and face from flying sparks, metal spatter, and slag chips produced during welding, brazing, soldering, and cutting operations. The Occupational Health and Safety Administration (OSHA) requires filter lenses to have a shade number appropriate to protect against the specific hazards of the work being performed in order to protect against harmful light radiation.
Laser safety goggles: These specialty goggles protect against intense concentrations of light produced by lasers. The type of laser safety goggles an employer chooses will depend upon the equipment and operating conditions in the workplace.
Face shields: These transparent sheets of plastic extend from the eyebrows to below the chin and across the entire width of the employee’s head. Some are polarized for glare protection. Face shields protect against nuisance dusts and potential splashes or sprays of hazardous liquids but will not provide adequate protection against impact hazards. Face shields used in combination with goggles or safety spectacles will provide additional protection against impact hazards.
Each type of protective eyewear is designed to protect against specific hazards. Employers can identify the specific workplace hazards that threaten employees’ eyes and faces by completing a hazard assessment.
Welding operations
The intense light associated with welding operations can cause serious and sometimes permanent eye damage if operators do not wear proper eye protection. The intensity of light or radiant energy produced by welding, cutting, or brazing operations varies according to several factors including the task producing the light, the electrode size, and the arc current.
Laser operations
Laser light radiation can be extremely dangerous to the unprotected eye and direct or reflected beams can cause permanent eye damage. Laser retinal burns can be painless, so it is essential that all personnel in or around laser operations wear appropriate eye protection.
Laser safety goggles should protect for the specific wavelength of the laser and must be of sufficient optical density for the energy involved. Safety goggles intended for use with laser beams must be labeled with the laser wavelengths for which they are intended to be used, the optical density of those wavelengths, and the visible light transmission.
What are the criteria for eye and face protection?
Eye and face protection equipment must meet the requirements specified in any of these American National Standards Institute (ANSI)/International Safety Equipment Association (ISEA) standards:
- ANSI/ISEA Z87.1-2010, Occupational and Educational Personal Eye and Face Protection Devices, Approved April 3, 2010; IBR approved for 1926.102(b).
- ANSI Z87.1-2003, Occupational and Educational Personal Eye and Face Protection Devices, Approved June 19, 2003; IBR approved for 1926.102(b).
- ANSI Z87.1-1989 (R-1998), Practice for Occupational and Educational Eye and Face Protection, Reaffirmation approved January 4, 1999; IBR approved for 1926.102(b).
The American National Standard for Occupational and Educational Personal Eye and Face Protection, ANSI/ISEA Z87.1-2015, provides guidelines for occupational eye and face protection devices including safety glasses/goggles, face shields, and welding helmets.
That version emphasizes the need to maintain requirements that reflect safety standards used in other countries, including the ability of the equipment to withstand impacts, and the level of protection that welding helmets provide. It also addresses evolving technologies and new safety hazards that may be produced by these technologies.
OSHA incorporates ANSI/ISEA Z87 into its regulations covering personal protective equipment. The updated standard is available from ANSI.
PPE for hearing protection
- Employers must provide hearing protection when their employees are exposed to workplace noise at a certain level.
- Employers must develop and administer an effective hearing conservation program for all employees who are exposed to noise at a certain level, to include providing hearing protectors at no charge.
Employers with employees working in areas where there is the possibility of exposure to sound levels exceeding those listed in Table D-2 must comply.
Excessive sound levels on construction sites are recognized by medical professionals and the Occupational Health and Safety Administration (OSHA) as an occupational hazard that can cause temporary or permanent hearing loss, stress, and other physical problems.
OSHA’s standard for hearing protection is detailed in 1926.52.
Employers covered by the standard must:
- Assess the workplace for areas where exposure to sound levels could exceed those listed in Table D-2.
- Implement administrative or engineering controls to control the sound levels.
- If administrative or engineering controls fail to reduce sound levels within the levels Table D-2, select appropriate hearing protection to reduce sound levels.
- Provide and require employees to wear hearing protection at no cost to the employee.
- Implement a hearing conservation program where sound levels exceed the Permissible Noise Exposures in Table D-2.
Table D-2—Permissible noise exposuresDuration per day, hours | Sound level dBA slow response |
---|
8 | 90 |
6 | 92 |
4 | 95 |
3 | 97 |
2 | 100 |
1 1/2 | 102 |
1 | 105 |
1/2 | 110 |
1/4 or less | 115 |
What are the types of hearing protection?
- The two main types of hearing protectors are ear plug and earmuffs.
- Employers should consider what level of noise employees are exposed to, and what the right hearing protection devices are for those conditions.
Some types of hearing protection include:
- Single-use earplugs are made of foam, silicone rubber, or fiberglass wool. They are self-forming and, when properly inserted, work as well as most molded earplugs.
- Pre-formed or molded earplugs must be individually fitted by a professional and can be disposable or reusable. Reusable plugs should be cleaned after each use.
- Earmuffs require a perfect seal around the ear. Glasses, facial hair, long hair, or facial movements (such as chewing) may reduce the protective value of earmuffs.
What are the criteria for hearing protection?
Hearing protectors reduce only the amount of noise that gets through to the ears. The amount of this reduction is referred to as attenuation, which differs according to the type of hearing protection used and how well it fits. Hearing protectors worn by employees must reduce an employee’s noise exposure to within the acceptable limits. Thus, employers must ensure that hearing protection meets the criteria to reduce noise exposure to acceptable limits.
Training and maintenance for hearing PPE
- Employers must train employees on the effects of excess noise on hearing, the purpose and use of hearing protection, the purpose of audiometric testing, and more.
- Employers must train employees to properly care for and maintain hearing protection devices.
Within a hearing conservation program, each employer must instruct each employee in the recognition and avoidance of unsafe conditions and the regulations applicable to the work environment to control or eliminate any hazards or other exposure to illness or injury.
An effective training program should be updated when protective equipment, work processes, or regulations change. It might include:
- Effects of noise and duration of noise on hearing;
- A discussion of any engineering and administrative controls implemented at the site.
- An explanation of the purpose of hearing protectors and the advantages, disadvantages, and attenuation of various types;
- Instructions on selection, fitting, use, and care of hearing protectors;
- An explanation of the purpose of audiometric testing and an explanation of test procedures;
- How to recognize and avoid unsafe conditions;
- The regulations 1926.52 and 1926.101 as they apply to each employee’s work environment; and
- How to control or eliminate any exposure.
Maintenance and inspection requirements
Employers must ensure that employees inspect their hearing protection for deficiencies. In addition, they must understand how to care for and replace their hearing protection when necessary.
Employers must ensure that employees inspect their hearing protection for deficiencies. In addition, they must understand how to care for and replace their hearing protection when necessary.
PPE for hand protection
- Employers must provide PPE to protect workers’ hands from cuts, burns, and chemical exposure.
- Employers must train employees to recognize the specific hazards their employees may be exposed to.
- Employers must train employees on proper use, care and maintenance of whichever type of hand protection they will use.
Employers with employees who could be exposed to hazards to the hands must provide hand protection.
Hand protection is extremely important in construction work, as employees can be exposed to hazards such as skin absorption of harmful substances, severe cuts or lacerations, severe abrasions, punctures, chemical burns, or harmful temperature extremes.
There isn’t a specific Occupational Health and Safety Administration (OSHA) construction rule requiring hand protection. However, OSHA does require at 1926.95(a) that “Protective equipment, including personal protective equipment for eyes, face, head, and extremities, protective clothing, respiratory devices, and protective shields and barriers, shall be provided, used, and maintained in a sanitary and reliable condition wherever it is necessary ... ”
In addition, 1926.21(b)(2) requires, “The employer shall instruct each employee in the recognition and avoidance of unsafe conditions and the regulations applicable to his work environment to control or eliminate any hazards or other exposure to illness or injury.”
Training, maintenance, and inspection requirements
Employers must train their employees on recognizing and avoiding unsafe conditions in the workplace. This includes training employees on how to control or eliminate hand-related hazards. In addition, employers must train their employees on how to properly select, use, and care for personal protective equipment.
Employers must also train employees on the various types of hand protection available on the jobsite and their various uses. In addition, employers should instruct employees on when they must care for their PPE, including how to inspect and maintain the equipment, to protect themselves from injury.
What are the types of hand protection?
- Gloves of various types and materials are the most common type of hand protection.
There are many types of gloves available to protect against a wide variety of hazards. The nature of the hazard and the operation involved will affect glove selection. The variety of potential occupational hand injuries makes selecting the right pair of gloves challenging. It is essential that employees use gloves specifically designed for the hazards and tasks found in their workplace because gloves designed for one function may not protect against a different function even though they may appear to be an appropriate protective device.
Gloves made from a wide variety of materials are designed for many types of workplace hazards, especially those found in the construction industry. In general, gloves fall into four groups:
- Gloves made of leather, canvas, or metal mesh.
- Fabric and coated fabric gloves.
- Chemical- and liquid-resistant gloves.
- Insulating rubber gloves.
Leather, canvas, or metal mesh gloves
- Sturdy gloves made from metal mesh, leather or canvas provide protection against cuts and burns. Leather or canvas gloves also protect against sustained heat.
- Leather gloves protect against sparks, moderate heat, blows, chips, and rough objects.
- Aluminized gloves provide reflective and insulating protection against heat and require an insert made of synthetic materials to protect against heat and cold.
- Aramid fiber gloves protect against heat and cold, are cut- and abrasive-resistant, and wear well.
- Synthetic gloves of various materials offer protection against heat and cold, are cut- and abrasive-resistant, and may withstand some diluted acids. These materials do not stand up against alkalis and solvents.
Fabric and coated fabric gloves
- Fabric and coated fabric gloves are made of cotton or other fabric to provide varying degrees of protection.
- Fabric gloves protect against dirt, slivers, chafing, and abrasions. They do not provide sufficient protection for use with rough, sharp, or heavy materials. Adding a plastic coating will strengthen some fabric gloves.
- Coated fabric gloves are normally made from cotton flannel with napping on one side. By coating the un-napped side with plastic, fabric gloves are transformed into general-purpose hand protection offering slip-resistant qualities. These gloves are used for tasks ranging from handling bricks and wire to chemical laboratory containers. When selecting gloves to protect against chemical exposure hazards, always check with the manufacturer or review the manufacturer’s product literature to determine the glove’s effectiveness against specific workplace chemicals and conditions.
Chemical- and liquid-resistant gloves
- Chemical-resistant gloves are made with different kinds of rubber: natural, butyl, neoprene, nitrile, and fluorocarbon (viton); or various kinds of plastic: polyvinyl chloride (PVC), polyvinyl alcohol, and polyethylene. These materials can be blended or laminated for better performance. Generally, the thicker the glove material, the greater the chemical resistance but thick gloves may impair grip and dexterity, having a negative impact on safety.
Some examples of chemical-resistant gloves include:
- Butyl gloves are made of a synthetic rubber and protect against a wide variety of chemicals, such as peroxide, rocket fuels, highly corrosive acids (nitric acid, sulfuric acid, hydrofluoric acid and red-fuming nitric acid), strong bases, alcohols, aldehydes, ketones, esters, and nitro-compounds. Butyl gloves also resist oxidation, ozone corrosion, and abrasion, and remain flexible at low temperatures. Butyl rubber does not perform well with aliphatic and aromatic hydrocarbons and halogenated solvents.
- Natural (latex) rubber gloves are comfortable to wear, which makes them a popular general-purpose glove. They feature outstanding tensile strength, elasticity, and temperature resistance. In addition to resisting abrasions caused by grinding and polishing, these gloves protect workers’ hands from most water solutions of acids, alkalis, salts, and ketones. Latex gloves have caused allergic reactions in some individuals and may not be appropriate for all employees. Hypoallergenic gloves, glove liners, and powderless gloves are possible alternatives for workers who are allergic to latex gloves.
- Neoprene gloves are made of synthetic rubber and offer good pliability, finger dexterity, high density, and tear resistance. They protect against hydraulic fluids, gasoline, alcohols, organic acids, and alkalis. They generally have chemical and wear resistance properties superior to those made of natural rubber.
- Nitrile gloves are made of a copolymer and provide protection from chlorinated solvents such as trichloroethylene and perchloroethylene. Although intended for jobs requiring dexterity and sensitivity, nitrile gloves stand up to heavy use even after prolonged exposure to substances that cause other gloves to deteriorate. They offer protection when working with oils, greases, acids, caustics, and alcohols but are generally not recommended for use with strong oxidizing agents, aromatic solvents, ketones, and acetates.
PPE for foot protection
- The OSHA standard for foot protection applies to all employers whose employees are exposed to certain hazards in the workplace.
- Employers must provide foot protection at no cost to employees whenever certain hazards are present.
- Foot protection must meet one of three industry standards: ANSI Z41-1991, ANSI-Z41 1999, or ASTM F-2412-2005 and F-2413-2005.
Employers must make sure that each affected employee uses protective footwear when working in areas where there is a danger of foot injuries due to falling or rolling objects, or objects piercing the sole, or when the use of protective footwear will protect the affected employee from an electrical hazard, such as a static-discharge or electric-shock hazard, that remains after the employer takes other necessary protective measures.
What are the PPE requirements for foot protection?
Employers who are covered by the standard must:
- Assess the workplace for areas where there is a danger of foot injuries due to falling or rolling objects, or objects piercing the sole, or when the use of protective footwear will protect the affected employee from an electrical hazard, such as a static-discharge or electric-shock hazard. NOTE: There isn’t a specific construction rule that requires a hazard assessment, like there is for General Industry. However, it is a best practice to complete one.
- Select footwear appropriate to the hazards of the job.
- Provide foot protection at no cost to the employee, except for non-specialty steel-toe shoes if the employer allows them to be taken off the jobsite.
- Ensure safety footwear meets one of four Occupational Safety and Health Administration (OSHA)-accepted industry standards (American National Standards Institute (ANSI) Z41-1991, ANSI-Z41 1999, or American Society for Testing and Materials (ASTM) F-2412-2005 and F-2413-2005) or Z41.1-1967.
- Train employees on the use, care, maintenance, and inspection of safety footwear.
Who must comply?
OSHA’s occupational foot protection rule (1926.96) applies to employers with employees who could be exposed to such hazards.
What are the types of foot protection?
- Types of foot protection include various styles of safety shoes, boots, and guards.
- Employers must train employees on the use and care of the specific type of foot protection that they will be using.
Safety shoes or boots with impact protection would be required for carrying or handling materials such as packages, objects, parts, or heavy tools which could be dropped, and for other activities where objects might fall onto the feet.
Safety shoes or boots with compression protection would be required for work activities involving equipment or materials (such as and heavy pipes) which could potentially roll over employees’ feet.
Safety shoes or boots with puncture protection would be required where sharp objects could be stepped on, causing a foot injury.
For protection of feet and legs from falling or rolling objects, sharp objects, hot tar, hot surfaces, and wet slippery surfaces workers should use appropriate footguards, safety shoes, or boots and leggings.
Aluminum alloy, fiberglass, or galvanized steel footguards can be worn over usual work shoes, although they present the possibility of catching on something and tripping workers.
Heat-resistant soled shoes protect against hot surfaces like those found in the roofing and paving industries.
Leggings protect the lower leg and feet from molten metal or welding sparks. Safety snaps permit their rapid removal.
Other foot and leg protection
Other options for protective footwear include:
- Shoes and boots with instep protection;
- Insulated boots for protection against extreme temperatures;
- Boots with built-in ankle protection;
- Rubber or plastic safety boots that are effective against water, oil, acids, corrosives, and chemicals;
- Foundry shoes with elastic gores rather than laces to provide easy removal in case sparks or hot metal get inside; and
- Add-on protections such as metatarsal guards, shoe covers, rubber spats, strap-on cleats, and puncture-proof steel inserts.
What are the criteria for foot protection?
The Occupational Health and Safety Administration (OSHA)’s construction regulation at 1926.96 states, “Safety-toe footwear for employees shall meet the requirements and specifications in American National Standard for Men’s Safety-Toe Footwear, Z41.1-1967.” However, the general industry standard at 1910.136 has the following requirements:
- American Society for Testing and Materials (ASTM) F-2412–2005, Standard Test Methods for Foot Protection and ASTM F–2413–2005, Standard Specification for Performance Requirements for Protective Footwear, or
- ANSI Z41-1999 — American National Standard for Personal Protection — Protective Footwear, or
- ANSI Z41-1991 — American National Standard for Personal Protection — Protective Footwear.
OSHA also states, “Protective footwear that the employer demonstrates is at least as effective as protective footwear that is constructed in accordance with one of the above consensus standards will be deemed to be in compliance with the requirements of this section.”
Training, maintenance and inspection requirements
Employers must train their employees on recognizing and avoiding unsafe conditions in the workplace. This includes training employees on how to control or eliminate foot/shin-related hazards. In addition, employers must train their employees on how to properly select, use, and care for personal protective equipment.
- Train employees on the various types of foot protection available on the jobsite and their various uses. In addition, instruct employees on when they must care for their PPE, including how to inspect and maintain the equipment, to protect themselves from injury.
PPE for head protection
- Head injuries are among the most severe injuries workers might experience.
- Employers must provide head protection at no cost to employees whenever certain hazards are present.
- Head protection must meet one of three editions of ANSI Z89.1 (1997, 2003, 2009)
Thousands of head injuries occur each year in construction. Head injuries are caused by falling or flying objects, bumping the head against a fixed object, or electrical shock and burns. Protecting employees from potential head injuries is a key element of any safety program. A head injury can impair an employee for life; sometimes it can be fatal. Wearing a safety helmet or hard hat is one of the easiest ways to protect an employee’s head from injury. Hard hats can protect employees from impact and penetration hazards as well as from electrical shock and burn hazards.
The Occupational Safety and Health Administration (OSHA) rule for head protection in Construction is 1926.100.
What are the PPE requirements for head protection?
The following are required by the Occupational Health and Safety Administration (OSHA) regarding head protection:
- Assess the workplace for areas where employees could receive head injury from falling objects, or contact with exposed electrical conductors.
- Select appropriate head protection for the hazard, taking into account any electrical hazards.
- Ensure head protection meets one of three editions of American National Standards Institute (ANSI) Z89.1 standards (1997, 2003, or 2009, or equivalent).
- Provide head protection at no cost to the employee.
- Train employees on how to use and care for head protection.
- Enforce the use of head protection when needed.
Who must comply?
Employers with employees working in areas where there is a possible danger of head injury from impact, or from falling or flying objects, or from electrical shock and burns must comply.
What are the types of head protection?
- Head protection is classified by ANSI as Type 1 or Type 2, and as Class G, E or C.
- Head protection should resist penetration, absorb shock, and be water resistant and slow burning.
- Head protection standards are set in ANSI Z89.1, American National Standard for Industrial Head Protection.
There are many types of hard hats available today. That’s why in addition to selecting protective headgear that meets American National Standards Institute (ANSI) standard requirements, employers should ensure that employees wear hard hats that provide appropriate protection against potential workplace hazards. It is important for employers to understand all potential hazards when making this selection, including electrical hazards. This can be done through a comprehensive hazard analysis and an awareness of the different types of protective headgear available.
When purchasing new hard hats, employers may run across the ANSI Z89.1 designation. There are two types of helmets based on impact capabilities:
Type | Helmets intended to reduce the force of impact resulting from a blow |
---|
1 | Only to the top of the head |
2 | Which may be received off center or to the top of the head |
ANSI also designated three classes based on electrical protection:
Class | Helmet description |
---|
*This voltage is not intended as an indication of the voltage at which the helmet protects the wearer. |
G (General) | Intended to reduce the danger of contact exposure to low voltage conductors. Test samples are proof tested at 2,200 volts (phase to ground).* |
E (Electrical) | Intended to reduce the danger of exposure to high voltage conductors. Test samples are proof tested at 20,000 volts (phase to ground).* |
C (Conductive) | Not intended to provide protection against contact with electrical conductors. |
The Occupational Safety and Health Administration (OSHA) will deem any head protection device that the employer demonstrates is at least as effective as a head protection device constructed in accordance with one of the identified ANSI consensus standards above to be in compliance with 1926.100. Whatever system you use, be sure you select the hard hat that gives adequate protection.
Another class of protective headgear on the market is called a “bump hat,” designed for use in areas with low head clearance. They are recommended for areas where protection is needed from head bumps and lacerations. These are not designed to protect against falling or flying objects and are not ANSI approved. It is essential to check the type of hard hat employees are using to ensure that the equipment provides appropriate protection. Each hat should bear a label inside the shell that lists the manufacturer, the ANSI designation, and the class of the hat.
An employer may run across the old designations (Class A, B, and C) from time to time. However, employers should purchase hard hats with new designations found in ANSI’s newest requirements for hard hats, and should pay particular attention to the new class designations for insulation against electrical hazards.
What are the criteria for head protection?
In general, protective helmets or hard hats should do the following:
- Resist penetration by objects.
- Absorb the shock of a blow.
- Be water-resistant and slow burning.
- Have clear instructions explaining proper adjustment and replacement of the suspension and headband.
Hard hats must have a hard outer shell and a shock-absorbing lining that incorporates a headband and straps that suspend the shell from 1 to 1¼ inches away from the head. This type of design provides shock absorption during an impact and ventilation during normal wear.
Protective headgear must meet the requirements of any of the following consensus standards incorporated by reference in 1926.6:
- American National Standards Institute (ANSI) Z89.1-2009, American National Standard for Industrial Head Protection;
- American National Standards Institute (ANSI) Z89.1-2003, American National Standard for Industrial Head Protection; or
- American National Standards Institute (ANSI) Z89.1-1997, American National Standard for Personnel Protection—Protective Headwear for Industrial Workers—Requirements.
In addition, the employer must ensure that the head protection provided for each employee exposed to high-voltage electric shock and burns also meets the specifications contained in Section 9.7 (“Electrical Insulation”) of any of the consensus standards mentioned above.
Training and maintenance for head PPE
- Employers must train employees in the use and care of the type of head protection they will be using.
- Helmets must be cleaned and inspected for damage regularly.
- Helmets must be stored properly
An effective head protection training program involves training employees, so they know:
- When head protection is necessary. Share company policies or show workers hard hat designated areas which may be indicated by signs.
- What head protection is necessary.
- How to properly don, doff, adjust, and wear head protection.
- The limitations of the head protection.
- The proper care, maintenance, useful life, and disposal of head protection.
Maintenance and inspection requirements
Periodic cleaning and inspection will extend the useful life of protective headgear. A daily inspection of the hard hat shell, suspension system, and other accessories for holes, cracks, tears, or other damage that might compromise the protective value of the hat is essential.
Paints, paint thinners, and some cleaning agents can weaken the shells of hard hats and may eliminate electrical resistance. Employers should consult the helmet manufacturer for information on the effects of paint and cleaning materials on their hard hats.
Employees should never drill holes, paint, or apply labels to protective headgear, as this may reduce the integrity of the protection.
Employees should be trained not to store protective headgear in direct sunlight, such as on the rear window shelf of a car, since sunlight and extreme heat can damage them.
Employers must always replace a hard hat if the hat sustains an impact, even if damage is not noticeable. Suspension systems are offered as replacement parts and should be replaced when damaged or when excessive wear is noticed. It is not necessary to replace the entire hard hat when deterioration or tears of the suspension systems are noticed.
Defective hard hats
Employers should remove from service hard hats with any of the following defects:
- Perforation, cracking, or deformity of the brim or shell.
- Indication of exposure of the brim or shell to heat, chemicals, ultraviolet light, and other radiation (in addition to a loss of surface gloss, such signs include chalking or flaking).
Electrical protective equipment
- The OSHA standard for electrical protective equipment applies to all employers whose employees are exposed to electricity hazards in the workplace.
Employees in a variety of industries work with or around electrical hazards. The Occupational Health and Safety Administration (OSHA) requires employers to protect these employees through a variety of methods and means, including, in some cases, the use of protective equipment — both the kind that can be worn and also some equipment that is not worn.
The electrical equipment rule protects employees exposed to potential electrical shock. Employers with employees who work with or around electrical hazards present in the workplace must comply. Employers involved in construction of electric power generation, transmission, and distribution lines and equipment must also comply.
Electrical protective equipment means rubber insulating blankets, rubber insulating matting, rubber insulating covers, rubber insulating line hose, rubber insulating gloves, and rubber insulating sleeves.
FR clothing, or flame-resistant clothing, is often used for protection from arc flashes, and has been designed and tested to provide protection against specified electrical/heat hazards.
The OSHA standard that applies to electrical protective equipment is 1926.97.
What are the criteria for electrical protective equipment?
- Electrical protective equipment must be clearly marked with the equipment class.
- Electrical protective equipment must also meet OSHA requirements as defined in 1926.97.
- Employers must ensure that electrical protective equipment is maintained in a safe and reliable condition.
Each electrical protective equipment item must be clearly marked as follows:
- Class 00 equipment shall be marked Class 00.
- Class 0 equipment shall be marked Class 0.
- Class 1 equipment shall be marked Class 1.
- Class 2 equipment shall be marked Class 2.
- Class 3 equipment shall be marked Class 3.
- Class 4 equipment shall be marked Class 4.
- Nonozone-resistant equipment shall be marked Type I.
In addition to the above criteria, the Occupational Health and Safety Administration (OSHA) requires that electrical protective equipment meet industry standards, including being capable of withstanding rigorous voltage testing. Employers should check all equipment and ensure it meets the requirements set out at 1926.97.
Maintenance and inspection requirements
OSHA requires that employers maintain electrical protective equipment in a safe and reliable condition. This includes ensuring that PPE is free of scratches, cuts, holes, brazes, or other conditions that compromise the equipment’s protective rating.
Safety vests
- Employees in construction must be protected in work zones with high-visibility clothing.
- OSHA requires construction flaggers to wear safety vests with high visibility during the day, and with retroreflective materialduring nighttime work.
- Employees must be trained to recognize hazards, to maintain equipment, and to understand communication methods in the work zone.
Employers with employees who operate in construction work zones must comply with the Occupational Health and Safety Administration (OSHA)’s standard for protecting flaggers. One important type of safety equipment for employees in construction zones is high-visibility clothing.
High-visibility safety apparel is critical in a construction work zone. At a minimum, the Occupational Health and Safety Administration (OSHA) requires that for daytime work flaggers wear a vest, shirt, or jacket that is orange, yellow, strong yellow green or fluorescent versions of these colors. For nighttime work, similar outside garments shall be retroreflective. The retroreflective material shall be orange, yellow, white, silver, strong yellow-green, or a fluorescent version of one of these colors and shall be visible at a minimum distance of 1,000 feet.
OSHA regulations require adherence to the Manual on Uniform Traffic Control Devices (MUTCD) for all traffic control signs and devices used for protecting construction workers. Flaggers must wear warning garments that meet requirements of the MUTCD per 1926.201(a). There are no OSHA requirements specific to the individual worker doing road work.
If the road work is a federal project, or the work is done for a state, county, or municipality, the inclusion of the requirements for warning garments in MUTCD will be enough to require construction companies to provide American National Standards Institute (ANSI) approved safety vests.
What employee training is required?
Work zones are dangerous places to work. Poor worker knowledge, due to lack of training or ineffective training, is a major cause of work zone injuries, illnesses, and fatalities. For this reason, the Occupational Health and Safety Administration (OSHA) requires personnel to be trained before they can work in the work zone. If the operation of equipment is involved, American National Standards Institute (ANSI) recommends that this training be based on the manufacturer’s manuals and that it includes hands-on instruction.
Employees must be trained on:
- How to recognize hazards while in a work zone,
- How to maintain their safety vests,
- Knowing the locations and sizes of blind spots around equipment, and
- Understanding communicating methods and alarms.
What are the criteria for safety vests?
- ANSI/ISEA 107 provides a uniform, authoritative guide to the criteria for high-visibility and retroreflective apparel.
Employers must be aware of the American National Standards Institute (ANSI)/International Safety Equipment Association (ISEA) standard, ANSI/ISEA 107, American National Standard for High-Visibility Safety Apparel and Headwear. The 2004 and 2010 editions of this standard are not required by the Occupational Health and Safety Administration (OSHA) but provide a uniform, authoritative guide for high-visibility and retroreflective apparel including:
- Design
- Performance specifications
- Proper use
Retroreflective apparel consists of vests, jackets, bib/jumpsuit coveralls, trousers and harnesses, as well as high-visibility and retroreflective headwear, including hard hats, baseball caps, wide-brimmed hats, and winter caps.
Garments that meet either edition of the standard may be worn 24 hours a day to provide users with a high level of conspicuity using combined fluorescent and retroreflective materials.
Although excellent standards for meeting the OSHA requirements, ANSI/ISEA 107-2004 and -2010 are voluntary industry consensus standards and are not mandatory. However, the ANSI/ISEA 107-2004 edition is referenced in the latest Manual on Uniform Traffic Control Devices (MUTCD). Plus, some state transportation agencies are requiring adherence to a specific edition of the ANSI/ISEA standard.
In general, the industry recognizes three classes of high-visibility apparel:
Here’s the breakdown:
- Class 1 safety apparel is often made with the least amount of reflective material and can be used by employees whose exposure to struck-by hazards is limited. For example, employees who work at large events (e.g., concerts) or groundskeepers.
- Class 2 safety apparel is made with a bit more reflective material to protect work-zone employees like flaggers. Keep in mind, flaggers and road-construction employees must wear class 2 apparel at the minimum to be protected adequately.
- Class 3 safety apparel is meant to protect employees high-risk struck-by areas such as employees who work on roads where speeds reach up to 50mph. Class 3 safety apparel must cover the employee’s arms and legs to outline the whole body.
There is a fourth class called Class E safety apparel. Often times, employers will combine a Class E apparel (tops) with Class 2 apparel (bottoms) to create a Class 3 ensemble. Employers can use this trick to help meet consensus requirements set out by ANSI.
Employers should make sure that each employee demonstrates an understanding of the PPE training as well as the ability to properly wear and use PPE before they are allowed to perform work requiring the use of the PPE.
Key definitions
- Key terms for personal protective equipment in General Industry and Construction are defined in this section.
Every year, many workers on jobsites in General Industry and Construction are killed or seriously injured because the hazards they’re exposed to. Although PPE isn’t meant to be a permanent solution, it plays a necessary role in every workplace. Reference the key definitions below to gain a better understanding of which types of PPE may be most useful in your workplace. The key definitions in this section will cover PPE including:
- Electrical protection
- Eye and face protection
- Foot protection
- Head protection
- Hearing protection
- Hand protection
- Respiratory protection
Electrical protection
FR clothing: Flame-resistant clothing, often used for protection from arc flashes, that has been designed and tested to provide protection against specified electrical/heat hazards.
Eye and face protection
American National Standards Institute (ANSI) Z87.1: An American National Standard that provides specification for testing, selecting, maintaining, and designing eye and face protection. The Occupational Health and Safety Administration (OSHA) accepts eye/face protection meeting one of three editions of ANSI Z87.1 (2010, 2003, and 1989-Rev1998)
Face shields: Secondary protectors intended to protect the entire face against exposure to impact hazards.
Safety goggles: Primary protectors intended to shield the eyes against flying fragments, objects, large chips, and particles.
Safety spectacles: Primary protectors intended to shield the eyes from a variety of impact hazards.
Side shields: A type of eye protection that provides angular protection from impact hazards in addition to frontal protection.
Foot protection
American National Standards Institute (ANSI) Z41: An American National Standard that provides criteria for design, testing, and use of protective footwear. The Occupational Health and Safety Administration (OSHA) accepts shoes that adhere to two editions of ANSI Z41 (1999, 1991), or American Society for Testing and Materials (ASTM) F–2412–2005, Standard Test Methods for Foot Protection and ASTM F–2413–2005, Standard Specification for Performance.
ASTM F-2412 and F-2413: The most current industry standards for design, testing, and use of protective footwear. OSHA accepts shoes that adhere to ASTM F–2412–2005, Standard Test Methods for Foot Protection and ASTM F–2413–2005, Standard Specification for Performance, or either of two editions of ANSI Z41 (1999, 1991)
Combination foot and shin guards: Protect the lower legs and feet, and may be used in combination with toe guards when greater protection is needed.
Electrically conductive shoes: Provide protection against the buildup of static electricity. Employees working in explosive and hazardous locations such as explosives manufacturing facilities or grain elevators must wear conductive shoes to reduce the risk of static electricity buildup on the body that could produce a spark and cause an explosion or fire. Foot powder should not be used in conjunction with protective conductive footwear because it provides insulation, reducing the conductive ability of the shoes. Silk, wool and nylon socks can produce static electricity and should not be worn with conductive footwear. Conductive shoes must be removed when the task requiring their use is completed. Note: Employees exposed to electrical hazards must never wear conductive shoes.
Electrical hazard, safety-toe shoes: Nonconductive shoes that will prevent the wearers’ feet from completing an electrical circuit to the ground. These shoes can protect against open circuits of up to 600 volts in dry conditions and should be used in conjunction with other insulating equipment and additional precautions to reduce the risk of a worker becoming a path for hazardous electrical energy. The insulating protection of electrical hazard, safety-toe shoes may be compromised if the shoes become wet, the soles are worn through, metal particles become embedded in the sole or heel, or workers touch conductive, grounded items. Note: Nonconductive footwear must not be used in explosive or hazardous locations.
Foundry shoes: Insulate the feet from the extreme heat of molten metal, and also keep hot metal from lodging in shoe eyelets, tongues or other shoe parts.
Leggings: Protect the lower legs and feet from heat hazards such as molten metal or welding sparks. Safety snaps allow leggings to be removed quickly.
Metatarsal guards: Protect the instep area from impact and compression. Made of aluminum, steel, fiber or plastic, these guards may be strapped to the outside of shoes.
Safety shoes: Shoes that have impact-resistant toes and heat-resistant soles that protect the feet against hot work surfaces common in roofing, paving and hot metal industries. The metal insoles of some safety shoes protect against puncture wounds. Safety shoes may also be designed to be electrically conductive to prevent the buildup of static electricity in areas with the potential for explosive atmospheres or nonconductive to protect workers from workplace electrical hazards.
Toe guards: Fit over the toes of regular shoes to protect the toes from impact and compression hazards. They may be made of steel, aluminum or plastic.
Head protection
American National Standards Institute (ANSI) Z89.1: An American National Standard for the design, testing, and use of head protection. There are three editions of the standard for which the Occupational Health and Safety Administration (OSHA) says head protection can meet to comply with 1910.135 (1997, 2003, and 2009).
Hard hats (head protectors): Hard hats are worn by employees to lessen injury from falling objects; the equipment has a hard outer shell and a suspension system inside. Head protection is currently made and labeled as one of two types and one of three classes:
- Type 1 helmets: Intended to reduce the force of impact resulting from a blow only to the top of the head.
- Type 2 helmets: Intended to reduce the force of impact resulting from a blow to the top or sides of the head.
- Class G helmets: Intended to reduce the danger of contact exposure to low voltage conductors. Test samples are proof-tested at 2200 volts (phase to ground). This voltage is not intended as an indication of the voltage at which the helmet protects the wearer.
- Class E helmets: Intended to reduce the danger of contact with higher voltage conductors. Test samples are proof-tested at 20,000 volts (phase to ground). This voltage is not intended as an indication of the voltage at which the helmet protects the wearer.
- Class C helmets: Not intended to provide protection against contact with electrical hazards.
Hearing protection
Action level: An eight-hour time-weighted average of 85 decibels measured on the A-scale, slow response, or equivalently, a dose of 50 percent.
Audiogram: A chart, graph, or table resulting from an audiometric test showing an individual’s hearing threshold levels as a function of frequency.
Baseline audiogram: The audiogram against which future audiograms are compared.
Decibel (dB): A unit of measurement of sound level.
Noise dosimeter: An instrument that integrates a function of sound pressure over a period of time in such a manner that it directly indicates a noise dose.
Representative exposure: A measurement of an employee’s noise dose or eight-hour time-weighted average sound level that the employers deem to be representative of the exposures of other employees in the workplace.
Time-weighted average sound level: A sound level that, if constant over an eight-hour exposure, would result in the same noise dose as is measured.
Hand protection
Aluminized gloves: Provide reflective and insulating protection against heat and require an insert made of synthetic materials to protect against heat and cold.
Aramid fiber gloves: Protect against heat and cold, are cut- and abrasive-resistant, and wear well.
Butyl gloves: Gloves made of a synthetic rubber and protect against a wide variety of chemicals, such as peroxide, rocket fuels, highly corrosive acids (nitric acid, sulfuric acid, hydrofluoric acid and red-fuming nitric acid), strong bases, alcohols, aldehydes, ketones, esters, and nitro compounds. Butyl gloves also resist oxidation, ozone corrosion and abrasion, and remain flexible at low temperatures. Butyl rubber does not perform well with aliphatic and aromatic hydrocarbons and halogenated solvents.
Coated fabric gloves: Gloves normally made from cotton flannel with napping on one side. By coating the un-napped side with plastic, fabric gloves are transformed into general-purpose hand protection offering slip-resistant qualities. These gloves are used for tasks ranging from handling bricks and wire to chemical laboratory containers. When selecting gloves to protect against chemical exposure hazards, employers should always check with the manufacturer or review the manufacturer’s product literature to determine the gloves’ effectiveness against specific workplace chemicals and conditions.
Fabric gloves: Protect against dirt, slivers, chafing and abrasions. They do not provide sufficient protection for use with rough, sharp or heavy materials. Adding a plastic coating will strengthen some fabric gloves.
Natural (latex) rubber gloves: A popular general-purpose glove. They feature outstanding tensile strength, elasticity and temperature resistance. In addition to resisting abrasions caused by grinding and polishing, these gloves protect workers’ hands from most water solutions of acids, alkalis, salts and ketones. Latex gloves can cause allergic reactions in some individuals and may not be appropriate for all employees. Hypoallergenic gloves, glove liners and powderless gloves are possible alternatives for workers who are allergic to latex gloves.
Leather gloves: Protect against sparks, moderate heat, blows, chips and rough objects.
Neoprene gloves: Made of synthetic rubber and offer good pliability, finger dexterity, high density, and tear resistance. They protect against hydraulic fluids, gasoline, alcohols, organic acids, and alkalis. They generally have chemical and wear resistance properties superior to gloves made of natural rubber.
Nitrile gloves: Made of a copolymer and provide protection from chlorinated solvents such as trichloroethylene and perchloroethylene. Although intended for jobs requiring dexterity and sensitivity, nitrile gloves stand up to heavy use even after prolonged exposure to substances that cause other gloves to deteriorate. They offer protection when working with oils, greases, acids, caustics, and alcohols but are generally not recommended for use with strong oxidizing agents, aromatic solvents, ketones, and acetates.
Synthetic gloves: Offer protection against heat and cold, are cut- and abrasive-resistant, and may withstand some diluted acids. These materials do not stand up against alkalis and solvents.
Respiratory protection
Air-purifying respirator: A respirator with an air-purifying filter, cartridge, or canister that removes specific air contaminants by passing ambient air through the air-purifying element.
Assigned protection factor (APF): The workplace level of respiratory protection that a respirator or class of respirators is expected to provide to employees when the employer implements a continuing, effective respiratory protection program.
Atmosphere-supplying respirator: A respirator that supplies the respirator user with breathing air from a source independent of the ambient atmosphere, including SARs and SCBA units.
Canister or cartridge: A container with a filter, sorbent, or catalyst, or combination of these, which removes specific contaminants from the air passed through the container.
Continuous flow respirator: An atmosphere-supplying respirator that provides a continuous flow of breathable air to the respirator facepiece.
Demand respirator: An atmosphere-supplying respirator that admits breathing air to the facepiece only when a negative pressure is created inside the facepiece by inhalation.
Elastomeric: A respirator facepiece made of a natural or synthetic elastic material such as natural rubber, silicone, or synthetic rubber.
Emergency situation: Any occurrence such as, but not limited to, equipment failure, rupture of containers, or failure of control equipment that may or does result in an uncontrolled significant release of an airborne contaminant
Employee exposure: Exposure to a concentration of an airborne contaminant that would occur if the employee were not using respiratory protection.
End-of-service-life indicator (ESLI): A system that warns the respirator user of the approach of the end of adequate respiratory protection; for example, if the canister or cartridge sorbent is approaching saturation or is no longer effective.
Escape-only respirator: A respirator intended to be used only for emergency exit.
Filter or air-purifying element: A component used in respirators to remove solid or liquid aerosols from the inspired air.
Filtering facepiece (or dust mask): A negative pressure particulate respirator with a filter as an integral part of the facepiece or with the entire facepiece composed of the filtering medium.
Fit factor: A quantitative estimate of the fit of a particular respirator to a specific individual. It typically estimates the ratio of the concentration of a substance in ambient air to its concentration inside the respirator when worn.
Fit test: The use of a protocol to qualitatively or quantitatively evaluate the fit of a tight-fitting respirator facepiece on an individual.
High-efficiency particulate air filter (HEPA): A filter that is at least 99.97% efficient in removing monodispersed particles of 0.3 micrometers in diameter. The equivalent National Institute for Occupational Safety & Health (NIOSH) 42 CFR 84 particulate filters are the N100, R100, and P100 filters.
Hood: A respiratory inlet covering that completely covers the head and neck and may also cover portions of the shoulders and torso.
Immediately dangerous to life or health (IDLH): An atmosphere that poses an immediate threat to life, would cause irreversible adverse health effects, or would impair an individual’s ability to escape from a dangerous atmosphere.
Interior structural firefighting: The physical activity of fire suppression, rescue, or both, inside of buildings or enclosed structures which are involved in a fire situation beyond the incipient stage. (See 1910.155).
Loose-fitting facepiece: A respiratory inlet covering that is designed to form a partial seal with the face.
Maximum use concentration (MUC): The maximum atmospheric concentration of a hazardous substance from which an employee can be expected to be protected when wearing a respirator, determined by the assigned protection factor of the respirator or class of respirators and the exposure limit of the hazardous substance. The MUC can be determined mathematically by multiplying the assigned protection factor specified for a respirator by the required the Occupational Health and Safety Administration (OSHA)’s permissible exposure limit, short-term exposure limit, or ceiling limit. When no OSHA exposure limit is available for a hazardous substance, an employer must determine an MUC on the basis of relevant available information and informed professional judgment.
Negative pressure respirator (tight-fitting): A respirator in which the air pressure inside the facepiece is negative during inhalation with respect to the ambient air pressure outside the respirator.
Oxygen deficient atmosphere: An atmosphere with an oxygen content below 19.5% by volume.
Permissible exposure limit (PEL): An occupational exposure limit specified by OSHA.
Physician or other licensed healthcare professional (PLHCP): An individual whose legally permitted scope of practice (i.e., license, registration, or certification) allows that individual to independently provide, or be delegated the responsibility to provide, some or all of the healthcare services.
Positive pressure respirator: A respirator in which the pressure inside the respiratory inlet covering exceeds the ambient air pressure outside the respirator.
Powered air-purifying respirator (PAPR): An air-purifying respirator that uses a blower to force the ambient air through air-purifying elements to the inlet covering.
Pressure demand respirator: A positive pressure atmosphere-supplying respirator that admits breathing air to the facepiece when the positive pressure is reduced inside the facepiece by inhalation.
Qualitative fit test (QLFT): A pass/fail fit test to assess the adequacy of respirator fit that relies on the individual’s response to the test agent.
Quantitative fit test (QNFT): An assessment of the adequacy of respirator fit by numerically measuring the amount of leakage into the respirator.
Recommended exposure limit (REL): An occupational exposure level recommended by the National Institute for Occupational Safety & Health (NIOSH).
Self-contained breathing apparatus (SCBA): An atmosphere-supplying respirator for which the breathing air source is designed to be carried by the user.
Supplied-air respirator (or airline) respirator (SAR): An atmosphere-supplying respirator for which the source of breathing air is not designed to be carried by the user.
Threshold limit value (TLV): An occupational exposure level recommended by the American Conference of Governmental Industrial Hygienists (ACGIH).
Tight-fitting facepiece: A respiratory inlet covering that forms a complete seal with the face.
User seal check: An action conducted by the respirator user to determine if the respirator is properly seated to the face.