Portable containers and small containers
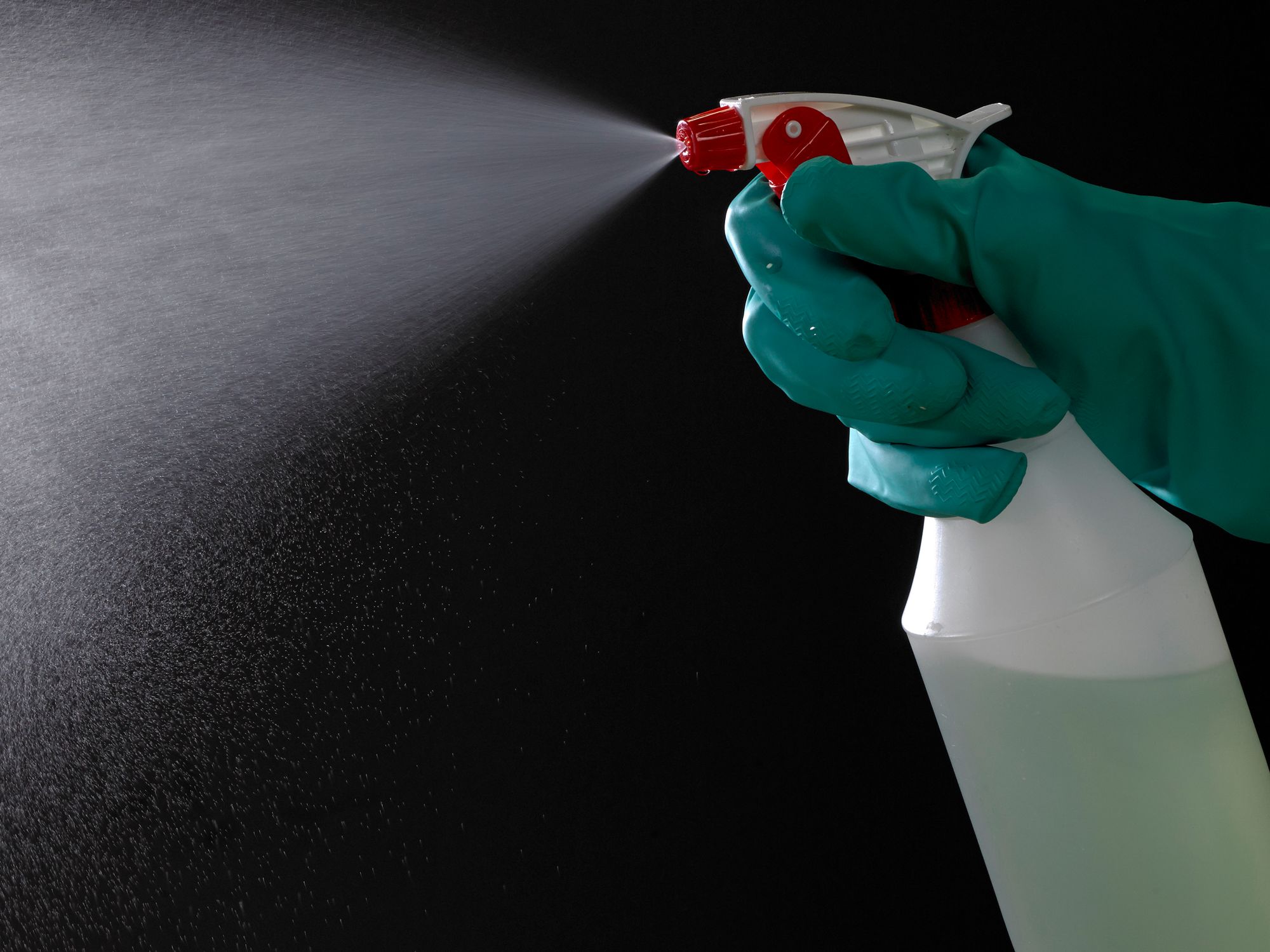
- The employer is not required to label portable containers where hazardous chemicals are transferred from labeled containers, and which are for immediate use.
- Just because a container is small does not mean it is exempt from a label.
Portable containers
The employer is not required to label portable containers into which hazardous chemicals are transferred from labeled containers, and which are intended only for the immediate use of the employee who performs the transfer. “Immediate use” means that the hazardous chemical will be under the control of and used only by the person who transfers it from a labeled container and only within the work shift in which it is transferred.
Problems arise when the shift ends and there is material left in the portable container, or if another employee needs to use the container/substance. Before the chemical can be passed along to another employee, the container must be properly labeled.
Quality control samples taken in a plant must be labeled, tagged, or marked unless the person taking the sample is also going to be performing the analysis, as the sample would then fall under the portable container exemption.
Small containers
There are no exemptions from labeling due to the size of the container. The Occupational Safety and Health Administration (OSHA) says labeling can be done with pull-out labels, fold-back labels, tags or other methods.
For shipped containers, chemical manufacturers, importers, or distributors can often demonstrate that it’s not feasible to use pull-out labels, fold-back labels, or tags with the full label information. If that’s the case, they have some labeling alternatives depending on the size of the container:
Containers less than or equal to: | Must: | And the immediate outer package must include both: |
---|---|---|
100 ml capacity | Include the product identifier, pictogram(s), signal word, chemical manufacturer's contact information, and a statement that the full label information is provided on the immediate outer package. | • The full label information for each hazardous chemical in the immediate outer package, and • A statement that the small container(s) inside must be stored in the immediate outer package bearing the complete label when not in use. |
3 ml capacity | Provide at least the product identifier where chemical manufacturers, importers, or distributors demonstrate that any label interferes with the normal use of the container. |