Chemical inventory and assessing workplace hazards
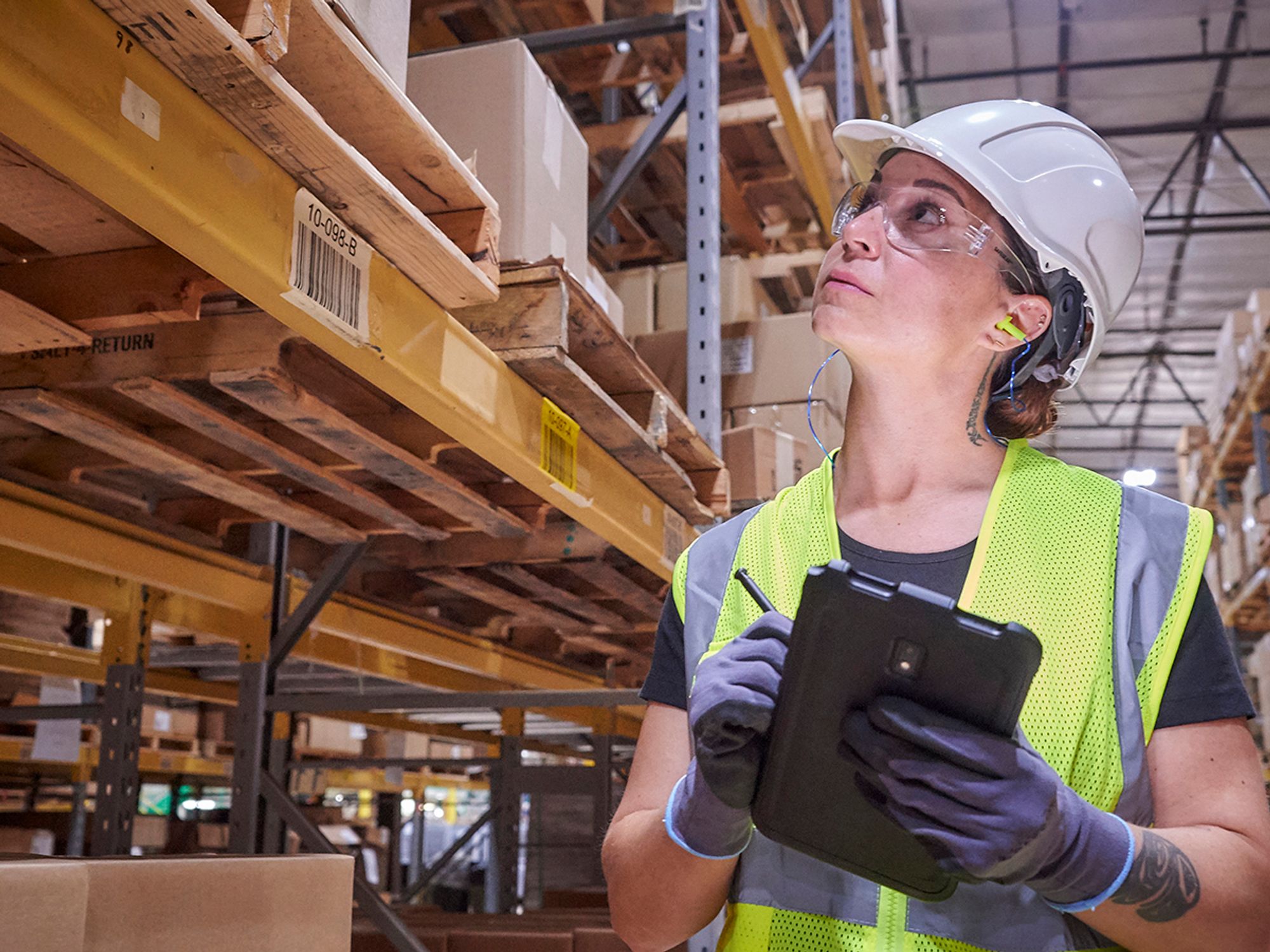
- The written HazCom program must include a list/inventory of the hazardous chemicals known to be present in the workplace.
- The inventory must use the “product identifier” for each chemical that aligns with the SDS and label.
- Identify any chemicals generated in the work operations.
Chemical inventory/list
The written HazCom program must include a list of the hazardous chemicals known to be present in the workplace. The list must include all hazardous chemicals present, even if the chemicals are stored or are not in use. The list can be maintained by work area or for the workplace as a whole.
Compiling the list for the entire workplace may be most suitable for very small facilities, while for larger workplaces, it may be more convenient to compile lists of hazardous chemicals by work area and then assemble them together as the list for the workplace. As new chemicals are purchased, the list should be updated.
The inventory must use the “product identifier” for each chemical that aligns with the safety data sheet (SDS) and label. It may be kept by product name, common name, or chemical name, as long as the identity used on the list matches that used on both the SDS and the label so that these documents can be cross-referenced.
The Occupational Safety and Health Administration (OSHA) does not specifically require that the list contain any other information.
Assess for workplace hazards
To prepare a comprehensive chemical list perform a department-by-department search for every chemical present. Include:
- Cleaning supplies, such as bathroom and window cleaners;
- Grounds maintenance chemicals, such as weed killers and fertilizer;
- Vendor samples being used on a trial basis;
- Fuels;
- Paints; and
- All chemicals used in daily operations.
Identify any chemicals generated in the work operations. For example, welding fumes, dusts, and exhaust fumes are all sources of chemical exposures. Some other suggestions include:
- Read labels provided by suppliers for hazard information,
- Make a list of all chemicals that are potentially hazardous,
- Note the storage and use location(s) of the products, and
- Note the hazards as found on the label.
Purchasing records may also help, and employers should establish procedures to ensure that purchasing procedures result in receiving safety data sheets (SDSs) before a material is used in the workplace. Prior to purchasing chemicals, review the hazards of the chemicals and evaluate if less hazardous chemicals can be used instead.
What to look for
While compiling this inventory, consider listing the substances separately by department. Employers will find that it makes it easier to conduct employee training to know which chemicals are used in which departments.