InstituteRisk Management ProgramRisk Management ProgramEnvironmentalEnglishSARA ComplianceAnalysisFocus AreaCompliance and Exceptions (Level 2)USA
What must RMP facilities do?
['Risk Management Program']
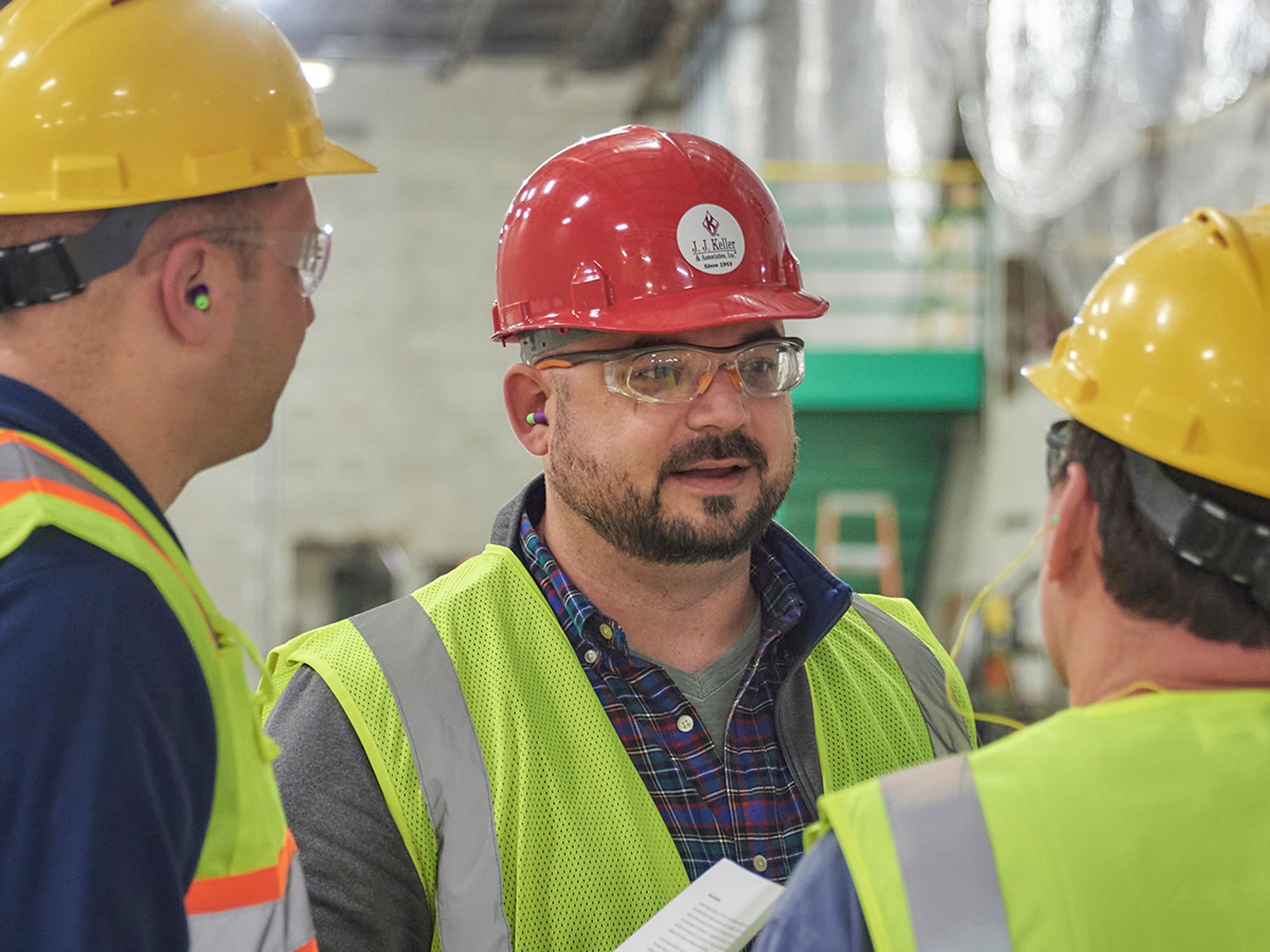
- For each RMP covered process, there are categories of requirements across the three different levels of programs.
Based on the operations and situation of a given facility, the owner or operator of a process covered under the Risk Management Plan (RMP) rule must:
- Prepare and submit a single RMP, including registration that covers all affected processes and chemicals.
- Conduct a worst-case release scenario, review accident history, ensure emergency response procedures are coordinated with community response organizations to determine eligibility for Program 1, and, if eligible, document the worst-case scenario and complete a Program 1 certification for the RMP.
- Conduct a hazard assessment, document a management system, implement a more extensive, but streamlined prevention program, and implement an emergency response program for Program 2 processes.
- Conduct a hazard assessment, document a management system, implement a prevention program that is fundamentally identical to the Occupational Safety and Health Administration (OSHA) Process Safety Management (PSM) standard, and implement an emergency response program for Program 3 processes.
Comparison of program requirements
The table below describes what the RMP requires of various facilities based on six categories of requirements across the three different levels of programs classified by the Environmental Protection Agency (EPA).
Requirement | Program 1 | Program 2 | Program 3 |
---|---|---|---|
Hazard assessment | Worst-case analysis | Worst-case analysis Alternative releases | Worst-case analysis Alternative releases |
Five-year accident history | Five-year accident history | Five-year accident history | Five-year accident history |
Management program | Document management system | Document management system | |
Prevention program | Certify no additional steps needed | Safety information Hazard review Operating procedures Training Maintenance Incident investigation Compliance audit | Process safety information Process hazard analysis Operating procedures Training Mechanical integrity Incident investigation Compliance audit Management of change Pre-startup review Contractors Employee participation Hot work permits |
Emergency response program | Coordinate with local responders | Develop plan and program | Develop plan and program |
RMP contents | Confidential business information (CBI) Document(s) supporting any CBI Executive summary Registration Worst-case data Five-year accident history Certification | Confidential business information (CBI) Document(s) supporting any CBI Executive summary Registration Worst-case data Alternative release data Five-year accident history Prevention program data Emergency response data Certification | Confidential business information (CBI) Document(s) supporting any CBI Executive summary Registration Worst-case data Alternative release data Five-year accident history Prevention program data Emergency response data Certification |