RMP applicability
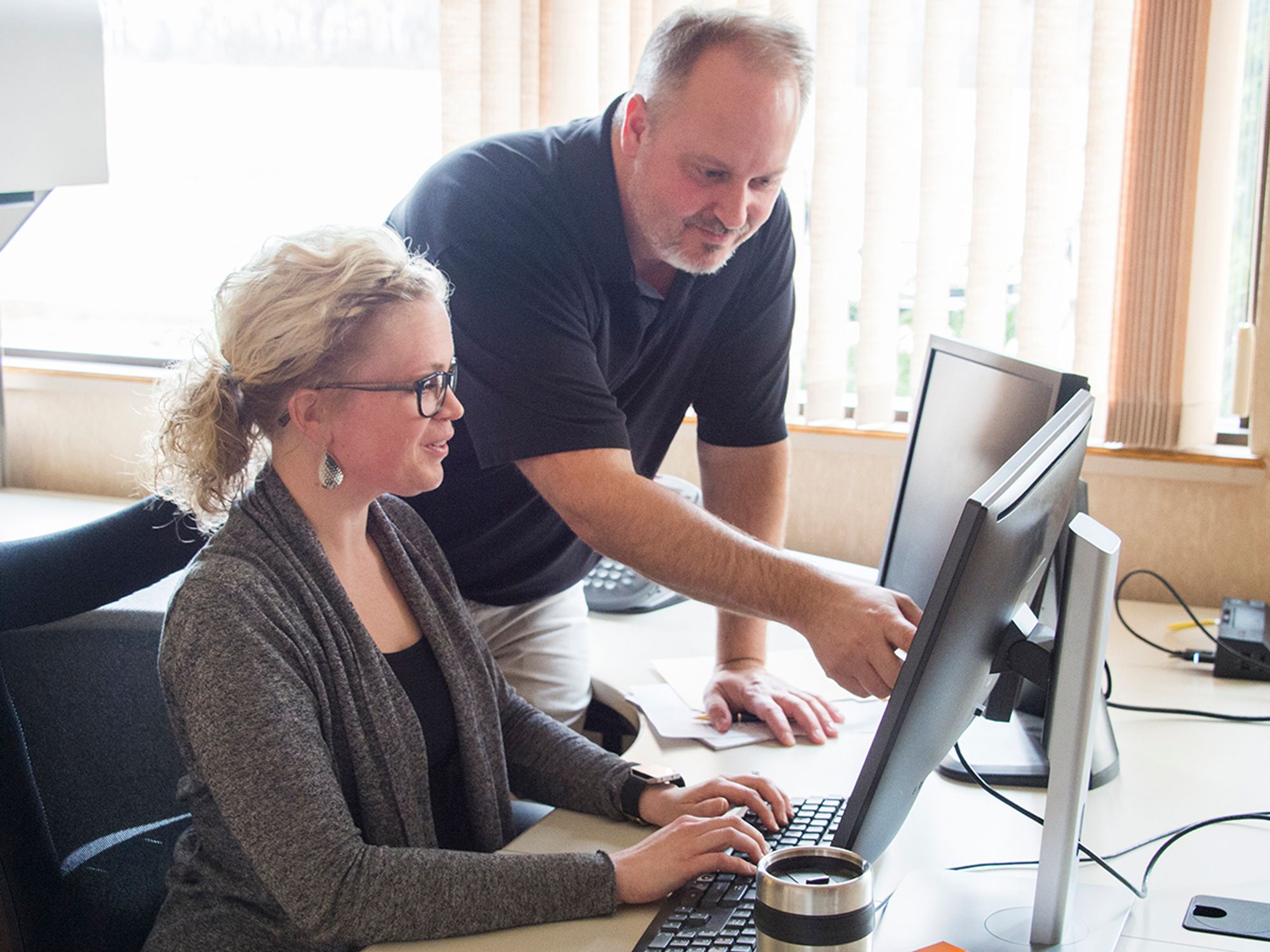
- The EPA requires owners and operators to develop plans and procedures that result in the implementation of a risk management program.
- Many facilities covered under CAA are also regulated under the PSM standard.
Cited under 40 Code of Federal Regulations (CFR) 68 — Chemical accident prevention provisions, the Environmental Protection Agency’s (EPA’s) Risk Management Plan (RMP) regulation requires owners and operators to develop plans and procedures that result in the implementation of a risk management program for all covered facilities within the organization. Three of the most important requirements include the following:
- A hazard assessment of workplace activities.
- A prevention program that is based on the Occupational Safety and Health Administration’s (OSHA’s) Process Safety Management (PSM) standard.
- An emergency response program to train employees and contractors in emergency response procedures.
Overlap with PSM
Many facilities covered under the Clean Air Act (CAA) and by extension the RMP rule are already regulated under the PSM standard. Requirements of PSM that also apply to RMP are:
- Safety and compliance audits
- Pre-startup safety reviews
- Mechanical integrity
- Operating procedures
- Process safety information
- Management of change
- Incident investigation
- Emergency planning and response
- Process hazard analysis
- Training programs
- Employee participation
- Hot-work permits
- Contractor requirements
- Recordkeeping requirements
- Trade secrets clause
While the PSM standard centers on worker safety, the RMP rule focuses on releases that would pose a hazard to public health and the environment. Provisions of RMP that are in addition to requirements under PSM are:
- Management systems requirements
- Off-site analysis
- Five-year incident history
- Worst-case release scenarios
- Plan coordination with local emergency planning committee (LEPC)
- Information sharing to the public
- Facility registration
- Risk management plan requirement
- Reporting requirements
- Response drills and exercises
- Regulatory audit requirements