The Hazardous Materials Regulations (HMR), managed by the Pipeline and Hazardous Materials Safety Administration (PHMSA), govern the transportation of hazardous materials in interstate, intrastate, and international commerce. The main goal of the HMR is to protect the public and professionals involved in the handling and transport of hazardous materials. To reduce risks, PHMSA establishes specific requirements for hazardous material shipments. The HMR are categorized into four general areas:
A basic understanding of the HMR is required for compliance with the regulations.
What are the general packaging guidelines?
- Follow the specific HMR guidelines if offering a hazardous material for transportation.
- The responsibility to understand preparation requirements falls on the company or person shipping hazardous materials.
Unless otherwise specified, a person must follow certain guidelines to offer a hazardous material for transportation in a packaging or container required by Part 173 of the Hazardous Materials Regulations (HMR).
The person who offers the hazardous material is required to:
- Classify and describe the hazardous material in accordance with Parts 172 and 173 of the HMR; and
- Determine if the packaging or container is an authorized packaging, including Part 173 requirements, and that it has been manufactured, assembled, and marked in accordance with:
- Section 173.7(a) and Parts 173, 178, or 179 of the HMR;
- A specification of the Department of Transportation (DOT) in effect at the date of manufacture of the packaging or container;
- National or international regulations based on the United Nations (UN) Recommendations on the Transport of Dangerous Goods, as authorized in Section 173.24(d)(2);
- An approval issued under the HMR; or
- An exemption/special permit issued under Subchapter A of Part 173.
What is a packaging?
According to the definition in Section 171.8, packaging means a receptacle and any other components or materials necessary for the receptacle to perform its containment function in conformance with the minimum packing requirements of the HMR.
The following marks may be used to determine whether or not the packaging is authorized:
- The manufacturer’s certification, specification, approval, or exemption/special permit marking (see Section 178.2 and 179.1), unless the packaging is a metal or plastic drum with a capacity over 100 L which has been reconditioned, remanufactured, or otherwise converted.
- The manufacturer’s identification plate or written certification of specification or exemption/special permit provided by the carrier, when a cargo tank is provided by the carrier.
DOT specification or UN standard packagings
A person who offers a DOT specification or UN standard packaging that is subject to the requirements in Part 178 of the HMR is required to perform all functions necessary to bring that package into compliance with Parts 173 and178 of the HMR, as identified by the packaging manufacturer or subsequent distributor, in accordance with Section 178.2 of the HMR.
Shipments of fissile radioactive materials, and Type B or highway route controlled quantity packages of radioactive materials
The shipper is required to notify the consignee of the dates of shipment and expected arrival. The shipper must also notify each consignee of any special loading/unloading instructions prior to the first shipment.
Shipments of irradiated reactor fuel
The shipper must provide physical protection in compliance with a plan established under either:
- The U.S. Nuclear Regulatory Commission; or
- Equivalent requirements approved by Pipeline and Hazardous Materials Safety Administration’s (PHMSA’s) Associate Administrator for Hazardous Materials Safety.
Notes: The shipper’s certification on a shipping paper for transportation of hazardous materials requires the shipper to certify that the above-named materials are properly classified, described, packaged, marked and labeled, and are in proper condition for transportation according to the applicable regulations of the DOT.
The shipper, or the person or employee of the person who originates the shipment for transportation is responsible for properly preparing the hazardous material for transportation. The hazardous material must be properly classified to ensure that it is prepared using the proper packaging, marking(s), and label(s). If a company is a shipper of hazardous material, it is responsible to understand the preparation requirements including all applicable packaging related requirements.
Authorized packaging only
- Only packaging authorized by Part 173 of the HMR can be used to prepare a hazardous material for transport.
In most cases, hazardous materials can only be transported in packaging authorized by the Hazardous Materials Regulations (HMR). The packaging authorized in Part 173 can only be used for a hazardous material if the section in Part 173 is referenced in Column 8 of the Hazardous Materials Table for the proper shipping name chosen for the material.
Part 173 provides detailed packaging rules for each class of hazardous materials. The packaging requirements set for a specific hazardous material are the same for all modes of transportation unless otherwise stated or exceptions are authorized.
Specification packaging
- The HMR requires manufacturers to mark all authorized packagings as manufactured and tested in accordance with regulations.
Specification packagings are cylinders, portable tanks, cargo tanks, and tank car tanks for which the Department of Transportation (DOT) has issued detailed manufacturing specifications.
Manufacturers must mark all authorized packagings as required by Parts 178 and 179 of the Hazardous Materials Regulations (HMR). The marking is the manufacturer’s certification that the packaging has been manufactured and tested in accordance with Parts 178 and 179.
Drop test
- Drop tests are required at periodic intervals and whenever a company needs to qualify a package design.
- Depending on the sample, passing the drop test involves a specific scenario.
At periodic intervals and whenever a company needs to qualify a package design, it must perform drop tests from distances between 2.2 feet and 5.9 feet, as specified in 178.601(e) and 178.603. For other than flat drops, the center of gravity of the test packaging must be vertically over the point of impact.
To periodically test single or composite packagings constructed of stainless steel, nickel, or money, the drop test may be conducted with two samples—one sample each for the two drop orientations. The regulations allow companies to use samples that may have previously been used for the hydrostatic pressure or stacking test.
For details about exceptions for the number of steel and aluminum packaging samples used for conducting the drop test, contact the Pipeline and Hazardous Materials Safety Administration (PHMSA).
Passing the test
A package is considered to successfully pass the drop tests if, for each sample tested:
- Receptacles containing liquid, each receptacle does not leak when equilibrium has been reached between the internal and external pressures;
- Removable head drums for solids, the entire contents are retained by an inner packaging (e.g., a plastic bag) even if the closure on the top head of the drum is no longer sift-proof;
- A bag, neither the outermost ply nor an outer packaging exhibits any damage likely to adversely affect safety during transport;
- A composite or combination packaging, there is no damage to the outer packaging likely to adversely affect safety during transport, and there is no leakage of the filling substance from the inner packaging;
- A drum, jerrican, or bag, any discharge from a closure is slight and ends immediately after impact with no further leakage; and
- Class 1 materials, no rupture is permitted which would allow spillage of loose explosive substances or articles from the outer packaging.
Leakproofness test
- Before packaging intended to contain liquids can be used in transportation, it must pass the leakproofness test.
Using compressed air or other suitable gases, a company must perform a leakproofness test on all packagings intended to contain liquids. The packaging must pass the test — i.e., no air leaks from the packaging — before being used in transportation and before any reuse authorized under 173.28. Normally, three samples of each different packaging must be tested.
For design qualification and periodic testing, packagings must be tested with closures in place. For production testing, however, this is not necessary, and removable heads need not be installed, either. For testing with closures in place, vented closures must either be replaced by similar non-vented closures, or the vent must be sealed.
In testing, the packaging must be restrained under water while an internal air pressure is applied, and the method of restraint must not affect the results of the test. The test must be conducted, for other than production testing, for a minimum time of five minutes. Other methods, at least equally effective, may be used in accordance with Appendix B of Part 178.
An internal air pressure (gauge) must be applied to the packaging as indicated for the following packing groups:
- Packing Group I: Not less than 30 kPa (4psi).
- Packing Group II: Not less than 20 kPa (3psi).
- Packing Group III: Not less than 20 kPa (3psi).
Passing the test
A packaging passes the leakproofness test if there is no leakage of air from the packaging.
Hydrostatic pressure test
- Metal, plastic, and composite packaging intended to contain liquids for transport must pass the hydrostatic pressure test.
- The test is not required for inner packagings of combination packagings.
At periodic intervals and whenever qualifying a metal, plastic, and composite packaging design type intended to contain liquids, a company must perform the hydrostatic pressure test as specified in 178.601(e) and 178.605, and no leakage can occur. This test is not required, however, for inner packagings of combination packagings. For internal pressure requirements for inner packagings of combination packagings intended for transportation by aircraft, see 173.27(c).
Normally, the hazmat regulations require three test samples for each different packaging — although one will suffice for packagings constructed of stainless steel, monel, or nickel. Other exceptions require approval from the Pipeline and Hazardous Materials Safety Administration (PHMSA).
Replace vented closures with similar non-vented closures or seal the vent during the test.
Metal packagings and composite packagings other than plastic (e.g., glass, porcelain or stoneware), including their closures, must be subjected to the test pressure for five minutes. Plastic packagings and composite packagings (plastic material), including their closures, must be subjected to the test pressure for 30 minutes.
This pressure is the one to be marked as required in 178.503(a)(5) of this part. The receptacles must be supported in a manner that does not invalidate the test. The test pressure — as specified in detail in 178.605(d) — must be applied continuously and evenly, and it must be kept constant throughout the test period.
Passing the test
A packaging passes the hydrostatic test if, for each sample, there is no leakage of liquid from the packaging.
Stacking test
- All packaging design types used in transportation must pass a stacking test.
All packaging design types, other than bags, must be subjected to a stacking test. The regulations require three test samples for each different packaging — except for one each for periodic retesting stainless steel, monel, or nickel packaging. Exceptions for the number of aluminum and steel sample packagings require approval from the Pipeline and Hazardous Materials Safety Administration (PHMSA). Notwithstanding the provisions of 178.602(a) of this subpart, combination packagings may be subjected to the stacking test without their inner packagings, except where this would invalidate the test results.
The test sample must be subjected to a force applied to the top surface of the test sample equivalent to the total weight of identical packages that might be stacked on it during transport. The minimum height of the stack, including the test sample, must be 3.0 m (10 feet). The duration of the test must be 24 hours, except that plastic drums, jerricans, and composite packaging 6HH, intended for liquids, shall be subjected to the stacking test for a period of 28 days at a temperature of not less than 40°C (104°F).
Alternative test methods that yield equivalent results may be used if the Associate Administrator approves. In guided load tests, stacking stability must be assessed after completion of the test by placing two filled packagings of the same type on the test sample. The stacked packages must maintain their position for one hour. Plastic packagings must be cooled to ambient temperature beforehand.
Periodic retesting must take place in accordance with 178.606(c)(1) or using a dynamic compression testing machine that meets the specifications of that section.
Passing the test
No test sample may leak. In composite packagings or combination packagings, there must be no leakage of the filling substance from the inner receptacle, or inner packaging. No test sample may show any deterioration that could adversely affect transportation safety or any distortion likely to:
- Reduce its strength,
- Cause instability in stacks of packages, or
- Cause damage to inner packagings that would be likely to reduce safety in transportation.
For the dynamic compression test, a container passes the test if, after application of the required load, there is no buckling of the sidewalls sufficient to cause damage to its expected contents. In no case, may the maximum deflection exceed one inch.
Vibration standard
- All packaging design types used in transportation must meet the vibration standard.
Each packaging must be capable of withstanding, without rupture or leakage, this vibration test procedure:
- Select three sample packagings at random that are filled and closed as for shipment.
- Place them on a vibrating platform that has a vertical or rotary double-amplitude (peak-to-peak displacement) of one inch.
- Note: The packages should be constrained horizontally to prevent them from falling off the platform, but must be left free to move vertically, bounce and rotate.
- Perform the test for one hour at a frequency that causes the package to be raised from the vibrating platform to such a degree that a piece of material of approximately 1.6 mm (0.063 inch) thickness (such as steel strapping or paperboard) can be passed between the bottom of any package and the platform.
- Immediately after the vibration period, remove each package from the platform, turn it on its side and look for any evidence of leakage.
Other equally effective methods can be used if approved by the Associate Administrator for Hazardous Materials Safety.
Passing the test
A packaging passes the vibration test if there is no rupture or leakage from any of the packages. No test sample should show any deterioration that could adversely affect transportation safety or any distortion liable to reduce packaging strength.
Packagings authorized under special permits
- A special permit is required for a person to offer a hazardous material for transportation in a packaging other than one specifically indicated in the HMR.
- This is different from an exception.
Unless otherwise specified, in order for a person to offer a hazardous material for transportation in a packaging authorized by a special permit, the person must be “the holder of” or “party to” the special permit.
If a special permit authorizes the use of a packaging for the shipment or transportation of a hazardous material by any person or class of persons other than or in addition to the holder of the special permit, that person or a member of the specified class of persons may use the packaging for the purposes authorized in the special permit subject to the terms specified in the special permit.
Copies of special permits may be obtained by accessing the Pipeline and Hazardous Materials Safety Administration (PHMSA) website or calling the Office of Hazardous Materials Special Permits and Approvals at (202) 366-4433.
When a special permit issued to a person who offers a hazardous material contains requirements that apply to a carrier of the hazardous material, the offeror must furnish a copy of the special permit to the carrier before or at the time a shipment is tendered. Notes: A special permit is different from an exception.
A special permit is a statement from PHMSA authorizing a person or persons to use a packaging other than specifically indicated in the Hazardous Materials Regulations (HMR). A company, in most cases, must apply to get, use, or be allowed to use (be a party to) an existing exemption/special permit.
In some cases, a special permit may be given to an unnamed group or a category of persons meeting certain criteria. This type of special permit allows broader use but may only be utilized when the involved parties are fully aware of the conditions required in the special permit and only if a copy of the special permit is maintained at the location using it.
An exception is a statement of conditions listed in the HMR, that allows any person who meets them to be excepted from certain requirements of the HMR. Meeting the criteria for an exception excepts a company from some or all of the HMR’s requirements. Which requirements are excepted will be specifically indicated in the wording of the exception.
UN or performance-oriented packaging
- Excluding cylinders, UN or performance-oriented packagings are non-bulk and have successfully passed five performance tests.
United Nations (UN) or performance-oriented packaging are non-bulk packagings—except cylinders—that have successfully passed all applicable performance tests: Drop Test, Leakproofness Test, Hydrostatic Pressure Test, Stacking Test, and the Vibration Standard.
Manufacturers must mark all authorized packagings (specification or performance-oriented) as required by Parts 178 and 179 of the Hazardous Materials Regulations (HMR). The marking is the manufacturer’s certification that the packaging has been manufactured and tested in accordance with Parts 178 and 179.
Markings required for non-bulk performance-oriented packagings
- UN markings indicate packagings have been manufactured and tested to meet standards.
- The markings must be durable, legible, and clearly visible.
The United Nations (UN) markings tell the user many things, including what type of packaging it is and to what level of testing it has passed. The marking must be durable, legible, and clearly visible. The marking must include:
- The United Nations symbol:
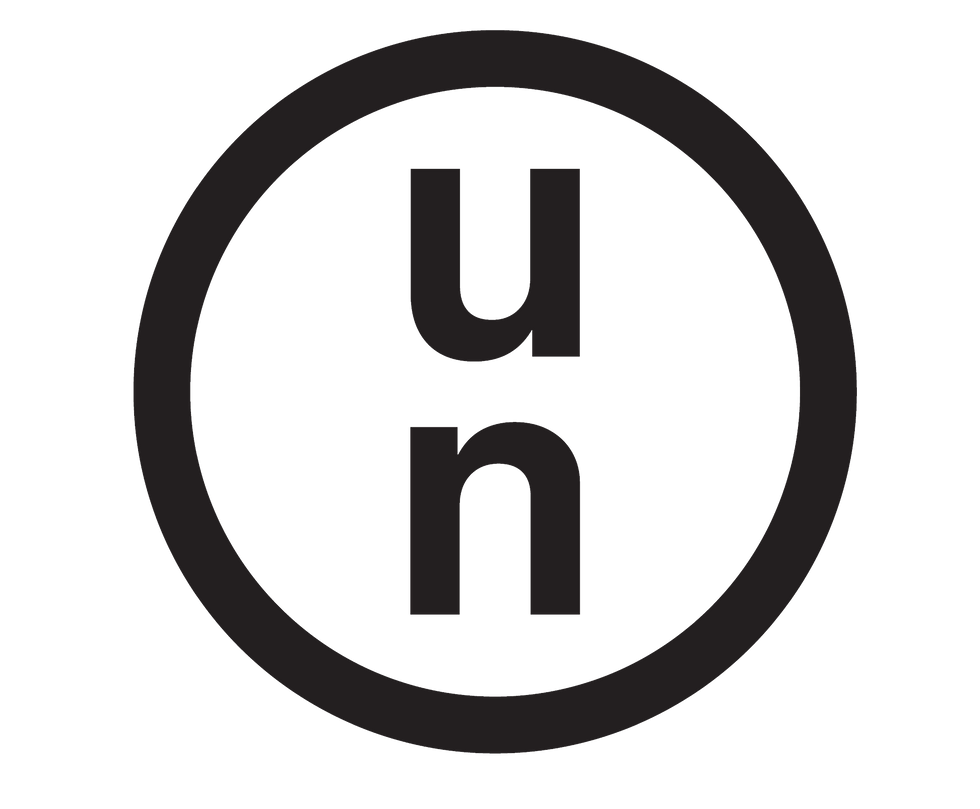
- Packaging identification code (i.e., 1A1 or 4G).
- Letter identifying the performance standard under which the packaging design has been successfully tested, as follows:
- “X” (for packagings meeting Packing Group I, II, and III tests)
- “Y” (for packagings meeting Packing Group II and III tests)
- “Z” (for packagings meeting Packing Group III tests)
- Designation of the specific gravity for outer packagings intended to contain liquids (which can be omitted if <1.2) or the maximum gross mass, in kilograms, for packagings intended for solids or inner packagings.
- For single and composite packagings for liquids, the test pressure in kilopascals rounded down to the nearest 10kPa of hydrostatic pressure, or, for solids and inner packagings, the letter “S.”
- Last two digits of the year of manufacture, except for plastic drums (1H) and jerricans (3H) which must also have the month of manufacture.
- Letters “USA” to indicate the package was manufactured in the USA and marked according to these regulations.
- Name and address or symbol of the manufacturer or approval agency certifying compliance. Symbols must be registered with the Associate Administrator for Hazardous Materials Safety.
- Minimum thickness in millimeters (mm) of the packaging materials for metal or plastic drums or jerricans intended for reuse or reconditioning, or the outer packaging of a composite packaging intended for reuse or reconditioning.
- IF a packaging is reconditioned, it shall be marked “near” the above markings with:
- Name of the country in which the reconditioning was performed. The letters “USA” will suffice for the United States.
- Name and address or symbol of the reconditioner. Symbols must be registered with the Associate Administrator for Hazardous Materials Safety.
- Last two digits of the year of reconditioning.
- Letter “R” (for reconditioned).
- Letter “L” (for packagings that have successfully passed the leakproofness test).
Examples:
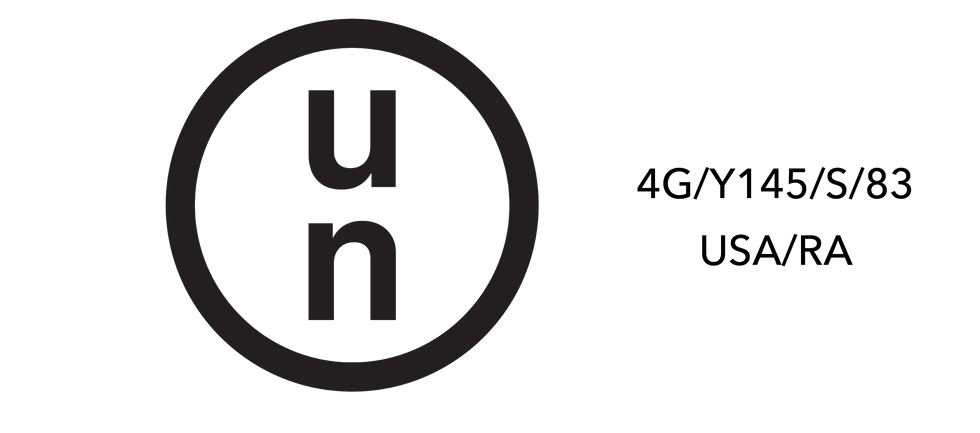
This is a fiberboard box (4G), tested for Packing Groups II and III (Y), with a maximum mass of 145 kilograms, designed to contain an inner packaging(S), and manufactured in 1983 (83). It was manufactured in the United States (USA) by a manufacturer whose registered symbol is “RA.”
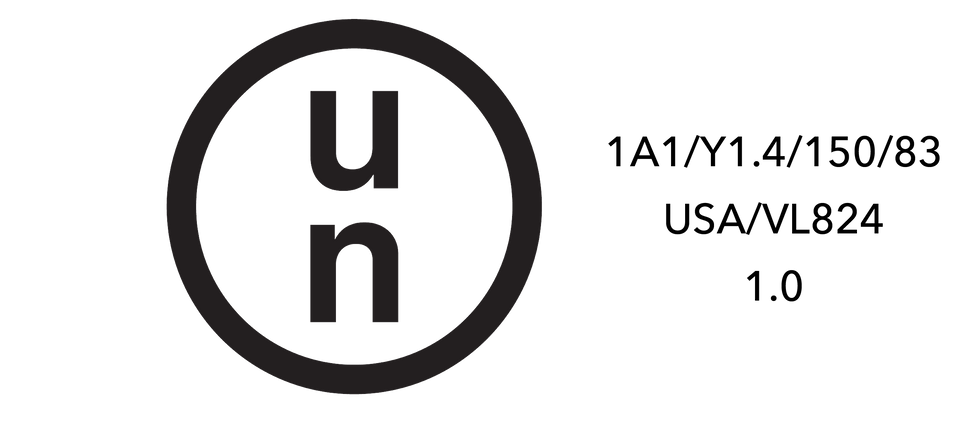
This is a steel non-removable head drum (1A1) designed as a single package for liquids, tested for Packing Groups II and III (Y) for materials with a specific gravity up to 1.4, hydrostatically tested to 150 kPa, and manufactured in 1983 (83). The drum was manufactured in the United States (USA) by a manufacturer whose registered symbol is “VL824.” The minimum thickness of the material is 1 millimeter.
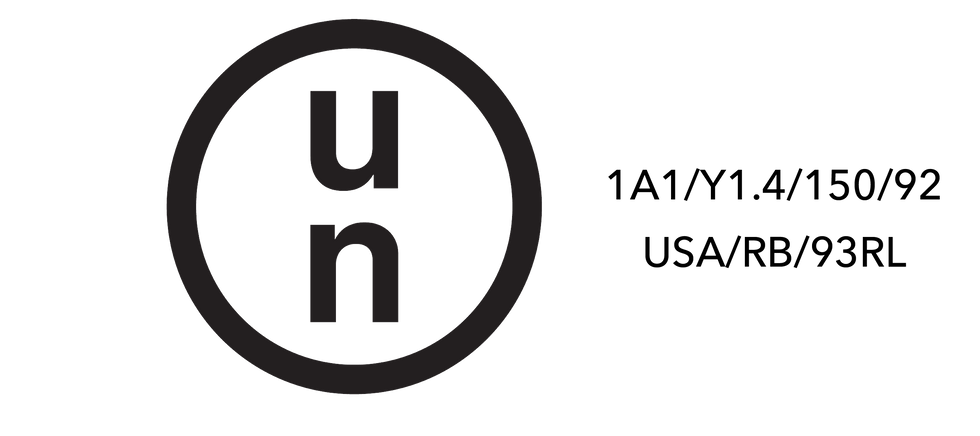
This marking indicates a steel, non-removable head drum (1A1), designed as a single packaging for liquids, tested for Packing Groups II and III (Y), for materials with a specific gravity of 1.4. It was hydrostatically tested to 150 kPa and was manufactured in 1992 (92). The drum was reconditioned in the United States (USA) by a reconditioner whose registered symbol is “RB” in 1993 (93). The drum was reconditioned (R) and successfully passed the leak proofness test (L).
Any packaging required by the Hazardous Materials Regulations to conform to a UN standard must be marked in a manner such as illustrated above.
- Excluding cylinders, UN or performance-oriented packagings are non-bulk and have successfully passed five performance tests.
United Nations (UN) or performance-oriented packaging are non-bulk packagings—except cylinders—that have successfully passed applicable performance tests: Drop Test, Leakproofness Test, Hydrostatic Pressure Test, Stacking Test, and the Vibration Standard.
Manufacturers must mark all authorized packagings (specification or performance-oriented) as required by Parts 178 and 179 of the Hazardous Materials Regulations (HMR). This marking is the manufacturer’s certification that the packaging has been manufactured and tested in accordance with Parts 178 and179.
Packing groups
- Packing groups determine how hazardous a material is, which calls for more restrictive packaging requirements.
The more hazardous the material, the more restrictive the packaging requirements will be. This is not just determined by the hazard class, but also by the degree of hazard, i.e., the packing group.
- Packing Group I — Great Danger
- Packing Group II — Medium Danger
- Packing Group III — Minor Danger
Example: Not all flammable liquids present the same degree of danger, and the packaging requirements recognize this. The packaging requirements for a Packing Group I, Class 3 (flammable) material (initial boiling point less than or equal to 35°C) are more restrictive than for a Packing Group II, Class 3 material (flashpoint less than 23°C, initial boiling point greater than 35°C).
Packaging test requirements are more or less restrictive depending upon the Packing Group of the material for which the package is to be used.
Example: For a material with a specific gravity £1.2, the drop height for Packing Group I is 1.8 m (5.9 feet), Packing Group II is 1.2 m (3.9 feet) and Packing Group III is 0.8 m (2.6 feet). For a material with a specific gravity >1.2, a formula exists for each packing group that is to be used in determining the drop height.
All packages or packaging (bulk and non-bulk) must comply with the “General requirements for packagings and packages” (173.24), including: new and reused packagings, and specification and non-specification packages, unless excepted. These requirements are in addition to those that Part 178 spells out. In addition, non-bulk packagings and packages must also be in compliance with the requirements of 173.24a “Additional general requirements for non-bulk packagings and packages,” and bulk packagings with the requirements of 173.24b “Additional general requirements for bulk packagings.”
Packaging compatibility
- The person offering the hazardous material for transport must ensure compatibility of the packagings and the HM.
It is the responsibility of the person offering a hazardous material for transportation to ensure that the packagings are compatible with the hazardous material they are used for. This particularly applies to corrosivity, permeability, softening, premature aging, and embrittlement.
Packaging materials and contents must be such that there will be no significant chemical or galvanic reaction between the materials and contents of the package.
Plastic packagings and receptacles
Plastic used in packagings and receptacles must be of a type compatible with the hazardous material the packaging will be used for and may not be permeable to an extent that a hazardous condition is likely to occur during transportation, handling, or refilling.
Each plastic packaging or receptacle which is used for liquid hazardous materials must be capable of withstanding without failure the procedure specified in Appendix B of Part 173 - Procedure for Testing Chemical Compatibility and Rate of Permeation in Plastic Packagings and Receptacles. See Section 173.24(e)(3)(ii) and (iii) for more specific information about required testing results.
Compatibility
Hazardous materials may not be packed or mixed together in the same outer packaging with other hazardous or nonhazardous materials if such materials are capable of reacting dangerously with each other and causing:
- Combustion or dangerous evolution of heat:
- Evolution of flammable, poisonous, or asphyxiant gases; or
- Formation of unstable or corrosive materials.
Packagings for solids which may change state during transportation
Packagings used for solids, which may become liquid at temperatures likely to be encountered during transportation, must be capable of containing the hazardous material in the liquid state.
Closing, venting, and filling packagings
- Closures, venting, and outage and filling limits are regulated when transporting hazardous materials.
- Additional requirements apply to packages offered or intended for transportation by aircraft.
Closures
Closures must be designed and closed that under conditions such as changes in temperature, pressure, and vibration which are normally encountered in transportation:
- There is no identifiable release of hazardous materials to the environment from the opening of the closure, except as otherwise provided for in the Hazardous Materials Regulations (HMR); and
- The closure remains secure and leakproof.
A closure, including gaskets or other closure components, if any, used on a specification packaging must conform to all applicable requirements of the specification, except as otherwise provided in the HMR.
Venting
Venting of packagings, to reduce internal pressure which may develop by the evolution of gas from the contents, is permitted only when:
- Transportation by aircraft is not involved;
- The evolved gases are not poisonous, likely to create a flammable mixture with air, or be asphyxiant under normal conditions of transportation, except as otherwise provided in the HMR;
- The packaging is designed to preclude an unintentional release of hazardous materials from the receptacle; and
- For shipments in bulk packagings, other than intermediate bulk containers (IBCs), venting is authorized for the specific hazardous material by a special provision in the Section 172.101 Hazardous Materials Transportation (HMT) or by the applicable bulk packaging specification in Part 178 of the HMR.
IBCs may be vented when required and must be of a type that has successfully passed applicable design qualification tests with no release of hazmat.
Outage and filling limits
When filling packagings and receptacles for liquids, sufficient ullage (outage) must be left to ensure that neither leakage nor permanent distortion of the packaging or receptacle will occur as a result of an expansion of the liquid caused by temperatures likely to be encountered during transportation.
Requirements for outage and filling limits for non-bulk and bulk packagings are specified in Section 173.24a(d) and 173.24b(a), respectively.
Filling limits for compressed gases and cryogenic liquids are specified in Section 173.301 through 173.306 for cylinders and 173.314 through 173.319 for bulk packagings.
Air transportation
Packages offered or intended for transportation by aircraft are subject to requirements additional to those of other modes of transport and must conform to the general requirements for transportation by aircraft in 173.27.
Additional information concerning packaging requirements for preparation of hazardous materials are found in other sections of the HMR.
- Forbidden materials and packages are discussed in Section 173.21.
- Use of tank cars is discussed in Section 173.31.
- Requirements for use of Specification IM portable tanks are discussed in Section 173.32. Approval of Specification IM portable tanks is in 178.273.
- Hazardous materials in cargo tank motor vehicles are discussed in Section 173.33.
- Packaging requirements for poisonous materials required to be packaged in cylinders in detailed in Section 173.40.
- Hazardous materials in intermediate bulk containers are discussed in Section 173.35.
Reusing packagings
- Packagings must be inspected and free from incompatible residue, rupture, or other damage which reduces its structural integrity before being reused.
- Metal drums may be reconditioned according to the HMR.
Packagings and receptacles used more than once must be in such condition, including closure devices and cushioning materials, that they conform in all respects to the prescribed requirements of the Hazardous Materials Regulations (HMR). Before reuse, each packaging must be inspected and may not be reused unless free from incompatible residue, rupture, or other damage which reduces its structural integrity.
A non-bulk packaging used more than once must conform to the provisions and limitations detailed in Section 173.28(b).
What is reconditioning?
Reconditioning of metal drums according to the HMR means:
- Cleaning to the base material of construction, with all former contents, internal and external corrosion, and any external coatings and labels removed;
- Restoring to the original shape and contour, with chimes (if any) straightened and sealed, and all non-integral gaskets replaced; and
- Inspecting after cleaning but before painting.
Packagings that have visible pitting, significant reduction in material thickness, metal fatigue, damaged threads or closures, or other significant defects, must be rejected.
Reconditioning of a non-bulk packaging other than a metal drum is restoring the packaging by repair or replacement of non-integral packaging components (such as removable gaskets, closure devices, cushioning material, etc.) to a condition such that it conforms in all respects with the prescribed requirements of the HMR.
For a United Nations (UN) 1H1 plastic drum, replacing a removable gasket or closure device with a replacement of the same design and material which provides equivalent performance does not constitute reconditioning. Packagings which have significant unrepairable defects may not be reused.
A person who reconditions a packaging manufactured and marked under the provisions of Subpart L of Part 178 of the HMR, must mark that packaging as required by Section 178.503(c) and (d). The marking is the certification of the reconditioner that the packaging conforms to the standard for which it is marked and that all functions performed by the reconditioner which are prescribed by the HMR have been performed in compliance with the HMR.
The markings applied by the reconditioner may be different from those applied by the manufacturer at the time of original manufacture but may not identify a greater performance capability than that for which the original design type had been tested. For example, the reconditioner may mark a drum which was originally marked as 1A1/Y1.8 as 1A1/Y1.2 or 1A1/Z2.0.
What is remanufacturing?
Remanufacturing of non-bulk packagings for the purpose of the HMR, is:
- The conversion of a non-specification, non-bulk packaging to a DOT specification of UN standard;
- The conversion of a packaging meeting one specification or standard to another specification or standard (such as conversion of 1A1 non-removable head drums to 1A2 removable head drums); or
- The replacement of integral structural packaging components (such as non-removable heads on drums).
A person who remanufactures a non-bulk packaging to conform to a specification or standard in Part 178 of the HMR is subject to the requirements of Part 178 of the HMR as a manufacturer.
What does NRC mean?
A packaging marked as NRC (non-reusable container) according to the Department of Transportation (DOT) specification or UN standard requirements in Part 178 of the HMR may be reused for the shipment of any material not required by the HMR to be shipped in a DOT specification or UN standard packaging.
Notes: The requirements for reuse of packagings are very specific. Be sure to include a thorough discussion of these guidelines in all function-specific training if a company reuses, reconditions, or remanufactures packagings.
- Follow the specific HMR guidelines if offering a hazardous material for transportation.
- The responsibility to understand preparation requirements falls on the company or person shipping hazardous materials.
Unless specifically indicated otherwise, a person must follow certain guidelines to offer a hazardous material for transportation in a packaging or container required by Part 173 of the Hazardous Materials Regulations (HMR).
The person who offers the hazardous material is required:
- To classify and describe the hazardous material in accordance with Parts 172 and 173 of the HMR; and
- To determine that the packaging or container is an authorized packaging, including Part 173 requirements, and that it has been manufactured, assembled, and marked in accordance with:
- Section 173.7(a) and Parts 173, 178, or 179 of the HMR;
- A specification of the Department of Transportation (DOT) in effect at the date of manufacture of the packaging or container;
- National or international regulations based on the United Nations (UN) Recommendations on the Transport of Dangerous Goods, as authorized in Section 173.24(d)(2);
- An approval issued under the HMR; or
- An exemption/special permit issued under Subchapter A of Part 173.
What is a packaging?
According to the definition in Section 171.8, packaging means a receptacle and any other components or materials necessary for the receptacle to perform its containment function in conformance with the minimum packing requirements of the HMR.
The following marks may be used to determine whether or not the packaging is authorized:
- The manufacturer’s certification, specification, approval, or exemption/special permit marking (see Section 178.2 and 179.1), unless the packaging is a metal or plastic drum with a capacity over 100 L which has been reconditioned, remanufactured, or otherwise converted.
- The manufacturer’s identification plate or written certification of specification or exemption/special permit provided by the carrier, when a cargo tank is provided by the carrier.
DOT specification or UN standard packagings
A person who offers a DOT specification or UN standard packaging that is subject to the requirements in Part 178 of the HMR is required to perform all functions necessary to bring that package into compliance with Parts 173 and 178 of the HMR, as identified by the packaging manufacturer or subsequent distributor, in accordance with Section 178.2 of the HMR.
Shipments of fissile radioactive materials, and Type B or highway route controlled quantity packages of radioactive materials
The shipper is required to notify the consignee of the dates of shipment and expected arrival. The shipper must also notify each consignee of any special loading/unloading instructions prior to the first shipment.
Shipments of irradiated reactor fuel
The shipper must provide physical protection in compliance with a plan established under either:
- The U.S. Nuclear Regulatory Commission; or
- Equivalent requirements approved by Pipeline and Hazardous Materials Safety Administration’s (PHMSA’s) Associate Administrator for Hazardous Materials Safety.
Notes: The shipper’s certification on a shipping paper for transportation of hazardous materials requires the shipper to certify that the above-named materials are properly classified, described, packaged, marked and labeled, and are in proper condition for transportation according to the applicable regulations of the DOT.
The shipper, or the person or employee of the person who originates the shipment for transportation is responsible for properly preparing the hazardous material for transportation. The hazardous material must be properly classified to ensure that it is prepared using the proper packaging, marking(s), and label(s). If a company is a shipper of hazardous material, it is responsible to understand the preparation requirements including all applicable packaging related requirements.
Requirements for specific types of packagings
- HMR define requirements for bulk, non-bulk, and empty packagings.
Specific types of packagings have different requirements for hazardous materials transportation. Hazardous Materials Regulations (HMR) define the terms and requirements for:
- Bulk packagings,
- Non-bulk packagings, and
- Empty packagings.
Common types of bulk packagings include cargo tanks, portable tanks, intermediate bulk containers (IBCs), and tank cars.
Common types of non-bulk packagings include boxes, drums, barrels, jerricans, pails, bags, composite packagings, and cylinders.
The regulations include maximum capacity, maximum net mass, and water capacity. Empty packaging must conform to certain provisions or be subject to other requirements of the HMR.
Bulk packaging
- Hazardous Materials Regulations define specifics for bulk packaging used to transport hazardous materials, including maximum capacity, maximum net mass, and water capacity.
A bulk packaging is a packaging in which hazardous materials are loaded with no intermediate form of containment AND has:
- A maximum capacity greater than 450 L (119 gal) as a receptacle for a liquid; or
- A maximum net mass greater than 400 kg (882 lb) and a maximum capacity greater than 450 L (119 gal) as a receptacle for a solid; or
- A water capacity greater than 454 kg (1,000 lb) as a receptacle for a gas.
Bulk packaging does not include a vessel or barge. Bulk packaging does include transport vehicles and freight containers. Common types of bulk packagings include cargo tanks, portable tanks, intermediate bulk containers (IBCs), and tank cars.
Bulk packaging is a term that is used throughout the Hazardous Materials Regulations (HMR). Knowing if a hazmat package is bulk or non-bulk is an essential piece of knowledge when determining what requirements in the regulations apply to the shipment.
Cargo tanks
- Cargo tanks are commonly used to transport hazardous materials such as liquids or gases.
- HMR outline several specifications for cargo tanks.
A cargo tank is a bulk packaging that is a tank intended primarily for the carriage of liquids or gases. The cargo tank includes appurtenances, reinforcements, fittings, and closures. A cargo tank is not fabricated under a specification for cylinders, intermediate bulk containers, portable tanks, multi-unit tank car tanks, or tank cars.
A cargo tank is permanently attached to or forms a part of a motor vehicle, or is not permanently attached to a motor vehicle but which, by reason of its size, construction or attachment is loaded or unloaded without being removed from the motor vehicle. The definition for cargo tank can be found in 171.8.
Common specification cargo tanks include MC 306, MC 307, MC 312, DOT 406, DOT 407, and DOT 412. The specifications for construction of cargo tanks can be found in Part 178, subpart J of the Hazardous Materials Regulations.
Cargo tanks are required to undergo certain tests and inspections.
Cargo tanks are required to be properly marked and placarded for transport.
Portable tanks
- The HMR outlines specifics for portable tanks used to transport hazardous materials.
A portable tank is a bulk packaging (except a cylinder having a water capacity of 1000 pounds or less) designed primarily to be loaded onto, or on, or temporarily attached to a transport vehicle or ship and equipped with skids, mountings, or accessories to facilitate handling of the tank by mechanical means. It does not include a cargo tank, tank car, multi-unit tank car tank, or trailer carrying 3AX, 3AAX or 3T cylinders. The definition for portable tank can be found in 171.8.
The specifications for construction of portable tanks can be found in Part 178, subpart H of the Hazardous Materials Regulations. Portable tanks include Department of Transportation (DOT) specification portable tanks, intermodal (IM) portable tanks and United Nations (UN) portable tanks.
Portable tanks are required to undergo certain tests and inspections. For more information see 178.276,178.277, and Part 180, subpart G.
Portable tanks are required to be properly marked, labeled or placarded for transport. For information on these topics see the ezExplanations Markings, Labeling, and Placarding.
Intermediate bulk containers (IBCs)
- The HMR outlines specifics for intermediate bulk containers used to transport hazardous materials.
An intermediate bulk container (IBC) is a rigid or flexible portable packaging, other than a cylinder or portable tank, which is designed for mechanical handling. The definition for intermediate bulk container can be found in 171.8.
The specifications for construction of intermediate bulk containers can be found in Part 178,subparts N and O of the Hazardous Materials Regulations.
Intermediate bulk containers are required to undergo certain tests and inspections. For more information see Part 180, subpart D.
Intermediate bulk containers are required to be properly marked, labeled or placarded for transport. For information on these topics see the ezExplanations Markings, Labeling, and Placarding.
Non-bulk packaging
- Hazardous Materials Regulations define specifics for non-bulk packaging used to transport hazardous materials, including maximum capacity, maximum net mass, and water capacity.
A non-bulk packaging is a packaging which has:
- A maximum capacity of 450 L (119 gal) or less as a receptacle for a liquid; or
- A maximum net mass of 400 kg (882 lb) or less and a maximum capacity of 450 L (119 gal) or less as a receptacle for a solid; or
- A water capacity of 454 kg (1,000 lb) or less as a receptacle for a gas.
The definition for non-bulk packaging can be found in 171.8.
Common types of non-bulk packagings include boxes, drums, barrels, jerricans, pails, bags, composite packagings, and cylinders.
Non-bulk packagings that meet the manufacturing requirements in the regulations must be marked with the appropriate United Nations (UN) marking specified in 178.503 or for cylinders the markings specified in Part 178, subpart C.
Non-bulk packaging is a term that is used throughout the Hazardous Materials Regulations. Knowing if a hazmat package is bulk or non-bulk is an essential piece of knowledge when determining what requirements in the regulations apply to the shipment.
Non-bulk packaging designs
- The HMR outlines specifics for non-bulk packaging designs used to transport hazardous materials.
The following design requirements apply to non-bulk packages, except as provided for liquid hazardous materials in non-bulk packagings, as detailed in Section 172.312.
- Inner packaging closures - A combination packaging containing liquid hazardous materials must be packed so that closures on inner packagings are upright.
- Friction - The nature and thickness of the outer packaging must be such that friction during transportation is not likely to generate an amount of heat sufficient to dangerously alter the chemical stability of the contents.
- Securing and cushioning inner packagings - Inner packagings of combination packagings must be packed, secured, and cushioned to prevent their breakage or leakage and to control their shifting within the outer packaging under conditions normally incident to transportation. Cushioning material must not be capable of reacting dangerously with the contents of the inner packagings or having its protective properties significantly weakened in the event of leakage.
- Metallic devices - Nails, staples, and other metallic devices shall not protrude into the interior of the outer packaging in such a manner as to be likely to damage inner packagings or receptacles.
- Vibration - Each non-bulk package must be capable of withstanding, without rupture or leakage, the vibration test procedure specified in Section 178.608 of the Hazardous Materials Regulations (HMR).
Filling limits for non-bulk packagings
- The HMR outlines filling limits for non-bulk packagings used to transport liquid hazardous material.
A single or composite non-bulk packaging may be filled with a liquid hazardous material only when the specific gravity of the material does not exceed that marked on the packaging, or a specific gravity of 1.2 if not marked, with the following exceptions:
- A Packing Group I packaging may be used for a Packing Group II material with a specific gravity not exceeding the greater of 1.8, or 1.5 times the specific gravity marked on the packaging, provided all the performance criteria can still be met with the higher specific gravity material;
- A Packing Group I packaging may be used for a Packing Group III material with a specific gravity not exceeding the greater of 2.7, or 2.25 times the specific gravity marked on the packaging, provided all the performance criteria can still be met with the higher specific gravity material; and
- A Packing Group II packaging may be used for a Packing Group III material with a specific gravity not exceeding the greater of 1.8, or 1.5 times the specific gravity marked on the packaging, provided all the performance criteria can still be met with the higher specific gravity material.
A non-bulk packaging may not be filled with a hazardous material to a gross mass greater than the maximum gross mass marked on the packaging, unless otherwise allowed in Section 173.24a.
- A single or composite non-bulk packaging which is tested and marked for Packing Group I liquid hazardous materials may be filled with a solid Packing Group II hazardous material to a gross mass, in kilograms, not exceeding the rated capacity of the packaging in liters, multiplied by 1.5, multiplied by the specific gravity marked on the packaging, or 1.2 if not marked.
- A single or composite non-bulk packaging which is tested and marked for Packing Group I liquid hazardous materials may be filled with a solid Packing Group III hazardous material to a gross mass, in kilograms, not exceeding the rated capacity of the packaging in liters, multiplied by 2.25, multiplied by the specific gravity marked on the packaging, or 1.2 if not marked.
- A single or composite non-bulk packaging which is tested and marked for Packing Group II liquid hazardous materials may be filled with a solid Packing Group III hazardous material to a gross mass, in kilograms, not exceeding the rated capacity of the packaging in liters, multiplied by 1.5, multiplied by the specific gravity marked on the packaging, or 1.2 if not marked.
Packagings tested with hydrostatic test pressure as prescribed in Section 178.605.
Packagings tested as prescribed in Section 178.503(a)(5) of the Hazardous Materials Regulations (HMR) may be used for liquids only when the vapor pressure of the liquid conforms to one of the following:
- The vapor pressure must be such that the total pressure in the packaging will not exceed two-thirds of the marked test pressure. The total pressure in the packaging is the vapor pressure of the liquid plus the partial pressure of air or other inert gases, less 100 kPa (15 psi) at 55 degrees C (131 degrees F), determined on the basis of a maximum degree of filling in accordance with Section 173.24a(d) and a filling temperature of 15 degrees C (59 degrees F);
- The vapor pressure at 50 degrees C (122 degrees F) must be less than four-sevenths of the sum of the marked test pressure plus 100 kPa (15 psi); or
- The vapor pressure at 55 degrees C (131 degrees F) must be less than two-thirds of the sum of the marked test pressure plus 100 kPa (15 psi).
No hazardous material may remain on the outside of a package after filling.
Mixed contents in a single packaging
- The HMR outlines limits for mixed contents in a single packaging used to transport more than one hazardous material.
An outer non-bulk packaging may contain more than one hazardous material only when:
- The inner and outer packagings used for each hazardous material conform to the relevant packaging sections of Part 173 applicable to that hazardous material;
- The package as prepared for shipment meets the performance tests prescribed in Part 178 of the Hazardous Materials Regulations (HMR) for the packing group indicating the highest order of hazard for the hazardous materials contained in the package;
- Corrosive materials in bottles are further packed in securely closed inner receptacles before packing in outer packagings; and
- For transportation by aircraft, the total net quantity does not exceed the lowest permitted maximum net quantity per package as shown in Column 9A or 9B, as appropriate, of the Section 172.101 Hazardous Materials Table. The permitted maximum net quantity must be calculated in kilograms if a package contains both a liquid and a solid.
A packaging containing inner packagings of Division 6.2 materials may not contain other hazardous materials, except dry ice.
Liquids must not completely fill a receptacle at a temperature of 55 degrees C (131 degrees F) or less.
Cylinders
- The HMR outlines specifics for cylinders used to transport hazardous materials.
A cylinder is a pressure vessel designed for pressure higher than 40 psia (pounds per square inch absolute) and has a circular cross section. It does not include a portable tank, multi-unit tank car tank, tank car, or cargo tank. The definition for cylinder can be found in 171.8.
The specifications for construction of cylinders can be found in Part 178, subpart C of the Hazardous Materials Regulations (HMR).
Cylinders are required to undergo certain tests and inspections. For more information see Part 180, subpart C.
Cylinders are required to be properly marked and labeled for transport. Placards may be required for transporting certain loads of cylinders.
Overpacks
- The HMR outlines specifics for overpacks used to transport hazardous materials.
- Certain labels and markings may be required.
What is an overpack? According to the definition in Section 171.8:
An overpack means an enclosure that is used by a single consignor to provide protection or convenience in handling of a package or to consolidate two or more packages, except as provided in Subpart K of Part 178. An overpack does not include a transport vehicle, freight container, or aircraft unit load device.
Examples of overpacks are one or more packages:
- Placed or stacked onto a load board such as a pallet and secured by strapping, shrink wrapping, stretch wrapping, or other suitable means; or
- Placed in a protective outer packaging such as a box or crate.
Authorized packages containing hazardous materials may be offered for transportation in an overpack as defined in Section 171.8 of the Hazardous Materials Regulations (HMR), if all of the following conditions are met:
- The package meets the requirements of Section 173.21 and 173.24 of the HMR.
- The overpack is marked with the proper shipping name and identification number, and labeled as required by the HMR for each hazardous material contained within the overpack unless markings and labels representative of each hazardous material in the overpack are visible.
- Each package subject to the orientation marking requirements of Section 172.312 of the HMR is packed in the overpack with its filling holes up and the overpack is marked with package orientation marking arrows on two opposite vertical sides of the overpack with the arrows pointing in the correct direction or orientation.
- The overpack is marked with the word “OVERPACK” when specification packagings are required, unless specification markings on the inside packagings are visible.
- Packages containing Class 8 (Corrosive) materials in Packing Group I or Division 5.1 (Oxidizing) materials in Packing Group I may not be overpacked with any other materials.
Shrink-wrapped or stretch-wrapped trays may be used as outer packagings for inner packagings prepared in accordance with the limited quantity provisions or consumer commodity provisions of the HMR, provided that the inner packagings are not fragile, liable to break or be easily punctured. Each package may not exceed 44 lbs (20 kg) gross weight.
Hazardous materials which are required to be labeled “POISON” may be transported in the same motor vehicle with material that is marked or known to be foodstuffs, feed or any edible material intended for consumption by humans or animals provided the hazardous materials:
- Are marked, labeled, and packaged in accordance with the HMR;
- Conform to the requirements of Section 173.25(a); and
- Are overpacked as specified in Section 177.841(e) of the HMR or in an overpack which is a United Nations (UN) 1A2, 1B2, or 1N2 drum tested and marked for a Packing Group II or higher performance level.
Notes: An overpack is generally thought of as being an outer enclosure containing a package or packages. Authorized overpacks for use in combination packagings will be discussed in more detail in the topic: Hazmat - Non-bulk Packagings.
- Hazardous Materials Regulations define specifics for non-bulk packaging used to transport hazardous materials, including maximum capacity, maximum net mass, and water capacity.
A non-bulk packaging is a packaging which has:
- A maximum capacity of 119 gal (450 L) or less as a receptacle for a liquid; or
- A maximum net mass of 882 lb (400 kg) or less and a maximum capacity of 119 gal (450 L) or less as a receptacle for a solid; or
- A water capacity of 1,000 lb (454 kg) or less as a receptacle for a gas.
The definition for non-bulk packaging can be found in 171.8.
Common types of non-bulk packagings include boxes, drums, barrels, jerricans, pails, bags, composite packagings, and cylinders.
Non-bulk packagings that meet the manufacturing requirements in the regulations must be marked with the appropriate United Nations (UN) marking specified in 178.503 or for cylinders the markings specified in Part 178, Subpart C.
Non-bulk packaging is a term that is used throughout the Hazardous Materials Regulations. Knowing if a hazmat package is bulk or non-bulk is an essential piece of knowledge when determining what requirements in the regulations apply to the shipment.
Empty packagings
- Empty packagings with the residue of a hazardous material must be treated the same as when the packaging contained a greater quantity of the HM.
- Additional HMR requirements do not apply if the empty packaging follows certain provisions.
An empty packaging containing only the residue of a hazardous material must be offered for transportation and transported in the same manner as when it previously contained a greater quantity of that hazardous material, unless otherwise provided in Section 173.29.
An empty packaging is not subject to any other requirements of the Hazardous Materials Regulations (HMR) if it conforms to the following provisions:
- Any hazardous material shipping name and identification number markings, any hazard warning labels or placards, and any other markings indicating that the material is hazardous are removed, obliterated, or securely covered in transportation. (The provision does not apply to transportation in a transport vehicle or a freight container if the packaging is not visible in transportation and the packaging is loaded by the shipper and unloaded by the shipper or consignee.)
- The packaging:
- Is unused;
- Is sufficiently cleaned of residue and purged of vapors to remove any potential hazard;
- Is refilled with a material which is not hazardous to such an extent that any residue remaining in the packaging no longer poses a hazard; or
- Contains only the residue of an Other Regulated Materials—Domestic (ORM-D) material; a non-flammable gas with no subsidiary hazard at an absolute pressure less than 280 kPa (40.6 psia) at 20 degrees C (68 degrees F); and
- Any material contained in the packaging does not meet the definitions in Section 171.8 of the HMR for a hazardous substance, a hazardous waste, or a marine pollutant.
A non-bulk packaging containing only the residue of a hazardous material covered by Table 2 of Section 172.504 of the HMR:
- Does not have to be included in determining the applicability of the placarding requirements of Subpart F of Part 172; and
- Is not subject to the shipping paper requirements of the HMR when collected and transported by a contract or private carrier for reconditioning, remanufacture or reuse.
Provisions for describing an empty packaging on a shipping paper are detailed in Section 172.203(e). A package which contains a residue of an elevated temperature material may remain marked in the same manner as when it contained a greater quantity of the materials even though it no longer meets the definition in Section 171.8 for an elevated temperature material.
Note: It is important to note that unless all traces of the hazardous material have been removed, the packaging still possesses the hazard of that material and as such still poses a risk in transportation.
What exceptions apply to the packaging requirements?
- Packaging exceptions are applied in certain situations where normal packaging requirements cannot be met.
- HMR define requirements for bulk, non-bulk, and empty packagings.
Specific types of packagings have different requirements for hazardous materials transportation. Hazardous Materials Regulations (HMR) define the terms and requirements for:
- Bulk packagings,
- Non-bulk packagings, and
- Empty packagings.
Common types of bulk packagings include cargo tanks, portable tanks, intermediate bulk containers (IBCs), and tank cars.
Common types of non-bulk packagings include boxes, drums, barrels, jerricans, pails, bags, composite packagings, and cylinders.
The regulations include maximum capacity, maximum net mass, and water capacity. Empty packaging must conform to certain provisions or be subject to other requirements of the HMR.