Elements of a safety program
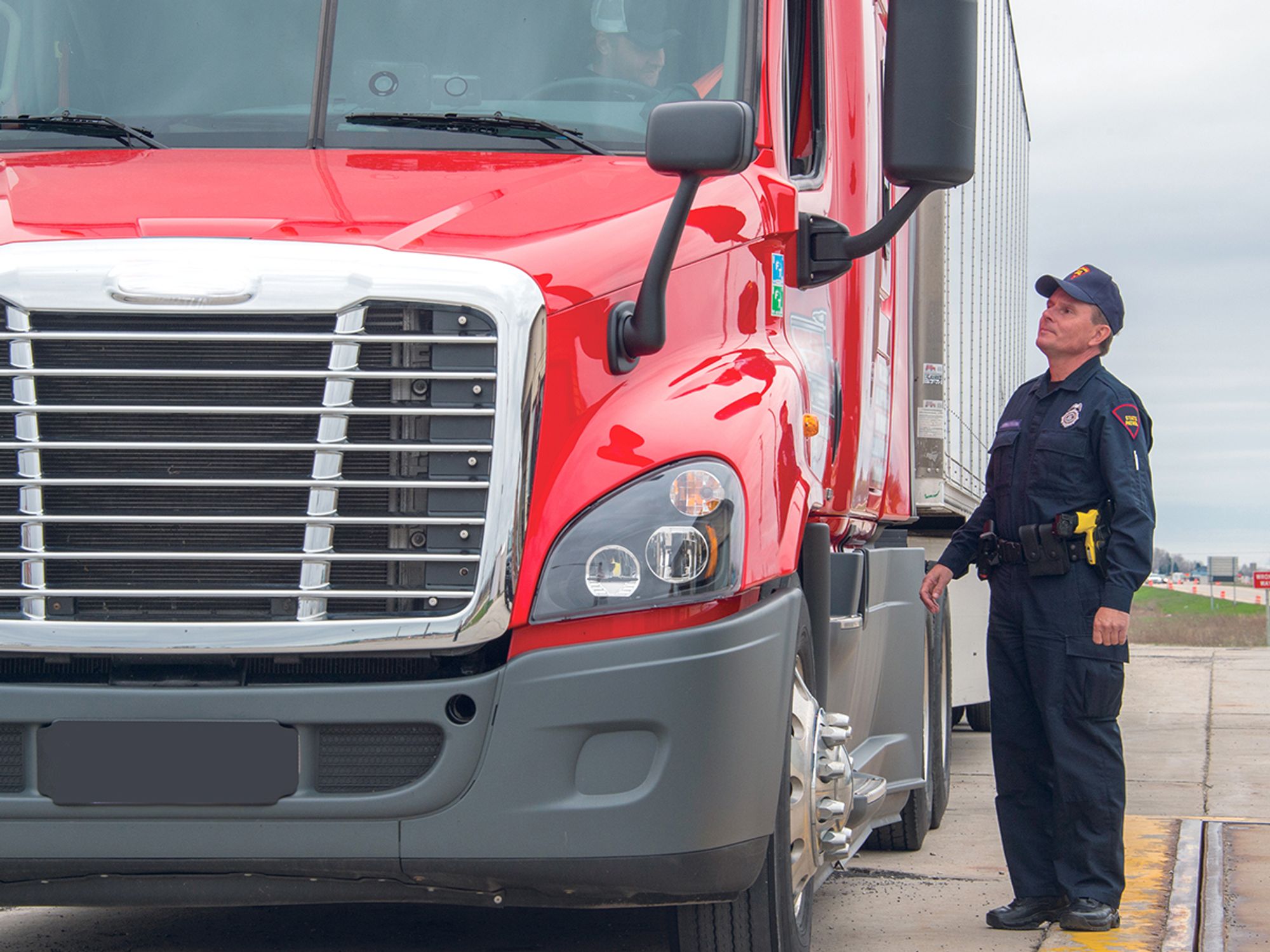
- Safety programs are in place set and uphold standards as well as identify deficiencies before crashes occur.
- Train and retrain all affected employees in your standards.
Most effective motor carrier safety management programs share common fundamental elements. When combined into a cohesive system, these elements can produce a continually improving safety management program that produces consistently positive results:
- Identify safety deficiencies — Predicting your safety results begins with inspecting and analyzing your organization’s current work processes and activities. What are your greatest safety and loss prevention concerns — vehicle accidents, injuries, driver turnover, all of the above? In its simplest terms, the process of continual improvement stresses developing standard procedures for virtually every work activity, and continually improving these processes.
- Develop your safety standards — Once you have established your starting point and identified unsafe behaviors and work activities in need of correction or improvement, the next step is to determine exactly what the corrections and/or improvements should look like.
In other words, you need to develop detailed safety standards and procedures for virtually every work activity and process of the organization — everything from how you expect your drivers to get in and out of their vehicles (3-points of contact) to how your dispatchers use their computers (office ergonomics).
For most motor carrier operations, employee risk exposure can be divided into two basic categories:
- Drivers who are exposed to both driving hazards and the potential for personal injury, and
- Non-driving employees are generally only exposed to potential personal injury hazards.
So, as the safety professional at your organization, you need to develop standards for safe driving to prevent accidents and incidents as well as general workplace safety to prevent injuries.
- Train all employees in your standards — Once you have established a safety standard, you need to train the affected employees in the standard. You are responsible to show and teach them exactly what is expected in the way of behavior and performance. There are two components to training:
- The actual training of employees in your new standards, and
- Management follow-up and enforcement.
Regardless of the type and method of training, if employees are allowed to deviate from the new standards, your safety results will not improve. Continual enforcement and enthusiastic follow-up are essential ingredients toward the success of your established safety standards.
Allowing deviation from your standards will significantly impact your safety effort. Drivers, supervisors, and all employees will learn immediately that current need or crisis will rarely compromise the established safety standards. Deviation is simply not an option in most situations.
Once deviation is accepted, a new, lower standard is created and your safety standards are compromised.
- Measure, monitor, and record — Unless you implement an effective system of monitoring and measuring, you will not know if your new safety standards and training efforts are positively impacting your overall results.
In addition, all collected data must be maintained so that a historical record can be developed over time. Your recordkeeping system should provide sufficient data that can be used to target specific areas in need of improvement and employees in need of training or other corrective action.
- Reinforce, recognize, and encourage — The final element of an effective motor carrier safety management program involves the management activities of providing:
- Constant reinforcement of your established safety standards,
- Appropriate recognition of employees who consistently meet your safety standards, and
- Enthusiastic support and encouragement for all employees to help them behave and perform according to your safety standards.
The purpose of developing and implementing a comprehensive safety program is to:
- Increase consistency, structure, and order to your entire operation;
- Add accountability and predictability of safety results as management tools;
- Communicate the safety goals, values, and philosophy of top management; and
- Improve overall safety results and profitability.
Your safety management program as a system We now know that a system is made up of a number of processes, with each process having its own individual desired result (output).
All motor carriers have work processes. For instance, you have a processes for recruiting, screening, hiring, and maintaining qualified drivers, maintaining your vehicles, assigning loads and other work assignments, and monitoring compliance in all of these areas.
How these processes are performed and who performs them make up your safety management controls and protect your company, it’s employees, and the motoring public.