While OSHA compliance and hazard mitigation are commonplace in the safety industry, “risk” is also important. Understanding risk is critical for safety professionals to manage priorities and communicate with upper management. Simply stated, risk refers to the probability an incident will occur multiplied by the severity that would result from such an incident. By assessing for risk, safety professionals can prioritize which projects to address first, as well as which controls should be utilized. Further, safety professionals can use risk to communicate to upper management the impact of specific issues on the business. Many safety management standards, such as ISO 45001 or ANSI Z10, offer risk matrices or guidance tools to assist in this effort.
Risk assessment and management
While many people use the terms “hazard” and “risk” interchangeably, they are actually quite different. “Hazard” refers to something that can cause harm, like a machine, electricity, or toxic fumes. “Risk” refers to how likely a hazard is to occur and how damaging it will be should it occur. Hazard is generally used within the context of safety/injury, while risk can refer to financial “hazards” (losses), IT networks, and a variety of other topics.
Most safety professionals have at some point handed upper management a list of hazards or “compliance issues” found in an audit. In response, a member of upper management likely asked, “So, what does this mean?” Too often, the safety professional responds by mentioning the possibility of the company being inspected and fined, or listing the regulations being violated. To better communicate with upper management, safety professionals should learn the language of upper management and frame their safety guidance and advice in terms of risk.
Risk rating matrix
- When assessing risk, employers must take into account the severity of injury or illness that could result from a hazard, as well as the likelihood of such an incident occurring. Hazards with high severity and high probability of occurring are the greatest risk.
The risk/hazard rating of a job or task usually considers two factors:
- Severity — the seriousness of the injury or illness (e.g., first-aid, minor, lost-time, permanent disability, fatality) that could result from an incident.
- Probability — the likelihood that an incident will occur (e.g., frequently, occasionally, unlikely).
A job or task with a high probability and high severity has the highest risk; when there is low probability and low severity, that is the lowest risk. However, there are numerous combinations of severity/probability in between.
Many companies utilize a risk matrix or table that assigns numeric measures to risk based on probability and severity; the ratings are used to prioritize safety efforts. A sample risk matrix is provided below.
The risk matrix should be tailored to suit each organization’s risk tolerance and should take into account the specific operations, hazards, and available controls.
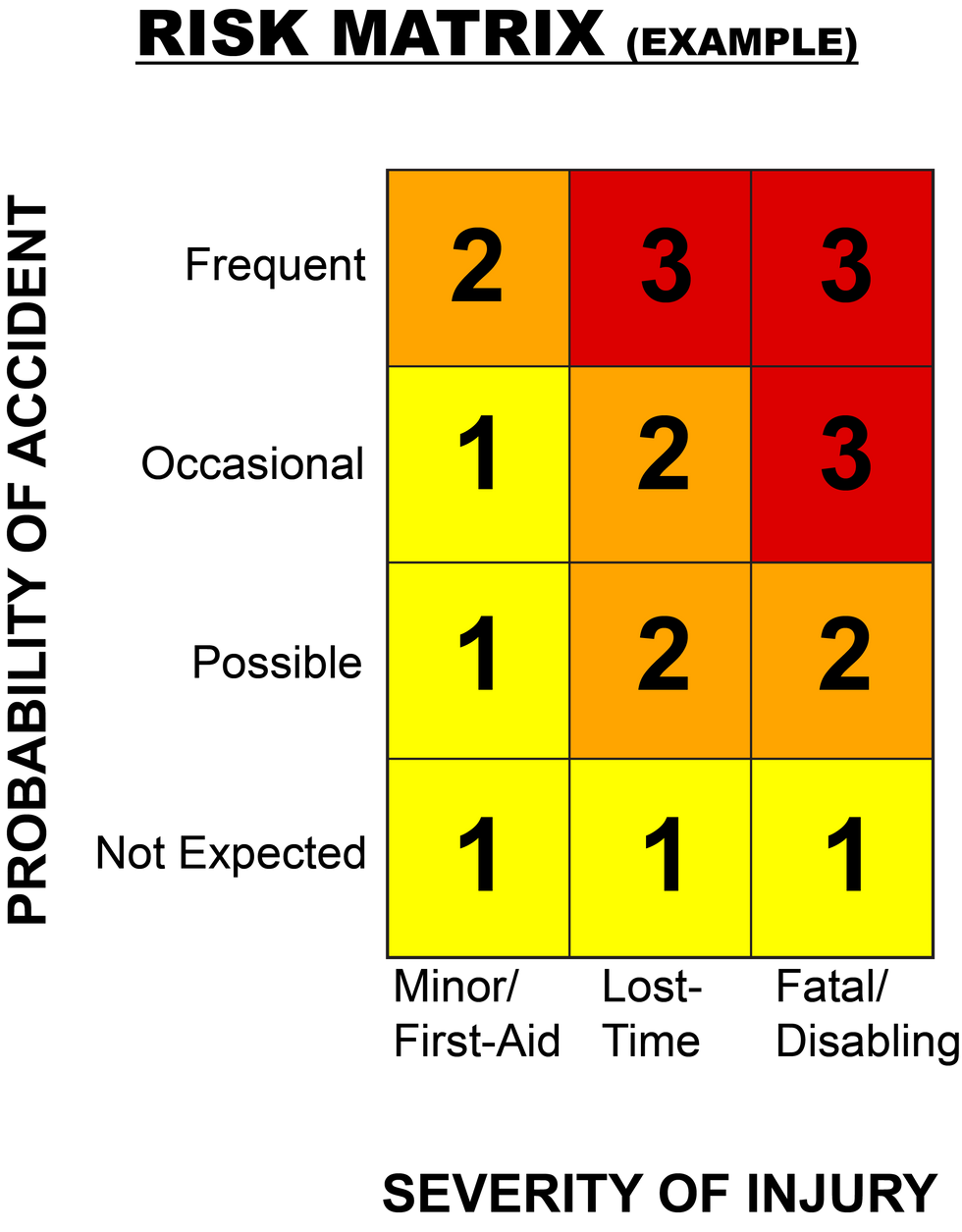
Priority legend
3 Highest priority — stop task until hazards are controlled
2 Hazards must be controlled as soon as possible
1 Risks are acceptable — no further controls required
Using the language of risk
- Safety professionals should learn to communicate safety needs in the workplace in terms of risk management to help business owners and executives understand the full impact of not managing hazards properly.
Imagine a safety professional asking upper management for a $500,000 investment to keep from getting a $7,000 fine from the Occupational Safety and Health Administration (OSHA). The request is unlikely to be approved. Stating the request in terms of risk management, however, would involve explaining an analysis and prioritizing of risk, along with the financial implications.
Risk is a common language between business owners and executives who manage risk every day. Putting hazards into the language of risk helps executives see the need for managing the identified safety risks or hazards.
Financial implications include suffering operational delays, which directly impacts the number of products a company might produce, for example, and could result in direct consequences.
Unfortunately, many safety professionals haven’t had formal training in risk management, so learning the concepts may take some time. However, it doesn’t have to be daunting, and tools are available to help.
Risk management industry standard
- The AASP Risk Management technical report offers expert guidance and tools to help safety professionals understand, assess, and manage risk in the workplace.
A technical report published by the American Society of Safety Professionals (ASSP) provides safety professionals with techniques and implementation strategies to combat risk and better protect workers. ASSP TR-31010-2020 Risk Management – Techniques for Safety Practitioners is designed to assist safety practitioners and company decision-makers in understanding, assessing, and managing risk so organizations can achieve their business objectives.
The technical report provides expert guidance on the selection, modification, combination, and application of 50 risk management techniques to help improve the way risk and uncertainty are managed. It includes basic techniques for industry newcomers and complex methods for seasoned safety professionals. The safety resource explains the fundamentals of risk assessment and risk treatment and covers prevention-through-design practices that are applicable throughout the life cycle of a system. Safety professionals can apply the techniques to a range of occupational settings, situations, and operational stages of a business.
Analysis tools
Examples of some of the 50 tools covered by the ASSP Technical Report include:
- ALARP – Getting to a risk level that is “as low as reasonably practicable” by classifying risks into specific categories.
- Risk Hierarchy – A comprehensive portfolio of risks organized by type.
- Causal Mapping – Identifies causality by mapping interactions between risks.
- Ishikawa (Fishbone) Analysis/Cause and Effect Analysis – A team-based approach using a pictorial display to help consider all possible scenarios and causes of a specific effect.
- Business Impact Analysis – A method to evaluate effects of incidents on critical business operations.
The Technical Report contains a table that provides information on the complexity of each of the 50 tools, along with guidance on how each may or may not apply to different situations a safety professional might encounter. For example, ALARP is a medium complexity tool strongly applicable to determining risk context, as well as for risk evaluation. However, it is not very applicable to risk analysis. On the other hand, Risk Hierarchy is low complexity and strongly applicable to communicating risk, but not as applicable to analysis.
Safety professionals don’t have to learn all 50 tools at once. To start out, the professional should choose about five tools for communicating with the next level manager. As safety professionals make progress and get invited to decision-makers’ meetings, they go back to the Technical Report and learn more. Then, next time, they’re part of the solution. Eventually, as safety professionals get into upper-level safety and start communicating with the CEO, there are tools in the report to help, focusing on enterprise-wide risk management.
Safety management industry standards
- There are two major industry standards to help guide employers in implementing a safety plan for the workplace: ISO 45001 and ANSI Z10.
- In certain industries, suppliers or potential contracts may require companies to implement one standard over the other.
Two major voluntary industry standards can help employers design and implement a safety and health management system:
- ISO 45001 — Occupational health and safety management systems – Requirements with guidance for use
- ANSI/ASSP Z10 — Occupational Health and Safety Management Systems
ISO 45001
The International Organization for Standardization (ISO) 45001 Occupational health and safety management systems — Requirements with guidance for use is a standard for the implementation and maintenance of occupational safety and health management systems. The standard guides companies in taking a systematic and proactive approach to worker safety, giving safety an equal “seat at the table” alongside other management systems such as environmental, quality, IT and data security, and product safety, all of which have had international standards for a while.
Like other management systems standards, ISO 45001 reduces risk and increases performance. In the case of ISO 45001, the risk is to worker safety and health. The standard provides a framework to systematically improve safety and business processes at the same time. It requires using concepts and techniques such as the hierarchy of controls, risk assessment, and root-cause analysis, along with significant input and participation from workers. While these techniques help reduce injuries and illnesses, they also improve business performance.
The indirect benefits of obtaining certification include recognition for achieving an international benchmark, lowering costs, reducing turnover and lost time, and reducing equipment and process downtime. The standard has other benefits as well. Investors will likely feel more confident in an ISO 45001-certified company because the company has shown it is actually identifying and managing the risks.
To achieve the maximum benefits and to claim official certification, a company must go through a third-party audit and approval process from an accredited registrar. Completing full certification is certainly no easy task. If a company already has an ISO management system in place, however, the transition will be less complicated.
For companies that want to implement a management system but are not interested in certification, the ISO 45001 standard can be used as a best-practice guidance. A company can purchase the standard and self-implement to whatever degree is appropriate, understanding that internal impacts (such as fewer injuries and better performance) may be seen, but external benefits (such as recognition) will not be gained without certification.
ANSI Z10
The American National Standards Institute (ANSI) Z10 Occupational Health and Safety Management Systems standard was originally released in 2005. Like most other ANSI standards, ANSI Z10 is “self-certifying” in that there is not necessarily a requirement for a third-party auditor to conduct a conformance assessment. A company can purchase the standard and implement it with no assistance from a third party.
The ANSI standard follows the same general principles as the Occupational Safety and Health Administration (OSHA)’s Recommended Practices, but provides much more guidance and many tools, covering such topics as management leadership, employee involvement, hazard identification/prevention/control, training, and evaluation. It contains tools such as job hazard analysis guidance and risk matrices.
Deciding on a standard
In choosing a standard, a company should consider what the organization hopes to accomplish and also what the stakeholders or customers are asking for. Some companies may choose to achieve certification to ISO 45001, but implement additional elements from ANSI Z10.
In certain industries, suppliers or potential contracts may ask for one standard over the other. Employers should talk with some organizations that have used these systems to find out pros and cons of each.
Hazard identification and assessment
- To properly assess the risks posed by hazards, employers first need to identify all potential hazards.
- Employers should include assessments of emergency and non-routine situations that may arise.
“Risk” is the product of hazard and exposure. Thus, risk can be reduced by controlling or eliminating the hazard or by reducing workers’ exposure to hazards. An assessment of risk helps employers understand hazards in the context of their own workplaces and prioritize hazards for permanent control.
One of the root causes of workplace injuries, illnesses, and incidents is the failure to identify or recognize hazards that are present, or that could have been anticipated. A critical element of any effective safety and health program is a proactive, ongoing process to identify and assess such hazards.
To identify and assess hazards, employers and workers should:
- Collect and review information about the hazards present or likely to be present in the workplace.
- Conduct initial and periodic workplace inspections of the workplace to identify new or recurring hazards.
- Investigate injuries, illnesses, incidents, and close calls/near misses to determine the underlying hazards, their causes, and safety and health program shortcomings.
- Group similar incidents and identify trends in injuries, illnesses, and hazards reported.
- Consider hazards associated with emergency or non-routine situations.
- Determine the severity and likelihood of incidents that could result for each hazard identified, and use this information to prioritize corrective actions.
Some hazards, such as housekeeping and tripping hazards, can and should be fixed as they are found. Fixing hazards on the spot emphasizes the importance of safety and health and takes advantage of a safety leadership opportunity.
Emergency and non-routine situations
Emergencies present hazards that need to be recognized and understood. Non-routine or infrequent tasks, including maintenance and startup/shutdown activities, also present potential hazards. Develop plans and procedures for responding appropriately and safely to hazards associated with foreseeable emergency scenarios and non-routine situations.
Identify foreseeable emergency scenarios and non-routine tasks, taking into account the types of material and equipment in use and the location within the facility. Scenarios such as the following may be foreseeable:
- Fires and explosions;
- Chemical releases;
- Hazardous material spills;
- Startups after planned or unplanned equipment shutdowns;
- Non-routine tasks, such as infrequently performed maintenance activities;
- Structural collapse;
- Disease outbreaks;
- Weather emergencies and natural disasters;
- Medical emergencies; and
- Workplace violence.
Gathering information and performing inspections
- Employers may already have internal and external data available to help with identifying hazards, including equipment operating manuals, Safety Data Sheets, inspection reports, records of previous illness/injury, and more.
- Employers must arrange for regular safety inspections, as well as inspections whenever working conditions (work processes, equipment, etc.) change. A follow-up plan is needed to ensure any safety issues found are corrected.
Information on hazards may already be available to employers and workers, from both internal and external sources.
Employers should collect, organize, and review information with workers to determine what types of hazards may be present and to which workers may be exposed or potentially exposed. Information available may include:
- Equipment and machinery operating manuals.
- Safety Data Sheets (SDS) provided by chemical manufacturers.
- Self-inspection reports and inspection reports from insurance carriers, government agencies, and consultants.
- Records of previous injuries and illnesses, such as Occupational Safety and Health Administration (OSHA) 300 and 301 logs and reports of incident investigations.
- Workers’ compensation records and reports.
- Patterns of frequently-occurring injuries and illnesses.
- Exposure monitoring results, industrial hygiene assessments, and medical records (appropriately redacted to ensure patient/worker privacy).
- Existing safety and health programs (lockout/tagout, confined spaces, process safety management, personal protective equipment, etc.).
- Input from workers, including surveys or minutes from safety and health committee meetings.
- Results of job hazard analyses, also known as job safety analyses.
Information about hazards may also be available from outside sources such as:
- Occupational Safety and Health Administration (OSHA), National Institute for Occupational Safety and Health (NIOSH), and Centers for Disease Control and Prevention (CDC) websites, publications, and alerts.
- Trade associations.
- Labor unions, state and local occupational safety and health committees/coalitions (“COSH groups”), and worker advocacy groups.
- Safety and health consultants.
Inspecting the workplace for safety hazards
Hazards can be introduced over time as workstations and processes change, equipment or tools become worn, maintenance is neglected, or housekeeping practices decline. Setting aside time to regularly inspect the workplace for hazards can help identify shortcomings so that they can be addressed before an incident occurs. Employers should:
- Conduct regular inspections of all operations, equipment, work areas and facilities. Have workers participate on the inspection team and talk to them about hazards that they see or report.
- Document inspections to later verify that hazardous conditions are corrected. Take photos or video of problem areas to facilitate later discussion and brainstorming about how to control them, and for use as learning aids.
- Include all areas and activities in these inspections, such as storage and warehousing, facility and equipment maintenance, purchasing and office functions, and the activities of on-site contractors, subcontractors, and temporary employees.
- Regularly inspect both plant vehicles (e.g., forklifts, powered industrial trucks) and transportation vehicles (e.g., cars, trucks).
- Use checklists that highlight things to look for. Typical hazards fall into several major categories, such as those listed below, although each workplace will have its own list:
- General housekeeping;
- Slip, trip, and fall hazards;
- Electrical hazards;
- Equipment operation;
- Equipment maintenance;
- Fire protection;
- Work organization and process flow (including staffing and scheduling);
- Work practices;
- Workplace violence;
- Ergonomic problems; and
- Lack of emergency procedures.
Employers should also plan to do safety inspections before changing operations, workstations, or workflow; making major organizational changes; or introducing new equipment, materials, or processes, seeking the input of workers and evaluating the planned changes for potential hazards and related risks.
Many hazards can be identified using common knowledge and available tools. For example, workers can easily identify or remove hazards such as broken stair rails or frayed electrical cords. Workers can be a very useful internal resource, especially if they are trained in how to identify and assess risks.
Identifying health hazards
- Health hazards that may be identified might be chemical, physical, biological, or ergonomic.
- In some cases, identifying such hazards may require specialized knowledge; small businesses can often obtain this help for free through OSHA’s On-Site Consultation Program.
Identifying health hazards is typically more complex than identifying physical safety hazards. For example, gases and vapors may be invisible, often have no odor, and may not have an immediately noticeable harmful health effect.
Health hazards include chemical hazards (solvents, adhesives, paints, toxic dusts, etc.); physical hazards (noise, radiation, heat, etc.); biological hazards (infectious diseases); and ergonomic risk factors (heavy lifting, repetitive motions, vibration).
Reviewing workers’ medical records (appropriately redacted to ensure patient/worker privacy) can be useful in identifying health hazards associated with workplace exposures. Employers should:
- Identify chemical hazards — Review Safety Data Sheets (SDSs) and product labels to identify chemicals in the workplace that have low exposure limits, are highly volatile, or are used in large quantities or in unventilated spaces. Identify activities that may result in skin exposure to chemicals.
- Identify physical hazards — Identify any exposures to excessive noise (areas where workers must raise their voices to be heard by others), elevated heat (indoor and outdoor), or sources of radiation (radioactive materials, X-rays, or radiofrequency radiation).
- Identify biological hazards — Determine whether workers may be exposed to sources of infectious diseases, molds, toxic or poisonous plants, or animal materials (fur or scat) capable of causing allergic reactions or occupational asthma.
- Identify ergonomic risk factors — Examine work activities that require heavy lifting, work above shoulder height, repetitive motions, or tasks with significant vibration.
- Conduct quantitative exposure assessments — When possible, using air sampling or direct reading instruments.
- Review medical records — To identify cases of musculoskeletal injuries, skin irritation or dermatitis, hearing loss, or lung disease that may be related to workplace exposures.
Identifying and assessing health hazards may require specialized knowledge. Small businesses can obtain free and confidential occupational safety and health advice services, including help identifying and assessing workplace hazards, through the Occupational Safety and Health Administration (OSHA)’s On-Site Consultation Program.
Conducting incident investigations
- Thoroughly investigating all safety incidents helps an employer to identify where hazards exist in their workplaces.
- Effective incident investigations will not stop when a single cause of an incident is found, but should continue until the root cause — the “why” — is identified.
Workplace incidents — including injuries, illnesses, close calls/near misses, and reports of other concerns — provide a clear indication of where hazards exist. Thoroughly investigating incidents and reports will help identify hazards that are likely to cause future harm. The purpose of an investigation must always be to identify the root causes (and there is often more than one) of the incident or concern, in order to prevent future occurrences. Employers should:
- Develop a clear plan and procedure for conducting incident investigations, so that an investigation can begin immediately when an incident occurs. The plan should cover items such as:
- Who will be involved;
- Lines of communication;
- Materials, equipment, and supplies needed; and
- Reporting forms and templates.
- Train investigative teams on incident investigation techniques, emphasizing objectivity and open-mindedness throughout the investigation process.
- Conduct investigations with a trained team that includes representatives of both management and workers.
- Investigate close calls/near misses.
- Identify and analyze root causes to address underlying program shortcomings that allowed the incidents to happen.
- Communicate the results of the investigation to managers, supervisors, and workers to prevent recurrence.
Effective incident investigations do not stop at identifying a single factor that triggered an incident. They ask the questions “Why?” and “What led to the failure?” For example, if a piece of equipment fails, a good investigation asks: “Why did it fail?” “Was it maintained properly?” “Was it beyond its service life?” and “How could this failure have been prevented?” Similarly, a good incident investigation does not stop when it concludes that a worker made an error. It asks such questions as: “Was the worker provided with appropriate tools and time to do the work?” “Was the worker adequately trained?” and “Was the worker properly supervised?”
Identifying Physical Hazards
What are physical hazards?
Physical hazards abound in the workplace. The mere fact that a company exists makes it prone to physical hazards — even the benign office has tripping and falling hazards. In an industrial setting, the huge variety of machines, processes, and equipment create a challenging set of hazards that a safety professional must deal with.
Processes that use large quantities of chemicals present a unique set of challenges. The physical properties of certain chemicals, such as flammable and combustible liquids, compressed gases, solvents, and explosives make them highly dangerous.
You may not think much about falls, but trips and falls often result in injury and lost time. Falls can even be fatal. In the workplace, there are many situations that contribute to falls:
- Floors with water, grease, or cracks
- Trash or stock piled in pedestrian walkways
- Ladders in need of repair
- Stairs with loose rails or step treads
Maintaining equipment in peak condition, practicing good housekeeping techniques, and providing signs to warn of physical hazards goes a long way to improve overall safe working conditions. Part of the safety professional’s job is to assess the workplace for physical hazards and see that they are corrected or controlled. There are many OSHA standards that have specific requirements for ensuring that physical hazards in the workplace are eliminated. In this section, you will find action steps, training action plans, tips, and checklists on a variety of topics related to controlling physical hazards.
Combustible dust
Combustible dusts are fine particles that present an explosion hazard when suspended in air in certain conditions. A dust explosion can be catastrophic and cause employee deaths, injuries, and destruction of entire buildings. In many combustible dust accidents, employers and employees were unaware that a hazard even existed. It is important that employers determine if their operations have this hazard, and if so, that they take action now to prevent tragic consequences.
A wide range of industries possess combustible dust hazards and a wide variety of materials cause combustible dust incidents. (Combustible dusts can be intentionally manufactured powders, such as corn starch or aluminum powder coatings, or may be generated by handling and processing solid combustible materials such as wood and plastic pellets. For example, polishing, grinding, transporting, and shaping many of these materials can produce very small particles.)
Action steps
The following are general action steps that should be taken to identify and control dust hazards. For detailed guidance specific to your operations, consult with a qualified professional, as well as industry standards, as applicable (for example, those published by the National Fire Protection Association).
- Assess your facility for processes that generate dust. Have dusts analyzed for combustibility hazards. (There are several factors that determine how explosive a dust can be, as well as some key measurements for determining dust explosibility. These include particle size, moisture content, ambient humidity, oxygen available for combustion, the shape of the dust particle, and the concentration of dust in the air, i.e., minimum explosive concentration or MEC.)
- Understand the five elements needed for a combustible dust explosion: Combustible dust (fuel); ignition source (heat); oxygen in air (oxidizer); dispersion of dust particles in sufficient quantity and concentration; and confinement of the dust cloud.
- Understand that there can be a primary explosion or event that shakes loose hidden dust (for example, from piping or rafters) which can cause a devastating secondary explosion.
- Ensure operations have proper engineering design and controls and inspect/maintain those controls. Seek outside assistance/expertise as needed to ensure proper dust control procedures/methods are in place.
- Develop an ignition control program, limiting and controlling potential ignition sources in dust accumulation areas.
- Train employees on the explosion hazards of combustible dusts.
- Implement a housekeeping program with regular cleaning frequencies for floors and horizontal surfaces, such as ducts, pipes, hoods, ledges, and beams, to minimize dust accumulations within operating areas of the facility. (Even seemingly small amounts of accumulated dust can cause catastrophic damage. The CSB estimated, for example, that the explosion that devastated a pharmaceutical plant in 2003 and killed six employees was caused by dust accumulations mainly under 0.25 inches deep. The CSB study references National Fire Protection Administration (NFPA) warnings that a catastrophic explosion can occur from as little as 1/32 of an inch of accumulated dust — around the thickness of a dime — covering just 5 percent of a room’s surface.)
- Ensure working surfaces are designed in a manner to minimize dust accumulation and facilitate cleaning.
- Ensure electrical equipment and electrically-powered cleaning devices such as vacuum cleaners are approved for the hazard classification for Class II locations.
- Select and use industrial trucks that are approved for the combustible dust locations.
- Prohibit the use of cleaning methods that can disperse combustible dust into the air (i.e., compressed air and dry sweeping).
- Ensure the ready availability of SDSs for the chemicals which could become combustible dust under normal operations. Note: The Chemical Safety Board has found that many SDSs do not provide sufficient data on combustible dust hazards. However, OSHA revised the HazCom rule in 2012. In the revised rule, combustible dust hazards must be addressed on labels and SDSs. Label elements are provided for combustible dust in the final HCS and include the signal word “warning” and the hazard statement “May form combustible dust concentrations in the air.”
- Implement an emergency action plan and maintain exit routes properly.
For chemicals in a solid form that do not present a combustible dust hazard, but may form combustible dusts while being processed in normal downstream uses, OSHA allows the chemical manufacturer some flexibility in labeling requirements. The manufacturer or importer may transmit the label to the customer at the time of the initial shipment, but the label does not need to be included with subsequent shipments unless it changes. This provides the needed information to the downstream users on the potential hazards in the workplace, while acknowledging that the solid metal or other materials do not present the same hazards that are produced when these materials are processed under normal conditions of use.
Training action plan
Workers are the first line of defense in preventing and mitigating fires and explosions. If the people closest to the source of the hazard are trained to recognize and prevent hazards associated with combustible dust in the plant, they can be instrumental in recognizing unsafe conditions, taking preventative action, and/or alerting management. While OSHA standards require training for certain employees, all employees should be trained in safe work practices applicable to their job tasks, as well as on the overall plant programs for dust control and ignition source control. They should be trained before they start work, periodically to refresh their knowledge, when reassigned, and when hazards or processes change.
- Define combustible dusts.
Combustible dusts are fine particles,
fibers, chips, chunks, or flakes
that could be an explosion hazard
when they’re suspended in air
under certain conditions.
Many products can be fuel for a
dust explosion when they’re used in powdered form. Here are some
examples:
- Flour, sugar, powdered milk, or other food-related products;
- Wood;
- Paper;
- Textiles;
- Charcoal and other carbon-rich materials;
- Sulfur and other chemicals;
- Aluminum, zinc, and other metals; and
- Epoxy resin and other plastics.
- Introduce the hazards.
A dust explosion can cause deaths
and serious injuries. An explosion
can destroy an entire building. In
many combustible dust incidents,
employers and employees didn’t
know that a hazard even existed.
Here’s an example of what happens
during a combustible dust explosion.
- In February 1999, a deadly fire and explosion occurred in a foundry in Massachusetts. An investigation found that a fire started in a molding machine and then spread to ventilation ducts. The small initial explosion in the ductwork disturbed resin dust that had settled on the outside of the ducts, creating a dust cloud. This dust provided fuel for a secondary explosion that was powerful enough to lift the roof and cause walls to collapse.
- Identify the types of industries that may be at risk. Combustible dust explosion hazards can exist in a variety of industries, including: agriculture, chemicals, food, grain, fertilizer, tobacco, plastics, wood, paper, tire and rubber, furniture, textiles, pesticides, pharmaceuticals, coal, metal processing, recycling operations, and others.
- Explain how dust explosions can happen. The familiar fire triangle is made up of: oxygen, an ignition source (heat), and fuel. All three conditions must be present for a fire to start. Because oxygen is normally always present in the air, fires are usually prevented by keeping the fuel separate from the ignition source. In addition to the fire triangle elements, the “dust explosion pentagon” adds two more conditions: dust particles and the confinement of the dust cloud. Similar to the fire triangle, if one part of the pentagon is missing, a combustible dust explosion can’t occur. If a dust cloud is ignited in an enclosed area such as a room, vessel, ductwork, or process equipment, it burns very fast and may explode. Even if the initial explosion is small, it could shake up accumulated dust in the area to form another dust cloud. Often these secondary explosions are far more destructive.
- Outline how to look for combustible
dust hazards.
To identify the factors that could
contribute to an explosion, employers
should evaluate the hazards of
all: materials, operations, spaces (including hidden ones),
and potential ignition sources. Some likely areas where dust can
build up include:
- Parts of the building’s structure,
- Conduit and pipe racks,
- Electrical cable trays,
- Floors,
- Areas above suspended ceilings, and
- On and around equipment (including leaks around dust collectors and ductwork).
- Discuss what can be done to
control dust build-up.
If the dust isn’t building up, it lowers the risk of a dust explosion. There
are many ways to keep dust under
control. Some of these methods are
to:
- Conduct regularly scheduled inspections,
- Clean up dust on a regular basis,
- Use proper dust collection systems and filters,
- Keep dust from escaping from equipment or ventilation systems,
- Use surfaces that are easy to clean,
- Provide easy access to inspect and clean hidden areas where dust might build up,
- Use cleaning methods that don’t stir up dust clouds, and
- Use vacuum cleaners approved for dust collection.
- Describe methods to prevent
dust from igniting.
Keeping ignition sources under
control is an important part of any
fire safety program. Some actions
employers can take include the following:
- Use proper wiring methods;
- Make sure electrically powered equipment (including forklifts) is approved for the location;
- Control static electricity (bond equipment to ground);
- Keep smoking areas, open flames, sparks, and heated surfaces separate from dusts;
- Follow a hot work permit program; and
- Follow a preventive maintenance program.
- Discuss some methods to minimize
injuries and damage from
a combustible dust explosion.
Some of the steps employers can
take to minimize injuries and damage
from a combustible dust explosion
could include:
- Developing an emergency action plan,
- Maintaining emergency exit routes,
- Setting up operations in areas where the hazards are away from workers and equipment,
- Setting up isolation barriers around hazardous operations,
- Making sure dust handling equipment has pressure relief venting that’s directed away from workers and equipment, and
- Installing specialized spark detection and fire suppression systems in dust handling equipment.
Tips
The amount of dust accumulation necessary to cause an explosive concentration can vary greatly. This is because there are so many variables — the particle size of the dust, the method of dispersion, ventilation system modes, air currents, physical barriers, and the volume of the area in which the dust cloud exists or may exist. As a result, simple rules of thumb regarding accumulation (such as writing in the dust or visibility in a dust cloud) can be subjective and misleading. The hazard analysis should be tailored to the specific circumstances in each facility and the full range of variables affecting the hazard.
Many locations need to be considered in an assessment. One obvious place for a dust explosion to initiate is where dust is concentrated. In equipment such as dust collectors, a combustible mixture could be present whenever the equipment is operating.
Other locations to consider are those where dust can settle, both in occupied areas and in hidden concealed spaces. A thorough analysis will consider all possible scenarios in which dust can be disbursed, both in the normal process and potential failure modes.The facility analysis must identify areas requiring special electrical equipment classification due to the presence (or potential presence) of combustible dust. Various OSHA standards as well as industry (e.g., NFPA) can be consulted.
Checklist
Follow these checklists to prevent combustible dust hazards.
Hazard assessment
- Are there processes that accumulate dust? If so, have the dusts been analyzed for combustibility?
- Are periodic assessments conducted to determine dust explosion possibilities?
- Are employees and supervisors involved in identifying dust explosion hazards, for example through job hazard analyses?
- Is particular attention given during the hazard assessment to dust collection systems and areas not in plain view?
Prevention
- Have proper engineering design and controls been implemented for operations involving combustible dust; for example, dust control in process equipment and fugitive dust control; grounding and bonding; and separator devices?
- Is a comprehensive housekeeping program implemented?
- Are potential ignition sources limited and controlled in dust accumulation areas?
- Is it prohibited to use compressed air and similar cleaning methods that could disperse combustible dusts into the air?
- Are electrical services appropriate for Class II location? Consult applicable codes, for example the National Electrical Code.
- Are industry standards, such as NFPA 654, followed as applicable?
- Is a preventive maintenance program in place to minimize release of fugitive dust?
Note: Minor, but steady leaks, can cause large amounts of dust to accumulate.
Training
- Have employees received training on the hazards of dust?
- Have employees received training on specific characteristics of the dust that they work with?
- Have employees been trained to recognize potential ignition sources?
- Do employees know which processes/locations accumulate dust (for example, cable trays, pipe racks, floors, above ceilings, and structural members)?
- Are employees instructed to report plant fires and near misses?
Confined spaces
Employees in industry and construction are often asked to perform work in confined spaces, but many confined spaces contain serious hazards that endanger the employees who enter those spaces. For this reason, the Occupational Safety and Health Administration requires employers to implement certain procedures that protect workers from the hazards posed by confined spaces. These include procedures for identifying physical hazards and hazardous atmospheres in confined spaces, controlling and eliminating these hazards, and more.
Action steps
- Evaluate the workplace to determine if any spaces are permit-required confined spaces.
- Inform exposed employees, by posting danger signs or by any other equally effective means, of the existence and location of and the danger posed by the permit spaces.
- Decide whether employees will enter spaces. (If employees will not enter spaces, take appropriate, effective prevention measures.)
- Implement a written permit space program.
- Evaluate hazards of permit spaces.
- Provide employees with the opportunity to observe any monitoring or testing of permit spaces.
- Develop and implement the means, procedures, and practices necessary for safe permit space entry operations.
- Establish a permit system.
- Provide training.
- Perform entry according to OSHA requirements.
- Verify that conditions in the permit space are acceptable for entry throughout the duration of an authorized entry.
- Provide appropriate equipment (PPE, rescue equipment, testing, monitoring, ventilation, lighting, etc.)
- Provide at least one attendant outside the permit space into which entry is authorized for the duration of entry operations.
- Develop and implement rescue procedures.
- If contractors are involved in the confined space entry, follow pertinent OSHA requirements.
Training action plans
Training must be such that all employees whose work is regulated by OSHA’s confined spaces standard acquire the understanding, knowledge, and skills necessary for the safe performance of the duties assigned.
Training must be provided to each affected employee:
- Before the employee is first assigned duties relative to the confined space.
- Before there is a change in assigned duties.
- Whenever there is a change in permit space operations that presents a hazard about which an employee has not previously been trained.
- Whenever you have reason to believe either that there are deviations from the permit space entry procedures or that there are inadequacies in the employee’s knowledge or use of these procedures.
The training must establish employee proficiency in the duties required by the confined spaces standard and must introduce new or revised procedures, as necessary, for compliance.
Training should be specific to the employee’s function relative to the confined space. For instance, if the employee is an authorized entrant, then training should focus specifically on tasks and hazards he may face in this role.
In general, training should cover:
- Equipment to be used,
- Communicating with others involved in the work,
- Hazard awareness and recognition,
- Specific roles and duties,
- Monitoring,
- Medical and first aid, and
- Rescue.
Any work that involves contractors also requires special training and communication, both from the host to the contractor and from the contractor to the host.
Documentation
The employer must certify that required training has been accomplished. The certification must contain:
- Each employee’s name,
- The signatures or initials of the trainers, and
- The dates of training.
Tips
- A permit-required confined space is a confined space that has one or more of the following characteristics:
- Contains or has the potential to contain a hazardous atmosphere;
- Contains a material that has the potential for engulfing an entrant;
- Has an internal configuration such that an entrant could be trapped or asphyxiated by inwardly converging walls or by a floor which slopes downward and tapers to a smaller cross section; or
- Contains any other recognized serious safety or health hazard.
- When workers enter a permit space, at least one person must remain outside to monitor, summon help, or provide assistance.
- An attendant may attend to more than one permit space provided he/she can perform all required duties without compromising the safety of any entrant in all spaces being monitored (there is no proximity requirement).
- An employee can be both an entry supervisor and entrant as long as the employee has had the appropriate training and the duties of one activity do not conflict with the duties of the other.
- The entrants need to wear chest or full body harnesses with retrieval lines to make non-entry rescue attempts easier.
- The attendant needs to communicate with the entrants to monitor their conditions. If a situation arises that requires emergency rescue, the attendant should summon the rescue service and stay outside of the permit space entrance.
- An attendant can be a trained member of the rescue service, but cannot enter the permit space until the rest of the team has arrived to start proper rescue procedures.
Checklist
View these confined space checklists to ensure safety and compliance at your facility.
Monitoring
- When working in permit-required confined spaces, are environmental monitoring tests taken?
- Are authorized entrants or their representatives provided an opportunity to observe any monitoring or testing of permit spaces?
- Are permit spaces tested to determine if acceptable entry conditions exist prior to entry?
- Are permit spaces tested or monitored as necessary to determine if acceptable entry conditions are being maintained during the course of entry operations?
Equipment
- Is necessary personal protective equipment available?
- Is rescue and emergency services equipment available?
- Is communications equipment provided to allow the attendant to communicate with authorized entrants as necessary to monitor entrant status and to alert entrants of the need to evacuate the permit space?
General
- Are those having active roles in entry operations appropriately designated (for example, authorized entrants, attendants, entry supervisors, and persons who test or monitor the atmosphere in a confined space)?
- Is at least one attendant stationed outside the confined space for the duration of the entry operation?
- Are appropriate rescue personnel available?
- Are permit spaces flushed, ventilated, purged, and rendered inert to eliminate or control atmospheric hazards prior to entry?
Emergency action plans
This regulation applies to all companies that fall under a particular OSHA standard that requires an emergency action plan. However, it is wise for all employers to have action plans for any emergency that may be reasonably expected to occur in the workplace. Where required by OSHA, employers must develop a plan (called an emergency action plan or EAP) for emergency situations so that there is a literal “plan of action” for employees to take in the event of fires, toxic chemical releases, hurricanes, tornadoes, blizzards, floods, and other similar catastrophic events.
Action steps
Include the following minimum requirements in the EAP to ensure that it covers those designated actions employers and employees must take to ensure employee safety from fire and other emergencies.
- Establish emergency escape procedures and emergency escape route assignments.
- Develop procedures to be followed by employees who remain to operate critical plant operations before they evacuate.
- Establish procedures to account for all employees after emergency evacuation has been completed.
- Assign rescue and medical duties for those employees who are to perform them.
- List the preferred means of reporting fires and other emergencies.
- Develop a list of employee names or regular job titles of persons or departments who can be contacted for further information or explanation of duties under the plan.
- Establish an employee alarm system. If the employee alarm system is used for alerting fire brigade members, or for other purposes, use a distinctive signal for each purpose.
- List the types of evacuation to be used in emergency circumstances.
- Designate and train a sufficient number of employees to assist in the safe and orderly emergency evacuation of employees before implementing the EAP.
- Review the EAP with each covered employee upon initial assignment, when the employee’s responsibility or designated actions under the plan change, and when the plan changes.
Training action plan
You should develop an emergency action team prior to implementing the EAP. Begin by designating and training a sufficient number of employees to assist in the safe and orderly emergency evacuation of their coworkers.
- List the names or job titles of persons who can be contacted for more information on the plan. Trainees should understand:
- The employee alarm system,
- How to report fires and other emergencies, and
- Which personnel are designated to perform rescue and medical duties and their individual responsibilities.
- Explain how all employees will be accounted for after the emergency evacuation has been completed. Make sure employees understand:
- Critical plant operations and who is designated to remain behind to operate it/shut it down before they evacuate, and
- Emergency escape procedures and emergency escape routes.
Tips
A map of the facility showing specific areas, exit routes, exit doors, and head count locations is a useful training tool and should also be posted around the company.
If a fire occurs, safe and orderly evacuation is necessary. Your company should have an established evacuation plan, with procedures and exits indicated. Find out what it is and where you are expected to go during a fire or fire drill. A head count location should be established so that once everyone is evacuated, you meet at a designated spot to account for each employee.
Other than fires, severe weather emergencies are the most common emergency situations that occur. Severe weather emergencies include hurricanes, tornadoes, excessive heat, heavy snow, and extreme cold weather conditions.
If a bomb threat is made at your facility, always take the threat seriously. Immediately notify a supervisor or the safety manager of the threat and evacuate the premises (do not search for a bomb unless instructed by police to look for foreign or suspicious objects).
Checklist
Follow these checklists to ensure you and your employees are prepared for any potential emergencies.
Emergency action plan
- Is there an emergency action plan (EAP) in place detailing procedures employees should follow in an emergency?
- Does the EAP include procedures for all anticipated emergency situations (i.e., fire, tornado, bomb threat, or explosion)?
- Does the EAP include escape procedures and routes?
- Does the EAP contain procedures for those remaining in the facility to perform critical operations?
- Do you have headcount procedures (location or methods for accounting for employees)?
- If your company is located in a high-rise building, does your emergency program include appropriate escape information?
- Do you have an employee assistance program or some other means to provide counseling to employees should a disaster occur?
Disaster recovery
- Have you established a work location that could be used should your facility be unavailable due to disaster or emergency?
- Does the temporary work location have all necessary equipment so critical business functions can be carried out?
- Have necessary safety measures been taken to ensure that the temporary location is safe and will have necessary protective equipment?
Rescue workers
- Is air monitoring conducted to make sure rescue area is safe?
- Are rescue workers protected against hazards that may be encountered (i.e., asbestos, silica)?
- Are rescue workers provided proper protective equipment for the hazards they face?
Alarms and warnings
- Does the employee alarm system provide warning for necessary emergency action as called for in the emergency action plan?
- Is the employee alarm capable of being perceived above ambient noise or light levels by all employees in the affected portions of the workplace?
- Is the employee alarm distinctive and recognizable as a signal to evacuate the work area or take necessary actions?
- Have all employees been informed of the preferred means of reporting emergencies, such as manual pull box alarms, public address systems, radio or telephones?
- Are emergency telephone numbers posted near telephones, or employee notice boards, and other conspicuous locations?
- Have procedures been established for sounding emergency alarms in the workplace?
Fire alarm systems
- If you have a non-supervised fire alarm system, is it tested bimonthly?
- If you have a supervised employee alarm system (that is, does the alarm have a device that indicates system malfunction), is it tested yearly?
Entrances and exits
If you are a general industry employer, the Subpart E Exit routes regulations apply to your company. Your facility must provide a safe means of exiting from buildings or structures for the purpose of general egress, or for the purpose of exiting in the case of fire or other emergencies. In addition, you must also provide a clear and unobstructed path to the entrance of your facility.
Action steps
- Make sure exit routes are permanent.
- Separate exits using fire resistant materials.
- Limit openings into an exit.
- Ensure the number of exit routes is adequate.
- Ensure there are at least two exit routes.
- Provide adequate exit discharge.
- Make sure exit doors are unlocked.
- Use side-hinged exit doors.
- Ensure the capacity of exit routes is adequate.
- Provide exit routes that meet minimum height and width requirements.
- Keep exit routes free of explosive or highly flammable furnishings or other decorations.
- Maintain exit routes free and unobstructed.
- Ensure lighting and marking is adequate and appropriate.
- Maintain exit routes during construction, repairs, or alterations.
- Ensure that the alarm system is operable.
Training action plan
You must designate and train employees to assist in a safe and orderly evacuation of other employees.
You must also review the emergency action plan with each employee covered by the plan. This review should be conducted:
- When the plan is developed or the employee is assigned initially to a job,
- When the employee’s responsibilities under the plan change, and
- When the plan is changed.
Tips
- The line-of-sight to an exit sign must be clearly visible at all times.
- Maintain exit routes during construction, repairs, or alterations.
- Ceilings of exit routes must be at least 7 feet, 6 inches high.
- Exit access must be at least 28 inches wide at all points.
Checklist
Review these checklists to ensure exit routes at your facility meet compliance.
Exit design
- Are exit routes made of approved components and permanently attached to the building?
- Are exit routes designed and maintained to provide adequate headroom?
- Are exit doors designed so that no device or alarm failure will impede or prevent emergency use of exits?
Capacity of means of egress
- Are width and capacity of exit routes in compliance with OSHA standards?
- Is the capacity of the exit route sufficient for the occupant load?
- Where more than one way of exit access leads to an exit, does each have a width adequate for the number of persons it must accommodate?
Arrangement of exits
- Have you assured that no furnishings, decorations, or other objects are placed as to obstruct exits or exit visibility?
- Are exits adequately lighted so an employee with normal vision can see along the exit route?
Access to exits
- Are exit doors unlocked?
- Are exits readily accessible at all times?
- Are doors, from a room to an exit or to a way of exit access, of the side-hinged, swinging type?
- Is access to an exit NOT through a bathroom, or other room subject to locking (except where the exit is required to serve only the room subject to locking)?
- Are ways of exit access and the doors to exits to which they lead clearly recognizable as such?
- Is exit access arranged so that it will not be necessary to travel toward any area of high hazard occupancy in order to reach the nearest exit?
- Is exit access travel effectively shielded from high hazard locations by suitable partitions or other physical barriers?
- Is the minimum width of any way of exit access at least 28 inches?
Arrangement of exits
- Are exits marked by a readily visible sign?
- Is access to exits marked by readily visible signs if it is not immediately visible?
- Is any door, passage, or stairway that could be mistaken for an exit or a way of exit access, identified by a sign reading “Not an Exit” or similar designation, or identified by a sign indicating its actual character?
Protective enclosure of exits
- When an exit is protected by separation from other parts of the building, does the separating construction meet OSHA requirements (i.e., 1-hour fire resistance rating when the exit connects three stories or less)?
Fire protection
OSHA has many requirements concerning fire protection in the workplace. These requirements are found in Subpart L and in some other specific standards. Among the items addressed by OSHA standards is fire brigades, all portable and fixed fire suppression equipment, fire detection systems, and fire or employee alarm systems.
Action steps
- Provide approved and appropriate portable fire extinguishers.
- Mount, locate, and identify portable fire extinguishers so that they are readily accessible to employees without subjecting the employees to possible injury.
- Maintain fire extinguishers in a fully charged and operable condition.
- Inspect, maintain, and test fire extinguishers.
- Provide necessary training to employees who are expected to use portable fire extinguishers.
- Ensure that hose and standpipe systems meet OSHA requirements.
- Ensure all automatic sprinkler systems meet OSHA requirements.
- Maintain any fixed extinguishing systems per OSHA requirements.
- Follow OSHA requirements for any fire brigade you choose to form.
- Ensure fire detection systems are maintained properly.
- Provide an employee alarm system that gives warning for necessary emergency action as called for in the emergency action plan, or for reaction time for safe escape of employees from the workplace or the immediate work area, or both.
Training action plan
The level and type of training needed for fire protection depends on the level and type of fire protection your facility has in place. For instance, if you have a fire brigade, extensive training must be provided to fire brigade members, per 1910.156.
Similarly, if you provide portable fire extinguishers for employee use, such employees must be trained. This training must familiarize employees with the general principles of fire extinguisher use and the hazards involved with incipient stage fire fighting. Training must be provided upon initial employment and at least annually thereafter.
You must also provide training to any employees who have been designated to use fire fighting equipment as part of an emergency action plan. Training must be provided upon initial employment and at least annually thereafter.
You should also train all employees on the actions they need to take relative to your emergency alarm system. They should be familiar with the distinct sounds of the system and what each sound means.
Tips
- Fire extinguishers have to be kept in their designated locations at all times when not being used.
- When extinguishers are removed for maintenance or testing, they must be replaced by an operable unit.
Checklists
Review these checklists to ensure fire safety at your facility.
Fire extinguishers
- Are portable fire extinguishers provided, mounted, located, and identified so that they are readily accessible to employees?
- Are only approved portable fire extinguishers used?
- Are portable fire extinguishers maintained, fully charged, operating properly, and kept in designated places?
- Are portable fire extinguishers provided for employee use and selected and distributed based on the classes of anticipated fires and on the size and degree of hazard that would affect their use?
- Are travel distances to extinguishers appropriate?
- Are all portable fire extinguishers in the workplace inspected, maintained, and tested?
- Is hydrostatic testing performed by trained persons with suitable testing equipment and facilities?
- Are portable extinguishers hydrostatically tested at the intervals listed in Table L-1 of 1910.157?
- Has an educational program been provided to familiarize employees with the general principles of fire extinguisher use and the hazards involved with incipient stage fire fighting?
- Have employees been trained (who have been designated to use fire fighting equipment) in the use of the equipment?
Fire alarm
- Have you established an employee alarm system that complies with 1910.165?
- If the employee alarm system is used for alerting fire brigade members, or for other purposes, is a distinctive signal used for each purpose?
- Are all employee alarm systems in proper working condition, except when undergoing repairs or maintenance?
Fire detection systems
- Are all devices approved for use?
- Are fire detection systems and components returned to normal operating condition as soon as possible after each use or test?
Fire brigades
- If you choose to form a fire brigade, are the requirements of 1910.156 met?
Sprinkler systems
- Are automatic sprinkler system water control valves, air and water pressure checked weekly/periodically as required?
- Are fire control sprinkler heads kept clean?
- Are sprinkler heads protected by metal guards when exposed to physical damage?
- Is proper clearance maintained below sprinkler heads?
Flammable liquids
OSHA’s Flammable Liquids regulation, 1910.106, applies to all persons who handle, use, store, or transport flammable liquids. A flammable liquid means any liquid having a flashpoint at or below 199.4°F (within that definition, there are four categories of flammable liquids).
Action steps
- Ensure flammable liquids are stored and handled properly.
- Familiarize yourself with the different categories of flammable liquids (this will determine storage and usage requirements).
- Ensure containers meet the design requirements in 1910.106.
- Provide adequate drainage, dikes, and walls for tanks.
- Take precautions to prevent ignition by eliminating or controlling sources of ignition.
- Ensure the design (including selection of materials) fabrication, assembly, test, and inspection of piping systems containing flammable liquids is suitable for the expected working pressures and structural stresses.
- Provide suitable emergency and fire protection.
- Ensure adequate ventilation.
- Install electrical wiring properly.
- Follow proper procedures for dispensing liquids.
Training action plan
Any employee involved in storage, transfer, use, or disposal of flammable liquids needs to be trained to handle them safely and to follow your company’s established procedure.
Generally, training content should cover:
- Categories of flammable liquids,
- Handling procedures,
- Storage procedures, and
- Spill cleanup.
In addition, if your company receives, stores, or handles flammable liquids in storage tanks in areas that have the potential to flood, you need to have employees trained on emergency response procedures.
A hands-on approach is appropriate in this part of the training session. In fact, you may want to demonstrate how to do specific procedures related to flammables at your facility. Then allow each employee to try the procedure, so they can perform them correctly and so they will remember them better.
Tips
- When transferring flammable liquids, always bond and ground the containers.
- If purchasing plastic containers of five gallons or less for use with flammable liquids, purchase those with a built-in metal grounding strip.
Checklist
Review these checklists to ensure flammable liquid safety at your facility.
Containers
- Are all connections on drums and piping, vapor and liquid tight?
- Are all flammable liquids kept in closed containers when not in use (e.g., parts cleaning tanks, pans, etc.)?
- Are approved containers and portable tanks used for the storage and handling of flammable liquids?
- Are bulk drums of flammable liquids grounded and bonded to containers during dispensing?
- Are flammable liquids, such as gasoline, kept in an approved safety can?
- Are portable storage tanks equipped with emergency venting that will relieve excessive internal pressure caused by fire exposure?
- Are safety cans used for dispensing flammable liquids at a point of use?
- Are storage cabinets used to hold flammable liquids, labeled “Flammable — Keep Fire Away”?
- Are storage tanks adequately vented to prevent the development of excessive vacuum or pressure as a result of filling, emptying, or atmosphere temperature changes?
Handling
- Are all containers over 30 gallons in inside storage rooms stacked individually?
- Are firm separators placed between containers of combustibles or flammables, when stacked one upon another, to assure their support and stability?
Storage
- Are “No Smoking” rules enforced in areas involving storage and use of hazardous materials?
- Are all solvent wastes, and flammable liquids kept in fire-resistant, covered containers until they are removed from the worksite?
- Are all spills of flammable liquids cleaned up promptly?
- Is proper storage of flammable materials practiced to minimize the risk of fire including spontaneous combustion?
- Is there one clear aisle at least 3 feet wide?
Ladders
OSHA’s ladder regulations, at 1910.23, apply to any general industry workplace that uses ladders to perform duties (other than construction work) at high elevations.
Action steps
- Use ladders that are designed and approved for the intended purpose.
- Ensure ladders meet OSHA specifications.
- Follow all ladder safety requirements.
- Train employees in safe ladder use.
- Maintain ladders in a safe condition.
- Inspect ladders as needed.
- Remove defective ladders from service.
Training action plan
Training content for ladders and stairways depends on the types of equipment and structures your facility has and what work will be performed. In general, workers need to be trained as follows:
Ladders
Content should include:
- Inspecting the ladder,
- Setting up the ladder,
- Safe ladder use,
- Ascending and descending the ladder,
- Maintaining three points of contact,
- Recognizing hazards,
- Carrying tools and equipment, and
- Using the right ladder for the job.
Tips
- Workers on ladders generally do not require fall protection.
- Be careful that painting ladders or applying stickers does not hide damage.
- Make sure the ladder is the best tool for the job.
- Ensure workers understand associated hazards (e.g., electrical, wind) that they may have to consider with selecting and/or using a ladder.
Checklist
Review these checklists to ensure ladder safety at your facility.
Design and construction
- If wood, is the portable ladder not coated with any material that may obscure structural defects?
- If metal, is the portable ladder made of corrosion-resistant material or protected against corrosion?
- If metal, are the rungs and steps of the portable ladder corrugated, knurled, dimpled, coated with skid-resistant material, or otherwise treated to minimize slipping?
- Are the rungs, steps, and cleats of the portable ladder spaced at least 10 inches and not more than 14 inches apart?
- Do the rungs, steps, and cleats of the portable ladder have a minimum clear width of 11.5 inches?
Stepladders
- Is the stepladder equipped with a metal spreader or locking device that securely holds the front and back sections in an open position while the ladder is in use?
Stepstools
- Are the steps on the stepstool spaced at least 8 inches and not more than 12 inches apart?
- Does the stepstool have a minimum clear width of 10.5 inches?
Inspection and maintenance
- Are portable ladders inspected regularly, and as necessary, to ensure they are in safe condition?
- Are deficiencies corrected or repaired before an employee uses the portable ladder again?
- If a portable ladder correction or repair cannot be made immediately, are employees prevented from using the portable ladder until repaired?
- If a portable ladder repair involves structural integrity, does a qualified person perform or supervise the correction or repair?
Training
- Is each employee who uses a portable ladder trained on how to properly use the ladder?
- Is each employee who uses a portable ladder trained to recognize the fall hazards in the work area?
- Is training conducted by a qualified person?
Note: Qualified, under this OSHA requirement, describes a person who, by possession of a recognized degree, certificate, or professional standing, or who by extensive knowledge, training, and experience has successfully demonstrated the ability to solve or resolve problems relating to the subject matter, the work, or the project. - Is information and training provided in a manner that each employee understands?
- Is retraining provided when deficiencies in performance or knowledge are noted, or there are changes in the workplace or equipment?
Personal protective equipment
OSHA’s Subpart I regulations apply to all persons involved in hazardous processes; environmental, chemical, radiological hazards; or mechanical irritants that are capable of causing injury or impairment of any body part through absorption, inhalation, or physical contact. The categories of personal protective equipment (PPE) include: eye and face equipment, head protection, hand protection, foot protection, fall protection, and respiratory protection (information about respiratory protection is provided in a separate topic area under Respiratory Protection, 1910.134).
Action steps
- Assess the workplace to determine what hazards are present that require PPE.
- Document and certify the PPE assessment.
- Provide appropriate and approved PPE based on the workplace hazards.
- Instruct employees in proper PPE usage.
- Ensure employees wear proper PPE.
- Establish inspection and maintenance procedures for PPE.
Training action plan
OSHA requires that you provide training to each employee who is required to use PPE. Each such employee shall be trained to know at least the following:
- When PPE is necessary.
- What PPE is necessary.
- How to properly don, doff, adjust, and wear PPE.
- The limitations of the PPE.
- The proper care, maintenance, useful life, and disposal of the PPE.
Each affected employee must also demonstrate an understanding of the training and the ability to use PPE properly, before being allowed to perform work requiring the use of PPE.
When you have reason to believe that any affected employee who has already been trained does not have the understanding and skill required, you must retrain each such employee. Circumstances where retraining is required include, but are not limited to, situations where:
- Changes in the workplace render previous training obsolete.
- Changes in the types of PPE to be used render previous training obsolete.
- Inadequacies in an employee’s knowledge or use of assigned PPE indicate that the employee has not retained the requisite understanding or skill.
Tips
- Make sure that protective eyewear does not affect the fit of respirators.
- Make sure that protective eyewear does not disturb the proper positioning of corrective lenses so as to inhibit or limit the employee’s vision.
- Ensure employees disinfect shared protective eyewear after each use.
- Always replace a hard hat if it sustains an impact, even if damage is not noticeable.
- Don’t let workers wear hard hats backward unless the hat has been tested and approved for such use.
Checklist
Review these checklists to ensure proper PPE usage at your facility.
General
- Are all employees required to use PPE as needed?
- Is PPE functional and in good repair?
- Is protective clothing and equipment provided and used when cleaning up spilled toxic or otherwise hazardous materials or liquids?
- Is PPE provided and are all employees required to use PPE as needed to protect against injury?
- Does PPE have ANSI or ASTM specifications marked on it?
Training
- Has each individual who is required to use PPE been provided with training?
- Have the trained individuals demonstrated an understanding of the training and the ability to use PPE properly before being allowed to perform work requiring the use of PPE?
- Are individuals retrained when there is reason to believe that they do not have the understanding or skill to use PPE properly?
Recordkeeping
- Have you documented that a hazard assessment has been done, when, and by whom?
- Have you documented that PPE training has been done, who has received it, and when?
Head, foot, and hand protection
- Are protective helmets used wherever there is the possible danger of head injury from impact, or from falling or flying objects, or from electrical shock and burns?
- Is protective footwear used wherever there is the danger of foot injuries due to falling or rolling objects, or objects piercing the sole, and where feet are exposed to electrical hazards?
- Are appropriate protective gloves used wherever there is the danger to hands of exposure to hazards such as those from skin absorption of harmful substances, severe cuts or lacerations, severe abrasions, punctures, chemical burns, thermal burns, and harmful temperature extremes?
Eye and face protection
- Are individuals issued and required to wear appropriate eye protective devices while participating or observing activities which present a potential eye safety hazard?
Personal fall protection
- Have all impacted individuals been trained to use personal fall protection equipment?
- Is the equipment inspected daily before use?
- Does fall protection meet the design requirements in 1910.140?
- Are ropes, belts, lanyards, lifelines, and harnesses used for personal fall protection compatible with connectors used?
Posting requirements
- Are all areas and equipment requiring the use of PPE devices posted with a sign indicating this requirement?
Process safety management
OSHA’s 1910.119 regulation applies to those companies that deal with any of more than 130 specific toxic and reactive chemicals in listed quantities (See 1910.119 Appendix A); it also includes any Category 1 flammable gas (as defined in 1910.1200(c)) or a flammable liquid with a flashpoint below 100°F (37.8°C) on site in one location, in a quantity of 10,000 pounds (4535.9 kg) or more (with a few exceptions, as outlined in 1910.119(a)(1)(ii)(A) and (B)).
Action steps
- Ensure employee participation in the process safety management program.
- Conduct adequate hazard analyses.Implement safety operating procedures.
- Conduct process safety training.
- Ensure process safety for contractors.
- Conduct pre-startup safety reviews.
- Ensure integrity of process equipment.
- Ensure management of change process and procedures are adequate.
- Investigate incidents per OSHA requirements.
- Ensure emergency planning and response efforts are adequate.
- Establish a process safety compliance audit process.
Training action plan
You must train each employee involved in operating a process and each employee before being involved in operating a newly assigned process. Training must include:
- An overview of the process and the operating procedures.
- Specific safety and health hazards.
- Emergency operations including shutdown.
- Safe work practices applicable to the employee’s job tasks.
Also, you must provide refresher training at least every three years, and more often if necessary, to each employee involved in operating a process to assure that the employee understands and adheres to the current operating procedures of the process. You, in consultation with the employees involved in operating the process, must determine the appropriate frequency of refresher training.
Documentation
You must prepare a record that contains the identity of the employee, the date of training, and the means used to verify that the employee understood the training.
Tips
- OSHA’s Process Safety Management (PSM) standard requires that mechanical integrity inspections have to be documented (including the name of the person performing the inspection or test) and list the information to be recorded.
- The PSM standard states that the employer must establish and implement written procedures.
- To comply with the PSM standard, employers must document that equipment complies with recognized and generally accepted good engineering practices. For existing equipment designed and constructed in accordance with codes, standards, or practices that are no longer in general use, the employer must determine and document that the equipment is designed, maintained, inspected, tested, and operated in a safe manner.
- All process hazard analyses must be updated and revalidated, based on their completion date, at least every five years.
- Employers must consult with employees and their representatives on the conduct and development of process hazard analyses and on the development of the other elements of process management, and they must provide to employees and their representatives access to process hazard analyses and to all other information required to be developed by the standard.
- Contract employees must be instructed on known potential fire, explosion, or toxic release hazards related to their job and the process, and in the applicable provisions of the emergency action plan.
Checklist
Review these process safety management checklists.
Process hazard analysis
- Has written process safety information been compiled before conducting any process hazard analysis (PHA)?
- Are the process hazard analyses performed by teams with expertise in engineering and process operations?
- Has a system been established to promptly address the team’s findings and recommendations?
- Are the PHA’s updated and revalidated to assure that the process hazard analysis is consistent with the current process?
Incident investigation
- Has each incident been investigated which resulted in, or could reasonably have resulted in, a catastrophic release of highly hazardous chemicals in the workplace?Has a system been established to promptly address and resolve the incident investigation report findings and recommendations?
Emergency action plan
- Has an emergency action plan been established and implemented for the entire plant in accordance with the requirements of 1910.38?
Written program
- Do you have an appropriate written program for PSM compliance?
- Do you have a written program regarding employee participation?
- Do written operating procedures exist for each covered process?
- Have safety and health considerations been included in the operating procedures?
Contractors
- Have safe work practices been developed and implemented for employees and contractors to control hazards?
- For employees and contractor employees involved in operating a process do initial and refresher training records exist?
- Has each employee and contractor employee been trained before being involved in a newly assigned process?
Pre-startup safety review
- Has a pre-startup safety review been performed for all new facilities and for modified facilities when the modification is significant enough to require a change in process safety information?
Mechanical integrity
- Are there written procedures to maintain the ongoing integrity of process equipment?
- Are appropriate inspections and tests performed on each item of process equipment included in the program?
- Have appropriate checks and inspections been made to assure equipment is installed properly and consistent with design specifications and manufacturer’s instructions?
Hot work permits
- Have hot work permits been issued for all hot work operations conducted on or near a process covered by the PSM standard?
Management of change
- Are there written procedures for managing changes (except for “replacements in kind”) to process chemicals, technology, equipment, and procedures and changes to facilities that affect a covered process?
Audits
- Do you conduct an audit of compliance with PSM at least every three years?
- Do you retain the two most recent compliance audit reports?
Training
- Have employees been trained properly regarding PSM?
- Are appropriate training records kept?
Signs and markings
OSHA’s 1910.144-.45 regulations provide specifications for signs and tags and are intended to cover all safety signs except those designed for streets, highways, railroads, and marine regulations. These specifications do not apply to plant bulletin boards or to safety posters.
Action steps
- Use appropriate colors for identification of equipment and hazards per OSHA regulations.
- Ensure emergency stop bars and buttons on hazardous machines are red.
- Ensure yellow is used for designating caution and for marking physical hazards such as: Striking against, stumbling, falling, tripping, and “caught in between.”
- Follow OSHA specifications for accident prevention signs and tags.
- Instruct employees in recognizing accident prevention signs and tags and the appropriate action to take regarding those markings.
- Ensure messages on signs and tags are clear and to the point.
Training action plan
Training on accident prevention signs and tags is required prior to or at the time of initial assignment to areas where accident prevention signs and tags are used. Training content should generally include:
- Sign color,
- Symbols,
- Labeling, and
- Company-specific marking systems.
Consider other safety training issues relative to safety signs such as hazard communication and the specific posting requirements of the chemical-specific standards found in Subpart Z of the 1910 regulations. Training might also cover the information found in the poster describing employee rights under OSHA (poster 2203) which must be displayed somewhere where workers will see it.
OSHA does not require training documentation for Specifications for Accident Prevention Signs and Tags, but it is always prudent to keep records anyway. Training records can tell you who was trained on what, when, and what was covered.
Tips
- The lines used to delineate the aisles may be any color so long as they clearly define the area considered as aisle space. The lines may be composed of dots, square, strip or continuous, but they too must define the aisle area.
- The recommended width of aisle markings varies from two inches to six inches; therefore, any width two inches or more is considered acceptable.
- Danger sign — The colors red, black, and white must be those of opaque glossy samples as specified in Table 1 of Fundamental Specification of Safety Colors for CIE Standard Source “C”, American National Standard Z53.1-1967.
- Caution sign — Standard color of the background must be yellow; and the panel, black with yellow letters. Any letters used against the yellow background must be black. The colors must be those of opaque glossy samples as specified in Table 1 of American National Standard Z53.1-1967.
- Safety instruction signs — Standard color of the background must be white; and the panel, green with white letters. Any letters used against the white background must be black. The colors must be those of opaque glossy samples as specified in Table 1 of American National Standard, Z53.1-1967.
Checklist
Review these checklists for signs and markings at your facility.
Hazardous substances
- Is every hazardous chemical in the workplace labeled with identification and hazard warnings?
- Are safety and other containers painted appropriately?
- Are equipment, containers, materials, or areas where biohazards are or could be present labeled with the biological hazard warning?
- Are any entrances to regulated areas where the 13 carcinogens listed at 1910.1003 are present marked with appropriate signage warning of the danger?
- Are signs posted warning of presence and hazards of asbestos where required?
Aisles
- Are permanent aisles and passageways appropriately marked?
Materials handling
- Are clearance signs warning of clearance limits provided?
- Are powered industrial trucks appropriately marked?
- Are cranes marked with the load rating on each side?
- Are crane pendant control boxes clearly marked for identification of functions?
Emergency
- Are exits marked by a readily visible sign?
- Are areas that could be mistaken for an exit identified by a sign reading “Not an Exit” or something similar?
- Are portable fire extinguishers mounted, located, and identified so they are readily accessible?
Ladders
- Are defective ladders withdrawn from service and tagged or marked as “Dangerous, Do Not Use”?
Lockout/tagout
- Do tagout devices warn against hazardous conditions if the machine or equipment is energized?
Confined spaces
- Are completed confined space permits posted at an appropriate location?
- Are signs posted at permit-required confined spaces describing the dangers present?
OSHA posters
- Is OSHA’s Form 2203 (or 3165) describing the OSH Act posted appropriately?
- Is the annual summary of OSHA No. 300 Form posted appropriately?
- Are citations received from OSHA posted at or near the place the violation(s) occurred?
Electrical
- Is the manufacturer’s description marked on all electrical equipment used?
- Are covers for pull and junction boxes permanently marked “HIGH VOLTAGE”?
Slips, trips, and falls
OSHA has various requirements to protect workers from slipping, tripping, or falling. These requirements are in Subpart D. Among other things, OSHA requires that all floors, platforms, runways, and wall and window openings where there is a drop of four feet or more have some type of guarding, or that workers utilize an appropriate personal fall arrest system.
Action steps
- Keep all places of employment, passageways, storerooms, and service rooms clean and orderly and in a sanitary condition.
- Ensure floors are maintained in a clean and, so far as possible, a dry condition.
- Maintain drainage where wet processes are used.
- Ensure every floor, working place, and passageway are kept free from protruding nails, splinters, holes, or loose boards.
- Provide sufficient safe clearances for aisles, at loading docks, through doorways and wherever mechanical handling equipment turns or passage must be made.
- Ensure permanent aisles and passageways are appropriately marked.
- Provide covers and/or guardrails to protect personnel from the hazards of open pits, tanks, vats, ditches, etc.
- Ensure ladders are maintained and used properly.
- Follow proper safety procedures for scaffold setup and use.
- Ensure all walking-working surfaces are maintained safely.
Training action plan
Before any employee is exposed to a fall hazard, OSHA requires that the employer must provide training for each employee who uses personal fall protection systems, as well as employees using certain equipment such as ladders, rope descent systems, and dockboards.
The employer must ensure that each employee is trained by a qualified person.
Training for impacted employees must cover pertinent topics, including:
- How to use, inspect, maintain, and disassemble a personal fall protection system,
- How to properly place dockboards, and
- Designated area set-up.
OSHA requires employees be retrained when there is reason to believe the employee does not have the understanding and skill required to work safely. Situations requiring retraining include, but are not limited to, the following:
- When changes in the workplace render previous training obsolete or inadequate;
- When changes in the types of fall protection systems or equipment to be used render previous training obsolete or inadequate; or
- When inadequacies in an affected employee’s knowledge or use of fall protection systems or equipment indicate that the employee no longer has the requisite understanding or skill necessary to use equipment or perform the job safely.
Training must be provided in a manner that the employee understands.
All employees should be aware of how to prevent slips, trips, and falls by following good housekeeping procedures and when they work on or around:
- Scaffolds,
- Ladders,
- Unprotected ledges or platforms,
- Rooftops,
- Open shafts,
- Trapdoors,
- Poles,
- Towers,
- Bridges,
- Trestles,
- Pits, and
- Open tanks.
Training content should generally focus on:
- Various “fall factors” present in your facility.
- What happens when you slip, trip, and fall.
- How to prevent injuries from slips, trips, and falls, including the use of appropriate footwear.
- Hazards of stairs.
- Fall prevention methods when using ladders and scaffolds.
Tips
- Assign responsibilities for ensuring areas are kept clean and orderly.
- Keep an eye out for uneven floors, labels and cords, wet processes, and low-light areas.
Checklist
Review these checklists to reduce slips, trips, and falls at your facility.
Walkways
- Are aisles and passageways kept clear?
- Are aisles and walkways marked as appropriate?
- Are wet surfaces covered with non-slip materials?
- Are holes in the floor, sidewalk, or other walking surface repaired properly, covered, or otherwise made safe?
- Is there safe clearance for walking in aisles where motorized or mechanical handling equipment is operating?
- Are materials or equipment stored in such a way that sharp projectiles will not interfere with the walkway?
- Are spilled materials cleaned up immediately?
- Are changes of direction or elevations readily identifiable?
- Are aisles or walkways that pass near moving or operating machinery, welding operations or similar operations arranged so employees will not be subjected to potential hazards?
- Are standard guardrails provided wherever aisle or walkway surfaces are elevated more than 30 inches (76.20 centimeters) above any adjacent floor or the ground?
Floor and wall openings
- Are floor openings guarded by a cover, a guardrail, or equivalent on all sides (except at entrance to stairways or ladders)?
- Are toeboards installed around the edges of permanent floor opening (where persons may pass below the opening)?
Dockboards
- Are all dockboards used capable of supporting the maximum intended load?
- Do dockboards that are put into initial service on or after January 17, 2017, have means (such as run-off guards or curbs) to prevent vehicles from running off the edge (unless it can be demonstrated there is no run-off hazard))?
- Are portable dockboards equipped with handholds or other means to permit safe handling?
- Are portable dockboards secured by anchoring in place or using equipment or devices that prevent the dockboard from moving out of a safe position?
- When securing the dockboard is not feasible, is there sufficient contact between the dockboard and the surface to prevent the dockboard from moving out of a safe position?
- Are measures, such as wheel chocks or sand shoes, used to prevent transport vehicles (e.g. a truck, semitrailer, trailer, or rail car) from moving while employees are on the dockboard?
- Is each employee on a dockboard protected from falling 4 feet or more to a lower level by a guardrail system or handrails?
Note: This does not apply when dockboards are being used solely for materials-handling with motorized equipment, the fall hazard is 10 feet or less, and the employees have been properly trained. - Are dockboards inspected regularly, and as necessary, to ensure they are in safe condition?
- Is each employee who uses a dockboard trained to properly place and secure the equipment?
Stairs and stairways
- Are standard stair rails or handrails on all stairways having four or more risers?
- Are all stairways at least 22 inches (55.88 centimeters) wide?
- Are step risers on stairs uniform from top to bottom?
- Are steps on stairs and stairways designed or provided with a surface that renders them slip resistant?
- Are stairway landings adequate?
Inspection and maintenance
- Are aisles and walkways inspected regularly, and as necessary, to ensure they are in safe condition?
- Are deficiencies corrected or repaired before an employee uses an aisle or walkway again?
- If an aisle or walkway correction or repair cannot be made immediately, are employees prevented from using the aisles or walkway until repaired?
- If an aisle or walkway repair involves structural integrity, does a qualified person perform or supervise the correction or repair?
Training
- Are employees trained in measures to protect themselves from slips, trips, and falls?
- Are employees trained to use any fall protection they may need?
- Is training provided in a manner the employees will understand?
Solvents
Solvents are commonly used both in the workplace and at home. They are safe to use when you understand their hazards and know how to protect yourself. Solvents can:
- Cause dizziness, nausea, and depress the central nervous system;
- Cause chronic illnesses such as cancer, liver disease, and nervous system disorders;
- Be toxic; and
- Be flammable.
One thing all solvents have in common is that they are used to dissolve another substance. They can be used as cleaners, degreasers, or as ingredients in paints, coatings, or adhesives. Some examples of common solvents include acetone, alcohol, mineral spirits, and perchloroethylene.
Action steps
- Assess the workplace to determine if solvents are being used, where, and in what processes/procedures.
- Ensure that there is an SDS for each hazardous solvent used in your facility.
- Properly store solvents.
- Ensure that waste and solvent by-products are properly contained and disposed.
- Determine which employees have on-the-job exposure.
- Provide appropriate protective equipment.
- Train affected employees to properly wear the PPE.
- Train affected employees about solvent hazards according to the requirements of the Hazard Communication standard at 1910.1200.
Note: OSHA regulations do not deal with specific solvents; however, some exceptions apply, depending on the chemical used, the potential for exposure, and the degree of exposure.
For more information, see the following regulations:
- Benzene, 1910.1028.
- Spray finishing, 1910.107.
- Dip tanks, 1910.122 through 1910.126.
- Solvents used in a process, 1910.119.
- Flammable liquids, 1910.106 (includes storage and handling requirements).
- HAZWOPER, 1910.120 (responding to spills and leaks).
Training action plan
Under the requirements of OSHA’s hazard communication standard, affected employees have to be given information and training on the hazards of the solvents they are exposed to at the time of their initial assignment, and whenever a new hazard is introduced into their work area.
Hazard communication
Hazard communication training has to include:
- Understanding the requirements of the OSHA hazard communication standard.
- Understanding the various components of your company’s hazard communication program.
- Knowing where the information is located in the company and how to access it.
- Knowing which operations and processes are using hazardous chemicals.
- Ability to read and understand the information on SDSs and labels.
- Knowing how to follow safe work practices and use PPE.
Solvents
Training content for an effective solvent training program should include:
- Identification of common solvents used in the workplace,
- How to recognize solvents,
- The chemistry of solvents,
- Physical and health hazards,
- Engineering controls used to reduce exposures,
- Use of protective equipment,
- Safe work procedures,
- Storage procedures,
- Clean-up and disposal procedures, and
- First aid and emergency procedures.
Tips
- Solvents are used to dissolve another substance. In general, “like dissolves like,” so the chemical composition of the solvent needs to have something in common with the chemical composition of the substance it can dissolve.
- Many solvents are combustible or flammable liquids. This means that they can easily ignite and burn. Acetone and methanol are examples of flammable solvents. Many types of petroleum distillates have a higher flash point and are considered combustible liquids.
- When engineering controls cannot completely eliminate the risk of exposure to solvents, affected employees will need to wear PPE. Chemical splash goggles, face shields, gloves, coveralls, aprons, shoe covers, and respirators are all examples of protective equipment. Refer to the product’s safety data sheet for PPE recommendations.
- Use only the amount of solvent needed for the job. This will minimize exposure and the quantity of waste solvent to be disposed.
- Store solvents in their original containers and be sure all containers in storage are clearly labeled.
Checklist
Review this solvent checklist to ensure safety and compliance at your facility.
- Have all solvents in the workplace been identified and documented?
- Are engineering controls in place to reduce exposures?
- Are hazardous solvents replaced with non-toxic solvents where possible?
- Are job activities controlled to prevent airborne solvent vapors from being generated and released into workers’ breathing area?
- Are workers free from medical complaints or symptoms that could be associated with solvent use?
- In areas where individual exposures are suspected to be above acceptable limits, has air monitoring been performed?
- Are affected persons provided with written copies of air monitoring results?
- Are workers who are exposed to solvent vapors above the permissible exposure limits provided with appropriate personal protective equipment (such as respirators) on an interim basis until engineering or administrative controls reduce exposures below permissible exposure limits?
- Are appropriate personal hygiene practices enforced such as washing hands?
- Is appropriate personal protective equipment (PPE) provided such as gloves, aprons, and goggles to protect against exposure?
- Have workers been trained regarding the hazards of solvents to which they might be exposed?
- Are first aid procedures in place for overexposures?
- Are there emergency procedures in case of a spill or leak?
Standard stairways
Stairways are a common fixture in many workplaces. However, they can pose hazards to workers if not constructed and maintained properly.
Action steps
- Ensure stairs meet OSHA’s specifications (strength, width, rise, etc.). See 29 CFR 1910.25 and 29 CFR 1910.28.
- Equip all stairways that are four feet or more above a lower surface with stair rail systems and guardrails.
- Ensure stairs have uniform riser heights and tread depths between landings.
- Provide proper landing platforms.Inspect all stairways regularly and as necessary.
- Maintain stairways in a safe condition.
Training action plan
Before any employee is exposed to a fall hazard, OSHA requires that the employer must provide training for that employee. In terms of stairs, items to keep in mind include:
- Caution employees not to carry large or bulky objects while climbing or descending stairs.
- Encourage employees to use railings.
- Remind employees not to jump from stairs, or skip steps.
Training must be provided in a manner that the employee understands.
Tips
- Provide stairs with good lighting and tread.
- Provide signage to remind employees of safe stair practices.
- Ensure the change in surface from stairs to platforms does not create a hazard.
- Keep stairs dry.
- Periodically inspect stairways for damage.
Checklist
Review the following standard stairway checklists.
General
- Are standard stairs provided for access from one walking-working surface to another when operations necessitate regular and routine travel between levels?
Condition
- Are stairs in good repair (e.g., loose handrails, corrosion)?
- Are stairs free of hazards (e.g., protruding objects, leaks, spills, snow and ice)?
- Are all steps reasonably slip-resistant?
Design and construction
- Are stairs at least 22 inches wide between vertical barriers?
- Are handrails, stair rail systems, or guardrails provided as necessary?
- Do stairways have at least a 6 feet, 8 inches vertical clearance from any tread to any overhead clearance measured from the leading edge of the tread?
- Can stairs support a load of five times the normal anticipated live load, but not less than 1,000 pounds?
Steps
- Do stairs have uniform riser heights and tread depths?
- Do the stairs have an angle between 30 and 50 degrees from the horizontal?
- Do stairs meet the rise and tread dimensions specified in Table D-1 of 1910.25(c) that achieve an angle between 30 and 50 degrees from the horizontal if installed before January 17, 2017?
- Do stairs have a maximum riser height of 9.5 inches if installed after January 17, 2017?
- Do stairs have a minimum tread depth of 9.5 inches if installed after January 17, 2017?
Fall protection
- Is a stair rail system and handrail(s) present on flights of stairs having at least 3 treads and at least 4 risers?
- Is at least one handrail present if the stairway is enclosed on both sides and is less than 44 inches wide?
- Are handrails present on both sides if the stairway is enclosed on both sides and is more than 44 inches wide but less than 88 inches wide?
- Are handrails present on each side and in the middle of the stair if it is enclosed on both sides and is more than 88 inches wide?
- Is a stair rail system with a handrail present on the open side of the stairway if it is less than 44 inches wide?
- Is a stair rail system with a handrail present on the open side of the stairway and a handrail on the enclosed side if it is more than 44 inches wide but less than 88 inches wide?
- Is a stair rail system with a handrail present on the open side, one handrail on the enclosed side, and one intermediate handrail located in the middle of the stair if it is greater than 88 inches wide?
- Is a stair rail system with a handrail present on each open side of the stairway if it is less than 44 inches wide?
- Is a stair rail system with a handrail present on the each open side of the stairway if it is more than 44 inches wide but less than 88 inches wide?
- Is a stair rail system with a handrail present on each open side and one intermediate handrail located in the middle of the stair if it is greater than 88 inches wide?
- Is a handrail on at least one side with earth built up on both sides present on exterior stairs less than 44 inches wide?
Handrails
- Is the height of handrails 30-38 inches measured from the leading edge of the stair tread to the top surface of the handrail?
- Is the clearance between handrails and any other object at least 2.25 inches?
- Are handrails smooth-surfaced?
- Do handrails have the shape and dimension necessary so that employees can grasp the handrail firmly?
- Do the ends of handrails not present projection hazards?
- Are handrails capable of withstanding, without failure, a force of at least 200 pounds applied in any downward or outward direction within 2 inches of any point along the top edge of the rail?
Stair rail systems
- Is the height of stair rail systems not less than 30 inches from the leading edge of the stair tread to the top surface of the top rail if installed before January 17, 2017?
- Is the height of stair rail systems not less than 42 inches from the leading edge of the stair tread to the top surface of the top rail if installed on or after January 17, 2017?
- Do the opening in stair rail systems not exceed 19 inches at its least dimension?
- If used as a handrail on stairs installed before January 17, 2017, is the height of stair rail systems 36-38 inches measured at the leading edge of the stair tread to the top surface of the top rail?
- If used as handrails, is the clearance between the stair rail systems and any other object at least 2.25 inches?
- Are stair rail systems smooth-surfaced?
- If used as a handrail, do stair rail systems have the shape and dimension necessary so that employees can grasp it firmly?
- Do the ends of stair rail systems not present projection hazards?
- Are stair rail systems capable of withstanding, without failure, a force of at least 200 pounds applied in any downward or outward direction within 2 inches of any point along the top edge of the rail?
Landings and platforms
- Is a platform provided when a door or gate opens directly onto a stairway?
- Is a guardrail or stair rail system provided if the landing is 4 feet or more above the lower level?
- Does the swing of the door or gate not reduce the platform’s usable depth to less than 20 inches if installed before January 17, 2017?
- Does the swing of the door or gate not reduce the platform’s usable depth to less than 22 inches if installed on or after January 17, 2017?
- Is the stairway landing or platform at least as wide as the stairway?
- Is the stairway landing or platform at least 30 inches in depth measured in the direction of travel?
Inspection and maintenance
- Are stairways inspected regularly, and as necessary, to ensure they are in safe condition?
- Are deficiencies corrected or repaired before an employee uses a stairway again?
- If a stairway correction or repair cannot be made immediately, are employees prevented from using the stairway until repaired?
- If a stairway repair involves structural integrity, does a qualified person perform or supervise the correction or repair?
Storage racks
Storage racks are a common fixture in many industrial workplaces, from warehouses to manufacturing facilities to retail to automotive repair shops. Common though they may be, these facilities can pose significant hazards if not installed, used, and maintained properly. Although OSHA does not have a specific standard addressing storage racks, the Agency expects employers to provide safe racking and has cited employers under the General Duty Clause of the OSH Act when racking posed serious hazards to workers.
Action steps
- Ensure all racks meet appropriate industry standards (e.g., ANSI/RMI MH 16.1).
- Install, use, and maintain racks per the manufacturer’s instructions.
- Check that load ratings are present.
- Ensure racks are anchored properly.
- Train workers on racking safety, including capacities and storage techniques.
- Install racks in accordance with local fire and building codes.
- Install bumper guards to prevent rack damage.
- Ensure repairs are made by qualified personnel.
- Replace damaged racks immediately or remove them from service.
Training action plan
- Explain the types of racking in your facility.
- Demonstrate proper stacking technique, including height restrictions.
- Ensure only trained material handling personnel place items on racking with powered equipment.
- Remind workers not to climb on racking (in rare cases where this may be needed, ensure the use of proper fall protection).
- Train workers how to read racking capacity plates.
- Instruct workers on how to report damaged racking.
Tips
- Assign responsibility for inspecting racks.
- Ensure racking repairs are made properly according to manufacturer’s instructions, and by qualified personnel, particularly where welding is performed.
- Maintain at least 18 inches clearance from sprinklers. (Local fire codes may have additional requirements for sprinklers and racking.)
- Conduct thorough root-cause analysis for racking damage.
Checklist
Review these storage rack checklists.
Design
- Have industrial steel storage racks been designed in accordance with American National Standards Institute (ANSI)/Rack Manufacturers Institute, Inc. (RMI) standard MH 16.1 specifications?
- Are modifications or rearrangements not within the original design not present? ANSI/RMI
- Are load application and rack configuration drawings available for each rack installation? ANSI/RMI
Installation
- Are racks installed on flooring (i.e., concrete) that will support the associated loads?
- ANSI/RMIIs flooring in good repair under and around racks?
- Are shims made of materials that meet or exceed the design bearing strength or allowable bearing strength of the floor? ANSI/RMI
- Is shim size and location under the base plates equal to or greater than the required base plate size and location? ANSI/RMI
- Does the total thickness of shims not exceed six times the diameter of the largest anchor bolt used in that base? ANSI/RMI
- Are shims interlocked or welded together if the total thickness is less than or equal to six times the anchor bolt diameter under bases with less than two anchor bolts? ANSI/RMI
Placarding
- Do storage racks display a permanent plaque that indicates load capacity? ANSI/RMI & General Duty Clause
- Is the plaque conspicuously located? ANSI/RMI
- Is the plaque at least 50 square inches? ANSI/RMI
- Does the plaque show clear, legible print? ANSI/RMI
- Does the plaque display the maximum permissible unit load and/or maximum uniformly distributed load per level? ANSI/RMI
- Does the plaque display the average unit load? ANSI/RMI
- Does the plaque display the maximum total load per bay? ANSI/RMI
- Are storage levels having multiple stacking of unit loads identified? ANSI/RMI
Anchoring
- Are rack columns anchored to the floor? ANSI/RMI & General Duty Clause
- Are an appropriate number of anchors, as recommended by the rack manufacturer, used? ANSI/RMI
- Are the anchors used the correct size as recommended by the rack manufacturer? ANSI/RMI
- Are an appropriate number of anchor bolts, as recommended by the rack manufacturer, used? ANSI/RMI
- Are the anchor bolts used the correct size as recommended by the rack manufacturer? ANSI/RMI
- Is decking fastened to the beams to prevent deck dropping? ANSI/RMI
Condition
- Are racks inspected and maintained per the manufacturer’s guidelines?
- Are racks plumb from top to bottom? ANSI/RMI
- Are rack columns straight? ANSI/RMI
- Are rack columns in good repair? ANSI/RMI
- Has frame bracing been installed as recommended by the manufacturer? ANSI/RMI
- Is frame bracing in good repair? ANSI/RMI
- Are anchors in good repair? ANSI/RMI
- Are column base plates in good repair? ANSI/RMI
- Are deflectors, fenders, and bumpers protecting the column as necessary? ANSI/RMI
- Is decking in good repair? ANSI/RMI
- Are other rack components (e.g., deflector angles, backer posts, etc.) in good repair? ANSI/RMI
Loads
- Is the weight of materials stored on storage racks below the load capacity rating? ANSI/RMI
- Are the heaviest products stored on the floor or lower levels and toward the middle of the rack system? ANSI/RMI
- Are pallets in good repair? ANSI/RMI
- Are pallets placed onto pallet load support members in a properly stacked and stable position? ANSI/RMI
- Are boxes, pallets, bags, containers, and other materials stacked/piled neatly? ANSI/RMI & 1910.176(b)
- Are stacks secure against sliding or collapse? 1910.176(b)
- Are stacks limited in height? 1910.176(b)
Fire protection and prevention
- Are racks, and materials stored on them, in accordance with local fire codes?
- Are materials on racks stored no closer than 18 inches away from sprinklers? 1910.159(c)(10)
Recordkeeping
- Has one copy of load application and rack configuration drawings of storage racks used been retained? ANSI/RMI
- Has one copy of load application and rack configuration drawings of storage racks used been retained by the dealer or manufacturer? ANSI/RMI
Welding
OSHA’s Subpart O regulations apply to all welders and welding operators who operate electric or gas welding and cutting equipment. The standards apply whether you have a single portable welding unit to do an occasional spot welding task, or if you have large electric welders to use in daily production.
Action steps
- Follow safety precautions for fire prevention and protection.
- Maintain suitable fire extinguishers.
- Provide a fire watch where required.
- Ensure areas are inspected and a permit issued before welding is allowed.
- Follow proper welding procedures.
- Provide PPE as needed.
- Ensure safety when working in confined spaces.
- Handle welding materials and equipment properly.
- Ensure proper marking of welding materials and equipment.
- Provide suitable ventilation.
- Maintain welding equipment.
Training action plan
Cutters, welders, and their supervisors are required to be trained in the safe operation of welding equipment. Also, fire watchers shall be trained in the use of fire extinguishing equipment. Training content should generally cover:
- Welding safety program guidelines established at your company,
- Welding hazards,
- Safe work practices,
- Fire watches,
- Welding safety when working in confined spaces, and
- Housekeeping.
Consider other safety training issues relative to your welding operations:
- Hazard communication for all hazardous substances generated during welding (e.g., certain gases, fluxes, wires, and rods contain cadmium, fluorides, zinc, beryllium, and so on, and require various protections).
- Spill cleanup procedures under HAZWOPER for leaky oxy fuel type cylinders or for situations with explosion or fire potential.
- Personal protective equipment, especially where respirators are required and eye shades are needed for arc welding operations.
- Employees must be informed of the status of their exposure records each year.
- Construction regulation requirements where welding operations involve new structures or modification of existing structures.
- Electrical codes for exposed live parts.
Training is required prior to or at the time of initial assignment.
Documentation
OSHA does not require training documentation for safety training on welding, but it is always prudent to keep records anyway. Training records can tell you who was trained on what, when, and who conducted the training.
Tips
- Adverse effects of overexposure to welding fumes can be acute or may occur only after repeated exposures.
- The hazards presented by welding fumes will vary based upon: the base material, the filler material, the gases being used, current level, arc length, and other factors.
- Welding fumes can cause nausea, headaches, dizziness, and metal fume fever.
Checklists
Follow these checklists to ensure welding safety at your facility.
General
- Are only authorized and trained personnel permitted to use welding, cutting, or brazing equipment?
- Are pressure-reducing regulators used only for the gas and pressures for which they are intended?
- Does each operator have a copy of the appropriate operating instructions and are they directed to follow them?
- Is a check made for adequate ventilation in and where welding or cutting is performed?
- Is red used to identify acetylene (and other fuel-gas) hose, green for oxygen hose, and black for inert gas and air hose?
- When working in confined places, are environmental monitoring tests taken and means provided for quick removal of welders in case of an emergency?
- Are compressed gases used and handled properly?
Welding: Equipment
- Are only approved apparatus (torches, regulators, pressure-reducing valves, acetylene generators, manifolds) used?
- Is grounding of the welding machine frame and safety ground connections of portable machines checked periodically?
- Is necessary personal protective equipment available?
- Is open circuit (No Load) voltage of arc welding and cutting machines as low as possible and not in excess of the recommended limits?
Welding: Fire prevention
- Are compressed gas cylinders kept away from sources of heat?
- Are fire watchers assigned when welding or cutting is performed in locations where a serious fire might develop?
- Are precautions taken to prevent the mixture of air or oxygen with flammable gases, except at a burner or in a standard torch?
- Are provisions made for personnel to perform fire watch duties under appropriate circumstances?
- Are provisions made to never crack a fuel-gas cylinder valve near sources of ignition?
- Are signs reading “DANGER NO SMOKING, MATCHES, OR OPEN LIGHTS” or the equivalent, posted in welding areas?
- Before hot work is begun, are used drums, barrels, tanks, and other containers so thoroughly cleaned that no substances remain that could explode, ignite, or produce toxic vapors?
- If welding gases are stored, are oxygen and acetylene separated by a 5-foot noncombustible barrier?
- Is combustible scrap, debris, and waste stored safely and removed from the work site promptly?
- When welding is done on metal walls, are precautions taken to protect combustibles on the other side?
Identifying Mechanical Hazards
What are mechanical hazards?
Power-driven equipment and machines pose many hazards to employees, particularly when used improperly or without adequate safeguards. Workers are at risk of lacerations, amputations, severed fingers, and blindness. If equipment is not properly grounded, a metal framework could become energized and possibly electrocute an employee. When driving a forklift in an unsafe manner, the operator runs the risk of tipping the vehicle or striking a pedestrian.
As a safety professional, you must know and understand the hazards posed by power-driven tools, equipment, and machines in your company. Employees using the equipment have to be adequately trained, not only in how to use it properly, but also must be made aware of the consequences of taking short-cuts, disabling or removing guards, and not following standard policies and procedures such as locking out equipment prior to maintenance or repairs.
Many OSHA standards have specific requirements for protecting employees from mechanical hazards. In this section, you will find action steps, tips, answers to frequently asked questions, checklists, and training exercises and handouts on a variety of topics related to mechanical hazards. All of these will help you ensure a safer workplace for those employees who work with powered tools, machines, and equipment.
Cranes
If you use industrial cranes or derricks in your workplace, then the regulations at 1910.179 through .181 apply. Among other things, these regulations require that only designated personnel must operate the equipment, and only authorized representatives should perform equipment repairs.
Action steps
- Use only ANSI approved cranes.
- Test new or altered cranes to ensure compliance with OSHA regulations.
- Ensure any modifications are checked thoroughly by a qualified engineer or the equipment manufacturer.
- Ensure the rated load of the crane is plainly marked on each side of the crane and on each hoisting unit if there is more than one hoisting unit.
- Maintain clearances as required by OSHA.
- Allow only designated personnel to operate a crane.
- Ensure equipment is adequate.
- Provide footwalks, ladders, and stairways as required.
- Install stops, bumpers, rail sweeps, and guards where needed.
- Make sure brakes are adequate.
- Ensure electric equipment complies with OSHA requirements.
- Inspect equipment and remove or repair any defective equipment.
- Maintain equipment.
- Follow manufacturer’s operating instructions.
Training action plans
Only designated personnel are permitted to operate a crane. These employees should receive adequate training to operate the equipment. This includes:
- Understanding the crane’s load-limit
- Lifting loads properly
- Positioning the hook
Training is to be provided prior to or at the time of initial assignment. No specific training documentation is required.
Tips
Tips for crane inspection include:
- Review the crane manufacturer’s inspection and maintenance requirements.
- While the engine is running, check all gauges and warning lights for proper readings and operate all controls to see that they are functioning properly.
- Check for any broken or cracked glass that may affect the view of the operator.
- Look at crane cab for properly marked controls, damaged instruments and for properly displayed and legible load charts.
- Inspect for excessive wear on drive sprockets and/or chain stretch.
- Check crane set up and stability of outriggers on hydraulics and/or the effectiveness of cribbing on crawlers.
- If possible, request that the crane be rotated to check all clearances and overall stability.
- Do not leave crane controls when the engine is running or when the platform is occupied.
- Stop all hoisting operations if there are any indications of danger, including weather conditions.
- Do not make any lifts on another load line of a crane or derrick that is being used to hoist personnel.
Checklist
Use these checklists to make sure your crane inspections keep everyone safe and compliant.
Daily visual inspection
- Is the crane visually inspected every day prior to use?
- Does visual inspection include checking for adjustment problems that may interfere with proper operation?
- Do you also check for deterioration or leakage in lines, tanks, valves, drain pumps, and other parts of air or hydraulic systems?
- Do you look for signs of wear, twist, cracks, distorted links, or excessive stretch in hooks, hoist chains, and end connections?
Frequent inspections (daily to monthly)
- Are “frequent” inspections (must include all of the adjustment and deterioration items under the daily inspection) performed as required?
- Do you also check for operating mechanisms with excessive component wear?
- Do you check for rope reeving that is not in compliance with manufacturer’s recommendations?
Periodic inspections (every 1-12 months)
- Are “periodic” inspections (must include all items under “frequent” inspection) performed as required?
- Are there no deformed, cracked, or corroded members?
- Do you make sure there are no loose bolts or rivets?
- Do you check for cracked or worn sheaves and drums?
- Are there no worn, cracked, or distorted parts such as pins, bearings, shafts, gears, rollers, locking and clamping devices?
- Do you check for excessive wear on brake system parts, linings, pawls, and ratchets?
- Do you make sure there are no inaccuracies in load, wind, and other indicators over their full range?
- Is the machine’s engine or motor performing properly?
- Are chain drive sprockets free of excessive wear and chain stretch?
- Do you look for signs of pitting or deterioration of electrical controller contacts, limit switches, and pushbutton stations?
Inspection documentation
- Are monthly, frequent, and periodic inspections documented?
- Does documentation of inspection include the signature of the person conducting the inspection?
- Does documentation also include the date of the inspection and an identification of the parts inspected?
Monthly rope inspections
- Are running ropes checked at least monthly?
- Are ropes that have been idle for a month or more due to shutdown of crane given a thorough inspection before use?
Dockboards
A dockboard is a portable or fixed device that spans a gap or compensates for a difference in elevation between a loading platform and a transport vehicle. Dockboards include, but are not limited to, bridge plates, dock plates, and dock levelers.
Action steps
- Ensure that dockboards can support the maximum intended load.
- Ensure that transfer vehicles cannot run-off the edge of the dockboard, unless they can prove there is no run-off hazard.
- Secure portable dockboards from moving while being used by employees.
- Ensure that portable dockboards have handholds or another means for safe transport.
- Prevent the accidental movement of transport vehicles while it is being used by employees.
Training action plans
Training must consist of a combination of formal instruction (e.g., lecture, discussion, interactive computer learning, DVD, written material), practical training (demonstrations performed by the trainer and practical exercises performed by the trainee), and evaluation of the operator’s performance in the workplace.
Training should cover the following topics:
- When and what type of dockboard to use
- Placement (using handholds)
- Capacity
- Inspection
- Placement check
- Securing the dockboard
- Communication with transport vehicle driver
- Periodically checking the dockboard during loading/unloading
Tips
- Make certain portable dockboards have a means for safe handling. OSHA suggests handholds or other means of gripping the dockboard. When portable dockboards will be moved mechanically, OSHA suggests the use of forklift loops, lugs, or other effective means.
- Use wheel chocks to prevent the transport vehicle from moving during loading.
- Train employees on recognizing the type of dockboard to use.
Checklist
Use these checklists to ensure dockboards are being used correctly.
Design and construction
- Are all dockboards used capable of supporting the maximum intended load?
- Do dockboards that are put into initial service on or after January 17, 2017, have means (such as run-off guards or curbs) to prevent vehicles from running off the edge (unless it can be demonstrated there is no run-off hazard)?
- Are portable dockboards equipped with handholds or other means to permit safe handling?
Use
- Are portable dockboards secured by anchoring in place or using equipment or devices that prevent the dockboard from moving out of a safe position?
- When securing the dockboard is not feasible, is there sufficient contact between the dockboard and the surface to prevent the dockboard from moving out of a safe position?
- Are measures, such as wheel chocks or sand shoes, used to prevent transport vehicles (e.g., a truck, semitrailer, trailer, or rail car) from moving while employees are on the dockboard?
Fall protection
- Is each employee on a dockboard protected from falling 4 feet or more to a lower level by a guardrail system or handrails? Note: This does not apply when dockboards are being used solely for materials-handling with motorized equipment, the fall hazard is 10 feet or less, and the employees have been properly trained.
Inspection and maintenance
- Are dockboards inspected regularly, and as necessary, to ensure they are in safe condition?
- Are deficiencies corrected or repaired before an employee uses the dockboard again?
- If a dockboard correction or repair cannot be made immediately, are employees prevented from using the dockboard until repaired?
- If a dockboard repair involves structural integrity, does a qualified person perform or supervise the correction or repair?
Training
- Is each employee who uses a dockboard trained to properly place and secure the equipment?
- Is each employee who uses a dockboard trained to recognize the fall hazards in the work area?
- Is training conducted by a qualified person?
Note: Qualified describes a person who, by possession of a recognized degree, certificate, or professional standing, or who by extensive knowledge, training, and experience has successfully demonstrated the ability to solve or resolve problems relating to the subject matter, the work, or the project. - Is information and training provided in a manner that each employee understands?
- Is retraining provided when deficiencies in performance or knowledge are noted, or there are changes in the workplace or equipment?
Electrical safety
OSHA’s electrical safety regulation 1910, Subpart S, is divided into two parts: Installation of Electrical Systems and Safety-Related Work Practices. 1910.399 provides important definitions for both parts. The first section Installation of Electrical Systems, 1910.302 to .308, for the most part, covers installation of electrical equipment. Its use is very similar to the National Electrical Code: electrical equipment installation. However, there are some sections of the installation requirements that do cover electrical safety. The primary example is providing appropriate working space for equipment likely to require examination, adjustment, servicing, or maintenance while energized. That “working space” is generally “built-in” when electrical equipment is installed. The requirements for ground-fault circuit interrupters are another example. The second section, Safety-Related Work Practices, 1910.331 to .335, provides requirements for electrical training, selecting appropriate work practices, lockout/tagout, and working on exposed energized parts.
The first priority in electrical work is locking out and tagging the equipment rendering it “electrically safe.” If that is not possible, then employers must ensure employees are protected against electrical hazards through safe work practices and appropriate PPE. The OSHA regulations do provide shock protection methods in 1910.137—Electrical protective devices. However, the OSHA rules do not provide for arc flash/blast protection. To protect employees from those hazards, employers must refer to an outside source such as the National Fire Protection Association’s NFPA 70E—Standard for Electrical Safety in the Workplace.
Action steps
- Ensure electrical equipment is approved and free from recognized hazards.
- Use listed or labeled equipment according to the instructions included in the listing or labeling.
- Ensure lockout/tagout procedures are provided and used when employees work on electrical components/systems.
- Determine that appropriate space is provided for electrical equipment that will likely require examination, adjustment, servicing, or maintenance while energized.
- Provide appropriate electrical personal protective equipment, insulated hand tools, and meters to protect employees from shock and arc flash/blast hazards when they must work on energized components/systems.
Training action plan
OSHA’s training requirements regarding electrical work apply to employees who face a risk of electric shock that is not reduced to a safe level by the electrical installation requirements of 1910.303 through 1910.308.
Content of training
Employees must be trained in and familiar with the safety-related work practices required by 1910.331 through 1910.335 that pertain to their respective job assignments. Unqualified persons must be trained in and familiar with any electrically-related practices necessary for their safety. Qualified persons (i.e., those permitted to work on or near exposed energized parts) must, at a minimum, be trained in and familiar with the following:
- The skills and techniques necessary to distinguish exposed live parts from other parts of electric equipment.
- The skills and techniques necessary to determine the nominal voltage of exposed live parts.
- The clearance distances specified in 1910.333(c) and the corresponding voltages to which the qualified person will be exposed.
Qualified employees whose work involves direct contact with energized equipment or contact using tools or materials must be capable of working safely and must be familiar with special precautionary techniques, appropriate PPE, insulating and shielding materials, and insulated tools.
The training must be of the classroom or on-the-job type. The degree of training provided must be determined by the risk to the employee.
Tips
- Use the National Electric Code (NFPA 70) and the NFPA 70E Standard for Electrical Safety in the Workplace as references for electrical questions and issues. The National Electric Code corresponds to OSHA’s Installation of Electrical Systems, 1910.302 to .308. The NFPA 70E supplements OSHA’s Safety-Related Work Practices, 1910.331 to .335.
- For arc flash/blast protection, use an outside source, such as the NFPA 70E for employee protection.
- When employees are working in the vicinity of or using conductive objects such as ladders, scaffolds, and work platforms around overhead power lines, the lines must be:
- Deenergized and grounded, or
- Guarded, isolated, or insulated, or
- Clearance distances provided in 1910.333(c) must be maintained.
Checklist
Use the checklists below to make sure your company has all its electrical safety measures in place.
Examination, installation, and use of equipment
- Are only approved conductors and equipment used for electrical installations?
- Is equipment used and installed in accordance with instructions on the listing or label?
- Is all electrical equipment free from recognized hazards that are likely to cause death or serious physical harm?
Arcing parts
- Are all parts of electrical equipment that ordinarily produce arcs, sparks, flames, or molten metal enclosed or isolated from all combustible material?
Marking
- Is all electrical equipment marked with the manufacturer’s identity?
- Is all electrical equipment marked with the voltage, current, wattage, ratings, and other markings as necessary?
- Are all overcurrent devices (circuit breakers, fuses, etc.) legibly marked to indicate their purpose?
Working space
- Is access and working space around electrical equipment sufficient to provide ready and safe operation and maintenance?
- Are required working spaces around electrical equipment kept free of stored materials?
Guarding of live parts
- Are live parts of electrical equipment operating at 50 volts or more guarded against contact by approved cabinets or other forms of approved enclosures? (Note: See the regulations for exceptions.)
- In areas where electrical equipment may be exposed to physical damage, are the enclosures or guards arranged and of such strength to prevent such damage?
- Are all entrances to rooms or other guarded locations containing exposed live parts marked with conspicuous warning signs forbidding unqualified persons to enter?
- When normally enclosed live parts are exposed for maintenance and repair, are they guarded to protect unqualified persons from contact?
- Are safety signs, safety symbols, or accident prevention tags used where necessary to warn employees about electrical hazards?
Forklifts
OSHA’s 1910.178 regulation applies to all persons who use powered industrial trucks for such things as lifting, pulling, stacking, and moving materials. The regulation does not apply to compressed air or nonflammable compressed gas-operated industrial trucks, nor to farm vehicles, nor to vehicles intended primarily for earth moving, or over-the-road hauling.
Action steps
- Select appropriate and approved equipment.
- Make sure name plates and markings are adequate.
- Use only approved equipment for the particular area.
- Store and handle fuels safely.
- Change, charge, and store batteries properly.
- Provide emergency response equipment for flushing and neutralizing spilled electrolyte, for fire protection, for protecting charging apparatus from damage by trucks, and for adequate ventilation for dispersal of fumes from gassing batteries.
- Set brakes of highway trucks and chock wheels when they are boarded with powered industrial trucks.
- Ensure forklift operators are competent and have completed training.
- Certify operator training.
- Ensure proper operation and loading of forklifts.
- Inspect trucks daily before each shift.
- Perform appropriate maintenance.
- Remove damaged equipment from use.
Training action plans
Training must consist of a combination of formal instruction (e.g., lecture, discussion, interactive computer learning, DVD, written material), practical training (demonstrations performed by the trainer and practical exercises performed by the trainee), and evaluation of the operator’s performance in the workplace.
Training should cover the following topics:
- Safe operation
- Truck-related topics:
- Operating instructions, warnings, and precautions for the types of truck the operator will be authorized to operate
- Differences between the truck and the automobile
- Truck controls and instrumentation: where they are located, what they do, and how they work
- Engine or motor operation
- Steering and maneuvering
- Visibility (including restrictions due to loading)
- Fork and attachment adaptation, operation, and use limitations
- Vehicle capacity
- Vehicle stability
- Any vehicle inspection and maintenance that the operator will be required to perform
- Refueling and/or charging and recharging of batteries
- Operating limitations
- Any other operating instructions, warnings, or precautions listed in the operator’s manual for the types of vehicle that the employee is being trained to operate
- Workplace-related topics:
- Surface conditions where the vehicle will be operated
- Composition of loads to be carried and load stability
- Load manipulation, stacking, and unstacking
- Pedestrian traffic in areas where the vehicle will be operated
- Narrow aisles and other restricted places where the vehicle will be operated
- Hazardous (classified) locations where the vehicle will be operated
- Ramps and other sloped surfaces that could affect the vehicle’s stability
- Closed environments and other areas where insufficient ventilation or poor vehicle maintenance could cause a buildup of carbon monoxide or diesel exhaust
- Other unique or potentially hazardous environmental conditions in the workplace that could affect safe operation
Refresher training must be given when needed and employers must perform a triennial evaluation of forklift operators.
Tips
- Use seatbelts if they are available.
- Do not jump from an overturning, sit-down type forklift. Stay with the truck, holding on firmly and leaning in the opposite direction of the overturn.
- Do not raise or lower the forks while the forklift is moving.
- Do not allow passengers to ride on forklift trucks unless a seat is provided.
- Do not drive to another location with the work platform elevated.
Checklist
The checklists below will help you and your company ensure all forklift operations are done safely and compliantly.
Forklift operations
- Are the forklifts in your facility correctly designated for your type of operation (based on atmosphere, hazards of materials handled, etc.)?
- Are the brakes on each industrial truck capable of bringing the vehicle to a complete and safe stop when fully loaded?
- Is directional lighting provided on each industrial truck that operates in an area with less than 2 foot-candles per square foot of general lighting?
- Will the industrial truck’s parking brake effectively prevent the vehicle from moving when unattended?
- Are the required lift truck operating rules posted and enforced?
- Are industrial trucks equipped with flashing lights, horn, overhead guard, and name plate (load limits)?
Fueling
- Are fueling operations done in such a manner that the likelihood of spillage will be minimal?
- Is filling fuel tanks prohibited while engines are running?
- When spillage occurs during fueling operations, are measures taken to control vapors before restarting the engine?
Training
- Are only trained personnel allowed to operate industrial trucks?
- Have you documented what methods you use to train forklift operators?
Maintenance and inspection
- Are your forklifts inspected before being placed in service? Inspections should be at least daily, or after each shift, if used around the clock.
- Are adequate inspection and maintenance records kept?
- Are all industrial trucks not in safe operating condition removed from service?
- Are repairs to fuel and ignition systems conducted only in areas specifically designated for them?
Lockout/tagout
OSHA’s 1910.147 regulation establishes minimum performance requirements for the control of hazardous energy and applies to general industry. The regulation covers the servicing and maintenance of machines and equipment in which the unexpected startup or the release of stored energy could cause injury to employees. If employees are performing servicing or maintenance tasks that do not expose them to the unexpected release of hazardous energy, the regulation does not apply.
Action steps
- Establish a program and utilize procedures for affixing appropriate lockout devices or tagout devices to energy isolating devices, and to otherwise disable machines or equipment to prevent unexpected energization, start up, or release of stored energy.
- Utilize lockout when possible.
- Use tagout when lockout is not possible.
- Use appropriate lockout/tagout devices.
- Standardize lockout and tagout devices within the facility.
- Conduct a periodic inspection of the energy control procedure at least annually.
- Provide training as required by OSHA.
- Ensure proper exchange of safety information when working with contractors.
Training action plan
OSHA requires that all authorized employees be trained in recognition of hazardous energy sources, hazardous energy sources in use at their facility, and how to perform the lockout/tagout procedure.
OSHA also requires that all affected employees must be trained in the purpose and use of lockout/tagout.OSHA requires that all other employees must be instructed on the purpose of the plan, but not in the actual use.
OSHA requires that retraining be done when there are changes in equipment, job assignment, or procedures; when an audit shows deficiencies with the procedure; and when the employer feels the procedures should be reviewed.
Some general lockout/tagout training topics include:
- Description of hazardous energy sources: electrical, mechanical, pneumatic, hydraulic, chemical, thermal, water under pressure, gravity, and potential energy (stored energy)
- Why lockout/tagout is necessary
- The functions covered by lockout/tagout
- What an energy control program is
- Steps for preparation of the shutdown
- Application of lockout/tagout devices
- Description of lockout devices to be used
- Description of tags and types of tags to be used
Tips
- Ensure that lockout/tagout devices identify the individual users.
- Lockout/tagout does not apply when the employee is performing minor tool changes or other minor servicing activities that are routine, repetitive, and integral to production, and that occur during normal production operations. In these cases, employees must have effective, alternative protection.
- A tagout device may evoke a false sense of security. OSHA considers lockout devices to be more secure and more effective than tagout devices in protecting employees.
- If an outside contractor services or maintains machinery, the onsite employer and the contractor must inform each other of their respective lockout or tagout procedures.
- Employers need to review their lockout/tagout procedures at least once a year.
Checklist
Use these checklists to check that all processes for lockout/tagout are done correctly, including recordkeeping, training, and inspections.
- Are appropriate employees provided with individually keyed personal safety locks?
- Are correct lockout/tagout procedures in use?
- Are equipment control valves provided with a means for locking out?
- Are provisions made to prevent machines from automatically starting after a shutdown?
- Are suspended loads or potential energy (such as compressed springs, hydraulics, or jacks) controlled to prevent hazards?
- Is all machinery or equipment capable of movement, required to be de-energized or disengaged and locked out during cleaning, servicing, adjusting or setting up operations, whenever required?
- Is the locking-out of control circuits in lieu of locking-out main power disconnects prohibited?
- Is there a means provided to identify employees who are working on locked-out equipment by their locks or accompanying tags?
Recordkeeping
- Do you specify steps for the placement, removal and transfer of lockout/tagout devices, and the responsibility for them?
- Do you specify steps for the shutting down, isolating, blocking, and securing machines or equipment to control hazardous energy?
- Have you developed and documented procedures for the control of potentially hazardous energy?
Devices
- Are lockout/tagout devices singularly identified?
- Are lockout/tagout devices capable of withstanding the environment to which they are exposed for the maximum period of time that exposure is expected?
- Are lockout/tagout devices standardized within the facility in at least one of the following criteria: Color; shape; or size; and additionally, in the case of tagout devices, print and format shall be standardized?
- Are tagout device attachment means of a non-reusable type, attachable by hand, and self-locking?
Energy control procedure inspection
- Do you conduct a periodic inspection of the energy control procedure at least annually?
- Is periodic inspection performed by an authorized employee other than the ones(s) utilizing the energy control procedure being inspected?
- Do you certify that the periodic inspections of the energy control procedure have been performed?
Training
- Have employees been trained properly to perform their roles and responsibilities regarding lockout/tagout?
Machine guarding
OSHA’s Subpart O regulations apply to the safeguarding of many types of machines, such as woodworking machinery, abrasive wheels, mills and calendars, power presses, forging machines, and mechanical power transmission apparatus. Machines not listed must comply with the current industry standards for that piece of equipment.
Action steps
- Provide one or more methods of machine guarding to protect the operator and other employees in the machine area from hazards such as those created by point of operation, ingoing nip points, rotating parts, flying chips and sparks.
- Ensure the point of operation of machines is guarded.
- Ensure necessary guards are affixed and secured.
- Anchor machines designed for a fixed location to prevent walking or moving.
Training action plan
OSHA does not specifically require employers to train employees on machine guarding. However, workers should be trained in methods of protection from the hazards created by rotating parts and reciprocating or transverse motions during equipment operation.
Generally, machine guard training should cover:
- Types of guards used
- Reasons NOT to remove guards
- Reporting damaged guards
- Safe operation of the equipment
Tips
- Any machine part, functions, or process that may cause injury must be guarded.
- Guards must not create potential hazards and must be attached to the machine where possible — attach elsewhere if it is not possible to attach to the machine.
- If specific standards are not available, make sure the machine construction prevents the operator from having any part of his/her body in the danger zone during the operating cycle.
Checklist
Use these checklists to make sure all the machines at your facility are safely guarded to avoid incidents.
General
- Are all moving chains and gears properly guarded?
- Are machinery guards secure and so arranged that they do not offer a hazard in their use?
- Are rotating or moving parts of equipment guarded to prevent physical contact?
- Are the noncurrent-carrying metal parts of electrically operated machines bonded and grounded?
- Are work positions, machinery, pits or holes, and hazardous operations adequately guarded?
- Are workers protected from sharp objects which might pierce the feet or cut the hands (e.g., machinery, food handling and storage, sawing and cutting)?
- Is sufficient clearance provided around and between machines to allow for safe operations, set up and servicing, material handling, and waste removal?
Portable power tools
- Are grinders, saws, and similar equipment provided with appropriate safety guards?
- Are power tools used with the correct shield, guard, or attachment recommended by the manufacturer?
- Does each portable power tool have a constant pressure switch (dead man switch) that will shut off the power when pressure is released?
Stationary equipment
- Are all pulleys and belts that are within seven feet of the floor or working level properly guarded?
- Are fan blades protected with a guard having openings no larger than 1/2 inch, when operating within seven feet of the floor?
- Are foot-operated switches guarded or arranged to prevent accidental actuation by personnel or falling objects?
- Are machines constructed so as to be free from excessive vibration when the largest size tool is mounted and run at full speed?
- Are radial arm saws so arranged that the cutting head will gently return to the back of the table when released?
- Are saws used for ripping equipped with anti-kick back devices and spreaders?
- Are splash guards mounted on machines that use coolant to prevent the coolant from reaching employees?
- Are workers protected from fixed objects that may cause injury, such as sharp machine edges?
- Do arbors and mandrels have firm and secure bearings and are they free from play?
- Is equipment and machinery securely placed and anchored, to prevent moving?
- Is fixed machinery provided with appropriate safety guards to prevent injuries to the operator and other employees resulting from point of operation, ingoing nip point, rotating parts, flying chip, and spark hazards?
- Is there a power shut-off switch within reach of the operator’s position at each machine?
Pallet jacks (powered/motorized)
Powered/motorized pallet jacks are a common fixture in many industries and workplaces. They allow workers to quickly move heavy loads from one location to another, go in tight spaces that forklifts cannot, and conveniently make frequent stops to “pick” materials. While they may seem like a straightforward and harmless piece of machinery, the fact is powered pallet jacks can pose deadly hazards if not operated properly and by trained individuals. In fact, OSHA requires training of powered pallet jack operators under the same requirement as that for forklift operators—the 1910.178 Powered Industrial Truck regulation.
Action steps
- Certify operator training. Just because an operator is trained/certified to operate a forklift does not make them automatically certified to operate a powered pallet jack: training must be specific to each “type” of equipment.
- Select appropriate and approved equipment.Make sure name plates, markings, and warning labels are in place and adequate.
- Use only approved equipment for the particular area.
- Change, charge, and store batteries properly.
- Provide emergency response equipment for flushing and neutralizing spilled electrolyte, for fire protection, for protecting charging apparatus from damage by trucks, and for adequate ventilation for dispersal of fumes from gassing batteries.
- Set brakes of highway trucks and chock wheels when they are boarded with powered industrial trucks.
- Ensure proper operation and loading.
- Inspect trucks daily before each shift.
- Perform appropriate maintenance.
- Remove damaged equipment from use.
- Become familiar with and follow the manufacturer’s operation, safety, and maintenance instructions.
Training action plans
Training must consist of a combination of formal instruction (e.g., lecture, discussion, interactive computer learning, video tape, written material), practical training (demonstrations performed by the trainer and practical exercises performed by the trainee), and evaluation of the operator’s performance in the workplace.Training should cover the following topics:
- Safe operation
- Truck-related topics:
- operating instructions, warnings, and precautions for the types of pallet jacks the operator will be authorized to operate
- differences between the pallet jack and the automobile
- controls and instrumentation: where they are located, what they do, and how they work
- engine or motor operation
- steering and maneuvering
- visibility (including restrictions due to loading)
- fork and attachment adaptation, operation, and use limitations
- capacity
- stability
- any inspection and maintenance that the operator will be required to perform
- refueling and/or charging and recharging of batteries
- operating limitations
- any other operating instructions, warnings, or precautions listed in the operator’s manual
- Workplace-related topics:
- surface conditions where the equipment will be operated
- composition of loads to be carried and load stability
- load manipulation
- pedestrian traffic in areas where the equipment will be operated
- hazardous (classified) locations where the vehicle will be operated
- ramps and other sloped surfaces that could affect stability
Refresher training must be given when needed and employers must perform a triennial evaluation of forklift operators.
Tips
- Be careful of rear-end swing when turning corners. The rear end will swing wide to the outside of a turn when operating with the load end leading. Extra clearance may be needed to avoid striking racking, pedestrians, etc.
- Check the data plate to determine the grades/inclines the equipment can operate safely on. When walking with a pallet truck with or without a load, the forks should be pointed downgrade, regardless of direction of travel. On walkie/riders, when in the riding position travel with loaded trucks with the load upgrade; when empty with the load end downgrade.
- Always look in the direction of travel. Pallet jack operators have had fingers and other parts crushed between the pallet jack and racks and walls—in particular, when backing out.
- Do not ride powered pallet jacks. Only walkie/riders have a platform for riding.
- Do not allow passengers on pallet jacks or walkie/riders.
- Inspect truck trailers before entering. Pallet jacks are heavier than they look and combined with a load can fall through a worn floor.
Checklist
These checklists will help ensure all pallet jacks are functioning safely and being used correctly.
Pallet jack operations
- Are the pallet jacks in your facility correctly designated for your type of operation (based on atmosphere, hazards of materials handled, etc.)?
- Are the brakes on each industrial truck capable of bringing the vehicle to a complete and safe stop when fully loaded?
Training
- Are only trained personnel allowed to operate pallet jacks?
- Have you documented what methods you use to train operators?
Maintenance and inspection
- Are your pallet jacks inspected before being placed in service? Inspections should be at least daily, or after each shift, if used around the clock.
- Are adequate inspection and maintenance records kept?
- Are all industrial trucks not in safe operating condition removed from service?
- Does the inspection include all items recommended by the manufacturer? At minimum, these typically include:
- Forks
- Brakes
- Quick disconnect, if equipped
- Hand guard
- Controls
- Battery and battery securing mechanism
- Warning labels/data plates
- Hydraulics (including fluid leaks)
- Horn
- Belly button, if equipped
Portable tools
OSHA’s 1910.242 regulation on hand and portable power tools applies to all employers who are responsible for the safe condition of tools and equipment used by employees, including tools and equipment that may be furnished by employees.
Action steps
- Ensure the safe condition of tools and equipment used by employees, including tools and equipment which may be furnished by employees.
- Ensure that compressed air is not used for cleaning purposes except where reduced to less than 30 p.s.i. and then only with effective chip guarding and personal protective equipment.
- Ensure portable power tools are guarded properly.
- Follow manufacturer’s instructions regarding tools.
- Maintain and inspect tools to prevent safety hazards.
Training action plan
OSHA’s regulations do not have specific employee training requirements for portable tools, but employees who understand the hazards and know how to use hand and portable powered tools correctly will have less risk of injury.
You should train workers to recognize the hazards associated with the different types of tools and the safety precautions necessary to prevent or control those hazards.
Generally, training should cover:
- Maintenance of tools
- Using the right tool for the job
- Inspecting tools before use
- Following manufacturers’ instructions
- Using PPE
Tips
- Recondition or replace chisels and punches, which develop mushroomed head during use, as necessary.
- Inspect and replace broken, cracked, or fractured handles on hammers, axes, and similar tools.
- Make sure that grinders, saws, and similar equipment is only used with appropriate safety guards.
- Inspect pneumatic and hydraulic hoses on power operated tools for deterioration or damage on a regular basis.
- Dull tools are more dangerous than sharp ones —keep cutting tools properly sharpened.
Checklist
Use these checklists to make sure all portable tools are in good working order.
General
- Are all portable hand or power tools maintained in a safe condition?
- If compressed air is used for cleaning purposes, is it used at pressures less than 30 p.s.i. and only with effective chip guarding and personal protective equipment?
- Are power tools equipped and used with guards whenever possible?
- Are all belts, gears, shafts, pulleys, sprockets, spindles, drums, flywheels, chains, or other reciprocating, rotating or moving parts of equipment guarded if operator is exposed to contact or if they otherwise create a hazard?
- Is all necessary personal protective equipment provided whenever the use of hand and power tools could create falling, flying or splashing debris, or harmful dusts, fumes, mists, vapors, or gases?
- On hand-held power tools, is the operating control located so as to minimize the possibility of accidental operation?
- Are all portable, electrically powered tools properly grounded or double insulated?
- Are impact tools, such as drift pins, wedges, and chisels, kept free of mushroomed heads?
- Are the wooden handles of tools kept free of splinters or cracks and are they fixed tightly in the tool?
- Is it prohibited to lower or hoist a tool by the cord?
- Do woodworking tools meet the American National Standards Institute (ANSI) safety codes?
Pneumatic power tools and hose
- Are pneumatic power tools secured to the hose or whip by some positive means, so as to prevent the tool from being accidentally disconnected?
- Are safety clips or retainers used on pneumatic impact (percussion) tools to prevent attachments from being accidentally expelled?
- Are all pneumatically driven nailers, staplers, and other similar equipment which have automatic fastener feeds and which operate at more than 100 p.s.i. pressure at the tool equipped with a safety device on the nozzle to prevent the tool from ejecting fasteners, unless the muzzle is in contact with the work surface?
- Are all compressed air hoses and hose connections designed for the pressure and service to which they are subjected?
Identifying Health Hazards
What are health hazards?
A substance is considered a “health hazard” if exposure through skin or eye contact, inhalation, or ingestion causes temporary or permanent injury. The health effects to the exposed individual may be acute or chronic, resulting from repeated long-term exposure to low concentrations of a hazardous substance. Exposure to excessive temperatures is also considered a health hazard. Extreme heat can cause heat exhaustion or heat stroke, which is a life threatening condition.
Acute and chronic health effects
An acute health effect usually occurs rapidly, following a brief exposure. A chronic health effect is long and continuous and follows repeated long-term exposure. Some examples of chemicals which exhibit health hazards are:
- Carcinogens
- Acute and chronic toxins
- Irritants
- Corrosives
- Sensitizers
As a safety professional, you need to be aware of the dangerous substances and temperature extremes in your workplace that pose health risks to employees. Everyone whose job involves exposure, or the risk of exposure, to hazardous chemicals and hot environments must be adequately informed, trained, and protected.
Many OSHA standards have specific requirements for protecting employees from these hazards. In this section, you will find action steps, tips, answers to frequently asked questions, checklists, and training exercises and handouts on a variety of health-related topics. All of these will help you ensure a safer workplace for those employees with health hazard exposure risks.
Asbestos
OSHA’s 1910.1001 standard on asbestos covers workers who may be exposed to asbestos, a substance found in installed products such as shingles, floor tiles, cement pipe and sheet, roofing felts, insulation, ceiling tiles, fire-resistant drywall, and acoustical products. The standard reduces employee exposure to asbestos to 0.1 fiber per cubic centimeter of air (f/cc) averaged over an 8-hour day. The standard also sets an action level; it is 0.1 f/cc averaged over eight hours. If this level is exceeded, employers must begin compliance activities such as air monitoring, employee training, and medical surveillance.
Action steps
- Establish and implement a written program to reduce employee exposure to or below the TWA and to or below the excursion limit by means of engineering and work practice controls and by the use of respiratory protection.
- Institute a training program for all employees who are exposed to airborne concentrations of asbestos at or above the permissible exposure limit and/or excursion limit and ensure their participation in the program.
- Establish regulated areas wherever airborne concentrations of asbestos and/or PACM are in excess of the TWA and/or excursion limit.
- Follow proper hygiene practices and provide a clean room.
- Implement appropriate monitoring and medical surveillance.
- Ensure appropriate medical evaluation.
- Provide adequate personal protective equipment and clothing.
- Implement appropriate engineering controls and work practices.
- Provide appropriate signs and labels to warn of and identify asbestos hazards.
- Follow proper procedures for working with and removing asbestos.
Training action plan
You must provide training to employees who are exposed to airborne asbestos levels that are at or above the permissible exposure limit and/or excursion limit. Training content should include:
- Health effects associated with asbestos exposure.
- Relationship between smoking and exposure to asbestos in producing lung cancer.
- Quantity, location, manner of use, release, and storage of asbestos, and the specific nature of the operations that could result in exposure to asbestos.
- Asbestos location.
- Specific procedures implemented to protect employees from exposure to asbestos, such as appropriate work practices, emergency clean-up procedures, and PPE to be used.
- Proper use and the limitations of respirators and protective clothing.
- Purpose and description of worker protection programs.
Training is required prior to or at the time of initial assignment of asbestos-related work.
Documentation
Training records must be maintained for one year beyond an employee’s last day of employment.
Tips
- Employers must create controlled zones known as regulated areas that are designed to protect employees where certain work with asbestos is performed.
- Workers who handle asbestos should wash their faces, hands, and forearms thoroughly with soap and water before eating, smoking, or using toilet facilities.
Checklist
Use the checklists below to make sure your company is meeting all the necessary safety precautions.
Work practices
- Are proper precautions being taken when handling asbestos and other fibrous materials?
- Are wet methods used, when practicable, to prevent the emission of airborne asbestos fibers, silica dust, and similar hazardous materials?
- Is smoking prohibited in areas where occupational exposure to asbestos occurs?
Personal Protective Equipment
- Are respirators used during periods necessary to install or implement feasible engineering and work-practice controls?
- Are respirators used during work operations, such as maintenance and repair activities, for which engineering and work-practice controls are not feasible?
- Are respirators used during work operations for which feasible engineering and work-practice controls are not yet sufficient to reduce employee exposure to or below the TWA and/or excursion limit?
- Are respirators used during emergencies?
- Is appropriate personal protective equipment used when working with asbestos?
Facilities marking
- Are signs posted warning of the presence and hazards of asbestos, where required?
- Are signs posted so that an employee may read the signs and take necessary protective steps before entering the area?
- Are warning labels affixed to all materials, mixtures, waste, etc., containing asbestos fibers, or to their containers?
- Are required asbestos signs and labels in compliance with EPA’s asbestos marking requirements?
Bloodborne pathogens
OSHA’s 1910.1030 Bloodborne Pathogens standard applies to any employer with employees who are occupationally exposed to blood or other potentially infectious materials; this determination must be made without considering use of any personal protective equipment (PPE).
Action steps
- Develop a written exposure control plan to eliminate or minimize employee exposure.
- Provide information and training.
- Ensure handwashing requirements are met.
- Provide containers for infectious materials.
- Ensure proper disposal and care of contaminated sharps.
- Ensure proper servicing and shipping of infectious equipment.
- Follow proper procedures for regulated waste containment.
- Make the hepatitis B vaccine and vaccination series available to all employees who have occupational exposure.
- Prepare an exposure determination.
- Maintain proper records.
- Provide proper personal protective equipment.
- Use engineering and work practice controls to eliminate or minimize employee exposure.
- Use proper labeling for biohazards.
- Document annually consideration and implementation of appropriate commercially available and effective safer medical devices designed to eliminate or minimize occupational exposure.
Training action plan
All employees with occupational exposure to bloodborne pathogens need training in OSHA’s requirements and the employer’s exposure control plan. For example, this might include first aid responders, emergency response team members, or health care workers.
Training content should cover:
- The epidemiology and symptoms of bloodborne diseases.
- How trainees may contact bloodborne diseases.
- The company’s Exposure Control Plan (ECP).
- Recognizing potential exposures to blood and other potentially infectious materials. Engineering controls affecting trainees.
- Location of handwashing facilities.
- Work practices affecting workers.
- General approach and selection process for Personal Protective Equipment (PPE).
- The hepatitis B vaccine, including its efficacy, safety, method of administration, and benefits of getting the vaccination.
- The company’s procedure to respond to a worker who has been exposed to blood or other potentially infectious material on the job.
- Follow-up available to workers involved in an exposure incident.
- The signs and labels your company uses to warn workers of biohazards.
- Location and explanation of regulatory text and ECP.
Employees must be trained prior to initial exposure to bloodborne pathogens and at least annually thereafter.
Documentation
Very specific training records must be maintained. Information must include dates of training, contents of training sessions, names and qualifications of trainers, names and job titles of those trained. Records must be retained for three years.
Tips
- In determining who is covered by the Bloodborne Pathogens standard, remember that if an employee is providing first aid or CPR as a Good Samaritan and not as a trained first aider, designated to perform first aid by the employer, that employee is not covered by the standard.
- Regarding designated responders, OSHA compliance directive CPL 02-02-069 states, “An employee who routinely provides first aid to fellow employees with the knowledge of the employer may also fall, de facto, under this designation even if the employer has not officially designated this employee as a first aid provider.” For example, if first aid supplies are stored in a supervisor’s office, and the supervisor regularly assists injured employees, the supervisor could be considered a de facto responder.
- Recapping, bending, or removing needles is permissible only if there is no feasible alternative or if required for a specific medical procedure such as blood gas analysis.
- Any specific eye, mouth, other mucous membrane, non-intact skin, or parenteral contact with blood or other potentially infectious materials is considered an exposure incident.
- Where employees are exposed to blood or OPIM, the employer must develop a written schedule for cleaning each area where exposures occur.
- If blood or OPIM is absorbed by kitty litter or other absorbents, and is no longer pourable, drippable, squeezable, or flakable, then the waste is not considered infectious waste.
Checklist
Review these bloodborne pathogens checklists to ensure safety and compliance at your facility.
General
- Do all employees who are expected to respond to medical emergencies as part of their work have available and understand how to use appropriate personal protective equipment to protect against exposure to bloodborne diseases?
Training
- Have all employees who are expected to respond to medical emergencies as part of their work had training on appropriate procedures to protect them from bloodborne pathogens, including universal precautions?
- Have all employees who are expected to respond to medical emergencies as part of their work received first-aid training?
Containers
- If you have a refrigerator where blood or other infectious materials are kept, do you prohibit storage of food or drink in it?
- Is a container provided for reusable sharps that is puncture resistant, properly labeled, and leakproof?
Medical
- Where employees have had an exposure incident involving bloodborne pathogens, was an immediate post exposure medical evaluation and follow up provided?
- If employees are expected to respond to medical emergencies as part of their work do they have available and understand how to use appropriate personal protective equipment to protect against exposure to bloodborne diseases?
Recordkeeping
- Do you establish and maintain an accurate record for each employee with occupational exposure to bloodborne pathogens?
- Do you ensure that employee medical records required by 1910.1030(h)(1) are kept confidential and appropriately maintained?
- Do training records include dates of training sessions and other required information?
- Are training records maintained for three years from the date on which the training occurred?
- If you have an employee(s) with occupational exposure as defined by 1910.1030(b) have you established an appropriate Exposure Control Plan?
- If applicable, do you document annually consideration and implementation of appropriate commercially available and effective safer medical devices designed to eliminate or minimize occupational exposure?
- If applicable, have you established and do you maintain a sharps injury log for the recording of percutaneous injuries from contaminated sharps?
Emergency eyewash and shower
OSHA requires emergency eyewashes and showers be present where the eyes or body of any person may be exposed to injurious corrosive materials. The emergency equipment must be available within 10 seconds.
Action steps
- Provide suitable facilities for drenching or flushing of the eyes and body where there is exposure to injurious corrosive materials.
- Ensure eyewash/showers are located within 10 seconds of the hazard.
- Inspect and maintain eyewash/shower equipment per manufacturer’s specifications and instructions.
- Train employees on locations and use of eyewash/shower equipment.
Training action plan
OSHA does not have specific training requirements regarding emergency eyewash and shower equipment. However, employees should be trained on the location and use of this equipment.
Additionally, you may want to train employees on safe handling of chemicals, proper protective equipment, location of SDSs, and other hazcom requirements.
Tips
- ANSI Z358.1-1998 contains additional information on permissible water temperatures for eyewashes and showers. The standard makes reference to a delivered flushing fluid temperature being “tepid,” which the standard defines as “moderately warm; lukewarm.”
- ANSI Z358.1 indicates that an eyewash unit must be positioned with the flushing fluid nozzles between 33 inches and 45 inches from the standing surface.
- OSHA does not specifically require floor markings around eyewash stations or emergency showers. But because OSHA requires that the stations and showers be provided for immediate emergency use and because ANSI recommends they be accessible and free of obstructions, floor markings are a popular method to help keep the area clear of obstructions.
- Acanthamoebea are small amoebae which have been found in portable and stationary eyewash stations. Infections caused by Acanthamoebae are difficult to recognize and treat and may result in the loss of the infected eye. Chlorination has been found to be effective in destroying Acanthamoebae.
Checklist
Review this emergency eyewash and shower checklist:
- Are there suitable facilities for drenching or flushing of the eyes and body where there is exposure to injurious corrosive materials?
- Are eyewash/showers located within 10 seconds of the hazard?
- Do you inspect and maintain eyewash/shower equipment per manufacturer’s specifications and instructions?
- Have employees been trained on locations and use of eyewash/shower equipment?
Ergonomics
There currently is no specific regulatory requirement for the development of an ergonomics program. However, under the General Duty Clause, the employer is responsible for providing a “safe and healthful work environment.” Therefore, every employer should assess the type of workplace being provided to employees, examine injury and illness records to see what types of injuries are being reported, and develop the appropriate ergonomic responses.
Action steps
- Evaluate workplace for ergonomic hazards (repetitive tasks, awkward posture, heavy lifting, etc.).
- Develop appropriate ergonomic controls.
- Train employees on proper work practices (i.e., safe lifting).
- Keep adequate records of injuries/illnesses.
Train action plan
OSHA does not have specific training requirements for ergonomics. However, employees who perform work involving repetitive motions, awkward postures, material handling, forceful exertions, etc., can benefit from training in ergonomics. OSHA regulates ergonomics hazards under the General Duty Clause (Section 5(a)(1)) of the Occupational Safety and Health Act of 1970. Employers have a general duty to provide a safe and healthful workplace.
Training content could include:
- Definition of ergonomics,
- Common injuries or illnesses (musculoskeletal disorders),
- Causes of ergonomics injuries or illnesses (repetitive motions, forceful exertions, vibrations, sustained or awkward postures, etc.),
- Workplace risk factors,
- Controls used,
- Work station redesign, and
- Medical management.
Tips
- Rotating employees into several different jobs during the course of a workshift is a way to distribute work so that each employee spends less time performing the same repetitive tasks.
- Designing jobs so they include a wider variety of tasks (or a longer motion pattern) may reduce the frequency and duration of repetitive motions.
- Micro breaks or rest pauses — building short micro pauses between motions or tasks is another way to give muscles and tendons recovery time.
- Computer desk areas should be deep enough to accommodate a monitor placed at least 20 inches away from the eyes.
- Ideally, a worker’s desk should have a work surface large enough to accommodate a monitor and a keyboard. Usually about 30 inches is deep enough to accommodate these items.
Checklist
Review these checklists to help prevent ergonomic hazards in your workplace.
General
- Are measures taken to identify and control all ergonomic hazards?
- Are all task requirements visible from comfortable positions?
- Are armrests and footrests provided where needed?
- Are cushioned floor mats provided for workers who are required to stand for long periods?
- Are mechanical aids and equipment provided where feasible?
- Are worker movements analyzed so that potential injuries (e.g., hand or foot injuries, repetitive motion injuries, or strain from lifting) are avoided?
- Are workers wearing protective clothing or equipment that is appropriate for the job, and does it fit properly?
- Are wrist supports present at computer workstations?
- Does the working space allow for a full range of work movements?
- Have you prevented employees’ hands or arms from being subjected to pressure from sharp edges on work surfaces?
- Is the work flow properly organized (e.g., is the worker required to move at an acceptable pace)?
- Is the work surface height proper and adjustable?
- Is the workstation designed to minimize or eliminate twisting at the waist, reaching above the shoulder, bending at the waist, static muscle loading, extension of the arms, bending or twisting of the wrist, and elevation of elbows?
Training
- Do you provide all employees with basic information about common musculoskeletal disorders and their signs and symptoms?
- Have all employees been provided basic information about how to report MSDs and their signs and symptoms in your workplace?
- Are all employees provided basic information about the kinds of risk factors, jobs, and work activities associated with MSD hazards?
Computer workstations
- Do you provide chairs that can be adjusted to different heights?
- Do chairs support the lower back (lumbar area)?
- Do chairs have padded seats and roll on wheels (casters)?
- Do chairs support the forearms with armrests while allowing the elbows to remain near the waist?
- Are the keyboard and mouse locations adjustable?
- Are wrist supports present at computer workstations?
- Is the monitor arranged to enable the employee to see the screen clearly without leaning forward?
- Is there enough space under the work surface for the employee’s knees?
- Are workers encouraged to take short breaks?
Recordkeeping
- Do you keep adequate records of musculoskeletal disorders and their signs, symptoms, and hazards?
Hazard communication
About one in every four workers routinely comes in contact with hazardous chemicals while performing his or her job. In many cases, the chemicals may be no more dangerous than those used at home. But in the workplace, exposure is likely to be greater, concentrations higher, and exposure time longer. Reactions to chemical exposures range from slight skin, eye, or respiratory irritation to life-threatening cancers, blood diseases, and debilitating lung damage.
OSHA developed the Hazard Communication Standard (HCS) to protect workers from these dangerous exposures. The standard was originally based on a simple concept—that employees have both a need and a right to know about the hazards and identities of the chemicals they are exposed to when working. In 2012, OSHA changed the HCS drastically, using the concept that the employees have a “right to understand” about the hazards of chemicals they are exposed to. They also need to know what they can do to protect themselves. Additionally, when employers have information about the chemicals being used, they can take steps to reduce exposures, substitute less hazardous materials, and establish safe work practices to prevent illnesses and injuries caused by these substances.
The HCS establishes uniform requirements to make sure that the hazards of all chemicals imported into, produced, or used in U.S. workplaces are evaluated and classified and that this hazard information is communicated to employers and exposed employees. Basically, the rule incorporates a downstream flow of information. This means that chemical manufacturers have the primary responsibility for generating and disseminating information and chemical users must obtain the information and transmit it to their exposed employees.
Evaluating and classifying chemical hazards involves technical concepts and is a process that requires the professional judgment of experienced experts. That’s why the HCS is designed so that employers who simply use chemicals, rather than produce or import them, are not required to evaluate the hazards of those substances.
Hazard classification is the responsibility of the producers and importers of the materials, who must then pass that information to the purchasers and end-users of the products. Employers that don’t produce or import chemicals need only focus on those parts of the rule that deal with establishing a workplace program and communicating information to their workers. (Note: If employers create mixtures in the workplace, there will be more responsibility and requirements than for employers who simply use chemicals that have already been evaluated and classified.)
Action steps
- Develop, implement, and maintain a written hazard communication program.
- Provide employees with effective information and training on hazardous chemicals in their work area.
- Comply with all hazard communication actions for any chemical which is known to be present in the workplace in such a manner that employees may be exposed under normal conditions of use or in a foreseeable emergency.
- Evaluate chemicals produced in or imported into the workplace to determine if they are hazardous.
- Obtain or develop a Safety Data Sheet or SDS for each hazardous chemical produced or imported.
- Maintain an SDS in the workplace for each hazardous chemical used.
- Make sure all containers of chemicals are labeled as required.
Training action plan
Under the provisions of this standard each employee exposed to hazardous chemicals must receive information about those chemicals through a comprehensive hazard communication program which includes identification of chemical hazards, chemical labeling, and safety data sheets in the training program.
You must provide hazcom training at the time your employees are initially assigned to their jobs, when a new chemical hazard is introduced into the work area or when the employee’s job duties change such that he or she is now exposed to a hazardous chemical.
The training must be comprehensible. If the employees must receive job instructions in a language other than English, then training and information will probably also need to be conducted in a foreign language.
Generally, training content should cover:
- Hazcom and chemical terminology,
- Physical and health hazards of chemicals,
- Written hazard communication program,
- Location of relevant hazcom documents and materials,
- Chemical protective measures,
- Safety data sheets (SDSs), and
- Labeling requirementsHazards of nonroutine tasks and unlabeled pipes related to hazardous chemicals.
Documentation
OSHA does not require training documentation for individual employees regarding hazard communication, but it is a good idea to keep it anyway. Training records can tell you who was trained on what, when, and who conducted the training.
Tips
- The employer does not have to retrain each new hire if that employee has already received training from a former employer, a union, or other entity. However, the employer would have to supply such information as location of SDSs, workplace hazards, labeling systems, and so on.
- An employer can claim trade secret status when it can support such a claim. However, chemical ingredients of public knowledge or of general knowledge in an industry that are disclosed by the goods one markets cannot be claimed as a trade secret.
- Chemicals generated in the work operations, such as welding fumes, dusts, and exhaust fumes, are sources of chemical exposure and must be listed on the chemical inventory.
- The chemical “identity” is any name or term that appears on the label, the SDSs, and the chemical inventory, and thus links these three sources of information.
- SDSs must be readily accessible to employees when they are in their work areas during their workshifts.
- Under the rule, “exposure” or “exposed” means that an employee is subjected to a hazardous chemical in the course of employment through any route of entry and includes potential exposure.
Checklist
Review these hazard communication checklists.
Labeling
- Do you ensure that each container of hazardous chemicals in the workplace is labeled, tagged or marked identifying the chemical it contains?
- Do you ensure that each container of hazardous chemicals is labeled, tagged or marked with the appropriate hazard warnings?
- If you remove or deface labels on incoming containers of hazardous chemicals, do you immediately mark the containers with the required information?
- Do you ensure that labels or other forms of warning are legible, in English, and prominently displayed on the container, or readily available in the work area throughout each work shift?
Safety data sheets
- Do you have a safety data sheet for each hazardous chemical you use?
- Are the sheets written in English?
- Does each sheet include everything that is required in 1910.1200?
- Do you ensure that sheets are readily accessible to employees in the work area during each work shift?
- If employees must travel between workplaces during a work shift, do you sheets in each workplace or at a central location at the primary workplace facility in case of an emergency?
Training
- Are employees provided required hazard communication training?
- Do you provide information to employees as to the location and availability of the written hazard communication program and safety data sheets?
Recordkeeping
- Have you compiled a hazardous chemical inventory?
- Have you documented the employee training that you have done under the Hazcom standard?
Written program
- Have you developed, implemented, and do you maintain a written hazard communication program?
- Does your hazard communication program include a list of the hazardous chemicals known to be present using an identity that is referenced on the appropriate safety data sheet?
- Do you make the written hazard communication program available upon request to the employees or designated representatives in accordance with 1910.20(e)?
Heat stress
Hot work environments can be found in any climate, any time of the year. Many employees working in foundries, glass or ceramic plants, mines, bakeries, as well as during roofing, farming, exterior painting, utility work, road repair, and construction activities are exposed to high heat on a regular basis. In addition to temperature, high humidity adds to the heat burden for workers in laundries, restaurant kitchens, and canneries. Overexposure can cause:
- Fatigue,
- Heat rash,
- Fainting,
- Muscle cramps,
- Heat exhaustion, and
- Heat stroke.
Reduce the risk of heat stress by:
- Eliminating steam leaks,
- Providing cooling fans,
- Modifying equipment, and
- Using power tools to reduce manual labor.
Although federal OSHA does not specifically regulate heat stress, it can issue citations under the General Duty Clause of the OSH Act when employees are exposed to serious hazards which the employer could reduce or eliminate.
Action steps
- Identify environmental factors in your facility that affect the level of heat stress:
- High temperatures (90ºF or above can cause heat stress),
- High humidity (sweat doesn’t evaporate rapidly),
- Intense radiant heat (such as from the sun or a furnace), and
- Low air velocity (lowers the rate at which sweat evaporates).
- Identify operations that expose employees to excessive heat. You may need to enlist the aid of an industrial hygienist to take temperature readings using specialized equipment.
- Evaluate employees’ work loads. Conduct a job analysis to determine activity levels of light, moderate, or heavy.
- Evaluate employees’ general health and physical condition. Personal characteristics such as age, weight, fitness, medical conditions, and acclimatization can affect an individual’s level of stress.
- Assess employees’ clothing, especially if they wear personal protective equipment such as heavy leather, chemical protective clothing, or respirators.
- Provide plenty of drinking water — as much as a quart per employee per hour.
- Alternate work and rest periods with longer rest periods in a cool area can help avoid heat stress. If possible, schedule heavy work during the cooler parts of the day and provide protective clothing.
- Implement engineering and administrative controls to reduce heat exposures. Consider the following to lessen the risk of heat stress:
- Increase general ventilation;
- Install spot cooling by local exhaust ventilation at points of high heat production;
- Use shields as protection from radiant heat sources;
- Install evaporative cooling and mechanical refrigeration; and
- Provide personal cooling devices or protective clothing.
Training action plan
Before you conduct training, you will want to assess the heat hazards in your facility. This includes monitoring the environment and evaluating your employees’ work loads. When you understand the hazards, you can answer your employees’ questions.
A good heat stress training program should include:
- The risk factors of being affected by the heat;
- The problems caused by heat (fatigue, rash, fainting, muscle cramps, and heat exhaustion);
- Recognizing danger signs and symptoms;
- Knowing the first aid procedures for heat stroke and that heat stroke can be life threatening;
- Employee responsibilities in avoiding heat stress; and
- Use of protective clothing and equipment.
Review the contents of this training action plan and decide which elements to use, based on conditions and operations at your facility. From these elements, build a training program that addresses your facility’s specific heat-related hazards.
- Identify the hot work environments.
- Describe the risk factors of being affected by the heat.
- Explain how heat can increase fatigue.
- Explain how heat rash can occur.
- Talk about how people can faint from the heat.
- Explain how muscle cramps can be caused by heat.
- Talk about heat exhaustion.
- Stress that heat stroke is a life-threatening condition.
- Explain how heat exposures can be measured and the risk evaluated.
- Describe how exposure to heat can be controlled, such as:
- Intermittent rest periods with water breaks,
- Relief workers,
- Pacing the work,
- Reducing the physical demands of the job,
- Providing cool recovery or rest areas, and
- Scheduling work for cooler times of the day, or when heat producing equipment isn’t being operated.
- Train members of the emergency response team to recognize and treat heat stress disorders.
- Train supervisors to detect early signs of heat stress.
- Document all training.
Tips
- Not everyone is affected equally by the heat. Age, weight, degree of physical fitness, metabolism, medications, use of alcohol or drugs, and a variety of medical conditions such as hypertension all affect a person’s sensitivity to heat.
- For workers who have had recent experience in jobs where heat levels were high enough to produce heat stress, the acclimatization regimen should be 50 percent exposure on day one, 60 percent on day two, 80 percent on day three, and 100 percent on day four.
- For new workers (and people who have been away from working in the heat for an extended time), the regimen should be 20 percent on day one, with a 20 percent increase in exposure each additional day.
- On the first day of work in a hot environment, the body temperature, pulse rate, and general discomfort will be higher. With each succeeding daily exposure, all of these responses will gradually decrease, while the sweat rate will increase. When the body becomes acclimated to the heat, the individual finds it possible to perform work with less strain and distress.
- Heat stroke is a life-threatening condition. It occurs when the body’s temperature regulatory system fails and sweating becomes inadequate to remove excess body heat. In heat stroke, the victim’s skin is hot and dry and body temperature is usually 105ºF or higher.
Checklist
This checklist may be used as part of employee awareness training regarding the hazards of working in high temperatures.
Symptoms of heat exhaustion
There are many symptoms related to heat exhaustion. Several can be present at the same time.
- Headaches.
- Dizziness.
- Light-headedness.
- Mental confusion.
- Weakness.
- Mood changes.
- Pale and clammy skin.
- Nausea.
- Dark-colored urine.
- Fainting.
Symptoms of heat stroke
Like heat exhaustion, heat stroke has multiple symptoms.
- Dry, pale skin with no sweating.
- Hot, red skin.
- Seizures.
- Mental confusion.
- Fainting.
- Mood changes.
Risk factors to consider
Factors that put you at greater risk for heat-induced illness include:
- Had a heat-induced illness in the past.
- Take certain medications.
- Drink alcoholic beverages.
- Obesity.
- Wear heavy or restrictive personal protective equipment like protective suits or respirators.
Treating heat-releated illnesses
When a coworker suffers a heat-related illness, you should:
- Move the person to a cool, shaded area.
- Stay with the person at all times (don’t leave the person unattended).
- Loosen and remove the person’s heavy clothing.
- Offer cool water — a small cup every 15 minutes.
- Cool the person by fanning, spraying with cool water, or putting cool, wet towels on the head or other exposed skin.
- Place ice packs (if available) under the arm pits and in the groin area.
- If the person is dizzy or lightheaded, lay the person on his or her back and raise the feet and legs several inches.
- If the person is nauseous, lay the person on his or her right side.
Call for help
If the person needs help beyond what you are providing, follow your company’s emergency procedures.
Protect yourself
When working in hot environments you should:
- Slowly build up tolerance to the heat.
- Avoid eating large meals before working in hot environments.
- Learn the signs and symptoms of heat-induced illnesses.
- Drink plenty of cool water.
- Avoid caffeine or alcoholic beverages because they make the body lose water and increase the risk for heat illnesses.
- Wear light, loose-fitting, breathable clothing (such as clothing made from cotton).
- Take short, frequent breaks in the shade or away from the heat (like in an air-conditioned vehicle) to allow the body to cool down.
- Use the buddy system so one person can check on the other.
Hexavalent chromium
Chromium hexavalent (CrVI) compounds, often called hexavalent chromium, exist in several forms. Industrial uses of hexavalent chromium compounds include chromate pigments in dyes, paints, inks, and plastics; chromates added as anticorrosive agents to paints, primers, and other surface coatings; and chromic acid electroplated onto metal parts to provide a decorative or protective coating. Hexavalent chromium can also be formed when performing “hot work” such as welding on stainless steel or melting chromium metal. In these situations the chromium is not originally hexavalent, but the high temperatures involved in the process result in oxidation that converts the chromium to a hexavalent state.
Action steps
- Survey your operations for potential exposure to hexavalent chromium. Employers can consult their suppliers or examine safety data sheets (SDSs) to identify Cr(VI)-containing materials that are present in the workplace. Also, remember Cr(VI) can be formed when performing “hot work” such as welding on stainless steel, melting chromium metal, or heating refractory bricks in kilns.
- Conduct an exposure determination. Employers must determine the 8-hour time-weighted average exposure to Cr(VI) for each employee exposed to Cr(VI). This assessment allows the employer to identify and prevent overexposures; collect exposure data so that proper control methods can be selected; and evaluate the effectiveness of those methods. An accurate exposure determination also provides important information concerning occupational Cr(VI) exposures to the physician or other licensed health care professional who performs medical examinations on employees.
- Notify employees of exposure determination results. Within 15 days, employers must provide written notification to affected employees of the results of the exposure determination (or post the results in a common area). Additionally, if the exposure determination indicates exposures exceeding the PEL, the employer notification must describe control measures being used to reduce exposures to levels at or below the PEL.
- Establish a regulated area. Employers must establish regulated areas wherever an employee’s exposure to Cr(VI) is, or can reasonably be expected to be, in excess of the PEL.
- Limit eight-hour time-weighted average hexavalent chromium exposure in the workplace to 5 micrograms or less per cubic meter of air. Engineering and work practice controls should be the primary control methods. When these controls are not sufficient, then employers must provide and ensure employees wear personal protective equipment, such as respiratory protection.
- Perform periodic monitoring. Employers can choose between two options for monitoring: either a scheduled monitoring option based on minimum OSHA requirements (e.g., every 3 months if exposures are above the PEL) or a performance-oriented option.
- Implement good personal hygiene and housekeeping practices to prevent hexavalent chromium exposure.
- Provide medical examinations to employees within 30 days of initial assignment, annually, to those exposed in an emergency situation, to those who experience signs or symptoms of adverse health effects associated with hexavalent chromium exposure, to those who are or may be exposed at or above the action level for 30 or more days a year, and at termination of employment.
- Train employees. In addition to the general training under the hazard communication standard, employers must also train employees exposed to hexavalent chromium on the contents of the Chromium (VI) standard, 1910.1026.
- Provide changing rooms and washing facilities.
- Maintain accurate records. This includes records of air monitoring, medical examination, and exposure records.
Training action plan
It is critically important that workers recognize the hazards associated with exposure to Cr(VI) and understand the measures they can take to protect themselves. OSHA’s Hazard Communication standard (29 CFR 1910.1200) establishes requirements for employers to provide workers with information on hazardous chemicals such as Cr(VI) through comprehensive chemical hazard communication programs that include SDSs, labels, and worker training. Employers must follow the requirements of the Hazard Communication standard with regard to workers exposed to Cr(VI).
- Provide details of the organization’s written hazard communication program. Employers must have a written hazard communication program that describes the labeling system, SDSs, and how employees receive training.
- The written hazard communication program must also include a list of the hazardous chemicals known to be present in the workplace.
- Employees must have access to SDSs and the written hazard communication program.
- Explain the requirements of OSHA’s Cr(VI) standard. OSHA requires employers to limit employee exposure to Cr(VI) to a specified permissible limit. OSHA also requires the employer to perform periodic monitoring, provide PPE, make medical examinations available to employees, train employees, observe proper housekeeping and hygiene practices, and keep exposure and medical records.
- Inform workers of operations where Cr(VI) is present. Cr(VI) is widely used in pigments, metal finishing (electroplating), wood preservatives and fungicides, and in chemical synthesis as an ingredient and catalyst. Hexavalent chromium may also be present in fumes generated during the production or welding of chrome alloys. Chromium metal is often alloyed with other metals or plated on metal and plastic substrates to improve corrosion resistance and provide protective coatings. The steel industry is a major consumer of chromium metal in the production of stainless steel. Examples of Cr(VI) compounds include:
- Ammonium dichromate;
- Calcium chromate;
- Chromium trioxide or chromic acid;
- Lead chromate;
- Potassium chromate;
- Potassium dichromate;
- Sodium chromate;
- Strontium chromate; and
- Zinc chromate.
- Explain the hazards of Cr(VI). The major health effects associated with exposure to Cr(VI) include lung cancer, asthma, nasal septum ulcerations and perforations, skin ulcerations, and allergic and irritant contact dermatitis.
- Breathing in high levels of Cr(VI) can cause irritation to the nose and throat. Symptoms may include runny nose, sneezing, coughing, itching, and a burning sensation. Repeated or prolonged exposure can cause sores to develop in the nose and result in nosebleeds. If the damage is severe, the nasal septum (a “wall” separating the nasal passages) develops a hole in it (perforation).
- Breathing small amounts of Cr(VI) even for long periods does not cause respiratory tract irritation in most people. Some employees become allergic to Cr(VI) so that inhaling chromate compounds can cause asthma symptoms such as wheezing and shortness of breath.
- Some employees can also develop an allergic skin reaction, called allergic contact dermatitis. This occurs from handling liquids or solids containing Cr(VI). Once an employee becomes allergic, brief skin contact causes swelling and a red, itchy rash that becomes crusty and thickened with prolonged exposure. Allergic contact dermatitis is long-lasting and more severe with repeated skin contact.
- Direct skin contact with Cr(VI) can cause a non-allergic skin irritation. Contact with non-intact skin can also lead to chrome ulcers. These are small crusted skin sores with a rounded border. They heal slowly and leave scars.
- Describe how employees can be exposed to Cr(VI). Employees can inhale airborne hexavalent chromium as a dust, fume or mist while:
- Producing chromate pigments and powders, chromic acid, chromium catalysts, dyes, and coatings;
- Working near chrome electroplating ;
- Welding and hot-working stainless steel, high chrome alloys and chrome-coated metal; and
- Applying and removing chromate-containing paints and other surface coatings.
Note: Skin exposure can occur during direct handling of hexavalent chromium-containing solutions, coatings, and cements.
- Describe the monitoring and exposure determination process at the company. Employees must be notified of hexavalent chromium exposure determinations.
- Describe control measures employees can take to protect themselves. OSHA sets exposure limits for airborne concentration of Cr(VI). Exposures to Cr(VI) can be reduced or eliminated through the use of engineering and work practice controls. If these control measures don’t reduce exposures to, or below, OSHA’s permissible exposure limit, employees must wear respirators. When eye or skin contact with Cr(VI) is possible, employees must use personal protective equipment.
- Describe to employees appropriate work practices, emergency procedures, and protective equipment to be used.
- Describe the medical surveillance program. The purpose of medical surveillance is to determine if an individual can be exposed to Cr(VI) at his or her workplace without experiencing adverse health effects; to identify Cr(VI)-related adverse health effects when they do occur so that appropriate intervention measures can be taken; and to determine a worker’s fitness to use personal protective equipment such as respirators. All medical examinations and procedures required by the standards must be performed by or under the supervision of a physician or other licensed healthcare professional (PLHCP). When medical surveillance is required it must be provided at no cost to workers and at a reasonable time and place. If participation requires travel away from the worksite, the employer must bear the cost. Workers must be paid for time spent taking medical examinations, including travel time.
- Make a copy of OSHA’s Cr(VI) standard available to employees.
Checklist
Review these hexavalent chromium checklists.
General
- Are employees aware of the hazards involved with Cr(VI) if they may be exposed to it in their work environment?
Training
- Have you instituted a training program for all employees who are subject to Cr(VI) exposure?
Monitoring
- Is employee exposure monitored and kept within acceptable levels?
- Are engineering and work practice controls used to reduce exposures to a permissible level?
Employee protection
- Is personal protective equipment (PPE) provided and are all employees required to use PPE as needed?
- Is PPE functional and in good repair?
- Do employees wash appropriately after working with Cr(VI)?
- Are employees provided appropriate change rooms and showers?
- Are employees prohibited from taking contaminated items from work area?
Respiratory protection
- Is a respiratory protection program in place?
- Are employees provided proper respiratory protection?
Emergency situations
- Are procedures in place for dealing with emergency situations?
Medical surveillance
- Is a medical surveillance program in place for employees who may be exposed to Cr(VI)?
- Have employees working with this substance been given appropriate medical examinations?
Marking and labeling
- Are caution labels and signs used to warn of this substance?
- Has a regulated area been established, and marked, where appropriate?
- Are containers used to store this substance marked appropriately?
Recordkeeping
- Are appropriate records maintained (exposure monitoring, medical surveillance, etc.)?
- Are employees given access to their exposure and medical records upon request?
Hazard communication
- Do you have a safety data sheet for every hazardous chemical you have at your facility?
- Do you maintain a written hazard communication program?
- Have you compiled a hazardous chemical inventory?
- Have you documented the employee training that you have done under the hazard communication standard?
- Are all chemical containers marked with contents name and hazards?
Ventilation
- Are ventilation systems used where appropriate?
Housekeeping
- Are all work areas clean, sanitary, orderly and adequately illuminated?
- Are adequate cleaning methods used (e.g., HEPA-filter vacuuming)?
- Are contaminated materials disposed of properly?
Isocyanates
Isocyanates are a family of highly reactive, low molecular weight chemicals. They are widely used in the manufacture of flexible and rigid foams, fibers, coatings such as paints and varnishes, and elastomers, and are increasingly used in the automobile industry, autobody repair, and building insulation materials. Spray-on polyurethane products containing isocyanates have been developed for a wide range of retail, commercial, and industrial uses to protect cement, wood, fiberglass, steel and aluminum, including protective coatings for truck beds, trailers, boats, foundations, and decks.
Isocyanates are powerful irritants to the mucous membranes of the eyes and gastrointestinal and respiratory tracts. Direct skin contact can also cause marked inflammation. Isocyanates can also sensitize workers, making them subject to severe asthma attacks if they are exposed again. There is evidence that both respiratory and dermal exposures can lead to sensitization. Death from severe asthma in some sensitized subjects has been reported. Workers potentially exposed to isocyanates who experience persistent or recurring eye irritation, nasal congestion, dry or sore throat, cold-like symptoms, cough, shortness of breath, wheezing, or chest tightness should see a physician knowledgeable in work-related health problems.
The most widely used compounds are diisocyanates, which contain two isocyanate groups, and polyisocyanates, which are usually derived from diisocyanates and may contain several isocyanate groups. The most commonly used diisocyanates include methylenebis(phenyl isocyanate) (MDI), toluene diisocyanate (TDI), and hexamethylene diisocyanate (HDI). Other common diisocyanates include naphthalene diisocyanate (NDI), methylene bis-cyclohexylisocyanate (HMDI)(hydrogenated MDI), and isophorone diisocyanate (IPDI). Examples of widely used polyisocyanates include HDI biuret and HDI isocyanurate.
Action steps
- Determine if your operations expose workers to isocyantes. Review the chemical inventory and safety data sheets (SDSs).
- Determine if your current controls are adequate, e.g., determine current exposure concentrations and compare them to recommended limits; and review injury/illness records for signs of respiratory illness, asthma, and other lung problems.
- Implement appropriate controls to prevent exposure. Preventing exposure to isocyanates is a critical step in eliminating the health hazard. Engineering controls such as closed systems and ventilation should be the principal method for minimizing isocyanate exposure in the workplace. Other controls, such as worker isolation and use of personal protective equipment such as respirators and personal protective clothing to prevent dermal exposures may also be necessary. Early recognition of sensitization and prompt and strict elimination of exposures is essential to reduce the risk of long-term or permanent respiratory problems for workers who have become sensitized.
- Consider alternatives to isocyanates.
- Conduct a PPE hazard assessment, and implement a respiratory protection program if respirators are to be used. Provide and ensure the use of the appropriate gloves (e.g., butyl, nitrile), goggles, and protective clothing when a potential for eye or dermal exposure exists (e.g., exposure to contaminated equipment, chemical containers, etc.)
- Implement good housekeeping procedures. Periodically check for surface contamination (e.g., visible foam/coating) on surfaces, tools and equipment near the operation using isocyanates as well as in places where contamination may not be expected such as drinking fountains, telephones, locker rooms, and lunchrooms, to identify potential sources of dermal exposure and evaluate housekeeping and PPE deficiencies.
- Monitor employee exposures on a regular basis.
- Provide separate lockers for work clothes and street clothes.
- Do not allow workers to eat, drink, apply cosmetics, or use tobacco products in work areas.
- Prohibit workers from leaving the workplace wearing protective work clothing or equipment or taking it home to launder.
- Ensure workers wash face, hands, and forearms before eating, drinking, smoking, or applying cosmetics.
- Ensure workers shower at the end of work shifts.
- Ensure workers immediately and thoroughly wash off skin with soap and flowing water if dermal contact occurs.
- Implement a medical surveillance program.
Training action plan
It is critically important that workers recognize the hazards associated with exposure to isocyanates. Employers should implement a comprehensive training program on hazard identification and safe work practices, including:
- Provide details of the organization’s written hazard communication program. Employers must have a written hazard communication program that describes the labeling system, SDSs, and how employees receive training.
- The written hazard communication program must also include a list of the hazardous chemicals known to be present in the workplace.
- Employees must have access to SDSs and the written hazard communication program.
- Inform workers where work areas may contain isocyanates.
- Inform workers on the signs and symptoms of isocyanate exposure. Workers should seek medical attention if they notice any signs or symptoms.
- Teach employees of the importance of avoiding dermal contact when working with isocyanates.
- Instruct employees on the engineering controls being used to reduce exposures.
- Train employees on the use of appropriate PPE, including respirators and skin protections, and on the limitation of that equipment.
- Explain the workplace monitoring program.
Checklists
Review these isocyanates checklists to ensure safety and compliance at your facilty.
General
- Are employees aware of the hazards involved with isocyanates if they may be exposed to it in their work environment?
Training
- Have you instituted a training program for all employees who are subject to isocyanates exposure?
Monitoring
- Is employee exposure monitored and kept within acceptable levels?
- Are engineering and work practice controls used to reduce exposures to a permissible level?
Employee protection
- Is personal protective equipment (PPE) provided and are all employees required to use PPE as needed?
- Is PPE functional and in good repair?
- Do employees wash appropriately after working with isocyanates?
- Are employees provided appropriate change rooms and showers?
- Are employees prohibited from taking contaminated items from work area?
Respiratory protection
- Is a respiratory protection program in place?
- Are employees provided proper respiratory protection?
Emergency situations
- Are procedures in place for dealing with emergency situations?
Medical surveillance
- Is a medical surveillance program in place for employees who may be exposed?
- Have employees working with this substance been given appropriate medical examinations?
Marking and labeling
- Are caution labels and signs used to warn of this substance?
- Has a regulated area been established, and marked, where appropriate?
- Are containers used to store this substance marked appropriately?
Recordkeeping
- Are appropriate records maintained (exposure monitoring, medical surveillance, etc.)?
- Are employees given access to their exposure and medical records upon request?
Hazard communication
- Do you have a safety data sheet for every hazardous chemical you have at your facility?
- Do you maintain a written hazard communication program?
- Have you compiled a hazardous chemical inventory?
- Have you documented the employee training that you have done under the hazard communication standard?
- Are all chemical containers marked with contents name and hazards?
Ventilation
- Are ventilation systems used where appropriate?
Housekeeping
- Are all work areas clean, sanitary, orderly and adequately illuminated?
- Are adequate cleaning methods used (e.g., HEPA-filter vacuuming)?
- Are contaminated materials disposed of properly?
Lead
Lead can be toxic when absorbed by the body through inhalation or ingestion. OSHA regulates an employee’s exposure to lead in order to prevent the absorption of harmful levels of lead. When the employee’s exposure exceeds 50 mg/m3 averaged over an 8-hour period, the area must be regulated for lead exposure.
Action steps
- Monitor employee exposures to lead and determine if any employee may be exposed to lead at concentrations greater than 50 mg/m3 of air during an 8-hour period.
- Establish and implement a written compliance program to reduce exposures at or below the permissible exposure limit (PEL), and interim levels if applicable, solely by means of engineering and work practice controls.
- Provide exposed employees with respirators and train according to 1910.134.
- Provide exposed employees with protective work clothing and equipment.
- Establish cleaning, laundering, or disposal procedures for contaminated protective clothing and equipment.
- Where employees are exposed to lead above the PEL, do not allow the presence or consumption of food or beverages, tobacco products, or the application of cosmetics.
- Provide separate change rooms, shower facilities, and lunchrooms.
- Post warning signs in each area where the PEL is exceeded.
- Institute a medical surveillance program for affected employees.
- Establish and maintain an accurate record for each employee subject to medical surveillance.
- Provide the physician conducting a medical examination or consultation with the information required in the Lead standard and furnish the employee with a copy of the written medical opinion.
- Establish a training program for all affected employees. Provide the training prior to the initial job assignment and at least annually thereafter.
- If ventilation is used to control lead exposure, take measurements at least every three months which demonstrate the effectiveness of the system in controlling exposure. Additionally, take measurements when there is a change in production, process, or control which could alter the lead level within 5 days of the change.
- If administrative controls are used to control lead exposure, implement a job rotation schedule.
Training action plan
You have to provide training for all employees who have lead exposures at or above the PEL. The training must be provided prior to the initial job assignment and then repeated at least annually. Make sure that each employee is informed of the following during training:
- Content of OSHA’s Lead standard at 1910.1025 and its Appendices A, B, C, and D; Specific nature of the operations which could result in exposure to lead above the action level;
- Purpose, proper selection, fitting, use, and limitations of respirators;
- Purpose and a description of the:
- Medical surveillance program; and
- Medical removal protection program, including information concerning the adverse health effects associated with excessive exposure to lead (with particular attention to the adverse reproductive effects on both males and females).
- Engineering controls and work practices associated with the employee’s job assignment;
- Contents of any compliance plan in effect; and
- Instructions to employees that chelating agents should not: routinely be used to remove lead from their bodies, and be used at all except under the direction of a licensed physician.
Include as part of your training and distribute to employees any materials made available to your facility by OSHA that pertain to the:
- Occupational Safety and Health Act, and
- Regulations issued pursuant to that Act and the Lead standard.
Make a copy of the Lead standard and its appendices available to all affected employees.
Provide, upon request, all materials relating to the employee information and training program to OSHA officials.
Documentation
Retain exposure monitoring records and medical surveillance and other medical records for at least 40 years or for the duration of employment plus 20 years, whichever is longer. Retain medical removal records for at least the duration of an employee’s employment.
Checklist
Use this checklist to ensure shop work safety:
- Is the work bench ventilated?
- Is there local exhaust ventilation on the torch?
- Are workers trained to decontaminate equipment using vacuum, water spray, or mechanical removal such as scraping or brushing in conjunction with local exhaust ventilation?
- Are low volume and high velocity ventilated hand tools provided?
- Are Laminar Flow (supplied air) Islands provided at work stations?
- Are wash-up sinks available for employees in the shop?
- Are surfaces kept free of lead contamination as much as possible?
- Are all shop vacuums equipped with HEPA filters capable of removing lead?
- Are vacuums emptied in a manner that minimizes the reentry of lead into the shop?
- Is there a program for routine ventilation system inspections?
- Does exhaust ventilation use HEPA filters?
- Are defective parts of the ventilation system replaced when identified?
- Are original installation documents, as well as all modifications, problems, and resolutions retained?
Mold
There is currently no specific OSHA standard for mold. However, indoor air quality (IAQ) hazards are addressed in specific standards, such as the 1910.94 ventilation standard. Poor IAQ is one of the most important health issues we face.
Action steps
- Evaluate the workplace for mold or indoor air quality problems.
- Eliminate or control all known and potential sources of microbial contaminants by prompt cleanup and repair of all areas where water collection and leakage has occurred.
- Remove and discard porous organic materials that are contaminated (e.g., damp insulation in ventilation system, moldy ceiling tiles, and mildewed carpets).
- Clean and disinfect nonporous surfaces where microbial growth has occurred with detergents, chlorine-generating slimicides, or other biocides and ensure that these cleaners have been removed before air handling units are turned on.
- Maintain indoor air relative humidity below 60 percent (50 percent where cold surfaces are in contact with room air).
- If ventilation is turned off during weekends or other periods, ensure that contaminant concentrations are sufficiently diluted prior to occupancy.
- Thoroughly evaluate personnel affected with hypersensitivity and controls implemented before returning them to the workplace.
Training action plan
There are no specific OSHA training requirements for mold. However, employees should be trained to report problems or suspected problems related to indoor air quality.
Tips
- There are thousands of species of mold, and the mold can be any color, including white, orange, green, brown, or black.
- Controlling the sources of moisture in a building is the key to preventing indoor mold growth.
- Porous or absorbent materials that become moldy, such as ceiling tiles, wallboard, or carpeting, should be replaced.
- When mold is discovered, communicate with building occupants to alleviate any potential health problems.
Checklist
Review this checklist to prevent mold at your facility:
- Has an evaluation been conducted to identify any mold or indoor air quality problems?
- Are measures taken to eliminate or control all known and potential sources of microbial contaminants by prompt cleanup and repair of all areas where water collection and leakage has occurred?
- Are porous organic materials that are contaminated (e.g., damp insulation in ventilation system, moldy ceiling tiles, and mildewed carpets) removed and discarded?
- Are nonporous surfaces where microbial growth has occurred cleaned and disinfected with detergents, chlorine-generating slimicides, or other biocides?
- Are cleaners and disinfectants used for mold removed before air handling units are turned on?
- Is indoor air relative humidity maintained below 60% (50% where cold surfaces are in contact with room air)?
- Is adequate ventilation in place?
Noise exposure
OSHA’s standard on occupational noise exposure, 1910.95, applies to all employees who are subjected to noise exposures that equal or exceed an 8-hour time-weighted average sound level of 85 decibels.
Action steps
- Administer a continuing, effective hearing conservation program IF employee noise exposures equal or exceed an 8-hour time-weighted average sound level (TWA) of 85 decibels measured on the A scale (slow response); OR equivalently, a dose of fifty percent.
- Institute a training program for all employees who are exposed to noise at or above an 8-hour time-weighted average of 85 decibels, AND ensure employee participation in such program.
- Make copies of 1910.95 available to affected employees or their representatives and also post a copy in the workplace.
- Use feasible administrative or engineering controls where needed.
- Establish and maintain an audiometric testing program by making audiometric testing available to all employees whose exposures equal or exceed an 8-hour time-weighted average of 85 decibels.
- Develop and implement a monitoring program if information indicates that any employee’s exposure may equal or exceed an 8-hour time-weighted average of 85 decibels.
- Maintain an accurate record of all employee exposure measurements required.
- Make hearing protectors available, at no cost, to all employees exposed to an 8-hour time-weighted average of 85 decibels or greater.
- Evaluate hearing protector attenuation for the specific noise environments in which the protector will be used.
Training action plan
You must provide training to all employees who are exposed to noise at or above an 8-hour time-weighted average of 85 decibels.
Employees must be trained prior to initial exposure and annually thereafter.
Generally, content should cover:
- Effects of noise,
- Specific noise hazards at your facility,
- Existing engineering controls,
- Selection procedures of hearing protection, and
- Purpose of and procedures for audiometric testing.
Tips
- There is no cure for noise-induced hearing loss, so prevention is the only way to avoid hearing damage.
- To reduce overall noise in the work area, place noisy machinery in a separate area away from as many workers as possible.
- To estimate employee noise exposures with a sound level meter it is generally necessary to take several measurements at different locations within the workplace.
Checklist
Review these checklists to help with noise exposure at your facility.
General
- Is protection against the effects of occupational noise exposure provided when sound levels exceed those of the OSHA noise standard?
- Do workplace noise levels conform to government standards?
- Are workers protected from sources of excessive noise?
- Have engineering controls been used to reduce excessive noise levels?
- Where engineering controls aren’t feasible, are administrative controls (that is, worker rotation) being used to minimize individual employee exposure to noise?
- Have you tried isolating noisy machinery from the rest of your operation?
Program
- Is there an ongoing, preventive health program to educate employees in:
- Safe levels of noise exposures,
- Effects of noise on their health, and
- The use of personal protection?
Posting
- Have work areas where noise levels make voice communication between employees difficult been identified and posted?
Monitoring
- Are noise levels being measured using a sound level meter or an octave band analyzer and are records being kept?
Personal protective equipment
- Is approved hearing protective equipment (noise attenuating devices) available to every employee working in noisy areas?
- If you use ear protectors, are employees properly fitted and instructed in their use?
Medical
- Are employees in high noise areas given periodic audiometric testing to ensure that you have an effective hearing protection system?
Pandemics
When a pandemic strikes, employers and safety professionals must be prepared. While you can’t plan for every virus that will emerge, you can create a flexible infectious disease preparedness plan.
A pandemic is a global disease outbreak. An influenza pandemic occurs when a new influenza virus emerges for which there is little or no immunity in the human population; begins to cause serious illness; and then spreads easily person-to-person worldwide. A worldwide influenza pandemic could have a major effect on the global economy, including travel, trade, tourism, food, consumption and eventually, investment and financial markets. Planning for pandemic influenza by business and industry is essential to minimize a pandemic’s impact. It is difficult to predict when the next influenza pandemic will occur or how severe it will be.
Wherever and whenever a pandemic starts, everyone around the world is at risk. Countries might, through measures such as border closures and travel restrictions, delay arrival of the virus, but cannot stop it. During a pandemic, transmission can be anticipated in the workplace, not only from patient to workers in health care settings, but also among co-workers in general work settings. A pandemic would cause high levels of illness, death, social disruption, and economic loss. Everyday life would be disrupted because so many people in so many places become seriously ill at the same time. Impacts could range from school and business closings to the interruption of basic services such as public transportation and food delivery. Education and outreach are critical to preparing for a pandemic.
Understanding what a pandemic is, what needs to be done at all levels to prepare for pandemic influenza, and what could happen during a pandemic helps us make informed decisions both as individuals and as a nation.
Action steps
- Identify a pandemic coordinator and/or team with defined roles and responsibilities for preparedness and response planning.
- Identify essential employees and other critical inputs (e.g. raw materials, suppliers, sub-contractor services/ products, and logistics) required to maintain business operations by location and function during a pandemic.
- Train and prepare ancillary workforce (e.g. contractors, employees in other job titles/descriptions, retirees).
- Develop and plan for scenarios likely to result in an increase or decrease in demand for your products and/or services during a pandemic (e.g. effect of restriction on mass gatherings, need for hygiene supplies).
- Determine potential impact of a pandemic on company business financials using multiple possible scenarios that affect different product lines and/or production sites.
- Determine potential impact of a pandemic on business-related domestic and international travel (e.g. quarantines, border closures).
- Find up-to-date, reliable pandemic information from community public health, emergency management, and other sources and make sustainable links.
- Establish an emergency communications plan and revise periodically. This plan includes identification of key contacts (with back-ups), chain of communications (including suppliers and customers), and processes for tracking and communicating business and employee status.
- Implement an exercise/drill to test your plan, and revise periodically.
- Forecast and allow for employee absences during a pandemic due to factors such as personal illness, family member illness, community containment measures and quarantines, school and/or business closures, and public transportation closures.
- Implement guidelines to modify the frequency and type of face-to-face contact (e.g. hand-shaking, seating in meetings, office layout, shared workstations) among employees and between employees and customers (refer to CDC recommendations).
- Encourage and track annual influenza vaccination for employees.
- Evaluate employee access to and availability of healthcare services during a pandemic, and improve services as needed.
- Evaluate employee access to and availability of mental health and social services during a pandemic, including corporate, community, and faith-based resources, and improve services as needed.
- Identify employees and key customers with special needs, and incorporate the requirements of such persons into your preparedness plan.
- Establish policies for employee compensation and sick-leave absences unique to a pandemic (e.g. non-punitive, liberal leave), including policies on when a previously ill person is no longer infectious and can return to work after illness.
- Establish policies for flexible worksite (e.g. telecommuting) and flexible work hours (e.g. staggered shifts).
- Establish policies for preventing influenza spread at the worksite (e.g. promoting respiratory hygiene/ cough etiquette, and prompt exclusion of people with influenza symptoms).
- Establish policies for employees who have been exposed to pandemic influenza, are suspected to be ill, or become ill at the worksite (e.g. infection control response, immediate mandatory sick leave).
- Establish policies for restricting travel to affected geographic areas (consider both domestic and international sites), evacuating employees working in or near an affected area when an outbreak begins, and guidance for employees returning from affected areas (refer to CDC travel recommendations).
- Set up authorities, triggers, and procedures for activating and terminating the company’s response plan, altering business operations (e.g. shutting down operations in affected areas), and transferring business knowledge to key employees.
Training action plan
All employees should be trained on the employer’s exposure control plan.
Training content should cover:
- The epidemiology and symptoms of pandemics.
- How exposures occur.
- The company’s exposure control plan.
- Recognizing potential exposures.
- Engineering controls affecting trainees.
- Location of handwashing facilities.
- Work practices affecting workers.
- General approach and selection process for Personal Protective Equipment (PPE).
- The company’s procedure to respond to a worker who has been exposed.
- Follow-up available to workers involved in an exposure incident.
Documentation
No current training records exist for non-bloodborne pathogens exposures (e.g., respiratory transmittable diseases). However, OSHA does consider work-related cases of these diseases, like tuberculosis, to be recordable if resulting in lost workdays, medical treatment, etc. The Agency requires employers to make a good-faith effort to determine whether or not the case was more likely than not related to an exposure in the workplace.
Tips
- Train workers who may use disinfectants or other chemicals. In a pandemic, even household cleaners can trigger Hazcom requirements if used more frequently than the manufacturer intends.
- Have a plan to shut-down operations, in case this is necessary or mandated. Also have a plan for keeping equipment, like ventilation and heating/cooling systems, working properly. You also should have a plan for conducting maintenance checks on equipment that has been idle for a while due to unexpected shutdown.
Tips
Review these pandemic checklists.
Assessment
- Has the company identified a pandemic coordinator and/or team with defined roles and responsibilities for preparedness and response planning?
- Has the company identified essential employees and other critical inputs (e.g., raw materials, suppliers, sub-contractor services/products, and logistics) required to maintain business operations during a pandemic?
- Has the company determined the potential impact of a pandemic on company business financials using multiple possible scenarios that affect different product lines and/or production sites?
- Has the company determined potential impact of a pandemic on business-related domestic and international travel (e.g., quarantines, border closures)?
Planning
- Is a pandemic plan in place outlining prevention and response measures the company will take?
- Is an emergency communications plan in place and up to date?
- Does the plan include identification of key contacts (with back-ups), chain of communications (including suppliers and customers), and processes for tracking and communicating business and employee status?
- Is the plan tested periodically by exercises/drills?
- Have policies been established for employee compensation and sick-leave absences unique to a pandemic (e.g., non-punitive, liberal leave), including policies on when a previously ill person is no longer infectious and can return to work after illness?
- Are there policies for flexible worksite (e.g., telecom-muting) and flexible work hours (e.g., staggered shifts)?
- Is there a policy for preventing influenza spread at the worksite (e.g., promoting respiratory hygiene/cough etiquette, and prompt exclusion of people with influenza symptoms)?
- Are policies in place for employees who have been exposed to pandemic influenza, are suspected to be ill, or become ill at the worksite (e.g., infection control response, immediate mandatory sick leave)?
- Are policies in place for restricting travel to affected geographic areas (consider both domestic and international sites), evacuating employees working in or near an affected area when an outbreak begins, and guidance for employees returning from affected areas (refer to CDC travel recommendations)?
- Has the company set up authorities, triggers, and procedures for activating and terminating the company’s response plan, altering business operations (e.g., shutting down operations in affected areas), and transferring business knowledge to key employees?
- Have resources been allocated to protect employees and customers during a pandemic (e.g., hand-hygiene products, tissues, and disposal containers)?
Training and communication
- Are employees made aware of the company’s pandemic preparedness and response plan?
- Has the company developed and disseminated programs and materials covering pandemic fundamentals (e.g., signs and symptoms of influenza, modes of transmission), personal and family protection and response strategies (e.g., hand hygiene, coughing/ sneezing etiquette, contingency plans)?
- Is information provided for the at-home care of ill employees and family members?
- Are means (e.g., hotlines, dedicated websites) set up for communicating pandemic status and actions to employees, vendors, suppliers, and customers inside and outside the worksite in a consistent and timely way, including redundancies in the emergency contact system?
- Has training been provided to ancillary workforce (e.g., contractors, employees in other job titles/ descriptions, retirees)?
External organizations
- Does the company collaborate with insurers, health plans, major local healthcare facilities, and local, state, and federal public health agencies to share pandemic plans and understand their capabilities and plans?
Respiratory protection
OSHA’s 1910.134 regulation applies to workers who perform welding, spray painting, grinding, sanding or related processes. Respirators are generally needed to protect employees from harmful dusts, fogs, fumes, mists, gases, smokes, sprays, and vapors when engineering controls, such as containment, ventilation, or the use of a less toxic substance, fail to provide adequate protection.
Action steps
- Identify and evaluate the respiratory hazard(s) in the workplace.
- Develop and implement a written respiratory protection program with required worksite-specific procedures and elements for required respirator use.
- Conduct evaluations of the workplace as necessary to ensure that the provisions of the current written program are being effectively implemented, and that it continues to be effective.
- Select and provide appropriate respirators.
- Train employees on respiratory protection.
- Provide a medical evaluation to determine the employee’s ability to use a respirator.
- Identify a physician or other licensed health care professional (PLHCP) to perform medical evaluations.
- Fit-test employees with the same make, model, style, and size of respirator that will be used.
- Clean and disinfect respirators per OSHA requirements.
- Store all respirators to protect them from damage, contamination, dust, sunlight, extreme temperatures, excessive moisture, and damaging chemicals.
- Use compressed air, compressed oxygen, liquid air, and liquid oxygen for respiration that meets OSHA specifications.
- Retain records of medical evaluations required by 1910.134, AND make them available in accordance with 1910.1020.
- Establish a record of the qualitative and quantitative fit tests administered to an employee.
- Retain fit test records for respirator users until the next fit test is administered.
- Retain a written copy of the current respirator program.
- Provide any retained written materials, upon request, to affected employees and to OSHA or designee for examination and copying.
Training action plan
You must train all employees who are, or may be, exposed to air contaminants above the permissible exposure limits or suggested exposure levels. You should also train employees who use respirators voluntarily or because of company policy.
Training must precede the use of a respirator. Retraining is required to be conducted annually, and whenever necessary to ensure safe use.
Generally, content for respiratory protection training should cover:
- Why the respirator is necessary.
- Type of respirator employees will be using.
- Proper fit, usage, and maintenance.
- Inspecting, putting on, and removal of respirator.
- Use and seal check of the respirator.
- Cleaning, storing, and repairing respirators.
- Responding to emergencies that involve respirator use.
- Recognizing medical signs and symptoms that may limit or prevent the effective use of respirators.
- The respiratory protection regulation.
Tips
- Whenever OSHA standards or employers require respirator use, there must be a complete respiratory protection program—even for N95 respirators. For voluntary use, the actions employers must take are not as substantial.
- Employees need to wear respirators whenever engineering and work practice control measures are not adequate to prevent atmospheric contamination at the worksite.
- A fit test is a method used to select the right size respirator for the user. A user seal check is a method to check to see if the user has correctly put on the respirator and adjusted it to fit properly.
- Dust masks are considered filtering facepieces under the Respiratory Protection standard, and are therefore, a type of respirator.
- Fit testing must be done prior to respirator use, when a different type of respirator is used, and at least annually thereafter.
- The “grimace exercise” is intended to test the respirator’s ability to reseal to the wearer’s face.
Checklist
Review these respiratory protection checklists to ensure safety and compliance at your facility.
Use
- Is the correct type of respirator being worn, where appropriate, by personnel?
- Do you conduct fit testing using the procedures set forth in Appendix A to 1910.134?
- Do individuals who use a tight-fitting respirator perform a user seal check each time the respirator is put on?
Respiratory protection program
- Do you have a written and implemented respiratory protection program with required worksite-specific procedures and elements?
- Has the program been updated as necessary to reflect those changes in workplace conditions that affect respirator use?
- Have you designated a qualified program administrator to oversee and evaluate the respiratory protection program?
Cleaning and inspection
- Are respirators cleaned according to the provisions of Appendix B-2 to 1910.134, or according to the recommendations of the manufacturer?
- Are all respirators used in routine situations inspected before each use, and during cleaning?
- Are all respirators maintained for use in emergency situations inspected at least monthly and in accordance with the manufacturer’s recommendations?
- Are all respirators maintained for use in emergency situations checked for proper function before and after each use?
- Are all emergency escape-only respirators inspected before being carried into the workplace for use?
Repairs
- Are repairs made according to the manufacturer’s recommendations and specifications for the type and extent of repairs to be performed?
Storage
- Are all respirators stored so that they are protected from damage?
Training and information
- Do you provide effective training to employees who are required to use respirators?
- Is the training comprehensive, understandable, and given annually (or more often if necessary)?
- Is the training provided before employees are required to use a respirator in the workplace?
Respirators for IDLH atmospheres
- Are all oxygen-deficient atmospheres considered IDLH?
- Do you provide appropriate respiratory protection for IDLH atmospheres?
Silica
Exposure to respirable crystalline silica can lead to lung cancer, silicosis, chronic obstructive pulmonary disease, and kidney disease in workers. OSHA’s rule on silica exposure requires employers to protect employees.
Action steps
- Survey your operations for potential exposure to silica. Employers can consult their suppliers or examine safety data sheets (SDSs) to identify silica-containing materials that are present in the workplace.
- Measure the amount of silica that workers are exposed to if it may be at or above an action level of 25 μg/m 3 (micrograms of silica per cubic meter of air), averaged over an 8-hour day.
- Protect workers from respirable crystalline silica exposures above the permissible exposure limit of 50 μg/m 3, averaged over an 8-hour day.
- Limit workers’ access to areas where they could be exposed above the PEL.
- Use dust controls to protect workers from silica exposures above the PEL.
- Provide respirators to workers when dust controls cannot limit exposures to the PEL.
- Restrict housekeeping practices that expose workers to silica where feasible alternatives are available.
- Establish and implement a written exposure control plan that identifies tasks that involve exposure and methods used to protect workers.
- Offer medical exams — including chest X-rays and lung function tests — every three years for workers exposed at or above the action level for 30 or more days per year.
- Train workers on work operations that result in silica exposure and ways to limit exposure.
- Keep records of workers’ silica exposure and medical exams.
Training action plan
It is critically important that workers recognize the hazards associated with exposure to silica and understand the measures they can take to protect themselves. OSHA’s Hazard Communication standard (29 CFR 1910.1200) establishes requirements for employers to provide workers with information on hazardous substances through comprehensive hazard communication programs that include SDSs, labels, and worker training. Employers must follow the requirements of the Hazard Communication standard with regard to workers exposed to silica.
- Provide details of the organization’s written hazard communication program. Employers must have a written hazard communication program that describes the labeling system, SDSs, and how employees receive training.
- The written hazard communication program must also include a list of the hazardous chemicals known to be present in the workplace.
- Employees must have access to SDSs and the written hazard communication program.
- Explain the requirements of OSHA’s silica standard.
- Inform workers of operations where silica is present. Exposures to crystalline silica dust occur in common workplace operations involving cutting, sawing, drilling, and crushing of concrete, brick, block, rock, and stone products (such as construction tasks), and operations using sand products (such as in glass manufacturing, foundries, sand blasting, and hydraulic fracturing).
- Explain the hazards of silica. Workers who inhale very small crystalline silica particles are at increased risk of developing serious — and often deadly — silica-related diseases. These tiny particles (known as “respirable” particles) can penetrate deep into workers’ lungs and cause silicosis, an incurable and sometimes fatal lung disease. Crystalline silica exposure also puts workers at risk for developing lung cancer, other potentially debilitating respiratory diseases such as chronic obstructive pulmonary disease, and kidney disease. Approximately 2.3 million people in the U.S. are exposed to silica at work.
- Describe how employees can be exposed to silica. Respirable crystalline silica – very small particles typically at least 100 times smaller than ordinary sand found on beaches or playgrounds – is generated by high-energy operations like cutting, sawing, grinding, drilling and crushing stone, rock, concrete, brick, block and mortar; or when using industrial sand. Activities such as abrasive blasting with sand; sawing brick or concrete; sanding or drilling into concrete walls; grinding mortar; manufacturing brick, concrete blocks, or ceramic products; and cutting or crushing stone generates respirable dust.
- Describe the monitoring and exposure determination process at the company. Employees must be notified of silica exposure determinations.
- Describe control measures employees can take to protect themselves. Employers must use engineering and work practice controls to reduce and maintain employee exposure to respirable crystalline silica to or below the PEL, unless the employer can demonstrate that such controls are not feasible. Wherever such feasible engineering and work practice controls are not sufficient to reduce employee exposure to or below the PEL, the employer must nonetheless use them to reduce employee exposure to the lowest feasible level and shall supplement them with the use of respiratory protection. Employees must use respiratory protection when it has been deemed necessary. Employees should also use proper housekeeping procedures, comply with medical surveillance requirements, observe warning/caution signs, and be aware of their rights to review the employer’s program.
- Describe the medical surveillance program. The purpose of medical surveillance is to identify adverse health effects associated with respirable crystalline silica exposure so that appropriate actions can be taken; determine if an employee has any condition, such as a lung disease, that might make him or her more sensitive to respirable crystalline silica exposure; and determine the employee’s fitness to use respirators.
- In response to the information gained through medical surveillance, employees can take actions to improve their health, such as making job choices to reduce exposures, wearing a respirator for extra protection, or making personal lifestyle or health decisions, such as quitting smoking or getting flu shots.
- Make a copy of OSHA’s silica standard available to employees.
Checklist
Review these silica checklists to ensure safety and compliance at your facility.
General
- Are employees aware of the hazards involved with silica if they may be exposed to it in their work environment?
- Is a written exposure control plan implemented?
Training
- Have you instituted a training program for all employees who are subject to silica exposure?
Monitoring
- Is employee exposure monitored and kept within acceptable levels?
- Are engineering and work practice controls used to reduce exposures to a permissible level?
Employee protection
- Are engineering controls used where feasible?
- Is personal protective equipment (PPE) provided and are all employees required to use PPE as needed?
- Is PPE functional and in good repair?
Respiratory protection
- Is a respiratory protection program in place?
- Are employees provided proper respiratory protection?
Medical surveillance
- Is a medical surveillance program in place for employees who may be exposed to silica?
Marking and labeling
- Are caution labels and signs used to warn of silica presence and hazards?
- Has a regulated area been established, and marked, where appropriate?
- Are containers used to store this substance marked appropriately?
Recordkeeping
- Are appropriate records maintained (exposure monitoring, medical surveillance, etc.)?
- Are employees given access to their exposure and medical records upon request?
Hazard communication
- Do you have a safety data sheet for every hazardous chemical you have at your facility?
- Do you maintain a written hazard communication program?
- Have you compiled a hazardous chemical inventory?
- Have you documented the employee training that you have done under the hazard communication standard?
- Are all chemical containers marked with contents name and hazards?
Ventilation
- Are ventilation systems used where appropriate?
Housekeeping
- Are all work areas clean, sanitary, orderly and adequately illuminated?
- Are adequate cleaning methods used (e.g., wet sweeping or HEPA-filter vacuuming)?
- Are contaminated materials disposed of properly?
Prioritizing risks and implementing controls
- Employers must evaluate the hazards found in the workplace and prioritize them so those with the greatest risk (in severity, high likelihood of occurrence, or both) are addressed first.
- A hazard control plan identifies workplace hazards and describes steps that will be taken to prevent and control them. Once a plan is in place, it must be implemented, evaluated for effectiveness, and updated as needed.
Employers must assess and understand the hazards identified and the types of incidents that could result from worker exposure to those hazards. This information can be used to develop interim controls and to prioritize hazards for permanent control. Employers will need to:
- Evaluate each hazard by considering the severity of potential outcomes, the likelihood that an event or exposure will occur, and the number of workers who might be exposed.
- Use interim control measures to protect workers until more permanent solutions can be implemented.
- Prioritize the hazards so that those presenting the greatest risk are addressed first. Note, however, that employers have an ongoing obligation to control all serious recognized hazards and to protect workers.
Developing and updating a hazard control plan
A hazard control plan describes the steps that will be taken to prevent and control the hazards identified. An effective plan will address serious hazards first. Interim controls may be necessary, but the overall goal is to ensure effective long-term hazard control. Employers should track progress toward completing the control plan and periodically verify that controls remain effective. This may include:
- Listing the hazards needing controls in order of priority.
- Assigning responsibility for installing or implementing the controls to a specific person or persons with the power or ability to implement the controls.
- Establishing a target completion date.
- Planning how to track progress toward completion.
- Planning how to verify the effectiveness of controls after they are installed or implemented.
Implementing selected controls
Once hazard prevention and control measures have been identified, they should be implemented according to the hazard control plan. This will include:
- Implementing hazard control measures according to the priorities established in the hazard control plan.
- When resources are limited, implementing measures on a “worst-first” basis, according to the hazard ranking priorities (risk) established during hazard identification and assessment. Note that, regardless of limited resources, employers have an obligation to protect workers from recognized, serious hazards.
- Promptly implementing any measures that are easy and inexpensive (e.g., general housekeeping, removal of obvious tripping hazards, basic lighting) regardless of the level of hazard they involve.
Risk rating matrix
- When assessing risk, employers must take into account the severity of injury or illness that could result from a hazard, as well as the likelihood of such an incident occurring. Hazards with high severity and high probability of occurring are the greatest risk.
The risk/hazard rating of a job or task usually considers two factors:
- Severity — the seriousness of the injury or illness (e.g., first-aid, minor, lost-time, permanent disability, fatality) that could result from an incident.
- Probability — the likelihood that an incident will occur (e.g., frequently, occasionally, unlikely).
A job or task with a high probability and high severity has the highest risk; when there is low probability and low severity, that is the lowest risk. However, there are numerous combinations of severity/probability in between.
Many companies utilize a risk matrix or table that assigns numeric measures to risk based on probability and severity; the ratings are used to prioritize safety efforts. A sample risk matrix is provided below.
The risk matrix should be tailored to suit each organization’s risk tolerance and should take into account the specific operations, hazards, and available controls.
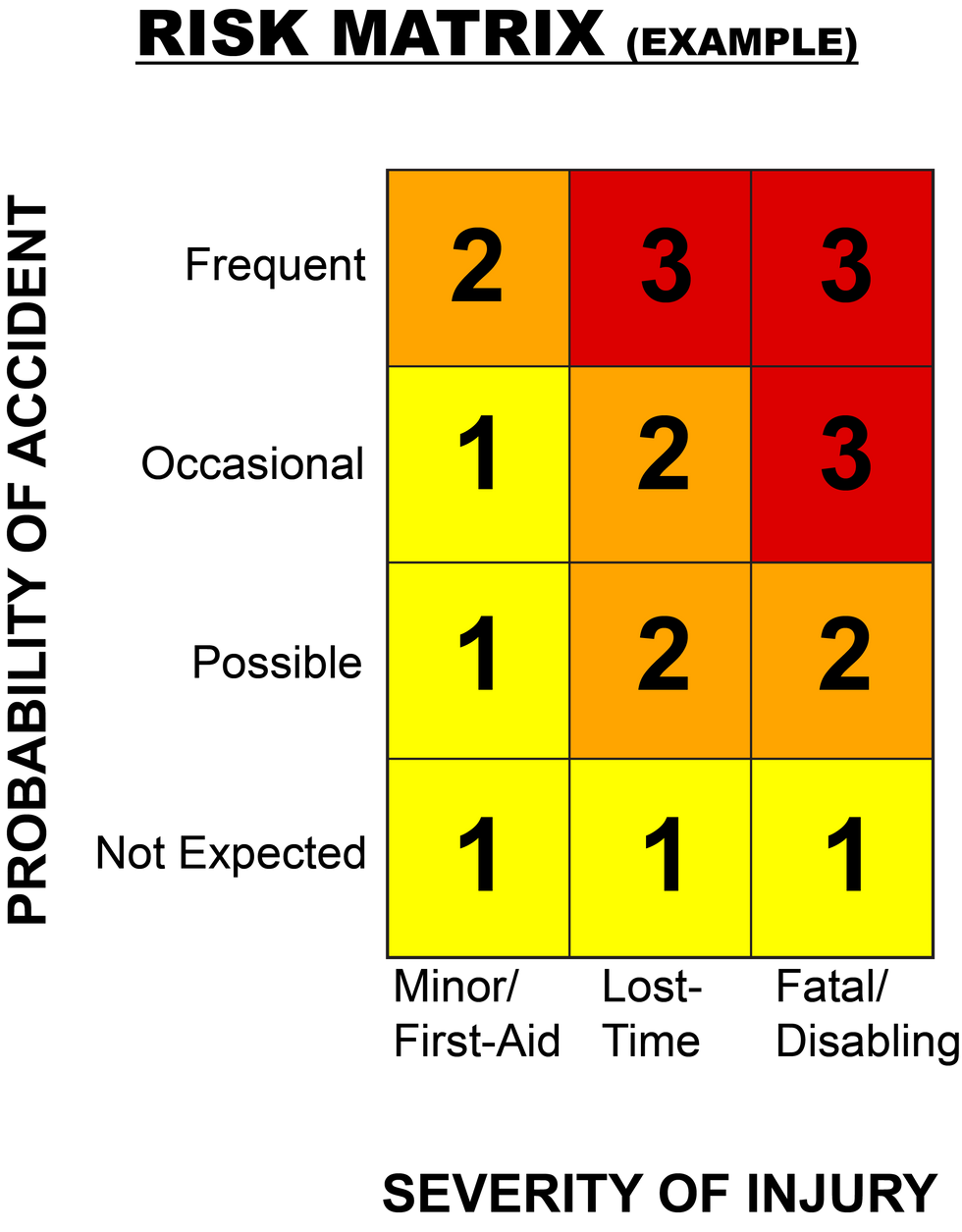
Priority legend
3 Highest priority — stop task until hazards are controlled
2 Hazards must be controlled as soon as possible
1 Risks are acceptable — no further controls required
Using the language of risk
- Safety professionals should learn to communicate safety needs in the workplace in terms of risk management to help business owners and executives understand the full impact of not managing hazards properly.
Imagine a safety professional asking upper management for a $500,000 investment to keep from getting a $7,000 fine from the Occupational Safety and Health Administration (OSHA). The request is unlikely to be approved. Stating the request in terms of risk management, however, would involve explaining an analysis and prioritizing of risk, along with the financial implications.
Risk is a common language between business owners and executives who manage risk every day. Putting hazards into the language of risk helps executives see the need for managing the identified safety risks or hazards.
Financial implications include suffering operational delays, which directly impacts the number of products a company might produce, for example, and could result in direct consequences.
Unfortunately, many safety professionals haven’t had formal training in risk management, so learning the concepts may take some time. However, it doesn’t have to be daunting, and tools are available to help.
Risk management industry standard
- The AASP Risk Management technical report offers expert guidance and tools to help safety professionals understand, assess, and manage risk in the workplace.
A technical report published by the American Society of Safety Professionals (ASSP) provides safety professionals with techniques and implementation strategies to combat risk and better protect workers. ASSP TR-31010-2020 Risk Management – Techniques for Safety Practitioners is designed to assist safety practitioners and company decision-makers in understanding, assessing, and managing risk so organizations can achieve their business objectives.
The technical report provides expert guidance on the selection, modification, combination, and application of 50 risk management techniques to help improve the way risk and uncertainty are managed. It includes basic techniques for industry newcomers and complex methods for seasoned safety professionals. The safety resource explains the fundamentals of risk assessment and risk treatment and covers prevention-through-design practices that are applicable throughout the life cycle of a system. Safety professionals can apply the techniques to a range of occupational settings, situations, and operational stages of a business.
Analysis tools
Examples of some of the 50 tools covered by the ASSP Technical Report include:
- ALARP – Getting to a risk level that is “as low as reasonably practicable” by classifying risks into specific categories.
- Risk Hierarchy – A comprehensive portfolio of risks organized by type.
- Causal Mapping – Identifies causality by mapping interactions between risks.
- Ishikawa (Fishbone) Analysis/Cause and Effect Analysis – A team-based approach using a pictorial display to help consider all possible scenarios and causes of a specific effect.
- Business Impact Analysis – A method to evaluate effects of incidents on critical business operations.
The Technical Report contains a table that provides information on the complexity of each of the 50 tools, along with guidance on how each may or may not apply to different situations a safety professional might encounter. For example, ALARP is a medium complexity tool strongly applicable to determining risk context, as well as for risk evaluation. However, it is not very applicable to risk analysis. On the other hand, Risk Hierarchy is low complexity and strongly applicable to communicating risk, but not as applicable to analysis.
Safety professionals don’t have to learn all 50 tools at once. To start out, the professional should choose about five tools for communicating with the next level manager. As safety professionals make progress and get invited to decision-makers’ meetings, they go back to the Technical Report and learn more. Then, next time, they’re part of the solution. Eventually, as safety professionals get into upper-level safety and start communicating with the CEO, there are tools in the report to help, focusing on enterprise-wide risk management.
Safety management industry standards
- There are two major industry standards to help guide employers in implementing a safety plan for the workplace: ISO 45001 and ANSI Z10.
- In certain industries, suppliers or potential contracts may require companies to implement one standard over the other.
Two major voluntary industry standards can help employers design and implement a safety and health management system:
- ISO 45001 — Occupational health and safety management systems – Requirements with guidance for use
- ANSI/ASSP Z10 — Occupational Health and Safety Management Systems
ISO 45001
The International Organization for Standardization (ISO) 45001 Occupational health and safety management systems — Requirements with guidance for use is a standard for the implementation and maintenance of occupational safety and health management systems. The standard guides companies in taking a systematic and proactive approach to worker safety, giving safety an equal “seat at the table” alongside other management systems such as environmental, quality, IT and data security, and product safety, all of which have had international standards for a while.
Like other management systems standards, ISO 45001 reduces risk and increases performance. In the case of ISO 45001, the risk is to worker safety and health. The standard provides a framework to systematically improve safety and business processes at the same time. It requires using concepts and techniques such as the hierarchy of controls, risk assessment, and root-cause analysis, along with significant input and participation from workers. While these techniques help reduce injuries and illnesses, they also improve business performance.
The indirect benefits of obtaining certification include recognition for achieving an international benchmark, lowering costs, reducing turnover and lost time, and reducing equipment and process downtime. The standard has other benefits as well. Investors will likely feel more confident in an ISO 45001-certified company because the company has shown it is actually identifying and managing the risks.
To achieve the maximum benefits and to claim official certification, a company must go through a third-party audit and approval process from an accredited registrar. Completing full certification is certainly no easy task. If a company already has an ISO management system in place, however, the transition will be less complicated.
For companies that want to implement a management system but are not interested in certification, the ISO 45001 standard can be used as a best-practice guidance. A company can purchase the standard and self-implement to whatever degree is appropriate, understanding that internal impacts (such as fewer injuries and better performance) may be seen, but external benefits (such as recognition) will not be gained without certification.
ANSI Z10
The American National Standards Institute (ANSI) Z10 Occupational Health and Safety Management Systems standard was originally released in 2005. Like most other ANSI standards, ANSI Z10 is “self-certifying” in that there is not necessarily a requirement for a third-party auditor to conduct a conformance assessment. A company can purchase the standard and implement it with no assistance from a third party.
The ANSI standard follows the same general principles as the Occupational Safety and Health Administration (OSHA)’s Recommended Practices, but provides much more guidance and many tools, covering such topics as management leadership, employee involvement, hazard identification/prevention/control, training, and evaluation. It contains tools such as job hazard analysis guidance and risk matrices.
Deciding on a standard
In choosing a standard, a company should consider what the organization hopes to accomplish and also what the stakeholders or customers are asking for. Some companies may choose to achieve certification to ISO 45001, but implement additional elements from ANSI Z10.
In certain industries, suppliers or potential contracts may ask for one standard over the other. Employers should talk with some organizations that have used these systems to find out pros and cons of each.
Hazard identification and assessment
- To properly assess the risks posed by hazards, employers first need to identify all potential hazards.
- Employers should include assessments of emergency and non-routine situations that may arise.
“Risk” is the product of hazard and exposure. Thus, risk can be reduced by controlling or eliminating the hazard or by reducing workers’ exposure to hazards. An assessment of risk helps employers understand hazards in the context of their own workplaces and prioritize hazards for permanent control.
One of the root causes of workplace injuries, illnesses, and incidents is the failure to identify or recognize hazards that are present, or that could have been anticipated. A critical element of any effective safety and health program is a proactive, ongoing process to identify and assess such hazards.
To identify and assess hazards, employers and workers should:
- Collect and review information about the hazards present or likely to be present in the workplace.
- Conduct initial and periodic workplace inspections of the workplace to identify new or recurring hazards.
- Investigate injuries, illnesses, incidents, and close calls/near misses to determine the underlying hazards, their causes, and safety and health program shortcomings.
- Group similar incidents and identify trends in injuries, illnesses, and hazards reported.
- Consider hazards associated with emergency or non-routine situations.
- Determine the severity and likelihood of incidents that could result for each hazard identified, and use this information to prioritize corrective actions.
Some hazards, such as housekeeping and tripping hazards, can and should be fixed as they are found. Fixing hazards on the spot emphasizes the importance of safety and health and takes advantage of a safety leadership opportunity.
Emergency and non-routine situations
Emergencies present hazards that need to be recognized and understood. Non-routine or infrequent tasks, including maintenance and startup/shutdown activities, also present potential hazards. Develop plans and procedures for responding appropriately and safely to hazards associated with foreseeable emergency scenarios and non-routine situations.
Identify foreseeable emergency scenarios and non-routine tasks, taking into account the types of material and equipment in use and the location within the facility. Scenarios such as the following may be foreseeable:
- Fires and explosions;
- Chemical releases;
- Hazardous material spills;
- Startups after planned or unplanned equipment shutdowns;
- Non-routine tasks, such as infrequently performed maintenance activities;
- Structural collapse;
- Disease outbreaks;
- Weather emergencies and natural disasters;
- Medical emergencies; and
- Workplace violence.
Gathering information and performing inspections
- Employers may already have internal and external data available to help with identifying hazards, including equipment operating manuals, Safety Data Sheets, inspection reports, records of previous illness/injury, and more.
- Employers must arrange for regular safety inspections, as well as inspections whenever working conditions (work processes, equipment, etc.) change. A follow-up plan is needed to ensure any safety issues found are corrected.
Information on hazards may already be available to employers and workers, from both internal and external sources.
Employers should collect, organize, and review information with workers to determine what types of hazards may be present and to which workers may be exposed or potentially exposed. Information available may include:
- Equipment and machinery operating manuals.
- Safety Data Sheets (SDS) provided by chemical manufacturers.
- Self-inspection reports and inspection reports from insurance carriers, government agencies, and consultants.
- Records of previous injuries and illnesses, such as Occupational Safety and Health Administration (OSHA) 300 and 301 logs and reports of incident investigations.
- Workers’ compensation records and reports.
- Patterns of frequently-occurring injuries and illnesses.
- Exposure monitoring results, industrial hygiene assessments, and medical records (appropriately redacted to ensure patient/worker privacy).
- Existing safety and health programs (lockout/tagout, confined spaces, process safety management, personal protective equipment, etc.).
- Input from workers, including surveys or minutes from safety and health committee meetings.
- Results of job hazard analyses, also known as job safety analyses.
Information about hazards may also be available from outside sources such as:
- Occupational Safety and Health Administration (OSHA), National Institute for Occupational Safety and Health (NIOSH), and Centers for Disease Control and Prevention (CDC) websites, publications, and alerts.
- Trade associations.
- Labor unions, state and local occupational safety and health committees/coalitions (“COSH groups”), and worker advocacy groups.
- Safety and health consultants.
Inspecting the workplace for safety hazards
Hazards can be introduced over time as workstations and processes change, equipment or tools become worn, maintenance is neglected, or housekeeping practices decline. Setting aside time to regularly inspect the workplace for hazards can help identify shortcomings so that they can be addressed before an incident occurs. Employers should:
- Conduct regular inspections of all operations, equipment, work areas and facilities. Have workers participate on the inspection team and talk to them about hazards that they see or report.
- Document inspections to later verify that hazardous conditions are corrected. Take photos or video of problem areas to facilitate later discussion and brainstorming about how to control them, and for use as learning aids.
- Include all areas and activities in these inspections, such as storage and warehousing, facility and equipment maintenance, purchasing and office functions, and the activities of on-site contractors, subcontractors, and temporary employees.
- Regularly inspect both plant vehicles (e.g., forklifts, powered industrial trucks) and transportation vehicles (e.g., cars, trucks).
- Use checklists that highlight things to look for. Typical hazards fall into several major categories, such as those listed below, although each workplace will have its own list:
- General housekeeping;
- Slip, trip, and fall hazards;
- Electrical hazards;
- Equipment operation;
- Equipment maintenance;
- Fire protection;
- Work organization and process flow (including staffing and scheduling);
- Work practices;
- Workplace violence;
- Ergonomic problems; and
- Lack of emergency procedures.
Employers should also plan to do safety inspections before changing operations, workstations, or workflow; making major organizational changes; or introducing new equipment, materials, or processes, seeking the input of workers and evaluating the planned changes for potential hazards and related risks.
Many hazards can be identified using common knowledge and available tools. For example, workers can easily identify or remove hazards such as broken stair rails or frayed electrical cords. Workers can be a very useful internal resource, especially if they are trained in how to identify and assess risks.
Identifying health hazards
- Health hazards that may be identified might be chemical, physical, biological, or ergonomic.
- In some cases, identifying such hazards may require specialized knowledge; small businesses can often obtain this help for free through OSHA’s On-Site Consultation Program.
Identifying health hazards is typically more complex than identifying physical safety hazards. For example, gases and vapors may be invisible, often have no odor, and may not have an immediately noticeable harmful health effect.
Health hazards include chemical hazards (solvents, adhesives, paints, toxic dusts, etc.); physical hazards (noise, radiation, heat, etc.); biological hazards (infectious diseases); and ergonomic risk factors (heavy lifting, repetitive motions, vibration).
Reviewing workers’ medical records (appropriately redacted to ensure patient/worker privacy) can be useful in identifying health hazards associated with workplace exposures. Employers should:
- Identify chemical hazards — Review Safety Data Sheets (SDSs) and product labels to identify chemicals in the workplace that have low exposure limits, are highly volatile, or are used in large quantities or in unventilated spaces. Identify activities that may result in skin exposure to chemicals.
- Identify physical hazards — Identify any exposures to excessive noise (areas where workers must raise their voices to be heard by others), elevated heat (indoor and outdoor), or sources of radiation (radioactive materials, X-rays, or radiofrequency radiation).
- Identify biological hazards — Determine whether workers may be exposed to sources of infectious diseases, molds, toxic or poisonous plants, or animal materials (fur or scat) capable of causing allergic reactions or occupational asthma.
- Identify ergonomic risk factors — Examine work activities that require heavy lifting, work above shoulder height, repetitive motions, or tasks with significant vibration.
- Conduct quantitative exposure assessments — When possible, using air sampling or direct reading instruments.
- Review medical records — To identify cases of musculoskeletal injuries, skin irritation or dermatitis, hearing loss, or lung disease that may be related to workplace exposures.
Identifying and assessing health hazards may require specialized knowledge. Small businesses can obtain free and confidential occupational safety and health advice services, including help identifying and assessing workplace hazards, through the Occupational Safety and Health Administration (OSHA)’s On-Site Consultation Program.
Conducting incident investigations
- Thoroughly investigating all safety incidents helps an employer to identify where hazards exist in their workplaces.
- Effective incident investigations will not stop when a single cause of an incident is found, but should continue until the root cause — the “why” — is identified.
Workplace incidents — including injuries, illnesses, close calls/near misses, and reports of other concerns — provide a clear indication of where hazards exist. Thoroughly investigating incidents and reports will help identify hazards that are likely to cause future harm. The purpose of an investigation must always be to identify the root causes (and there is often more than one) of the incident or concern, in order to prevent future occurrences. Employers should:
- Develop a clear plan and procedure for conducting incident investigations, so that an investigation can begin immediately when an incident occurs. The plan should cover items such as:
- Who will be involved;
- Lines of communication;
- Materials, equipment, and supplies needed; and
- Reporting forms and templates.
- Train investigative teams on incident investigation techniques, emphasizing objectivity and open-mindedness throughout the investigation process.
- Conduct investigations with a trained team that includes representatives of both management and workers.
- Investigate close calls/near misses.
- Identify and analyze root causes to address underlying program shortcomings that allowed the incidents to happen.
- Communicate the results of the investigation to managers, supervisors, and workers to prevent recurrence.
Effective incident investigations do not stop at identifying a single factor that triggered an incident. They ask the questions “Why?” and “What led to the failure?” For example, if a piece of equipment fails, a good investigation asks: “Why did it fail?” “Was it maintained properly?” “Was it beyond its service life?” and “How could this failure have been prevented?” Similarly, a good incident investigation does not stop when it concludes that a worker made an error. It asks such questions as: “Was the worker provided with appropriate tools and time to do the work?” “Was the worker adequately trained?” and “Was the worker properly supervised?”
Identifying Physical Hazards
What are physical hazards?
Physical hazards abound in the workplace. The mere fact that a company exists makes it prone to physical hazards — even the benign office has tripping and falling hazards. In an industrial setting, the huge variety of machines, processes, and equipment create a challenging set of hazards that a safety professional must deal with.
Processes that use large quantities of chemicals present a unique set of challenges. The physical properties of certain chemicals, such as flammable and combustible liquids, compressed gases, solvents, and explosives make them highly dangerous.
You may not think much about falls, but trips and falls often result in injury and lost time. Falls can even be fatal. In the workplace, there are many situations that contribute to falls:
- Floors with water, grease, or cracks
- Trash or stock piled in pedestrian walkways
- Ladders in need of repair
- Stairs with loose rails or step treads
Maintaining equipment in peak condition, practicing good housekeeping techniques, and providing signs to warn of physical hazards goes a long way to improve overall safe working conditions. Part of the safety professional’s job is to assess the workplace for physical hazards and see that they are corrected or controlled. There are many OSHA standards that have specific requirements for ensuring that physical hazards in the workplace are eliminated. In this section, you will find action steps, training action plans, tips, and checklists on a variety of topics related to controlling physical hazards.
Combustible dust
Combustible dusts are fine particles that present an explosion hazard when suspended in air in certain conditions. A dust explosion can be catastrophic and cause employee deaths, injuries, and destruction of entire buildings. In many combustible dust accidents, employers and employees were unaware that a hazard even existed. It is important that employers determine if their operations have this hazard, and if so, that they take action now to prevent tragic consequences.
A wide range of industries possess combustible dust hazards and a wide variety of materials cause combustible dust incidents. (Combustible dusts can be intentionally manufactured powders, such as corn starch or aluminum powder coatings, or may be generated by handling and processing solid combustible materials such as wood and plastic pellets. For example, polishing, grinding, transporting, and shaping many of these materials can produce very small particles.)
Action steps
The following are general action steps that should be taken to identify and control dust hazards. For detailed guidance specific to your operations, consult with a qualified professional, as well as industry standards, as applicable (for example, those published by the National Fire Protection Association).
- Assess your facility for processes that generate dust. Have dusts analyzed for combustibility hazards. (There are several factors that determine how explosive a dust can be, as well as some key measurements for determining dust explosibility. These include particle size, moisture content, ambient humidity, oxygen available for combustion, the shape of the dust particle, and the concentration of dust in the air, i.e., minimum explosive concentration or MEC.)
- Understand the five elements needed for a combustible dust explosion: Combustible dust (fuel); ignition source (heat); oxygen in air (oxidizer); dispersion of dust particles in sufficient quantity and concentration; and confinement of the dust cloud.
- Understand that there can be a primary explosion or event that shakes loose hidden dust (for example, from piping or rafters) which can cause a devastating secondary explosion.
- Ensure operations have proper engineering design and controls and inspect/maintain those controls. Seek outside assistance/expertise as needed to ensure proper dust control procedures/methods are in place.
- Develop an ignition control program, limiting and controlling potential ignition sources in dust accumulation areas.
- Train employees on the explosion hazards of combustible dusts.
- Implement a housekeeping program with regular cleaning frequencies for floors and horizontal surfaces, such as ducts, pipes, hoods, ledges, and beams, to minimize dust accumulations within operating areas of the facility. (Even seemingly small amounts of accumulated dust can cause catastrophic damage. The CSB estimated, for example, that the explosion that devastated a pharmaceutical plant in 2003 and killed six employees was caused by dust accumulations mainly under 0.25 inches deep. The CSB study references National Fire Protection Administration (NFPA) warnings that a catastrophic explosion can occur from as little as 1/32 of an inch of accumulated dust — around the thickness of a dime — covering just 5 percent of a room’s surface.)
- Ensure working surfaces are designed in a manner to minimize dust accumulation and facilitate cleaning.
- Ensure electrical equipment and electrically-powered cleaning devices such as vacuum cleaners are approved for the hazard classification for Class II locations.
- Select and use industrial trucks that are approved for the combustible dust locations.
- Prohibit the use of cleaning methods that can disperse combustible dust into the air (i.e., compressed air and dry sweeping).
- Ensure the ready availability of SDSs for the chemicals which could become combustible dust under normal operations. Note: The Chemical Safety Board has found that many SDSs do not provide sufficient data on combustible dust hazards. However, OSHA revised the HazCom rule in 2012. In the revised rule, combustible dust hazards must be addressed on labels and SDSs. Label elements are provided for combustible dust in the final HCS and include the signal word “warning” and the hazard statement “May form combustible dust concentrations in the air.”
- Implement an emergency action plan and maintain exit routes properly.
For chemicals in a solid form that do not present a combustible dust hazard, but may form combustible dusts while being processed in normal downstream uses, OSHA allows the chemical manufacturer some flexibility in labeling requirements. The manufacturer or importer may transmit the label to the customer at the time of the initial shipment, but the label does not need to be included with subsequent shipments unless it changes. This provides the needed information to the downstream users on the potential hazards in the workplace, while acknowledging that the solid metal or other materials do not present the same hazards that are produced when these materials are processed under normal conditions of use.
Training action plan
Workers are the first line of defense in preventing and mitigating fires and explosions. If the people closest to the source of the hazard are trained to recognize and prevent hazards associated with combustible dust in the plant, they can be instrumental in recognizing unsafe conditions, taking preventative action, and/or alerting management. While OSHA standards require training for certain employees, all employees should be trained in safe work practices applicable to their job tasks, as well as on the overall plant programs for dust control and ignition source control. They should be trained before they start work, periodically to refresh their knowledge, when reassigned, and when hazards or processes change.
- Define combustible dusts.
Combustible dusts are fine particles,
fibers, chips, chunks, or flakes
that could be an explosion hazard
when they’re suspended in air
under certain conditions.
Many products can be fuel for a
dust explosion when they’re used in powdered form. Here are some
examples:
- Flour, sugar, powdered milk, or other food-related products;
- Wood;
- Paper;
- Textiles;
- Charcoal and other carbon-rich materials;
- Sulfur and other chemicals;
- Aluminum, zinc, and other metals; and
- Epoxy resin and other plastics.
- Introduce the hazards.
A dust explosion can cause deaths
and serious injuries. An explosion
can destroy an entire building. In
many combustible dust incidents,
employers and employees didn’t
know that a hazard even existed.
Here’s an example of what happens
during a combustible dust explosion.
- In February 1999, a deadly fire and explosion occurred in a foundry in Massachusetts. An investigation found that a fire started in a molding machine and then spread to ventilation ducts. The small initial explosion in the ductwork disturbed resin dust that had settled on the outside of the ducts, creating a dust cloud. This dust provided fuel for a secondary explosion that was powerful enough to lift the roof and cause walls to collapse.
- Identify the types of industries that may be at risk. Combustible dust explosion hazards can exist in a variety of industries, including: agriculture, chemicals, food, grain, fertilizer, tobacco, plastics, wood, paper, tire and rubber, furniture, textiles, pesticides, pharmaceuticals, coal, metal processing, recycling operations, and others.
- Explain how dust explosions can happen. The familiar fire triangle is made up of: oxygen, an ignition source (heat), and fuel. All three conditions must be present for a fire to start. Because oxygen is normally always present in the air, fires are usually prevented by keeping the fuel separate from the ignition source. In addition to the fire triangle elements, the “dust explosion pentagon” adds two more conditions: dust particles and the confinement of the dust cloud. Similar to the fire triangle, if one part of the pentagon is missing, a combustible dust explosion can’t occur. If a dust cloud is ignited in an enclosed area such as a room, vessel, ductwork, or process equipment, it burns very fast and may explode. Even if the initial explosion is small, it could shake up accumulated dust in the area to form another dust cloud. Often these secondary explosions are far more destructive.
- Outline how to look for combustible
dust hazards.
To identify the factors that could
contribute to an explosion, employers
should evaluate the hazards of
all: materials, operations, spaces (including hidden ones),
and potential ignition sources. Some likely areas where dust can
build up include:
- Parts of the building’s structure,
- Conduit and pipe racks,
- Electrical cable trays,
- Floors,
- Areas above suspended ceilings, and
- On and around equipment (including leaks around dust collectors and ductwork).
- Discuss what can be done to
control dust build-up.
If the dust isn’t building up, it lowers the risk of a dust explosion. There
are many ways to keep dust under
control. Some of these methods are
to:
- Conduct regularly scheduled inspections,
- Clean up dust on a regular basis,
- Use proper dust collection systems and filters,
- Keep dust from escaping from equipment or ventilation systems,
- Use surfaces that are easy to clean,
- Provide easy access to inspect and clean hidden areas where dust might build up,
- Use cleaning methods that don’t stir up dust clouds, and
- Use vacuum cleaners approved for dust collection.
- Describe methods to prevent
dust from igniting.
Keeping ignition sources under
control is an important part of any
fire safety program. Some actions
employers can take include the following:
- Use proper wiring methods;
- Make sure electrically powered equipment (including forklifts) is approved for the location;
- Control static electricity (bond equipment to ground);
- Keep smoking areas, open flames, sparks, and heated surfaces separate from dusts;
- Follow a hot work permit program; and
- Follow a preventive maintenance program.
- Discuss some methods to minimize
injuries and damage from
a combustible dust explosion.
Some of the steps employers can
take to minimize injuries and damage
from a combustible dust explosion
could include:
- Developing an emergency action plan,
- Maintaining emergency exit routes,
- Setting up operations in areas where the hazards are away from workers and equipment,
- Setting up isolation barriers around hazardous operations,
- Making sure dust handling equipment has pressure relief venting that’s directed away from workers and equipment, and
- Installing specialized spark detection and fire suppression systems in dust handling equipment.
Tips
The amount of dust accumulation necessary to cause an explosive concentration can vary greatly. This is because there are so many variables — the particle size of the dust, the method of dispersion, ventilation system modes, air currents, physical barriers, and the volume of the area in which the dust cloud exists or may exist. As a result, simple rules of thumb regarding accumulation (such as writing in the dust or visibility in a dust cloud) can be subjective and misleading. The hazard analysis should be tailored to the specific circumstances in each facility and the full range of variables affecting the hazard.
Many locations need to be considered in an assessment. One obvious place for a dust explosion to initiate is where dust is concentrated. In equipment such as dust collectors, a combustible mixture could be present whenever the equipment is operating.
Other locations to consider are those where dust can settle, both in occupied areas and in hidden concealed spaces. A thorough analysis will consider all possible scenarios in which dust can be disbursed, both in the normal process and potential failure modes.The facility analysis must identify areas requiring special electrical equipment classification due to the presence (or potential presence) of combustible dust. Various OSHA standards as well as industry (e.g., NFPA) can be consulted.
Checklist
Follow these checklists to prevent combustible dust hazards.
Hazard assessment
- Are there processes that accumulate dust? If so, have the dusts been analyzed for combustibility?
- Are periodic assessments conducted to determine dust explosion possibilities?
- Are employees and supervisors involved in identifying dust explosion hazards, for example through job hazard analyses?
- Is particular attention given during the hazard assessment to dust collection systems and areas not in plain view?
Prevention
- Have proper engineering design and controls been implemented for operations involving combustible dust; for example, dust control in process equipment and fugitive dust control; grounding and bonding; and separator devices?
- Is a comprehensive housekeeping program implemented?
- Are potential ignition sources limited and controlled in dust accumulation areas?
- Is it prohibited to use compressed air and similar cleaning methods that could disperse combustible dusts into the air?
- Are electrical services appropriate for Class II location? Consult applicable codes, for example the National Electrical Code.
- Are industry standards, such as NFPA 654, followed as applicable?
- Is a preventive maintenance program in place to minimize release of fugitive dust?
Note: Minor, but steady leaks, can cause large amounts of dust to accumulate.
Training
- Have employees received training on the hazards of dust?
- Have employees received training on specific characteristics of the dust that they work with?
- Have employees been trained to recognize potential ignition sources?
- Do employees know which processes/locations accumulate dust (for example, cable trays, pipe racks, floors, above ceilings, and structural members)?
- Are employees instructed to report plant fires and near misses?
Confined spaces
Employees in industry and construction are often asked to perform work in confined spaces, but many confined spaces contain serious hazards that endanger the employees who enter those spaces. For this reason, the Occupational Safety and Health Administration requires employers to implement certain procedures that protect workers from the hazards posed by confined spaces. These include procedures for identifying physical hazards and hazardous atmospheres in confined spaces, controlling and eliminating these hazards, and more.
Action steps
- Evaluate the workplace to determine if any spaces are permit-required confined spaces.
- Inform exposed employees, by posting danger signs or by any other equally effective means, of the existence and location of and the danger posed by the permit spaces.
- Decide whether employees will enter spaces. (If employees will not enter spaces, take appropriate, effective prevention measures.)
- Implement a written permit space program.
- Evaluate hazards of permit spaces.
- Provide employees with the opportunity to observe any monitoring or testing of permit spaces.
- Develop and implement the means, procedures, and practices necessary for safe permit space entry operations.
- Establish a permit system.
- Provide training.
- Perform entry according to OSHA requirements.
- Verify that conditions in the permit space are acceptable for entry throughout the duration of an authorized entry.
- Provide appropriate equipment (PPE, rescue equipment, testing, monitoring, ventilation, lighting, etc.)
- Provide at least one attendant outside the permit space into which entry is authorized for the duration of entry operations.
- Develop and implement rescue procedures.
- If contractors are involved in the confined space entry, follow pertinent OSHA requirements.
Training action plans
Training must be such that all employees whose work is regulated by OSHA’s confined spaces standard acquire the understanding, knowledge, and skills necessary for the safe performance of the duties assigned.
Training must be provided to each affected employee:
- Before the employee is first assigned duties relative to the confined space.
- Before there is a change in assigned duties.
- Whenever there is a change in permit space operations that presents a hazard about which an employee has not previously been trained.
- Whenever you have reason to believe either that there are deviations from the permit space entry procedures or that there are inadequacies in the employee’s knowledge or use of these procedures.
The training must establish employee proficiency in the duties required by the confined spaces standard and must introduce new or revised procedures, as necessary, for compliance.
Training should be specific to the employee’s function relative to the confined space. For instance, if the employee is an authorized entrant, then training should focus specifically on tasks and hazards he may face in this role.
In general, training should cover:
- Equipment to be used,
- Communicating with others involved in the work,
- Hazard awareness and recognition,
- Specific roles and duties,
- Monitoring,
- Medical and first aid, and
- Rescue.
Any work that involves contractors also requires special training and communication, both from the host to the contractor and from the contractor to the host.
Documentation
The employer must certify that required training has been accomplished. The certification must contain:
- Each employee’s name,
- The signatures or initials of the trainers, and
- The dates of training.
Tips
- A permit-required confined space is a confined space that has one or more of the following characteristics:
- Contains or has the potential to contain a hazardous atmosphere;
- Contains a material that has the potential for engulfing an entrant;
- Has an internal configuration such that an entrant could be trapped or asphyxiated by inwardly converging walls or by a floor which slopes downward and tapers to a smaller cross section; or
- Contains any other recognized serious safety or health hazard.
- When workers enter a permit space, at least one person must remain outside to monitor, summon help, or provide assistance.
- An attendant may attend to more than one permit space provided he/she can perform all required duties without compromising the safety of any entrant in all spaces being monitored (there is no proximity requirement).
- An employee can be both an entry supervisor and entrant as long as the employee has had the appropriate training and the duties of one activity do not conflict with the duties of the other.
- The entrants need to wear chest or full body harnesses with retrieval lines to make non-entry rescue attempts easier.
- The attendant needs to communicate with the entrants to monitor their conditions. If a situation arises that requires emergency rescue, the attendant should summon the rescue service and stay outside of the permit space entrance.
- An attendant can be a trained member of the rescue service, but cannot enter the permit space until the rest of the team has arrived to start proper rescue procedures.
Checklist
View these confined space checklists to ensure safety and compliance at your facility.
Monitoring
- When working in permit-required confined spaces, are environmental monitoring tests taken?
- Are authorized entrants or their representatives provided an opportunity to observe any monitoring or testing of permit spaces?
- Are permit spaces tested to determine if acceptable entry conditions exist prior to entry?
- Are permit spaces tested or monitored as necessary to determine if acceptable entry conditions are being maintained during the course of entry operations?
Equipment
- Is necessary personal protective equipment available?
- Is rescue and emergency services equipment available?
- Is communications equipment provided to allow the attendant to communicate with authorized entrants as necessary to monitor entrant status and to alert entrants of the need to evacuate the permit space?
General
- Are those having active roles in entry operations appropriately designated (for example, authorized entrants, attendants, entry supervisors, and persons who test or monitor the atmosphere in a confined space)?
- Is at least one attendant stationed outside the confined space for the duration of the entry operation?
- Are appropriate rescue personnel available?
- Are permit spaces flushed, ventilated, purged, and rendered inert to eliminate or control atmospheric hazards prior to entry?
Emergency action plans
This regulation applies to all companies that fall under a particular OSHA standard that requires an emergency action plan. However, it is wise for all employers to have action plans for any emergency that may be reasonably expected to occur in the workplace. Where required by OSHA, employers must develop a plan (called an emergency action plan or EAP) for emergency situations so that there is a literal “plan of action” for employees to take in the event of fires, toxic chemical releases, hurricanes, tornadoes, blizzards, floods, and other similar catastrophic events.
Action steps
Include the following minimum requirements in the EAP to ensure that it covers those designated actions employers and employees must take to ensure employee safety from fire and other emergencies.
- Establish emergency escape procedures and emergency escape route assignments.
- Develop procedures to be followed by employees who remain to operate critical plant operations before they evacuate.
- Establish procedures to account for all employees after emergency evacuation has been completed.
- Assign rescue and medical duties for those employees who are to perform them.
- List the preferred means of reporting fires and other emergencies.
- Develop a list of employee names or regular job titles of persons or departments who can be contacted for further information or explanation of duties under the plan.
- Establish an employee alarm system. If the employee alarm system is used for alerting fire brigade members, or for other purposes, use a distinctive signal for each purpose.
- List the types of evacuation to be used in emergency circumstances.
- Designate and train a sufficient number of employees to assist in the safe and orderly emergency evacuation of employees before implementing the EAP.
- Review the EAP with each covered employee upon initial assignment, when the employee’s responsibility or designated actions under the plan change, and when the plan changes.
Training action plan
You should develop an emergency action team prior to implementing the EAP. Begin by designating and training a sufficient number of employees to assist in the safe and orderly emergency evacuation of their coworkers.
- List the names or job titles of persons who can be contacted for more information on the plan. Trainees should understand:
- The employee alarm system,
- How to report fires and other emergencies, and
- Which personnel are designated to perform rescue and medical duties and their individual responsibilities.
- Explain how all employees will be accounted for after the emergency evacuation has been completed. Make sure employees understand:
- Critical plant operations and who is designated to remain behind to operate it/shut it down before they evacuate, and
- Emergency escape procedures and emergency escape routes.
Tips
A map of the facility showing specific areas, exit routes, exit doors, and head count locations is a useful training tool and should also be posted around the company.
If a fire occurs, safe and orderly evacuation is necessary. Your company should have an established evacuation plan, with procedures and exits indicated. Find out what it is and where you are expected to go during a fire or fire drill. A head count location should be established so that once everyone is evacuated, you meet at a designated spot to account for each employee.
Other than fires, severe weather emergencies are the most common emergency situations that occur. Severe weather emergencies include hurricanes, tornadoes, excessive heat, heavy snow, and extreme cold weather conditions.
If a bomb threat is made at your facility, always take the threat seriously. Immediately notify a supervisor or the safety manager of the threat and evacuate the premises (do not search for a bomb unless instructed by police to look for foreign or suspicious objects).
Checklist
Follow these checklists to ensure you and your employees are prepared for any potential emergencies.
Emergency action plan
- Is there an emergency action plan (EAP) in place detailing procedures employees should follow in an emergency?
- Does the EAP include procedures for all anticipated emergency situations (i.e., fire, tornado, bomb threat, or explosion)?
- Does the EAP include escape procedures and routes?
- Does the EAP contain procedures for those remaining in the facility to perform critical operations?
- Do you have headcount procedures (location or methods for accounting for employees)?
- If your company is located in a high-rise building, does your emergency program include appropriate escape information?
- Do you have an employee assistance program or some other means to provide counseling to employees should a disaster occur?
Disaster recovery
- Have you established a work location that could be used should your facility be unavailable due to disaster or emergency?
- Does the temporary work location have all necessary equipment so critical business functions can be carried out?
- Have necessary safety measures been taken to ensure that the temporary location is safe and will have necessary protective equipment?
Rescue workers
- Is air monitoring conducted to make sure rescue area is safe?
- Are rescue workers protected against hazards that may be encountered (i.e., asbestos, silica)?
- Are rescue workers provided proper protective equipment for the hazards they face?
Alarms and warnings
- Does the employee alarm system provide warning for necessary emergency action as called for in the emergency action plan?
- Is the employee alarm capable of being perceived above ambient noise or light levels by all employees in the affected portions of the workplace?
- Is the employee alarm distinctive and recognizable as a signal to evacuate the work area or take necessary actions?
- Have all employees been informed of the preferred means of reporting emergencies, such as manual pull box alarms, public address systems, radio or telephones?
- Are emergency telephone numbers posted near telephones, or employee notice boards, and other conspicuous locations?
- Have procedures been established for sounding emergency alarms in the workplace?
Fire alarm systems
- If you have a non-supervised fire alarm system, is it tested bimonthly?
- If you have a supervised employee alarm system (that is, does the alarm have a device that indicates system malfunction), is it tested yearly?
Entrances and exits
If you are a general industry employer, the Subpart E Exit routes regulations apply to your company. Your facility must provide a safe means of exiting from buildings or structures for the purpose of general egress, or for the purpose of exiting in the case of fire or other emergencies. In addition, you must also provide a clear and unobstructed path to the entrance of your facility.
Action steps
- Make sure exit routes are permanent.
- Separate exits using fire resistant materials.
- Limit openings into an exit.
- Ensure the number of exit routes is adequate.
- Ensure there are at least two exit routes.
- Provide adequate exit discharge.
- Make sure exit doors are unlocked.
- Use side-hinged exit doors.
- Ensure the capacity of exit routes is adequate.
- Provide exit routes that meet minimum height and width requirements.
- Keep exit routes free of explosive or highly flammable furnishings or other decorations.
- Maintain exit routes free and unobstructed.
- Ensure lighting and marking is adequate and appropriate.
- Maintain exit routes during construction, repairs, or alterations.
- Ensure that the alarm system is operable.
Training action plan
You must designate and train employees to assist in a safe and orderly evacuation of other employees.
You must also review the emergency action plan with each employee covered by the plan. This review should be conducted:
- When the plan is developed or the employee is assigned initially to a job,
- When the employee’s responsibilities under the plan change, and
- When the plan is changed.
Tips
- The line-of-sight to an exit sign must be clearly visible at all times.
- Maintain exit routes during construction, repairs, or alterations.
- Ceilings of exit routes must be at least 7 feet, 6 inches high.
- Exit access must be at least 28 inches wide at all points.
Checklist
Review these checklists to ensure exit routes at your facility meet compliance.
Exit design
- Are exit routes made of approved components and permanently attached to the building?
- Are exit routes designed and maintained to provide adequate headroom?
- Are exit doors designed so that no device or alarm failure will impede or prevent emergency use of exits?
Capacity of means of egress
- Are width and capacity of exit routes in compliance with OSHA standards?
- Is the capacity of the exit route sufficient for the occupant load?
- Where more than one way of exit access leads to an exit, does each have a width adequate for the number of persons it must accommodate?
Arrangement of exits
- Have you assured that no furnishings, decorations, or other objects are placed as to obstruct exits or exit visibility?
- Are exits adequately lighted so an employee with normal vision can see along the exit route?
Access to exits
- Are exit doors unlocked?
- Are exits readily accessible at all times?
- Are doors, from a room to an exit or to a way of exit access, of the side-hinged, swinging type?
- Is access to an exit NOT through a bathroom, or other room subject to locking (except where the exit is required to serve only the room subject to locking)?
- Are ways of exit access and the doors to exits to which they lead clearly recognizable as such?
- Is exit access arranged so that it will not be necessary to travel toward any area of high hazard occupancy in order to reach the nearest exit?
- Is exit access travel effectively shielded from high hazard locations by suitable partitions or other physical barriers?
- Is the minimum width of any way of exit access at least 28 inches?
Arrangement of exits
- Are exits marked by a readily visible sign?
- Is access to exits marked by readily visible signs if it is not immediately visible?
- Is any door, passage, or stairway that could be mistaken for an exit or a way of exit access, identified by a sign reading “Not an Exit” or similar designation, or identified by a sign indicating its actual character?
Protective enclosure of exits
- When an exit is protected by separation from other parts of the building, does the separating construction meet OSHA requirements (i.e., 1-hour fire resistance rating when the exit connects three stories or less)?
Fire protection
OSHA has many requirements concerning fire protection in the workplace. These requirements are found in Subpart L and in some other specific standards. Among the items addressed by OSHA standards is fire brigades, all portable and fixed fire suppression equipment, fire detection systems, and fire or employee alarm systems.
Action steps
- Provide approved and appropriate portable fire extinguishers.
- Mount, locate, and identify portable fire extinguishers so that they are readily accessible to employees without subjecting the employees to possible injury.
- Maintain fire extinguishers in a fully charged and operable condition.
- Inspect, maintain, and test fire extinguishers.
- Provide necessary training to employees who are expected to use portable fire extinguishers.
- Ensure that hose and standpipe systems meet OSHA requirements.
- Ensure all automatic sprinkler systems meet OSHA requirements.
- Maintain any fixed extinguishing systems per OSHA requirements.
- Follow OSHA requirements for any fire brigade you choose to form.
- Ensure fire detection systems are maintained properly.
- Provide an employee alarm system that gives warning for necessary emergency action as called for in the emergency action plan, or for reaction time for safe escape of employees from the workplace or the immediate work area, or both.
Training action plan
The level and type of training needed for fire protection depends on the level and type of fire protection your facility has in place. For instance, if you have a fire brigade, extensive training must be provided to fire brigade members, per 1910.156.
Similarly, if you provide portable fire extinguishers for employee use, such employees must be trained. This training must familiarize employees with the general principles of fire extinguisher use and the hazards involved with incipient stage fire fighting. Training must be provided upon initial employment and at least annually thereafter.
You must also provide training to any employees who have been designated to use fire fighting equipment as part of an emergency action plan. Training must be provided upon initial employment and at least annually thereafter.
You should also train all employees on the actions they need to take relative to your emergency alarm system. They should be familiar with the distinct sounds of the system and what each sound means.
Tips
- Fire extinguishers have to be kept in their designated locations at all times when not being used.
- When extinguishers are removed for maintenance or testing, they must be replaced by an operable unit.
Checklists
Review these checklists to ensure fire safety at your facility.
Fire extinguishers
- Are portable fire extinguishers provided, mounted, located, and identified so that they are readily accessible to employees?
- Are only approved portable fire extinguishers used?
- Are portable fire extinguishers maintained, fully charged, operating properly, and kept in designated places?
- Are portable fire extinguishers provided for employee use and selected and distributed based on the classes of anticipated fires and on the size and degree of hazard that would affect their use?
- Are travel distances to extinguishers appropriate?
- Are all portable fire extinguishers in the workplace inspected, maintained, and tested?
- Is hydrostatic testing performed by trained persons with suitable testing equipment and facilities?
- Are portable extinguishers hydrostatically tested at the intervals listed in Table L-1 of 1910.157?
- Has an educational program been provided to familiarize employees with the general principles of fire extinguisher use and the hazards involved with incipient stage fire fighting?
- Have employees been trained (who have been designated to use fire fighting equipment) in the use of the equipment?
Fire alarm
- Have you established an employee alarm system that complies with 1910.165?
- If the employee alarm system is used for alerting fire brigade members, or for other purposes, is a distinctive signal used for each purpose?
- Are all employee alarm systems in proper working condition, except when undergoing repairs or maintenance?
Fire detection systems
- Are all devices approved for use?
- Are fire detection systems and components returned to normal operating condition as soon as possible after each use or test?
Fire brigades
- If you choose to form a fire brigade, are the requirements of 1910.156 met?
Sprinkler systems
- Are automatic sprinkler system water control valves, air and water pressure checked weekly/periodically as required?
- Are fire control sprinkler heads kept clean?
- Are sprinkler heads protected by metal guards when exposed to physical damage?
- Is proper clearance maintained below sprinkler heads?
Flammable liquids
OSHA’s Flammable Liquids regulation, 1910.106, applies to all persons who handle, use, store, or transport flammable liquids. A flammable liquid means any liquid having a flashpoint at or below 199.4°F (within that definition, there are four categories of flammable liquids).
Action steps
- Ensure flammable liquids are stored and handled properly.
- Familiarize yourself with the different categories of flammable liquids (this will determine storage and usage requirements).
- Ensure containers meet the design requirements in 1910.106.
- Provide adequate drainage, dikes, and walls for tanks.
- Take precautions to prevent ignition by eliminating or controlling sources of ignition.
- Ensure the design (including selection of materials) fabrication, assembly, test, and inspection of piping systems containing flammable liquids is suitable for the expected working pressures and structural stresses.
- Provide suitable emergency and fire protection.
- Ensure adequate ventilation.
- Install electrical wiring properly.
- Follow proper procedures for dispensing liquids.
Training action plan
Any employee involved in storage, transfer, use, or disposal of flammable liquids needs to be trained to handle them safely and to follow your company’s established procedure.
Generally, training content should cover:
- Categories of flammable liquids,
- Handling procedures,
- Storage procedures, and
- Spill cleanup.
In addition, if your company receives, stores, or handles flammable liquids in storage tanks in areas that have the potential to flood, you need to have employees trained on emergency response procedures.
A hands-on approach is appropriate in this part of the training session. In fact, you may want to demonstrate how to do specific procedures related to flammables at your facility. Then allow each employee to try the procedure, so they can perform them correctly and so they will remember them better.
Tips
- When transferring flammable liquids, always bond and ground the containers.
- If purchasing plastic containers of five gallons or less for use with flammable liquids, purchase those with a built-in metal grounding strip.
Checklist
Review these checklists to ensure flammable liquid safety at your facility.
Containers
- Are all connections on drums and piping, vapor and liquid tight?
- Are all flammable liquids kept in closed containers when not in use (e.g., parts cleaning tanks, pans, etc.)?
- Are approved containers and portable tanks used for the storage and handling of flammable liquids?
- Are bulk drums of flammable liquids grounded and bonded to containers during dispensing?
- Are flammable liquids, such as gasoline, kept in an approved safety can?
- Are portable storage tanks equipped with emergency venting that will relieve excessive internal pressure caused by fire exposure?
- Are safety cans used for dispensing flammable liquids at a point of use?
- Are storage cabinets used to hold flammable liquids, labeled “Flammable — Keep Fire Away”?
- Are storage tanks adequately vented to prevent the development of excessive vacuum or pressure as a result of filling, emptying, or atmosphere temperature changes?
Handling
- Are all containers over 30 gallons in inside storage rooms stacked individually?
- Are firm separators placed between containers of combustibles or flammables, when stacked one upon another, to assure their support and stability?
Storage
- Are “No Smoking” rules enforced in areas involving storage and use of hazardous materials?
- Are all solvent wastes, and flammable liquids kept in fire-resistant, covered containers until they are removed from the worksite?
- Are all spills of flammable liquids cleaned up promptly?
- Is proper storage of flammable materials practiced to minimize the risk of fire including spontaneous combustion?
- Is there one clear aisle at least 3 feet wide?
Ladders
OSHA’s ladder regulations, at 1910.23, apply to any general industry workplace that uses ladders to perform duties (other than construction work) at high elevations.
Action steps
- Use ladders that are designed and approved for the intended purpose.
- Ensure ladders meet OSHA specifications.
- Follow all ladder safety requirements.
- Train employees in safe ladder use.
- Maintain ladders in a safe condition.
- Inspect ladders as needed.
- Remove defective ladders from service.
Training action plan
Training content for ladders and stairways depends on the types of equipment and structures your facility has and what work will be performed. In general, workers need to be trained as follows:
Ladders
Content should include:
- Inspecting the ladder,
- Setting up the ladder,
- Safe ladder use,
- Ascending and descending the ladder,
- Maintaining three points of contact,
- Recognizing hazards,
- Carrying tools and equipment, and
- Using the right ladder for the job.
Tips
- Workers on ladders generally do not require fall protection.
- Be careful that painting ladders or applying stickers does not hide damage.
- Make sure the ladder is the best tool for the job.
- Ensure workers understand associated hazards (e.g., electrical, wind) that they may have to consider with selecting and/or using a ladder.
Checklist
Review these checklists to ensure ladder safety at your facility.
Design and construction
- If wood, is the portable ladder not coated with any material that may obscure structural defects?
- If metal, is the portable ladder made of corrosion-resistant material or protected against corrosion?
- If metal, are the rungs and steps of the portable ladder corrugated, knurled, dimpled, coated with skid-resistant material, or otherwise treated to minimize slipping?
- Are the rungs, steps, and cleats of the portable ladder spaced at least 10 inches and not more than 14 inches apart?
- Do the rungs, steps, and cleats of the portable ladder have a minimum clear width of 11.5 inches?
Stepladders
- Is the stepladder equipped with a metal spreader or locking device that securely holds the front and back sections in an open position while the ladder is in use?
Stepstools
- Are the steps on the stepstool spaced at least 8 inches and not more than 12 inches apart?
- Does the stepstool have a minimum clear width of 10.5 inches?
Inspection and maintenance
- Are portable ladders inspected regularly, and as necessary, to ensure they are in safe condition?
- Are deficiencies corrected or repaired before an employee uses the portable ladder again?
- If a portable ladder correction or repair cannot be made immediately, are employees prevented from using the portable ladder until repaired?
- If a portable ladder repair involves structural integrity, does a qualified person perform or supervise the correction or repair?
Training
- Is each employee who uses a portable ladder trained on how to properly use the ladder?
- Is each employee who uses a portable ladder trained to recognize the fall hazards in the work area?
- Is training conducted by a qualified person?
Note: Qualified, under this OSHA requirement, describes a person who, by possession of a recognized degree, certificate, or professional standing, or who by extensive knowledge, training, and experience has successfully demonstrated the ability to solve or resolve problems relating to the subject matter, the work, or the project. - Is information and training provided in a manner that each employee understands?
- Is retraining provided when deficiencies in performance or knowledge are noted, or there are changes in the workplace or equipment?
Personal protective equipment
OSHA’s Subpart I regulations apply to all persons involved in hazardous processes; environmental, chemical, radiological hazards; or mechanical irritants that are capable of causing injury or impairment of any body part through absorption, inhalation, or physical contact. The categories of personal protective equipment (PPE) include: eye and face equipment, head protection, hand protection, foot protection, fall protection, and respiratory protection (information about respiratory protection is provided in a separate topic area under Respiratory Protection, 1910.134).
Action steps
- Assess the workplace to determine what hazards are present that require PPE.
- Document and certify the PPE assessment.
- Provide appropriate and approved PPE based on the workplace hazards.
- Instruct employees in proper PPE usage.
- Ensure employees wear proper PPE.
- Establish inspection and maintenance procedures for PPE.
Training action plan
OSHA requires that you provide training to each employee who is required to use PPE. Each such employee shall be trained to know at least the following:
- When PPE is necessary.
- What PPE is necessary.
- How to properly don, doff, adjust, and wear PPE.
- The limitations of the PPE.
- The proper care, maintenance, useful life, and disposal of the PPE.
Each affected employee must also demonstrate an understanding of the training and the ability to use PPE properly, before being allowed to perform work requiring the use of PPE.
When you have reason to believe that any affected employee who has already been trained does not have the understanding and skill required, you must retrain each such employee. Circumstances where retraining is required include, but are not limited to, situations where:
- Changes in the workplace render previous training obsolete.
- Changes in the types of PPE to be used render previous training obsolete.
- Inadequacies in an employee’s knowledge or use of assigned PPE indicate that the employee has not retained the requisite understanding or skill.
Tips
- Make sure that protective eyewear does not affect the fit of respirators.
- Make sure that protective eyewear does not disturb the proper positioning of corrective lenses so as to inhibit or limit the employee’s vision.
- Ensure employees disinfect shared protective eyewear after each use.
- Always replace a hard hat if it sustains an impact, even if damage is not noticeable.
- Don’t let workers wear hard hats backward unless the hat has been tested and approved for such use.
Checklist
Review these checklists to ensure proper PPE usage at your facility.
General
- Are all employees required to use PPE as needed?
- Is PPE functional and in good repair?
- Is protective clothing and equipment provided and used when cleaning up spilled toxic or otherwise hazardous materials or liquids?
- Is PPE provided and are all employees required to use PPE as needed to protect against injury?
- Does PPE have ANSI or ASTM specifications marked on it?
Training
- Has each individual who is required to use PPE been provided with training?
- Have the trained individuals demonstrated an understanding of the training and the ability to use PPE properly before being allowed to perform work requiring the use of PPE?
- Are individuals retrained when there is reason to believe that they do not have the understanding or skill to use PPE properly?
Recordkeeping
- Have you documented that a hazard assessment has been done, when, and by whom?
- Have you documented that PPE training has been done, who has received it, and when?
Head, foot, and hand protection
- Are protective helmets used wherever there is the possible danger of head injury from impact, or from falling or flying objects, or from electrical shock and burns?
- Is protective footwear used wherever there is the danger of foot injuries due to falling or rolling objects, or objects piercing the sole, and where feet are exposed to electrical hazards?
- Are appropriate protective gloves used wherever there is the danger to hands of exposure to hazards such as those from skin absorption of harmful substances, severe cuts or lacerations, severe abrasions, punctures, chemical burns, thermal burns, and harmful temperature extremes?
Eye and face protection
- Are individuals issued and required to wear appropriate eye protective devices while participating or observing activities which present a potential eye safety hazard?
Personal fall protection
- Have all impacted individuals been trained to use personal fall protection equipment?
- Is the equipment inspected daily before use?
- Does fall protection meet the design requirements in 1910.140?
- Are ropes, belts, lanyards, lifelines, and harnesses used for personal fall protection compatible with connectors used?
Posting requirements
- Are all areas and equipment requiring the use of PPE devices posted with a sign indicating this requirement?
Process safety management
OSHA’s 1910.119 regulation applies to those companies that deal with any of more than 130 specific toxic and reactive chemicals in listed quantities (See 1910.119 Appendix A); it also includes any Category 1 flammable gas (as defined in 1910.1200(c)) or a flammable liquid with a flashpoint below 100°F (37.8°C) on site in one location, in a quantity of 10,000 pounds (4535.9 kg) or more (with a few exceptions, as outlined in 1910.119(a)(1)(ii)(A) and (B)).
Action steps
- Ensure employee participation in the process safety management program.
- Conduct adequate hazard analyses.Implement safety operating procedures.
- Conduct process safety training.
- Ensure process safety for contractors.
- Conduct pre-startup safety reviews.
- Ensure integrity of process equipment.
- Ensure management of change process and procedures are adequate.
- Investigate incidents per OSHA requirements.
- Ensure emergency planning and response efforts are adequate.
- Establish a process safety compliance audit process.
Training action plan
You must train each employee involved in operating a process and each employee before being involved in operating a newly assigned process. Training must include:
- An overview of the process and the operating procedures.
- Specific safety and health hazards.
- Emergency operations including shutdown.
- Safe work practices applicable to the employee’s job tasks.
Also, you must provide refresher training at least every three years, and more often if necessary, to each employee involved in operating a process to assure that the employee understands and adheres to the current operating procedures of the process. You, in consultation with the employees involved in operating the process, must determine the appropriate frequency of refresher training.
Documentation
You must prepare a record that contains the identity of the employee, the date of training, and the means used to verify that the employee understood the training.
Tips
- OSHA’s Process Safety Management (PSM) standard requires that mechanical integrity inspections have to be documented (including the name of the person performing the inspection or test) and list the information to be recorded.
- The PSM standard states that the employer must establish and implement written procedures.
- To comply with the PSM standard, employers must document that equipment complies with recognized and generally accepted good engineering practices. For existing equipment designed and constructed in accordance with codes, standards, or practices that are no longer in general use, the employer must determine and document that the equipment is designed, maintained, inspected, tested, and operated in a safe manner.
- All process hazard analyses must be updated and revalidated, based on their completion date, at least every five years.
- Employers must consult with employees and their representatives on the conduct and development of process hazard analyses and on the development of the other elements of process management, and they must provide to employees and their representatives access to process hazard analyses and to all other information required to be developed by the standard.
- Contract employees must be instructed on known potential fire, explosion, or toxic release hazards related to their job and the process, and in the applicable provisions of the emergency action plan.
Checklist
Review these process safety management checklists.
Process hazard analysis
- Has written process safety information been compiled before conducting any process hazard analysis (PHA)?
- Are the process hazard analyses performed by teams with expertise in engineering and process operations?
- Has a system been established to promptly address the team’s findings and recommendations?
- Are the PHA’s updated and revalidated to assure that the process hazard analysis is consistent with the current process?
Incident investigation
- Has each incident been investigated which resulted in, or could reasonably have resulted in, a catastrophic release of highly hazardous chemicals in the workplace?Has a system been established to promptly address and resolve the incident investigation report findings and recommendations?
Emergency action plan
- Has an emergency action plan been established and implemented for the entire plant in accordance with the requirements of 1910.38?
Written program
- Do you have an appropriate written program for PSM compliance?
- Do you have a written program regarding employee participation?
- Do written operating procedures exist for each covered process?
- Have safety and health considerations been included in the operating procedures?
Contractors
- Have safe work practices been developed and implemented for employees and contractors to control hazards?
- For employees and contractor employees involved in operating a process do initial and refresher training records exist?
- Has each employee and contractor employee been trained before being involved in a newly assigned process?
Pre-startup safety review
- Has a pre-startup safety review been performed for all new facilities and for modified facilities when the modification is significant enough to require a change in process safety information?
Mechanical integrity
- Are there written procedures to maintain the ongoing integrity of process equipment?
- Are appropriate inspections and tests performed on each item of process equipment included in the program?
- Have appropriate checks and inspections been made to assure equipment is installed properly and consistent with design specifications and manufacturer’s instructions?
Hot work permits
- Have hot work permits been issued for all hot work operations conducted on or near a process covered by the PSM standard?
Management of change
- Are there written procedures for managing changes (except for “replacements in kind”) to process chemicals, technology, equipment, and procedures and changes to facilities that affect a covered process?
Audits
- Do you conduct an audit of compliance with PSM at least every three years?
- Do you retain the two most recent compliance audit reports?
Training
- Have employees been trained properly regarding PSM?
- Are appropriate training records kept?
Signs and markings
OSHA’s 1910.144-.45 regulations provide specifications for signs and tags and are intended to cover all safety signs except those designed for streets, highways, railroads, and marine regulations. These specifications do not apply to plant bulletin boards or to safety posters.
Action steps
- Use appropriate colors for identification of equipment and hazards per OSHA regulations.
- Ensure emergency stop bars and buttons on hazardous machines are red.
- Ensure yellow is used for designating caution and for marking physical hazards such as: Striking against, stumbling, falling, tripping, and “caught in between.”
- Follow OSHA specifications for accident prevention signs and tags.
- Instruct employees in recognizing accident prevention signs and tags and the appropriate action to take regarding those markings.
- Ensure messages on signs and tags are clear and to the point.
Training action plan
Training on accident prevention signs and tags is required prior to or at the time of initial assignment to areas where accident prevention signs and tags are used. Training content should generally include:
- Sign color,
- Symbols,
- Labeling, and
- Company-specific marking systems.
Consider other safety training issues relative to safety signs such as hazard communication and the specific posting requirements of the chemical-specific standards found in Subpart Z of the 1910 regulations. Training might also cover the information found in the poster describing employee rights under OSHA (poster 2203) which must be displayed somewhere where workers will see it.
OSHA does not require training documentation for Specifications for Accident Prevention Signs and Tags, but it is always prudent to keep records anyway. Training records can tell you who was trained on what, when, and what was covered.
Tips
- The lines used to delineate the aisles may be any color so long as they clearly define the area considered as aisle space. The lines may be composed of dots, square, strip or continuous, but they too must define the aisle area.
- The recommended width of aisle markings varies from two inches to six inches; therefore, any width two inches or more is considered acceptable.
- Danger sign — The colors red, black, and white must be those of opaque glossy samples as specified in Table 1 of Fundamental Specification of Safety Colors for CIE Standard Source “C”, American National Standard Z53.1-1967.
- Caution sign — Standard color of the background must be yellow; and the panel, black with yellow letters. Any letters used against the yellow background must be black. The colors must be those of opaque glossy samples as specified in Table 1 of American National Standard Z53.1-1967.
- Safety instruction signs — Standard color of the background must be white; and the panel, green with white letters. Any letters used against the white background must be black. The colors must be those of opaque glossy samples as specified in Table 1 of American National Standard, Z53.1-1967.
Checklist
Review these checklists for signs and markings at your facility.
Hazardous substances
- Is every hazardous chemical in the workplace labeled with identification and hazard warnings?
- Are safety and other containers painted appropriately?
- Are equipment, containers, materials, or areas where biohazards are or could be present labeled with the biological hazard warning?
- Are any entrances to regulated areas where the 13 carcinogens listed at 1910.1003 are present marked with appropriate signage warning of the danger?
- Are signs posted warning of presence and hazards of asbestos where required?
Aisles
- Are permanent aisles and passageways appropriately marked?
Materials handling
- Are clearance signs warning of clearance limits provided?
- Are powered industrial trucks appropriately marked?
- Are cranes marked with the load rating on each side?
- Are crane pendant control boxes clearly marked for identification of functions?
Emergency
- Are exits marked by a readily visible sign?
- Are areas that could be mistaken for an exit identified by a sign reading “Not an Exit” or something similar?
- Are portable fire extinguishers mounted, located, and identified so they are readily accessible?
Ladders
- Are defective ladders withdrawn from service and tagged or marked as “Dangerous, Do Not Use”?
Lockout/tagout
- Do tagout devices warn against hazardous conditions if the machine or equipment is energized?
Confined spaces
- Are completed confined space permits posted at an appropriate location?
- Are signs posted at permit-required confined spaces describing the dangers present?
OSHA posters
- Is OSHA’s Form 2203 (or 3165) describing the OSH Act posted appropriately?
- Is the annual summary of OSHA No. 300 Form posted appropriately?
- Are citations received from OSHA posted at or near the place the violation(s) occurred?
Electrical
- Is the manufacturer’s description marked on all electrical equipment used?
- Are covers for pull and junction boxes permanently marked “HIGH VOLTAGE”?
Slips, trips, and falls
OSHA has various requirements to protect workers from slipping, tripping, or falling. These requirements are in Subpart D. Among other things, OSHA requires that all floors, platforms, runways, and wall and window openings where there is a drop of four feet or more have some type of guarding, or that workers utilize an appropriate personal fall arrest system.
Action steps
- Keep all places of employment, passageways, storerooms, and service rooms clean and orderly and in a sanitary condition.
- Ensure floors are maintained in a clean and, so far as possible, a dry condition.
- Maintain drainage where wet processes are used.
- Ensure every floor, working place, and passageway are kept free from protruding nails, splinters, holes, or loose boards.
- Provide sufficient safe clearances for aisles, at loading docks, through doorways and wherever mechanical handling equipment turns or passage must be made.
- Ensure permanent aisles and passageways are appropriately marked.
- Provide covers and/or guardrails to protect personnel from the hazards of open pits, tanks, vats, ditches, etc.
- Ensure ladders are maintained and used properly.
- Follow proper safety procedures for scaffold setup and use.
- Ensure all walking-working surfaces are maintained safely.
Training action plan
Before any employee is exposed to a fall hazard, OSHA requires that the employer must provide training for each employee who uses personal fall protection systems, as well as employees using certain equipment such as ladders, rope descent systems, and dockboards.
The employer must ensure that each employee is trained by a qualified person.
Training for impacted employees must cover pertinent topics, including:
- How to use, inspect, maintain, and disassemble a personal fall protection system,
- How to properly place dockboards, and
- Designated area set-up.
OSHA requires employees be retrained when there is reason to believe the employee does not have the understanding and skill required to work safely. Situations requiring retraining include, but are not limited to, the following:
- When changes in the workplace render previous training obsolete or inadequate;
- When changes in the types of fall protection systems or equipment to be used render previous training obsolete or inadequate; or
- When inadequacies in an affected employee’s knowledge or use of fall protection systems or equipment indicate that the employee no longer has the requisite understanding or skill necessary to use equipment or perform the job safely.
Training must be provided in a manner that the employee understands.
All employees should be aware of how to prevent slips, trips, and falls by following good housekeeping procedures and when they work on or around:
- Scaffolds,
- Ladders,
- Unprotected ledges or platforms,
- Rooftops,
- Open shafts,
- Trapdoors,
- Poles,
- Towers,
- Bridges,
- Trestles,
- Pits, and
- Open tanks.
Training content should generally focus on:
- Various “fall factors” present in your facility.
- What happens when you slip, trip, and fall.
- How to prevent injuries from slips, trips, and falls, including the use of appropriate footwear.
- Hazards of stairs.
- Fall prevention methods when using ladders and scaffolds.
Tips
- Assign responsibilities for ensuring areas are kept clean and orderly.
- Keep an eye out for uneven floors, labels and cords, wet processes, and low-light areas.
Checklist
Review these checklists to reduce slips, trips, and falls at your facility.
Walkways
- Are aisles and passageways kept clear?
- Are aisles and walkways marked as appropriate?
- Are wet surfaces covered with non-slip materials?
- Are holes in the floor, sidewalk, or other walking surface repaired properly, covered, or otherwise made safe?
- Is there safe clearance for walking in aisles where motorized or mechanical handling equipment is operating?
- Are materials or equipment stored in such a way that sharp projectiles will not interfere with the walkway?
- Are spilled materials cleaned up immediately?
- Are changes of direction or elevations readily identifiable?
- Are aisles or walkways that pass near moving or operating machinery, welding operations or similar operations arranged so employees will not be subjected to potential hazards?
- Are standard guardrails provided wherever aisle or walkway surfaces are elevated more than 30 inches (76.20 centimeters) above any adjacent floor or the ground?
Floor and wall openings
- Are floor openings guarded by a cover, a guardrail, or equivalent on all sides (except at entrance to stairways or ladders)?
- Are toeboards installed around the edges of permanent floor opening (where persons may pass below the opening)?
Dockboards
- Are all dockboards used capable of supporting the maximum intended load?
- Do dockboards that are put into initial service on or after January 17, 2017, have means (such as run-off guards or curbs) to prevent vehicles from running off the edge (unless it can be demonstrated there is no run-off hazard))?
- Are portable dockboards equipped with handholds or other means to permit safe handling?
- Are portable dockboards secured by anchoring in place or using equipment or devices that prevent the dockboard from moving out of a safe position?
- When securing the dockboard is not feasible, is there sufficient contact between the dockboard and the surface to prevent the dockboard from moving out of a safe position?
- Are measures, such as wheel chocks or sand shoes, used to prevent transport vehicles (e.g. a truck, semitrailer, trailer, or rail car) from moving while employees are on the dockboard?
- Is each employee on a dockboard protected from falling 4 feet or more to a lower level by a guardrail system or handrails?
Note: This does not apply when dockboards are being used solely for materials-handling with motorized equipment, the fall hazard is 10 feet or less, and the employees have been properly trained. - Are dockboards inspected regularly, and as necessary, to ensure they are in safe condition?
- Is each employee who uses a dockboard trained to properly place and secure the equipment?
Stairs and stairways
- Are standard stair rails or handrails on all stairways having four or more risers?
- Are all stairways at least 22 inches (55.88 centimeters) wide?
- Are step risers on stairs uniform from top to bottom?
- Are steps on stairs and stairways designed or provided with a surface that renders them slip resistant?
- Are stairway landings adequate?
Inspection and maintenance
- Are aisles and walkways inspected regularly, and as necessary, to ensure they are in safe condition?
- Are deficiencies corrected or repaired before an employee uses an aisle or walkway again?
- If an aisle or walkway correction or repair cannot be made immediately, are employees prevented from using the aisles or walkway until repaired?
- If an aisle or walkway repair involves structural integrity, does a qualified person perform or supervise the correction or repair?
Training
- Are employees trained in measures to protect themselves from slips, trips, and falls?
- Are employees trained to use any fall protection they may need?
- Is training provided in a manner the employees will understand?
Solvents
Solvents are commonly used both in the workplace and at home. They are safe to use when you understand their hazards and know how to protect yourself. Solvents can:
- Cause dizziness, nausea, and depress the central nervous system;
- Cause chronic illnesses such as cancer, liver disease, and nervous system disorders;
- Be toxic; and
- Be flammable.
One thing all solvents have in common is that they are used to dissolve another substance. They can be used as cleaners, degreasers, or as ingredients in paints, coatings, or adhesives. Some examples of common solvents include acetone, alcohol, mineral spirits, and perchloroethylene.
Action steps
- Assess the workplace to determine if solvents are being used, where, and in what processes/procedures.
- Ensure that there is an SDS for each hazardous solvent used in your facility.
- Properly store solvents.
- Ensure that waste and solvent by-products are properly contained and disposed.
- Determine which employees have on-the-job exposure.
- Provide appropriate protective equipment.
- Train affected employees to properly wear the PPE.
- Train affected employees about solvent hazards according to the requirements of the Hazard Communication standard at 1910.1200.
Note: OSHA regulations do not deal with specific solvents; however, some exceptions apply, depending on the chemical used, the potential for exposure, and the degree of exposure.
For more information, see the following regulations:
- Benzene, 1910.1028.
- Spray finishing, 1910.107.
- Dip tanks, 1910.122 through 1910.126.
- Solvents used in a process, 1910.119.
- Flammable liquids, 1910.106 (includes storage and handling requirements).
- HAZWOPER, 1910.120 (responding to spills and leaks).
Training action plan
Under the requirements of OSHA’s hazard communication standard, affected employees have to be given information and training on the hazards of the solvents they are exposed to at the time of their initial assignment, and whenever a new hazard is introduced into their work area.
Hazard communication
Hazard communication training has to include:
- Understanding the requirements of the OSHA hazard communication standard.
- Understanding the various components of your company’s hazard communication program.
- Knowing where the information is located in the company and how to access it.
- Knowing which operations and processes are using hazardous chemicals.
- Ability to read and understand the information on SDSs and labels.
- Knowing how to follow safe work practices and use PPE.
Solvents
Training content for an effective solvent training program should include:
- Identification of common solvents used in the workplace,
- How to recognize solvents,
- The chemistry of solvents,
- Physical and health hazards,
- Engineering controls used to reduce exposures,
- Use of protective equipment,
- Safe work procedures,
- Storage procedures,
- Clean-up and disposal procedures, and
- First aid and emergency procedures.
Tips
- Solvents are used to dissolve another substance. In general, “like dissolves like,” so the chemical composition of the solvent needs to have something in common with the chemical composition of the substance it can dissolve.
- Many solvents are combustible or flammable liquids. This means that they can easily ignite and burn. Acetone and methanol are examples of flammable solvents. Many types of petroleum distillates have a higher flash point and are considered combustible liquids.
- When engineering controls cannot completely eliminate the risk of exposure to solvents, affected employees will need to wear PPE. Chemical splash goggles, face shields, gloves, coveralls, aprons, shoe covers, and respirators are all examples of protective equipment. Refer to the product’s safety data sheet for PPE recommendations.
- Use only the amount of solvent needed for the job. This will minimize exposure and the quantity of waste solvent to be disposed.
- Store solvents in their original containers and be sure all containers in storage are clearly labeled.
Checklist
Review this solvent checklist to ensure safety and compliance at your facility.
- Have all solvents in the workplace been identified and documented?
- Are engineering controls in place to reduce exposures?
- Are hazardous solvents replaced with non-toxic solvents where possible?
- Are job activities controlled to prevent airborne solvent vapors from being generated and released into workers’ breathing area?
- Are workers free from medical complaints or symptoms that could be associated with solvent use?
- In areas where individual exposures are suspected to be above acceptable limits, has air monitoring been performed?
- Are affected persons provided with written copies of air monitoring results?
- Are workers who are exposed to solvent vapors above the permissible exposure limits provided with appropriate personal protective equipment (such as respirators) on an interim basis until engineering or administrative controls reduce exposures below permissible exposure limits?
- Are appropriate personal hygiene practices enforced such as washing hands?
- Is appropriate personal protective equipment (PPE) provided such as gloves, aprons, and goggles to protect against exposure?
- Have workers been trained regarding the hazards of solvents to which they might be exposed?
- Are first aid procedures in place for overexposures?
- Are there emergency procedures in case of a spill or leak?
Standard stairways
Stairways are a common fixture in many workplaces. However, they can pose hazards to workers if not constructed and maintained properly.
Action steps
- Ensure stairs meet OSHA’s specifications (strength, width, rise, etc.). See 29 CFR 1910.25 and 29 CFR 1910.28.
- Equip all stairways that are four feet or more above a lower surface with stair rail systems and guardrails.
- Ensure stairs have uniform riser heights and tread depths between landings.
- Provide proper landing platforms.Inspect all stairways regularly and as necessary.
- Maintain stairways in a safe condition.
Training action plan
Before any employee is exposed to a fall hazard, OSHA requires that the employer must provide training for that employee. In terms of stairs, items to keep in mind include:
- Caution employees not to carry large or bulky objects while climbing or descending stairs.
- Encourage employees to use railings.
- Remind employees not to jump from stairs, or skip steps.
Training must be provided in a manner that the employee understands.
Tips
- Provide stairs with good lighting and tread.
- Provide signage to remind employees of safe stair practices.
- Ensure the change in surface from stairs to platforms does not create a hazard.
- Keep stairs dry.
- Periodically inspect stairways for damage.
Checklist
Review the following standard stairway checklists.
General
- Are standard stairs provided for access from one walking-working surface to another when operations necessitate regular and routine travel between levels?
Condition
- Are stairs in good repair (e.g., loose handrails, corrosion)?
- Are stairs free of hazards (e.g., protruding objects, leaks, spills, snow and ice)?
- Are all steps reasonably slip-resistant?
Design and construction
- Are stairs at least 22 inches wide between vertical barriers?
- Are handrails, stair rail systems, or guardrails provided as necessary?
- Do stairways have at least a 6 feet, 8 inches vertical clearance from any tread to any overhead clearance measured from the leading edge of the tread?
- Can stairs support a load of five times the normal anticipated live load, but not less than 1,000 pounds?
Steps
- Do stairs have uniform riser heights and tread depths?
- Do the stairs have an angle between 30 and 50 degrees from the horizontal?
- Do stairs meet the rise and tread dimensions specified in Table D-1 of 1910.25(c) that achieve an angle between 30 and 50 degrees from the horizontal if installed before January 17, 2017?
- Do stairs have a maximum riser height of 9.5 inches if installed after January 17, 2017?
- Do stairs have a minimum tread depth of 9.5 inches if installed after January 17, 2017?
Fall protection
- Is a stair rail system and handrail(s) present on flights of stairs having at least 3 treads and at least 4 risers?
- Is at least one handrail present if the stairway is enclosed on both sides and is less than 44 inches wide?
- Are handrails present on both sides if the stairway is enclosed on both sides and is more than 44 inches wide but less than 88 inches wide?
- Are handrails present on each side and in the middle of the stair if it is enclosed on both sides and is more than 88 inches wide?
- Is a stair rail system with a handrail present on the open side of the stairway if it is less than 44 inches wide?
- Is a stair rail system with a handrail present on the open side of the stairway and a handrail on the enclosed side if it is more than 44 inches wide but less than 88 inches wide?
- Is a stair rail system with a handrail present on the open side, one handrail on the enclosed side, and one intermediate handrail located in the middle of the stair if it is greater than 88 inches wide?
- Is a stair rail system with a handrail present on each open side of the stairway if it is less than 44 inches wide?
- Is a stair rail system with a handrail present on the each open side of the stairway if it is more than 44 inches wide but less than 88 inches wide?
- Is a stair rail system with a handrail present on each open side and one intermediate handrail located in the middle of the stair if it is greater than 88 inches wide?
- Is a handrail on at least one side with earth built up on both sides present on exterior stairs less than 44 inches wide?
Handrails
- Is the height of handrails 30-38 inches measured from the leading edge of the stair tread to the top surface of the handrail?
- Is the clearance between handrails and any other object at least 2.25 inches?
- Are handrails smooth-surfaced?
- Do handrails have the shape and dimension necessary so that employees can grasp the handrail firmly?
- Do the ends of handrails not present projection hazards?
- Are handrails capable of withstanding, without failure, a force of at least 200 pounds applied in any downward or outward direction within 2 inches of any point along the top edge of the rail?
Stair rail systems
- Is the height of stair rail systems not less than 30 inches from the leading edge of the stair tread to the top surface of the top rail if installed before January 17, 2017?
- Is the height of stair rail systems not less than 42 inches from the leading edge of the stair tread to the top surface of the top rail if installed on or after January 17, 2017?
- Do the opening in stair rail systems not exceed 19 inches at its least dimension?
- If used as a handrail on stairs installed before January 17, 2017, is the height of stair rail systems 36-38 inches measured at the leading edge of the stair tread to the top surface of the top rail?
- If used as handrails, is the clearance between the stair rail systems and any other object at least 2.25 inches?
- Are stair rail systems smooth-surfaced?
- If used as a handrail, do stair rail systems have the shape and dimension necessary so that employees can grasp it firmly?
- Do the ends of stair rail systems not present projection hazards?
- Are stair rail systems capable of withstanding, without failure, a force of at least 200 pounds applied in any downward or outward direction within 2 inches of any point along the top edge of the rail?
Landings and platforms
- Is a platform provided when a door or gate opens directly onto a stairway?
- Is a guardrail or stair rail system provided if the landing is 4 feet or more above the lower level?
- Does the swing of the door or gate not reduce the platform’s usable depth to less than 20 inches if installed before January 17, 2017?
- Does the swing of the door or gate not reduce the platform’s usable depth to less than 22 inches if installed on or after January 17, 2017?
- Is the stairway landing or platform at least as wide as the stairway?
- Is the stairway landing or platform at least 30 inches in depth measured in the direction of travel?
Inspection and maintenance
- Are stairways inspected regularly, and as necessary, to ensure they are in safe condition?
- Are deficiencies corrected or repaired before an employee uses a stairway again?
- If a stairway correction or repair cannot be made immediately, are employees prevented from using the stairway until repaired?
- If a stairway repair involves structural integrity, does a qualified person perform or supervise the correction or repair?
Storage racks
Storage racks are a common fixture in many industrial workplaces, from warehouses to manufacturing facilities to retail to automotive repair shops. Common though they may be, these facilities can pose significant hazards if not installed, used, and maintained properly. Although OSHA does not have a specific standard addressing storage racks, the Agency expects employers to provide safe racking and has cited employers under the General Duty Clause of the OSH Act when racking posed serious hazards to workers.
Action steps
- Ensure all racks meet appropriate industry standards (e.g., ANSI/RMI MH 16.1).
- Install, use, and maintain racks per the manufacturer’s instructions.
- Check that load ratings are present.
- Ensure racks are anchored properly.
- Train workers on racking safety, including capacities and storage techniques.
- Install racks in accordance with local fire and building codes.
- Install bumper guards to prevent rack damage.
- Ensure repairs are made by qualified personnel.
- Replace damaged racks immediately or remove them from service.
Training action plan
- Explain the types of racking in your facility.
- Demonstrate proper stacking technique, including height restrictions.
- Ensure only trained material handling personnel place items on racking with powered equipment.
- Remind workers not to climb on racking (in rare cases where this may be needed, ensure the use of proper fall protection).
- Train workers how to read racking capacity plates.
- Instruct workers on how to report damaged racking.
Tips
- Assign responsibility for inspecting racks.
- Ensure racking repairs are made properly according to manufacturer’s instructions, and by qualified personnel, particularly where welding is performed.
- Maintain at least 18 inches clearance from sprinklers. (Local fire codes may have additional requirements for sprinklers and racking.)
- Conduct thorough root-cause analysis for racking damage.
Checklist
Review these storage rack checklists.
Design
- Have industrial steel storage racks been designed in accordance with American National Standards Institute (ANSI)/Rack Manufacturers Institute, Inc. (RMI) standard MH 16.1 specifications?
- Are modifications or rearrangements not within the original design not present? ANSI/RMI
- Are load application and rack configuration drawings available for each rack installation? ANSI/RMI
Installation
- Are racks installed on flooring (i.e., concrete) that will support the associated loads?
- ANSI/RMIIs flooring in good repair under and around racks?
- Are shims made of materials that meet or exceed the design bearing strength or allowable bearing strength of the floor? ANSI/RMI
- Is shim size and location under the base plates equal to or greater than the required base plate size and location? ANSI/RMI
- Does the total thickness of shims not exceed six times the diameter of the largest anchor bolt used in that base? ANSI/RMI
- Are shims interlocked or welded together if the total thickness is less than or equal to six times the anchor bolt diameter under bases with less than two anchor bolts? ANSI/RMI
Placarding
- Do storage racks display a permanent plaque that indicates load capacity? ANSI/RMI & General Duty Clause
- Is the plaque conspicuously located? ANSI/RMI
- Is the plaque at least 50 square inches? ANSI/RMI
- Does the plaque show clear, legible print? ANSI/RMI
- Does the plaque display the maximum permissible unit load and/or maximum uniformly distributed load per level? ANSI/RMI
- Does the plaque display the average unit load? ANSI/RMI
- Does the plaque display the maximum total load per bay? ANSI/RMI
- Are storage levels having multiple stacking of unit loads identified? ANSI/RMI
Anchoring
- Are rack columns anchored to the floor? ANSI/RMI & General Duty Clause
- Are an appropriate number of anchors, as recommended by the rack manufacturer, used? ANSI/RMI
- Are the anchors used the correct size as recommended by the rack manufacturer? ANSI/RMI
- Are an appropriate number of anchor bolts, as recommended by the rack manufacturer, used? ANSI/RMI
- Are the anchor bolts used the correct size as recommended by the rack manufacturer? ANSI/RMI
- Is decking fastened to the beams to prevent deck dropping? ANSI/RMI
Condition
- Are racks inspected and maintained per the manufacturer’s guidelines?
- Are racks plumb from top to bottom? ANSI/RMI
- Are rack columns straight? ANSI/RMI
- Are rack columns in good repair? ANSI/RMI
- Has frame bracing been installed as recommended by the manufacturer? ANSI/RMI
- Is frame bracing in good repair? ANSI/RMI
- Are anchors in good repair? ANSI/RMI
- Are column base plates in good repair? ANSI/RMI
- Are deflectors, fenders, and bumpers protecting the column as necessary? ANSI/RMI
- Is decking in good repair? ANSI/RMI
- Are other rack components (e.g., deflector angles, backer posts, etc.) in good repair? ANSI/RMI
Loads
- Is the weight of materials stored on storage racks below the load capacity rating? ANSI/RMI
- Are the heaviest products stored on the floor or lower levels and toward the middle of the rack system? ANSI/RMI
- Are pallets in good repair? ANSI/RMI
- Are pallets placed onto pallet load support members in a properly stacked and stable position? ANSI/RMI
- Are boxes, pallets, bags, containers, and other materials stacked/piled neatly? ANSI/RMI & 1910.176(b)
- Are stacks secure against sliding or collapse? 1910.176(b)
- Are stacks limited in height? 1910.176(b)
Fire protection and prevention
- Are racks, and materials stored on them, in accordance with local fire codes?
- Are materials on racks stored no closer than 18 inches away from sprinklers? 1910.159(c)(10)
Recordkeeping
- Has one copy of load application and rack configuration drawings of storage racks used been retained? ANSI/RMI
- Has one copy of load application and rack configuration drawings of storage racks used been retained by the dealer or manufacturer? ANSI/RMI
Welding
OSHA’s Subpart O regulations apply to all welders and welding operators who operate electric or gas welding and cutting equipment. The standards apply whether you have a single portable welding unit to do an occasional spot welding task, or if you have large electric welders to use in daily production.
Action steps
- Follow safety precautions for fire prevention and protection.
- Maintain suitable fire extinguishers.
- Provide a fire watch where required.
- Ensure areas are inspected and a permit issued before welding is allowed.
- Follow proper welding procedures.
- Provide PPE as needed.
- Ensure safety when working in confined spaces.
- Handle welding materials and equipment properly.
- Ensure proper marking of welding materials and equipment.
- Provide suitable ventilation.
- Maintain welding equipment.
Training action plan
Cutters, welders, and their supervisors are required to be trained in the safe operation of welding equipment. Also, fire watchers shall be trained in the use of fire extinguishing equipment. Training content should generally cover:
- Welding safety program guidelines established at your company,
- Welding hazards,
- Safe work practices,
- Fire watches,
- Welding safety when working in confined spaces, and
- Housekeeping.
Consider other safety training issues relative to your welding operations:
- Hazard communication for all hazardous substances generated during welding (e.g., certain gases, fluxes, wires, and rods contain cadmium, fluorides, zinc, beryllium, and so on, and require various protections).
- Spill cleanup procedures under HAZWOPER for leaky oxy fuel type cylinders or for situations with explosion or fire potential.
- Personal protective equipment, especially where respirators are required and eye shades are needed for arc welding operations.
- Employees must be informed of the status of their exposure records each year.
- Construction regulation requirements where welding operations involve new structures or modification of existing structures.
- Electrical codes for exposed live parts.
Training is required prior to or at the time of initial assignment.
Documentation
OSHA does not require training documentation for safety training on welding, but it is always prudent to keep records anyway. Training records can tell you who was trained on what, when, and who conducted the training.
Tips
- Adverse effects of overexposure to welding fumes can be acute or may occur only after repeated exposures.
- The hazards presented by welding fumes will vary based upon: the base material, the filler material, the gases being used, current level, arc length, and other factors.
- Welding fumes can cause nausea, headaches, dizziness, and metal fume fever.
Checklists
Follow these checklists to ensure welding safety at your facility.
General
- Are only authorized and trained personnel permitted to use welding, cutting, or brazing equipment?
- Are pressure-reducing regulators used only for the gas and pressures for which they are intended?
- Does each operator have a copy of the appropriate operating instructions and are they directed to follow them?
- Is a check made for adequate ventilation in and where welding or cutting is performed?
- Is red used to identify acetylene (and other fuel-gas) hose, green for oxygen hose, and black for inert gas and air hose?
- When working in confined places, are environmental monitoring tests taken and means provided for quick removal of welders in case of an emergency?
- Are compressed gases used and handled properly?
Welding: Equipment
- Are only approved apparatus (torches, regulators, pressure-reducing valves, acetylene generators, manifolds) used?
- Is grounding of the welding machine frame and safety ground connections of portable machines checked periodically?
- Is necessary personal protective equipment available?
- Is open circuit (No Load) voltage of arc welding and cutting machines as low as possible and not in excess of the recommended limits?
Welding: Fire prevention
- Are compressed gas cylinders kept away from sources of heat?
- Are fire watchers assigned when welding or cutting is performed in locations where a serious fire might develop?
- Are precautions taken to prevent the mixture of air or oxygen with flammable gases, except at a burner or in a standard torch?
- Are provisions made for personnel to perform fire watch duties under appropriate circumstances?
- Are provisions made to never crack a fuel-gas cylinder valve near sources of ignition?
- Are signs reading “DANGER NO SMOKING, MATCHES, OR OPEN LIGHTS” or the equivalent, posted in welding areas?
- Before hot work is begun, are used drums, barrels, tanks, and other containers so thoroughly cleaned that no substances remain that could explode, ignite, or produce toxic vapors?
- If welding gases are stored, are oxygen and acetylene separated by a 5-foot noncombustible barrier?
- Is combustible scrap, debris, and waste stored safely and removed from the work site promptly?
- When welding is done on metal walls, are precautions taken to protect combustibles on the other side?
Identifying Mechanical Hazards
What are mechanical hazards?
Power-driven equipment and machines pose many hazards to employees, particularly when used improperly or without adequate safeguards. Workers are at risk of lacerations, amputations, severed fingers, and blindness. If equipment is not properly grounded, a metal framework could become energized and possibly electrocute an employee. When driving a forklift in an unsafe manner, the operator runs the risk of tipping the vehicle or striking a pedestrian.
As a safety professional, you must know and understand the hazards posed by power-driven tools, equipment, and machines in your company. Employees using the equipment have to be adequately trained, not only in how to use it properly, but also must be made aware of the consequences of taking short-cuts, disabling or removing guards, and not following standard policies and procedures such as locking out equipment prior to maintenance or repairs.
Many OSHA standards have specific requirements for protecting employees from mechanical hazards. In this section, you will find action steps, tips, answers to frequently asked questions, checklists, and training exercises and handouts on a variety of topics related to mechanical hazards. All of these will help you ensure a safer workplace for those employees who work with powered tools, machines, and equipment.
Cranes
If you use industrial cranes or derricks in your workplace, then the regulations at 1910.179 through .181 apply. Among other things, these regulations require that only designated personnel must operate the equipment, and only authorized representatives should perform equipment repairs.
Action steps
- Use only ANSI approved cranes.
- Test new or altered cranes to ensure compliance with OSHA regulations.
- Ensure any modifications are checked thoroughly by a qualified engineer or the equipment manufacturer.
- Ensure the rated load of the crane is plainly marked on each side of the crane and on each hoisting unit if there is more than one hoisting unit.
- Maintain clearances as required by OSHA.
- Allow only designated personnel to operate a crane.
- Ensure equipment is adequate.
- Provide footwalks, ladders, and stairways as required.
- Install stops, bumpers, rail sweeps, and guards where needed.
- Make sure brakes are adequate.
- Ensure electric equipment complies with OSHA requirements.
- Inspect equipment and remove or repair any defective equipment.
- Maintain equipment.
- Follow manufacturer’s operating instructions.
Training action plans
Only designated personnel are permitted to operate a crane. These employees should receive adequate training to operate the equipment. This includes:
- Understanding the crane’s load-limit
- Lifting loads properly
- Positioning the hook
Training is to be provided prior to or at the time of initial assignment. No specific training documentation is required.
Tips
Tips for crane inspection include:
- Review the crane manufacturer’s inspection and maintenance requirements.
- While the engine is running, check all gauges and warning lights for proper readings and operate all controls to see that they are functioning properly.
- Check for any broken or cracked glass that may affect the view of the operator.
- Look at crane cab for properly marked controls, damaged instruments and for properly displayed and legible load charts.
- Inspect for excessive wear on drive sprockets and/or chain stretch.
- Check crane set up and stability of outriggers on hydraulics and/or the effectiveness of cribbing on crawlers.
- If possible, request that the crane be rotated to check all clearances and overall stability.
- Do not leave crane controls when the engine is running or when the platform is occupied.
- Stop all hoisting operations if there are any indications of danger, including weather conditions.
- Do not make any lifts on another load line of a crane or derrick that is being used to hoist personnel.
Checklist
Use these checklists to make sure your crane inspections keep everyone safe and compliant.
Daily visual inspection
- Is the crane visually inspected every day prior to use?
- Does visual inspection include checking for adjustment problems that may interfere with proper operation?
- Do you also check for deterioration or leakage in lines, tanks, valves, drain pumps, and other parts of air or hydraulic systems?
- Do you look for signs of wear, twist, cracks, distorted links, or excessive stretch in hooks, hoist chains, and end connections?
Frequent inspections (daily to monthly)
- Are “frequent” inspections (must include all of the adjustment and deterioration items under the daily inspection) performed as required?
- Do you also check for operating mechanisms with excessive component wear?
- Do you check for rope reeving that is not in compliance with manufacturer’s recommendations?
Periodic inspections (every 1-12 months)
- Are “periodic” inspections (must include all items under “frequent” inspection) performed as required?
- Are there no deformed, cracked, or corroded members?
- Do you make sure there are no loose bolts or rivets?
- Do you check for cracked or worn sheaves and drums?
- Are there no worn, cracked, or distorted parts such as pins, bearings, shafts, gears, rollers, locking and clamping devices?
- Do you check for excessive wear on brake system parts, linings, pawls, and ratchets?
- Do you make sure there are no inaccuracies in load, wind, and other indicators over their full range?
- Is the machine’s engine or motor performing properly?
- Are chain drive sprockets free of excessive wear and chain stretch?
- Do you look for signs of pitting or deterioration of electrical controller contacts, limit switches, and pushbutton stations?
Inspection documentation
- Are monthly, frequent, and periodic inspections documented?
- Does documentation of inspection include the signature of the person conducting the inspection?
- Does documentation also include the date of the inspection and an identification of the parts inspected?
Monthly rope inspections
- Are running ropes checked at least monthly?
- Are ropes that have been idle for a month or more due to shutdown of crane given a thorough inspection before use?
Dockboards
A dockboard is a portable or fixed device that spans a gap or compensates for a difference in elevation between a loading platform and a transport vehicle. Dockboards include, but are not limited to, bridge plates, dock plates, and dock levelers.
Action steps
- Ensure that dockboards can support the maximum intended load.
- Ensure that transfer vehicles cannot run-off the edge of the dockboard, unless they can prove there is no run-off hazard.
- Secure portable dockboards from moving while being used by employees.
- Ensure that portable dockboards have handholds or another means for safe transport.
- Prevent the accidental movement of transport vehicles while it is being used by employees.
Training action plans
Training must consist of a combination of formal instruction (e.g., lecture, discussion, interactive computer learning, DVD, written material), practical training (demonstrations performed by the trainer and practical exercises performed by the trainee), and evaluation of the operator’s performance in the workplace.
Training should cover the following topics:
- When and what type of dockboard to use
- Placement (using handholds)
- Capacity
- Inspection
- Placement check
- Securing the dockboard
- Communication with transport vehicle driver
- Periodically checking the dockboard during loading/unloading
Tips
- Make certain portable dockboards have a means for safe handling. OSHA suggests handholds or other means of gripping the dockboard. When portable dockboards will be moved mechanically, OSHA suggests the use of forklift loops, lugs, or other effective means.
- Use wheel chocks to prevent the transport vehicle from moving during loading.
- Train employees on recognizing the type of dockboard to use.
Checklist
Use these checklists to ensure dockboards are being used correctly.
Design and construction
- Are all dockboards used capable of supporting the maximum intended load?
- Do dockboards that are put into initial service on or after January 17, 2017, have means (such as run-off guards or curbs) to prevent vehicles from running off the edge (unless it can be demonstrated there is no run-off hazard)?
- Are portable dockboards equipped with handholds or other means to permit safe handling?
Use
- Are portable dockboards secured by anchoring in place or using equipment or devices that prevent the dockboard from moving out of a safe position?
- When securing the dockboard is not feasible, is there sufficient contact between the dockboard and the surface to prevent the dockboard from moving out of a safe position?
- Are measures, such as wheel chocks or sand shoes, used to prevent transport vehicles (e.g., a truck, semitrailer, trailer, or rail car) from moving while employees are on the dockboard?
Fall protection
- Is each employee on a dockboard protected from falling 4 feet or more to a lower level by a guardrail system or handrails? Note: This does not apply when dockboards are being used solely for materials-handling with motorized equipment, the fall hazard is 10 feet or less, and the employees have been properly trained.
Inspection and maintenance
- Are dockboards inspected regularly, and as necessary, to ensure they are in safe condition?
- Are deficiencies corrected or repaired before an employee uses the dockboard again?
- If a dockboard correction or repair cannot be made immediately, are employees prevented from using the dockboard until repaired?
- If a dockboard repair involves structural integrity, does a qualified person perform or supervise the correction or repair?
Training
- Is each employee who uses a dockboard trained to properly place and secure the equipment?
- Is each employee who uses a dockboard trained to recognize the fall hazards in the work area?
- Is training conducted by a qualified person?
Note: Qualified describes a person who, by possession of a recognized degree, certificate, or professional standing, or who by extensive knowledge, training, and experience has successfully demonstrated the ability to solve or resolve problems relating to the subject matter, the work, or the project. - Is information and training provided in a manner that each employee understands?
- Is retraining provided when deficiencies in performance or knowledge are noted, or there are changes in the workplace or equipment?
Electrical safety
OSHA’s electrical safety regulation 1910, Subpart S, is divided into two parts: Installation of Electrical Systems and Safety-Related Work Practices. 1910.399 provides important definitions for both parts. The first section Installation of Electrical Systems, 1910.302 to .308, for the most part, covers installation of electrical equipment. Its use is very similar to the National Electrical Code: electrical equipment installation. However, there are some sections of the installation requirements that do cover electrical safety. The primary example is providing appropriate working space for equipment likely to require examination, adjustment, servicing, or maintenance while energized. That “working space” is generally “built-in” when electrical equipment is installed. The requirements for ground-fault circuit interrupters are another example. The second section, Safety-Related Work Practices, 1910.331 to .335, provides requirements for electrical training, selecting appropriate work practices, lockout/tagout, and working on exposed energized parts.
The first priority in electrical work is locking out and tagging the equipment rendering it “electrically safe.” If that is not possible, then employers must ensure employees are protected against electrical hazards through safe work practices and appropriate PPE. The OSHA regulations do provide shock protection methods in 1910.137—Electrical protective devices. However, the OSHA rules do not provide for arc flash/blast protection. To protect employees from those hazards, employers must refer to an outside source such as the National Fire Protection Association’s NFPA 70E—Standard for Electrical Safety in the Workplace.
Action steps
- Ensure electrical equipment is approved and free from recognized hazards.
- Use listed or labeled equipment according to the instructions included in the listing or labeling.
- Ensure lockout/tagout procedures are provided and used when employees work on electrical components/systems.
- Determine that appropriate space is provided for electrical equipment that will likely require examination, adjustment, servicing, or maintenance while energized.
- Provide appropriate electrical personal protective equipment, insulated hand tools, and meters to protect employees from shock and arc flash/blast hazards when they must work on energized components/systems.
Training action plan
OSHA’s training requirements regarding electrical work apply to employees who face a risk of electric shock that is not reduced to a safe level by the electrical installation requirements of 1910.303 through 1910.308.
Content of training
Employees must be trained in and familiar with the safety-related work practices required by 1910.331 through 1910.335 that pertain to their respective job assignments. Unqualified persons must be trained in and familiar with any electrically-related practices necessary for their safety. Qualified persons (i.e., those permitted to work on or near exposed energized parts) must, at a minimum, be trained in and familiar with the following:
- The skills and techniques necessary to distinguish exposed live parts from other parts of electric equipment.
- The skills and techniques necessary to determine the nominal voltage of exposed live parts.
- The clearance distances specified in 1910.333(c) and the corresponding voltages to which the qualified person will be exposed.
Qualified employees whose work involves direct contact with energized equipment or contact using tools or materials must be capable of working safely and must be familiar with special precautionary techniques, appropriate PPE, insulating and shielding materials, and insulated tools.
The training must be of the classroom or on-the-job type. The degree of training provided must be determined by the risk to the employee.
Tips
- Use the National Electric Code (NFPA 70) and the NFPA 70E Standard for Electrical Safety in the Workplace as references for electrical questions and issues. The National Electric Code corresponds to OSHA’s Installation of Electrical Systems, 1910.302 to .308. The NFPA 70E supplements OSHA’s Safety-Related Work Practices, 1910.331 to .335.
- For arc flash/blast protection, use an outside source, such as the NFPA 70E for employee protection.
- When employees are working in the vicinity of or using conductive objects such as ladders, scaffolds, and work platforms around overhead power lines, the lines must be:
- Deenergized and grounded, or
- Guarded, isolated, or insulated, or
- Clearance distances provided in 1910.333(c) must be maintained.
Checklist
Use the checklists below to make sure your company has all its electrical safety measures in place.
Examination, installation, and use of equipment
- Are only approved conductors and equipment used for electrical installations?
- Is equipment used and installed in accordance with instructions on the listing or label?
- Is all electrical equipment free from recognized hazards that are likely to cause death or serious physical harm?
Arcing parts
- Are all parts of electrical equipment that ordinarily produce arcs, sparks, flames, or molten metal enclosed or isolated from all combustible material?
Marking
- Is all electrical equipment marked with the manufacturer’s identity?
- Is all electrical equipment marked with the voltage, current, wattage, ratings, and other markings as necessary?
- Are all overcurrent devices (circuit breakers, fuses, etc.) legibly marked to indicate their purpose?
Working space
- Is access and working space around electrical equipment sufficient to provide ready and safe operation and maintenance?
- Are required working spaces around electrical equipment kept free of stored materials?
Guarding of live parts
- Are live parts of electrical equipment operating at 50 volts or more guarded against contact by approved cabinets or other forms of approved enclosures? (Note: See the regulations for exceptions.)
- In areas where electrical equipment may be exposed to physical damage, are the enclosures or guards arranged and of such strength to prevent such damage?
- Are all entrances to rooms or other guarded locations containing exposed live parts marked with conspicuous warning signs forbidding unqualified persons to enter?
- When normally enclosed live parts are exposed for maintenance and repair, are they guarded to protect unqualified persons from contact?
- Are safety signs, safety symbols, or accident prevention tags used where necessary to warn employees about electrical hazards?
Forklifts
OSHA’s 1910.178 regulation applies to all persons who use powered industrial trucks for such things as lifting, pulling, stacking, and moving materials. The regulation does not apply to compressed air or nonflammable compressed gas-operated industrial trucks, nor to farm vehicles, nor to vehicles intended primarily for earth moving, or over-the-road hauling.
Action steps
- Select appropriate and approved equipment.
- Make sure name plates and markings are adequate.
- Use only approved equipment for the particular area.
- Store and handle fuels safely.
- Change, charge, and store batteries properly.
- Provide emergency response equipment for flushing and neutralizing spilled electrolyte, for fire protection, for protecting charging apparatus from damage by trucks, and for adequate ventilation for dispersal of fumes from gassing batteries.
- Set brakes of highway trucks and chock wheels when they are boarded with powered industrial trucks.
- Ensure forklift operators are competent and have completed training.
- Certify operator training.
- Ensure proper operation and loading of forklifts.
- Inspect trucks daily before each shift.
- Perform appropriate maintenance.
- Remove damaged equipment from use.
Training action plans
Training must consist of a combination of formal instruction (e.g., lecture, discussion, interactive computer learning, DVD, written material), practical training (demonstrations performed by the trainer and practical exercises performed by the trainee), and evaluation of the operator’s performance in the workplace.
Training should cover the following topics:
- Safe operation
- Truck-related topics:
- Operating instructions, warnings, and precautions for the types of truck the operator will be authorized to operate
- Differences between the truck and the automobile
- Truck controls and instrumentation: where they are located, what they do, and how they work
- Engine or motor operation
- Steering and maneuvering
- Visibility (including restrictions due to loading)
- Fork and attachment adaptation, operation, and use limitations
- Vehicle capacity
- Vehicle stability
- Any vehicle inspection and maintenance that the operator will be required to perform
- Refueling and/or charging and recharging of batteries
- Operating limitations
- Any other operating instructions, warnings, or precautions listed in the operator’s manual for the types of vehicle that the employee is being trained to operate
- Workplace-related topics:
- Surface conditions where the vehicle will be operated
- Composition of loads to be carried and load stability
- Load manipulation, stacking, and unstacking
- Pedestrian traffic in areas where the vehicle will be operated
- Narrow aisles and other restricted places where the vehicle will be operated
- Hazardous (classified) locations where the vehicle will be operated
- Ramps and other sloped surfaces that could affect the vehicle’s stability
- Closed environments and other areas where insufficient ventilation or poor vehicle maintenance could cause a buildup of carbon monoxide or diesel exhaust
- Other unique or potentially hazardous environmental conditions in the workplace that could affect safe operation
Refresher training must be given when needed and employers must perform a triennial evaluation of forklift operators.
Tips
- Use seatbelts if they are available.
- Do not jump from an overturning, sit-down type forklift. Stay with the truck, holding on firmly and leaning in the opposite direction of the overturn.
- Do not raise or lower the forks while the forklift is moving.
- Do not allow passengers to ride on forklift trucks unless a seat is provided.
- Do not drive to another location with the work platform elevated.
Checklist
The checklists below will help you and your company ensure all forklift operations are done safely and compliantly.
Forklift operations
- Are the forklifts in your facility correctly designated for your type of operation (based on atmosphere, hazards of materials handled, etc.)?
- Are the brakes on each industrial truck capable of bringing the vehicle to a complete and safe stop when fully loaded?
- Is directional lighting provided on each industrial truck that operates in an area with less than 2 foot-candles per square foot of general lighting?
- Will the industrial truck’s parking brake effectively prevent the vehicle from moving when unattended?
- Are the required lift truck operating rules posted and enforced?
- Are industrial trucks equipped with flashing lights, horn, overhead guard, and name plate (load limits)?
Fueling
- Are fueling operations done in such a manner that the likelihood of spillage will be minimal?
- Is filling fuel tanks prohibited while engines are running?
- When spillage occurs during fueling operations, are measures taken to control vapors before restarting the engine?
Training
- Are only trained personnel allowed to operate industrial trucks?
- Have you documented what methods you use to train forklift operators?
Maintenance and inspection
- Are your forklifts inspected before being placed in service? Inspections should be at least daily, or after each shift, if used around the clock.
- Are adequate inspection and maintenance records kept?
- Are all industrial trucks not in safe operating condition removed from service?
- Are repairs to fuel and ignition systems conducted only in areas specifically designated for them?
Lockout/tagout
OSHA’s 1910.147 regulation establishes minimum performance requirements for the control of hazardous energy and applies to general industry. The regulation covers the servicing and maintenance of machines and equipment in which the unexpected startup or the release of stored energy could cause injury to employees. If employees are performing servicing or maintenance tasks that do not expose them to the unexpected release of hazardous energy, the regulation does not apply.
Action steps
- Establish a program and utilize procedures for affixing appropriate lockout devices or tagout devices to energy isolating devices, and to otherwise disable machines or equipment to prevent unexpected energization, start up, or release of stored energy.
- Utilize lockout when possible.
- Use tagout when lockout is not possible.
- Use appropriate lockout/tagout devices.
- Standardize lockout and tagout devices within the facility.
- Conduct a periodic inspection of the energy control procedure at least annually.
- Provide training as required by OSHA.
- Ensure proper exchange of safety information when working with contractors.
Training action plan
OSHA requires that all authorized employees be trained in recognition of hazardous energy sources, hazardous energy sources in use at their facility, and how to perform the lockout/tagout procedure.
OSHA also requires that all affected employees must be trained in the purpose and use of lockout/tagout.OSHA requires that all other employees must be instructed on the purpose of the plan, but not in the actual use.
OSHA requires that retraining be done when there are changes in equipment, job assignment, or procedures; when an audit shows deficiencies with the procedure; and when the employer feels the procedures should be reviewed.
Some general lockout/tagout training topics include:
- Description of hazardous energy sources: electrical, mechanical, pneumatic, hydraulic, chemical, thermal, water under pressure, gravity, and potential energy (stored energy)
- Why lockout/tagout is necessary
- The functions covered by lockout/tagout
- What an energy control program is
- Steps for preparation of the shutdown
- Application of lockout/tagout devices
- Description of lockout devices to be used
- Description of tags and types of tags to be used
Tips
- Ensure that lockout/tagout devices identify the individual users.
- Lockout/tagout does not apply when the employee is performing minor tool changes or other minor servicing activities that are routine, repetitive, and integral to production, and that occur during normal production operations. In these cases, employees must have effective, alternative protection.
- A tagout device may evoke a false sense of security. OSHA considers lockout devices to be more secure and more effective than tagout devices in protecting employees.
- If an outside contractor services or maintains machinery, the onsite employer and the contractor must inform each other of their respective lockout or tagout procedures.
- Employers need to review their lockout/tagout procedures at least once a year.
Checklist
Use these checklists to check that all processes for lockout/tagout are done correctly, including recordkeeping, training, and inspections.
- Are appropriate employees provided with individually keyed personal safety locks?
- Are correct lockout/tagout procedures in use?
- Are equipment control valves provided with a means for locking out?
- Are provisions made to prevent machines from automatically starting after a shutdown?
- Are suspended loads or potential energy (such as compressed springs, hydraulics, or jacks) controlled to prevent hazards?
- Is all machinery or equipment capable of movement, required to be de-energized or disengaged and locked out during cleaning, servicing, adjusting or setting up operations, whenever required?
- Is the locking-out of control circuits in lieu of locking-out main power disconnects prohibited?
- Is there a means provided to identify employees who are working on locked-out equipment by their locks or accompanying tags?
Recordkeeping
- Do you specify steps for the placement, removal and transfer of lockout/tagout devices, and the responsibility for them?
- Do you specify steps for the shutting down, isolating, blocking, and securing machines or equipment to control hazardous energy?
- Have you developed and documented procedures for the control of potentially hazardous energy?
Devices
- Are lockout/tagout devices singularly identified?
- Are lockout/tagout devices capable of withstanding the environment to which they are exposed for the maximum period of time that exposure is expected?
- Are lockout/tagout devices standardized within the facility in at least one of the following criteria: Color; shape; or size; and additionally, in the case of tagout devices, print and format shall be standardized?
- Are tagout device attachment means of a non-reusable type, attachable by hand, and self-locking?
Energy control procedure inspection
- Do you conduct a periodic inspection of the energy control procedure at least annually?
- Is periodic inspection performed by an authorized employee other than the ones(s) utilizing the energy control procedure being inspected?
- Do you certify that the periodic inspections of the energy control procedure have been performed?
Training
- Have employees been trained properly to perform their roles and responsibilities regarding lockout/tagout?
Machine guarding
OSHA’s Subpart O regulations apply to the safeguarding of many types of machines, such as woodworking machinery, abrasive wheels, mills and calendars, power presses, forging machines, and mechanical power transmission apparatus. Machines not listed must comply with the current industry standards for that piece of equipment.
Action steps
- Provide one or more methods of machine guarding to protect the operator and other employees in the machine area from hazards such as those created by point of operation, ingoing nip points, rotating parts, flying chips and sparks.
- Ensure the point of operation of machines is guarded.
- Ensure necessary guards are affixed and secured.
- Anchor machines designed for a fixed location to prevent walking or moving.
Training action plan
OSHA does not specifically require employers to train employees on machine guarding. However, workers should be trained in methods of protection from the hazards created by rotating parts and reciprocating or transverse motions during equipment operation.
Generally, machine guard training should cover:
- Types of guards used
- Reasons NOT to remove guards
- Reporting damaged guards
- Safe operation of the equipment
Tips
- Any machine part, functions, or process that may cause injury must be guarded.
- Guards must not create potential hazards and must be attached to the machine where possible — attach elsewhere if it is not possible to attach to the machine.
- If specific standards are not available, make sure the machine construction prevents the operator from having any part of his/her body in the danger zone during the operating cycle.
Checklist
Use these checklists to make sure all the machines at your facility are safely guarded to avoid incidents.
General
- Are all moving chains and gears properly guarded?
- Are machinery guards secure and so arranged that they do not offer a hazard in their use?
- Are rotating or moving parts of equipment guarded to prevent physical contact?
- Are the noncurrent-carrying metal parts of electrically operated machines bonded and grounded?
- Are work positions, machinery, pits or holes, and hazardous operations adequately guarded?
- Are workers protected from sharp objects which might pierce the feet or cut the hands (e.g., machinery, food handling and storage, sawing and cutting)?
- Is sufficient clearance provided around and between machines to allow for safe operations, set up and servicing, material handling, and waste removal?
Portable power tools
- Are grinders, saws, and similar equipment provided with appropriate safety guards?
- Are power tools used with the correct shield, guard, or attachment recommended by the manufacturer?
- Does each portable power tool have a constant pressure switch (dead man switch) that will shut off the power when pressure is released?
Stationary equipment
- Are all pulleys and belts that are within seven feet of the floor or working level properly guarded?
- Are fan blades protected with a guard having openings no larger than 1/2 inch, when operating within seven feet of the floor?
- Are foot-operated switches guarded or arranged to prevent accidental actuation by personnel or falling objects?
- Are machines constructed so as to be free from excessive vibration when the largest size tool is mounted and run at full speed?
- Are radial arm saws so arranged that the cutting head will gently return to the back of the table when released?
- Are saws used for ripping equipped with anti-kick back devices and spreaders?
- Are splash guards mounted on machines that use coolant to prevent the coolant from reaching employees?
- Are workers protected from fixed objects that may cause injury, such as sharp machine edges?
- Do arbors and mandrels have firm and secure bearings and are they free from play?
- Is equipment and machinery securely placed and anchored, to prevent moving?
- Is fixed machinery provided with appropriate safety guards to prevent injuries to the operator and other employees resulting from point of operation, ingoing nip point, rotating parts, flying chip, and spark hazards?
- Is there a power shut-off switch within reach of the operator’s position at each machine?
Pallet jacks (powered/motorized)
Powered/motorized pallet jacks are a common fixture in many industries and workplaces. They allow workers to quickly move heavy loads from one location to another, go in tight spaces that forklifts cannot, and conveniently make frequent stops to “pick” materials. While they may seem like a straightforward and harmless piece of machinery, the fact is powered pallet jacks can pose deadly hazards if not operated properly and by trained individuals. In fact, OSHA requires training of powered pallet jack operators under the same requirement as that for forklift operators—the 1910.178 Powered Industrial Truck regulation.
Action steps
- Certify operator training. Just because an operator is trained/certified to operate a forklift does not make them automatically certified to operate a powered pallet jack: training must be specific to each “type” of equipment.
- Select appropriate and approved equipment.Make sure name plates, markings, and warning labels are in place and adequate.
- Use only approved equipment for the particular area.
- Change, charge, and store batteries properly.
- Provide emergency response equipment for flushing and neutralizing spilled electrolyte, for fire protection, for protecting charging apparatus from damage by trucks, and for adequate ventilation for dispersal of fumes from gassing batteries.
- Set brakes of highway trucks and chock wheels when they are boarded with powered industrial trucks.
- Ensure proper operation and loading.
- Inspect trucks daily before each shift.
- Perform appropriate maintenance.
- Remove damaged equipment from use.
- Become familiar with and follow the manufacturer’s operation, safety, and maintenance instructions.
Training action plans
Training must consist of a combination of formal instruction (e.g., lecture, discussion, interactive computer learning, video tape, written material), practical training (demonstrations performed by the trainer and practical exercises performed by the trainee), and evaluation of the operator’s performance in the workplace.Training should cover the following topics:
- Safe operation
- Truck-related topics:
- operating instructions, warnings, and precautions for the types of pallet jacks the operator will be authorized to operate
- differences between the pallet jack and the automobile
- controls and instrumentation: where they are located, what they do, and how they work
- engine or motor operation
- steering and maneuvering
- visibility (including restrictions due to loading)
- fork and attachment adaptation, operation, and use limitations
- capacity
- stability
- any inspection and maintenance that the operator will be required to perform
- refueling and/or charging and recharging of batteries
- operating limitations
- any other operating instructions, warnings, or precautions listed in the operator’s manual
- Workplace-related topics:
- surface conditions where the equipment will be operated
- composition of loads to be carried and load stability
- load manipulation
- pedestrian traffic in areas where the equipment will be operated
- hazardous (classified) locations where the vehicle will be operated
- ramps and other sloped surfaces that could affect stability
Refresher training must be given when needed and employers must perform a triennial evaluation of forklift operators.
Tips
- Be careful of rear-end swing when turning corners. The rear end will swing wide to the outside of a turn when operating with the load end leading. Extra clearance may be needed to avoid striking racking, pedestrians, etc.
- Check the data plate to determine the grades/inclines the equipment can operate safely on. When walking with a pallet truck with or without a load, the forks should be pointed downgrade, regardless of direction of travel. On walkie/riders, when in the riding position travel with loaded trucks with the load upgrade; when empty with the load end downgrade.
- Always look in the direction of travel. Pallet jack operators have had fingers and other parts crushed between the pallet jack and racks and walls—in particular, when backing out.
- Do not ride powered pallet jacks. Only walkie/riders have a platform for riding.
- Do not allow passengers on pallet jacks or walkie/riders.
- Inspect truck trailers before entering. Pallet jacks are heavier than they look and combined with a load can fall through a worn floor.
Checklist
These checklists will help ensure all pallet jacks are functioning safely and being used correctly.
Pallet jack operations
- Are the pallet jacks in your facility correctly designated for your type of operation (based on atmosphere, hazards of materials handled, etc.)?
- Are the brakes on each industrial truck capable of bringing the vehicle to a complete and safe stop when fully loaded?
Training
- Are only trained personnel allowed to operate pallet jacks?
- Have you documented what methods you use to train operators?
Maintenance and inspection
- Are your pallet jacks inspected before being placed in service? Inspections should be at least daily, or after each shift, if used around the clock.
- Are adequate inspection and maintenance records kept?
- Are all industrial trucks not in safe operating condition removed from service?
- Does the inspection include all items recommended by the manufacturer? At minimum, these typically include:
- Forks
- Brakes
- Quick disconnect, if equipped
- Hand guard
- Controls
- Battery and battery securing mechanism
- Warning labels/data plates
- Hydraulics (including fluid leaks)
- Horn
- Belly button, if equipped
Portable tools
OSHA’s 1910.242 regulation on hand and portable power tools applies to all employers who are responsible for the safe condition of tools and equipment used by employees, including tools and equipment that may be furnished by employees.
Action steps
- Ensure the safe condition of tools and equipment used by employees, including tools and equipment which may be furnished by employees.
- Ensure that compressed air is not used for cleaning purposes except where reduced to less than 30 p.s.i. and then only with effective chip guarding and personal protective equipment.
- Ensure portable power tools are guarded properly.
- Follow manufacturer’s instructions regarding tools.
- Maintain and inspect tools to prevent safety hazards.
Training action plan
OSHA’s regulations do not have specific employee training requirements for portable tools, but employees who understand the hazards and know how to use hand and portable powered tools correctly will have less risk of injury.
You should train workers to recognize the hazards associated with the different types of tools and the safety precautions necessary to prevent or control those hazards.
Generally, training should cover:
- Maintenance of tools
- Using the right tool for the job
- Inspecting tools before use
- Following manufacturers’ instructions
- Using PPE
Tips
- Recondition or replace chisels and punches, which develop mushroomed head during use, as necessary.
- Inspect and replace broken, cracked, or fractured handles on hammers, axes, and similar tools.
- Make sure that grinders, saws, and similar equipment is only used with appropriate safety guards.
- Inspect pneumatic and hydraulic hoses on power operated tools for deterioration or damage on a regular basis.
- Dull tools are more dangerous than sharp ones —keep cutting tools properly sharpened.
Checklist
Use these checklists to make sure all portable tools are in good working order.
General
- Are all portable hand or power tools maintained in a safe condition?
- If compressed air is used for cleaning purposes, is it used at pressures less than 30 p.s.i. and only with effective chip guarding and personal protective equipment?
- Are power tools equipped and used with guards whenever possible?
- Are all belts, gears, shafts, pulleys, sprockets, spindles, drums, flywheels, chains, or other reciprocating, rotating or moving parts of equipment guarded if operator is exposed to contact or if they otherwise create a hazard?
- Is all necessary personal protective equipment provided whenever the use of hand and power tools could create falling, flying or splashing debris, or harmful dusts, fumes, mists, vapors, or gases?
- On hand-held power tools, is the operating control located so as to minimize the possibility of accidental operation?
- Are all portable, electrically powered tools properly grounded or double insulated?
- Are impact tools, such as drift pins, wedges, and chisels, kept free of mushroomed heads?
- Are the wooden handles of tools kept free of splinters or cracks and are they fixed tightly in the tool?
- Is it prohibited to lower or hoist a tool by the cord?
- Do woodworking tools meet the American National Standards Institute (ANSI) safety codes?
Pneumatic power tools and hose
- Are pneumatic power tools secured to the hose or whip by some positive means, so as to prevent the tool from being accidentally disconnected?
- Are safety clips or retainers used on pneumatic impact (percussion) tools to prevent attachments from being accidentally expelled?
- Are all pneumatically driven nailers, staplers, and other similar equipment which have automatic fastener feeds and which operate at more than 100 p.s.i. pressure at the tool equipped with a safety device on the nozzle to prevent the tool from ejecting fasteners, unless the muzzle is in contact with the work surface?
- Are all compressed air hoses and hose connections designed for the pressure and service to which they are subjected?
Identifying Health Hazards
What are health hazards?
A substance is considered a “health hazard” if exposure through skin or eye contact, inhalation, or ingestion causes temporary or permanent injury. The health effects to the exposed individual may be acute or chronic, resulting from repeated long-term exposure to low concentrations of a hazardous substance. Exposure to excessive temperatures is also considered a health hazard. Extreme heat can cause heat exhaustion or heat stroke, which is a life threatening condition.
Acute and chronic health effects
An acute health effect usually occurs rapidly, following a brief exposure. A chronic health effect is long and continuous and follows repeated long-term exposure. Some examples of chemicals which exhibit health hazards are:
- Carcinogens
- Acute and chronic toxins
- Irritants
- Corrosives
- Sensitizers
As a safety professional, you need to be aware of the dangerous substances and temperature extremes in your workplace that pose health risks to employees. Everyone whose job involves exposure, or the risk of exposure, to hazardous chemicals and hot environments must be adequately informed, trained, and protected.
Many OSHA standards have specific requirements for protecting employees from these hazards. In this section, you will find action steps, tips, answers to frequently asked questions, checklists, and training exercises and handouts on a variety of health-related topics. All of these will help you ensure a safer workplace for those employees with health hazard exposure risks.
Asbestos
OSHA’s 1910.1001 standard on asbestos covers workers who may be exposed to asbestos, a substance found in installed products such as shingles, floor tiles, cement pipe and sheet, roofing felts, insulation, ceiling tiles, fire-resistant drywall, and acoustical products. The standard reduces employee exposure to asbestos to 0.1 fiber per cubic centimeter of air (f/cc) averaged over an 8-hour day. The standard also sets an action level; it is 0.1 f/cc averaged over eight hours. If this level is exceeded, employers must begin compliance activities such as air monitoring, employee training, and medical surveillance.
Action steps
- Establish and implement a written program to reduce employee exposure to or below the TWA and to or below the excursion limit by means of engineering and work practice controls and by the use of respiratory protection.
- Institute a training program for all employees who are exposed to airborne concentrations of asbestos at or above the permissible exposure limit and/or excursion limit and ensure their participation in the program.
- Establish regulated areas wherever airborne concentrations of asbestos and/or PACM are in excess of the TWA and/or excursion limit.
- Follow proper hygiene practices and provide a clean room.
- Implement appropriate monitoring and medical surveillance.
- Ensure appropriate medical evaluation.
- Provide adequate personal protective equipment and clothing.
- Implement appropriate engineering controls and work practices.
- Provide appropriate signs and labels to warn of and identify asbestos hazards.
- Follow proper procedures for working with and removing asbestos.
Training action plan
You must provide training to employees who are exposed to airborne asbestos levels that are at or above the permissible exposure limit and/or excursion limit. Training content should include:
- Health effects associated with asbestos exposure.
- Relationship between smoking and exposure to asbestos in producing lung cancer.
- Quantity, location, manner of use, release, and storage of asbestos, and the specific nature of the operations that could result in exposure to asbestos.
- Asbestos location.
- Specific procedures implemented to protect employees from exposure to asbestos, such as appropriate work practices, emergency clean-up procedures, and PPE to be used.
- Proper use and the limitations of respirators and protective clothing.
- Purpose and description of worker protection programs.
Training is required prior to or at the time of initial assignment of asbestos-related work.
Documentation
Training records must be maintained for one year beyond an employee’s last day of employment.
Tips
- Employers must create controlled zones known as regulated areas that are designed to protect employees where certain work with asbestos is performed.
- Workers who handle asbestos should wash their faces, hands, and forearms thoroughly with soap and water before eating, smoking, or using toilet facilities.
Checklist
Use the checklists below to make sure your company is meeting all the necessary safety precautions.
Work practices
- Are proper precautions being taken when handling asbestos and other fibrous materials?
- Are wet methods used, when practicable, to prevent the emission of airborne asbestos fibers, silica dust, and similar hazardous materials?
- Is smoking prohibited in areas where occupational exposure to asbestos occurs?
Personal Protective Equipment
- Are respirators used during periods necessary to install or implement feasible engineering and work-practice controls?
- Are respirators used during work operations, such as maintenance and repair activities, for which engineering and work-practice controls are not feasible?
- Are respirators used during work operations for which feasible engineering and work-practice controls are not yet sufficient to reduce employee exposure to or below the TWA and/or excursion limit?
- Are respirators used during emergencies?
- Is appropriate personal protective equipment used when working with asbestos?
Facilities marking
- Are signs posted warning of the presence and hazards of asbestos, where required?
- Are signs posted so that an employee may read the signs and take necessary protective steps before entering the area?
- Are warning labels affixed to all materials, mixtures, waste, etc., containing asbestos fibers, or to their containers?
- Are required asbestos signs and labels in compliance with EPA’s asbestos marking requirements?
Bloodborne pathogens
OSHA’s 1910.1030 Bloodborne Pathogens standard applies to any employer with employees who are occupationally exposed to blood or other potentially infectious materials; this determination must be made without considering use of any personal protective equipment (PPE).
Action steps
- Develop a written exposure control plan to eliminate or minimize employee exposure.
- Provide information and training.
- Ensure handwashing requirements are met.
- Provide containers for infectious materials.
- Ensure proper disposal and care of contaminated sharps.
- Ensure proper servicing and shipping of infectious equipment.
- Follow proper procedures for regulated waste containment.
- Make the hepatitis B vaccine and vaccination series available to all employees who have occupational exposure.
- Prepare an exposure determination.
- Maintain proper records.
- Provide proper personal protective equipment.
- Use engineering and work practice controls to eliminate or minimize employee exposure.
- Use proper labeling for biohazards.
- Document annually consideration and implementation of appropriate commercially available and effective safer medical devices designed to eliminate or minimize occupational exposure.
Training action plan
All employees with occupational exposure to bloodborne pathogens need training in OSHA’s requirements and the employer’s exposure control plan. For example, this might include first aid responders, emergency response team members, or health care workers.
Training content should cover:
- The epidemiology and symptoms of bloodborne diseases.
- How trainees may contact bloodborne diseases.
- The company’s Exposure Control Plan (ECP).
- Recognizing potential exposures to blood and other potentially infectious materials. Engineering controls affecting trainees.
- Location of handwashing facilities.
- Work practices affecting workers.
- General approach and selection process for Personal Protective Equipment (PPE).
- The hepatitis B vaccine, including its efficacy, safety, method of administration, and benefits of getting the vaccination.
- The company’s procedure to respond to a worker who has been exposed to blood or other potentially infectious material on the job.
- Follow-up available to workers involved in an exposure incident.
- The signs and labels your company uses to warn workers of biohazards.
- Location and explanation of regulatory text and ECP.
Employees must be trained prior to initial exposure to bloodborne pathogens and at least annually thereafter.
Documentation
Very specific training records must be maintained. Information must include dates of training, contents of training sessions, names and qualifications of trainers, names and job titles of those trained. Records must be retained for three years.
Tips
- In determining who is covered by the Bloodborne Pathogens standard, remember that if an employee is providing first aid or CPR as a Good Samaritan and not as a trained first aider, designated to perform first aid by the employer, that employee is not covered by the standard.
- Regarding designated responders, OSHA compliance directive CPL 02-02-069 states, “An employee who routinely provides first aid to fellow employees with the knowledge of the employer may also fall, de facto, under this designation even if the employer has not officially designated this employee as a first aid provider.” For example, if first aid supplies are stored in a supervisor’s office, and the supervisor regularly assists injured employees, the supervisor could be considered a de facto responder.
- Recapping, bending, or removing needles is permissible only if there is no feasible alternative or if required for a specific medical procedure such as blood gas analysis.
- Any specific eye, mouth, other mucous membrane, non-intact skin, or parenteral contact with blood or other potentially infectious materials is considered an exposure incident.
- Where employees are exposed to blood or OPIM, the employer must develop a written schedule for cleaning each area where exposures occur.
- If blood or OPIM is absorbed by kitty litter or other absorbents, and is no longer pourable, drippable, squeezable, or flakable, then the waste is not considered infectious waste.
Checklist
Review these bloodborne pathogens checklists to ensure safety and compliance at your facility.
General
- Do all employees who are expected to respond to medical emergencies as part of their work have available and understand how to use appropriate personal protective equipment to protect against exposure to bloodborne diseases?
Training
- Have all employees who are expected to respond to medical emergencies as part of their work had training on appropriate procedures to protect them from bloodborne pathogens, including universal precautions?
- Have all employees who are expected to respond to medical emergencies as part of their work received first-aid training?
Containers
- If you have a refrigerator where blood or other infectious materials are kept, do you prohibit storage of food or drink in it?
- Is a container provided for reusable sharps that is puncture resistant, properly labeled, and leakproof?
Medical
- Where employees have had an exposure incident involving bloodborne pathogens, was an immediate post exposure medical evaluation and follow up provided?
- If employees are expected to respond to medical emergencies as part of their work do they have available and understand how to use appropriate personal protective equipment to protect against exposure to bloodborne diseases?
Recordkeeping
- Do you establish and maintain an accurate record for each employee with occupational exposure to bloodborne pathogens?
- Do you ensure that employee medical records required by 1910.1030(h)(1) are kept confidential and appropriately maintained?
- Do training records include dates of training sessions and other required information?
- Are training records maintained for three years from the date on which the training occurred?
- If you have an employee(s) with occupational exposure as defined by 1910.1030(b) have you established an appropriate Exposure Control Plan?
- If applicable, do you document annually consideration and implementation of appropriate commercially available and effective safer medical devices designed to eliminate or minimize occupational exposure?
- If applicable, have you established and do you maintain a sharps injury log for the recording of percutaneous injuries from contaminated sharps?
Emergency eyewash and shower
OSHA requires emergency eyewashes and showers be present where the eyes or body of any person may be exposed to injurious corrosive materials. The emergency equipment must be available within 10 seconds.
Action steps
- Provide suitable facilities for drenching or flushing of the eyes and body where there is exposure to injurious corrosive materials.
- Ensure eyewash/showers are located within 10 seconds of the hazard.
- Inspect and maintain eyewash/shower equipment per manufacturer’s specifications and instructions.
- Train employees on locations and use of eyewash/shower equipment.
Training action plan
OSHA does not have specific training requirements regarding emergency eyewash and shower equipment. However, employees should be trained on the location and use of this equipment.
Additionally, you may want to train employees on safe handling of chemicals, proper protective equipment, location of SDSs, and other hazcom requirements.
Tips
- ANSI Z358.1-1998 contains additional information on permissible water temperatures for eyewashes and showers. The standard makes reference to a delivered flushing fluid temperature being “tepid,” which the standard defines as “moderately warm; lukewarm.”
- ANSI Z358.1 indicates that an eyewash unit must be positioned with the flushing fluid nozzles between 33 inches and 45 inches from the standing surface.
- OSHA does not specifically require floor markings around eyewash stations or emergency showers. But because OSHA requires that the stations and showers be provided for immediate emergency use and because ANSI recommends they be accessible and free of obstructions, floor markings are a popular method to help keep the area clear of obstructions.
- Acanthamoebea are small amoebae which have been found in portable and stationary eyewash stations. Infections caused by Acanthamoebae are difficult to recognize and treat and may result in the loss of the infected eye. Chlorination has been found to be effective in destroying Acanthamoebae.
Checklist
Review this emergency eyewash and shower checklist:
- Are there suitable facilities for drenching or flushing of the eyes and body where there is exposure to injurious corrosive materials?
- Are eyewash/showers located within 10 seconds of the hazard?
- Do you inspect and maintain eyewash/shower equipment per manufacturer’s specifications and instructions?
- Have employees been trained on locations and use of eyewash/shower equipment?
Ergonomics
There currently is no specific regulatory requirement for the development of an ergonomics program. However, under the General Duty Clause, the employer is responsible for providing a “safe and healthful work environment.” Therefore, every employer should assess the type of workplace being provided to employees, examine injury and illness records to see what types of injuries are being reported, and develop the appropriate ergonomic responses.
Action steps
- Evaluate workplace for ergonomic hazards (repetitive tasks, awkward posture, heavy lifting, etc.).
- Develop appropriate ergonomic controls.
- Train employees on proper work practices (i.e., safe lifting).
- Keep adequate records of injuries/illnesses.
Train action plan
OSHA does not have specific training requirements for ergonomics. However, employees who perform work involving repetitive motions, awkward postures, material handling, forceful exertions, etc., can benefit from training in ergonomics. OSHA regulates ergonomics hazards under the General Duty Clause (Section 5(a)(1)) of the Occupational Safety and Health Act of 1970. Employers have a general duty to provide a safe and healthful workplace.
Training content could include:
- Definition of ergonomics,
- Common injuries or illnesses (musculoskeletal disorders),
- Causes of ergonomics injuries or illnesses (repetitive motions, forceful exertions, vibrations, sustained or awkward postures, etc.),
- Workplace risk factors,
- Controls used,
- Work station redesign, and
- Medical management.
Tips
- Rotating employees into several different jobs during the course of a workshift is a way to distribute work so that each employee spends less time performing the same repetitive tasks.
- Designing jobs so they include a wider variety of tasks (or a longer motion pattern) may reduce the frequency and duration of repetitive motions.
- Micro breaks or rest pauses — building short micro pauses between motions or tasks is another way to give muscles and tendons recovery time.
- Computer desk areas should be deep enough to accommodate a monitor placed at least 20 inches away from the eyes.
- Ideally, a worker’s desk should have a work surface large enough to accommodate a monitor and a keyboard. Usually about 30 inches is deep enough to accommodate these items.
Checklist
Review these checklists to help prevent ergonomic hazards in your workplace.
General
- Are measures taken to identify and control all ergonomic hazards?
- Are all task requirements visible from comfortable positions?
- Are armrests and footrests provided where needed?
- Are cushioned floor mats provided for workers who are required to stand for long periods?
- Are mechanical aids and equipment provided where feasible?
- Are worker movements analyzed so that potential injuries (e.g., hand or foot injuries, repetitive motion injuries, or strain from lifting) are avoided?
- Are workers wearing protective clothing or equipment that is appropriate for the job, and does it fit properly?
- Are wrist supports present at computer workstations?
- Does the working space allow for a full range of work movements?
- Have you prevented employees’ hands or arms from being subjected to pressure from sharp edges on work surfaces?
- Is the work flow properly organized (e.g., is the worker required to move at an acceptable pace)?
- Is the work surface height proper and adjustable?
- Is the workstation designed to minimize or eliminate twisting at the waist, reaching above the shoulder, bending at the waist, static muscle loading, extension of the arms, bending or twisting of the wrist, and elevation of elbows?
Training
- Do you provide all employees with basic information about common musculoskeletal disorders and their signs and symptoms?
- Have all employees been provided basic information about how to report MSDs and their signs and symptoms in your workplace?
- Are all employees provided basic information about the kinds of risk factors, jobs, and work activities associated with MSD hazards?
Computer workstations
- Do you provide chairs that can be adjusted to different heights?
- Do chairs support the lower back (lumbar area)?
- Do chairs have padded seats and roll on wheels (casters)?
- Do chairs support the forearms with armrests while allowing the elbows to remain near the waist?
- Are the keyboard and mouse locations adjustable?
- Are wrist supports present at computer workstations?
- Is the monitor arranged to enable the employee to see the screen clearly without leaning forward?
- Is there enough space under the work surface for the employee’s knees?
- Are workers encouraged to take short breaks?
Recordkeeping
- Do you keep adequate records of musculoskeletal disorders and their signs, symptoms, and hazards?
Hazard communication
About one in every four workers routinely comes in contact with hazardous chemicals while performing his or her job. In many cases, the chemicals may be no more dangerous than those used at home. But in the workplace, exposure is likely to be greater, concentrations higher, and exposure time longer. Reactions to chemical exposures range from slight skin, eye, or respiratory irritation to life-threatening cancers, blood diseases, and debilitating lung damage.
OSHA developed the Hazard Communication Standard (HCS) to protect workers from these dangerous exposures. The standard was originally based on a simple concept—that employees have both a need and a right to know about the hazards and identities of the chemicals they are exposed to when working. In 2012, OSHA changed the HCS drastically, using the concept that the employees have a “right to understand” about the hazards of chemicals they are exposed to. They also need to know what they can do to protect themselves. Additionally, when employers have information about the chemicals being used, they can take steps to reduce exposures, substitute less hazardous materials, and establish safe work practices to prevent illnesses and injuries caused by these substances.
The HCS establishes uniform requirements to make sure that the hazards of all chemicals imported into, produced, or used in U.S. workplaces are evaluated and classified and that this hazard information is communicated to employers and exposed employees. Basically, the rule incorporates a downstream flow of information. This means that chemical manufacturers have the primary responsibility for generating and disseminating information and chemical users must obtain the information and transmit it to their exposed employees.
Evaluating and classifying chemical hazards involves technical concepts and is a process that requires the professional judgment of experienced experts. That’s why the HCS is designed so that employers who simply use chemicals, rather than produce or import them, are not required to evaluate the hazards of those substances.
Hazard classification is the responsibility of the producers and importers of the materials, who must then pass that information to the purchasers and end-users of the products. Employers that don’t produce or import chemicals need only focus on those parts of the rule that deal with establishing a workplace program and communicating information to their workers. (Note: If employers create mixtures in the workplace, there will be more responsibility and requirements than for employers who simply use chemicals that have already been evaluated and classified.)
Action steps
- Develop, implement, and maintain a written hazard communication program.
- Provide employees with effective information and training on hazardous chemicals in their work area.
- Comply with all hazard communication actions for any chemical which is known to be present in the workplace in such a manner that employees may be exposed under normal conditions of use or in a foreseeable emergency.
- Evaluate chemicals produced in or imported into the workplace to determine if they are hazardous.
- Obtain or develop a Safety Data Sheet or SDS for each hazardous chemical produced or imported.
- Maintain an SDS in the workplace for each hazardous chemical used.
- Make sure all containers of chemicals are labeled as required.
Training action plan
Under the provisions of this standard each employee exposed to hazardous chemicals must receive information about those chemicals through a comprehensive hazard communication program which includes identification of chemical hazards, chemical labeling, and safety data sheets in the training program.
You must provide hazcom training at the time your employees are initially assigned to their jobs, when a new chemical hazard is introduced into the work area or when the employee’s job duties change such that he or she is now exposed to a hazardous chemical.
The training must be comprehensible. If the employees must receive job instructions in a language other than English, then training and information will probably also need to be conducted in a foreign language.
Generally, training content should cover:
- Hazcom and chemical terminology,
- Physical and health hazards of chemicals,
- Written hazard communication program,
- Location of relevant hazcom documents and materials,
- Chemical protective measures,
- Safety data sheets (SDSs), and
- Labeling requirementsHazards of nonroutine tasks and unlabeled pipes related to hazardous chemicals.
Documentation
OSHA does not require training documentation for individual employees regarding hazard communication, but it is a good idea to keep it anyway. Training records can tell you who was trained on what, when, and who conducted the training.
Tips
- The employer does not have to retrain each new hire if that employee has already received training from a former employer, a union, or other entity. However, the employer would have to supply such information as location of SDSs, workplace hazards, labeling systems, and so on.
- An employer can claim trade secret status when it can support such a claim. However, chemical ingredients of public knowledge or of general knowledge in an industry that are disclosed by the goods one markets cannot be claimed as a trade secret.
- Chemicals generated in the work operations, such as welding fumes, dusts, and exhaust fumes, are sources of chemical exposure and must be listed on the chemical inventory.
- The chemical “identity” is any name or term that appears on the label, the SDSs, and the chemical inventory, and thus links these three sources of information.
- SDSs must be readily accessible to employees when they are in their work areas during their workshifts.
- Under the rule, “exposure” or “exposed” means that an employee is subjected to a hazardous chemical in the course of employment through any route of entry and includes potential exposure.
Checklist
Review these hazard communication checklists.
Labeling
- Do you ensure that each container of hazardous chemicals in the workplace is labeled, tagged or marked identifying the chemical it contains?
- Do you ensure that each container of hazardous chemicals is labeled, tagged or marked with the appropriate hazard warnings?
- If you remove or deface labels on incoming containers of hazardous chemicals, do you immediately mark the containers with the required information?
- Do you ensure that labels or other forms of warning are legible, in English, and prominently displayed on the container, or readily available in the work area throughout each work shift?
Safety data sheets
- Do you have a safety data sheet for each hazardous chemical you use?
- Are the sheets written in English?
- Does each sheet include everything that is required in 1910.1200?
- Do you ensure that sheets are readily accessible to employees in the work area during each work shift?
- If employees must travel between workplaces during a work shift, do you sheets in each workplace or at a central location at the primary workplace facility in case of an emergency?
Training
- Are employees provided required hazard communication training?
- Do you provide information to employees as to the location and availability of the written hazard communication program and safety data sheets?
Recordkeeping
- Have you compiled a hazardous chemical inventory?
- Have you documented the employee training that you have done under the Hazcom standard?
Written program
- Have you developed, implemented, and do you maintain a written hazard communication program?
- Does your hazard communication program include a list of the hazardous chemicals known to be present using an identity that is referenced on the appropriate safety data sheet?
- Do you make the written hazard communication program available upon request to the employees or designated representatives in accordance with 1910.20(e)?
Heat stress
Hot work environments can be found in any climate, any time of the year. Many employees working in foundries, glass or ceramic plants, mines, bakeries, as well as during roofing, farming, exterior painting, utility work, road repair, and construction activities are exposed to high heat on a regular basis. In addition to temperature, high humidity adds to the heat burden for workers in laundries, restaurant kitchens, and canneries. Overexposure can cause:
- Fatigue,
- Heat rash,
- Fainting,
- Muscle cramps,
- Heat exhaustion, and
- Heat stroke.
Reduce the risk of heat stress by:
- Eliminating steam leaks,
- Providing cooling fans,
- Modifying equipment, and
- Using power tools to reduce manual labor.
Although federal OSHA does not specifically regulate heat stress, it can issue citations under the General Duty Clause of the OSH Act when employees are exposed to serious hazards which the employer could reduce or eliminate.
Action steps
- Identify environmental factors in your facility that affect the level of heat stress:
- High temperatures (90ºF or above can cause heat stress),
- High humidity (sweat doesn’t evaporate rapidly),
- Intense radiant heat (such as from the sun or a furnace), and
- Low air velocity (lowers the rate at which sweat evaporates).
- Identify operations that expose employees to excessive heat. You may need to enlist the aid of an industrial hygienist to take temperature readings using specialized equipment.
- Evaluate employees’ work loads. Conduct a job analysis to determine activity levels of light, moderate, or heavy.
- Evaluate employees’ general health and physical condition. Personal characteristics such as age, weight, fitness, medical conditions, and acclimatization can affect an individual’s level of stress.
- Assess employees’ clothing, especially if they wear personal protective equipment such as heavy leather, chemical protective clothing, or respirators.
- Provide plenty of drinking water — as much as a quart per employee per hour.
- Alternate work and rest periods with longer rest periods in a cool area can help avoid heat stress. If possible, schedule heavy work during the cooler parts of the day and provide protective clothing.
- Implement engineering and administrative controls to reduce heat exposures. Consider the following to lessen the risk of heat stress:
- Increase general ventilation;
- Install spot cooling by local exhaust ventilation at points of high heat production;
- Use shields as protection from radiant heat sources;
- Install evaporative cooling and mechanical refrigeration; and
- Provide personal cooling devices or protective clothing.
Training action plan
Before you conduct training, you will want to assess the heat hazards in your facility. This includes monitoring the environment and evaluating your employees’ work loads. When you understand the hazards, you can answer your employees’ questions.
A good heat stress training program should include:
- The risk factors of being affected by the heat;
- The problems caused by heat (fatigue, rash, fainting, muscle cramps, and heat exhaustion);
- Recognizing danger signs and symptoms;
- Knowing the first aid procedures for heat stroke and that heat stroke can be life threatening;
- Employee responsibilities in avoiding heat stress; and
- Use of protective clothing and equipment.
Review the contents of this training action plan and decide which elements to use, based on conditions and operations at your facility. From these elements, build a training program that addresses your facility’s specific heat-related hazards.
- Identify the hot work environments.
- Describe the risk factors of being affected by the heat.
- Explain how heat can increase fatigue.
- Explain how heat rash can occur.
- Talk about how people can faint from the heat.
- Explain how muscle cramps can be caused by heat.
- Talk about heat exhaustion.
- Stress that heat stroke is a life-threatening condition.
- Explain how heat exposures can be measured and the risk evaluated.
- Describe how exposure to heat can be controlled, such as:
- Intermittent rest periods with water breaks,
- Relief workers,
- Pacing the work,
- Reducing the physical demands of the job,
- Providing cool recovery or rest areas, and
- Scheduling work for cooler times of the day, or when heat producing equipment isn’t being operated.
- Train members of the emergency response team to recognize and treat heat stress disorders.
- Train supervisors to detect early signs of heat stress.
- Document all training.
Tips
- Not everyone is affected equally by the heat. Age, weight, degree of physical fitness, metabolism, medications, use of alcohol or drugs, and a variety of medical conditions such as hypertension all affect a person’s sensitivity to heat.
- For workers who have had recent experience in jobs where heat levels were high enough to produce heat stress, the acclimatization regimen should be 50 percent exposure on day one, 60 percent on day two, 80 percent on day three, and 100 percent on day four.
- For new workers (and people who have been away from working in the heat for an extended time), the regimen should be 20 percent on day one, with a 20 percent increase in exposure each additional day.
- On the first day of work in a hot environment, the body temperature, pulse rate, and general discomfort will be higher. With each succeeding daily exposure, all of these responses will gradually decrease, while the sweat rate will increase. When the body becomes acclimated to the heat, the individual finds it possible to perform work with less strain and distress.
- Heat stroke is a life-threatening condition. It occurs when the body’s temperature regulatory system fails and sweating becomes inadequate to remove excess body heat. In heat stroke, the victim’s skin is hot and dry and body temperature is usually 105ºF or higher.
Checklist
This checklist may be used as part of employee awareness training regarding the hazards of working in high temperatures.
Symptoms of heat exhaustion
There are many symptoms related to heat exhaustion. Several can be present at the same time.
- Headaches.
- Dizziness.
- Light-headedness.
- Mental confusion.
- Weakness.
- Mood changes.
- Pale and clammy skin.
- Nausea.
- Dark-colored urine.
- Fainting.
Symptoms of heat stroke
Like heat exhaustion, heat stroke has multiple symptoms.
- Dry, pale skin with no sweating.
- Hot, red skin.
- Seizures.
- Mental confusion.
- Fainting.
- Mood changes.
Risk factors to consider
Factors that put you at greater risk for heat-induced illness include:
- Had a heat-induced illness in the past.
- Take certain medications.
- Drink alcoholic beverages.
- Obesity.
- Wear heavy or restrictive personal protective equipment like protective suits or respirators.
Treating heat-releated illnesses
When a coworker suffers a heat-related illness, you should:
- Move the person to a cool, shaded area.
- Stay with the person at all times (don’t leave the person unattended).
- Loosen and remove the person’s heavy clothing.
- Offer cool water — a small cup every 15 minutes.
- Cool the person by fanning, spraying with cool water, or putting cool, wet towels on the head or other exposed skin.
- Place ice packs (if available) under the arm pits and in the groin area.
- If the person is dizzy or lightheaded, lay the person on his or her back and raise the feet and legs several inches.
- If the person is nauseous, lay the person on his or her right side.
Call for help
If the person needs help beyond what you are providing, follow your company’s emergency procedures.
Protect yourself
When working in hot environments you should:
- Slowly build up tolerance to the heat.
- Avoid eating large meals before working in hot environments.
- Learn the signs and symptoms of heat-induced illnesses.
- Drink plenty of cool water.
- Avoid caffeine or alcoholic beverages because they make the body lose water and increase the risk for heat illnesses.
- Wear light, loose-fitting, breathable clothing (such as clothing made from cotton).
- Take short, frequent breaks in the shade or away from the heat (like in an air-conditioned vehicle) to allow the body to cool down.
- Use the buddy system so one person can check on the other.
Hexavalent chromium
Chromium hexavalent (CrVI) compounds, often called hexavalent chromium, exist in several forms. Industrial uses of hexavalent chromium compounds include chromate pigments in dyes, paints, inks, and plastics; chromates added as anticorrosive agents to paints, primers, and other surface coatings; and chromic acid electroplated onto metal parts to provide a decorative or protective coating. Hexavalent chromium can also be formed when performing “hot work” such as welding on stainless steel or melting chromium metal. In these situations the chromium is not originally hexavalent, but the high temperatures involved in the process result in oxidation that converts the chromium to a hexavalent state.
Action steps
- Survey your operations for potential exposure to hexavalent chromium. Employers can consult their suppliers or examine safety data sheets (SDSs) to identify Cr(VI)-containing materials that are present in the workplace. Also, remember Cr(VI) can be formed when performing “hot work” such as welding on stainless steel, melting chromium metal, or heating refractory bricks in kilns.
- Conduct an exposure determination. Employers must determine the 8-hour time-weighted average exposure to Cr(VI) for each employee exposed to Cr(VI). This assessment allows the employer to identify and prevent overexposures; collect exposure data so that proper control methods can be selected; and evaluate the effectiveness of those methods. An accurate exposure determination also provides important information concerning occupational Cr(VI) exposures to the physician or other licensed health care professional who performs medical examinations on employees.
- Notify employees of exposure determination results. Within 15 days, employers must provide written notification to affected employees of the results of the exposure determination (or post the results in a common area). Additionally, if the exposure determination indicates exposures exceeding the PEL, the employer notification must describe control measures being used to reduce exposures to levels at or below the PEL.
- Establish a regulated area. Employers must establish regulated areas wherever an employee’s exposure to Cr(VI) is, or can reasonably be expected to be, in excess of the PEL.
- Limit eight-hour time-weighted average hexavalent chromium exposure in the workplace to 5 micrograms or less per cubic meter of air. Engineering and work practice controls should be the primary control methods. When these controls are not sufficient, then employers must provide and ensure employees wear personal protective equipment, such as respiratory protection.
- Perform periodic monitoring. Employers can choose between two options for monitoring: either a scheduled monitoring option based on minimum OSHA requirements (e.g., every 3 months if exposures are above the PEL) or a performance-oriented option.
- Implement good personal hygiene and housekeeping practices to prevent hexavalent chromium exposure.
- Provide medical examinations to employees within 30 days of initial assignment, annually, to those exposed in an emergency situation, to those who experience signs or symptoms of adverse health effects associated with hexavalent chromium exposure, to those who are or may be exposed at or above the action level for 30 or more days a year, and at termination of employment.
- Train employees. In addition to the general training under the hazard communication standard, employers must also train employees exposed to hexavalent chromium on the contents of the Chromium (VI) standard, 1910.1026.
- Provide changing rooms and washing facilities.
- Maintain accurate records. This includes records of air monitoring, medical examination, and exposure records.
Training action plan
It is critically important that workers recognize the hazards associated with exposure to Cr(VI) and understand the measures they can take to protect themselves. OSHA’s Hazard Communication standard (29 CFR 1910.1200) establishes requirements for employers to provide workers with information on hazardous chemicals such as Cr(VI) through comprehensive chemical hazard communication programs that include SDSs, labels, and worker training. Employers must follow the requirements of the Hazard Communication standard with regard to workers exposed to Cr(VI).
- Provide details of the organization’s written hazard communication program. Employers must have a written hazard communication program that describes the labeling system, SDSs, and how employees receive training.
- The written hazard communication program must also include a list of the hazardous chemicals known to be present in the workplace.
- Employees must have access to SDSs and the written hazard communication program.
- Explain the requirements of OSHA’s Cr(VI) standard. OSHA requires employers to limit employee exposure to Cr(VI) to a specified permissible limit. OSHA also requires the employer to perform periodic monitoring, provide PPE, make medical examinations available to employees, train employees, observe proper housekeeping and hygiene practices, and keep exposure and medical records.
- Inform workers of operations where Cr(VI) is present. Cr(VI) is widely used in pigments, metal finishing (electroplating), wood preservatives and fungicides, and in chemical synthesis as an ingredient and catalyst. Hexavalent chromium may also be present in fumes generated during the production or welding of chrome alloys. Chromium metal is often alloyed with other metals or plated on metal and plastic substrates to improve corrosion resistance and provide protective coatings. The steel industry is a major consumer of chromium metal in the production of stainless steel. Examples of Cr(VI) compounds include:
- Ammonium dichromate;
- Calcium chromate;
- Chromium trioxide or chromic acid;
- Lead chromate;
- Potassium chromate;
- Potassium dichromate;
- Sodium chromate;
- Strontium chromate; and
- Zinc chromate.
- Explain the hazards of Cr(VI). The major health effects associated with exposure to Cr(VI) include lung cancer, asthma, nasal septum ulcerations and perforations, skin ulcerations, and allergic and irritant contact dermatitis.
- Breathing in high levels of Cr(VI) can cause irritation to the nose and throat. Symptoms may include runny nose, sneezing, coughing, itching, and a burning sensation. Repeated or prolonged exposure can cause sores to develop in the nose and result in nosebleeds. If the damage is severe, the nasal septum (a “wall” separating the nasal passages) develops a hole in it (perforation).
- Breathing small amounts of Cr(VI) even for long periods does not cause respiratory tract irritation in most people. Some employees become allergic to Cr(VI) so that inhaling chromate compounds can cause asthma symptoms such as wheezing and shortness of breath.
- Some employees can also develop an allergic skin reaction, called allergic contact dermatitis. This occurs from handling liquids or solids containing Cr(VI). Once an employee becomes allergic, brief skin contact causes swelling and a red, itchy rash that becomes crusty and thickened with prolonged exposure. Allergic contact dermatitis is long-lasting and more severe with repeated skin contact.
- Direct skin contact with Cr(VI) can cause a non-allergic skin irritation. Contact with non-intact skin can also lead to chrome ulcers. These are small crusted skin sores with a rounded border. They heal slowly and leave scars.
- Describe how employees can be exposed to Cr(VI). Employees can inhale airborne hexavalent chromium as a dust, fume or mist while:
- Producing chromate pigments and powders, chromic acid, chromium catalysts, dyes, and coatings;
- Working near chrome electroplating ;
- Welding and hot-working stainless steel, high chrome alloys and chrome-coated metal; and
- Applying and removing chromate-containing paints and other surface coatings.
Note: Skin exposure can occur during direct handling of hexavalent chromium-containing solutions, coatings, and cements.
- Describe the monitoring and exposure determination process at the company. Employees must be notified of hexavalent chromium exposure determinations.
- Describe control measures employees can take to protect themselves. OSHA sets exposure limits for airborne concentration of Cr(VI). Exposures to Cr(VI) can be reduced or eliminated through the use of engineering and work practice controls. If these control measures don’t reduce exposures to, or below, OSHA’s permissible exposure limit, employees must wear respirators. When eye or skin contact with Cr(VI) is possible, employees must use personal protective equipment.
- Describe to employees appropriate work practices, emergency procedures, and protective equipment to be used.
- Describe the medical surveillance program. The purpose of medical surveillance is to determine if an individual can be exposed to Cr(VI) at his or her workplace without experiencing adverse health effects; to identify Cr(VI)-related adverse health effects when they do occur so that appropriate intervention measures can be taken; and to determine a worker’s fitness to use personal protective equipment such as respirators. All medical examinations and procedures required by the standards must be performed by or under the supervision of a physician or other licensed healthcare professional (PLHCP). When medical surveillance is required it must be provided at no cost to workers and at a reasonable time and place. If participation requires travel away from the worksite, the employer must bear the cost. Workers must be paid for time spent taking medical examinations, including travel time.
- Make a copy of OSHA’s Cr(VI) standard available to employees.
Checklist
Review these hexavalent chromium checklists.
General
- Are employees aware of the hazards involved with Cr(VI) if they may be exposed to it in their work environment?
Training
- Have you instituted a training program for all employees who are subject to Cr(VI) exposure?
Monitoring
- Is employee exposure monitored and kept within acceptable levels?
- Are engineering and work practice controls used to reduce exposures to a permissible level?
Employee protection
- Is personal protective equipment (PPE) provided and are all employees required to use PPE as needed?
- Is PPE functional and in good repair?
- Do employees wash appropriately after working with Cr(VI)?
- Are employees provided appropriate change rooms and showers?
- Are employees prohibited from taking contaminated items from work area?
Respiratory protection
- Is a respiratory protection program in place?
- Are employees provided proper respiratory protection?
Emergency situations
- Are procedures in place for dealing with emergency situations?
Medical surveillance
- Is a medical surveillance program in place for employees who may be exposed to Cr(VI)?
- Have employees working with this substance been given appropriate medical examinations?
Marking and labeling
- Are caution labels and signs used to warn of this substance?
- Has a regulated area been established, and marked, where appropriate?
- Are containers used to store this substance marked appropriately?
Recordkeeping
- Are appropriate records maintained (exposure monitoring, medical surveillance, etc.)?
- Are employees given access to their exposure and medical records upon request?
Hazard communication
- Do you have a safety data sheet for every hazardous chemical you have at your facility?
- Do you maintain a written hazard communication program?
- Have you compiled a hazardous chemical inventory?
- Have you documented the employee training that you have done under the hazard communication standard?
- Are all chemical containers marked with contents name and hazards?
Ventilation
- Are ventilation systems used where appropriate?
Housekeeping
- Are all work areas clean, sanitary, orderly and adequately illuminated?
- Are adequate cleaning methods used (e.g., HEPA-filter vacuuming)?
- Are contaminated materials disposed of properly?
Isocyanates
Isocyanates are a family of highly reactive, low molecular weight chemicals. They are widely used in the manufacture of flexible and rigid foams, fibers, coatings such as paints and varnishes, and elastomers, and are increasingly used in the automobile industry, autobody repair, and building insulation materials. Spray-on polyurethane products containing isocyanates have been developed for a wide range of retail, commercial, and industrial uses to protect cement, wood, fiberglass, steel and aluminum, including protective coatings for truck beds, trailers, boats, foundations, and decks.
Isocyanates are powerful irritants to the mucous membranes of the eyes and gastrointestinal and respiratory tracts. Direct skin contact can also cause marked inflammation. Isocyanates can also sensitize workers, making them subject to severe asthma attacks if they are exposed again. There is evidence that both respiratory and dermal exposures can lead to sensitization. Death from severe asthma in some sensitized subjects has been reported. Workers potentially exposed to isocyanates who experience persistent or recurring eye irritation, nasal congestion, dry or sore throat, cold-like symptoms, cough, shortness of breath, wheezing, or chest tightness should see a physician knowledgeable in work-related health problems.
The most widely used compounds are diisocyanates, which contain two isocyanate groups, and polyisocyanates, which are usually derived from diisocyanates and may contain several isocyanate groups. The most commonly used diisocyanates include methylenebis(phenyl isocyanate) (MDI), toluene diisocyanate (TDI), and hexamethylene diisocyanate (HDI). Other common diisocyanates include naphthalene diisocyanate (NDI), methylene bis-cyclohexylisocyanate (HMDI)(hydrogenated MDI), and isophorone diisocyanate (IPDI). Examples of widely used polyisocyanates include HDI biuret and HDI isocyanurate.
Action steps
- Determine if your operations expose workers to isocyantes. Review the chemical inventory and safety data sheets (SDSs).
- Determine if your current controls are adequate, e.g., determine current exposure concentrations and compare them to recommended limits; and review injury/illness records for signs of respiratory illness, asthma, and other lung problems.
- Implement appropriate controls to prevent exposure. Preventing exposure to isocyanates is a critical step in eliminating the health hazard. Engineering controls such as closed systems and ventilation should be the principal method for minimizing isocyanate exposure in the workplace. Other controls, such as worker isolation and use of personal protective equipment such as respirators and personal protective clothing to prevent dermal exposures may also be necessary. Early recognition of sensitization and prompt and strict elimination of exposures is essential to reduce the risk of long-term or permanent respiratory problems for workers who have become sensitized.
- Consider alternatives to isocyanates.
- Conduct a PPE hazard assessment, and implement a respiratory protection program if respirators are to be used. Provide and ensure the use of the appropriate gloves (e.g., butyl, nitrile), goggles, and protective clothing when a potential for eye or dermal exposure exists (e.g., exposure to contaminated equipment, chemical containers, etc.)
- Implement good housekeeping procedures. Periodically check for surface contamination (e.g., visible foam/coating) on surfaces, tools and equipment near the operation using isocyanates as well as in places where contamination may not be expected such as drinking fountains, telephones, locker rooms, and lunchrooms, to identify potential sources of dermal exposure and evaluate housekeeping and PPE deficiencies.
- Monitor employee exposures on a regular basis.
- Provide separate lockers for work clothes and street clothes.
- Do not allow workers to eat, drink, apply cosmetics, or use tobacco products in work areas.
- Prohibit workers from leaving the workplace wearing protective work clothing or equipment or taking it home to launder.
- Ensure workers wash face, hands, and forearms before eating, drinking, smoking, or applying cosmetics.
- Ensure workers shower at the end of work shifts.
- Ensure workers immediately and thoroughly wash off skin with soap and flowing water if dermal contact occurs.
- Implement a medical surveillance program.
Training action plan
It is critically important that workers recognize the hazards associated with exposure to isocyanates. Employers should implement a comprehensive training program on hazard identification and safe work practices, including:
- Provide details of the organization’s written hazard communication program. Employers must have a written hazard communication program that describes the labeling system, SDSs, and how employees receive training.
- The written hazard communication program must also include a list of the hazardous chemicals known to be present in the workplace.
- Employees must have access to SDSs and the written hazard communication program.
- Inform workers where work areas may contain isocyanates.
- Inform workers on the signs and symptoms of isocyanate exposure. Workers should seek medical attention if they notice any signs or symptoms.
- Teach employees of the importance of avoiding dermal contact when working with isocyanates.
- Instruct employees on the engineering controls being used to reduce exposures.
- Train employees on the use of appropriate PPE, including respirators and skin protections, and on the limitation of that equipment.
- Explain the workplace monitoring program.
Checklists
Review these isocyanates checklists to ensure safety and compliance at your facilty.
General
- Are employees aware of the hazards involved with isocyanates if they may be exposed to it in their work environment?
Training
- Have you instituted a training program for all employees who are subject to isocyanates exposure?
Monitoring
- Is employee exposure monitored and kept within acceptable levels?
- Are engineering and work practice controls used to reduce exposures to a permissible level?
Employee protection
- Is personal protective equipment (PPE) provided and are all employees required to use PPE as needed?
- Is PPE functional and in good repair?
- Do employees wash appropriately after working with isocyanates?
- Are employees provided appropriate change rooms and showers?
- Are employees prohibited from taking contaminated items from work area?
Respiratory protection
- Is a respiratory protection program in place?
- Are employees provided proper respiratory protection?
Emergency situations
- Are procedures in place for dealing with emergency situations?
Medical surveillance
- Is a medical surveillance program in place for employees who may be exposed?
- Have employees working with this substance been given appropriate medical examinations?
Marking and labeling
- Are caution labels and signs used to warn of this substance?
- Has a regulated area been established, and marked, where appropriate?
- Are containers used to store this substance marked appropriately?
Recordkeeping
- Are appropriate records maintained (exposure monitoring, medical surveillance, etc.)?
- Are employees given access to their exposure and medical records upon request?
Hazard communication
- Do you have a safety data sheet for every hazardous chemical you have at your facility?
- Do you maintain a written hazard communication program?
- Have you compiled a hazardous chemical inventory?
- Have you documented the employee training that you have done under the hazard communication standard?
- Are all chemical containers marked with contents name and hazards?
Ventilation
- Are ventilation systems used where appropriate?
Housekeeping
- Are all work areas clean, sanitary, orderly and adequately illuminated?
- Are adequate cleaning methods used (e.g., HEPA-filter vacuuming)?
- Are contaminated materials disposed of properly?
Lead
Lead can be toxic when absorbed by the body through inhalation or ingestion. OSHA regulates an employee’s exposure to lead in order to prevent the absorption of harmful levels of lead. When the employee’s exposure exceeds 50 mg/m3 averaged over an 8-hour period, the area must be regulated for lead exposure.
Action steps
- Monitor employee exposures to lead and determine if any employee may be exposed to lead at concentrations greater than 50 mg/m3 of air during an 8-hour period.
- Establish and implement a written compliance program to reduce exposures at or below the permissible exposure limit (PEL), and interim levels if applicable, solely by means of engineering and work practice controls.
- Provide exposed employees with respirators and train according to 1910.134.
- Provide exposed employees with protective work clothing and equipment.
- Establish cleaning, laundering, or disposal procedures for contaminated protective clothing and equipment.
- Where employees are exposed to lead above the PEL, do not allow the presence or consumption of food or beverages, tobacco products, or the application of cosmetics.
- Provide separate change rooms, shower facilities, and lunchrooms.
- Post warning signs in each area where the PEL is exceeded.
- Institute a medical surveillance program for affected employees.
- Establish and maintain an accurate record for each employee subject to medical surveillance.
- Provide the physician conducting a medical examination or consultation with the information required in the Lead standard and furnish the employee with a copy of the written medical opinion.
- Establish a training program for all affected employees. Provide the training prior to the initial job assignment and at least annually thereafter.
- If ventilation is used to control lead exposure, take measurements at least every three months which demonstrate the effectiveness of the system in controlling exposure. Additionally, take measurements when there is a change in production, process, or control which could alter the lead level within 5 days of the change.
- If administrative controls are used to control lead exposure, implement a job rotation schedule.
Training action plan
You have to provide training for all employees who have lead exposures at or above the PEL. The training must be provided prior to the initial job assignment and then repeated at least annually. Make sure that each employee is informed of the following during training:
- Content of OSHA’s Lead standard at 1910.1025 and its Appendices A, B, C, and D; Specific nature of the operations which could result in exposure to lead above the action level;
- Purpose, proper selection, fitting, use, and limitations of respirators;
- Purpose and a description of the:
- Medical surveillance program; and
- Medical removal protection program, including information concerning the adverse health effects associated with excessive exposure to lead (with particular attention to the adverse reproductive effects on both males and females).
- Engineering controls and work practices associated with the employee’s job assignment;
- Contents of any compliance plan in effect; and
- Instructions to employees that chelating agents should not: routinely be used to remove lead from their bodies, and be used at all except under the direction of a licensed physician.
Include as part of your training and distribute to employees any materials made available to your facility by OSHA that pertain to the:
- Occupational Safety and Health Act, and
- Regulations issued pursuant to that Act and the Lead standard.
Make a copy of the Lead standard and its appendices available to all affected employees.
Provide, upon request, all materials relating to the employee information and training program to OSHA officials.
Documentation
Retain exposure monitoring records and medical surveillance and other medical records for at least 40 years or for the duration of employment plus 20 years, whichever is longer. Retain medical removal records for at least the duration of an employee’s employment.
Checklist
Use this checklist to ensure shop work safety:
- Is the work bench ventilated?
- Is there local exhaust ventilation on the torch?
- Are workers trained to decontaminate equipment using vacuum, water spray, or mechanical removal such as scraping or brushing in conjunction with local exhaust ventilation?
- Are low volume and high velocity ventilated hand tools provided?
- Are Laminar Flow (supplied air) Islands provided at work stations?
- Are wash-up sinks available for employees in the shop?
- Are surfaces kept free of lead contamination as much as possible?
- Are all shop vacuums equipped with HEPA filters capable of removing lead?
- Are vacuums emptied in a manner that minimizes the reentry of lead into the shop?
- Is there a program for routine ventilation system inspections?
- Does exhaust ventilation use HEPA filters?
- Are defective parts of the ventilation system replaced when identified?
- Are original installation documents, as well as all modifications, problems, and resolutions retained?
Mold
There is currently no specific OSHA standard for mold. However, indoor air quality (IAQ) hazards are addressed in specific standards, such as the 1910.94 ventilation standard. Poor IAQ is one of the most important health issues we face.
Action steps
- Evaluate the workplace for mold or indoor air quality problems.
- Eliminate or control all known and potential sources of microbial contaminants by prompt cleanup and repair of all areas where water collection and leakage has occurred.
- Remove and discard porous organic materials that are contaminated (e.g., damp insulation in ventilation system, moldy ceiling tiles, and mildewed carpets).
- Clean and disinfect nonporous surfaces where microbial growth has occurred with detergents, chlorine-generating slimicides, or other biocides and ensure that these cleaners have been removed before air handling units are turned on.
- Maintain indoor air relative humidity below 60 percent (50 percent where cold surfaces are in contact with room air).
- If ventilation is turned off during weekends or other periods, ensure that contaminant concentrations are sufficiently diluted prior to occupancy.
- Thoroughly evaluate personnel affected with hypersensitivity and controls implemented before returning them to the workplace.
Training action plan
There are no specific OSHA training requirements for mold. However, employees should be trained to report problems or suspected problems related to indoor air quality.
Tips
- There are thousands of species of mold, and the mold can be any color, including white, orange, green, brown, or black.
- Controlling the sources of moisture in a building is the key to preventing indoor mold growth.
- Porous or absorbent materials that become moldy, such as ceiling tiles, wallboard, or carpeting, should be replaced.
- When mold is discovered, communicate with building occupants to alleviate any potential health problems.
Checklist
Review this checklist to prevent mold at your facility:
- Has an evaluation been conducted to identify any mold or indoor air quality problems?
- Are measures taken to eliminate or control all known and potential sources of microbial contaminants by prompt cleanup and repair of all areas where water collection and leakage has occurred?
- Are porous organic materials that are contaminated (e.g., damp insulation in ventilation system, moldy ceiling tiles, and mildewed carpets) removed and discarded?
- Are nonporous surfaces where microbial growth has occurred cleaned and disinfected with detergents, chlorine-generating slimicides, or other biocides?
- Are cleaners and disinfectants used for mold removed before air handling units are turned on?
- Is indoor air relative humidity maintained below 60% (50% where cold surfaces are in contact with room air)?
- Is adequate ventilation in place?
Noise exposure
OSHA’s standard on occupational noise exposure, 1910.95, applies to all employees who are subjected to noise exposures that equal or exceed an 8-hour time-weighted average sound level of 85 decibels.
Action steps
- Administer a continuing, effective hearing conservation program IF employee noise exposures equal or exceed an 8-hour time-weighted average sound level (TWA) of 85 decibels measured on the A scale (slow response); OR equivalently, a dose of fifty percent.
- Institute a training program for all employees who are exposed to noise at or above an 8-hour time-weighted average of 85 decibels, AND ensure employee participation in such program.
- Make copies of 1910.95 available to affected employees or their representatives and also post a copy in the workplace.
- Use feasible administrative or engineering controls where needed.
- Establish and maintain an audiometric testing program by making audiometric testing available to all employees whose exposures equal or exceed an 8-hour time-weighted average of 85 decibels.
- Develop and implement a monitoring program if information indicates that any employee’s exposure may equal or exceed an 8-hour time-weighted average of 85 decibels.
- Maintain an accurate record of all employee exposure measurements required.
- Make hearing protectors available, at no cost, to all employees exposed to an 8-hour time-weighted average of 85 decibels or greater.
- Evaluate hearing protector attenuation for the specific noise environments in which the protector will be used.
Training action plan
You must provide training to all employees who are exposed to noise at or above an 8-hour time-weighted average of 85 decibels.
Employees must be trained prior to initial exposure and annually thereafter.
Generally, content should cover:
- Effects of noise,
- Specific noise hazards at your facility,
- Existing engineering controls,
- Selection procedures of hearing protection, and
- Purpose of and procedures for audiometric testing.
Tips
- There is no cure for noise-induced hearing loss, so prevention is the only way to avoid hearing damage.
- To reduce overall noise in the work area, place noisy machinery in a separate area away from as many workers as possible.
- To estimate employee noise exposures with a sound level meter it is generally necessary to take several measurements at different locations within the workplace.
Checklist
Review these checklists to help with noise exposure at your facility.
General
- Is protection against the effects of occupational noise exposure provided when sound levels exceed those of the OSHA noise standard?
- Do workplace noise levels conform to government standards?
- Are workers protected from sources of excessive noise?
- Have engineering controls been used to reduce excessive noise levels?
- Where engineering controls aren’t feasible, are administrative controls (that is, worker rotation) being used to minimize individual employee exposure to noise?
- Have you tried isolating noisy machinery from the rest of your operation?
Program
- Is there an ongoing, preventive health program to educate employees in:
- Safe levels of noise exposures,
- Effects of noise on their health, and
- The use of personal protection?
Posting
- Have work areas where noise levels make voice communication between employees difficult been identified and posted?
Monitoring
- Are noise levels being measured using a sound level meter or an octave band analyzer and are records being kept?
Personal protective equipment
- Is approved hearing protective equipment (noise attenuating devices) available to every employee working in noisy areas?
- If you use ear protectors, are employees properly fitted and instructed in their use?
Medical
- Are employees in high noise areas given periodic audiometric testing to ensure that you have an effective hearing protection system?
Pandemics
When a pandemic strikes, employers and safety professionals must be prepared. While you can’t plan for every virus that will emerge, you can create a flexible infectious disease preparedness plan.
A pandemic is a global disease outbreak. An influenza pandemic occurs when a new influenza virus emerges for which there is little or no immunity in the human population; begins to cause serious illness; and then spreads easily person-to-person worldwide. A worldwide influenza pandemic could have a major effect on the global economy, including travel, trade, tourism, food, consumption and eventually, investment and financial markets. Planning for pandemic influenza by business and industry is essential to minimize a pandemic’s impact. It is difficult to predict when the next influenza pandemic will occur or how severe it will be.
Wherever and whenever a pandemic starts, everyone around the world is at risk. Countries might, through measures such as border closures and travel restrictions, delay arrival of the virus, but cannot stop it. During a pandemic, transmission can be anticipated in the workplace, not only from patient to workers in health care settings, but also among co-workers in general work settings. A pandemic would cause high levels of illness, death, social disruption, and economic loss. Everyday life would be disrupted because so many people in so many places become seriously ill at the same time. Impacts could range from school and business closings to the interruption of basic services such as public transportation and food delivery. Education and outreach are critical to preparing for a pandemic.
Understanding what a pandemic is, what needs to be done at all levels to prepare for pandemic influenza, and what could happen during a pandemic helps us make informed decisions both as individuals and as a nation.
Action steps
- Identify a pandemic coordinator and/or team with defined roles and responsibilities for preparedness and response planning.
- Identify essential employees and other critical inputs (e.g. raw materials, suppliers, sub-contractor services/ products, and logistics) required to maintain business operations by location and function during a pandemic.
- Train and prepare ancillary workforce (e.g. contractors, employees in other job titles/descriptions, retirees).
- Develop and plan for scenarios likely to result in an increase or decrease in demand for your products and/or services during a pandemic (e.g. effect of restriction on mass gatherings, need for hygiene supplies).
- Determine potential impact of a pandemic on company business financials using multiple possible scenarios that affect different product lines and/or production sites.
- Determine potential impact of a pandemic on business-related domestic and international travel (e.g. quarantines, border closures).
- Find up-to-date, reliable pandemic information from community public health, emergency management, and other sources and make sustainable links.
- Establish an emergency communications plan and revise periodically. This plan includes identification of key contacts (with back-ups), chain of communications (including suppliers and customers), and processes for tracking and communicating business and employee status.
- Implement an exercise/drill to test your plan, and revise periodically.
- Forecast and allow for employee absences during a pandemic due to factors such as personal illness, family member illness, community containment measures and quarantines, school and/or business closures, and public transportation closures.
- Implement guidelines to modify the frequency and type of face-to-face contact (e.g. hand-shaking, seating in meetings, office layout, shared workstations) among employees and between employees and customers (refer to CDC recommendations).
- Encourage and track annual influenza vaccination for employees.
- Evaluate employee access to and availability of healthcare services during a pandemic, and improve services as needed.
- Evaluate employee access to and availability of mental health and social services during a pandemic, including corporate, community, and faith-based resources, and improve services as needed.
- Identify employees and key customers with special needs, and incorporate the requirements of such persons into your preparedness plan.
- Establish policies for employee compensation and sick-leave absences unique to a pandemic (e.g. non-punitive, liberal leave), including policies on when a previously ill person is no longer infectious and can return to work after illness.
- Establish policies for flexible worksite (e.g. telecommuting) and flexible work hours (e.g. staggered shifts).
- Establish policies for preventing influenza spread at the worksite (e.g. promoting respiratory hygiene/ cough etiquette, and prompt exclusion of people with influenza symptoms).
- Establish policies for employees who have been exposed to pandemic influenza, are suspected to be ill, or become ill at the worksite (e.g. infection control response, immediate mandatory sick leave).
- Establish policies for restricting travel to affected geographic areas (consider both domestic and international sites), evacuating employees working in or near an affected area when an outbreak begins, and guidance for employees returning from affected areas (refer to CDC travel recommendations).
- Set up authorities, triggers, and procedures for activating and terminating the company’s response plan, altering business operations (e.g. shutting down operations in affected areas), and transferring business knowledge to key employees.
Training action plan
All employees should be trained on the employer’s exposure control plan.
Training content should cover:
- The epidemiology and symptoms of pandemics.
- How exposures occur.
- The company’s exposure control plan.
- Recognizing potential exposures.
- Engineering controls affecting trainees.
- Location of handwashing facilities.
- Work practices affecting workers.
- General approach and selection process for Personal Protective Equipment (PPE).
- The company’s procedure to respond to a worker who has been exposed.
- Follow-up available to workers involved in an exposure incident.
Documentation
No current training records exist for non-bloodborne pathogens exposures (e.g., respiratory transmittable diseases). However, OSHA does consider work-related cases of these diseases, like tuberculosis, to be recordable if resulting in lost workdays, medical treatment, etc. The Agency requires employers to make a good-faith effort to determine whether or not the case was more likely than not related to an exposure in the workplace.
Tips
- Train workers who may use disinfectants or other chemicals. In a pandemic, even household cleaners can trigger Hazcom requirements if used more frequently than the manufacturer intends.
- Have a plan to shut-down operations, in case this is necessary or mandated. Also have a plan for keeping equipment, like ventilation and heating/cooling systems, working properly. You also should have a plan for conducting maintenance checks on equipment that has been idle for a while due to unexpected shutdown.
Tips
Review these pandemic checklists.
Assessment
- Has the company identified a pandemic coordinator and/or team with defined roles and responsibilities for preparedness and response planning?
- Has the company identified essential employees and other critical inputs (e.g., raw materials, suppliers, sub-contractor services/products, and logistics) required to maintain business operations during a pandemic?
- Has the company determined the potential impact of a pandemic on company business financials using multiple possible scenarios that affect different product lines and/or production sites?
- Has the company determined potential impact of a pandemic on business-related domestic and international travel (e.g., quarantines, border closures)?
Planning
- Is a pandemic plan in place outlining prevention and response measures the company will take?
- Is an emergency communications plan in place and up to date?
- Does the plan include identification of key contacts (with back-ups), chain of communications (including suppliers and customers), and processes for tracking and communicating business and employee status?
- Is the plan tested periodically by exercises/drills?
- Have policies been established for employee compensation and sick-leave absences unique to a pandemic (e.g., non-punitive, liberal leave), including policies on when a previously ill person is no longer infectious and can return to work after illness?
- Are there policies for flexible worksite (e.g., telecom-muting) and flexible work hours (e.g., staggered shifts)?
- Is there a policy for preventing influenza spread at the worksite (e.g., promoting respiratory hygiene/cough etiquette, and prompt exclusion of people with influenza symptoms)?
- Are policies in place for employees who have been exposed to pandemic influenza, are suspected to be ill, or become ill at the worksite (e.g., infection control response, immediate mandatory sick leave)?
- Are policies in place for restricting travel to affected geographic areas (consider both domestic and international sites), evacuating employees working in or near an affected area when an outbreak begins, and guidance for employees returning from affected areas (refer to CDC travel recommendations)?
- Has the company set up authorities, triggers, and procedures for activating and terminating the company’s response plan, altering business operations (e.g., shutting down operations in affected areas), and transferring business knowledge to key employees?
- Have resources been allocated to protect employees and customers during a pandemic (e.g., hand-hygiene products, tissues, and disposal containers)?
Training and communication
- Are employees made aware of the company’s pandemic preparedness and response plan?
- Has the company developed and disseminated programs and materials covering pandemic fundamentals (e.g., signs and symptoms of influenza, modes of transmission), personal and family protection and response strategies (e.g., hand hygiene, coughing/ sneezing etiquette, contingency plans)?
- Is information provided for the at-home care of ill employees and family members?
- Are means (e.g., hotlines, dedicated websites) set up for communicating pandemic status and actions to employees, vendors, suppliers, and customers inside and outside the worksite in a consistent and timely way, including redundancies in the emergency contact system?
- Has training been provided to ancillary workforce (e.g., contractors, employees in other job titles/ descriptions, retirees)?
External organizations
- Does the company collaborate with insurers, health plans, major local healthcare facilities, and local, state, and federal public health agencies to share pandemic plans and understand their capabilities and plans?
Respiratory protection
OSHA’s 1910.134 regulation applies to workers who perform welding, spray painting, grinding, sanding or related processes. Respirators are generally needed to protect employees from harmful dusts, fogs, fumes, mists, gases, smokes, sprays, and vapors when engineering controls, such as containment, ventilation, or the use of a less toxic substance, fail to provide adequate protection.
Action steps
- Identify and evaluate the respiratory hazard(s) in the workplace.
- Develop and implement a written respiratory protection program with required worksite-specific procedures and elements for required respirator use.
- Conduct evaluations of the workplace as necessary to ensure that the provisions of the current written program are being effectively implemented, and that it continues to be effective.
- Select and provide appropriate respirators.
- Train employees on respiratory protection.
- Provide a medical evaluation to determine the employee’s ability to use a respirator.
- Identify a physician or other licensed health care professional (PLHCP) to perform medical evaluations.
- Fit-test employees with the same make, model, style, and size of respirator that will be used.
- Clean and disinfect respirators per OSHA requirements.
- Store all respirators to protect them from damage, contamination, dust, sunlight, extreme temperatures, excessive moisture, and damaging chemicals.
- Use compressed air, compressed oxygen, liquid air, and liquid oxygen for respiration that meets OSHA specifications.
- Retain records of medical evaluations required by 1910.134, AND make them available in accordance with 1910.1020.
- Establish a record of the qualitative and quantitative fit tests administered to an employee.
- Retain fit test records for respirator users until the next fit test is administered.
- Retain a written copy of the current respirator program.
- Provide any retained written materials, upon request, to affected employees and to OSHA or designee for examination and copying.
Training action plan
You must train all employees who are, or may be, exposed to air contaminants above the permissible exposure limits or suggested exposure levels. You should also train employees who use respirators voluntarily or because of company policy.
Training must precede the use of a respirator. Retraining is required to be conducted annually, and whenever necessary to ensure safe use.
Generally, content for respiratory protection training should cover:
- Why the respirator is necessary.
- Type of respirator employees will be using.
- Proper fit, usage, and maintenance.
- Inspecting, putting on, and removal of respirator.
- Use and seal check of the respirator.
- Cleaning, storing, and repairing respirators.
- Responding to emergencies that involve respirator use.
- Recognizing medical signs and symptoms that may limit or prevent the effective use of respirators.
- The respiratory protection regulation.
Tips
- Whenever OSHA standards or employers require respirator use, there must be a complete respiratory protection program—even for N95 respirators. For voluntary use, the actions employers must take are not as substantial.
- Employees need to wear respirators whenever engineering and work practice control measures are not adequate to prevent atmospheric contamination at the worksite.
- A fit test is a method used to select the right size respirator for the user. A user seal check is a method to check to see if the user has correctly put on the respirator and adjusted it to fit properly.
- Dust masks are considered filtering facepieces under the Respiratory Protection standard, and are therefore, a type of respirator.
- Fit testing must be done prior to respirator use, when a different type of respirator is used, and at least annually thereafter.
- The “grimace exercise” is intended to test the respirator’s ability to reseal to the wearer’s face.
Checklist
Review these respiratory protection checklists to ensure safety and compliance at your facility.
Use
- Is the correct type of respirator being worn, where appropriate, by personnel?
- Do you conduct fit testing using the procedures set forth in Appendix A to 1910.134?
- Do individuals who use a tight-fitting respirator perform a user seal check each time the respirator is put on?
Respiratory protection program
- Do you have a written and implemented respiratory protection program with required worksite-specific procedures and elements?
- Has the program been updated as necessary to reflect those changes in workplace conditions that affect respirator use?
- Have you designated a qualified program administrator to oversee and evaluate the respiratory protection program?
Cleaning and inspection
- Are respirators cleaned according to the provisions of Appendix B-2 to 1910.134, or according to the recommendations of the manufacturer?
- Are all respirators used in routine situations inspected before each use, and during cleaning?
- Are all respirators maintained for use in emergency situations inspected at least monthly and in accordance with the manufacturer’s recommendations?
- Are all respirators maintained for use in emergency situations checked for proper function before and after each use?
- Are all emergency escape-only respirators inspected before being carried into the workplace for use?
Repairs
- Are repairs made according to the manufacturer’s recommendations and specifications for the type and extent of repairs to be performed?
Storage
- Are all respirators stored so that they are protected from damage?
Training and information
- Do you provide effective training to employees who are required to use respirators?
- Is the training comprehensive, understandable, and given annually (or more often if necessary)?
- Is the training provided before employees are required to use a respirator in the workplace?
Respirators for IDLH atmospheres
- Are all oxygen-deficient atmospheres considered IDLH?
- Do you provide appropriate respiratory protection for IDLH atmospheres?
Silica
Exposure to respirable crystalline silica can lead to lung cancer, silicosis, chronic obstructive pulmonary disease, and kidney disease in workers. OSHA’s rule on silica exposure requires employers to protect employees.
Action steps
- Survey your operations for potential exposure to silica. Employers can consult their suppliers or examine safety data sheets (SDSs) to identify silica-containing materials that are present in the workplace.
- Measure the amount of silica that workers are exposed to if it may be at or above an action level of 25 μg/m 3 (micrograms of silica per cubic meter of air), averaged over an 8-hour day.
- Protect workers from respirable crystalline silica exposures above the permissible exposure limit of 50 μg/m 3, averaged over an 8-hour day.
- Limit workers’ access to areas where they could be exposed above the PEL.
- Use dust controls to protect workers from silica exposures above the PEL.
- Provide respirators to workers when dust controls cannot limit exposures to the PEL.
- Restrict housekeeping practices that expose workers to silica where feasible alternatives are available.
- Establish and implement a written exposure control plan that identifies tasks that involve exposure and methods used to protect workers.
- Offer medical exams — including chest X-rays and lung function tests — every three years for workers exposed at or above the action level for 30 or more days per year.
- Train workers on work operations that result in silica exposure and ways to limit exposure.
- Keep records of workers’ silica exposure and medical exams.
Training action plan
It is critically important that workers recognize the hazards associated with exposure to silica and understand the measures they can take to protect themselves. OSHA’s Hazard Communication standard (29 CFR 1910.1200) establishes requirements for employers to provide workers with information on hazardous substances through comprehensive hazard communication programs that include SDSs, labels, and worker training. Employers must follow the requirements of the Hazard Communication standard with regard to workers exposed to silica.
- Provide details of the organization’s written hazard communication program. Employers must have a written hazard communication program that describes the labeling system, SDSs, and how employees receive training.
- The written hazard communication program must also include a list of the hazardous chemicals known to be present in the workplace.
- Employees must have access to SDSs and the written hazard communication program.
- Explain the requirements of OSHA’s silica standard.
- Inform workers of operations where silica is present. Exposures to crystalline silica dust occur in common workplace operations involving cutting, sawing, drilling, and crushing of concrete, brick, block, rock, and stone products (such as construction tasks), and operations using sand products (such as in glass manufacturing, foundries, sand blasting, and hydraulic fracturing).
- Explain the hazards of silica. Workers who inhale very small crystalline silica particles are at increased risk of developing serious — and often deadly — silica-related diseases. These tiny particles (known as “respirable” particles) can penetrate deep into workers’ lungs and cause silicosis, an incurable and sometimes fatal lung disease. Crystalline silica exposure also puts workers at risk for developing lung cancer, other potentially debilitating respiratory diseases such as chronic obstructive pulmonary disease, and kidney disease. Approximately 2.3 million people in the U.S. are exposed to silica at work.
- Describe how employees can be exposed to silica. Respirable crystalline silica – very small particles typically at least 100 times smaller than ordinary sand found on beaches or playgrounds – is generated by high-energy operations like cutting, sawing, grinding, drilling and crushing stone, rock, concrete, brick, block and mortar; or when using industrial sand. Activities such as abrasive blasting with sand; sawing brick or concrete; sanding or drilling into concrete walls; grinding mortar; manufacturing brick, concrete blocks, or ceramic products; and cutting or crushing stone generates respirable dust.
- Describe the monitoring and exposure determination process at the company. Employees must be notified of silica exposure determinations.
- Describe control measures employees can take to protect themselves. Employers must use engineering and work practice controls to reduce and maintain employee exposure to respirable crystalline silica to or below the PEL, unless the employer can demonstrate that such controls are not feasible. Wherever such feasible engineering and work practice controls are not sufficient to reduce employee exposure to or below the PEL, the employer must nonetheless use them to reduce employee exposure to the lowest feasible level and shall supplement them with the use of respiratory protection. Employees must use respiratory protection when it has been deemed necessary. Employees should also use proper housekeeping procedures, comply with medical surveillance requirements, observe warning/caution signs, and be aware of their rights to review the employer’s program.
- Describe the medical surveillance program. The purpose of medical surveillance is to identify adverse health effects associated with respirable crystalline silica exposure so that appropriate actions can be taken; determine if an employee has any condition, such as a lung disease, that might make him or her more sensitive to respirable crystalline silica exposure; and determine the employee’s fitness to use respirators.
- In response to the information gained through medical surveillance, employees can take actions to improve their health, such as making job choices to reduce exposures, wearing a respirator for extra protection, or making personal lifestyle or health decisions, such as quitting smoking or getting flu shots.
- Make a copy of OSHA’s silica standard available to employees.
Checklist
Review these silica checklists to ensure safety and compliance at your facility.
General
- Are employees aware of the hazards involved with silica if they may be exposed to it in their work environment?
- Is a written exposure control plan implemented?
Training
- Have you instituted a training program for all employees who are subject to silica exposure?
Monitoring
- Is employee exposure monitored and kept within acceptable levels?
- Are engineering and work practice controls used to reduce exposures to a permissible level?
Employee protection
- Are engineering controls used where feasible?
- Is personal protective equipment (PPE) provided and are all employees required to use PPE as needed?
- Is PPE functional and in good repair?
Respiratory protection
- Is a respiratory protection program in place?
- Are employees provided proper respiratory protection?
Medical surveillance
- Is a medical surveillance program in place for employees who may be exposed to silica?
Marking and labeling
- Are caution labels and signs used to warn of silica presence and hazards?
- Has a regulated area been established, and marked, where appropriate?
- Are containers used to store this substance marked appropriately?
Recordkeeping
- Are appropriate records maintained (exposure monitoring, medical surveillance, etc.)?
- Are employees given access to their exposure and medical records upon request?
Hazard communication
- Do you have a safety data sheet for every hazardous chemical you have at your facility?
- Do you maintain a written hazard communication program?
- Have you compiled a hazardous chemical inventory?
- Have you documented the employee training that you have done under the hazard communication standard?
- Are all chemical containers marked with contents name and hazards?
Ventilation
- Are ventilation systems used where appropriate?
Housekeeping
- Are all work areas clean, sanitary, orderly and adequately illuminated?
- Are adequate cleaning methods used (e.g., wet sweeping or HEPA-filter vacuuming)?
- Are contaminated materials disposed of properly?
Gathering information and performing inspections
- Employers may already have internal and external data available to help with identifying hazards, including equipment operating manuals, Safety Data Sheets, inspection reports, records of previous illness/injury, and more.
- Employers must arrange for regular safety inspections, as well as inspections whenever working conditions (work processes, equipment, etc.) change. A follow-up plan is needed to ensure any safety issues found are corrected.
Information on hazards may already be available to employers and workers, from both internal and external sources.
Employers should collect, organize, and review information with workers to determine what types of hazards may be present and to which workers may be exposed or potentially exposed. Information available may include:
- Equipment and machinery operating manuals.
- Safety Data Sheets (SDS) provided by chemical manufacturers.
- Self-inspection reports and inspection reports from insurance carriers, government agencies, and consultants.
- Records of previous injuries and illnesses, such as Occupational Safety and Health Administration (OSHA) 300 and 301 logs and reports of incident investigations.
- Workers’ compensation records and reports.
- Patterns of frequently-occurring injuries and illnesses.
- Exposure monitoring results, industrial hygiene assessments, and medical records (appropriately redacted to ensure patient/worker privacy).
- Existing safety and health programs (lockout/tagout, confined spaces, process safety management, personal protective equipment, etc.).
- Input from workers, including surveys or minutes from safety and health committee meetings.
- Results of job hazard analyses, also known as job safety analyses.
Information about hazards may also be available from outside sources such as:
- Occupational Safety and Health Administration (OSHA), National Institute for Occupational Safety and Health (NIOSH), and Centers for Disease Control and Prevention (CDC) websites, publications, and alerts.
- Trade associations.
- Labor unions, state and local occupational safety and health committees/coalitions (“COSH groups”), and worker advocacy groups.
- Safety and health consultants.
Inspecting the workplace for safety hazards
Hazards can be introduced over time as workstations and processes change, equipment or tools become worn, maintenance is neglected, or housekeeping practices decline. Setting aside time to regularly inspect the workplace for hazards can help identify shortcomings so that they can be addressed before an incident occurs. Employers should:
- Conduct regular inspections of all operations, equipment, work areas and facilities. Have workers participate on the inspection team and talk to them about hazards that they see or report.
- Document inspections to later verify that hazardous conditions are corrected. Take photos or video of problem areas to facilitate later discussion and brainstorming about how to control them, and for use as learning aids.
- Include all areas and activities in these inspections, such as storage and warehousing, facility and equipment maintenance, purchasing and office functions, and the activities of on-site contractors, subcontractors, and temporary employees.
- Regularly inspect both plant vehicles (e.g., forklifts, powered industrial trucks) and transportation vehicles (e.g., cars, trucks).
- Use checklists that highlight things to look for. Typical hazards fall into several major categories, such as those listed below, although each workplace will have its own list:
- General housekeeping;
- Slip, trip, and fall hazards;
- Electrical hazards;
- Equipment operation;
- Equipment maintenance;
- Fire protection;
- Work organization and process flow (including staffing and scheduling);
- Work practices;
- Workplace violence;
- Ergonomic problems; and
- Lack of emergency procedures.
Employers should also plan to do safety inspections before changing operations, workstations, or workflow; making major organizational changes; or introducing new equipment, materials, or processes, seeking the input of workers and evaluating the planned changes for potential hazards and related risks.
Many hazards can be identified using common knowledge and available tools. For example, workers can easily identify or remove hazards such as broken stair rails or frayed electrical cords. Workers can be a very useful internal resource, especially if they are trained in how to identify and assess risks.
Identifying health hazards
- Health hazards that may be identified might be chemical, physical, biological, or ergonomic.
- In some cases, identifying such hazards may require specialized knowledge; small businesses can often obtain this help for free through OSHA’s On-Site Consultation Program.
Identifying health hazards is typically more complex than identifying physical safety hazards. For example, gases and vapors may be invisible, often have no odor, and may not have an immediately noticeable harmful health effect.
Health hazards include chemical hazards (solvents, adhesives, paints, toxic dusts, etc.); physical hazards (noise, radiation, heat, etc.); biological hazards (infectious diseases); and ergonomic risk factors (heavy lifting, repetitive motions, vibration).
Reviewing workers’ medical records (appropriately redacted to ensure patient/worker privacy) can be useful in identifying health hazards associated with workplace exposures. Employers should:
- Identify chemical hazards — Review Safety Data Sheets (SDSs) and product labels to identify chemicals in the workplace that have low exposure limits, are highly volatile, or are used in large quantities or in unventilated spaces. Identify activities that may result in skin exposure to chemicals.
- Identify physical hazards — Identify any exposures to excessive noise (areas where workers must raise their voices to be heard by others), elevated heat (indoor and outdoor), or sources of radiation (radioactive materials, X-rays, or radiofrequency radiation).
- Identify biological hazards — Determine whether workers may be exposed to sources of infectious diseases, molds, toxic or poisonous plants, or animal materials (fur or scat) capable of causing allergic reactions or occupational asthma.
- Identify ergonomic risk factors — Examine work activities that require heavy lifting, work above shoulder height, repetitive motions, or tasks with significant vibration.
- Conduct quantitative exposure assessments — When possible, using air sampling or direct reading instruments.
- Review medical records — To identify cases of musculoskeletal injuries, skin irritation or dermatitis, hearing loss, or lung disease that may be related to workplace exposures.
Identifying and assessing health hazards may require specialized knowledge. Small businesses can obtain free and confidential occupational safety and health advice services, including help identifying and assessing workplace hazards, through the Occupational Safety and Health Administration (OSHA)’s On-Site Consultation Program.
Conducting incident investigations
- Thoroughly investigating all safety incidents helps an employer to identify where hazards exist in their workplaces.
- Effective incident investigations will not stop when a single cause of an incident is found, but should continue until the root cause — the “why” — is identified.
Workplace incidents — including injuries, illnesses, close calls/near misses, and reports of other concerns — provide a clear indication of where hazards exist. Thoroughly investigating incidents and reports will help identify hazards that are likely to cause future harm. The purpose of an investigation must always be to identify the root causes (and there is often more than one) of the incident or concern, in order to prevent future occurrences. Employers should:
- Develop a clear plan and procedure for conducting incident investigations, so that an investigation can begin immediately when an incident occurs. The plan should cover items such as:
- Who will be involved;
- Lines of communication;
- Materials, equipment, and supplies needed; and
- Reporting forms and templates.
- Train investigative teams on incident investigation techniques, emphasizing objectivity and open-mindedness throughout the investigation process.
- Conduct investigations with a trained team that includes representatives of both management and workers.
- Investigate close calls/near misses.
- Identify and analyze root causes to address underlying program shortcomings that allowed the incidents to happen.
- Communicate the results of the investigation to managers, supervisors, and workers to prevent recurrence.
Effective incident investigations do not stop at identifying a single factor that triggered an incident. They ask the questions “Why?” and “What led to the failure?” For example, if a piece of equipment fails, a good investigation asks: “Why did it fail?” “Was it maintained properly?” “Was it beyond its service life?” and “How could this failure have been prevented?” Similarly, a good incident investigation does not stop when it concludes that a worker made an error. It asks such questions as: “Was the worker provided with appropriate tools and time to do the work?” “Was the worker adequately trained?” and “Was the worker properly supervised?”
Identifying Physical Hazards
What are physical hazards?
Physical hazards abound in the workplace. The mere fact that a company exists makes it prone to physical hazards — even the benign office has tripping and falling hazards. In an industrial setting, the huge variety of machines, processes, and equipment create a challenging set of hazards that a safety professional must deal with.
Processes that use large quantities of chemicals present a unique set of challenges. The physical properties of certain chemicals, such as flammable and combustible liquids, compressed gases, solvents, and explosives make them highly dangerous.
You may not think much about falls, but trips and falls often result in injury and lost time. Falls can even be fatal. In the workplace, there are many situations that contribute to falls:
- Floors with water, grease, or cracks
- Trash or stock piled in pedestrian walkways
- Ladders in need of repair
- Stairs with loose rails or step treads
Maintaining equipment in peak condition, practicing good housekeeping techniques, and providing signs to warn of physical hazards goes a long way to improve overall safe working conditions. Part of the safety professional’s job is to assess the workplace for physical hazards and see that they are corrected or controlled. There are many OSHA standards that have specific requirements for ensuring that physical hazards in the workplace are eliminated. In this section, you will find action steps, training action plans, tips, and checklists on a variety of topics related to controlling physical hazards.
Combustible dust
Combustible dusts are fine particles that present an explosion hazard when suspended in air in certain conditions. A dust explosion can be catastrophic and cause employee deaths, injuries, and destruction of entire buildings. In many combustible dust accidents, employers and employees were unaware that a hazard even existed. It is important that employers determine if their operations have this hazard, and if so, that they take action now to prevent tragic consequences.
A wide range of industries possess combustible dust hazards and a wide variety of materials cause combustible dust incidents. (Combustible dusts can be intentionally manufactured powders, such as corn starch or aluminum powder coatings, or may be generated by handling and processing solid combustible materials such as wood and plastic pellets. For example, polishing, grinding, transporting, and shaping many of these materials can produce very small particles.)
Action steps
The following are general action steps that should be taken to identify and control dust hazards. For detailed guidance specific to your operations, consult with a qualified professional, as well as industry standards, as applicable (for example, those published by the National Fire Protection Association).
- Assess your facility for processes that generate dust. Have dusts analyzed for combustibility hazards. (There are several factors that determine how explosive a dust can be, as well as some key measurements for determining dust explosibility. These include particle size, moisture content, ambient humidity, oxygen available for combustion, the shape of the dust particle, and the concentration of dust in the air, i.e., minimum explosive concentration or MEC.)
- Understand the five elements needed for a combustible dust explosion: Combustible dust (fuel); ignition source (heat); oxygen in air (oxidizer); dispersion of dust particles in sufficient quantity and concentration; and confinement of the dust cloud.
- Understand that there can be a primary explosion or event that shakes loose hidden dust (for example, from piping or rafters) which can cause a devastating secondary explosion.
- Ensure operations have proper engineering design and controls and inspect/maintain those controls. Seek outside assistance/expertise as needed to ensure proper dust control procedures/methods are in place.
- Develop an ignition control program, limiting and controlling potential ignition sources in dust accumulation areas.
- Train employees on the explosion hazards of combustible dusts.
- Implement a housekeeping program with regular cleaning frequencies for floors and horizontal surfaces, such as ducts, pipes, hoods, ledges, and beams, to minimize dust accumulations within operating areas of the facility. (Even seemingly small amounts of accumulated dust can cause catastrophic damage. The CSB estimated, for example, that the explosion that devastated a pharmaceutical plant in 2003 and killed six employees was caused by dust accumulations mainly under 0.25 inches deep. The CSB study references National Fire Protection Administration (NFPA) warnings that a catastrophic explosion can occur from as little as 1/32 of an inch of accumulated dust — around the thickness of a dime — covering just 5 percent of a room’s surface.)
- Ensure working surfaces are designed in a manner to minimize dust accumulation and facilitate cleaning.
- Ensure electrical equipment and electrically-powered cleaning devices such as vacuum cleaners are approved for the hazard classification for Class II locations.
- Select and use industrial trucks that are approved for the combustible dust locations.
- Prohibit the use of cleaning methods that can disperse combustible dust into the air (i.e., compressed air and dry sweeping).
- Ensure the ready availability of SDSs for the chemicals which could become combustible dust under normal operations. Note: The Chemical Safety Board has found that many SDSs do not provide sufficient data on combustible dust hazards. However, OSHA revised the HazCom rule in 2012. In the revised rule, combustible dust hazards must be addressed on labels and SDSs. Label elements are provided for combustible dust in the final HCS and include the signal word “warning” and the hazard statement “May form combustible dust concentrations in the air.”
- Implement an emergency action plan and maintain exit routes properly.
For chemicals in a solid form that do not present a combustible dust hazard, but may form combustible dusts while being processed in normal downstream uses, OSHA allows the chemical manufacturer some flexibility in labeling requirements. The manufacturer or importer may transmit the label to the customer at the time of the initial shipment, but the label does not need to be included with subsequent shipments unless it changes. This provides the needed information to the downstream users on the potential hazards in the workplace, while acknowledging that the solid metal or other materials do not present the same hazards that are produced when these materials are processed under normal conditions of use.
Training action plan
Workers are the first line of defense in preventing and mitigating fires and explosions. If the people closest to the source of the hazard are trained to recognize and prevent hazards associated with combustible dust in the plant, they can be instrumental in recognizing unsafe conditions, taking preventative action, and/or alerting management. While OSHA standards require training for certain employees, all employees should be trained in safe work practices applicable to their job tasks, as well as on the overall plant programs for dust control and ignition source control. They should be trained before they start work, periodically to refresh their knowledge, when reassigned, and when hazards or processes change.
- Define combustible dusts.
Combustible dusts are fine particles,
fibers, chips, chunks, or flakes
that could be an explosion hazard
when they’re suspended in air
under certain conditions.
Many products can be fuel for a
dust explosion when they’re used in powdered form. Here are some
examples:
- Flour, sugar, powdered milk, or other food-related products;
- Wood;
- Paper;
- Textiles;
- Charcoal and other carbon-rich materials;
- Sulfur and other chemicals;
- Aluminum, zinc, and other metals; and
- Epoxy resin and other plastics.
- Introduce the hazards.
A dust explosion can cause deaths
and serious injuries. An explosion
can destroy an entire building. In
many combustible dust incidents,
employers and employees didn’t
know that a hazard even existed.
Here’s an example of what happens
during a combustible dust explosion.
- In February 1999, a deadly fire and explosion occurred in a foundry in Massachusetts. An investigation found that a fire started in a molding machine and then spread to ventilation ducts. The small initial explosion in the ductwork disturbed resin dust that had settled on the outside of the ducts, creating a dust cloud. This dust provided fuel for a secondary explosion that was powerful enough to lift the roof and cause walls to collapse.
- Identify the types of industries that may be at risk. Combustible dust explosion hazards can exist in a variety of industries, including: agriculture, chemicals, food, grain, fertilizer, tobacco, plastics, wood, paper, tire and rubber, furniture, textiles, pesticides, pharmaceuticals, coal, metal processing, recycling operations, and others.
- Explain how dust explosions can happen. The familiar fire triangle is made up of: oxygen, an ignition source (heat), and fuel. All three conditions must be present for a fire to start. Because oxygen is normally always present in the air, fires are usually prevented by keeping the fuel separate from the ignition source. In addition to the fire triangle elements, the “dust explosion pentagon” adds two more conditions: dust particles and the confinement of the dust cloud. Similar to the fire triangle, if one part of the pentagon is missing, a combustible dust explosion can’t occur. If a dust cloud is ignited in an enclosed area such as a room, vessel, ductwork, or process equipment, it burns very fast and may explode. Even if the initial explosion is small, it could shake up accumulated dust in the area to form another dust cloud. Often these secondary explosions are far more destructive.
- Outline how to look for combustible
dust hazards.
To identify the factors that could
contribute to an explosion, employers
should evaluate the hazards of
all: materials, operations, spaces (including hidden ones),
and potential ignition sources. Some likely areas where dust can
build up include:
- Parts of the building’s structure,
- Conduit and pipe racks,
- Electrical cable trays,
- Floors,
- Areas above suspended ceilings, and
- On and around equipment (including leaks around dust collectors and ductwork).
- Discuss what can be done to
control dust build-up.
If the dust isn’t building up, it lowers the risk of a dust explosion. There
are many ways to keep dust under
control. Some of these methods are
to:
- Conduct regularly scheduled inspections,
- Clean up dust on a regular basis,
- Use proper dust collection systems and filters,
- Keep dust from escaping from equipment or ventilation systems,
- Use surfaces that are easy to clean,
- Provide easy access to inspect and clean hidden areas where dust might build up,
- Use cleaning methods that don’t stir up dust clouds, and
- Use vacuum cleaners approved for dust collection.
- Describe methods to prevent
dust from igniting.
Keeping ignition sources under
control is an important part of any
fire safety program. Some actions
employers can take include the following:
- Use proper wiring methods;
- Make sure electrically powered equipment (including forklifts) is approved for the location;
- Control static electricity (bond equipment to ground);
- Keep smoking areas, open flames, sparks, and heated surfaces separate from dusts;
- Follow a hot work permit program; and
- Follow a preventive maintenance program.
- Discuss some methods to minimize
injuries and damage from
a combustible dust explosion.
Some of the steps employers can
take to minimize injuries and damage
from a combustible dust explosion
could include:
- Developing an emergency action plan,
- Maintaining emergency exit routes,
- Setting up operations in areas where the hazards are away from workers and equipment,
- Setting up isolation barriers around hazardous operations,
- Making sure dust handling equipment has pressure relief venting that’s directed away from workers and equipment, and
- Installing specialized spark detection and fire suppression systems in dust handling equipment.
Tips
The amount of dust accumulation necessary to cause an explosive concentration can vary greatly. This is because there are so many variables — the particle size of the dust, the method of dispersion, ventilation system modes, air currents, physical barriers, and the volume of the area in which the dust cloud exists or may exist. As a result, simple rules of thumb regarding accumulation (such as writing in the dust or visibility in a dust cloud) can be subjective and misleading. The hazard analysis should be tailored to the specific circumstances in each facility and the full range of variables affecting the hazard.
Many locations need to be considered in an assessment. One obvious place for a dust explosion to initiate is where dust is concentrated. In equipment such as dust collectors, a combustible mixture could be present whenever the equipment is operating.
Other locations to consider are those where dust can settle, both in occupied areas and in hidden concealed spaces. A thorough analysis will consider all possible scenarios in which dust can be disbursed, both in the normal process and potential failure modes.The facility analysis must identify areas requiring special electrical equipment classification due to the presence (or potential presence) of combustible dust. Various OSHA standards as well as industry (e.g., NFPA) can be consulted.
Checklist
Follow these checklists to prevent combustible dust hazards.
Hazard assessment
- Are there processes that accumulate dust? If so, have the dusts been analyzed for combustibility?
- Are periodic assessments conducted to determine dust explosion possibilities?
- Are employees and supervisors involved in identifying dust explosion hazards, for example through job hazard analyses?
- Is particular attention given during the hazard assessment to dust collection systems and areas not in plain view?
Prevention
- Have proper engineering design and controls been implemented for operations involving combustible dust; for example, dust control in process equipment and fugitive dust control; grounding and bonding; and separator devices?
- Is a comprehensive housekeeping program implemented?
- Are potential ignition sources limited and controlled in dust accumulation areas?
- Is it prohibited to use compressed air and similar cleaning methods that could disperse combustible dusts into the air?
- Are electrical services appropriate for Class II location? Consult applicable codes, for example the National Electrical Code.
- Are industry standards, such as NFPA 654, followed as applicable?
- Is a preventive maintenance program in place to minimize release of fugitive dust?
Note: Minor, but steady leaks, can cause large amounts of dust to accumulate.
Training
- Have employees received training on the hazards of dust?
- Have employees received training on specific characteristics of the dust that they work with?
- Have employees been trained to recognize potential ignition sources?
- Do employees know which processes/locations accumulate dust (for example, cable trays, pipe racks, floors, above ceilings, and structural members)?
- Are employees instructed to report plant fires and near misses?
Confined spaces
Employees in industry and construction are often asked to perform work in confined spaces, but many confined spaces contain serious hazards that endanger the employees who enter those spaces. For this reason, the Occupational Safety and Health Administration requires employers to implement certain procedures that protect workers from the hazards posed by confined spaces. These include procedures for identifying physical hazards and hazardous atmospheres in confined spaces, controlling and eliminating these hazards, and more.
Action steps
- Evaluate the workplace to determine if any spaces are permit-required confined spaces.
- Inform exposed employees, by posting danger signs or by any other equally effective means, of the existence and location of and the danger posed by the permit spaces.
- Decide whether employees will enter spaces. (If employees will not enter spaces, take appropriate, effective prevention measures.)
- Implement a written permit space program.
- Evaluate hazards of permit spaces.
- Provide employees with the opportunity to observe any monitoring or testing of permit spaces.
- Develop and implement the means, procedures, and practices necessary for safe permit space entry operations.
- Establish a permit system.
- Provide training.
- Perform entry according to OSHA requirements.
- Verify that conditions in the permit space are acceptable for entry throughout the duration of an authorized entry.
- Provide appropriate equipment (PPE, rescue equipment, testing, monitoring, ventilation, lighting, etc.)
- Provide at least one attendant outside the permit space into which entry is authorized for the duration of entry operations.
- Develop and implement rescue procedures.
- If contractors are involved in the confined space entry, follow pertinent OSHA requirements.
Training action plans
Training must be such that all employees whose work is regulated by OSHA’s confined spaces standard acquire the understanding, knowledge, and skills necessary for the safe performance of the duties assigned.
Training must be provided to each affected employee:
- Before the employee is first assigned duties relative to the confined space.
- Before there is a change in assigned duties.
- Whenever there is a change in permit space operations that presents a hazard about which an employee has not previously been trained.
- Whenever you have reason to believe either that there are deviations from the permit space entry procedures or that there are inadequacies in the employee’s knowledge or use of these procedures.
The training must establish employee proficiency in the duties required by the confined spaces standard and must introduce new or revised procedures, as necessary, for compliance.
Training should be specific to the employee’s function relative to the confined space. For instance, if the employee is an authorized entrant, then training should focus specifically on tasks and hazards he may face in this role.
In general, training should cover:
- Equipment to be used,
- Communicating with others involved in the work,
- Hazard awareness and recognition,
- Specific roles and duties,
- Monitoring,
- Medical and first aid, and
- Rescue.
Any work that involves contractors also requires special training and communication, both from the host to the contractor and from the contractor to the host.
Documentation
The employer must certify that required training has been accomplished. The certification must contain:
- Each employee’s name,
- The signatures or initials of the trainers, and
- The dates of training.
Tips
- A permit-required confined space is a confined space that has one or more of the following characteristics:
- Contains or has the potential to contain a hazardous atmosphere;
- Contains a material that has the potential for engulfing an entrant;
- Has an internal configuration such that an entrant could be trapped or asphyxiated by inwardly converging walls or by a floor which slopes downward and tapers to a smaller cross section; or
- Contains any other recognized serious safety or health hazard.
- When workers enter a permit space, at least one person must remain outside to monitor, summon help, or provide assistance.
- An attendant may attend to more than one permit space provided he/she can perform all required duties without compromising the safety of any entrant in all spaces being monitored (there is no proximity requirement).
- An employee can be both an entry supervisor and entrant as long as the employee has had the appropriate training and the duties of one activity do not conflict with the duties of the other.
- The entrants need to wear chest or full body harnesses with retrieval lines to make non-entry rescue attempts easier.
- The attendant needs to communicate with the entrants to monitor their conditions. If a situation arises that requires emergency rescue, the attendant should summon the rescue service and stay outside of the permit space entrance.
- An attendant can be a trained member of the rescue service, but cannot enter the permit space until the rest of the team has arrived to start proper rescue procedures.
Checklist
View these confined space checklists to ensure safety and compliance at your facility.
Monitoring
- When working in permit-required confined spaces, are environmental monitoring tests taken?
- Are authorized entrants or their representatives provided an opportunity to observe any monitoring or testing of permit spaces?
- Are permit spaces tested to determine if acceptable entry conditions exist prior to entry?
- Are permit spaces tested or monitored as necessary to determine if acceptable entry conditions are being maintained during the course of entry operations?
Equipment
- Is necessary personal protective equipment available?
- Is rescue and emergency services equipment available?
- Is communications equipment provided to allow the attendant to communicate with authorized entrants as necessary to monitor entrant status and to alert entrants of the need to evacuate the permit space?
General
- Are those having active roles in entry operations appropriately designated (for example, authorized entrants, attendants, entry supervisors, and persons who test or monitor the atmosphere in a confined space)?
- Is at least one attendant stationed outside the confined space for the duration of the entry operation?
- Are appropriate rescue personnel available?
- Are permit spaces flushed, ventilated, purged, and rendered inert to eliminate or control atmospheric hazards prior to entry?
Emergency action plans
This regulation applies to all companies that fall under a particular OSHA standard that requires an emergency action plan. However, it is wise for all employers to have action plans for any emergency that may be reasonably expected to occur in the workplace. Where required by OSHA, employers must develop a plan (called an emergency action plan or EAP) for emergency situations so that there is a literal “plan of action” for employees to take in the event of fires, toxic chemical releases, hurricanes, tornadoes, blizzards, floods, and other similar catastrophic events.
Action steps
Include the following minimum requirements in the EAP to ensure that it covers those designated actions employers and employees must take to ensure employee safety from fire and other emergencies.
- Establish emergency escape procedures and emergency escape route assignments.
- Develop procedures to be followed by employees who remain to operate critical plant operations before they evacuate.
- Establish procedures to account for all employees after emergency evacuation has been completed.
- Assign rescue and medical duties for those employees who are to perform them.
- List the preferred means of reporting fires and other emergencies.
- Develop a list of employee names or regular job titles of persons or departments who can be contacted for further information or explanation of duties under the plan.
- Establish an employee alarm system. If the employee alarm system is used for alerting fire brigade members, or for other purposes, use a distinctive signal for each purpose.
- List the types of evacuation to be used in emergency circumstances.
- Designate and train a sufficient number of employees to assist in the safe and orderly emergency evacuation of employees before implementing the EAP.
- Review the EAP with each covered employee upon initial assignment, when the employee’s responsibility or designated actions under the plan change, and when the plan changes.
Training action plan
You should develop an emergency action team prior to implementing the EAP. Begin by designating and training a sufficient number of employees to assist in the safe and orderly emergency evacuation of their coworkers.
- List the names or job titles of persons who can be contacted for more information on the plan. Trainees should understand:
- The employee alarm system,
- How to report fires and other emergencies, and
- Which personnel are designated to perform rescue and medical duties and their individual responsibilities.
- Explain how all employees will be accounted for after the emergency evacuation has been completed. Make sure employees understand:
- Critical plant operations and who is designated to remain behind to operate it/shut it down before they evacuate, and
- Emergency escape procedures and emergency escape routes.
Tips
A map of the facility showing specific areas, exit routes, exit doors, and head count locations is a useful training tool and should also be posted around the company.
If a fire occurs, safe and orderly evacuation is necessary. Your company should have an established evacuation plan, with procedures and exits indicated. Find out what it is and where you are expected to go during a fire or fire drill. A head count location should be established so that once everyone is evacuated, you meet at a designated spot to account for each employee.
Other than fires, severe weather emergencies are the most common emergency situations that occur. Severe weather emergencies include hurricanes, tornadoes, excessive heat, heavy snow, and extreme cold weather conditions.
If a bomb threat is made at your facility, always take the threat seriously. Immediately notify a supervisor or the safety manager of the threat and evacuate the premises (do not search for a bomb unless instructed by police to look for foreign or suspicious objects).
Checklist
Follow these checklists to ensure you and your employees are prepared for any potential emergencies.
Emergency action plan
- Is there an emergency action plan (EAP) in place detailing procedures employees should follow in an emergency?
- Does the EAP include procedures for all anticipated emergency situations (i.e., fire, tornado, bomb threat, or explosion)?
- Does the EAP include escape procedures and routes?
- Does the EAP contain procedures for those remaining in the facility to perform critical operations?
- Do you have headcount procedures (location or methods for accounting for employees)?
- If your company is located in a high-rise building, does your emergency program include appropriate escape information?
- Do you have an employee assistance program or some other means to provide counseling to employees should a disaster occur?
Disaster recovery
- Have you established a work location that could be used should your facility be unavailable due to disaster or emergency?
- Does the temporary work location have all necessary equipment so critical business functions can be carried out?
- Have necessary safety measures been taken to ensure that the temporary location is safe and will have necessary protective equipment?
Rescue workers
- Is air monitoring conducted to make sure rescue area is safe?
- Are rescue workers protected against hazards that may be encountered (i.e., asbestos, silica)?
- Are rescue workers provided proper protective equipment for the hazards they face?
Alarms and warnings
- Does the employee alarm system provide warning for necessary emergency action as called for in the emergency action plan?
- Is the employee alarm capable of being perceived above ambient noise or light levels by all employees in the affected portions of the workplace?
- Is the employee alarm distinctive and recognizable as a signal to evacuate the work area or take necessary actions?
- Have all employees been informed of the preferred means of reporting emergencies, such as manual pull box alarms, public address systems, radio or telephones?
- Are emergency telephone numbers posted near telephones, or employee notice boards, and other conspicuous locations?
- Have procedures been established for sounding emergency alarms in the workplace?
Fire alarm systems
- If you have a non-supervised fire alarm system, is it tested bimonthly?
- If you have a supervised employee alarm system (that is, does the alarm have a device that indicates system malfunction), is it tested yearly?
Entrances and exits
If you are a general industry employer, the Subpart E Exit routes regulations apply to your company. Your facility must provide a safe means of exiting from buildings or structures for the purpose of general egress, or for the purpose of exiting in the case of fire or other emergencies. In addition, you must also provide a clear and unobstructed path to the entrance of your facility.
Action steps
- Make sure exit routes are permanent.
- Separate exits using fire resistant materials.
- Limit openings into an exit.
- Ensure the number of exit routes is adequate.
- Ensure there are at least two exit routes.
- Provide adequate exit discharge.
- Make sure exit doors are unlocked.
- Use side-hinged exit doors.
- Ensure the capacity of exit routes is adequate.
- Provide exit routes that meet minimum height and width requirements.
- Keep exit routes free of explosive or highly flammable furnishings or other decorations.
- Maintain exit routes free and unobstructed.
- Ensure lighting and marking is adequate and appropriate.
- Maintain exit routes during construction, repairs, or alterations.
- Ensure that the alarm system is operable.
Training action plan
You must designate and train employees to assist in a safe and orderly evacuation of other employees.
You must also review the emergency action plan with each employee covered by the plan. This review should be conducted:
- When the plan is developed or the employee is assigned initially to a job,
- When the employee’s responsibilities under the plan change, and
- When the plan is changed.
Tips
- The line-of-sight to an exit sign must be clearly visible at all times.
- Maintain exit routes during construction, repairs, or alterations.
- Ceilings of exit routes must be at least 7 feet, 6 inches high.
- Exit access must be at least 28 inches wide at all points.
Checklist
Review these checklists to ensure exit routes at your facility meet compliance.
Exit design
- Are exit routes made of approved components and permanently attached to the building?
- Are exit routes designed and maintained to provide adequate headroom?
- Are exit doors designed so that no device or alarm failure will impede or prevent emergency use of exits?
Capacity of means of egress
- Are width and capacity of exit routes in compliance with OSHA standards?
- Is the capacity of the exit route sufficient for the occupant load?
- Where more than one way of exit access leads to an exit, does each have a width adequate for the number of persons it must accommodate?
Arrangement of exits
- Have you assured that no furnishings, decorations, or other objects are placed as to obstruct exits or exit visibility?
- Are exits adequately lighted so an employee with normal vision can see along the exit route?
Access to exits
- Are exit doors unlocked?
- Are exits readily accessible at all times?
- Are doors, from a room to an exit or to a way of exit access, of the side-hinged, swinging type?
- Is access to an exit NOT through a bathroom, or other room subject to locking (except where the exit is required to serve only the room subject to locking)?
- Are ways of exit access and the doors to exits to which they lead clearly recognizable as such?
- Is exit access arranged so that it will not be necessary to travel toward any area of high hazard occupancy in order to reach the nearest exit?
- Is exit access travel effectively shielded from high hazard locations by suitable partitions or other physical barriers?
- Is the minimum width of any way of exit access at least 28 inches?
Arrangement of exits
- Are exits marked by a readily visible sign?
- Is access to exits marked by readily visible signs if it is not immediately visible?
- Is any door, passage, or stairway that could be mistaken for an exit or a way of exit access, identified by a sign reading “Not an Exit” or similar designation, or identified by a sign indicating its actual character?
Protective enclosure of exits
- When an exit is protected by separation from other parts of the building, does the separating construction meet OSHA requirements (i.e., 1-hour fire resistance rating when the exit connects three stories or less)?
Fire protection
OSHA has many requirements concerning fire protection in the workplace. These requirements are found in Subpart L and in some other specific standards. Among the items addressed by OSHA standards is fire brigades, all portable and fixed fire suppression equipment, fire detection systems, and fire or employee alarm systems.
Action steps
- Provide approved and appropriate portable fire extinguishers.
- Mount, locate, and identify portable fire extinguishers so that they are readily accessible to employees without subjecting the employees to possible injury.
- Maintain fire extinguishers in a fully charged and operable condition.
- Inspect, maintain, and test fire extinguishers.
- Provide necessary training to employees who are expected to use portable fire extinguishers.
- Ensure that hose and standpipe systems meet OSHA requirements.
- Ensure all automatic sprinkler systems meet OSHA requirements.
- Maintain any fixed extinguishing systems per OSHA requirements.
- Follow OSHA requirements for any fire brigade you choose to form.
- Ensure fire detection systems are maintained properly.
- Provide an employee alarm system that gives warning for necessary emergency action as called for in the emergency action plan, or for reaction time for safe escape of employees from the workplace or the immediate work area, or both.
Training action plan
The level and type of training needed for fire protection depends on the level and type of fire protection your facility has in place. For instance, if you have a fire brigade, extensive training must be provided to fire brigade members, per 1910.156.
Similarly, if you provide portable fire extinguishers for employee use, such employees must be trained. This training must familiarize employees with the general principles of fire extinguisher use and the hazards involved with incipient stage fire fighting. Training must be provided upon initial employment and at least annually thereafter.
You must also provide training to any employees who have been designated to use fire fighting equipment as part of an emergency action plan. Training must be provided upon initial employment and at least annually thereafter.
You should also train all employees on the actions they need to take relative to your emergency alarm system. They should be familiar with the distinct sounds of the system and what each sound means.
Tips
- Fire extinguishers have to be kept in their designated locations at all times when not being used.
- When extinguishers are removed for maintenance or testing, they must be replaced by an operable unit.
Checklists
Review these checklists to ensure fire safety at your facility.
Fire extinguishers
- Are portable fire extinguishers provided, mounted, located, and identified so that they are readily accessible to employees?
- Are only approved portable fire extinguishers used?
- Are portable fire extinguishers maintained, fully charged, operating properly, and kept in designated places?
- Are portable fire extinguishers provided for employee use and selected and distributed based on the classes of anticipated fires and on the size and degree of hazard that would affect their use?
- Are travel distances to extinguishers appropriate?
- Are all portable fire extinguishers in the workplace inspected, maintained, and tested?
- Is hydrostatic testing performed by trained persons with suitable testing equipment and facilities?
- Are portable extinguishers hydrostatically tested at the intervals listed in Table L-1 of 1910.157?
- Has an educational program been provided to familiarize employees with the general principles of fire extinguisher use and the hazards involved with incipient stage fire fighting?
- Have employees been trained (who have been designated to use fire fighting equipment) in the use of the equipment?
Fire alarm
- Have you established an employee alarm system that complies with 1910.165?
- If the employee alarm system is used for alerting fire brigade members, or for other purposes, is a distinctive signal used for each purpose?
- Are all employee alarm systems in proper working condition, except when undergoing repairs or maintenance?
Fire detection systems
- Are all devices approved for use?
- Are fire detection systems and components returned to normal operating condition as soon as possible after each use or test?
Fire brigades
- If you choose to form a fire brigade, are the requirements of 1910.156 met?
Sprinkler systems
- Are automatic sprinkler system water control valves, air and water pressure checked weekly/periodically as required?
- Are fire control sprinkler heads kept clean?
- Are sprinkler heads protected by metal guards when exposed to physical damage?
- Is proper clearance maintained below sprinkler heads?
Flammable liquids
OSHA’s Flammable Liquids regulation, 1910.106, applies to all persons who handle, use, store, or transport flammable liquids. A flammable liquid means any liquid having a flashpoint at or below 199.4°F (within that definition, there are four categories of flammable liquids).
Action steps
- Ensure flammable liquids are stored and handled properly.
- Familiarize yourself with the different categories of flammable liquids (this will determine storage and usage requirements).
- Ensure containers meet the design requirements in 1910.106.
- Provide adequate drainage, dikes, and walls for tanks.
- Take precautions to prevent ignition by eliminating or controlling sources of ignition.
- Ensure the design (including selection of materials) fabrication, assembly, test, and inspection of piping systems containing flammable liquids is suitable for the expected working pressures and structural stresses.
- Provide suitable emergency and fire protection.
- Ensure adequate ventilation.
- Install electrical wiring properly.
- Follow proper procedures for dispensing liquids.
Training action plan
Any employee involved in storage, transfer, use, or disposal of flammable liquids needs to be trained to handle them safely and to follow your company’s established procedure.
Generally, training content should cover:
- Categories of flammable liquids,
- Handling procedures,
- Storage procedures, and
- Spill cleanup.
In addition, if your company receives, stores, or handles flammable liquids in storage tanks in areas that have the potential to flood, you need to have employees trained on emergency response procedures.
A hands-on approach is appropriate in this part of the training session. In fact, you may want to demonstrate how to do specific procedures related to flammables at your facility. Then allow each employee to try the procedure, so they can perform them correctly and so they will remember them better.
Tips
- When transferring flammable liquids, always bond and ground the containers.
- If purchasing plastic containers of five gallons or less for use with flammable liquids, purchase those with a built-in metal grounding strip.
Checklist
Review these checklists to ensure flammable liquid safety at your facility.
Containers
- Are all connections on drums and piping, vapor and liquid tight?
- Are all flammable liquids kept in closed containers when not in use (e.g., parts cleaning tanks, pans, etc.)?
- Are approved containers and portable tanks used for the storage and handling of flammable liquids?
- Are bulk drums of flammable liquids grounded and bonded to containers during dispensing?
- Are flammable liquids, such as gasoline, kept in an approved safety can?
- Are portable storage tanks equipped with emergency venting that will relieve excessive internal pressure caused by fire exposure?
- Are safety cans used for dispensing flammable liquids at a point of use?
- Are storage cabinets used to hold flammable liquids, labeled “Flammable — Keep Fire Away”?
- Are storage tanks adequately vented to prevent the development of excessive vacuum or pressure as a result of filling, emptying, or atmosphere temperature changes?
Handling
- Are all containers over 30 gallons in inside storage rooms stacked individually?
- Are firm separators placed between containers of combustibles or flammables, when stacked one upon another, to assure their support and stability?
Storage
- Are “No Smoking” rules enforced in areas involving storage and use of hazardous materials?
- Are all solvent wastes, and flammable liquids kept in fire-resistant, covered containers until they are removed from the worksite?
- Are all spills of flammable liquids cleaned up promptly?
- Is proper storage of flammable materials practiced to minimize the risk of fire including spontaneous combustion?
- Is there one clear aisle at least 3 feet wide?
Ladders
OSHA’s ladder regulations, at 1910.23, apply to any general industry workplace that uses ladders to perform duties (other than construction work) at high elevations.
Action steps
- Use ladders that are designed and approved for the intended purpose.
- Ensure ladders meet OSHA specifications.
- Follow all ladder safety requirements.
- Train employees in safe ladder use.
- Maintain ladders in a safe condition.
- Inspect ladders as needed.
- Remove defective ladders from service.
Training action plan
Training content for ladders and stairways depends on the types of equipment and structures your facility has and what work will be performed. In general, workers need to be trained as follows:
Ladders
Content should include:
- Inspecting the ladder,
- Setting up the ladder,
- Safe ladder use,
- Ascending and descending the ladder,
- Maintaining three points of contact,
- Recognizing hazards,
- Carrying tools and equipment, and
- Using the right ladder for the job.
Tips
- Workers on ladders generally do not require fall protection.
- Be careful that painting ladders or applying stickers does not hide damage.
- Make sure the ladder is the best tool for the job.
- Ensure workers understand associated hazards (e.g., electrical, wind) that they may have to consider with selecting and/or using a ladder.
Checklist
Review these checklists to ensure ladder safety at your facility.
Design and construction
- If wood, is the portable ladder not coated with any material that may obscure structural defects?
- If metal, is the portable ladder made of corrosion-resistant material or protected against corrosion?
- If metal, are the rungs and steps of the portable ladder corrugated, knurled, dimpled, coated with skid-resistant material, or otherwise treated to minimize slipping?
- Are the rungs, steps, and cleats of the portable ladder spaced at least 10 inches and not more than 14 inches apart?
- Do the rungs, steps, and cleats of the portable ladder have a minimum clear width of 11.5 inches?
Stepladders
- Is the stepladder equipped with a metal spreader or locking device that securely holds the front and back sections in an open position while the ladder is in use?
Stepstools
- Are the steps on the stepstool spaced at least 8 inches and not more than 12 inches apart?
- Does the stepstool have a minimum clear width of 10.5 inches?
Inspection and maintenance
- Are portable ladders inspected regularly, and as necessary, to ensure they are in safe condition?
- Are deficiencies corrected or repaired before an employee uses the portable ladder again?
- If a portable ladder correction or repair cannot be made immediately, are employees prevented from using the portable ladder until repaired?
- If a portable ladder repair involves structural integrity, does a qualified person perform or supervise the correction or repair?
Training
- Is each employee who uses a portable ladder trained on how to properly use the ladder?
- Is each employee who uses a portable ladder trained to recognize the fall hazards in the work area?
- Is training conducted by a qualified person?
Note: Qualified, under this OSHA requirement, describes a person who, by possession of a recognized degree, certificate, or professional standing, or who by extensive knowledge, training, and experience has successfully demonstrated the ability to solve or resolve problems relating to the subject matter, the work, or the project. - Is information and training provided in a manner that each employee understands?
- Is retraining provided when deficiencies in performance or knowledge are noted, or there are changes in the workplace or equipment?
Personal protective equipment
OSHA’s Subpart I regulations apply to all persons involved in hazardous processes; environmental, chemical, radiological hazards; or mechanical irritants that are capable of causing injury or impairment of any body part through absorption, inhalation, or physical contact. The categories of personal protective equipment (PPE) include: eye and face equipment, head protection, hand protection, foot protection, fall protection, and respiratory protection (information about respiratory protection is provided in a separate topic area under Respiratory Protection, 1910.134).
Action steps
- Assess the workplace to determine what hazards are present that require PPE.
- Document and certify the PPE assessment.
- Provide appropriate and approved PPE based on the workplace hazards.
- Instruct employees in proper PPE usage.
- Ensure employees wear proper PPE.
- Establish inspection and maintenance procedures for PPE.
Training action plan
OSHA requires that you provide training to each employee who is required to use PPE. Each such employee shall be trained to know at least the following:
- When PPE is necessary.
- What PPE is necessary.
- How to properly don, doff, adjust, and wear PPE.
- The limitations of the PPE.
- The proper care, maintenance, useful life, and disposal of the PPE.
Each affected employee must also demonstrate an understanding of the training and the ability to use PPE properly, before being allowed to perform work requiring the use of PPE.
When you have reason to believe that any affected employee who has already been trained does not have the understanding and skill required, you must retrain each such employee. Circumstances where retraining is required include, but are not limited to, situations where:
- Changes in the workplace render previous training obsolete.
- Changes in the types of PPE to be used render previous training obsolete.
- Inadequacies in an employee’s knowledge or use of assigned PPE indicate that the employee has not retained the requisite understanding or skill.
Tips
- Make sure that protective eyewear does not affect the fit of respirators.
- Make sure that protective eyewear does not disturb the proper positioning of corrective lenses so as to inhibit or limit the employee’s vision.
- Ensure employees disinfect shared protective eyewear after each use.
- Always replace a hard hat if it sustains an impact, even if damage is not noticeable.
- Don’t let workers wear hard hats backward unless the hat has been tested and approved for such use.
Checklist
Review these checklists to ensure proper PPE usage at your facility.
General
- Are all employees required to use PPE as needed?
- Is PPE functional and in good repair?
- Is protective clothing and equipment provided and used when cleaning up spilled toxic or otherwise hazardous materials or liquids?
- Is PPE provided and are all employees required to use PPE as needed to protect against injury?
- Does PPE have ANSI or ASTM specifications marked on it?
Training
- Has each individual who is required to use PPE been provided with training?
- Have the trained individuals demonstrated an understanding of the training and the ability to use PPE properly before being allowed to perform work requiring the use of PPE?
- Are individuals retrained when there is reason to believe that they do not have the understanding or skill to use PPE properly?
Recordkeeping
- Have you documented that a hazard assessment has been done, when, and by whom?
- Have you documented that PPE training has been done, who has received it, and when?
Head, foot, and hand protection
- Are protective helmets used wherever there is the possible danger of head injury from impact, or from falling or flying objects, or from electrical shock and burns?
- Is protective footwear used wherever there is the danger of foot injuries due to falling or rolling objects, or objects piercing the sole, and where feet are exposed to electrical hazards?
- Are appropriate protective gloves used wherever there is the danger to hands of exposure to hazards such as those from skin absorption of harmful substances, severe cuts or lacerations, severe abrasions, punctures, chemical burns, thermal burns, and harmful temperature extremes?
Eye and face protection
- Are individuals issued and required to wear appropriate eye protective devices while participating or observing activities which present a potential eye safety hazard?
Personal fall protection
- Have all impacted individuals been trained to use personal fall protection equipment?
- Is the equipment inspected daily before use?
- Does fall protection meet the design requirements in 1910.140?
- Are ropes, belts, lanyards, lifelines, and harnesses used for personal fall protection compatible with connectors used?
Posting requirements
- Are all areas and equipment requiring the use of PPE devices posted with a sign indicating this requirement?
Process safety management
OSHA’s 1910.119 regulation applies to those companies that deal with any of more than 130 specific toxic and reactive chemicals in listed quantities (See 1910.119 Appendix A); it also includes any Category 1 flammable gas (as defined in 1910.1200(c)) or a flammable liquid with a flashpoint below 100°F (37.8°C) on site in one location, in a quantity of 10,000 pounds (4535.9 kg) or more (with a few exceptions, as outlined in 1910.119(a)(1)(ii)(A) and (B)).
Action steps
- Ensure employee participation in the process safety management program.
- Conduct adequate hazard analyses.Implement safety operating procedures.
- Conduct process safety training.
- Ensure process safety for contractors.
- Conduct pre-startup safety reviews.
- Ensure integrity of process equipment.
- Ensure management of change process and procedures are adequate.
- Investigate incidents per OSHA requirements.
- Ensure emergency planning and response efforts are adequate.
- Establish a process safety compliance audit process.
Training action plan
You must train each employee involved in operating a process and each employee before being involved in operating a newly assigned process. Training must include:
- An overview of the process and the operating procedures.
- Specific safety and health hazards.
- Emergency operations including shutdown.
- Safe work practices applicable to the employee’s job tasks.
Also, you must provide refresher training at least every three years, and more often if necessary, to each employee involved in operating a process to assure that the employee understands and adheres to the current operating procedures of the process. You, in consultation with the employees involved in operating the process, must determine the appropriate frequency of refresher training.
Documentation
You must prepare a record that contains the identity of the employee, the date of training, and the means used to verify that the employee understood the training.
Tips
- OSHA’s Process Safety Management (PSM) standard requires that mechanical integrity inspections have to be documented (including the name of the person performing the inspection or test) and list the information to be recorded.
- The PSM standard states that the employer must establish and implement written procedures.
- To comply with the PSM standard, employers must document that equipment complies with recognized and generally accepted good engineering practices. For existing equipment designed and constructed in accordance with codes, standards, or practices that are no longer in general use, the employer must determine and document that the equipment is designed, maintained, inspected, tested, and operated in a safe manner.
- All process hazard analyses must be updated and revalidated, based on their completion date, at least every five years.
- Employers must consult with employees and their representatives on the conduct and development of process hazard analyses and on the development of the other elements of process management, and they must provide to employees and their representatives access to process hazard analyses and to all other information required to be developed by the standard.
- Contract employees must be instructed on known potential fire, explosion, or toxic release hazards related to their job and the process, and in the applicable provisions of the emergency action plan.
Checklist
Review these process safety management checklists.
Process hazard analysis
- Has written process safety information been compiled before conducting any process hazard analysis (PHA)?
- Are the process hazard analyses performed by teams with expertise in engineering and process operations?
- Has a system been established to promptly address the team’s findings and recommendations?
- Are the PHA’s updated and revalidated to assure that the process hazard analysis is consistent with the current process?
Incident investigation
- Has each incident been investigated which resulted in, or could reasonably have resulted in, a catastrophic release of highly hazardous chemicals in the workplace?Has a system been established to promptly address and resolve the incident investigation report findings and recommendations?
Emergency action plan
- Has an emergency action plan been established and implemented for the entire plant in accordance with the requirements of 1910.38?
Written program
- Do you have an appropriate written program for PSM compliance?
- Do you have a written program regarding employee participation?
- Do written operating procedures exist for each covered process?
- Have safety and health considerations been included in the operating procedures?
Contractors
- Have safe work practices been developed and implemented for employees and contractors to control hazards?
- For employees and contractor employees involved in operating a process do initial and refresher training records exist?
- Has each employee and contractor employee been trained before being involved in a newly assigned process?
Pre-startup safety review
- Has a pre-startup safety review been performed for all new facilities and for modified facilities when the modification is significant enough to require a change in process safety information?
Mechanical integrity
- Are there written procedures to maintain the ongoing integrity of process equipment?
- Are appropriate inspections and tests performed on each item of process equipment included in the program?
- Have appropriate checks and inspections been made to assure equipment is installed properly and consistent with design specifications and manufacturer’s instructions?
Hot work permits
- Have hot work permits been issued for all hot work operations conducted on or near a process covered by the PSM standard?
Management of change
- Are there written procedures for managing changes (except for “replacements in kind”) to process chemicals, technology, equipment, and procedures and changes to facilities that affect a covered process?
Audits
- Do you conduct an audit of compliance with PSM at least every three years?
- Do you retain the two most recent compliance audit reports?
Training
- Have employees been trained properly regarding PSM?
- Are appropriate training records kept?
Signs and markings
OSHA’s 1910.144-.45 regulations provide specifications for signs and tags and are intended to cover all safety signs except those designed for streets, highways, railroads, and marine regulations. These specifications do not apply to plant bulletin boards or to safety posters.
Action steps
- Use appropriate colors for identification of equipment and hazards per OSHA regulations.
- Ensure emergency stop bars and buttons on hazardous machines are red.
- Ensure yellow is used for designating caution and for marking physical hazards such as: Striking against, stumbling, falling, tripping, and “caught in between.”
- Follow OSHA specifications for accident prevention signs and tags.
- Instruct employees in recognizing accident prevention signs and tags and the appropriate action to take regarding those markings.
- Ensure messages on signs and tags are clear and to the point.
Training action plan
Training on accident prevention signs and tags is required prior to or at the time of initial assignment to areas where accident prevention signs and tags are used. Training content should generally include:
- Sign color,
- Symbols,
- Labeling, and
- Company-specific marking systems.
Consider other safety training issues relative to safety signs such as hazard communication and the specific posting requirements of the chemical-specific standards found in Subpart Z of the 1910 regulations. Training might also cover the information found in the poster describing employee rights under OSHA (poster 2203) which must be displayed somewhere where workers will see it.
OSHA does not require training documentation for Specifications for Accident Prevention Signs and Tags, but it is always prudent to keep records anyway. Training records can tell you who was trained on what, when, and what was covered.
Tips
- The lines used to delineate the aisles may be any color so long as they clearly define the area considered as aisle space. The lines may be composed of dots, square, strip or continuous, but they too must define the aisle area.
- The recommended width of aisle markings varies from two inches to six inches; therefore, any width two inches or more is considered acceptable.
- Danger sign — The colors red, black, and white must be those of opaque glossy samples as specified in Table 1 of Fundamental Specification of Safety Colors for CIE Standard Source “C”, American National Standard Z53.1-1967.
- Caution sign — Standard color of the background must be yellow; and the panel, black with yellow letters. Any letters used against the yellow background must be black. The colors must be those of opaque glossy samples as specified in Table 1 of American National Standard Z53.1-1967.
- Safety instruction signs — Standard color of the background must be white; and the panel, green with white letters. Any letters used against the white background must be black. The colors must be those of opaque glossy samples as specified in Table 1 of American National Standard, Z53.1-1967.
Checklist
Review these checklists for signs and markings at your facility.
Hazardous substances
- Is every hazardous chemical in the workplace labeled with identification and hazard warnings?
- Are safety and other containers painted appropriately?
- Are equipment, containers, materials, or areas where biohazards are or could be present labeled with the biological hazard warning?
- Are any entrances to regulated areas where the 13 carcinogens listed at 1910.1003 are present marked with appropriate signage warning of the danger?
- Are signs posted warning of presence and hazards of asbestos where required?
Aisles
- Are permanent aisles and passageways appropriately marked?
Materials handling
- Are clearance signs warning of clearance limits provided?
- Are powered industrial trucks appropriately marked?
- Are cranes marked with the load rating on each side?
- Are crane pendant control boxes clearly marked for identification of functions?
Emergency
- Are exits marked by a readily visible sign?
- Are areas that could be mistaken for an exit identified by a sign reading “Not an Exit” or something similar?
- Are portable fire extinguishers mounted, located, and identified so they are readily accessible?
Ladders
- Are defective ladders withdrawn from service and tagged or marked as “Dangerous, Do Not Use”?
Lockout/tagout
- Do tagout devices warn against hazardous conditions if the machine or equipment is energized?
Confined spaces
- Are completed confined space permits posted at an appropriate location?
- Are signs posted at permit-required confined spaces describing the dangers present?
OSHA posters
- Is OSHA’s Form 2203 (or 3165) describing the OSH Act posted appropriately?
- Is the annual summary of OSHA No. 300 Form posted appropriately?
- Are citations received from OSHA posted at or near the place the violation(s) occurred?
Electrical
- Is the manufacturer’s description marked on all electrical equipment used?
- Are covers for pull and junction boxes permanently marked “HIGH VOLTAGE”?
Slips, trips, and falls
OSHA has various requirements to protect workers from slipping, tripping, or falling. These requirements are in Subpart D. Among other things, OSHA requires that all floors, platforms, runways, and wall and window openings where there is a drop of four feet or more have some type of guarding, or that workers utilize an appropriate personal fall arrest system.
Action steps
- Keep all places of employment, passageways, storerooms, and service rooms clean and orderly and in a sanitary condition.
- Ensure floors are maintained in a clean and, so far as possible, a dry condition.
- Maintain drainage where wet processes are used.
- Ensure every floor, working place, and passageway are kept free from protruding nails, splinters, holes, or loose boards.
- Provide sufficient safe clearances for aisles, at loading docks, through doorways and wherever mechanical handling equipment turns or passage must be made.
- Ensure permanent aisles and passageways are appropriately marked.
- Provide covers and/or guardrails to protect personnel from the hazards of open pits, tanks, vats, ditches, etc.
- Ensure ladders are maintained and used properly.
- Follow proper safety procedures for scaffold setup and use.
- Ensure all walking-working surfaces are maintained safely.
Training action plan
Before any employee is exposed to a fall hazard, OSHA requires that the employer must provide training for each employee who uses personal fall protection systems, as well as employees using certain equipment such as ladders, rope descent systems, and dockboards.
The employer must ensure that each employee is trained by a qualified person.
Training for impacted employees must cover pertinent topics, including:
- How to use, inspect, maintain, and disassemble a personal fall protection system,
- How to properly place dockboards, and
- Designated area set-up.
OSHA requires employees be retrained when there is reason to believe the employee does not have the understanding and skill required to work safely. Situations requiring retraining include, but are not limited to, the following:
- When changes in the workplace render previous training obsolete or inadequate;
- When changes in the types of fall protection systems or equipment to be used render previous training obsolete or inadequate; or
- When inadequacies in an affected employee’s knowledge or use of fall protection systems or equipment indicate that the employee no longer has the requisite understanding or skill necessary to use equipment or perform the job safely.
Training must be provided in a manner that the employee understands.
All employees should be aware of how to prevent slips, trips, and falls by following good housekeeping procedures and when they work on or around:
- Scaffolds,
- Ladders,
- Unprotected ledges or platforms,
- Rooftops,
- Open shafts,
- Trapdoors,
- Poles,
- Towers,
- Bridges,
- Trestles,
- Pits, and
- Open tanks.
Training content should generally focus on:
- Various “fall factors” present in your facility.
- What happens when you slip, trip, and fall.
- How to prevent injuries from slips, trips, and falls, including the use of appropriate footwear.
- Hazards of stairs.
- Fall prevention methods when using ladders and scaffolds.
Tips
- Assign responsibilities for ensuring areas are kept clean and orderly.
- Keep an eye out for uneven floors, labels and cords, wet processes, and low-light areas.
Checklist
Review these checklists to reduce slips, trips, and falls at your facility.
Walkways
- Are aisles and passageways kept clear?
- Are aisles and walkways marked as appropriate?
- Are wet surfaces covered with non-slip materials?
- Are holes in the floor, sidewalk, or other walking surface repaired properly, covered, or otherwise made safe?
- Is there safe clearance for walking in aisles where motorized or mechanical handling equipment is operating?
- Are materials or equipment stored in such a way that sharp projectiles will not interfere with the walkway?
- Are spilled materials cleaned up immediately?
- Are changes of direction or elevations readily identifiable?
- Are aisles or walkways that pass near moving or operating machinery, welding operations or similar operations arranged so employees will not be subjected to potential hazards?
- Are standard guardrails provided wherever aisle or walkway surfaces are elevated more than 30 inches (76.20 centimeters) above any adjacent floor or the ground?
Floor and wall openings
- Are floor openings guarded by a cover, a guardrail, or equivalent on all sides (except at entrance to stairways or ladders)?
- Are toeboards installed around the edges of permanent floor opening (where persons may pass below the opening)?
Dockboards
- Are all dockboards used capable of supporting the maximum intended load?
- Do dockboards that are put into initial service on or after January 17, 2017, have means (such as run-off guards or curbs) to prevent vehicles from running off the edge (unless it can be demonstrated there is no run-off hazard))?
- Are portable dockboards equipped with handholds or other means to permit safe handling?
- Are portable dockboards secured by anchoring in place or using equipment or devices that prevent the dockboard from moving out of a safe position?
- When securing the dockboard is not feasible, is there sufficient contact between the dockboard and the surface to prevent the dockboard from moving out of a safe position?
- Are measures, such as wheel chocks or sand shoes, used to prevent transport vehicles (e.g. a truck, semitrailer, trailer, or rail car) from moving while employees are on the dockboard?
- Is each employee on a dockboard protected from falling 4 feet or more to a lower level by a guardrail system or handrails?
Note: This does not apply when dockboards are being used solely for materials-handling with motorized equipment, the fall hazard is 10 feet or less, and the employees have been properly trained. - Are dockboards inspected regularly, and as necessary, to ensure they are in safe condition?
- Is each employee who uses a dockboard trained to properly place and secure the equipment?
Stairs and stairways
- Are standard stair rails or handrails on all stairways having four or more risers?
- Are all stairways at least 22 inches (55.88 centimeters) wide?
- Are step risers on stairs uniform from top to bottom?
- Are steps on stairs and stairways designed or provided with a surface that renders them slip resistant?
- Are stairway landings adequate?
Inspection and maintenance
- Are aisles and walkways inspected regularly, and as necessary, to ensure they are in safe condition?
- Are deficiencies corrected or repaired before an employee uses an aisle or walkway again?
- If an aisle or walkway correction or repair cannot be made immediately, are employees prevented from using the aisles or walkway until repaired?
- If an aisle or walkway repair involves structural integrity, does a qualified person perform or supervise the correction or repair?
Training
- Are employees trained in measures to protect themselves from slips, trips, and falls?
- Are employees trained to use any fall protection they may need?
- Is training provided in a manner the employees will understand?
Solvents
Solvents are commonly used both in the workplace and at home. They are safe to use when you understand their hazards and know how to protect yourself. Solvents can:
- Cause dizziness, nausea, and depress the central nervous system;
- Cause chronic illnesses such as cancer, liver disease, and nervous system disorders;
- Be toxic; and
- Be flammable.
One thing all solvents have in common is that they are used to dissolve another substance. They can be used as cleaners, degreasers, or as ingredients in paints, coatings, or adhesives. Some examples of common solvents include acetone, alcohol, mineral spirits, and perchloroethylene.
Action steps
- Assess the workplace to determine if solvents are being used, where, and in what processes/procedures.
- Ensure that there is an SDS for each hazardous solvent used in your facility.
- Properly store solvents.
- Ensure that waste and solvent by-products are properly contained and disposed.
- Determine which employees have on-the-job exposure.
- Provide appropriate protective equipment.
- Train affected employees to properly wear the PPE.
- Train affected employees about solvent hazards according to the requirements of the Hazard Communication standard at 1910.1200.
Note: OSHA regulations do not deal with specific solvents; however, some exceptions apply, depending on the chemical used, the potential for exposure, and the degree of exposure.
For more information, see the following regulations:
- Benzene, 1910.1028.
- Spray finishing, 1910.107.
- Dip tanks, 1910.122 through 1910.126.
- Solvents used in a process, 1910.119.
- Flammable liquids, 1910.106 (includes storage and handling requirements).
- HAZWOPER, 1910.120 (responding to spills and leaks).
Training action plan
Under the requirements of OSHA’s hazard communication standard, affected employees have to be given information and training on the hazards of the solvents they are exposed to at the time of their initial assignment, and whenever a new hazard is introduced into their work area.
Hazard communication
Hazard communication training has to include:
- Understanding the requirements of the OSHA hazard communication standard.
- Understanding the various components of your company’s hazard communication program.
- Knowing where the information is located in the company and how to access it.
- Knowing which operations and processes are using hazardous chemicals.
- Ability to read and understand the information on SDSs and labels.
- Knowing how to follow safe work practices and use PPE.
Solvents
Training content for an effective solvent training program should include:
- Identification of common solvents used in the workplace,
- How to recognize solvents,
- The chemistry of solvents,
- Physical and health hazards,
- Engineering controls used to reduce exposures,
- Use of protective equipment,
- Safe work procedures,
- Storage procedures,
- Clean-up and disposal procedures, and
- First aid and emergency procedures.
Tips
- Solvents are used to dissolve another substance. In general, “like dissolves like,” so the chemical composition of the solvent needs to have something in common with the chemical composition of the substance it can dissolve.
- Many solvents are combustible or flammable liquids. This means that they can easily ignite and burn. Acetone and methanol are examples of flammable solvents. Many types of petroleum distillates have a higher flash point and are considered combustible liquids.
- When engineering controls cannot completely eliminate the risk of exposure to solvents, affected employees will need to wear PPE. Chemical splash goggles, face shields, gloves, coveralls, aprons, shoe covers, and respirators are all examples of protective equipment. Refer to the product’s safety data sheet for PPE recommendations.
- Use only the amount of solvent needed for the job. This will minimize exposure and the quantity of waste solvent to be disposed.
- Store solvents in their original containers and be sure all containers in storage are clearly labeled.
Checklist
Review this solvent checklist to ensure safety and compliance at your facility.
- Have all solvents in the workplace been identified and documented?
- Are engineering controls in place to reduce exposures?
- Are hazardous solvents replaced with non-toxic solvents where possible?
- Are job activities controlled to prevent airborne solvent vapors from being generated and released into workers’ breathing area?
- Are workers free from medical complaints or symptoms that could be associated with solvent use?
- In areas where individual exposures are suspected to be above acceptable limits, has air monitoring been performed?
- Are affected persons provided with written copies of air monitoring results?
- Are workers who are exposed to solvent vapors above the permissible exposure limits provided with appropriate personal protective equipment (such as respirators) on an interim basis until engineering or administrative controls reduce exposures below permissible exposure limits?
- Are appropriate personal hygiene practices enforced such as washing hands?
- Is appropriate personal protective equipment (PPE) provided such as gloves, aprons, and goggles to protect against exposure?
- Have workers been trained regarding the hazards of solvents to which they might be exposed?
- Are first aid procedures in place for overexposures?
- Are there emergency procedures in case of a spill or leak?
Standard stairways
Stairways are a common fixture in many workplaces. However, they can pose hazards to workers if not constructed and maintained properly.
Action steps
- Ensure stairs meet OSHA’s specifications (strength, width, rise, etc.). See 29 CFR 1910.25 and 29 CFR 1910.28.
- Equip all stairways that are four feet or more above a lower surface with stair rail systems and guardrails.
- Ensure stairs have uniform riser heights and tread depths between landings.
- Provide proper landing platforms.Inspect all stairways regularly and as necessary.
- Maintain stairways in a safe condition.
Training action plan
Before any employee is exposed to a fall hazard, OSHA requires that the employer must provide training for that employee. In terms of stairs, items to keep in mind include:
- Caution employees not to carry large or bulky objects while climbing or descending stairs.
- Encourage employees to use railings.
- Remind employees not to jump from stairs, or skip steps.
Training must be provided in a manner that the employee understands.
Tips
- Provide stairs with good lighting and tread.
- Provide signage to remind employees of safe stair practices.
- Ensure the change in surface from stairs to platforms does not create a hazard.
- Keep stairs dry.
- Periodically inspect stairways for damage.
Checklist
Review the following standard stairway checklists.
General
- Are standard stairs provided for access from one walking-working surface to another when operations necessitate regular and routine travel between levels?
Condition
- Are stairs in good repair (e.g., loose handrails, corrosion)?
- Are stairs free of hazards (e.g., protruding objects, leaks, spills, snow and ice)?
- Are all steps reasonably slip-resistant?
Design and construction
- Are stairs at least 22 inches wide between vertical barriers?
- Are handrails, stair rail systems, or guardrails provided as necessary?
- Do stairways have at least a 6 feet, 8 inches vertical clearance from any tread to any overhead clearance measured from the leading edge of the tread?
- Can stairs support a load of five times the normal anticipated live load, but not less than 1,000 pounds?
Steps
- Do stairs have uniform riser heights and tread depths?
- Do the stairs have an angle between 30 and 50 degrees from the horizontal?
- Do stairs meet the rise and tread dimensions specified in Table D-1 of 1910.25(c) that achieve an angle between 30 and 50 degrees from the horizontal if installed before January 17, 2017?
- Do stairs have a maximum riser height of 9.5 inches if installed after January 17, 2017?
- Do stairs have a minimum tread depth of 9.5 inches if installed after January 17, 2017?
Fall protection
- Is a stair rail system and handrail(s) present on flights of stairs having at least 3 treads and at least 4 risers?
- Is at least one handrail present if the stairway is enclosed on both sides and is less than 44 inches wide?
- Are handrails present on both sides if the stairway is enclosed on both sides and is more than 44 inches wide but less than 88 inches wide?
- Are handrails present on each side and in the middle of the stair if it is enclosed on both sides and is more than 88 inches wide?
- Is a stair rail system with a handrail present on the open side of the stairway if it is less than 44 inches wide?
- Is a stair rail system with a handrail present on the open side of the stairway and a handrail on the enclosed side if it is more than 44 inches wide but less than 88 inches wide?
- Is a stair rail system with a handrail present on the open side, one handrail on the enclosed side, and one intermediate handrail located in the middle of the stair if it is greater than 88 inches wide?
- Is a stair rail system with a handrail present on each open side of the stairway if it is less than 44 inches wide?
- Is a stair rail system with a handrail present on the each open side of the stairway if it is more than 44 inches wide but less than 88 inches wide?
- Is a stair rail system with a handrail present on each open side and one intermediate handrail located in the middle of the stair if it is greater than 88 inches wide?
- Is a handrail on at least one side with earth built up on both sides present on exterior stairs less than 44 inches wide?
Handrails
- Is the height of handrails 30-38 inches measured from the leading edge of the stair tread to the top surface of the handrail?
- Is the clearance between handrails and any other object at least 2.25 inches?
- Are handrails smooth-surfaced?
- Do handrails have the shape and dimension necessary so that employees can grasp the handrail firmly?
- Do the ends of handrails not present projection hazards?
- Are handrails capable of withstanding, without failure, a force of at least 200 pounds applied in any downward or outward direction within 2 inches of any point along the top edge of the rail?
Stair rail systems
- Is the height of stair rail systems not less than 30 inches from the leading edge of the stair tread to the top surface of the top rail if installed before January 17, 2017?
- Is the height of stair rail systems not less than 42 inches from the leading edge of the stair tread to the top surface of the top rail if installed on or after January 17, 2017?
- Do the opening in stair rail systems not exceed 19 inches at its least dimension?
- If used as a handrail on stairs installed before January 17, 2017, is the height of stair rail systems 36-38 inches measured at the leading edge of the stair tread to the top surface of the top rail?
- If used as handrails, is the clearance between the stair rail systems and any other object at least 2.25 inches?
- Are stair rail systems smooth-surfaced?
- If used as a handrail, do stair rail systems have the shape and dimension necessary so that employees can grasp it firmly?
- Do the ends of stair rail systems not present projection hazards?
- Are stair rail systems capable of withstanding, without failure, a force of at least 200 pounds applied in any downward or outward direction within 2 inches of any point along the top edge of the rail?
Landings and platforms
- Is a platform provided when a door or gate opens directly onto a stairway?
- Is a guardrail or stair rail system provided if the landing is 4 feet or more above the lower level?
- Does the swing of the door or gate not reduce the platform’s usable depth to less than 20 inches if installed before January 17, 2017?
- Does the swing of the door or gate not reduce the platform’s usable depth to less than 22 inches if installed on or after January 17, 2017?
- Is the stairway landing or platform at least as wide as the stairway?
- Is the stairway landing or platform at least 30 inches in depth measured in the direction of travel?
Inspection and maintenance
- Are stairways inspected regularly, and as necessary, to ensure they are in safe condition?
- Are deficiencies corrected or repaired before an employee uses a stairway again?
- If a stairway correction or repair cannot be made immediately, are employees prevented from using the stairway until repaired?
- If a stairway repair involves structural integrity, does a qualified person perform or supervise the correction or repair?
Storage racks
Storage racks are a common fixture in many industrial workplaces, from warehouses to manufacturing facilities to retail to automotive repair shops. Common though they may be, these facilities can pose significant hazards if not installed, used, and maintained properly. Although OSHA does not have a specific standard addressing storage racks, the Agency expects employers to provide safe racking and has cited employers under the General Duty Clause of the OSH Act when racking posed serious hazards to workers.
Action steps
- Ensure all racks meet appropriate industry standards (e.g., ANSI/RMI MH 16.1).
- Install, use, and maintain racks per the manufacturer’s instructions.
- Check that load ratings are present.
- Ensure racks are anchored properly.
- Train workers on racking safety, including capacities and storage techniques.
- Install racks in accordance with local fire and building codes.
- Install bumper guards to prevent rack damage.
- Ensure repairs are made by qualified personnel.
- Replace damaged racks immediately or remove them from service.
Training action plan
- Explain the types of racking in your facility.
- Demonstrate proper stacking technique, including height restrictions.
- Ensure only trained material handling personnel place items on racking with powered equipment.
- Remind workers not to climb on racking (in rare cases where this may be needed, ensure the use of proper fall protection).
- Train workers how to read racking capacity plates.
- Instruct workers on how to report damaged racking.
Tips
- Assign responsibility for inspecting racks.
- Ensure racking repairs are made properly according to manufacturer’s instructions, and by qualified personnel, particularly where welding is performed.
- Maintain at least 18 inches clearance from sprinklers. (Local fire codes may have additional requirements for sprinklers and racking.)
- Conduct thorough root-cause analysis for racking damage.
Checklist
Review these storage rack checklists.
Design
- Have industrial steel storage racks been designed in accordance with American National Standards Institute (ANSI)/Rack Manufacturers Institute, Inc. (RMI) standard MH 16.1 specifications?
- Are modifications or rearrangements not within the original design not present? ANSI/RMI
- Are load application and rack configuration drawings available for each rack installation? ANSI/RMI
Installation
- Are racks installed on flooring (i.e., concrete) that will support the associated loads?
- ANSI/RMIIs flooring in good repair under and around racks?
- Are shims made of materials that meet or exceed the design bearing strength or allowable bearing strength of the floor? ANSI/RMI
- Is shim size and location under the base plates equal to or greater than the required base plate size and location? ANSI/RMI
- Does the total thickness of shims not exceed six times the diameter of the largest anchor bolt used in that base? ANSI/RMI
- Are shims interlocked or welded together if the total thickness is less than or equal to six times the anchor bolt diameter under bases with less than two anchor bolts? ANSI/RMI
Placarding
- Do storage racks display a permanent plaque that indicates load capacity? ANSI/RMI & General Duty Clause
- Is the plaque conspicuously located? ANSI/RMI
- Is the plaque at least 50 square inches? ANSI/RMI
- Does the plaque show clear, legible print? ANSI/RMI
- Does the plaque display the maximum permissible unit load and/or maximum uniformly distributed load per level? ANSI/RMI
- Does the plaque display the average unit load? ANSI/RMI
- Does the plaque display the maximum total load per bay? ANSI/RMI
- Are storage levels having multiple stacking of unit loads identified? ANSI/RMI
Anchoring
- Are rack columns anchored to the floor? ANSI/RMI & General Duty Clause
- Are an appropriate number of anchors, as recommended by the rack manufacturer, used? ANSI/RMI
- Are the anchors used the correct size as recommended by the rack manufacturer? ANSI/RMI
- Are an appropriate number of anchor bolts, as recommended by the rack manufacturer, used? ANSI/RMI
- Are the anchor bolts used the correct size as recommended by the rack manufacturer? ANSI/RMI
- Is decking fastened to the beams to prevent deck dropping? ANSI/RMI
Condition
- Are racks inspected and maintained per the manufacturer’s guidelines?
- Are racks plumb from top to bottom? ANSI/RMI
- Are rack columns straight? ANSI/RMI
- Are rack columns in good repair? ANSI/RMI
- Has frame bracing been installed as recommended by the manufacturer? ANSI/RMI
- Is frame bracing in good repair? ANSI/RMI
- Are anchors in good repair? ANSI/RMI
- Are column base plates in good repair? ANSI/RMI
- Are deflectors, fenders, and bumpers protecting the column as necessary? ANSI/RMI
- Is decking in good repair? ANSI/RMI
- Are other rack components (e.g., deflector angles, backer posts, etc.) in good repair? ANSI/RMI
Loads
- Is the weight of materials stored on storage racks below the load capacity rating? ANSI/RMI
- Are the heaviest products stored on the floor or lower levels and toward the middle of the rack system? ANSI/RMI
- Are pallets in good repair? ANSI/RMI
- Are pallets placed onto pallet load support members in a properly stacked and stable position? ANSI/RMI
- Are boxes, pallets, bags, containers, and other materials stacked/piled neatly? ANSI/RMI & 1910.176(b)
- Are stacks secure against sliding or collapse? 1910.176(b)
- Are stacks limited in height? 1910.176(b)
Fire protection and prevention
- Are racks, and materials stored on them, in accordance with local fire codes?
- Are materials on racks stored no closer than 18 inches away from sprinklers? 1910.159(c)(10)
Recordkeeping
- Has one copy of load application and rack configuration drawings of storage racks used been retained? ANSI/RMI
- Has one copy of load application and rack configuration drawings of storage racks used been retained by the dealer or manufacturer? ANSI/RMI
Welding
OSHA’s Subpart O regulations apply to all welders and welding operators who operate electric or gas welding and cutting equipment. The standards apply whether you have a single portable welding unit to do an occasional spot welding task, or if you have large electric welders to use in daily production.
Action steps
- Follow safety precautions for fire prevention and protection.
- Maintain suitable fire extinguishers.
- Provide a fire watch where required.
- Ensure areas are inspected and a permit issued before welding is allowed.
- Follow proper welding procedures.
- Provide PPE as needed.
- Ensure safety when working in confined spaces.
- Handle welding materials and equipment properly.
- Ensure proper marking of welding materials and equipment.
- Provide suitable ventilation.
- Maintain welding equipment.
Training action plan
Cutters, welders, and their supervisors are required to be trained in the safe operation of welding equipment. Also, fire watchers shall be trained in the use of fire extinguishing equipment. Training content should generally cover:
- Welding safety program guidelines established at your company,
- Welding hazards,
- Safe work practices,
- Fire watches,
- Welding safety when working in confined spaces, and
- Housekeeping.
Consider other safety training issues relative to your welding operations:
- Hazard communication for all hazardous substances generated during welding (e.g., certain gases, fluxes, wires, and rods contain cadmium, fluorides, zinc, beryllium, and so on, and require various protections).
- Spill cleanup procedures under HAZWOPER for leaky oxy fuel type cylinders or for situations with explosion or fire potential.
- Personal protective equipment, especially where respirators are required and eye shades are needed for arc welding operations.
- Employees must be informed of the status of their exposure records each year.
- Construction regulation requirements where welding operations involve new structures or modification of existing structures.
- Electrical codes for exposed live parts.
Training is required prior to or at the time of initial assignment.
Documentation
OSHA does not require training documentation for safety training on welding, but it is always prudent to keep records anyway. Training records can tell you who was trained on what, when, and who conducted the training.
Tips
- Adverse effects of overexposure to welding fumes can be acute or may occur only after repeated exposures.
- The hazards presented by welding fumes will vary based upon: the base material, the filler material, the gases being used, current level, arc length, and other factors.
- Welding fumes can cause nausea, headaches, dizziness, and metal fume fever.
Checklists
Follow these checklists to ensure welding safety at your facility.
General
- Are only authorized and trained personnel permitted to use welding, cutting, or brazing equipment?
- Are pressure-reducing regulators used only for the gas and pressures for which they are intended?
- Does each operator have a copy of the appropriate operating instructions and are they directed to follow them?
- Is a check made for adequate ventilation in and where welding or cutting is performed?
- Is red used to identify acetylene (and other fuel-gas) hose, green for oxygen hose, and black for inert gas and air hose?
- When working in confined places, are environmental monitoring tests taken and means provided for quick removal of welders in case of an emergency?
- Are compressed gases used and handled properly?
Welding: Equipment
- Are only approved apparatus (torches, regulators, pressure-reducing valves, acetylene generators, manifolds) used?
- Is grounding of the welding machine frame and safety ground connections of portable machines checked periodically?
- Is necessary personal protective equipment available?
- Is open circuit (No Load) voltage of arc welding and cutting machines as low as possible and not in excess of the recommended limits?
Welding: Fire prevention
- Are compressed gas cylinders kept away from sources of heat?
- Are fire watchers assigned when welding or cutting is performed in locations where a serious fire might develop?
- Are precautions taken to prevent the mixture of air or oxygen with flammable gases, except at a burner or in a standard torch?
- Are provisions made for personnel to perform fire watch duties under appropriate circumstances?
- Are provisions made to never crack a fuel-gas cylinder valve near sources of ignition?
- Are signs reading “DANGER NO SMOKING, MATCHES, OR OPEN LIGHTS” or the equivalent, posted in welding areas?
- Before hot work is begun, are used drums, barrels, tanks, and other containers so thoroughly cleaned that no substances remain that could explode, ignite, or produce toxic vapors?
- If welding gases are stored, are oxygen and acetylene separated by a 5-foot noncombustible barrier?
- Is combustible scrap, debris, and waste stored safely and removed from the work site promptly?
- When welding is done on metal walls, are precautions taken to protect combustibles on the other side?
Combustible dust
Combustible dusts are fine particles that present an explosion hazard when suspended in air in certain conditions. A dust explosion can be catastrophic and cause employee deaths, injuries, and destruction of entire buildings. In many combustible dust accidents, employers and employees were unaware that a hazard even existed. It is important that employers determine if their operations have this hazard, and if so, that they take action now to prevent tragic consequences.
A wide range of industries possess combustible dust hazards and a wide variety of materials cause combustible dust incidents. (Combustible dusts can be intentionally manufactured powders, such as corn starch or aluminum powder coatings, or may be generated by handling and processing solid combustible materials such as wood and plastic pellets. For example, polishing, grinding, transporting, and shaping many of these materials can produce very small particles.)
Action steps
The following are general action steps that should be taken to identify and control dust hazards. For detailed guidance specific to your operations, consult with a qualified professional, as well as industry standards, as applicable (for example, those published by the National Fire Protection Association).
- Assess your facility for processes that generate dust. Have dusts analyzed for combustibility hazards. (There are several factors that determine how explosive a dust can be, as well as some key measurements for determining dust explosibility. These include particle size, moisture content, ambient humidity, oxygen available for combustion, the shape of the dust particle, and the concentration of dust in the air, i.e., minimum explosive concentration or MEC.)
- Understand the five elements needed for a combustible dust explosion: Combustible dust (fuel); ignition source (heat); oxygen in air (oxidizer); dispersion of dust particles in sufficient quantity and concentration; and confinement of the dust cloud.
- Understand that there can be a primary explosion or event that shakes loose hidden dust (for example, from piping or rafters) which can cause a devastating secondary explosion.
- Ensure operations have proper engineering design and controls and inspect/maintain those controls. Seek outside assistance/expertise as needed to ensure proper dust control procedures/methods are in place.
- Develop an ignition control program, limiting and controlling potential ignition sources in dust accumulation areas.
- Train employees on the explosion hazards of combustible dusts.
- Implement a housekeeping program with regular cleaning frequencies for floors and horizontal surfaces, such as ducts, pipes, hoods, ledges, and beams, to minimize dust accumulations within operating areas of the facility. (Even seemingly small amounts of accumulated dust can cause catastrophic damage. The CSB estimated, for example, that the explosion that devastated a pharmaceutical plant in 2003 and killed six employees was caused by dust accumulations mainly under 0.25 inches deep. The CSB study references National Fire Protection Administration (NFPA) warnings that a catastrophic explosion can occur from as little as 1/32 of an inch of accumulated dust — around the thickness of a dime — covering just 5 percent of a room’s surface.)
- Ensure working surfaces are designed in a manner to minimize dust accumulation and facilitate cleaning.
- Ensure electrical equipment and electrically-powered cleaning devices such as vacuum cleaners are approved for the hazard classification for Class II locations.
- Select and use industrial trucks that are approved for the combustible dust locations.
- Prohibit the use of cleaning methods that can disperse combustible dust into the air (i.e., compressed air and dry sweeping).
- Ensure the ready availability of SDSs for the chemicals which could become combustible dust under normal operations. Note: The Chemical Safety Board has found that many SDSs do not provide sufficient data on combustible dust hazards. However, OSHA revised the HazCom rule in 2012. In the revised rule, combustible dust hazards must be addressed on labels and SDSs. Label elements are provided for combustible dust in the final HCS and include the signal word “warning” and the hazard statement “May form combustible dust concentrations in the air.”
- Implement an emergency action plan and maintain exit routes properly.
For chemicals in a solid form that do not present a combustible dust hazard, but may form combustible dusts while being processed in normal downstream uses, OSHA allows the chemical manufacturer some flexibility in labeling requirements. The manufacturer or importer may transmit the label to the customer at the time of the initial shipment, but the label does not need to be included with subsequent shipments unless it changes. This provides the needed information to the downstream users on the potential hazards in the workplace, while acknowledging that the solid metal or other materials do not present the same hazards that are produced when these materials are processed under normal conditions of use.
Training action plan
Workers are the first line of defense in preventing and mitigating fires and explosions. If the people closest to the source of the hazard are trained to recognize and prevent hazards associated with combustible dust in the plant, they can be instrumental in recognizing unsafe conditions, taking preventative action, and/or alerting management. While OSHA standards require training for certain employees, all employees should be trained in safe work practices applicable to their job tasks, as well as on the overall plant programs for dust control and ignition source control. They should be trained before they start work, periodically to refresh their knowledge, when reassigned, and when hazards or processes change.
- Define combustible dusts.
Combustible dusts are fine particles,
fibers, chips, chunks, or flakes
that could be an explosion hazard
when they’re suspended in air
under certain conditions.
Many products can be fuel for a
dust explosion when they’re used in powdered form. Here are some
examples:
- Flour, sugar, powdered milk, or other food-related products;
- Wood;
- Paper;
- Textiles;
- Charcoal and other carbon-rich materials;
- Sulfur and other chemicals;
- Aluminum, zinc, and other metals; and
- Epoxy resin and other plastics.
- Introduce the hazards.
A dust explosion can cause deaths
and serious injuries. An explosion
can destroy an entire building. In
many combustible dust incidents,
employers and employees didn’t
know that a hazard even existed.
Here’s an example of what happens
during a combustible dust explosion.
- In February 1999, a deadly fire and explosion occurred in a foundry in Massachusetts. An investigation found that a fire started in a molding machine and then spread to ventilation ducts. The small initial explosion in the ductwork disturbed resin dust that had settled on the outside of the ducts, creating a dust cloud. This dust provided fuel for a secondary explosion that was powerful enough to lift the roof and cause walls to collapse.
- Identify the types of industries that may be at risk. Combustible dust explosion hazards can exist in a variety of industries, including: agriculture, chemicals, food, grain, fertilizer, tobacco, plastics, wood, paper, tire and rubber, furniture, textiles, pesticides, pharmaceuticals, coal, metal processing, recycling operations, and others.
- Explain how dust explosions can happen. The familiar fire triangle is made up of: oxygen, an ignition source (heat), and fuel. All three conditions must be present for a fire to start. Because oxygen is normally always present in the air, fires are usually prevented by keeping the fuel separate from the ignition source. In addition to the fire triangle elements, the “dust explosion pentagon” adds two more conditions: dust particles and the confinement of the dust cloud. Similar to the fire triangle, if one part of the pentagon is missing, a combustible dust explosion can’t occur. If a dust cloud is ignited in an enclosed area such as a room, vessel, ductwork, or process equipment, it burns very fast and may explode. Even if the initial explosion is small, it could shake up accumulated dust in the area to form another dust cloud. Often these secondary explosions are far more destructive.
- Outline how to look for combustible
dust hazards.
To identify the factors that could
contribute to an explosion, employers
should evaluate the hazards of
all: materials, operations, spaces (including hidden ones),
and potential ignition sources. Some likely areas where dust can
build up include:
- Parts of the building’s structure,
- Conduit and pipe racks,
- Electrical cable trays,
- Floors,
- Areas above suspended ceilings, and
- On and around equipment (including leaks around dust collectors and ductwork).
- Discuss what can be done to
control dust build-up.
If the dust isn’t building up, it lowers the risk of a dust explosion. There
are many ways to keep dust under
control. Some of these methods are
to:
- Conduct regularly scheduled inspections,
- Clean up dust on a regular basis,
- Use proper dust collection systems and filters,
- Keep dust from escaping from equipment or ventilation systems,
- Use surfaces that are easy to clean,
- Provide easy access to inspect and clean hidden areas where dust might build up,
- Use cleaning methods that don’t stir up dust clouds, and
- Use vacuum cleaners approved for dust collection.
- Describe methods to prevent
dust from igniting.
Keeping ignition sources under
control is an important part of any
fire safety program. Some actions
employers can take include the following:
- Use proper wiring methods;
- Make sure electrically powered equipment (including forklifts) is approved for the location;
- Control static electricity (bond equipment to ground);
- Keep smoking areas, open flames, sparks, and heated surfaces separate from dusts;
- Follow a hot work permit program; and
- Follow a preventive maintenance program.
- Discuss some methods to minimize
injuries and damage from
a combustible dust explosion.
Some of the steps employers can
take to minimize injuries and damage
from a combustible dust explosion
could include:
- Developing an emergency action plan,
- Maintaining emergency exit routes,
- Setting up operations in areas where the hazards are away from workers and equipment,
- Setting up isolation barriers around hazardous operations,
- Making sure dust handling equipment has pressure relief venting that’s directed away from workers and equipment, and
- Installing specialized spark detection and fire suppression systems in dust handling equipment.
Tips
The amount of dust accumulation necessary to cause an explosive concentration can vary greatly. This is because there are so many variables — the particle size of the dust, the method of dispersion, ventilation system modes, air currents, physical barriers, and the volume of the area in which the dust cloud exists or may exist. As a result, simple rules of thumb regarding accumulation (such as writing in the dust or visibility in a dust cloud) can be subjective and misleading. The hazard analysis should be tailored to the specific circumstances in each facility and the full range of variables affecting the hazard.
Many locations need to be considered in an assessment. One obvious place for a dust explosion to initiate is where dust is concentrated. In equipment such as dust collectors, a combustible mixture could be present whenever the equipment is operating.
Other locations to consider are those where dust can settle, both in occupied areas and in hidden concealed spaces. A thorough analysis will consider all possible scenarios in which dust can be disbursed, both in the normal process and potential failure modes.The facility analysis must identify areas requiring special electrical equipment classification due to the presence (or potential presence) of combustible dust. Various OSHA standards as well as industry (e.g., NFPA) can be consulted.
Checklist
Follow these checklists to prevent combustible dust hazards.
Hazard assessment
- Are there processes that accumulate dust? If so, have the dusts been analyzed for combustibility?
- Are periodic assessments conducted to determine dust explosion possibilities?
- Are employees and supervisors involved in identifying dust explosion hazards, for example through job hazard analyses?
- Is particular attention given during the hazard assessment to dust collection systems and areas not in plain view?
Prevention
- Have proper engineering design and controls been implemented for operations involving combustible dust; for example, dust control in process equipment and fugitive dust control; grounding and bonding; and separator devices?
- Is a comprehensive housekeeping program implemented?
- Are potential ignition sources limited and controlled in dust accumulation areas?
- Is it prohibited to use compressed air and similar cleaning methods that could disperse combustible dusts into the air?
- Are electrical services appropriate for Class II location? Consult applicable codes, for example the National Electrical Code.
- Are industry standards, such as NFPA 654, followed as applicable?
- Is a preventive maintenance program in place to minimize release of fugitive dust?
Note: Minor, but steady leaks, can cause large amounts of dust to accumulate.
Training
- Have employees received training on the hazards of dust?
- Have employees received training on specific characteristics of the dust that they work with?
- Have employees been trained to recognize potential ignition sources?
- Do employees know which processes/locations accumulate dust (for example, cable trays, pipe racks, floors, above ceilings, and structural members)?
- Are employees instructed to report plant fires and near misses?
Confined spaces
Employees in industry and construction are often asked to perform work in confined spaces, but many confined spaces contain serious hazards that endanger the employees who enter those spaces. For this reason, the Occupational Safety and Health Administration requires employers to implement certain procedures that protect workers from the hazards posed by confined spaces. These include procedures for identifying physical hazards and hazardous atmospheres in confined spaces, controlling and eliminating these hazards, and more.
Action steps
- Evaluate the workplace to determine if any spaces are permit-required confined spaces.
- Inform exposed employees, by posting danger signs or by any other equally effective means, of the existence and location of and the danger posed by the permit spaces.
- Decide whether employees will enter spaces. (If employees will not enter spaces, take appropriate, effective prevention measures.)
- Implement a written permit space program.
- Evaluate hazards of permit spaces.
- Provide employees with the opportunity to observe any monitoring or testing of permit spaces.
- Develop and implement the means, procedures, and practices necessary for safe permit space entry operations.
- Establish a permit system.
- Provide training.
- Perform entry according to OSHA requirements.
- Verify that conditions in the permit space are acceptable for entry throughout the duration of an authorized entry.
- Provide appropriate equipment (PPE, rescue equipment, testing, monitoring, ventilation, lighting, etc.)
- Provide at least one attendant outside the permit space into which entry is authorized for the duration of entry operations.
- Develop and implement rescue procedures.
- If contractors are involved in the confined space entry, follow pertinent OSHA requirements.
Training action plans
Training must be such that all employees whose work is regulated by OSHA’s confined spaces standard acquire the understanding, knowledge, and skills necessary for the safe performance of the duties assigned.
Training must be provided to each affected employee:
- Before the employee is first assigned duties relative to the confined space.
- Before there is a change in assigned duties.
- Whenever there is a change in permit space operations that presents a hazard about which an employee has not previously been trained.
- Whenever you have reason to believe either that there are deviations from the permit space entry procedures or that there are inadequacies in the employee’s knowledge or use of these procedures.
The training must establish employee proficiency in the duties required by the confined spaces standard and must introduce new or revised procedures, as necessary, for compliance.
Training should be specific to the employee’s function relative to the confined space. For instance, if the employee is an authorized entrant, then training should focus specifically on tasks and hazards he may face in this role.
In general, training should cover:
- Equipment to be used,
- Communicating with others involved in the work,
- Hazard awareness and recognition,
- Specific roles and duties,
- Monitoring,
- Medical and first aid, and
- Rescue.
Any work that involves contractors also requires special training and communication, both from the host to the contractor and from the contractor to the host.
Documentation
The employer must certify that required training has been accomplished. The certification must contain:
- Each employee’s name,
- The signatures or initials of the trainers, and
- The dates of training.
Tips
- A permit-required confined space is a confined space that has one or more of the following characteristics:
- Contains or has the potential to contain a hazardous atmosphere;
- Contains a material that has the potential for engulfing an entrant;
- Has an internal configuration such that an entrant could be trapped or asphyxiated by inwardly converging walls or by a floor which slopes downward and tapers to a smaller cross section; or
- Contains any other recognized serious safety or health hazard.
- When workers enter a permit space, at least one person must remain outside to monitor, summon help, or provide assistance.
- An attendant may attend to more than one permit space provided he/she can perform all required duties without compromising the safety of any entrant in all spaces being monitored (there is no proximity requirement).
- An employee can be both an entry supervisor and entrant as long as the employee has had the appropriate training and the duties of one activity do not conflict with the duties of the other.
- The entrants need to wear chest or full body harnesses with retrieval lines to make non-entry rescue attempts easier.
- The attendant needs to communicate with the entrants to monitor their conditions. If a situation arises that requires emergency rescue, the attendant should summon the rescue service and stay outside of the permit space entrance.
- An attendant can be a trained member of the rescue service, but cannot enter the permit space until the rest of the team has arrived to start proper rescue procedures.
Checklist
View these confined space checklists to ensure safety and compliance at your facility.
Monitoring
- When working in permit-required confined spaces, are environmental monitoring tests taken?
- Are authorized entrants or their representatives provided an opportunity to observe any monitoring or testing of permit spaces?
- Are permit spaces tested to determine if acceptable entry conditions exist prior to entry?
- Are permit spaces tested or monitored as necessary to determine if acceptable entry conditions are being maintained during the course of entry operations?
Equipment
- Is necessary personal protective equipment available?
- Is rescue and emergency services equipment available?
- Is communications equipment provided to allow the attendant to communicate with authorized entrants as necessary to monitor entrant status and to alert entrants of the need to evacuate the permit space?
General
- Are those having active roles in entry operations appropriately designated (for example, authorized entrants, attendants, entry supervisors, and persons who test or monitor the atmosphere in a confined space)?
- Is at least one attendant stationed outside the confined space for the duration of the entry operation?
- Are appropriate rescue personnel available?
- Are permit spaces flushed, ventilated, purged, and rendered inert to eliminate or control atmospheric hazards prior to entry?
Emergency action plans
This regulation applies to all companies that fall under a particular OSHA standard that requires an emergency action plan. However, it is wise for all employers to have action plans for any emergency that may be reasonably expected to occur in the workplace. Where required by OSHA, employers must develop a plan (called an emergency action plan or EAP) for emergency situations so that there is a literal “plan of action” for employees to take in the event of fires, toxic chemical releases, hurricanes, tornadoes, blizzards, floods, and other similar catastrophic events.
Action steps
Include the following minimum requirements in the EAP to ensure that it covers those designated actions employers and employees must take to ensure employee safety from fire and other emergencies.
- Establish emergency escape procedures and emergency escape route assignments.
- Develop procedures to be followed by employees who remain to operate critical plant operations before they evacuate.
- Establish procedures to account for all employees after emergency evacuation has been completed.
- Assign rescue and medical duties for those employees who are to perform them.
- List the preferred means of reporting fires and other emergencies.
- Develop a list of employee names or regular job titles of persons or departments who can be contacted for further information or explanation of duties under the plan.
- Establish an employee alarm system. If the employee alarm system is used for alerting fire brigade members, or for other purposes, use a distinctive signal for each purpose.
- List the types of evacuation to be used in emergency circumstances.
- Designate and train a sufficient number of employees to assist in the safe and orderly emergency evacuation of employees before implementing the EAP.
- Review the EAP with each covered employee upon initial assignment, when the employee’s responsibility or designated actions under the plan change, and when the plan changes.
Training action plan
You should develop an emergency action team prior to implementing the EAP. Begin by designating and training a sufficient number of employees to assist in the safe and orderly emergency evacuation of their coworkers.
- List the names or job titles of persons who can be contacted for more information on the plan. Trainees should understand:
- The employee alarm system,
- How to report fires and other emergencies, and
- Which personnel are designated to perform rescue and medical duties and their individual responsibilities.
- Explain how all employees will be accounted for after the emergency evacuation has been completed. Make sure employees understand:
- Critical plant operations and who is designated to remain behind to operate it/shut it down before they evacuate, and
- Emergency escape procedures and emergency escape routes.
Tips
A map of the facility showing specific areas, exit routes, exit doors, and head count locations is a useful training tool and should also be posted around the company.
If a fire occurs, safe and orderly evacuation is necessary. Your company should have an established evacuation plan, with procedures and exits indicated. Find out what it is and where you are expected to go during a fire or fire drill. A head count location should be established so that once everyone is evacuated, you meet at a designated spot to account for each employee.
Other than fires, severe weather emergencies are the most common emergency situations that occur. Severe weather emergencies include hurricanes, tornadoes, excessive heat, heavy snow, and extreme cold weather conditions.
If a bomb threat is made at your facility, always take the threat seriously. Immediately notify a supervisor or the safety manager of the threat and evacuate the premises (do not search for a bomb unless instructed by police to look for foreign or suspicious objects).
Checklist
Follow these checklists to ensure you and your employees are prepared for any potential emergencies.
Emergency action plan
- Is there an emergency action plan (EAP) in place detailing procedures employees should follow in an emergency?
- Does the EAP include procedures for all anticipated emergency situations (i.e., fire, tornado, bomb threat, or explosion)?
- Does the EAP include escape procedures and routes?
- Does the EAP contain procedures for those remaining in the facility to perform critical operations?
- Do you have headcount procedures (location or methods for accounting for employees)?
- If your company is located in a high-rise building, does your emergency program include appropriate escape information?
- Do you have an employee assistance program or some other means to provide counseling to employees should a disaster occur?
Disaster recovery
- Have you established a work location that could be used should your facility be unavailable due to disaster or emergency?
- Does the temporary work location have all necessary equipment so critical business functions can be carried out?
- Have necessary safety measures been taken to ensure that the temporary location is safe and will have necessary protective equipment?
Rescue workers
- Is air monitoring conducted to make sure rescue area is safe?
- Are rescue workers protected against hazards that may be encountered (i.e., asbestos, silica)?
- Are rescue workers provided proper protective equipment for the hazards they face?
Alarms and warnings
- Does the employee alarm system provide warning for necessary emergency action as called for in the emergency action plan?
- Is the employee alarm capable of being perceived above ambient noise or light levels by all employees in the affected portions of the workplace?
- Is the employee alarm distinctive and recognizable as a signal to evacuate the work area or take necessary actions?
- Have all employees been informed of the preferred means of reporting emergencies, such as manual pull box alarms, public address systems, radio or telephones?
- Are emergency telephone numbers posted near telephones, or employee notice boards, and other conspicuous locations?
- Have procedures been established for sounding emergency alarms in the workplace?
Fire alarm systems
- If you have a non-supervised fire alarm system, is it tested bimonthly?
- If you have a supervised employee alarm system (that is, does the alarm have a device that indicates system malfunction), is it tested yearly?
Entrances and exits
If you are a general industry employer, the Subpart E Exit routes regulations apply to your company. Your facility must provide a safe means of exiting from buildings or structures for the purpose of general egress, or for the purpose of exiting in the case of fire or other emergencies. In addition, you must also provide a clear and unobstructed path to the entrance of your facility.
Action steps
- Make sure exit routes are permanent.
- Separate exits using fire resistant materials.
- Limit openings into an exit.
- Ensure the number of exit routes is adequate.
- Ensure there are at least two exit routes.
- Provide adequate exit discharge.
- Make sure exit doors are unlocked.
- Use side-hinged exit doors.
- Ensure the capacity of exit routes is adequate.
- Provide exit routes that meet minimum height and width requirements.
- Keep exit routes free of explosive or highly flammable furnishings or other decorations.
- Maintain exit routes free and unobstructed.
- Ensure lighting and marking is adequate and appropriate.
- Maintain exit routes during construction, repairs, or alterations.
- Ensure that the alarm system is operable.
Training action plan
You must designate and train employees to assist in a safe and orderly evacuation of other employees.
You must also review the emergency action plan with each employee covered by the plan. This review should be conducted:
- When the plan is developed or the employee is assigned initially to a job,
- When the employee’s responsibilities under the plan change, and
- When the plan is changed.
Tips
- The line-of-sight to an exit sign must be clearly visible at all times.
- Maintain exit routes during construction, repairs, or alterations.
- Ceilings of exit routes must be at least 7 feet, 6 inches high.
- Exit access must be at least 28 inches wide at all points.
Checklist
Review these checklists to ensure exit routes at your facility meet compliance.
Exit design
- Are exit routes made of approved components and permanently attached to the building?
- Are exit routes designed and maintained to provide adequate headroom?
- Are exit doors designed so that no device or alarm failure will impede or prevent emergency use of exits?
Capacity of means of egress
- Are width and capacity of exit routes in compliance with OSHA standards?
- Is the capacity of the exit route sufficient for the occupant load?
- Where more than one way of exit access leads to an exit, does each have a width adequate for the number of persons it must accommodate?
Arrangement of exits
- Have you assured that no furnishings, decorations, or other objects are placed as to obstruct exits or exit visibility?
- Are exits adequately lighted so an employee with normal vision can see along the exit route?
Access to exits
- Are exit doors unlocked?
- Are exits readily accessible at all times?
- Are doors, from a room to an exit or to a way of exit access, of the side-hinged, swinging type?
- Is access to an exit NOT through a bathroom, or other room subject to locking (except where the exit is required to serve only the room subject to locking)?
- Are ways of exit access and the doors to exits to which they lead clearly recognizable as such?
- Is exit access arranged so that it will not be necessary to travel toward any area of high hazard occupancy in order to reach the nearest exit?
- Is exit access travel effectively shielded from high hazard locations by suitable partitions or other physical barriers?
- Is the minimum width of any way of exit access at least 28 inches?
Arrangement of exits
- Are exits marked by a readily visible sign?
- Is access to exits marked by readily visible signs if it is not immediately visible?
- Is any door, passage, or stairway that could be mistaken for an exit or a way of exit access, identified by a sign reading “Not an Exit” or similar designation, or identified by a sign indicating its actual character?
Protective enclosure of exits
- When an exit is protected by separation from other parts of the building, does the separating construction meet OSHA requirements (i.e., 1-hour fire resistance rating when the exit connects three stories or less)?
Fire protection
OSHA has many requirements concerning fire protection in the workplace. These requirements are found in Subpart L and in some other specific standards. Among the items addressed by OSHA standards is fire brigades, all portable and fixed fire suppression equipment, fire detection systems, and fire or employee alarm systems.
Action steps
- Provide approved and appropriate portable fire extinguishers.
- Mount, locate, and identify portable fire extinguishers so that they are readily accessible to employees without subjecting the employees to possible injury.
- Maintain fire extinguishers in a fully charged and operable condition.
- Inspect, maintain, and test fire extinguishers.
- Provide necessary training to employees who are expected to use portable fire extinguishers.
- Ensure that hose and standpipe systems meet OSHA requirements.
- Ensure all automatic sprinkler systems meet OSHA requirements.
- Maintain any fixed extinguishing systems per OSHA requirements.
- Follow OSHA requirements for any fire brigade you choose to form.
- Ensure fire detection systems are maintained properly.
- Provide an employee alarm system that gives warning for necessary emergency action as called for in the emergency action plan, or for reaction time for safe escape of employees from the workplace or the immediate work area, or both.
Training action plan
The level and type of training needed for fire protection depends on the level and type of fire protection your facility has in place. For instance, if you have a fire brigade, extensive training must be provided to fire brigade members, per 1910.156.
Similarly, if you provide portable fire extinguishers for employee use, such employees must be trained. This training must familiarize employees with the general principles of fire extinguisher use and the hazards involved with incipient stage fire fighting. Training must be provided upon initial employment and at least annually thereafter.
You must also provide training to any employees who have been designated to use fire fighting equipment as part of an emergency action plan. Training must be provided upon initial employment and at least annually thereafter.
You should also train all employees on the actions they need to take relative to your emergency alarm system. They should be familiar with the distinct sounds of the system and what each sound means.
Tips
- Fire extinguishers have to be kept in their designated locations at all times when not being used.
- When extinguishers are removed for maintenance or testing, they must be replaced by an operable unit.
Checklists
Review these checklists to ensure fire safety at your facility.
Fire extinguishers
- Are portable fire extinguishers provided, mounted, located, and identified so that they are readily accessible to employees?
- Are only approved portable fire extinguishers used?
- Are portable fire extinguishers maintained, fully charged, operating properly, and kept in designated places?
- Are portable fire extinguishers provided for employee use and selected and distributed based on the classes of anticipated fires and on the size and degree of hazard that would affect their use?
- Are travel distances to extinguishers appropriate?
- Are all portable fire extinguishers in the workplace inspected, maintained, and tested?
- Is hydrostatic testing performed by trained persons with suitable testing equipment and facilities?
- Are portable extinguishers hydrostatically tested at the intervals listed in Table L-1 of 1910.157?
- Has an educational program been provided to familiarize employees with the general principles of fire extinguisher use and the hazards involved with incipient stage fire fighting?
- Have employees been trained (who have been designated to use fire fighting equipment) in the use of the equipment?
Fire alarm
- Have you established an employee alarm system that complies with 1910.165?
- If the employee alarm system is used for alerting fire brigade members, or for other purposes, is a distinctive signal used for each purpose?
- Are all employee alarm systems in proper working condition, except when undergoing repairs or maintenance?
Fire detection systems
- Are all devices approved for use?
- Are fire detection systems and components returned to normal operating condition as soon as possible after each use or test?
Fire brigades
- If you choose to form a fire brigade, are the requirements of 1910.156 met?
Sprinkler systems
- Are automatic sprinkler system water control valves, air and water pressure checked weekly/periodically as required?
- Are fire control sprinkler heads kept clean?
- Are sprinkler heads protected by metal guards when exposed to physical damage?
- Is proper clearance maintained below sprinkler heads?
Flammable liquids
OSHA’s Flammable Liquids regulation, 1910.106, applies to all persons who handle, use, store, or transport flammable liquids. A flammable liquid means any liquid having a flashpoint at or below 199.4°F (within that definition, there are four categories of flammable liquids).
Action steps
- Ensure flammable liquids are stored and handled properly.
- Familiarize yourself with the different categories of flammable liquids (this will determine storage and usage requirements).
- Ensure containers meet the design requirements in 1910.106.
- Provide adequate drainage, dikes, and walls for tanks.
- Take precautions to prevent ignition by eliminating or controlling sources of ignition.
- Ensure the design (including selection of materials) fabrication, assembly, test, and inspection of piping systems containing flammable liquids is suitable for the expected working pressures and structural stresses.
- Provide suitable emergency and fire protection.
- Ensure adequate ventilation.
- Install electrical wiring properly.
- Follow proper procedures for dispensing liquids.
Training action plan
Any employee involved in storage, transfer, use, or disposal of flammable liquids needs to be trained to handle them safely and to follow your company’s established procedure.
Generally, training content should cover:
- Categories of flammable liquids,
- Handling procedures,
- Storage procedures, and
- Spill cleanup.
In addition, if your company receives, stores, or handles flammable liquids in storage tanks in areas that have the potential to flood, you need to have employees trained on emergency response procedures.
A hands-on approach is appropriate in this part of the training session. In fact, you may want to demonstrate how to do specific procedures related to flammables at your facility. Then allow each employee to try the procedure, so they can perform them correctly and so they will remember them better.
Tips
- When transferring flammable liquids, always bond and ground the containers.
- If purchasing plastic containers of five gallons or less for use with flammable liquids, purchase those with a built-in metal grounding strip.
Checklist
Review these checklists to ensure flammable liquid safety at your facility.
Containers
- Are all connections on drums and piping, vapor and liquid tight?
- Are all flammable liquids kept in closed containers when not in use (e.g., parts cleaning tanks, pans, etc.)?
- Are approved containers and portable tanks used for the storage and handling of flammable liquids?
- Are bulk drums of flammable liquids grounded and bonded to containers during dispensing?
- Are flammable liquids, such as gasoline, kept in an approved safety can?
- Are portable storage tanks equipped with emergency venting that will relieve excessive internal pressure caused by fire exposure?
- Are safety cans used for dispensing flammable liquids at a point of use?
- Are storage cabinets used to hold flammable liquids, labeled “Flammable — Keep Fire Away”?
- Are storage tanks adequately vented to prevent the development of excessive vacuum or pressure as a result of filling, emptying, or atmosphere temperature changes?
Handling
- Are all containers over 30 gallons in inside storage rooms stacked individually?
- Are firm separators placed between containers of combustibles or flammables, when stacked one upon another, to assure their support and stability?
Storage
- Are “No Smoking” rules enforced in areas involving storage and use of hazardous materials?
- Are all solvent wastes, and flammable liquids kept in fire-resistant, covered containers until they are removed from the worksite?
- Are all spills of flammable liquids cleaned up promptly?
- Is proper storage of flammable materials practiced to minimize the risk of fire including spontaneous combustion?
- Is there one clear aisle at least 3 feet wide?
Ladders
OSHA’s ladder regulations, at 1910.23, apply to any general industry workplace that uses ladders to perform duties (other than construction work) at high elevations.
Action steps
- Use ladders that are designed and approved for the intended purpose.
- Ensure ladders meet OSHA specifications.
- Follow all ladder safety requirements.
- Train employees in safe ladder use.
- Maintain ladders in a safe condition.
- Inspect ladders as needed.
- Remove defective ladders from service.
Training action plan
Training content for ladders and stairways depends on the types of equipment and structures your facility has and what work will be performed. In general, workers need to be trained as follows:
Ladders
Content should include:
- Inspecting the ladder,
- Setting up the ladder,
- Safe ladder use,
- Ascending and descending the ladder,
- Maintaining three points of contact,
- Recognizing hazards,
- Carrying tools and equipment, and
- Using the right ladder for the job.
Tips
- Workers on ladders generally do not require fall protection.
- Be careful that painting ladders or applying stickers does not hide damage.
- Make sure the ladder is the best tool for the job.
- Ensure workers understand associated hazards (e.g., electrical, wind) that they may have to consider with selecting and/or using a ladder.
Checklist
Review these checklists to ensure ladder safety at your facility.
Design and construction
- If wood, is the portable ladder not coated with any material that may obscure structural defects?
- If metal, is the portable ladder made of corrosion-resistant material or protected against corrosion?
- If metal, are the rungs and steps of the portable ladder corrugated, knurled, dimpled, coated with skid-resistant material, or otherwise treated to minimize slipping?
- Are the rungs, steps, and cleats of the portable ladder spaced at least 10 inches and not more than 14 inches apart?
- Do the rungs, steps, and cleats of the portable ladder have a minimum clear width of 11.5 inches?
Stepladders
- Is the stepladder equipped with a metal spreader or locking device that securely holds the front and back sections in an open position while the ladder is in use?
Stepstools
- Are the steps on the stepstool spaced at least 8 inches and not more than 12 inches apart?
- Does the stepstool have a minimum clear width of 10.5 inches?
Inspection and maintenance
- Are portable ladders inspected regularly, and as necessary, to ensure they are in safe condition?
- Are deficiencies corrected or repaired before an employee uses the portable ladder again?
- If a portable ladder correction or repair cannot be made immediately, are employees prevented from using the portable ladder until repaired?
- If a portable ladder repair involves structural integrity, does a qualified person perform or supervise the correction or repair?
Training
- Is each employee who uses a portable ladder trained on how to properly use the ladder?
- Is each employee who uses a portable ladder trained to recognize the fall hazards in the work area?
- Is training conducted by a qualified person?
Note: Qualified, under this OSHA requirement, describes a person who, by possession of a recognized degree, certificate, or professional standing, or who by extensive knowledge, training, and experience has successfully demonstrated the ability to solve or resolve problems relating to the subject matter, the work, or the project. - Is information and training provided in a manner that each employee understands?
- Is retraining provided when deficiencies in performance or knowledge are noted, or there are changes in the workplace or equipment?
Personal protective equipment
OSHA’s Subpart I regulations apply to all persons involved in hazardous processes; environmental, chemical, radiological hazards; or mechanical irritants that are capable of causing injury or impairment of any body part through absorption, inhalation, or physical contact. The categories of personal protective equipment (PPE) include: eye and face equipment, head protection, hand protection, foot protection, fall protection, and respiratory protection (information about respiratory protection is provided in a separate topic area under Respiratory Protection, 1910.134).
Action steps
- Assess the workplace to determine what hazards are present that require PPE.
- Document and certify the PPE assessment.
- Provide appropriate and approved PPE based on the workplace hazards.
- Instruct employees in proper PPE usage.
- Ensure employees wear proper PPE.
- Establish inspection and maintenance procedures for PPE.
Training action plan
OSHA requires that you provide training to each employee who is required to use PPE. Each such employee shall be trained to know at least the following:
- When PPE is necessary.
- What PPE is necessary.
- How to properly don, doff, adjust, and wear PPE.
- The limitations of the PPE.
- The proper care, maintenance, useful life, and disposal of the PPE.
Each affected employee must also demonstrate an understanding of the training and the ability to use PPE properly, before being allowed to perform work requiring the use of PPE.
When you have reason to believe that any affected employee who has already been trained does not have the understanding and skill required, you must retrain each such employee. Circumstances where retraining is required include, but are not limited to, situations where:
- Changes in the workplace render previous training obsolete.
- Changes in the types of PPE to be used render previous training obsolete.
- Inadequacies in an employee’s knowledge or use of assigned PPE indicate that the employee has not retained the requisite understanding or skill.
Tips
- Make sure that protective eyewear does not affect the fit of respirators.
- Make sure that protective eyewear does not disturb the proper positioning of corrective lenses so as to inhibit or limit the employee’s vision.
- Ensure employees disinfect shared protective eyewear after each use.
- Always replace a hard hat if it sustains an impact, even if damage is not noticeable.
- Don’t let workers wear hard hats backward unless the hat has been tested and approved for such use.
Checklist
Review these checklists to ensure proper PPE usage at your facility.
General
- Are all employees required to use PPE as needed?
- Is PPE functional and in good repair?
- Is protective clothing and equipment provided and used when cleaning up spilled toxic or otherwise hazardous materials or liquids?
- Is PPE provided and are all employees required to use PPE as needed to protect against injury?
- Does PPE have ANSI or ASTM specifications marked on it?
Training
- Has each individual who is required to use PPE been provided with training?
- Have the trained individuals demonstrated an understanding of the training and the ability to use PPE properly before being allowed to perform work requiring the use of PPE?
- Are individuals retrained when there is reason to believe that they do not have the understanding or skill to use PPE properly?
Recordkeeping
- Have you documented that a hazard assessment has been done, when, and by whom?
- Have you documented that PPE training has been done, who has received it, and when?
Head, foot, and hand protection
- Are protective helmets used wherever there is the possible danger of head injury from impact, or from falling or flying objects, or from electrical shock and burns?
- Is protective footwear used wherever there is the danger of foot injuries due to falling or rolling objects, or objects piercing the sole, and where feet are exposed to electrical hazards?
- Are appropriate protective gloves used wherever there is the danger to hands of exposure to hazards such as those from skin absorption of harmful substances, severe cuts or lacerations, severe abrasions, punctures, chemical burns, thermal burns, and harmful temperature extremes?
Eye and face protection
- Are individuals issued and required to wear appropriate eye protective devices while participating or observing activities which present a potential eye safety hazard?
Personal fall protection
- Have all impacted individuals been trained to use personal fall protection equipment?
- Is the equipment inspected daily before use?
- Does fall protection meet the design requirements in 1910.140?
- Are ropes, belts, lanyards, lifelines, and harnesses used for personal fall protection compatible with connectors used?
Posting requirements
- Are all areas and equipment requiring the use of PPE devices posted with a sign indicating this requirement?
Process safety management
OSHA’s 1910.119 regulation applies to those companies that deal with any of more than 130 specific toxic and reactive chemicals in listed quantities (See 1910.119 Appendix A); it also includes any Category 1 flammable gas (as defined in 1910.1200(c)) or a flammable liquid with a flashpoint below 100°F (37.8°C) on site in one location, in a quantity of 10,000 pounds (4535.9 kg) or more (with a few exceptions, as outlined in 1910.119(a)(1)(ii)(A) and (B)).
Action steps
- Ensure employee participation in the process safety management program.
- Conduct adequate hazard analyses.Implement safety operating procedures.
- Conduct process safety training.
- Ensure process safety for contractors.
- Conduct pre-startup safety reviews.
- Ensure integrity of process equipment.
- Ensure management of change process and procedures are adequate.
- Investigate incidents per OSHA requirements.
- Ensure emergency planning and response efforts are adequate.
- Establish a process safety compliance audit process.
Training action plan
You must train each employee involved in operating a process and each employee before being involved in operating a newly assigned process. Training must include:
- An overview of the process and the operating procedures.
- Specific safety and health hazards.
- Emergency operations including shutdown.
- Safe work practices applicable to the employee’s job tasks.
Also, you must provide refresher training at least every three years, and more often if necessary, to each employee involved in operating a process to assure that the employee understands and adheres to the current operating procedures of the process. You, in consultation with the employees involved in operating the process, must determine the appropriate frequency of refresher training.
Documentation
You must prepare a record that contains the identity of the employee, the date of training, and the means used to verify that the employee understood the training.
Tips
- OSHA’s Process Safety Management (PSM) standard requires that mechanical integrity inspections have to be documented (including the name of the person performing the inspection or test) and list the information to be recorded.
- The PSM standard states that the employer must establish and implement written procedures.
- To comply with the PSM standard, employers must document that equipment complies with recognized and generally accepted good engineering practices. For existing equipment designed and constructed in accordance with codes, standards, or practices that are no longer in general use, the employer must determine and document that the equipment is designed, maintained, inspected, tested, and operated in a safe manner.
- All process hazard analyses must be updated and revalidated, based on their completion date, at least every five years.
- Employers must consult with employees and their representatives on the conduct and development of process hazard analyses and on the development of the other elements of process management, and they must provide to employees and their representatives access to process hazard analyses and to all other information required to be developed by the standard.
- Contract employees must be instructed on known potential fire, explosion, or toxic release hazards related to their job and the process, and in the applicable provisions of the emergency action plan.
Checklist
Review these process safety management checklists.
Process hazard analysis
- Has written process safety information been compiled before conducting any process hazard analysis (PHA)?
- Are the process hazard analyses performed by teams with expertise in engineering and process operations?
- Has a system been established to promptly address the team’s findings and recommendations?
- Are the PHA’s updated and revalidated to assure that the process hazard analysis is consistent with the current process?
Incident investigation
- Has each incident been investigated which resulted in, or could reasonably have resulted in, a catastrophic release of highly hazardous chemicals in the workplace?Has a system been established to promptly address and resolve the incident investigation report findings and recommendations?
Emergency action plan
- Has an emergency action plan been established and implemented for the entire plant in accordance with the requirements of 1910.38?
Written program
- Do you have an appropriate written program for PSM compliance?
- Do you have a written program regarding employee participation?
- Do written operating procedures exist for each covered process?
- Have safety and health considerations been included in the operating procedures?
Contractors
- Have safe work practices been developed and implemented for employees and contractors to control hazards?
- For employees and contractor employees involved in operating a process do initial and refresher training records exist?
- Has each employee and contractor employee been trained before being involved in a newly assigned process?
Pre-startup safety review
- Has a pre-startup safety review been performed for all new facilities and for modified facilities when the modification is significant enough to require a change in process safety information?
Mechanical integrity
- Are there written procedures to maintain the ongoing integrity of process equipment?
- Are appropriate inspections and tests performed on each item of process equipment included in the program?
- Have appropriate checks and inspections been made to assure equipment is installed properly and consistent with design specifications and manufacturer’s instructions?
Hot work permits
- Have hot work permits been issued for all hot work operations conducted on or near a process covered by the PSM standard?
Management of change
- Are there written procedures for managing changes (except for “replacements in kind”) to process chemicals, technology, equipment, and procedures and changes to facilities that affect a covered process?
Audits
- Do you conduct an audit of compliance with PSM at least every three years?
- Do you retain the two most recent compliance audit reports?
Training
- Have employees been trained properly regarding PSM?
- Are appropriate training records kept?
Signs and markings
OSHA’s 1910.144-.45 regulations provide specifications for signs and tags and are intended to cover all safety signs except those designed for streets, highways, railroads, and marine regulations. These specifications do not apply to plant bulletin boards or to safety posters.
Action steps
- Use appropriate colors for identification of equipment and hazards per OSHA regulations.
- Ensure emergency stop bars and buttons on hazardous machines are red.
- Ensure yellow is used for designating caution and for marking physical hazards such as: Striking against, stumbling, falling, tripping, and “caught in between.”
- Follow OSHA specifications for accident prevention signs and tags.
- Instruct employees in recognizing accident prevention signs and tags and the appropriate action to take regarding those markings.
- Ensure messages on signs and tags are clear and to the point.
Training action plan
Training on accident prevention signs and tags is required prior to or at the time of initial assignment to areas where accident prevention signs and tags are used. Training content should generally include:
- Sign color,
- Symbols,
- Labeling, and
- Company-specific marking systems.
Consider other safety training issues relative to safety signs such as hazard communication and the specific posting requirements of the chemical-specific standards found in Subpart Z of the 1910 regulations. Training might also cover the information found in the poster describing employee rights under OSHA (poster 2203) which must be displayed somewhere where workers will see it.
OSHA does not require training documentation for Specifications for Accident Prevention Signs and Tags, but it is always prudent to keep records anyway. Training records can tell you who was trained on what, when, and what was covered.
Tips
- The lines used to delineate the aisles may be any color so long as they clearly define the area considered as aisle space. The lines may be composed of dots, square, strip or continuous, but they too must define the aisle area.
- The recommended width of aisle markings varies from two inches to six inches; therefore, any width two inches or more is considered acceptable.
- Danger sign — The colors red, black, and white must be those of opaque glossy samples as specified in Table 1 of Fundamental Specification of Safety Colors for CIE Standard Source “C”, American National Standard Z53.1-1967.
- Caution sign — Standard color of the background must be yellow; and the panel, black with yellow letters. Any letters used against the yellow background must be black. The colors must be those of opaque glossy samples as specified in Table 1 of American National Standard Z53.1-1967.
- Safety instruction signs — Standard color of the background must be white; and the panel, green with white letters. Any letters used against the white background must be black. The colors must be those of opaque glossy samples as specified in Table 1 of American National Standard, Z53.1-1967.
Checklist
Review these checklists for signs and markings at your facility.
Hazardous substances
- Is every hazardous chemical in the workplace labeled with identification and hazard warnings?
- Are safety and other containers painted appropriately?
- Are equipment, containers, materials, or areas where biohazards are or could be present labeled with the biological hazard warning?
- Are any entrances to regulated areas where the 13 carcinogens listed at 1910.1003 are present marked with appropriate signage warning of the danger?
- Are signs posted warning of presence and hazards of asbestos where required?
Aisles
- Are permanent aisles and passageways appropriately marked?
Materials handling
- Are clearance signs warning of clearance limits provided?
- Are powered industrial trucks appropriately marked?
- Are cranes marked with the load rating on each side?
- Are crane pendant control boxes clearly marked for identification of functions?
Emergency
- Are exits marked by a readily visible sign?
- Are areas that could be mistaken for an exit identified by a sign reading “Not an Exit” or something similar?
- Are portable fire extinguishers mounted, located, and identified so they are readily accessible?
Ladders
- Are defective ladders withdrawn from service and tagged or marked as “Dangerous, Do Not Use”?
Lockout/tagout
- Do tagout devices warn against hazardous conditions if the machine or equipment is energized?
Confined spaces
- Are completed confined space permits posted at an appropriate location?
- Are signs posted at permit-required confined spaces describing the dangers present?
OSHA posters
- Is OSHA’s Form 2203 (or 3165) describing the OSH Act posted appropriately?
- Is the annual summary of OSHA No. 300 Form posted appropriately?
- Are citations received from OSHA posted at or near the place the violation(s) occurred?
Electrical
- Is the manufacturer’s description marked on all electrical equipment used?
- Are covers for pull and junction boxes permanently marked “HIGH VOLTAGE”?