Safety management industry standards
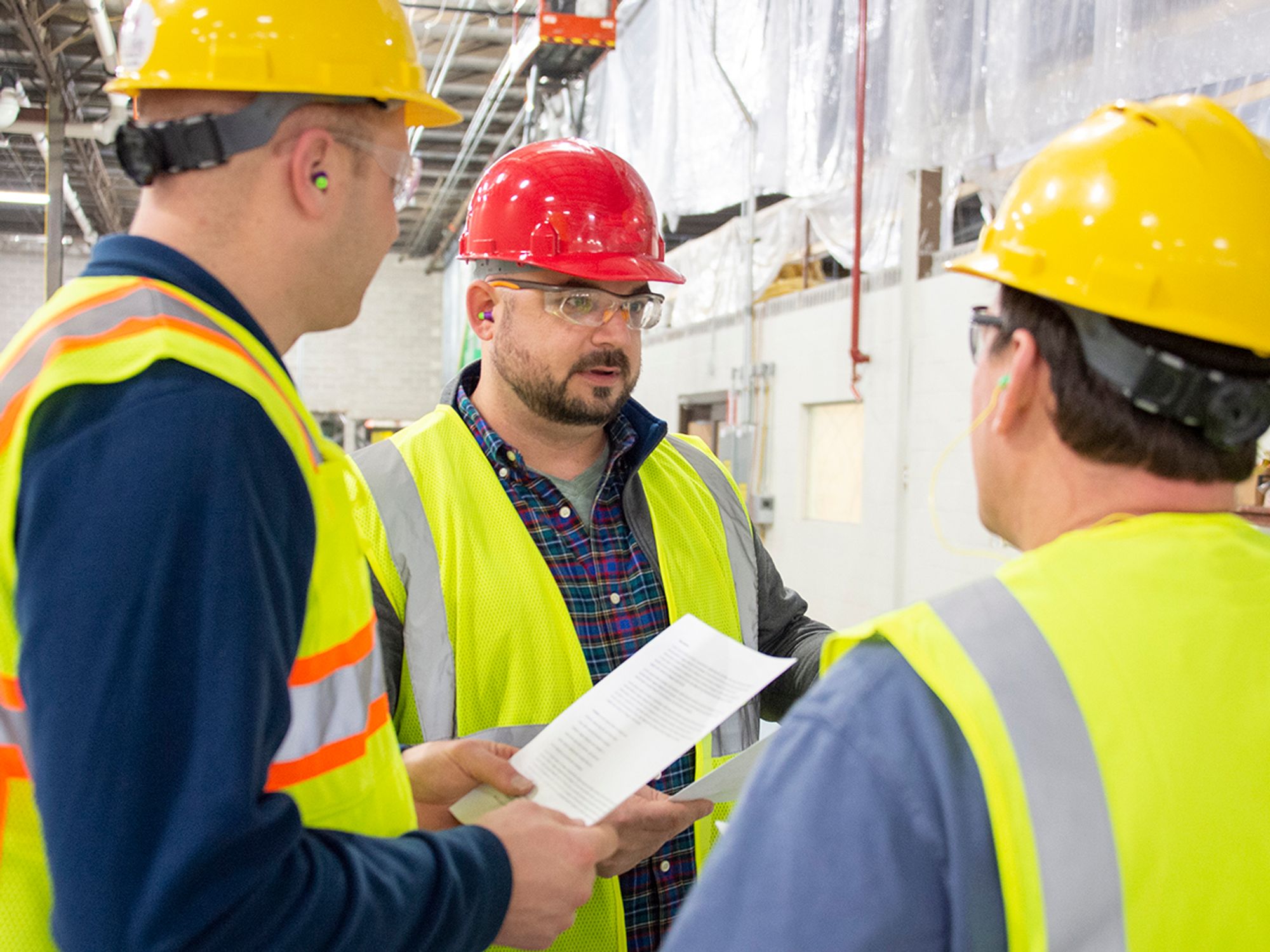
- There are two major industry standards to help guide employers in implementing a safety plan for the workplace: ISO 45001 and ANSI Z10.
- In certain industries, suppliers or potential contracts may require companies to implement one standard over the other.
Two major voluntary industry standards can help employers design and implement a safety and health management system:
- ISO 45001 — Occupational health and safety management systems – Requirements with guidance for use
- ANSI/ASSP Z10 — Occupational Health and Safety Management Systems
ISO 45001
The International Organization for Standardization (ISO) 45001 Occupational health and safety management systems — Requirements with guidance for use is a standard for the implementation and maintenance of occupational safety and health management systems. The standard guides companies in taking a systematic and proactive approach to worker safety, giving safety an equal “seat at the table” alongside other management systems such as environmental, quality, IT and data security, and product safety, all of which have had international standards for a while.
Like other management systems standards, ISO 45001 reduces risk and increases performance. In the case of ISO 45001, the risk is to worker safety and health. The standard provides a framework to systematically improve safety and business processes at the same time. It requires using concepts and techniques such as the hierarchy of controls, risk assessment, and root-cause analysis, along with significant input and participation from workers. While these techniques help reduce injuries and illnesses, they also improve business performance.
The indirect benefits of obtaining certification include recognition for achieving an international benchmark, lowering costs, reducing turnover and lost time, and reducing equipment and process downtime. The standard has other benefits as well. Investors will likely feel more confident in an ISO 45001-certified company because the company has shown it is actually identifying and managing the risks.
To achieve the maximum benefits and to claim official certification, a company must go through a third-party audit and approval process from an accredited registrar. Completing full certification is certainly no easy task. If a company already has an ISO management system in place, however, the transition will be less complicated.
For companies that want to implement a management system but are not interested in certification, the ISO 45001 standard can be used as a best-practice guidance. A company can purchase the standard and self-implement to whatever degree is appropriate, understanding that internal impacts (such as fewer injuries and better performance) may be seen, but external benefits (such as recognition) will not be gained without certification.
ANSI Z10
The American National Standards Institute (ANSI) Z10 Occupational Health and Safety Management Systems standard was originally released in 2005. Like most other ANSI standards, ANSI Z10 is “self-certifying” in that there is not necessarily a requirement for a third-party auditor to conduct a conformance assessment. A company can purchase the standard and implement it with no assistance from a third party.
The ANSI standard follows the same general principles as the Occupational Safety and Health Administration (OSHA)’s Recommended Practices, but provides much more guidance and many tools, covering such topics as management leadership, employee involvement, hazard identification/prevention/control, training, and evaluation. It contains tools such as job hazard analysis guidance and risk matrices.
Deciding on a standard
In choosing a standard, a company should consider what the organization hopes to accomplish and also what the stakeholders or customers are asking for. Some companies may choose to achieve certification to ISO 45001, but implement additional elements from ANSI Z10.
In certain industries, suppliers or potential contracts may ask for one standard over the other. Employers should talk with some organizations that have used these systems to find out pros and cons of each.