Work activity requirements
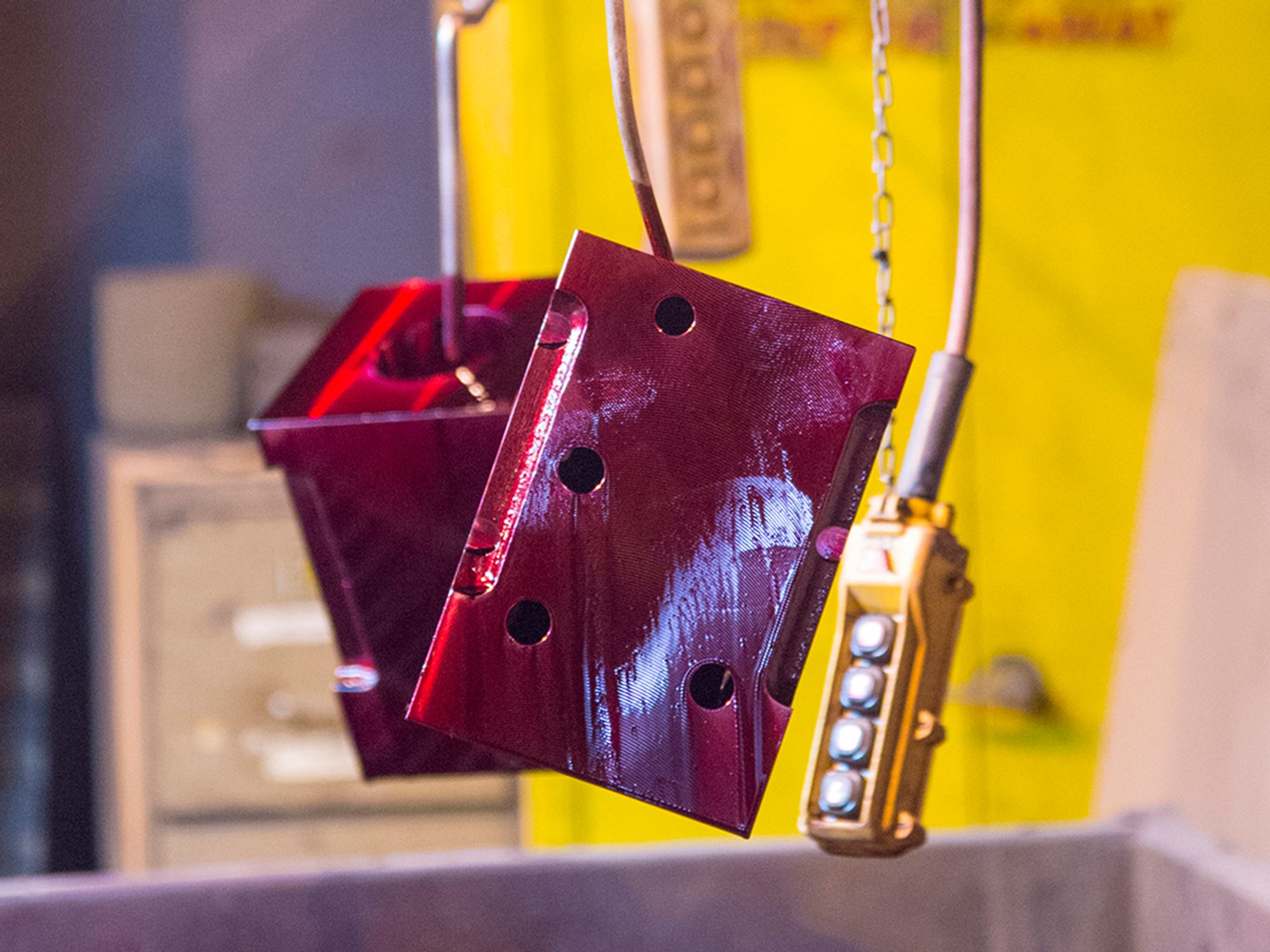
- Certain work activities — especially dipping, coating, welding, and cutting — have significant and specific ventilation hazards, with corresponding requirements.
Some work activities require more ventilation than others. In particular, workers who are involved in dipping and coating processes and in welding and cutting processes are at risk from a variety of airborne substances.
Dipping and coating
Dipping and coating pose inhalation and fire hazards due to the liquids used in these processes. Employers are responsible for controlling these hazards as much as possible and providing workers with appropriate protection.
When a liquid in a dip tank creates an exposure hazard covered by a standard listed in 1910 Subpart Z, worker exposure must be controlled as required by that standard.
The ventilation provided in a vapor area must keep the airborne concentration of any substance below 25 percent of its lower flammable limit (LFL). Employers must have a system that sounds an alarm and automatically shuts down the operation when the vapor concentration for any substance in the exhaust airstream exceeds 25 percent of its LFL.
Exhaust air may not be recirculated when any substance in that air poses a health hazard to employees or exceeds 25 percent of its LFL. The employer must ensure that any exhaust air recirculated from a dipping or coating operation using flammable liquids or liquids with flashpoints greater than 199.4°F (93°C) is:
- Free of any solid particulate that poses a health or safety hazard for employees; and
- Monitored by approved equipment.
When mechanical ventilation is used, each dip tank must have an independent exhaust system unless the combination of substances being removed will not cause a fire, explosion, or chemical reaction. Mechanical ventilation must draw the flow of air into a hood or exhaust duct.
Any mechanical ventilation used must conform to the following standards that are incorporated by reference as specified in 1910.6:
- American National Standards Institute (ANSI) Z9.2-1979, Fundamentals Governing the Design and Operation of Local Exhaust Systems;
- National Fire Protection Association (NFPA) 34-1995, Standard for Dip Tanks Containing Flammable or Combustible Liquids;
- American Conference of Governmental Industrial Hygienists (ACGIH,Industrial Ventilation: A Manual of Recommended Practice (22nd ed., 1995); and
- ANSI Z9.1-1971, Practices for Ventilation and Operation of Open-Surface Tanks, and NFPA 34-1966, Standard for Dip Tanks Containing Flammable or Combustible Liquids.
A tank cover or material that floats on the surface of the liquid in a dip tank may be used to replace or supplement ventilation. The method or combination of methods used must maintain the airborne concentration of the hazardous material and the workers’ exposure within the limits specified in paragraphs (b)(1) and (b)(2) of 1910.124.
Welding and cutting
Welders can be exposed to a number of fumes, gases, and dusts. These contaminants can harm the health of workers and accumulate to the point of causing a fire. Ventilation can help to reduce their concentration.
According to the Occupational Safety and Health Administration (OSHA), whenever and wherever welding, also known as “hot work,” occurs, everyone involved in the operation must be aware of welding fumes and gases and take necessary, especially ventilation, precautions.
Welding ventilation techniques vary. Often, however, a relatively simple ventilation method like the appropriate use of fans is all that is needed. OSHA’s standard at 1910.252(c) specifies that if mechanical ventilation is used, it must consist of either:
- General mechanical ventilation, or
- A local exhaust system.
Mechanical ventilation changes the air. In contrast, local exhaust systems, like hoods at the arc and fans, remove fumes and smoke at the source. Both ventilation methods help to reduce the concentration of hazardous fumes and gases.
Ventilation also prevents the accumulation of flammable gases, vapors, and dusts that could cause fire. Open spaces, too, can help reduce accumulations.
When ventilation doesn’t give enough protection or when welding creates an oxygen-deficient area, workers should wear respirators. Workers should also be trained not to get too close to the fume or gas plume. They should know the symptoms of overexposure to fumes and gases and leave the area if symptoms develop.
Confined spaces can pose additional fume and gas hazards because welding fumes and gases can displace oxygen or fill a confined space. Flammable or combustible fumes and gases can accumulate and cause fire, explosion, and asphyxiation. For these reasons, employers should evaluate the atmospheres of the confined space for hazards and use ventilation and respirators properly.
Because many toxic gases and vapors on the job cannot be smelled or seen, atmospheric testing and monitoring is very important. Generally, if a space has a hazardous atmosphere, the hazard must be eliminated or reduced by:
- Purging the hazardous atmosphere,
- Displacing the noncombustible gas,
- Flushing the hazardous atmosphere, and/or
- Ventilating with forced air.
For more information about welding and cutting, see Welding and Cutting.