Administrative and work practice controls
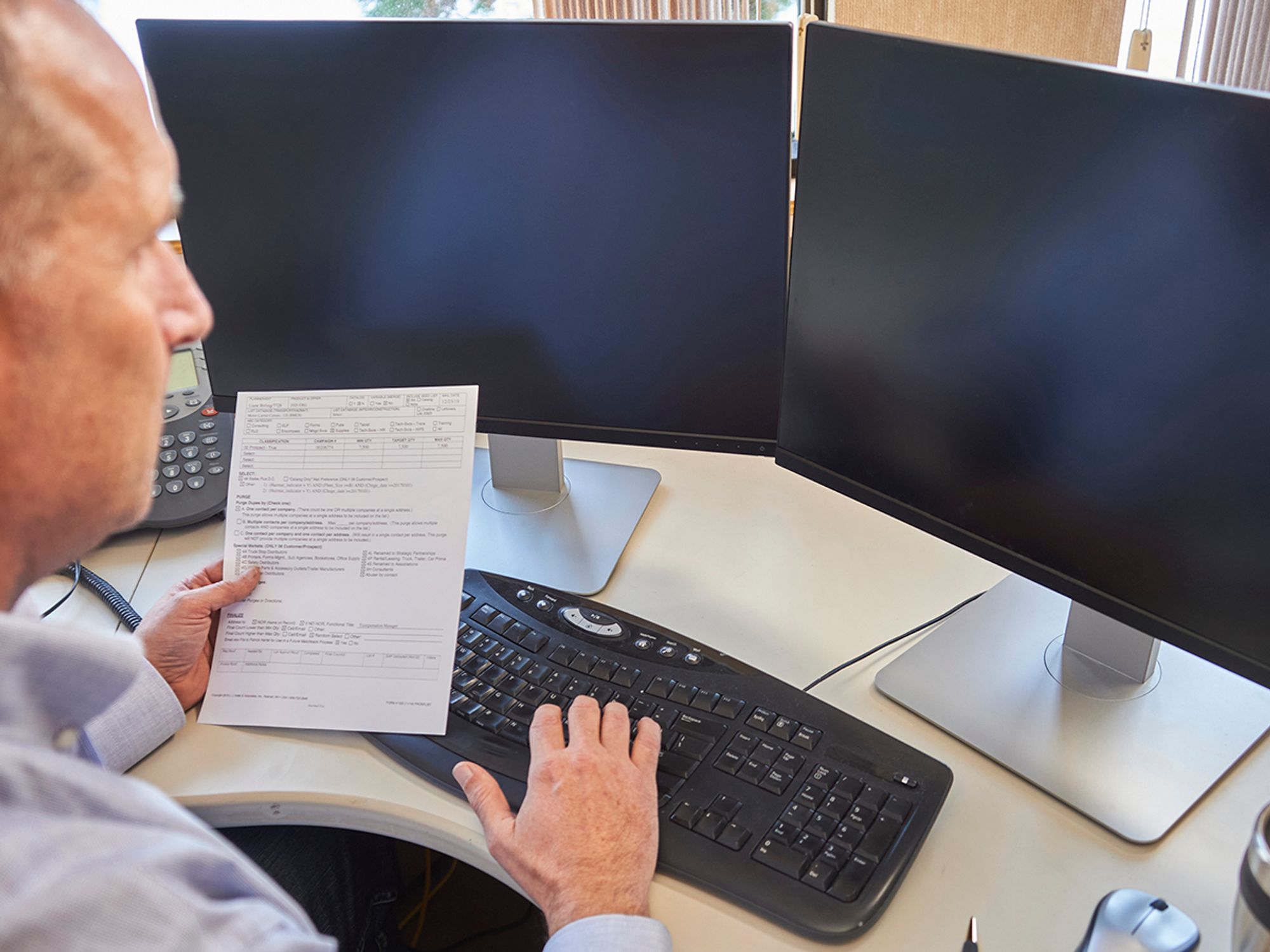
- Administrative and work practice controls emphasize worker activities, such as reducing time spent working in a noisy area or shutting down unused equipment, to help reduce noise exposure.
Unlike engineering controls that prevent hazardous noise from reaching a worker, administrative controls manage workers’ activities to reduce their exposure. Closely related to administrative controls are work practice controls, which emphasize safe practices.
Administrative and work practice controls are usually less expensive than engineering controls because there are no significant capital costs involved in changing or modifying equipment. In some cases, administrative controls can reduce employee exposure to noise and increase productivity by rotating employees through a demanding, noisy task. Work practice controls can also improve performance by emphasizing safe work practices.
Administrative and work practice controls may not be as effective as engineering controls because they don’t control the noise exposure. Noisy machines are still noisy and the exposure is still present. Some controls that can be used to reduce exposure include:
- Reducing the time employees spend working in noisy areas;
- Rotating two or more employees so that each is exposed to noise less than 85 decibels, averaged over an eight-hour day.
- Shutting down noisy equipment when it’s not needed for production.
- Ensuring that employees maintain equipment so that it runs smoothly and quietly.
- Ensuring that employees know how to perform their tasks and operate equipment at safe noise levels.
- Using warning signs to identify work areas where noise exceeds safe levels.
- Encouraging employees to report noise hazards to supervisors.
If it’s not possible to eliminate or control noise with an engineering control, it may be possible to control it with an administrative control. However, if an administrative control won’t reduce employee exposures to safe levels, an additional noise-control tool may be needed — hearing protectors.