Waste minimization
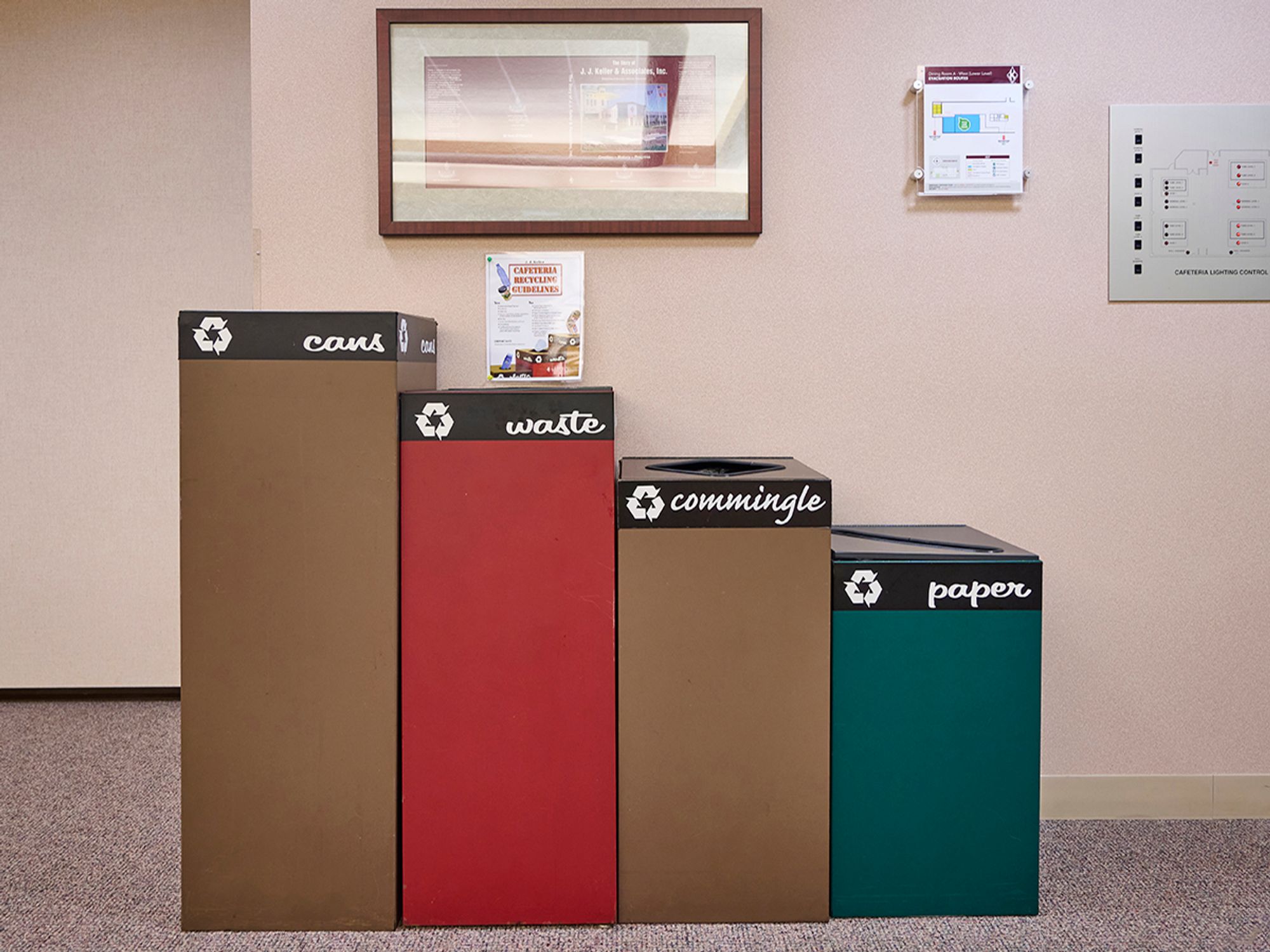
- A waste minimization plan can help a company meet goals for sustainability.
- Compacting, neutralizing, diluting, and incineration are not typically considered waste minimization practices.
Reducing, reusing, and/or eliminating waste is a major component of corporate sustainability. All organizations generate waste, and these items can range from food wrappers to fluorescent lamps to ink cartridges to cardboard boxes to manufacturing byproducts... the list is endless.
Under the Resource Conservation and Recovery Act (RCRA), facilities that generate or manage hazardous waste must certify that they have a waste minimization program in place that reduces the quantity and toxicity of hazardous waste generated to the extent economically practicable.
A waste minimization plan can help a company meet goals for sustainability — even if operations do not generate hazardous waste. Even better, pollution prevention plans can identify areas to reduce or eliminate waste at the source.
Waste minimization refers to the use of source reduction and/or environmentally sound recycling methods prior to energy recovery, treatment, or disposal of wastes. Waste minimization does not include waste treatment, that is, any process designed to change the physical, chemical, or biological composition of waste streams. For example, compacting, neutralizing, diluting, and incineration are not typically considered waste minimization practices. A sound hierarchical approach to materials management includes source reduction, recycling, energy recovery, treatment, and finally, disposal.
Source reduction, commonly known as pollution prevention, reduces or eliminates the generation of waste at the source and refers to any practice that reduces the use of hazardous materials in production processes.
Common examples of source reduction include:
- Early retirement of equipment such as mercury-containing devices like switches and thermostats;
- Reformulating or redesigning products, such as creating new polyvinyl chloride (PVC) compounds without using lead;
- Using less toxic materials, such as switching to the use of lead-free solder in manufacturing;
- Improving work practices, such as reorganizing paint batches in order to reduce cleaning operations.
Recycling, or reclaiming value from production byproducts, can often be used when source reduction is not economically practical. Recycling includes the reuse or recovery of in-process materials or materials generated as byproducts that can be processed further on-site or sent offsite to reclaim value. Recycling is a broad term that encompasses the reuse of materials in original or changed forms rather than discarding them as wastes. Recycling can also be thought of as the collection and reprocessing of a resource so it can be used again, though not necessarily for its original purpose.
Examples of recycling include:
- Direct use/reuse of a waste in a process to make a product, such as reusing a purge product used to clean paint lines rather than disposing of it by incineration.
- Processing the waste to recover or regenerate a usable product, such as collecting vapor from dry cleaning operations, turning it back into liquid, and reusing the liquid to clean more clothes.
- Using/reusing waste as a substitute for a commercial product. When mercury is recycled from old equipment like switches, it can be used in new products that still require mercury, such as fluorescent bulbs. Recycling of mercury has been so successful that there is now enough recycled mercury in the U.S. that manufacturers do not need to use new mercury from mines.
A material is “recovered” if it is processed to recover a usable product, or if it is regenerated. This is known as materials recovery. In energy recovery, waste is converted into usable fuel.