Lean manufacturing
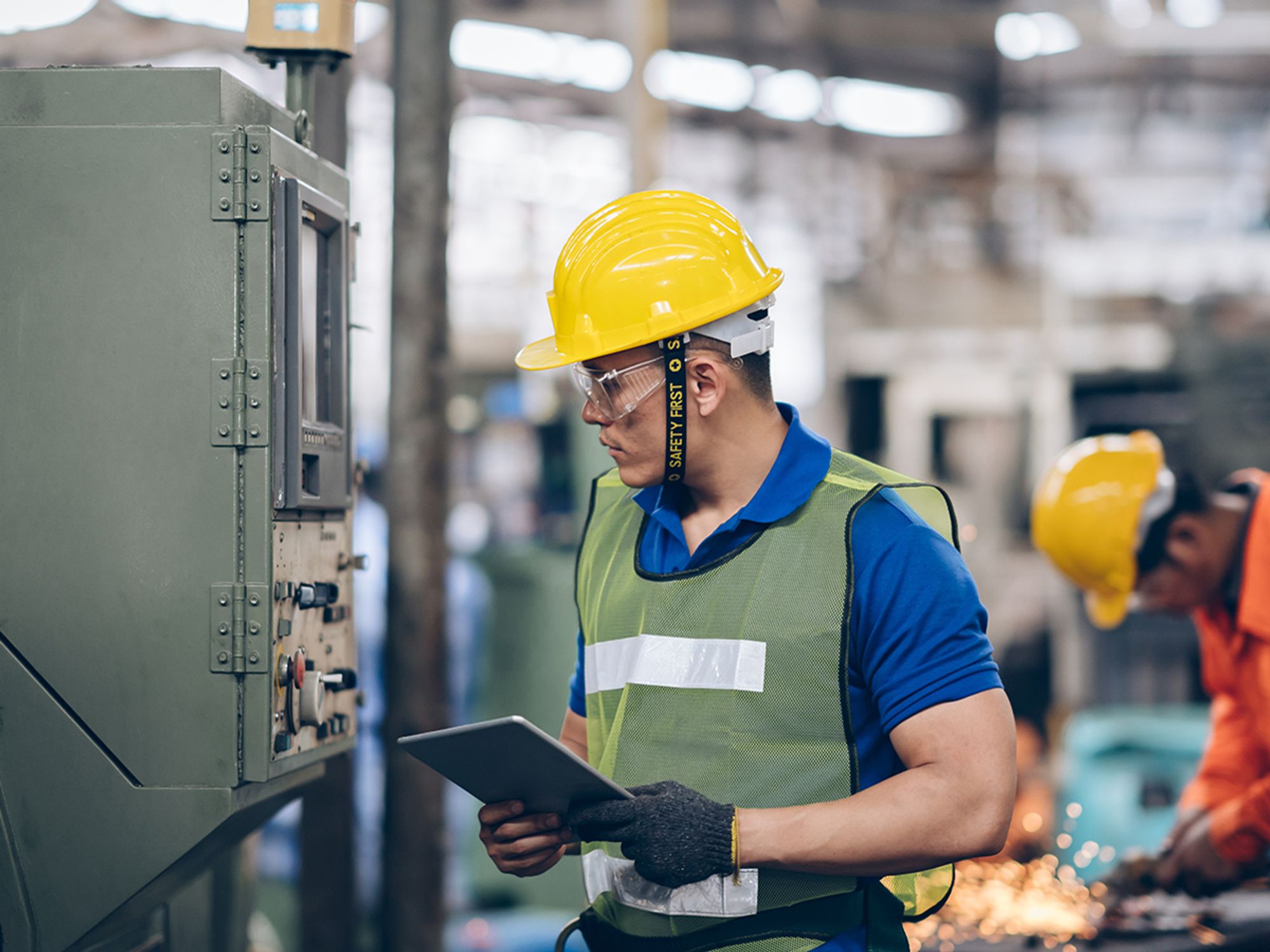
- Most organizations start by implementing lean techniques in a certain production location or at a “pilot” facility, and then grow the use of the methods over time.
Lean manufacturing is a business model and assembly of planned methods that highlights the eradication of non-value-added activities (waste) while delivering superior products on time at the least cost with higher efficiency. In the United States, lean implementation is quickly growing in popularity throughout diverse manufacturing and service areas including aerospace, automotive, electronics, furniture production, and health care as a central business strategy for developing a competitive edge.
While the focal point of lean manufacturing is on driving fast and ongoing improvement in cost, quality, service, and delivery, substantial environmental advantages usually “ride the coattails” or happen coincidentally as a result of these production-focused efforts. Lean production techniques typically develop a culture of steady improvement, employee empowerment, and waste minimization.
Lean involves a core paradigm change from a standard “batch and queue” mass production to a product-aligned “one-piece flow” pull production. Whereas “batch and queue” involves mass production of huge lots of products in advance based on likely or forecasted customer demands, a “one-piece flow” system alters production activities in a way that processing steps of unlike types are conducted right away, adjacent to each other in a constant flow.
This shift needs largely controlled processes operated in a well-maintained, ordered, and unsoiled environment that includes principles of employee-involved, system-wide, ongoing improvement.
While most of these methods are interdependent and can happen jointly, most organizations start by implementing lean techniques in a certain production location or at a “pilot” facility, and then grow the use of the methods over time. Companies commonly tailor these methods to tackle their own distinct needs and circumstances. In doing so, they may create their own terminology around their unique methods.