Storage containers at tank battery, separation, and treating areas
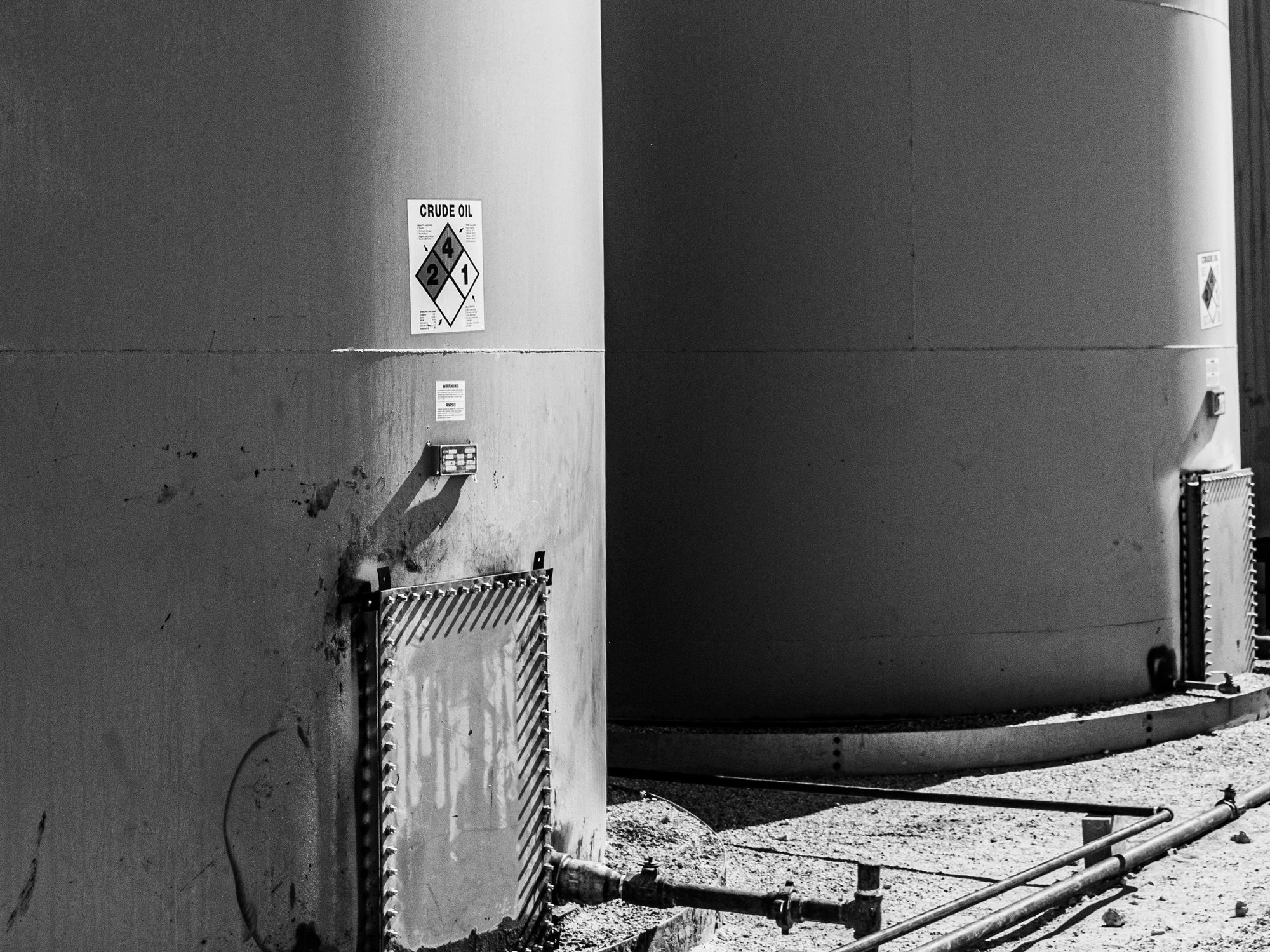
- Bulk storage containers at oil production facilities must be compatible with the materials stored and condition of storage; provided with appropriate secondary containment; undergo regular inspection; and more.
An oil production facility typically includes, at a minimum, a wellhead, a tank battery, and flowlines connecting the wellhead to the tank battery and in some cases, the tank battery to an injection wellhead. The tank battery includes separation and treating equipment, a crude oil or condensate container (oil stock tank), drums of oil-based products and typically a produced water container, which receives both oil and produced water from the separator. Bulk storage containers at oil production facilities must be:
- Compatible with the materials stored and condition of storage;
- Provided with secondary containment sized for the largest single container and sufficient freeboard to contain precipitation for those containers at the tank battery, separation, and treating facility installations;
- Visually inspected periodically and upon a regular schedule for deterioration and maintenance needs, including the foundation and support; and
- Engineered in accordance with good engineering practice to prevent discharges by:
- Ensuring adequate container capacity to assure that a container will not overfill if a pumper/gauger is delayed in making regularly scheduled rounds;
- Providing overflow equalizing lines between containers so that a full container can overflow to an adjacent container;
- Providing adequate vacuum protection to prevent container collapse during a pipeline run or other transfer of oil from the container; or
- Providing high level sensors to generate and transmit an alarm signal to the computer where the facility is subject to a computer production control system.
Alternative measures are provided for flow-through process vessels and produced water containers in lieu of the secondary containment and inspection requirements of Part 112.9(c)(2) and (3) as described below.
Flow-through process vessels
Separation and treating installations at an oil production facility typically include equipment whose primary purpose is to separate the well fluid into its marketable or waste fractions (e.g., oil, gas, produced water, and solids), and to treat the crude oil as needed for further storage and shipping. Flow-through process vessels, such as horizontal or vertical separation vessels (e.g., heater-treater, separator, gun barrel, free-water knockout, etc.), have the primary purpose of separating the oil from other fractions (water and/or gas) and sending the fluid streams to the appropriate container.
Flow-through process vessels at separation and treatment installations are bulk storage containers and count toward the facility aggregate oil storage capacity. They are also subject to general secondary containment under 112.7(c) and the bulk storage container requirements of 112.9(c). The facility owner or operator must either provide sized secondary containment for flow-through process vessels in accordance with 112.9(c)(2) and inspect them following 112.9(c)(3) or comply with the general secondary containment under 112.7(c) and alternative measures provided in 112.9(c)(5).
Produced water containers
Produced water containers are bulk storage containers typically located within the tank battery. Produced water containers are part of the process that separates the oil from other fractions (water and/or gas).
Oil discharges to navigable waters or adjoining shorelines from an oil/water mixture in a produced water container may cause harm. Such mixtures are regulated as oil under Part 112. Therefore, the capacity of produced water containers counts toward the facility aggregate oil storage capacity. Produced water containers are subject to general secondary containment under 112.7(c) and the bulk storage container requirements in 112.9(c). The facility owner or operator must either provide sized secondary containment for produced water containers in accordance with 112.9(c)(2) and inspect them following 112.9(c)(3) or comply with general secondary containment under 112.7(c) and alternative measures provided in 112.9(c)(6).
The alternative measures require that the facility owner or operator conduct visual inspections; perform maintenance and corrective action; and remove, or stabilize and remediate, oil discharges. Additionally, a professional engineer (PE) must describe in the Spill Prevention, Control, and Countermeasure (SPCC) Plan and certify that a practice is established that is designed to remove the amount of free-phase oil from the produced water container on a scheduled and routine basis.